This article introduces the paper ['Ultra Large Castings to Produce Low Cost Aluminum Vehicle Structures'] presented at the ['SAE TECHNICAL PAPER SERIES']
1. Overview:
- Title: Ultra Large Castings to Produce Low Cost Aluminum Vehicle Structures
- Author: T. N. Meyer, M. J. Kinosz, E. M. Bradac, M. Mbaye, J. T. Burg and M. A. Klingensmith
- Publication Year: 1999
- Publishing Journal/Academic Society: SAE TECHNICAL PAPER SERIES, presented at the Government/Industry Meeting, Washington, D.C., April 26-28, 1999.
- Keywords: Ultra Large Castings, Aluminum Vehicle Structures, Low Cost, Die Casting, Metal Mold, Multiport Injection, Vertical Casting Process, Automotive, Lightweighting.
2. Research Background:
Background of the Research Topic:
The automotive industry is continuously striving to reduce vehicle weight to meet increasingly stringent environmental emission standards and enhance fuel efficiency. While aluminum offers significant lightweighting potential, its broader adoption in ground transportation vehicles (autos, sport utility vehicles/light trucks/vans, buses, and large trucks) is hindered by its higher cost compared to steel. This cost is attributed to both the basic material cost of aluminum products (e.g., sheet, extrusion, or cast product) and the subsequent fabrication and assembly costs (e.g., forming, joining, finishing operations).
Status of Existing Research:
Conventional manufacturing of vehicle structures, such as floor pan frames, typically involves assembling multiple formed steel stampings using resistance spot welding. While Alcoa's existing Aluminum Vacuum Die Casting (AVDC) process (U.S. Patent 5,370,171) is capable of producing high-quality thin wall castings, further advancements are needed to address the cost and complexity associated with ultra-large components. The level pour casting process, utilized in aerospace, is unsuitable for complex geometries and presents challenges in runner removal for large, thin-walled parts.
Necessity of the Research:
To overcome the cost barrier of lightweight aluminum structures and facilitate their high-volume production (e.g., 100,000 units/year) in the automotive sector, there is a critical need for innovative casting processes capable of producing ultra-large, thin-wall components at a reduced cost. This research aims to bridge the cost gap between conventional steel assemblies and lighter weight aluminum alternatives.
3. Research Purpose and Research Questions:
Research Purpose:
The primary research purpose is to develop and demonstrate a novel casting process for producing ultra-large, thin-wall aluminum components for vehicle structures. This process aims to significantly reduce both component count and assembly costs, thereby lowering the overall cost of lightweight transportation vehicle structures.
Key Research:
The key research focuses on the development and implementation of a low pressure, hot chamber, multiport injection vertical casting process. The research also involves:
- Selecting a demonstration part that represents size and geometric complexity.
- Developing a hot chamber injection system compatible with economic and process requirements.
- Designing the part to meet structural and casting process requirements, optimizing metal injection port locations and initial injection conditions.
- Establishing a system for molten metal delivery to the injector system.
- Specifying, fabricating, installing, and debugging all system components.
Research Hypotheses:
While not explicitly stated as hypotheses, the research operates under the premise that:
- Ultra-large castings, produced via the developed process, can substantially reduce the cost of aluminum vehicle structures.
- A low-pressure, hot-chamber, multiport vertical casting process is a viable and efficient method for manufacturing such large, thin-wall aluminum components.
4. Research Methodology
Research Design:
This research employs a developmental and demonstrative research design. It involves the conceptualization, design, fabrication, and testing of a novel ultra-large casting system. The Chrysler minivan liftgate inner panel was chosen as a demonstration component to evaluate the process.
Data Collection Method:
Data collection methods include:
- Computer Simulation: Finite Element Analysis (FEA) for structural performance evaluation and casting simulation (filling and solidification) to optimize process parameters and part design.
- System Development and Testing: Practical implementation and testing of the developed casting system, including component fabrication, system integration, and process shakedown.
- Cost Analysis: Economic evaluation of the production facility and process to assess the cost-effectiveness of the ultra-large casting approach.
Analysis Method:
- Finite Element Analysis (FEA): Used to analyze the structural performance of the cast aluminum inner panel and compare it to the conventional steel assembly.
- Casting Simulation: Employed to optimize the casting process, including injection port locations, die temperature control, and cooling requirements, aiming to avoid gas entrapment, porosity, and ensure directional solidification.
