This introduction paper is based on the paper "Analysis and Optimisation of High Pressure Die Casting Parameters to Achieve Six Sigma Quality Product Using Numerical Simulation Approach" published by "International Journal of Engineering and Management Research".
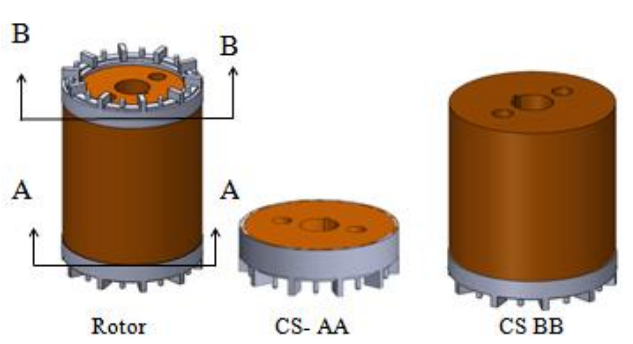
1. Overview:
- Title: Analysis and Optimisation of High Pressure Die Casting Parameters to Achieve Six Sigma Quality Product Using Numerical Simulation Approach
- Author: Suraj R. Marathe¹ and Dr. Carmo E. Quadros² (¹Research Scholar, Mechanical Department, ASSAM DON BOSCO University, INDIA; ²Professor, Mechanical Department, ASSAM DON BOSCO University, INDIA)
- Year of publication: 2021 (February)
- Journal/academic society of publication: International Journal of Engineering and Management Research
- Keywords: High Pressure Die Casting (HPDC), Parameters, ProCAST, Simulation, Six Sigma Quality
2. Abstract:
A numerical simulation approach is proposed to predict the optimal parameter setting during high pressure die casting. The contribution from the optimal parameters, the temperature, showed more influence on the casting quality than the other parameters. This study's outcome was beneficial for finding the solution for casting defects that occurs due to incorrect setting of process parameters in die casting. Thus, a combination of numerical optimisation techniques and casting simulation serves as a tool to improve the casting product quality in die casting industries. This paper aims to analyse and optimise critical parameters like injection pressure, molten metal temperature, holding time, and plunger velocity, contributing to the defects. In this research paper, an effort has been made to give optimal pressure, temperature, holding time, and plunger velocity parameters using ProCAST simulation software that uses finite element analysis technology. Numerical analysis for optimising the parameters by varying the temperature of molten metal, injection pressure, holding time, and plunger velocity, concerning solidification time at hot spots, is an essential parameter for studying the defect analysis in the simulated model.
3. Introduction:
Die casting processes often suffer from poor quality and productivity, with rejection levels reported between 11 to 13 per cent due to defects like blowholes, insufficient injection pressure, improper filling time, porosities, and hot spots. Controlling process parameters is crucial for achieving zero-defect parts, requiring an understanding of how these parameters influence casting defects. This study investigates the die casting of a rotor component, analysing the process parameters' effects using numerical simulation, focusing on the component and two cross-sections (molten entry and bottom section) as shown in Figure 1.
4. Summary of the study:
Background of the research topic:
High Pressure Die Casting (HPDC) processes are susceptible to quality issues and low productivity due to variations in process parameters. These variations can lead to casting defects such as blowholes, porosity, improper filling, and hot spots, resulting in significant rejection rates (11-13%).
Status of previous research:
Previous work, such as Mohanty and Jena (2014), highlighted the necessity of controlling process parameters to achieve zero-defect parts and noted the high rejection levels in the industry. The primary reasons identified for rejection include defects directly linked to incorrect parameter settings.
Purpose of the study:
The study aims to analyse and optimise critical HPDC parameters – specifically injection pressure, molten metal temperature, holding time, and plunger velocity – using a numerical simulation approach. The goal is to determine the optimal parameter settings that minimize solidification time, thereby reducing casting defects and improving product quality towards a Six Sigma level.
Core study:
The core of the study involves using ProCAST simulation software, which employs finite element analysis (FEA), to model the HPDC process for a rotor component. A systematic numerical optimization technique is applied, varying the four key parameters (Temperature, Pressure, Velocity, Holding Time) over defined ranges (Table 2). The study analyses the impact of these variations on the solidification time at hot spots for the rotor and specific cross-sections (CS AA and CS BB, Figure 1). The objective is to identify the parameter combination that yields the minimum solidification time, considered essential for defect analysis and quality improvement.
