This article introduces the paper ['Optimization of Die casting process based on Taguchi approach'] published by ['Elsevier'].
1. Overview:
- Title: Optimization of Die casting process based on Taguchi approach
- Author: K.Ch. Apparao and Anil Kumar Birru
- Publication Year: 2017
- Publishing Journal/Academic Society: Materials Today: Proceedings 4 (2017) 1852–1859, 5th International Conference of Materials Processing and Characterization (ICMPC 2016)
- Keywords: optimization, Taguchi method, Die casting
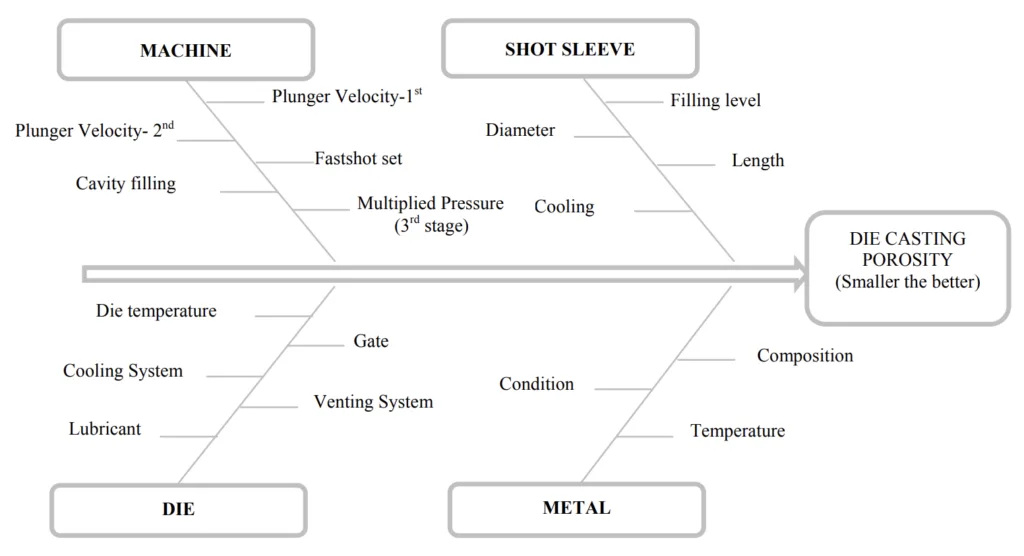
2. Abstracts or Introduction
Due to its attributes of light weight and good formability, aluminium die casting is significantly important in the automotive industry. Porosity is a frequently encountered defect in aluminium die castings, limiting the application of die-cast parts in critical high strength applications. This research conceptualized the Taguchi approach to determine optimal settings for die casting parameters. The aim is to enhance the die casting quality and efficiency of Al-Si8Cu3Fe (EN AC-46500) aluminium alloy by minimizing porosity formation. The study investigated the effects of selected parameters on porosity and established optimal parameter settings using the Taguchi approach. The results demonstrated that optimized parameters effectively reduce porosity in Al-Si8Cu3Fe aluminium alloy die castings.
3. Research Background:
Background of the Research Topic:
In contemporary industries, there is a growing demand for lightweight materials, particularly in the automotive sector. Consequently, the global production and consumption of aluminium alloys have increased. Aluminium remains a widely utilized metal in die casting for engineering components across aerospace, defense, and automotive industries. Die casting (DC) is a specialized manufacturing process essential for producing parts unattainable through other methods. Its advantages include mold conformity, favorable mechanical properties, and cost-effectiveness. The aluminium die casting process involves numerous parameters that, when effectively managed, can improve the quality of die-cast parts. Internal porosity is a prevalent defect in die castings, primarily caused by air entrapment during the initial filling stages of the die casting process. Porosity in pressure die castings remains a persistent issue, and despite advancements in research, design, and development, the increasing complexity of castings makes complete porosity elimination challenging. However, parameter optimization techniques can limit porosity to non-critical areas. Porosity in aluminium alloys is of significant concern due to its detrimental effects on mechanical properties, machinability, and surface quality. Implementing the Taguchi technique in die casting can substantially reduce porosity formation.
