This article introduces the paper "Advanced metals for aerospace and automotive use" presented at the Materials Science and Engineering, A184 (1994) 119-133
1. Overview:
- Title: Advanced metals for aerospace and automotive use
- Author: F. H. Froes
- Publication Year: 1994
- Publishing Journal/Academic Society: Materials Science and Engineering, A
- Keywords: aerospace systems, automobiles, improved performance, enhanced characteristics, synthesis/processing, microstructure-property relationships, strength, temperature capability, ductility, forgiveness, density, cost, light metals, aluminum, magnesium, titanium, titanium aluminides, advanced materials, ingot metallurgy, castings, rapid solidification, mechanical alloying, nanostructured materials, spray deposition, vapor deposition, thermochemical processing, metal matrix composites, fusion joining.
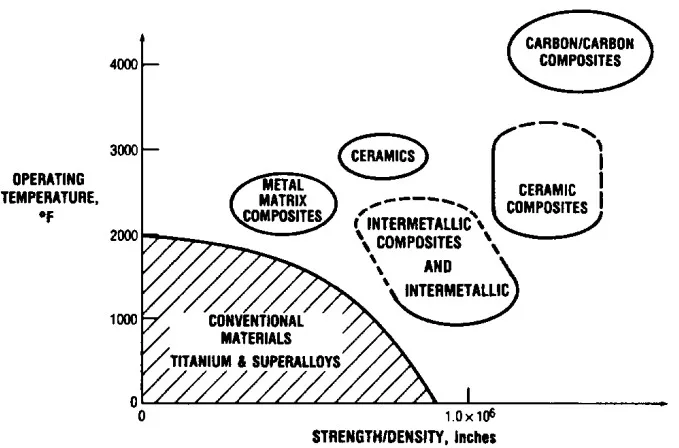
2. Research Background:
The pursuit of enhanced performance in aerospace systems and automobiles necessitates materials exhibiting superior characteristics compared to conventional materials. This is particularly critical for automotive powertrains. Historically, advancements in material properties were sought through refining the understanding of microstructure-property relationships. However, recent progress emphasizes the significance of improved synthesis and processing methodologies as the primary drivers for enhancing material performance. The objective is to achieve an "enhanced trend band" (Fig. 1), maximizing properties like strength, ductility, temperature capability, and "forgiveness" (fracture toughness, fatigue crack growth rate), while minimizing density and cost. Weight reduction is a critical factor, with its value varying across industries (Table 1), and density reduction being the most effective approach to weight saving (Fig. 2). Light metals, specifically aluminum, magnesium, titanium, and titanium aluminides, are particularly attractive due to their low density for both aerospace and automotive applications.
3. Research Purpose and Research Questions:
- Research Purpose: To discuss advanced materials in general and specifically for aerospace and automobile applications, and to present various synthesis and processing methods for lightweight metals aimed at achieving enhanced physical and mechanical properties.
- Key Research Questions:
- What are the limitations of conventional microstructure-property relationship approaches in achieving enhanced material performance?
- How can advanced synthesis and processing techniques contribute to improved material characteristics for aerospace and automotive applications?
- What are the specific advanced materials and processing methods suitable for lightweight metals like aluminum, magnesium, titanium, and titanium aluminides to enhance their properties?
- What are the challenges and opportunities associated with implementing these advanced materials and processes in aerospace and automotive industries?
- Research Hypotheses: (While not explicitly stated as hypotheses in a traditional format, the paper implicitly operates under the premise that) Advanced synthesis and processing methods offer a more effective route to enhance material properties for demanding applications compared to solely focusing on microstructure control within conventional processing routes. Lightweight metals, processed using advanced techniques, can meet the stringent performance requirements of aerospace and automotive industries while addressing weight and cost concerns.
4. Research Methodology
- Research Design: This paper employs a descriptive review design, surveying and summarizing the state-of-the-art in advanced materials and processing techniques relevant to aerospace and automotive applications. It synthesizes information from existing literature and examples of material applications to illustrate advancements in the field.
