This article introduces the paper "Development of a Housing Component for an Auto-compressor Using Vacuum Ladling Die Casting" presented at the Transactions of Materials Processing.
1. Overview:
- Title: Development of a Housing Component for an Auto-compressor Using Vacuum Ladling Die Casting
- Authors: H. S. Lee, J. S. Park (이항수, 박정식)
- Publication Year: 2012
- Publishing Journal/Academic Society: Transactions of Materials Processing, 한국소성가공학회지 (Journal of the Korean Society for Technology of Plastics)
- Keywords: Vacuum Ladling, Compressor Housing, High Vacuum, Die Casting, Aluminium
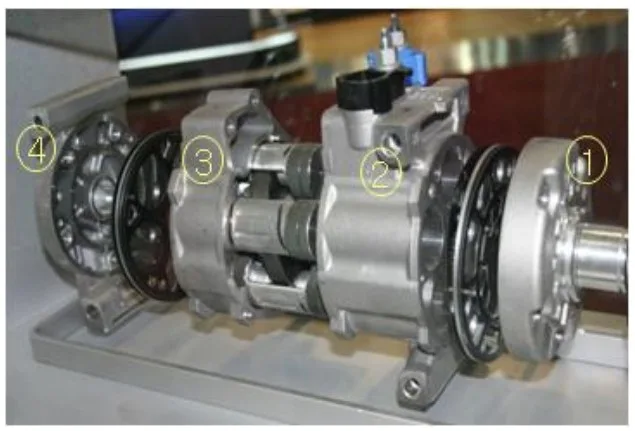
2. Research Background:
- Social/Academic Context of the Research Topic: The automotive industry demands high-performance components, particularly for air conditioning compressors. These components, often made of aluminum, require exceptional airtightness and pressure resistance to contain refrigerants under harsh operating conditions. Achieving low porosity in die-cast parts is crucial for these applications.
- Limitations of Existing Research: Conventional die casting methods often struggle to meet the stringent quality requirements for compressor housings due to inherent porosity issues. While vacuum die casting is employed, standard vacuum levels (around 50mbar or 37.5mmHg) may not be sufficient for these critical parts. Furthermore, ensuring consistent quality across multiple cavities in multi-cavity die casting presents challenges. There is a gap in research specifically focusing on vacuum ladling die casting for product development in this area.
- Necessity of the Research: This research addresses the need for a more advanced die casting method to produce high-quality, low-porosity automotive components. The study aims to develop and evaluate a high vacuum die casting system utilizing vacuum ladling to achieve significantly higher vacuum levels (below 35mbar or 26.25mmHg). The research also explores the use of multi-cavity molds to enhance production efficiency while maintaining part quality.
3. Research Purpose and Research Questions:
- Research Purpose: The primary goal of this research is to develop a vacuum ladling-based high vacuum die casting system and apply it to the manufacturing of automotive air conditioner compressor housings. A secondary purpose is to develop a multi-cavity mold to improve production rates for these components.
- Key Research Questions:
- Can a vacuum ladling system effectively achieve higher vacuum levels in die casting compared to conventional methods?
- Does the application of high vacuum ladling die casting reduce porosity and improve the overall quality of compressor housings?
- Is it feasible to utilize multi-cavity molds in conjunction with vacuum ladling die casting for efficient mass production of these parts?
- Research Hypotheses:
- Vacuum ladling die casting is capable of achieving higher vacuum levels than traditional vacuum die casting systems.
- Higher vacuum levels attained through vacuum ladling will lead to a significant reduction in internal porosity within die-cast compressor housings, thereby improving their quality.
- Multi-cavity molds can be successfully integrated with vacuum ladling die casting to enable efficient and high-quality mass production.
4. Research Methodology:
- Research Design: This study employs an experimental research approach, centered around the development and testing of a vacuum ladling die casting system. Computational flow analysis was used to optimize the casting design.
- Data Collection Method: The research team collected data through several methods:
- Vacuum Level Measurement: Vacuum levels were measured at three points within the system to assess vacuum performance.
- Density Test: Density measurements were conducted to quantify the porosity of the die-cast samples.
- X-ray Analysis: X-ray imaging was used to visually assess internal porosity and defect distribution.
- Leak Test: Leak tests were performed to evaluate the airtightness and pressure resistance of the compressor housings.
- Analysis Method:
- Statistical Analysis: Statistical methods were used to analyze density test results and porosity data, comparing samples produced with and without high vacuum ladling.
