This article introduces the paper ['Finite element analysis for die casting parameters in high-pressure die casting process'] presented at the ['CHINA FOUNDRY']
1. Overview:
- Title: Finite element analysis for die casting parameters in high-pressure die casting process
- Author: Xin-yu Qin, Yong Su, Jian Chen, Lan-jun Liu
- Publication Year: 2019
- Publishing Journal/Academic Society: CHINA FOUNDRY
- Keywords: aluminum alloy; die casting process; simulation optimization
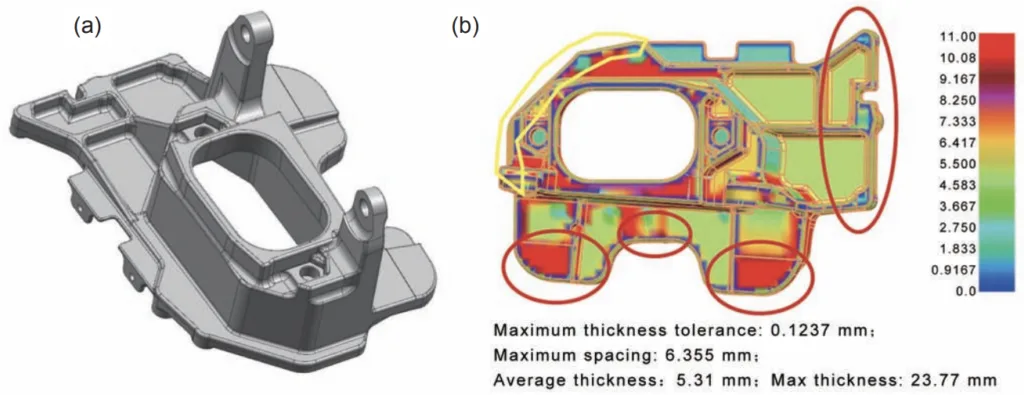
2. Research Background:
Background of the Research Topic:
Aluminum alloy die casting technology is a forming method characterized by filling the cavity with liquid metal at high velocity and solidifying under high pressure. Current research in this domain predominantly focuses on interfacial heat transfer, injection velocity, and die casting temperature.
Status of Existing Research:
Prior investigations have established foundational knowledge concerning critical aspects of die casting. Paliani [1] developed an inverse model through experimental means, determining the heat transfer coefficient between liquid metal and the injection chamber to be approximately 1.2 kW·m⁻²·K⁻¹. El-Mahallawy et al. [2] highlighted the inverse relationship between casting density and gate velocity. Pitsaris et al. [3] emphasized the significant influence of die casting temperature on the mechanical properties of die castings, noting that increased temperature reduces pre-crystallization and enhances mechanical properties. Syrcros [4] identified injection velocity, casting temperature, filling time, and pressure as primary factors affecting die casting quality.
Necessity of the Research:
The advent of computer technology has facilitated the visualization of high pressure die casting (HPDC) processes. This research leverages ProCAST finite element analysis software to visualize die-casting process parameters within the HPDC process, aiming to elucidate the rules of die casting for shell parts through the study of a representative shell part.
3. Research Purpose and Research Questions:
Research Purpose:
The primary research purpose is to reveal the rules governing die casting for shell parts. This is achieved through a detailed study of the die casting process of a single representative shell part, utilizing ProCAST finite element analysis software to visualize and analyze the process.
Key Research:
This study focuses on four key die casting process parameters:
- Injection temperature
- Low-pressure velocity
- Switching position of low- and high-pressure velocity
- High-pressure velocity
Research Hypotheses:
The research implicitly hypothesizes that through systematic simulation and optimization of the aforementioned die casting parameters, it is possible to mitigate defects such as pre-crystallization and air entrapment, thereby enhancing the quality of HPDC components.
4. Research Methodology
Research Design:
The research employs a simulation-based design utilizing ProCAST software to visualize and optimize the die casting process. This is complemented by experimental verification conducted on an YZM-800T die casting machine to validate the simulation findings.
Data Collection Method:
Data is collected through:
- ProCAST software simulations, generating data on fluid flow, temperature distribution, and solidification patterns under varying process parameters.
- Experimental trials on the YZM-800T die casting machine to produce physical castings under specific parameter sets.
- X-ray inspection of the produced castings to assess internal quality and detect defects such as shrinkage.
