This article introduces the paper "Aluminium Foam and Magnesium Compound Casting Produced by High-Pressure Die Casting" presented in Metals, MDPI
1. Overview:
- Title: Aluminium Foam and Magnesium Compound Casting Produced by High-Pressure Die Casting
- Authors: Iban Vicario, Ignacio Crespo, Luis Maria Plaza, Patricia Caballero, and Ion Kepa Idoiaga
- Publication Year: 2016
- Publishing Journal: Metals, published by MDPI
- Keywords: high pressure die casting (HPDC); hybrid magnesium aluminium foam cast composite; aluminium foam core; magnesium cast composite
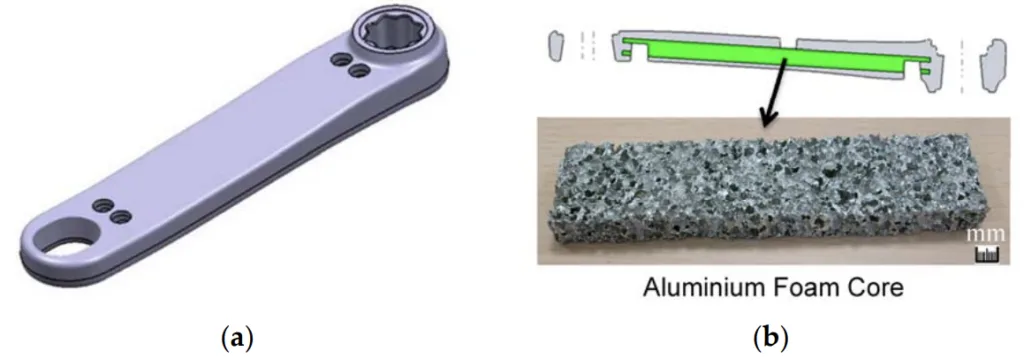
2. Research Background:
In the automotive and transport industries, reducing vehicle weight is a primary focus to decrease fuel consumption and carbon dioxide emissions. Substituting traditional heavier materials like steel and iron with lighter alternatives such as plastics, carbon fiber, aluminium, and magnesium alloys is a significant trend. This is particularly evident in the bicycle industry, where carbon fiber is increasingly replacing steel, aluminium, and titanium for high-performance applications.
Magnesium components produced via High-Pressure Die Casting (HPDC) are already utilized in automotive and bicycle applications. However, the industry continuously seeks new opportunities to leverage the balance of lightness and mechanical properties offered by magnesium-lightened structures. HPDC is a cost-effective, high-productivity process suitable for large production volumes (more than 5000–10,000 parts per year).
Existing research and applications of HPDC face limitations. A key drawback of HPDC is internal porosity, which arises from turbulent flow during metal injection. This porosity complicates heat treatment and reduces achievable mechanical properties compared to other casting methods. Furthermore, challenges exist in creating composite castings with dissimilar materials. While aluminium-magnesium composites are explored, achieving metallurgical bonding between magnesium and aluminium foam cores is difficult due to the alumina layer on the aluminium foam surface. Alternative methods like using salt cores to create hollow parts in HPDC also present complexities in removing the core material and may limit part design. Therefore, there is a necessity to explore innovative approaches to overcome these limitations and further enhance the performance of HPDC components.
This research addresses the need to reduce component weight in HPDC by investigating the use of aluminium foam cores within magnesium castings. This approach aims to achieve a compromise between weight reduction and mechanical properties.
3. Research Purpose and Research Questions:
Research Purpose:
The primary aim of this research is to evaluate the influence of different types of aluminium foams and high-pressure die casting (HPDC) injection parameters on the properties of magnesium composite castings. The goal is to produce sound compound castings that achieve a balance between reduced weight and acceptable mechanical properties by using aluminium foams as cores within a magnesium cast part.
Key Research Questions:
- How do different aluminium foam types (Alporas, Formgrip, and Alulight) affect the quality of magnesium-aluminium foam composite castings produced by HPDC?
- What is the influence of HPDC injection parameters, specifically metal temperature, plunger speed, and multiplication pressure, on the final casting quality of these composite parts?
- Can a magnesium-aluminium foam composite produced by HPDC achieve a significant weight reduction while maintaining acceptable mechanical properties for structural applications, such as a bicycle component?