- Qualitative Analysis: X-ray images were analyzed qualitatively to assess the presence and nature of internal defects. Leak test results were evaluated to determine defect rates.
- Flow Analysis: Anycasting software was used to simulate the molten metal flow during the die casting process, both with and without vacuum, to understand the impact of vacuum on filling characteristics.
- Research Subjects and Scope: The research focused on developing an aluminum alloy rear-head housing for an automotive air conditioner compressor. A 6-cavity die casting mold was designed and utilized to produce sample parts using the developed vacuum ladling system.
5. Main Research Results:
- Key Research Results: The study successfully developed a vacuum ladling die casting system capable of achieving a high vacuum level of 17.8 mmHg. Flow analysis indicated that the filling speed during vacuum ladling is faster compared to non-vacuum systems. The research demonstrated a significant reduction in internal porosity, with the high vacuum ladling system reducing porosity by as much as 57.8% compared to non-vacuum die casting. Leak testing revealed a low defective rate of only 0.17% for parts produced using vacuum ladling.
- Statistical/Qualitative Analysis Results:
- Density Test: The average density of samples produced with high vacuum ladling was 2.64g/cm³, a notable improvement over the 2.55g/cm³ density of samples cast without vacuum.
- Air Content: Air content within the die-cast aluminum alloy was reduced from 2.32cc/100g in non-vacuum samples to 0.98cc/100g with high vacuum ladling, representing a 57.8% reduction.
- Air Hole Size: The average size of air holes was significantly reduced from 1.023mm in non-vacuum samples to 0.156mm with vacuum ladling.
- Leak Test (NG Ratio): The non-good (NG) ratio from leak tests decreased from 0.6% for parts produced without high vacuum to 0.17% with high vacuum ladling.
- Data Interpretation: The results clearly indicate that the high vacuum ladling system effectively reduces porosity and improves the quality of die-cast aluminum compressor housings. The enhanced density, reduced air content and air hole size, and lower defect rate from leak testing all point to the superior performance of the vacuum ladling die casting method.
- Figure Name List:
- Fig. 1 Components of a air-conditioning compressor
- Fig. 2 Analysis model of a rear head housing
- Fig. 3 Flow analysis of high vacuum die-casting
- Fig. 4 Analysis results of filling die cavity
- Fig. 5 Cavity view of flow analysis
- Fig. 6 Die-casting system with vacuum ladling
- Fig. 7 Experimental model of the sample product
- Fig. 8 Die-casting full shot of rear head housing
- Fig. 9 X-ray photos of rear head housing
- Fig. 10 Leak on the surface of rear head housing
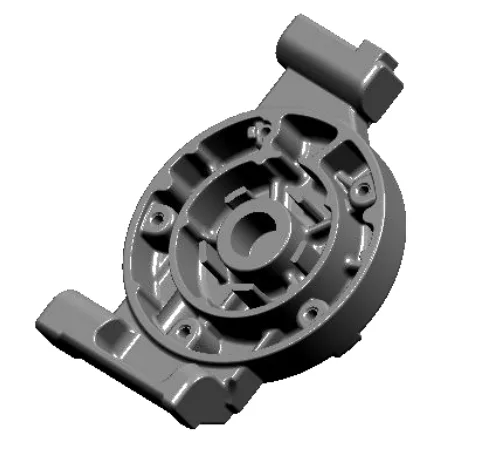
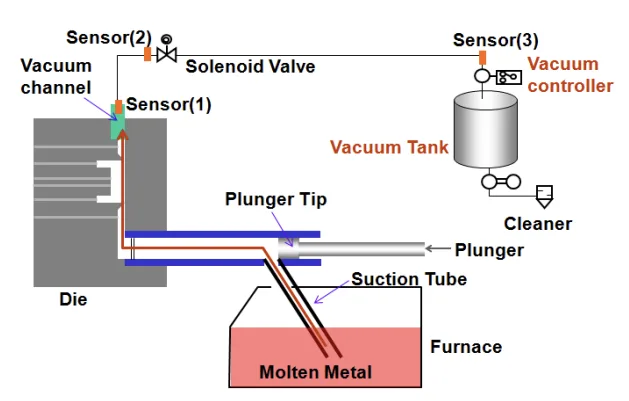
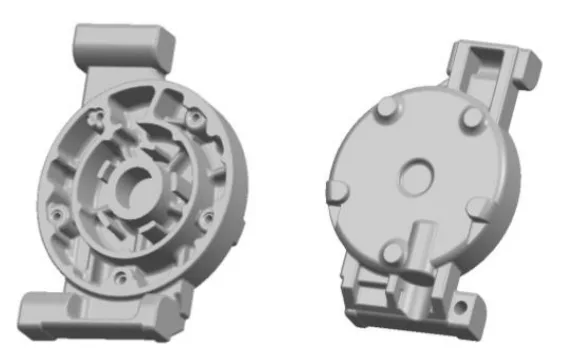
6. Conclusion and Discussion:
- Summary of Main Results: This research successfully developed and implemented a vacuum ladling die casting system that achieved a high vacuum level of 17.8 mmHg. The system was applied to the production of automotive compressor housings using a 6-cavity mold. The results demonstrated a significant reduction in porosity, a lower defect rate, and improved density and airtightness of the die-cast parts.