Status of Existing Research:
Porosity in pressure die castings has been a long-standing problem. Despite considerable research, design, and development efforts, the increasing complexity of casting designs demanded by industry makes it virtually impossible to eliminate porosity completely. However, casting parameter optimization techniques can limit porosity to non-critical areas.
Necessity of the Research:
Traditional trial and error methods for optimizing die casting parameters are time-consuming and costly. The Taguchi technique offers a more efficient approach for continuous and rapid quality improvements in die casting by systematically optimizing process parameters to minimize porosity formation, which is crucial for enhancing the mechanical and surface properties of aluminium die castings.
4. Research Purpose and Research Questions:
Research Purpose:
The primary focus of this research is to investigate the influence of process parameters on porosity formation in pressure die casting to enhance the quality of castings.
Key Research:
The research aims to identify the optimal settings of die casting parameters to minimize porosity formation in Al-Si8Cu3Fe aluminium alloy die castings using the Taguchi approach.
Research Hypotheses:
This paper does not explicitly state research hypotheses. However, implicitly, the research operates under the assumption that by applying the Taguchi method to optimize die casting parameters (pouring temperature, filling time, die temperature, and injection pressure), it is possible to significantly reduce porosity in Al-Si8Cu3Fe aluminium alloy die castings.
5. Research Methodology
Research Design:
The research employed the Taguchi method, a statistical experimental design technique, to optimize die casting process parameters. A L9 orthogonal array with three levels for each of the four selected parameters was utilized to conduct experiments and analyze the effects of these parameters on porosity. The quality characteristic aimed for was "lower the better" casting porosity.
Data Collection Method:
Experiments were conducted on a high-pressure die casting machine, Technocrats model TDC-120. The test sample was a square plate of AlSi8Cu3Fe aluminium alloy with dimensions 100mm x 100mm x 20 mm. For each of the nine trial conditions defined by the L9 orthogonal array, three castings were produced using a randomization technique. Casting density was measured using an experimental density device, and porosity was calculated using equation (1):
Porosity (%) =(Po-Ps) × 100 (1)
Where ps is the measured casting density and po is the density of a fully dense casting having no porosity (2.79 g/cm³).
Analysis Method:
The Signal-to-Noise (S/N) ratio was used to analyze the variation in porosity, with the goal of minimizing it ("Lower the better" characteristic). The S/N ratio was calculated using equation (2):
S/N ratio (n) = − 10 log (∑(1/yᵢ²)/n) (2)
Analysis of Variance (ANOVA) was performed to determine the statistical significance and percentage contribution of each parameter to the casting porosity.
Research Subjects and Scope:
The research focused on optimizing the die casting process for Al-Si8Cu3Fe (EN AC-46500) aluminium alloy. The process parameters investigated were:
- Pouring temperature (Factor A)
- Filling time (Factor B)
- Die temperature (Factor C)
- Injection pressure (Factor D)
The ranges and levels for these parameters are detailed in Table 1.
Table 1 Process parameters with their ranges and values at three levels
Parameter destination | Process parameters | Range | Level 1 | Level 2 | Level 3 |
---|---|---|---|---|---|
A | Pouring temperature(°C) | 650-750 | 650 | 700 | 750 |
B | Filling time (ms) | 40-130 | 40 | 85 | 130 |
C | Die temperature (°C) | 180-260 | 180 | 220 | 260 |
D | Injection pressure(bar) | 120 - 240 | 120 | 180 | 240 |
6. Main Research Results:
Key Research Results:
The analysis revealed that injection pressure (parameter D) and pouring temperature (parameter A) are the most significant parameters affecting casting porosity. Optimal levels for minimizing porosity were identified as:
- Pouring temperature: Level 3 (750°C)
- Filling time: Level 3 (130 ms)
- Die temperature: Level 1 (180°C)
- Injection pressure: Level 3 (240 bar)
ANOVA results indicated that injection pressure contributed approximately 46.931% and pouring temperature contributed 43.606% to the variation in casting porosity. Filling time and die temperature had smaller contributions of 4.733% and 4.730% respectively.