Research Hypotheses:
While not explicitly stated as hypotheses, the research operates under the premise that:
- By carefully selecting the type of aluminium foam core and optimizing HPDC injection parameters, it is possible to produce sound magnesium-aluminium foam composite castings.
- The use of aluminium foam cores in magnesium castings will lead to a significant reduction in weight compared to solid magnesium parts.
- The mechanical properties of the composite castings will be influenced by the type of aluminium foam core and the HPDC process parameters.
4. Research Methodology
Research Design:
This study employed an experimental research design to investigate the production of magnesium-aluminium foam composite castings using HPDC. The research involved systematically varying the type of aluminium foam core and key HPDC injection parameters to assess their impact on the final casting quality and properties.
Data Collection Method:
The quality of the produced composite castings was evaluated using:
- Visual Inspection: Castings were visually examined for surface defects and overall form.
- Radiographic Inspection (RX): X-ray analysis was performed using a General Electric X-cube 44XL at 160 kV to assess internal soundness, detect porosity, and confirm the integrity and placement of the aluminium foam cores within the magnesium matrix.
- Tensile Testing: Mechanical properties were evaluated through tensile tests conducted according to UNE-EN ISO 6892-1 B:2010 standards at room temperature using an Instron 3369 electromechanical testing machine with a crosshead speed of 5 mm/min. Tensile stress, ultimate tensile strength (UTS), and elongation were measured.
Analysis Method:
- Qualitative Analysis: Visual and RX inspection data were used to qualitatively assess the casting quality, focusing on defects such as short fill, cold shut, gas porosity, and foam core integrity.
- Quantitative Analysis: Tensile test data were analyzed quantitatively to determine the mechanical properties of both solid AM60B magnesium alloy castings and magnesium-aluminium foam composite castings. Statistical analysis was used to compare the properties and assess the impact of the aluminium foam core.
Research Subjects and Scope:
- Materials:
- Magnesium Alloy: AM60B was used as the cast magnesium alloy.
- Aluminium Foams: Three different types of closed-pore aluminium foams were evaluated:
- Alporas ALPO-PLA-03 (Alcan)
- Formgrip-based foam (Tecnalia processed)
- Alulight 0.4% TiB2 AlSi12 foam (Alulight)
- Process: High-Pressure Die Casting (HPDC)
- Component: A bicycle rod component was chosen as a demonstration part to evaluate the feasibility and benefits of the composite casting approach.
- Parameters Varied:
- Aluminium Foam Type and Density
- Metal Casting Temperature (680 °C and 720 °C)
- Injection Pressure (16-40 MPa for plastic injection simulation, 20-80 MPa for HPDC)
- Plunger Speed (0.25 m/s first phase, 20-80 m/s second phase)
- Core Placement (horizontal and vertical to metal flow)
- Squeeze Pin Application
5. Main Research Results:
Key Research Results:
- Sound Composite Castings Achieved: The study successfully produced sound magnesium-aluminium foam composite castings using HPDC.
- Importance of Foam Skin and Placement: The presence of an external continuous skin on the aluminium foam core and the correct placement of the foam within the die cavity were found to be critical for obtaining good quality parts. The skin prevents gas liberation and collapse of the foam during magnesium injection. Vertical placement of the foam core relative to the metal flow was superior to horizontal placement.
- Alulight Foam Performance: Among the tested foams, Alulight foam, which possesses an external skin, demonstrated the best performance in supporting the HPDC process and maintaining its integrity.
- Weight Reduction: A magnesium-aluminium foam composite bicycle component achieved a weight reduction of approximately 35% compared to a solid magnesium part.
- Optimized Parameters: A minimum pouring temperature of 720 °C for the magnesium alloy and standard HPDC parameters with a second phase injection speed of 80 m/s and specific pressure of 80 MPa were identified as suitable for producing sound composite castings. Squeeze pins were found to damage the foam core.
Statistical/Qualitative Analysis Results:
- Casting Temperature Effect (Figure 8): Casting AM60B at 680 °C resulted in "short fill/cold shut" defects and gas porosity. Increasing the temperature to 720 °C eliminated these defects.