Analysis Method:
The analysis is performed using finite element analysis within ProCAST to simulate and visualize the HPDC process. The simulation results are then compared with experimental outcomes and X-ray inspection data to validate the optimized parameters.
Research Subjects and Scope:
The research focuses on shell die casting, specifically utilizing ADC12 aluminum alloy. The scope is limited to optimizing the injection parameters within the HPDC process for a single representative shell part geometry. The material of the casting is ADC12 aluminium alloy and the shape of the casting is shown in Fig. 1(a).
5. Main Research Results:
Key Research Results:
The study yielded several key findings regarding the influence of die casting parameters:
- Injection Temperature and Low-Pressure Velocity: Higher injection temperatures and low-pressure velocities were found to mitigate pre-crystallization within the injection chamber.
- Low-Pressure Velocity Limit: Exceeding a low-pressure velocity of 0.2 m·s⁻¹ leads to air entrapment within the chamber.
- High-Pressure Velocity Limit: When high-pressure velocity surpasses 2.5 m·s⁻¹, the overflow channel at the final filling position is prematurely covered by liquid metal.
- Optimal Parameters: Through simulation, the optimal parameters were determined as:
- Injection temperature: 650 °C
- Low-pressure velocity: 0.2 m·s⁻¹
- Switching position of low- and high-pressure velocity: 320 mm
- High-pressure velocity: 2 m·s⁻¹
Data Interpretation:
Simulation results, visualized in figures such as Fig. 4 and Fig. 5, demonstrated the effects of varying low-pressure velocities and injection temperatures on pre-crystallization and air entrapment. Fig. 4 illustrates that at a low-pressure velocity of 0.1 m·s⁻¹, pre-crystallization occurs in the chamber, while at 0.3 m·s⁻¹, serious air entrapment is observed. Fig. 5 shows that increasing die casting temperature reduces the pre-crystallization area. Fig. 7 further clarifies the impact of high-pressure velocities on the filling process and overflow channel blockage.