- Data Collection Method: The paper relies on a review of existing research, technical literature, and industry examples. Data is collected from published articles, reports, and industry data (e.g., Boeing Company data for weight savings, NASA Lewis data for temperature capability). Figures and tables from various sources are incorporated to support the discussion.
- Analysis Method: The analysis is primarily qualitative, involving a descriptive synthesis of information on various advanced materials and processing methods. The paper compares and contrasts different techniques like ingot metallurgy, rapid solidification, mechanical alloying, etc., in terms of their capabilities and applications. Quantitative data, where presented (e.g., property values, weight savings), is directly quoted from the referenced sources to illustrate the benefits of advanced materials and processes.
- Research Subjects and Scope: The scope of the paper encompasses advanced metallic materials, particularly lightweight alloys based on aluminum, magnesium, titanium, and titanium aluminides. The focus is on synthesis and processing techniques including: ingot metallurgy and castings, rapid solidification, mechanical alloying, nanostructured materials, spray deposition, vapor deposition, thermochemical processing, metal matrix composites, and fusion joining. The applications are primarily within the aerospace and automotive industries.
5. Main Research Results:
- Key Research Results:
- Advanced synthesis and processing methods are crucial for achieving enhanced material properties beyond conventional microstructure control.
- Lightweight metals (Al, Mg, Ti, Ti-aluminides) are vital for aerospace and automotive applications due to density advantages.
- Various advanced processing techniques (RS, MA, Nanomaterials, Spray Deposition, Vapor Deposition, TCP, MMC) offer specific advantages in enhancing properties like strength, temperature capability, wear resistance, and corrosion resistance.
- Ingot metallurgy (IM) and casting are conventional but improving with HIP and innovative processing for enhanced properties.
- Rapid solidification (RS) extends alloying limits and refines microstructure, improving properties in Al alloys and Ti aluminides.
- Mechanical alloying (MA) enables solubility extension, novel phase formation, and fine grain structures, beneficial for Al, Mg, and Ti alloys and aluminides.
- Nanostructured materials produced via MA and plasma processing show superior properties.
- Spray deposition allows direct preform production and is suitable for metal matrix composites.
- Vapor deposition offers microstructural control and unique alloy production (e.g., Ti-Mg).
- Thermochemical processing (TCP) improves processability and properties of Ti alloys.
- Metal matrix composites (MMCs) enhance stiffness, strength, and creep resistance in Al and Mg matrices.
- Fusion joining techniques like EB welding are adapted to maintain or recreate the microstructure of advanced materials.
- Statistical/Qualitative Analysis Results: The paper primarily presents qualitative comparisons and descriptions. Quantitative results are presented in figures and tables, directly sourced from other studies or industry data, illustrating the property improvements achieved by advanced materials and processes. For example:
- Table 1: Dollar value of weight savings varies by industry (Automobile: $3, Space: $30,000).
- Fig. 2: Shows the effect of property improvement on structural weight reduction.
- Fig. 5: Demonstrates the significant contribution of new materials to structural weight reduction in fighter aircraft compared to other technologies.
- Fig. 12: Illustrates weight savings achieved by replacing conventional disc-spacer assembly with titanium aluminide composite ring.
- Fig. 13: Shows US government-legislated fuel economy requirements.
- Fig. 27: Depicts enhanced fracture toughness in spray-deposited Al-7075 material compared to DC cast.
- Data Interpretation: The data presented consistently supports the central theme: advanced materials and processing techniques are essential for meeting increasing performance demands in aerospace and automotive sectors. Lightweight metals, when processed using these advanced methods, offer significant advantages in terms of performance enhancement and weight reduction.
- Figure Name List:
- Fig. 1. Trend bands exhibited by basic materials and enhanced trend band characteristic of engineered materials.
- Fig. 2. Effect of property improvement on structural weight (courtesy Lockheed).
- Fig. 3. Temperature capability of various material classes (courtesy NASA Lewis).
- Fig. 4. Combat envelope for future fighter aircraft.
- Fig. 5. Trends in structural weight reduction for fighter aircraft, showing the significance of new and improved materials.