- Academic Significance of the Research: This study provides valuable empirical evidence for the effectiveness of vacuum ladling in achieving high vacuum levels in die casting. It quantifies the benefits of this approach in terms of porosity reduction and quality improvement for die-cast aluminum components.
- Practical Implications: The findings of this research have significant practical implications for the die casting industry, particularly for the manufacturing of high-performance aluminum components requiring high internal pressure resistance. Vacuum ladling die casting proves to be a useful process for producing such components, like automotive compressor housings. The successful implementation of multi-cavity molds further enhances the practical value by addressing the need for mass production.
- Limitations of the Research: While the paper demonstrates significant improvements, it primarily focuses on a specific aluminum alloy and compressor housing design. The generalizability of these findings to other aluminum alloys, part geometries, and die casting applications may require further investigation.
7. Future Follow-up Research:
- Directions for Follow-up Research: Future research could focus on optimizing the vacuum ladling process parameters for different alloys and part complexities. Further exploration into the long-term reliability and performance of components produced using this method would be beneficial.
- Areas Requiring Further Exploration: Areas for further exploration include a comprehensive cost-effectiveness analysis of vacuum ladling die casting for industrial implementation, and the application of this technology to a wider range of die-cast components and alloy systems.
8. References:
- [1] K. Y. Kim, 2007, New Diecasting Trend, J. Kor. Foundry Soc., Vol. 27, No. 7, pp. 81~90.
- [2] N. Nishi, 2005, New Development of Aluminium Diecating Technology, J. Jpn. Foundry Eng. Soc., Vol. 76, No. 4, pp. 226~271.
- [3] E. S. Kim, 2005, Die Casting Process Design for Gear Housing of Automobile Transmission by Using MAGMAsoft, Trans. Mater. Process., Vol. 14, No. 2, pp. 112~120.
- [4] D. Kim, I. H. Choo, Y. S. Lee, S. W. Kim, 2010, Internal Defect Minimization of Die Cast Impeller Blade Using Taguchi's Design of Experiment, Trans. Mater. Process., Vol. 19, No. 3, pp. 173~178.
- [5] J. H. Park, C. W. Jang, S. K. Kim, S. H. Han, Y. K. Seo, C. G. Kang, J. H. Lee, 2005, Proc. Kor. Soc. Tech. Plast. Spring Conf.(C. G. Kang), Kor. Soc. Tech. Plast., Seoul, Korea, pp. 415~418.
- [6] S. J. Kim, S. E. Park, I. H. So, 2005, Proc. Kor. Soc. Tech. Plast. Spring Conf.(C. G. Kang), Kor. Soc. Tech. Plast., Seoul, Korea, p. 344.
- [7] E, K, Jeon, J, Y, Park, E, M, Park, 2007, Application Trend of Aluminum castings in Automotive Component, J. Kor. Foundry Soc., Vol. 27, No. 21, pp. 20~23.
- [8] K. Takao, 2009, Die Casting Technology for Welding Application, J. Jpn. Foundry Eng. Soc., Vol. 81, No. 5, pp. 249~253.
- [9] B. Andresen, 2005, Diecasting Engineering, Marcel Dekker, New York, USA, pp. 33~42.
- [10] K, Y, Kim, S, M, Lee, 1995, Determination of Gas Content in Aluminium Alloy Melt, J. Kor. Foundry Soc., Vol. 14, No. 3, pp. 205~211.
9. Copyright:
- This material is H. S. Lee, J. S. Park's paper: Based on Development of a Housing Component for an Auto-compressor Using Vacuum Ladling Die Casting.
- Paper Source: http://dx.doi.org/10.5228/KSTP.2012.21.3.195
This material was summarized based on the above paper, and unauthorized use for commercial purposes is prohibited.
Copyright © 2025 CASTMAN. All rights reserved.