Figure Name List:
- Fig. 1: (a) Three-dimensional casting model; (b) Wall thickness distribution of casting
- Fig. 2: Schematic diagram of pouring scheme
- Fig. 3: Schematic diagram of geometric model
- Fig. 4: Filling diagram for different low-pressure velocities: (a) 0.1 m·s⁻¹, (b) 0.2 m·s⁻¹, (c) 0.3 m·s⁻¹
- Fig. 5: Pre-crystallization diagram of different injection temperatures: (a) 640 °C, (b) 650 °C, (c) 660 °C
- Fig. 6: Filling diagram of different switching positions: (a) 300 mm, (b)320 mm, (c) 340 mm
- Fig. 7: Filling diagram for different high-pressure velocities: (a1) 2 m·s⁻¹, 70% filling; (a2) 2 m·s⁻¹, 80% filling; (a3) 2 m·s⁻¹, 90% filling; (b1) 2.5 m·s⁻¹, 70% filling; (b2) 2.5 m·s⁻¹, 80% filling; (b3) 2.5 m·s⁻¹, 90% filling; (c1) 3 m·s⁻¹, 70% filling; (c2) 3 m·s⁻¹, 80% filling; (c3) 3 m·s⁻¹, 90% filling
- Fig. 8: Side view (a) and front view (b) of X-ray detection of casting
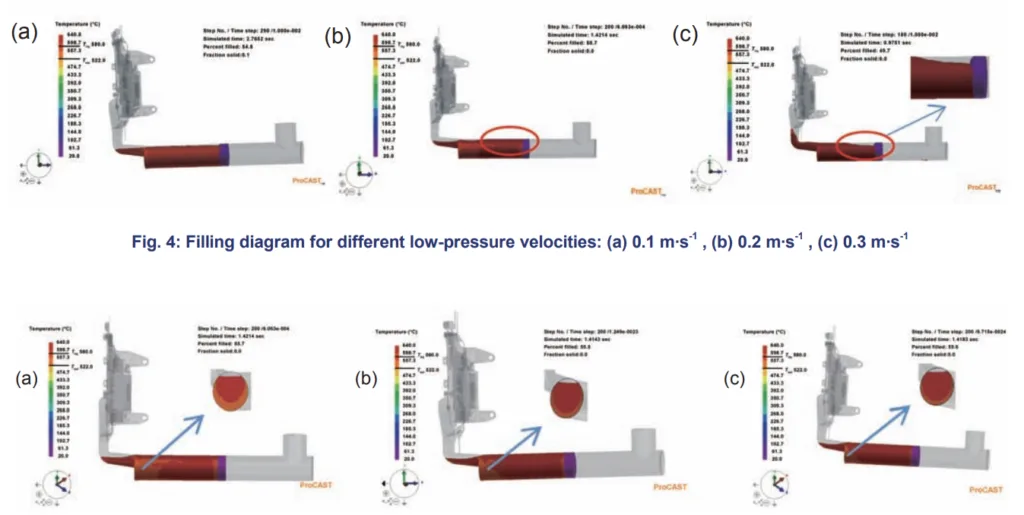

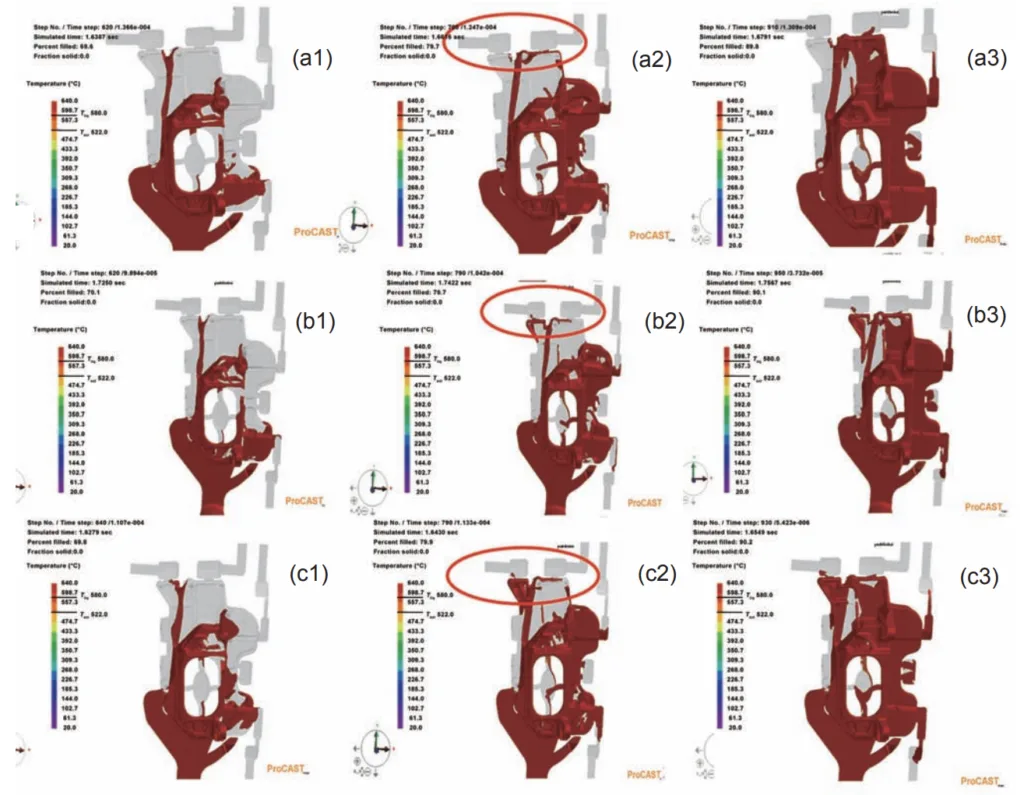
6. Conclusion:
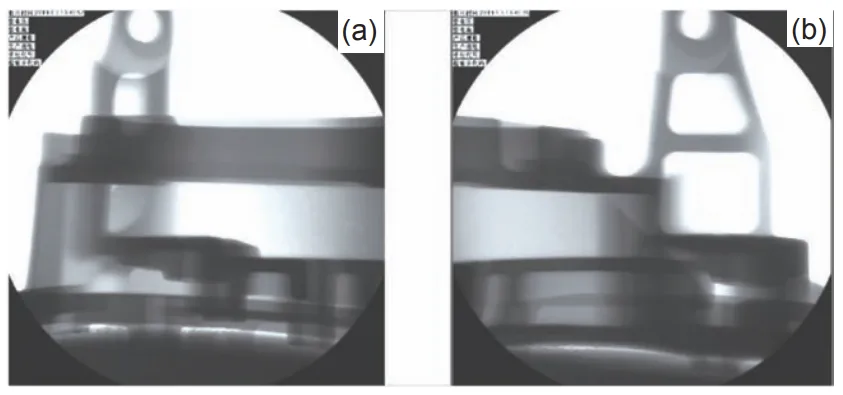
Summary of Main Results:
This research successfully designed a gating and overflow system based on casting structure analysis and wall thickness considerations. The study identified optimal die casting parameters for HPDC of ADC12 aluminum alloy shell parts through ProCAST simulations and experimental validation. The optimal parameters—injection temperature of 650 °C, low-pressure velocity of 0.2 m·s⁻¹, switching position of 320 mm, and high-pressure velocity of 2 m·s⁻¹—effectively minimize pre-crystallization and air entrapment, enhancing casting quality.