- Economic Analysis: Performed to estimate the production cost of the cast aluminum part and compare it to the cost of the existing steel assembly.
Research Subjects and Scope:
The research focuses on the development of an ultra-large casting process for aluminum vehicle structures. The scope is limited to the demonstration of the process using a specific automotive component – the Daimler-Chrysler minivan liftgate inner panel. The system is designed to be capable of producing large automotive components, exemplified by the floor pan frame and side wall aperture structure.
5. Main Research Results:
Key Research Results:
The research successfully developed a low pressure, metal mold, multiport injection vertical casting process for producing ultra large thin wall components. A dedicated casting system was designed and fabricated at Alcoa's Technology Center, capable of producing parts up to 3 M long, 1.7 M wide, and 0.4 M high. The Chrysler minivan liftgate inner panel, an 11-part steel assembly, was redesigned as a single-piece aluminum casting for process demonstration (Figure 2b). FEA confirmed the cast aluminum design met Daimler-Chrysler's performance requirements. While an initial weight reduction goal was 40%, the stiffness-driven design, constrained by the existing steel part envelope, resulted in a weight reduction closer to 25%. Cost analysis of a production facility (Figure 5) indicated a potential cost premium of $7.00 to $14.00 for the 26 lb cast aluminum part compared to the 33 lb steel assembly.
Data Interpretation:
The development of the hot chamber metal injection system and the maintenance of metal quality beneath the mold are highlighted as key achievements. The successful casting of the complex geometry liftgate inner panel demonstrates the feasibility of the ultra-large casting process. The cost analysis (Figure 6) suggests that while a cost premium exists, the potential for weight reduction and part consolidation offers significant advantages. Achieving the targeted 40% weight reduction, potentially through aluminum-specific design optimization, could further reduce the cost premium and enhance the competitiveness of aluminum structures.
Figure Name List:
- Figure 1. Candidate Parts for Ultra Large Castings
- Figure 2a. Conventional Steel Inner Panel
- Figure 2b. Single Aluminum Cast Inner Panel
- Figure 3. Liftgate Permanent Mold
- Figure 4. Minivan Located on Press Platen to Scale
- Figure 5. Production System Layout
- Figure 6. Cost Breakdown for Production Facility
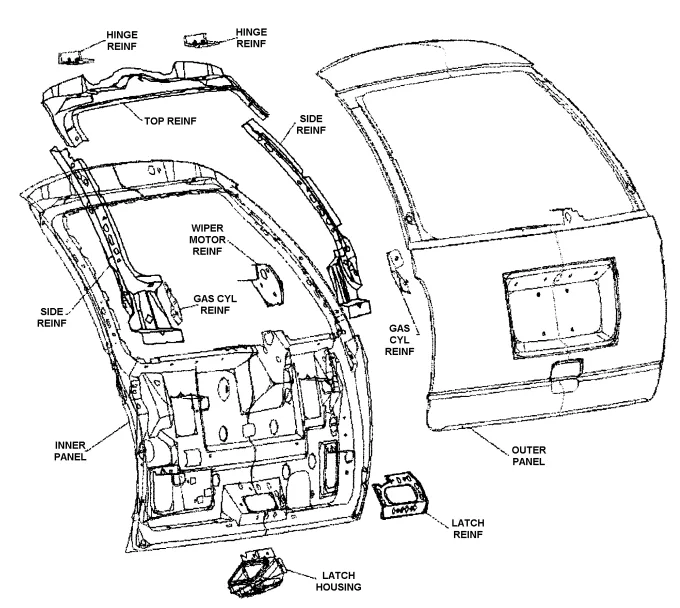
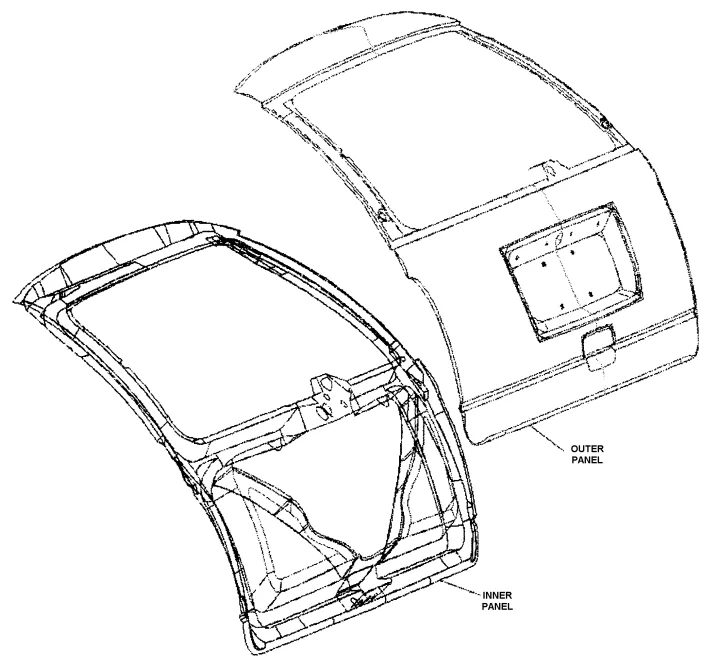
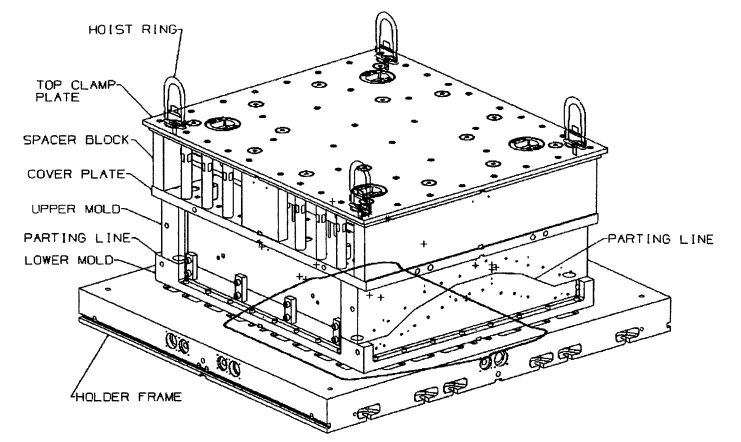
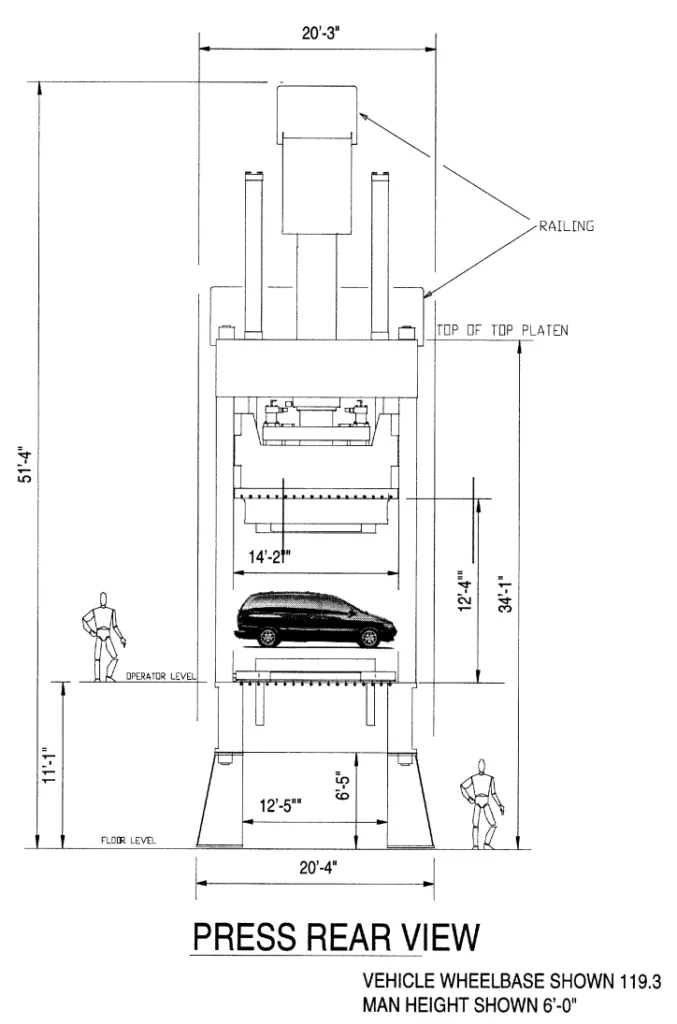
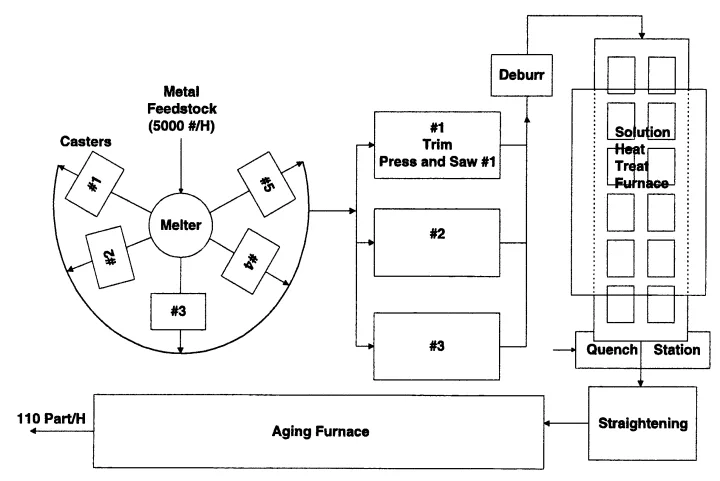
6. Conclusion:
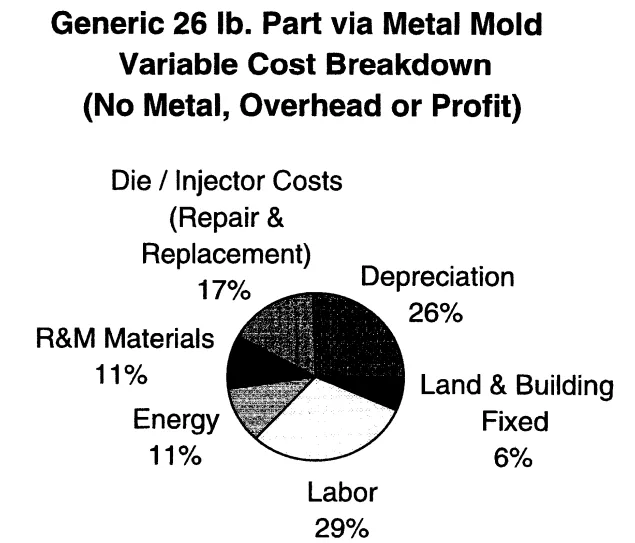
Summary of Key Findings:
This research successfully demonstrated the feasibility of a low pressure, hot chamber, multiport vertical casting process for producing ultra-large, thin-wall aluminum vehicle structures. The developed process and casting system offer a pathway to significant cost reduction in lightweight aluminum components by reducing part count and assembly operations. The Chrysler minivan liftgate inner panel demonstration showcased the capability to cast complex geometries and achieve weight reduction compared to conventional steel assemblies.
Academic Significance of the Study:
This study contributes to the advancement of die casting technology by introducing and validating a novel approach for producing large, complex aluminum castings. It provides valuable insights into the design and implementation of low-pressure, hot-chamber, multiport injection systems and their application in automotive lightweighting.
Practical Implications:
The successful development of this ultra-large casting process holds significant practical implications for the automotive industry. It offers a potential solution to reduce the cost of aluminum vehicle structures, making them more economically competitive with steel and facilitating broader adoption of lightweighting strategies to improve fuel efficiency and reduce emissions.
Limitations of the Study and Areas for Future Research:
The weight reduction achieved in the demonstration was limited by the stiffness requirements imposed by the existing steel part envelope. Future research should focus on optimizing part design specifically for aluminum to maximize weight reduction potential. Further process optimization, industrial scaling, and exploration of broader applications beyond the demonstration component are recommended areas for future research.
7. References:
- U.S. Patent 5,370,171, December 06, 1994, "Die Casting Process and Equipment," by J. R. Fields, et al., Alcoa.
8. Copyright:
- This material is "T. N. Meyer, M. J. Kinosz, E. M. Bradac, M. Mbaye, J. T. Burg and M. A. Klingensmith"'s paper: Based on "Ultra Large Castings to Produce Low Cost Aluminum Vehicle Structures".
- Paper Source: SAE TECHNICAL PAPER SERIES 1999-01-2252
This material was summarized based on the above paper, and unauthorized use for commercial purposes is prohibited.
Copyright © 2025 CASTMAN. All rights reserved.