This article introduces the paper "Advances in Technology of Soluble Cores for Die Castings" presented at the Archives of Foundry Engineering
1. Overview:
- Title: Advances in Technology of Soluble Cores for Die Castings
- Author: P. Jelínek, E. Adámková, F. Mikšovský, J. Beňo
- Publication Year: 2015
- Publishing Journal/Academic Society: Archives of Foundry Engineering
- Keywords: Salt cores, Manufacture by squeezing and shooting, The use of cooking salts, Bonding of cores, Salinity of cleaning water, Electric conductance
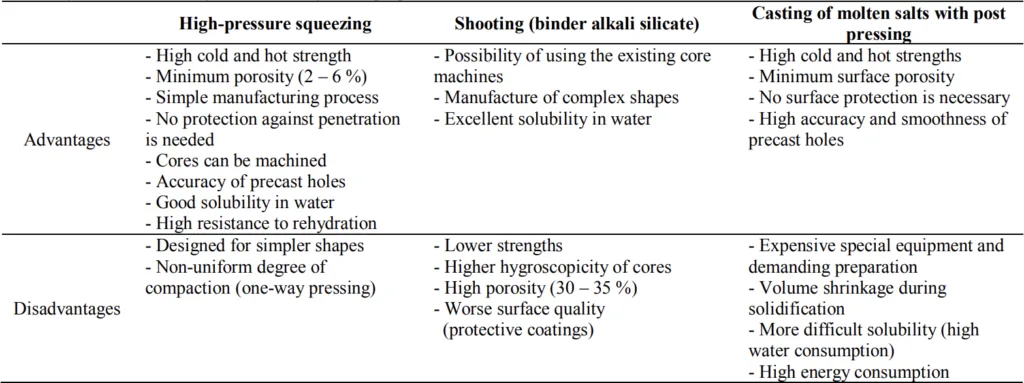
2. Research Background:
The increasing complexity of casting designs presents a significant challenge to traditional die casting methods that rely on simple metal cores. These existing methods struggle to meet the rising demands for intricate internal geometries in castings. Consequently, there is a growing interest in "soluble" cores, also known as lost cores, as a viable alternative. Among soluble core materials, inorganic salts hold the greatest potential due to their inherent solubility in water, simplifying core removal after casting. However, these salt cores must fulfill several critical requirements, including:
- Dimensional accuracy
- Sufficient bench life (resistance to hydration)
- Strength at elevated temperatures (up to 700 °C)
- Smoothness of precast cavities (low Ra value)
- Ease of solubility in water
While some research suggests salt cores are suitable for lower mold filling rates (below 35 m/s) and processes like rheocasting, further development is needed to optimize their application in high-pressure die casting. This paper addresses the development of salt cores manufactured through high-pressure squeezing and shooting techniques, utilizing binders, and explores the impact of salt type and additives on core properties. It also investigates bonding methods for salt cores and the management of salinity in water used for core removal.
3. Research Purpose and Research Questions:
This research aims to advance the technology of soluble salt cores for high-pressure die casting. The primary research purpose is to investigate and optimize the manufacturing and application of salt cores by addressing the following key research questions:
- How do high-pressure squeezing and shooting methods affect the properties of salt cores, particularly strength and porosity?
- What is the influence of the shape of NaCl salt crystals and the addition of various additives on the strength characteristics of salt cores?
- Can effective bonding technologies be developed for joining salt cores to create complex internal geometries, and for combining salt cores with metal components?
- How can the salinity of circulating water used for dissolving salt cores be effectively monitored and controlled to ensure efficient core removal and potential water recycling?
The research hypothesizes that:
- The incorporation of specific additives into composite salt formulations will enhance the mechanical strength of salt cores.
- Monitoring the electrical conductance of water used for core removal can serve as a reliable method for assessing and managing water salinity, ensuring consistent core dissolution.