- Fig. 6. Variation of airframe construction price with type of aircraft.
- Fig. 7. Large titanium engine part casting, densified by HIP (courtesy Precision Castparts Corporation).
- Fig. 8. Forged RS aluminum alloy landing gear wheel (courtesy Allied Signal).
- Fig. 9. Flap track cap produced from MA aluminum alloy (courtesy INCOmap).
- Fig. 10. Vane produced from Ti-48 at.% Al using a PM/isothermal forging approach (courtesy VILS).
- Fig. 11. GE T700 engine compressor produced from cast TiAl.
- Fig. 12. Weight savings achieved by replacing a conventional disc-and-spacer assembly with a titanium aluminide composite ring.
- Fig. 13. US government-legislated fuel economy requirements.
- Fig. 14. Hypothetical relationship between valve component cost and the extent of engine applications.
- Fig. 15. Major reciprocating and rotating mass components in the piston assembly which affect fuel economy and emissions.
- Fig. 16. TiAl piston head hot isostatically pressed from PREP powder (courtesy VILS).
- Fig. 17. Blended elemental PM titanium connector rod.
- Fig. 18. Engine horsepower output as a function of speed for valves of varying mass.
- Fig. 19. Upper-wing skin plate alloy/temper chronology.
- Fig. 20. Electron-beam (left) and plasma (right) cold-hearth furnaces.
- Fig. 21. Elevated-temperature strength and creep properties of titanium alloys.
- Fig. 22. (a) Wear resistance of aluminum materials. (b) Schematic of wear test apparatus.
- Fig. 23. Schematic of the mechanical alloying process.
- Fig. 24. Comparison of the microstructure of Ti3Al+2Er powder compacts: (a) RS, hot isostatically pressed at 850 °C; (b) MA, hot isostatically pressed at 1000 °C.
- Fig. 25. Schematic of equiaxed nanostructural material: dark circles are atoms within grains, white atoms are in grain boundaries (courtesy H. Gleiter).
- Fig. 26. Nanostructured grains in HIP'ed Ti-55at.%Al, produced from amorphous MA powder.
- Fig. 27. Enhanced fracture toughness in spray-deposited Al-7075 material.
- Fig. 28. Schematic of the factors influencing the toughness of discontinuously reinforced aluminum material.
- Fig. 29. Toughness-yield strength relationships for a variety of discontinuously reinforced aluminum materials, demonstrating the wide range of combinations obtained.
- Fig. 30. Microstructure of CermeTi material.
- Fig. 31. CermeTi material: (left) dual-hardness gear CermeTi/monolithic PM Ti-6Al-4V, and (right) seven-layer ballistic plate made up of alternate layers of CermeTi and monolithic PM Ti-6Al-4V (courtesy Dynamet).
- Fig. 32. Light (top) and SEM (bottom) micrographs of electron-beam welds in Al-8Fe-2Mo sheet.
- Fig. 33. Solid-state crack in electron-beam welded gamma titanium aluminide.