Academic Significance of the Research:
This study demonstrates the effective application of finite element analysis, specifically ProCAST software, in optimizing die casting process parameters. It provides valuable insights into the complex interplay between injection parameters and casting defects in HPDC, contributing to the theoretical understanding of the process.
Practical Implications:
The determined optimal parameters offer direct practical benefits for the die casting industry. Implementation of these parameters for ADC12 aluminum alloy shell part production can lead to improved casting quality, reduced defect rates, and enhanced production efficiency. The design of the gating system and overflow system, as shown in Fig. 2, provides a blueprint for similar applications.
Limitations of the Research
The research is primarily focused on a single representative shell part geometry and ADC12 aluminum alloy. The general applicability of the optimized parameters to diverse casting geometries, alloy systems, and die casting machine types requires further investigation.
7. Future Follow-up Research:
- Directions for Follow-up Research
Future research should extend the investigation to:- Explore the applicability of the optimized parameters to a broader range of casting geometries and complexities.
- Investigate different aluminum alloys and other die casting materials to broaden the scope of the findings.
- Examine the influence of additional process parameters, such as die temperature and cooling rates, on casting quality.
- Develop more refined simulation models to enhance predictive accuracy and incorporate additional defect mechanisms.
- Areas Requiring Further Exploration
Further exploration is needed in:- Optimizing gating and overflow systems for complex geometries using CAE tools.
- Investigating real-time control systems to dynamically adjust process parameters based on simulation feedback.
- Studying the long-term performance and reliability of castings produced using simulation-optimized parameters.
8. References:
- [1] Paliani P. Thermoelastic Deformation of Cold Chamber Die Casting Machine Shot Sleeves [MS Thesis]. US: Ohio State University, 1993.
- [2] El-Mahallawy AN, Taha M A, Pokora E, et al. On the influence of process variables on the thermal conditions and properties of high pressure die-cast magnesium alloys. Journal of Materials Processing Technology, 1997, 73(1): 125-138.
- [3] Pitsaris C, Abbott T, Davies C, et al. Influence of Process Parameters on the Microstructure and Mechanical Properties of Magnesium Die Castings. In: Magnesium: Proceedings Applications of the 6th International Conference Magnesium Alloys and Their Applications, 2005.
- [4] Syrcos G P. Die casting process optimization using Taguchi methods. Journal of Materials Processing Technology, 2003, 135(1): 68-74.
- [5] Kwon H J, Kwon H K. Computer aided engineering (CAE) simulation for the design optimization of gate system on high pressure die casting (HPDC) process. Robotics and Computer-Integrated Manufacturing, 2018, 55: 147-153.
- [6] Kwon H K, Seo K K. Simulation Study on HPDC Process for Automobile Part with Aluminum Alloy. Materials Science Forum, 2013, 761: 4.
- [7] Duan H Z, Shen J N, Li Y P. Comparative Analysis of HPDC Process of an Auto Part with ProCAST and FLOW-3D. Applied Mechanics and Materials, 2012, 184-185: 90-94.
- [8] Rai JK, Lajimi A M, Xirouchakis P. An intelligent system for predicting HPDC process variables in interactive environment. Journal of Materials Processing Technology, 2008, 203(1-3): 72-79.
- [9] Kwon H J, Kwon H K. Computer aided engineering (CAE) simulation for the design optimization of gate system on high pressure die casting (HPDC) process. Robotics and Computer-Integrated Manufacturing, 2019, 55: 147-153.
9. Copyright:
- This material is "Yong Su"'s paper: Based on "Finite element analysis for die casting parameters in high-pressure die casting process".
- Paper Source: https://doi.org/10.1007/s41230-019-8088-8
This material was summarized based on the above paper, and unauthorized use for commercial purposes is prohibited.
Copyright © 2025 CASTMAN. All rights reserved.