- Plastic Injection Simulation (Table 4, Figure 10): Plastic injection tests simulating HPDC pressure showed that Alulight foam (density 0.54-1.55 Kg/dm³) could withstand 40 MPa pressure without collapsing, while Alporas (0.25-0.4 Kg/dm³) and Formgrip (0.4-0.55 Kg/dm³) foams failed at both 16 MPa and 40 MPa.
- Squeeze Pin Impact (Figure 14): Application of squeeze pin pressure (up to 200 MPa) directly onto the aluminium foam core resulted in the destruction of the foam, regardless of density.
- Core Placement Effect (Figures 15 & 16): Horizontal placement of the foam core relative to the metal flow led to shear rupture of the foam. Vertical placement minimized damage and resulted in only small shrinkage porosity.
- Injection Speed Effect (Figures 18 & 19): Reducing the second phase injection speed to 20 m/s resulted in "very poor filling." Standard HPDC parameters with 80 m/s second phase speed produced parts with good filling and only small solidification porosity.
- Mechanical Properties (Table 5):
- AM60B (Solid): Yield Strength (YS) = 141 ± 4.3 MPa, Ultimate Tensile Strength (UTS) = 219 ± 3.6 MPa, Elongation = 3 ± 0.5%.
- Composite: YS = 79 + 1.75 MPa, UTS = 122 ± 2.16 MPa, Elongation = 3 + 0.5%.
- Extrapolated Composite Properties (47% area reduction): YS = 149 ± 3.3 MPa, UTS = 230 ± 4.1 MPa, Elongation = 3 + 0.5%.
Data Interpretation:
The results indicate that producing magnesium-aluminium foam composite castings via HPDC is feasible, but requires careful selection of aluminium foam type and optimization of process parameters. Alulight foam, with its external skin, is suitable for this application due to its ability to withstand HPDC pressures and prevent gas porosity. Core placement and injection speed are critical parameters influencing casting quality. While a significant weight reduction is achieved, the initial mechanical properties of the composite are lower than solid magnesium. However, extrapolated values suggest that with optimized design and material utilization, the composite could potentially match or even slightly exceed the mechanical performance of solid magnesium in terms of tensile strength, while offering substantial weight savings.
Figure Name List:
- Figure 1: Some of the most employed processes to produce aluminium foams.
- Figure 2: (a) 3D rod design; and (b) detail of the placement and example of an aluminium foam core.
- Figure 3: Metallic die to produce Aluminium foams with Alulight.
- Figure 4: Metallic die to die cast magnesium over the aluminium foam.
- Figure 5: The plastic injection mould with an aluminium foam.
- Figure 6: HPDC process in order to obtain the magnesium-aluminium foam core composite.
- Figure 7: Detail of fixing pins in the fixed die cavity for placing the aluminium foam.
- Figure 8: (a) Short fill and cold shut defects; and (b) gas porosity defects.
- Figure 9: Central aluminium core covered with AM60B.
- Figure 10: Different configurations for plastic injection over the aluminium foams.
- Figure 11: (a) Alpora's foam (0.25 to 0.4 Kg/dm³); and (b) Formgrip's foam (0.4 to 0.65 Kg/dm³).
- Figure 12: HPDC part with totally destroyed aluminium foam.
- Figure 13: (a) Placement of a skinned foam with a non-skin area in the die; and (b) release of gas from the foam in the non-skinned area.
- Figure 14: 1.55 Kg/dm³ Aluminium foam after squeeze pin application.
- Figure 15: Horizontal placement to the metal flow of the core.
- Figure 16: Horizontal core placement to metal flow.
- Figure 17: Rod made by magnesium HPDC with the internal core of aluminium foam.
- Figure 18: Reduced second phase speed (20 m/s) HPDC cast part.
- Figure 19: Injected HPDC with core foam at standard parameters.