- Table 1. Dollar value of weight savingsª
- Table 2. Drivers for introduction of new materials/processes into automobiles
- Table 3. Typical properties of Ti3Al-type titanium aluminides
- Table 4. Microstructure and mechanical properties in Ti-46.5Al-2.5V-1Cr TiAl-type
- Table 5. Tensile properties of elevated temperature PM/RS aluminum alloys at 315 °C
- Table 6. Room-temperature mechanical properties of mechanically alloyed aluminum alloys
- Table 7. Typical longitudinal properties of extruded rod
- Table 8. Mechanical properties of reinforced ZK60A (Mg-5.5Zn-0.5Zr) extruded rodª
- Table 9. Mechanical properties of titanium metal-matrix composites
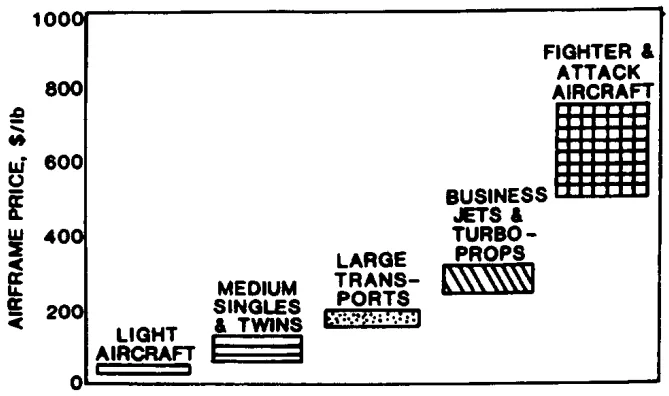
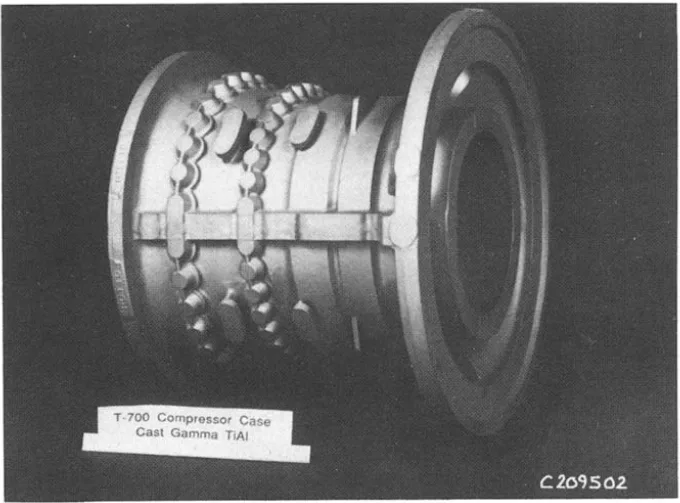
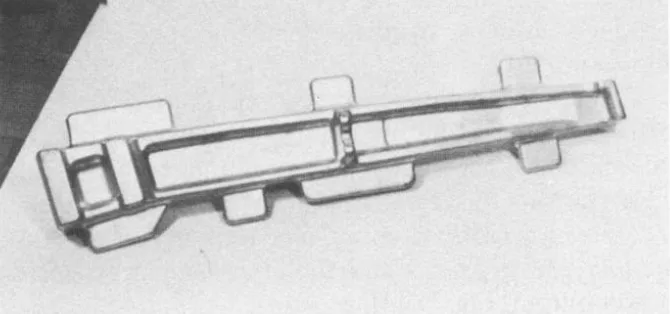

6. Conclusion and Discussion:
- Summary of Main Results: The paper concludes that achieving enhanced performance in aerospace and automotive systems relies heavily on the utilization of high-performance lightweight materials. The focus has shifted from solely understanding microstructure-property relationships to actively employing advanced synthesis and processing techniques. Lightweight materials based on aluminum, magnesium, titanium, and titanium aluminides, processed through methods like rapid solidification, mechanical alloying, spray deposition, vapor deposition, thermochemical processing, and metal matrix composite fabrication, demonstrate significantly improved physical and mechanical characteristics. These advancements address critical performance parameters such as strength, temperature capability, ductility, and "forgiveness" while minimizing density and cost.
- Academic Significance of the Research: This paper provides a comprehensive overview of the evolution of advanced metallic materials and processing techniques. It highlights the limitations of traditional approaches and emphasizes the critical role of innovative synthesis and processing in pushing the boundaries of material performance. The review serves as a valuable resource for researchers and engineers in materials science, aerospace, and automotive engineering, providing a broad understanding of the advanced materials landscape and future directions.
- Practical Implications: The advancements discussed have significant practical implications for both aerospace and automotive industries. The development and application of lightweight, high-performance materials directly translate to improved fuel efficiency, enhanced performance, and increased structural integrity in vehicles and aircraft. The paper underscores the importance of considering cost-effectiveness and manufacturability alongside performance when implementing these advanced materials in real-world applications. The examples of components fabricated using these techniques (Figs. 7-11, 16, 17, 31) demonstrate the tangible impact of these research areas.