5. Research Methodology
Research Design:
The research employs a numerical simulation and optimization methodology. The HPDC process for a rotor component was simulated using ProCAST software based on the Finite Element Method (FEM). A multi-stage optimization approach (Figure 5, Figure 6) was used, where each of the four key parameters (Temperature, Pressure, Velocity, Holding Time) was analysed sequentially across 25 levels within a defined range (Table 2, Figure 4) to minimize solidification time.
Data Collection and Analysis Methods:
- Modeling: A 3D geometrical model of the rotor casting, gating system, and mould was created using Unigraphics NX4.0 and converted to *.x_t files.
- Meshing: Finite element meshes were generated using the MeshCAST module of ProCAST (Figure 7).
- Simulation: ProCAST software was used to simulate the HPDC process. Initial boundary conditions and process parameters (Table 2) were defined in the pre-processor. A total of 7800 simulation experiments were planned (Figure 4).
- Analysis: Simulation results (e.g., solidification time, fraction solid, shrinkage porosity, hotspots, temperature at filling time, gas misruns sensitivity, injection pressure) were analysed using the Visual-Viewer (Cast) post-processor. The primary analysis focused on minimizing solidification time for the rotor component and cross-sections AA and BB at each optimization stage (Figures 8-15). Optimal parameters were determined based on these results (Tables 3-10). Industrial data from Crompton Greaves Ltd (CGL) provided context for the heat cycle (Figure 2, Table 1) and experimental setup (Figure 3).
Research Topics and Scope:
The research focuses on the High Pressure Die Casting (HPDC) of an aluminium alloy rotor component (outer radius 100 mm, inner radius 25 mm, height 135 mm). The scope includes the numerical simulation and optimization of four critical process parameters:
- Molten Metal Temperature (T): 680 °C to 752 °C
- Injection Pressure (P): 300 bar to 348 bar
- Plunger Velocity (V): 116.6 m/s to 121.4 m/s
- Holding Time (HT): 52 s to 76 s
The objective is to minimize solidification time as a means to reduce casting defects and achieve Six Sigma quality.
6. Key Results:
Key Results:
- The numerical simulation approach using ProCAST successfully identified optimal process parameter settings for minimizing solidification time in the HPDC rotor component.
- Temperature was found to have a more significant influence on casting quality compared to the other parameters studied (Pressure, Velocity, Holding Time).
- The multi-stage optimization process yielded the following optimal parameter ranges (Table 11):
- Temperature (T): 728 ≤ T ≤ 731 °C
- Pressure (P): 330 ≤ P ≤ 332 bar
- Velocity (V): 119.6 ≤ V ≤ 120 m/s
- Holding Time (HT): 67 ≤ HT ≤ 69 s (Note: Table 11 states 65 ≤ HT ≤ 69, but stage results tables 3, 6, 8, 10 show optimal times at 67, 69, 69, 68 respectively. The final conclusion mentions 67s. Using the range from Table 11 for consistency with that summary table).
- Mean optimal settings identified were: T = 730 °C, P = 331 bar, V = 119.8 m/s, HT = 67 s.
- Confirmation experiments conducted with these optimal parameters reportedly reduced the rejection rate of motors due to rotor contribution from 4.35% to 0.89% (data from CGL).
- ProCAST simulations performed using the optimal settings showed no significant defects regarding filling time, total shrinkage porosity, and misrun sensitivity (Figure 16).
- Figure 3: Experimentation setup: vertical die casting machine of the capacity of 100 Tons (Industrial caseCGL)
- Figure 4: The proposed experimentation set up for solving flow for optimisation of parameters
- Figure 5: Block diagram showing four stages of numerical simulation for the optimisation of solidification time
- Figure 6: Flow diagram showing the final stage of a numerical simulation approach
- Figure 7: Meshed and position of cross-sections of the rotor component
- Figure 8: Graphical representation of temperature analysis of the rotor and at cross-sections AA and BB
- Figure 14: Graphical representation of holding time at various sections
- Figure 15: (a, b, and c) Simulation output for solidification time at rotor component, Cross-Section AA and BB.
Figure Name List:
- Figure 1: Die casting rotor component and cs at AA and BB for numerical analysis
- Figure 2: Die casting heat process cycle represented on a timeline in seconds (Industrial case-CGL)
- Figure 3: Experimentation setup: vertical die casting machine of the capacity of 100 Tons (Industrial case-CGL)
- Figure 4: The proposed experimentation set up for solving flow for optimisation of parameters
- Figure 5: Block diagram showing four stages of numerical simulation for the optimisation of solidification time
- Figure 6: Flow diagram showing the final stage of a numerical simulation approach
- Figure 7: Meshed and position of cross-sections of the rotor component
- Figure 8: Graphical representation of temperature analysis of the rotor and at cross-sections AA and BB
- Figure 9: (a, b, and c) Simulation output for solidification time at rotor component, Cross-Section AA and BB.