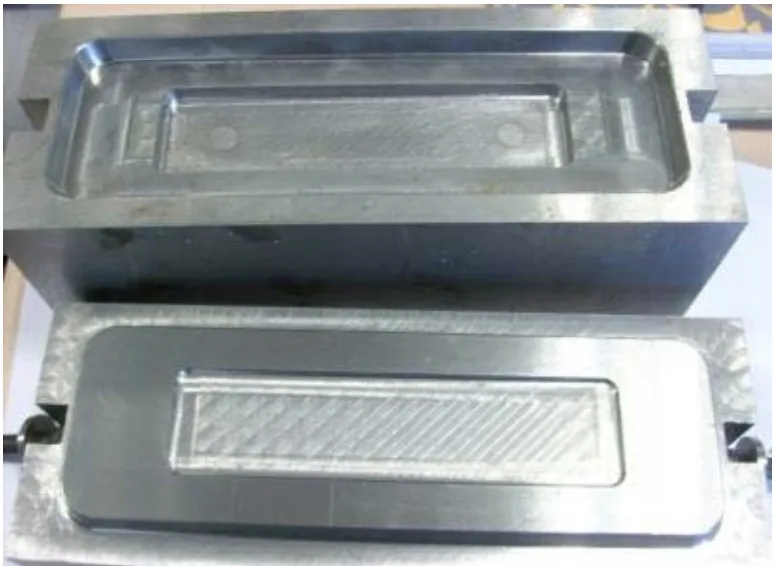
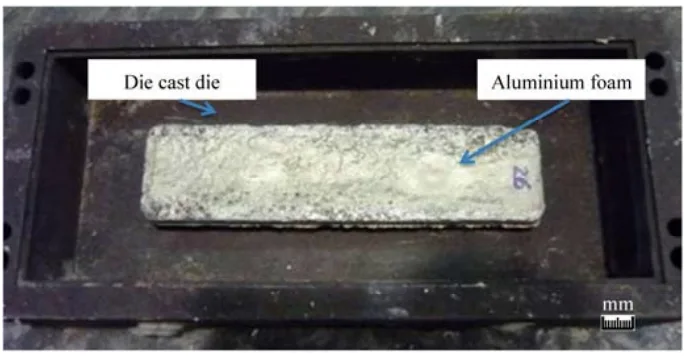
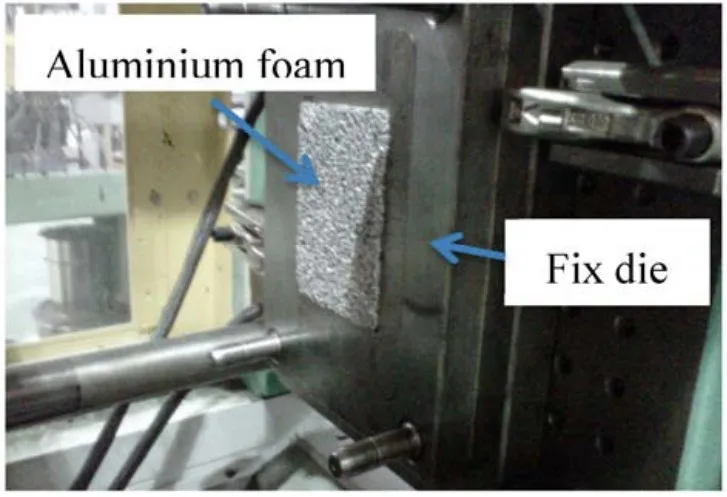
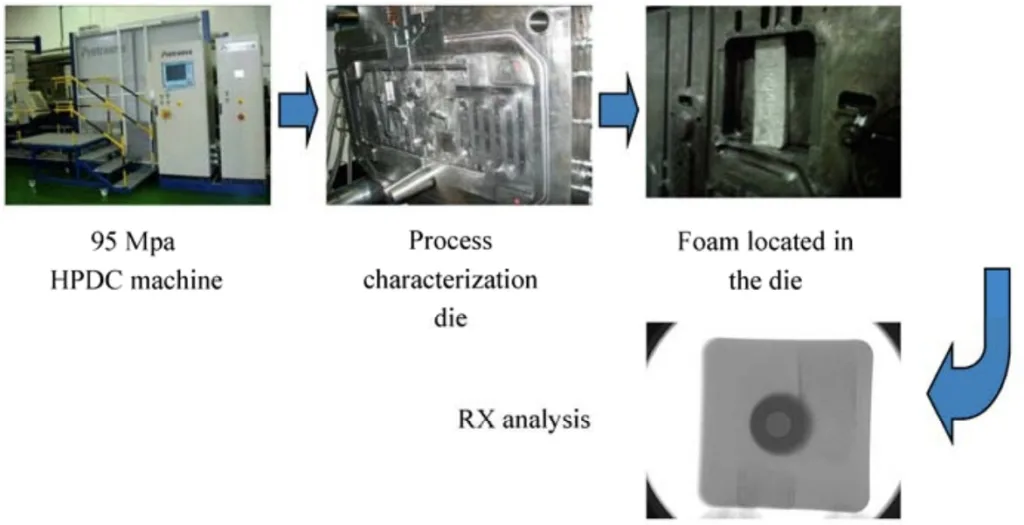
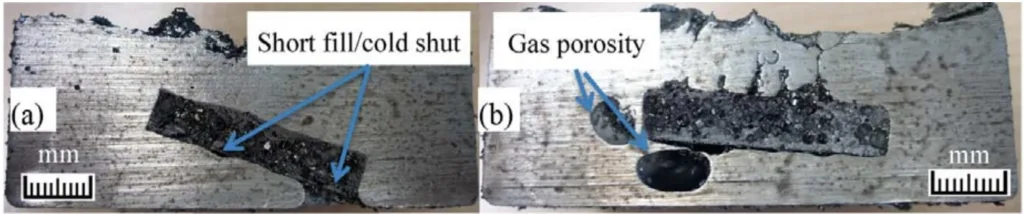
6. Conclusion and Discussion:
Summary of Main Results:
This research successfully demonstrated the feasibility of producing magnesium-aluminium foam composite castings using High-Pressure Die Casting (HPDC). The study identified Alulight-type aluminium foam, characterized by its external skin, as a suitable core material for this process. Optimized HPDC parameters, including a magnesium pouring temperature of 720 °C, a second phase injection speed of 80 m/s, and vertical placement of the foam core, are crucial for achieving sound castings. Using this approach, a bicycle rod component with a 35% weight reduction was successfully produced.
Academic Significance of the Research:
This study contributes to the academic field by demonstrating a viable method for creating lightweight metal matrix composites using HPDC. It expands the understanding of how aluminium foam cores behave within a magnesium casting environment under HPDC conditions and highlights the importance of foam type, skin presence, core placement, and injection parameters.
Practical Implications:
The findings have significant practical implications for industries seeking lightweighting solutions, particularly in transportation. The developed HPDC magnesium-aluminium foam composite casting process offers a pathway to manufacture lighter components, such as bicycle parts, potentially replacing heavier materials like solid aluminium, titanium, or steel. This can lead to improved fuel efficiency in vehicles and enhanced performance in applications like bicycles. The estimated material and production cost of using aluminium foam in a bicycle rod is approximately 0.3 Euros/part, suggesting economic viability.