Analysis of presented data:
Figure 1 Cause and effect diagram, illustrates the casting process parameters that may affect die casting porosity. Pouring temperature, filling time, die temperature, and injection pressure were identified as critical parameters for experimental design.
Figure 2 Average values of casting porosity for Al-Si8Cu3Fe aluminium alloy castings under the parameter values given in Table 1, and Figure 3 Average values of the S/N rations forAl-Si8Cu3Fe aluminium alloy castings under the parameter values given in Table 1, visually represent the effects of each parameter at different levels on porosity and S/N ratio. These figures, along with Table 4 Average values of casting density at the different levels and their main effects and Table 5 Average values of S/N ratios at the different levels(1-3) and their main effects, show that porosity tends to decrease at higher levels of pouring temperature, filling time, and injection pressure, while it is minimized at the lowest level of die temperature.
Table 6 ANOVA of die casting density and Table 7 S/N ANOVA of die casting density, quantify the contribution of each parameter to the variation in casting porosity. These tables confirm that injection pressure and pouring temperature are the most influential parameters.
Figure Name List:
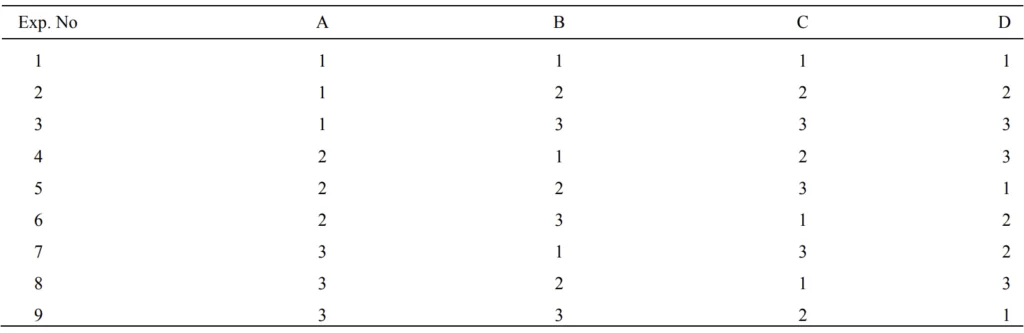
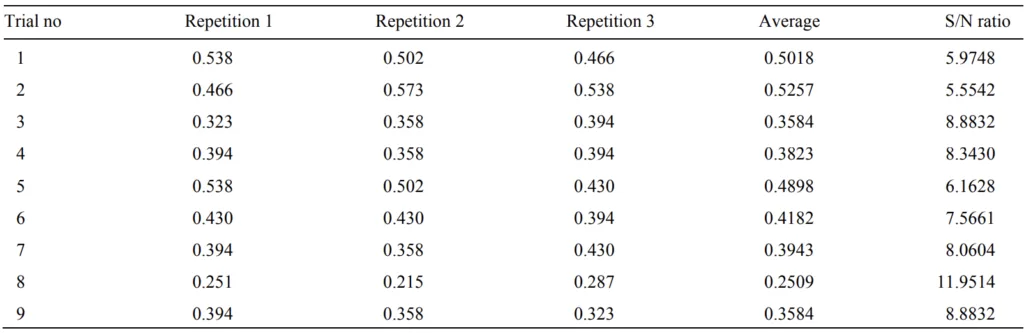

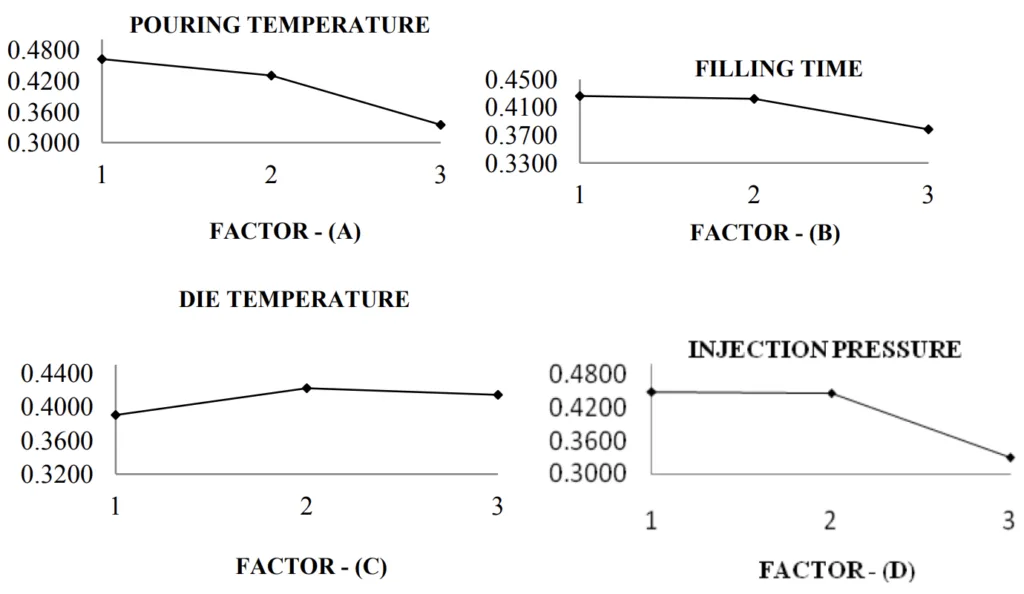
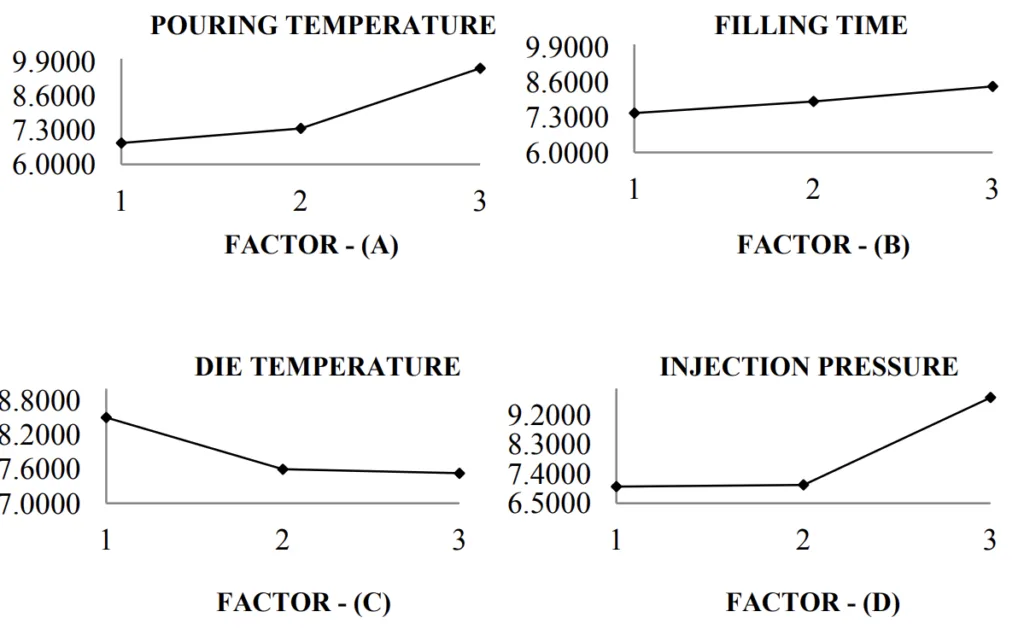
7. Conclusion:
Summary of Key Findings:
The study conclusively demonstrated that variations in die casting process parameters significantly impact porosity formation in Al-Si8Cu3Fe aluminium alloy die castings. Pouring temperature, filling time, die temperature, and injection pressure are identified as influential parameters affecting porosity. Optimal parameter levels for minimizing porosity were determined using the Taguchi method: pouring temperature at 750°C, filling time at 130 ms, die temperature at 180°C, and injection pressure at 240 bar.