- Limitations of the Research: As a review paper, the primary limitation is its reliance on existing published data. It does not present novel experimental data or in-depth analysis of specific mechanisms. The paper provides a broad overview, and further detailed research is needed in each specific area of advanced materials and processing to fully optimize their potential and address specific application requirements. The paper also acknowledges challenges like the low room-temperature ductility of titanium aluminides and the need for cost-effective manufacturing of nanostructured materials and metal matrix composites.
7. Future Follow-up Research:
- Directions for Follow-up Research:
- Further research is needed to optimize the processing parameters for each advanced synthesis technique to achieve consistent and reliable material properties at scale.
- Addressing the limitations of titanium aluminides, particularly low room-temperature ductility, is crucial for wider application.
- Cost reduction in the production of advanced materials, especially nanostructured materials and metal matrix composites, is essential for broader adoption, particularly in the automotive industry.
- Continued exploration of novel alloy compositions and processing methods for lightweight metals to further enhance their performance characteristics.
- Investigating the long-term performance and durability of components made from these advanced materials in real-world operating conditions.
- Areas Requiring Further Exploration:
- Deeper understanding of the fundamental mechanisms governing property enhancement in materials processed by RS, MA, vapor deposition, etc.
- Development of more efficient and scalable manufacturing processes for advanced materials.
- Addressing the challenges of joining dissimilar advanced materials and integrating them into existing structures.
- Exploring the recyclability and environmental impact of advanced materials throughout their lifecycle.
8. References:
- [1] F.H. Froes, P. Tsakiropoulos, C. Suryanarayana and W. Baeslack, in N.J. Kim (ed.), Light Materials for Transportation Systems, CAAM, Postech, Pohang, Korea, 1993, p. 27.
- [2] F.H. Froes, Mater. Design, 10(3) (1989) 186.
- [3] J.E. Allison and G.S. Cole, JOM, 45(1) (1993) 19.
- [4] W.F. Jandeska, Jr., in F.H. Froes (ed.), P/M in Aerospace, Defense and Demanding Applications - 1993, Metal Powder Industries Federation, Princeton, NJ, p. 45.
- [5] F.H. Froes and C. Suryanarayana, Titanium Aluminides, in V.K. Sikka and N. Stoloff (eds.), Physical Metallurgy and Processing of Intermetallic Compounds, Van Nostrand Reinhold, New York, NY, in press, 1994.
- [6] F.H. Froes, in F.H. Froes and R.A. Cull (eds.), Space Age Metals Technology, SAMPE, Covina, CA, 1988, p. 1.
- [7] F.H. Froes, Light Metal Age, 50(3-4) (1992) 66.
- [8] F.H. Froes, D. Eylon and H.B. Bomberger, Titanium Technology: Present Status and Future Trends, 1985, Titanium Development Association, Denver, CO.
- [9] F.H. Froes and W. Baeslack, in J.C. Danko and E.E. Nolting (eds.), Advanced Metals for Aerospace Component Fabrication, American Welding Society-High Energy Electron Beam Welding and Materials Processing Workshop, Boston, MA, Sept. 21-23, 1992, American Welding Society, Miami, FL, 1993, p. 219.
- [10] F.H. Froes and C. Suryanarayana, in A. Bose, R. German and A. Lawley (eds.), Powder Processing of Titanium Alloys, Book Series on Reviews in Particulate Materials, Metal Powder Industries Federation, Princeton, NJ, 1993, Vol. 1, p. 223.
- [11] J. Staley, Alcoa Research Center, Pittsburgh, PA, 1993
- [12] A. Mortenson, Fabrication of Particulate Reinforced Metal Composites, ASM Int., Materials Park, OH, 1990, p. 217.
9. Copyright:
- This material is "F. H. Froes"'s paper: Based on "Advanced metals for aerospace and automotive use".
- Paper Source: https://doi.org/10.1016/0921-5093(93)01104-H
This material was summarized based on the above paper, and unauthorized use for commercial purposes is prohibited.
Copyright © 2025 CASTMAN. All rights reserved.