Limitations of the Research:
- Lack of Chemical Bonding: The study acknowledges the absence of chemical bonding between the aluminium foam core and the magnesium alloy due to the alumina layer on the foam. This lack of bonding may limit the overall mechanical performance of the composite.
- Reduced Mechanical Properties: While weight reduction is significant, the initial mechanical properties of the composite castings are lower than those of solid AM60B magnesium alloy. Although extrapolated values suggest potential for improvement, further optimization is needed.
- Limited Tensile Test Data for Alulight Foam: The study notes that the increase in tensile test values specifically for Alulight-type foams was limited, suggesting a need for more in-depth mechanical characterization.
7. Future Follow-up Research:
Directions for Follow-up Research:
Future research should focus on addressing the limitation of chemical bonding between the aluminium foam and magnesium. Exploring surface treatments for the aluminium foam core is a key direction.
Areas Requiring Further Exploration:
Specifically, investigating the application of surface treatments, such as Zn-based coatings, to the aluminium foam core is recommended. This could potentially create a continuous interphase between the aluminium foam and the cast magnesium, enhancing bond strength and mechanical interlocking. Further research could also explore the potential benefits of aluminium foam cores in improving vibration damping, sound control, crash performance, or compression properties in various applications.
8. References:
- [1] Schultz, R. Aluminium Association Auto and Light Truck Group 2009 Update on North American Light Vehicle Aluminium Content Compared to the other Countries and Regions of the World. Phase II; Ducker Worlwide LLC: Troy, MI, USA, 2008; pp. 8–19.