Academic Significance of the Study:
This research provides a systematic approach using the Taguchi method for optimizing die casting parameters to minimize porosity. It highlights the effectiveness of statistical experimental design in improving die casting quality and offers valuable insights into the influence of individual process parameters on porosity formation in Al-Si8Cu3Fe aluminium alloy.
Practical Implications:
The findings offer practical guidelines for die casting industries to optimize their process parameters for Al-Si8Cu3Fe aluminium alloy, specifically to reduce porosity and enhance casting quality. By implementing the identified optimal settings, manufacturers can improve the mechanical properties and surface finish of die-cast parts, leading to higher quality components, especially for critical applications.
Limitations of the Study and Areas for Future Research:
The paper does not explicitly mention limitations or future research areas. However, it can be inferred that the study is limited to the specific alloy (Al-Si8Cu3Fe) and parameter ranges investigated. Future research could explore:
- The applicability of these optimal parameters to other aluminium alloys and die casting machine types.
- Investigating other process parameters not considered in this study.
- Exploring the interaction effects between parameters in more detail.
- Validating these findings in industrial production settings for scalability and robustness.
8. References:
- [1] Anuj Dixit, Koushik Kumar, Journal of Materials Today: Proceedings,2, (2015), pp 2359 – 2366.
- [2] Shashi Prakash Dwivedi, S. Sharma, R. K. Mishra., Journal of Advanced Materials Manufacturing &Characterization, 14 (2014), pp 81-82.
- [3] Dahle, A. K., Arnberg, L., Apelian, D., AFS Trans., 1997, 160, 963-969.
- [4] Emadi, D., Gruzleski. Effects of casting and melt variables on porosity in directionally solidified Al-Si alloys. AFS Trans., 1994, 95, 307-312.
- [5] Klein, F. and Wimmer, P. In NADCA International Die Casting Congress, Indianapolis, 2-5 October 1995, paper T95-035, pp. 101-111.
- [6] Chiesa, F., Fuoco, R. and Gruzleski, J. E.. Int. J. Cast Metals, 1995, 7(2), 113-122.
- [7] Ross, P. J. Taguchi Techniques for Quality Engineering, 1988 (McGraw-Hill, New York).
- [8] Logothetis, N. Total Quality Control, 1992 [Prentice-Hall International (UK) Limited].
- [9] Taguchi, G. Introduction to Quality Engineering, 1986 (Asian Productivity Organization, UNIPUB, White Plains, New York).
- [10] Phadke, S. M. Quality Engineering Using Robust Design, 1989 (Prentice-Hall, Englewood Clis, New Jersey).
- [11] Johnston, R. E. Design of experiments: Taguchi in the foundry. AFS Trans., 1989, 82, 415-418.
- [12] Johnston, R. E. Statistical methods in foundry experiments, AFS Trans. 72(1964) 17-18.
- [13] Makhlouf, M., Wang, L., Apelian, D. and Yang, L.Thermal conductivity of Al die casting alloys, AFS Trans., 1999, 12, 501-505.
- [14] D.M.Byrne, S. Taguchi, The Taguchi Approach to parameter Design, Quality progress, December 1987, pp. 19-26
- [15] Roy, R. K. Design of Experiments Using the Taguchi Approach: 16 Steps to Product and Process Improvement, 2001 (J. Wiley, New York).
- [16] Taguchi, G. and Konishi, S. Orthogonal Arrays and Linear Graphs, 1987 (American Supplier Institute, Dearborn, Michigan).
9. Copyright:
- This material is "K.Ch. Apparao and Anil Kumar Birru"'s paper: Based on "Optimization of Die casting process based on Taguchi approach".
- Paper Source: https://doi.org/10.1016/j.matpr.2017.07.097
This material was summarized based on the above paper, and unauthorized use for commercial purposes is prohibited.
Copyright © 2025 CASTMAN. All rights reserved.