- Figure 10: Graphical representation of pressure analysis at various sections
- Figure 11: (a, b, and c). Simulation output for solidification time at rotor component, Cross-Section AA, and BB.
- Figure 12: Graphical representation of plunger velocity analysis at various sections
- Figure 13: (a, b, and c) Simulation output for solidification time at rotor component, Cross-Section AA and BB.
- Figure 14: Graphical representation of holding time at various sections
- Figure 15: (a, b, and c) Simulation output for solidification time at rotor component, Cross-Section AA and BB.
- Figure 16: (a, b, c,) ProCAST simulated results for filling time, total shrinkage porosity and misrun sensitivity
7. Conclusion:
The numerical simulation algorithm effectively optimised the HPDC process parameters by minimizing solidification time. Lower solidification time is generally associated with reduced internal defects like blowholes and porosity. The study involved 7800 simulation experiments to analyse the effect of die casting parameters. The identified optimal parameters (pouring temperature 730 °C, pressure 331 bar, plunger velocity 119.8 m/s, holding time 67 s) were validated through confirmation experiments, which showed a significant reduction in motor rejection rates due to rotor defects (from 4.35% to 0.89%, data from CGL). ProCAST simulations at these optimal settings confirmed minimal defects (filling time, shrinkage porosity, misrun). Temperature showed the most significant influence on casting quality. The combination of numerical optimisation techniques and casting simulation serves as a valuable tool for improving casting product quality in die casting industries, providing a decision tool for setting optimum parameters towards Six Sigma quality.
8. References:
- [1] Domkin, K., Hattel, J., & Thorborg, J. (2009). Modelling of high temperature and diffusion controlled die soldering in high aluminium pressure die casting. Journal of Material Processing Technology, 209(8), 4051-4061.
- [2] Fiorese, E., Richiedei, D., & Bonollo, F. (2016). Improving the quality of die castings through optimal plunger motion planning: analytical computation and experimental validation. International Journal of Advanced Manufacturing Technology, 88, 1475–1484.
- [3] Fu, J. & Wang, K. (2014) Modelling and simulation of the die casting process for A356 semi-solid alloy. Procedia Engineering, 81, 1565–1570.
- [4] Jorstad, J. & Apelian, D. (2009). Pressure assisted processes for high integrity aluminium castings - part 1. International Journal of Metal Casting, 250-254.
- [5] Kumar, S., Gupta, A., & Chandna, P. (2012). Optimisation of process parameters of pressure die casting using taguchi methodology. World Academy of Science, Engineering and Technology, 6, 590-594.
- [6] Lattanzi, L., Fabrizi, A., Fortini, A., Merlin, M., & Timelli, G. (2017). Effects of microstructure and casting defects on the fatigue behaviour of the high-pressure die-cast AlSi9Cu3 (Fe) alloy. Procedia Structural Integrity, 7, 505-512.
- [7] Mohanty, C. & Jena, B. (2014). Optimisation of aluminium die casting process using artificial neural network. International Journal of Emerging Technology and Advanced Engineering, 4(7), 146-149.
- [8] Syrcos, G. (2002). Die casting process optimisation using taguchi methods. Journal of Material Processing Technology, 135, 68-74.
- [9] Wang, L., Turnley, P., & Savage, G. (2011) Gas content in high pressure die castings. Journal of Materials Processing Technology, 211, 1510–1515.
- [10] Zhang, M., Xing, S., Xiao, L., Bao, P., Liu, W., & Xin, Q. (2008). Design of process parameters for direct squeeze casting. Journal of University of Science and Technology, 15(3), 339-343.
- [11] Zhang, X., Xiong, S., & Xu, Q. (2006). Numerical methods to improve the computational efficiency of solidification simulation for the investment casting process. Journal of Materials Processing Technology, 173, 70-74.
9. Copyright:
- This material is a paper by "Suraj R. Marathe and Dr. Carmo E. Quadros". Based on "Analysis and Optimisation of High Pressure Die Casting Parameters to Achieve Six Sigma Quality Product Using Numerical Simulation Approach".
- Source of the paper: https://doi.org/10.31033/ijemr.11.1.15
This material is summarized based on the above paper, and unauthorized use for commercial purposes is prohibited.
Copyright © 2025 CASTMAN. All rights reserved.