- [2] Bonollo, F.; Urban, J.; Bonatto, B.; Botter, M. Gravity and low pressure die casting of aluminium alloys: A technical and economical benchmark. Metall. Ital. 2005, 97, 23-32.
- [3] Luo, A.A. Magnesium casting technology for structural applications. J. Magnes. Alloys 2013, 1, 2-22.
- [4] Gertsberg, G.; Nagar, N.; Lautzker, M.; Bronfin, B. Effect of HPDC parameters on the performance of creep resistant alloys MRI153M and MRI230D. SAE Tech. Pap. 2005, 1, 1–7.
- [5] Otarawanna, S.; Laukli, H.I.; Gourlay, C.M.; Dahle, A.K. Feeding mechanisms in high-pressure die castings. Metall. Mater. Trans. A 2010, 41, 1836-1846.
- [6] Bonollo, F.; Gramegna, N.; Timelli, G. High-pressure die-casting: Contradictions and challenges. JOM 2015, 67, 901-908.
- [7] Yim, C.D.; Shin, K.S. Semi-solid processing of magnesium alloys. Mater. Trans. 2003, 44, 558–561.
- [8] Sabau, A.S.; Dinwiddie, R.B. Characterization of spray lubricants for the high pressure die casting processes. J. Mater. Process. Technol. 2008, 195, 267–274.
- [9] Kimura, R.; Yoshida, M.; Sasaki, G.; Pan, J.; Fukunaga, H. Characterization of heat insulating and lubricating ability of powder lubricants for clean and high quality die casting. J. Mater. Process. Technol. 2002, 130–131, 289-293.
- [10] Puschmann, F.; Specht, E. Transient measurement of heat transfer in metal quenching with atomized sprays. Exp. Therm. Fluid Sci. 2004, 28, 607-615.
- [11] Rogers, K.J.; Savage, G. In-cavity pressure sensors-errors, robustness and some process insights. Die Cast Eng. 2000, 44, 76-80.
- [12] Kong, L.X.; She, F.H.; Gao, W.M.; Nahavandi, S.; Hodgson, P.D. Integrated optimization system for high pressure die casting processes. J. Mater. Process. Technol. 2008, 201, 629-634.
- [13] Keber, K.; Bormann, D.; Möhwald, K.; Hollander, U.; Bach, W. Compound casting of aluminium and magnesium alloys by High Pressure Die Casting. In Proceedings of the Magnesium 8th International Conference on Magnesium Alloys and Their Applications, Weimar, Germany, 26-29 October 2009; pp. 390-397.
- [14] Kunst, M.; Fischersworring-bunk, A.; Liebscher, C.; Glatzel, U.; Esperance, G.L.; Plamondon, P.; Baril, E.; Labelle, P. Microstructural characterization of Die Cast Mg-Al-Sr (AJ) Alloy. In Proceedings of the Magnesium: Proceedings of the 7th International Conference on Magnesium Alloys and Their Applications, Dresden, Germany, 6–9 November 2006; pp. 498-505.
- [15] Vicario, I. Study of high pressure die cast AZ91D magnesium alloy with surface treated aluminium 6063 cores for Al-Mg multi-material. In Proceedings of the 2nd Annual World Congress of Advanced Materials, Suzhou, China, 5-7 June 2013; pp. 7–21.
- [16] Yaokawa, J.; Miura, D.; Anzai1, K.; Yamada, Y.; Yoshii, H. Strength of salt core composed of alkali carbonate and alkali chloride mixtures made by casting technique. Mater. Trans. 2007, 5, 1034–1041.
- [17] Moschini, R. Production of Hollow Components in HPDC through the Use of Ceramic Lost Cores; XXXI Congreso Tecnico di Fonderia: Vincenza, Italy, 2012; pp. 1–33.
- [18] Yamada, Y.; Yaokawa, J.; Yoshii, H.; Anzai, K.; Noda, Y.; Fujiwara, A.; Suzuki, T.; Fukui, H. Developments and application of expendable salt core materials for high pressure die casting to apply closed-deck type cylinder block. SAE Int. 2007, 32-0084, 1–5.
- [19] Vicario, I.; Egizabal, P.; Galarraga, H.; Plaza, L.M.; Crespo, I. Study of an Al-Si-Cu HPDC alloy with high Zn content for the production of components requiring high ductility and tensile properties. Int. J. Mater. Res. 2013, 4, 392-397.
- [20] Benedick, C. Production and application of aluminium foam, past product potential revisited in the new millennium. Light Met. Age 2002, 60, 24-29.
- [21] Bausmesiter, J.; Weise, J. Structural Materials and Processes in Transportation, Metal Foams; John Wiley & Sons: Hoboken, NJ, USA, 2013; pp. 415-440.
- [22] Banhar, J. Metal foams: Production and stability. Adv. Eng. Mater. 2006, 9, 781–794.
- [23] Coleto, J.; Goñi, J.; Maudes, J.; Leizaola, I. Applications and manufacture of open and closed cell metal foams by foundry routes. In Proceedings of International Congress Eurofond, La Rochelle, France, 2–4 June 2004; pp. 1-10.
- [24] Körner, C.; Hirschmann, M.; Wiehler, H. Integral Foam Moulding of Light Metals. Mater. Trans. 2006, 47, 2188-2194.
- [25] Baumeister, J.; Weise, J. Application of aluminium-polymer hybrid foam sandwiches in battery housings for electric vehicles. Procedia Mater. Sci. 2014, 4, 301-330.
- [26] Vesenjak, M.; Borovinšek, M.; Fiedler, T.; Higa, Y.; Ren, Z. Structural characterisation of advanced pore morphology (APM) foam elements. Mater. Lett. 2013, 110, 201-203.
- [27] Miyoshi, T.; Itoh, M.; Akiyama, S.; Kitahara, A. Aluminium foam, “ALPORAS": The production process, properties and application. In Materials Research Society Symposium Proceedings, Boston, MA, USA, 1-3 December 1998; 1998; pp. 133-137.
- [28] Miyoshi, T.; Itoh, M.; Akiyama, S.; Kitahara, A. Alporas aluminum foam: Production process, properties, and applications. Adv. Eng. Mater. 2000, 2, 179–183.
- [29] Gegerly, V.; Clyne, T.W. The formgrip process: Foaming of reinforced metals by gas release in precursors. Adv. Eng. Mater. 2002, 2, 175–178.
- [30] Gergely, V.; Curran, D.C.; Clyne, T.W. Advances in the melt route production of closed cell aluminium foams using gas-generating agents. In Proceedings of Global Symposium of Materials Processing and Manufacturing Processing & Properties of Lightweight Cellular Metals and Structures, Seattle, WA, USA, 17-21 February 2002; pp. 3-8.
- [31] Baumeister, J. Production technology for aluminium foam/steel sandwiches. In Proceedings of the International Conference on Metal Foams and Porous Metal Structures, Bremen, Germany, 14-16 June 1999; pp. 113-118.
- [32] Seeliger, H.W. Cellular Metals: Manufacture, properties, applications. In Proceedings of the MetFoam, Berlin, Germany, 23-25 June 2003; pp. 5-12.
- [33] Kováãik, J.; Simančík, F.; Jerz, J.; Tobolka, P. Reinforced aluminium foams. In Proceedings of the International Conference on Advanced Metallic Materials, Smolenice, Slovakia, 5–7 November 2003; pp. 154–159.
- [34] Braune, R.; Otto, A. Tailored blanks based on foamable aluminium sandwich material. In Proceedings of the International Conference on Metal Foams and Porous Metal Structures, Bremen, Germany, 14-16 June 1999; pp. 119-124.
- [35] Gutiérrez-Vázquez, J.A.; Oñoro, J. Fabricación y comportamiento de espumas de aluminio con diferente densidad a partir de un precursor AlSi12. Rev. Metal. 2010, 46, 274–284.
9. Copyright:
This material is Iban Vicario, Ignacio Crespo, Luis Maria Plaza, Patricia Caballero, and Ion Kepa Idoiaga's paper: Based on Aluminium Foam and Magnesium Compound Casting Produced by High-Pressure Die Casting.
Paper Source: doi:10.3390/met6010024
This material was summarized based on the above paper, and unauthorized use for commercial purposes is prohibited.
Copyright © 2025 CASTMAN. All rights reserved.