4. Research Methodology:
This research employed an experimental design to evaluate different aspects of salt core technology. The core manufacturing methods investigated were high-pressure squeezing and shooting, utilizing alkali silicate binders. Data collection focused on measuring key properties of the manufactured salt cores and related processes:
- Core Strength: Bending strength (for squeezed cores) and shear strength (for glued joints) were measured to assess mechanical performance.
- Porosity: Porosity levels were evaluated to understand the compactness of cores produced by different methods.
- Solubility: The rate of core dissolution in water and saturated salt solutions was measured to assess core removal efficiency.
- Hygroscopicity: Weight gain measurements over time were used to determine the cores' susceptibility to moisture absorption from the air.
- Electrical Conductance and pH: These parameters were monitored in water used for core dissolution to track salinity changes.
- Microstructure Analysis: Scanning Electron Microscopy (SEM) and Energy-Dispersive X-ray Spectroscopy (EDX) were used to analyze the shape of salt grains and the distribution of additives.
The research scope included:
- Salt Types: Various types of cooking salts were tested, including edible rock salt, Alpine salt, fine sea salt, and chemically pure NaCl (p.a.).
- Additives: Composite salts were formulated with additives such as ZrSiO4, Al2O3, Fe2O3, and SiO2 to enhance core properties.
- Binders: Alkali silicate was used as a binder in the shooting method.
- Gluing Agents: Several commercially available glues and a research product (VŠB-TUO) were evaluated for bonding salt cores and salt-metal joints.
5. Main Research Results:
The study yielded several key findings regarding the manufacturing and properties of salt cores:
- Manufacturing Method Impact: High-pressure squeezing consistently produced salt cores with significantly higher bending strength compared to the shooting method using alkali silicate binders.
- Salt Type and Strength: KCl salt cores exhibited higher cold and hot strength than NaCl cores. Among NaCl salts, crushed rock salts and sea salt resulted in higher strengths than Alpine salt, except for standard NaCl (p.a.) which also showed high strength.
- Influence of Grain Shape: "Dipyramidal, regular" shaped NaCl grains (as found in standard NaCl p.a.) led to high strength in both squeezed and shot cores. Conversely, cubic grains (Alpine salts) resulted in lower strength.
- Effect of Additives: The addition of composite salts, particularly α-Al2O3, significantly increased both cold and hot strength of salt cores. Primary bending strength exceeded 9 MPa, approximately three times higher than PUR Cold-Box cores.
- Porosity and Strength: Increasing pressing forces in the squeezing method reduced core porosity to below 6%, resulting in glassy, monolithic cores with enhanced strength and surface smoothness (Ra < 5 µm).
- Gluing of Salt Cores: Effective bonding of salt cores (salt-salt and salt-metal) was demonstrated using various industrial glues and a research-developed glue (VŠB-TUO). Shear strength of salt-salt joints ranged from 63 to 105 N/cm², and salt-metal joints from 160 to 232 N/cm².
- Water Salinity Monitoring: Electrical conductance proved to be a reliable indicator of water salinity during core dissolution. Increased salinity (NaCl concentration) slowed down the dissolution rate. A critical value of electric conductance can be determined to ensure effective core solubility in a closed-loop water circulation system.
Figure Name List:
- Fig. 1. Comparison of hygroscopicity of squeezed and shot cores
- Fig. 2. Comparison of strengths of salt cores squeezed and shot from different kinds of cooking salts
- Fig. 3. Shattered surface of crushed rock salts (samples Nos 1, 2) and EDX analysis of chemical composition
- Fig. 4. Regular cubic grains of Alpine salts (samples Nos 3, 4) and EDX analysis confirming the presence of anticaking additives on the salt grain surface (MgCO3, CaCO3)
- Fig. 5. Dipyramidal regular shape of NaCl, p.a. - standard (sample No 6) and EDX analysis of chemical composition
- Fig. 6. H 2400 during dissolution of the glued core
- Fig. 7. Test with the VŠB – TUO glue during dissolution of the glued core
- Fig. 8. Comparison of dissolving the salt cores in two types of saturated solutions and in pure water
- Fig. 9. Kinetics of dissolution of salt cores in dependence on pH and electric conductance
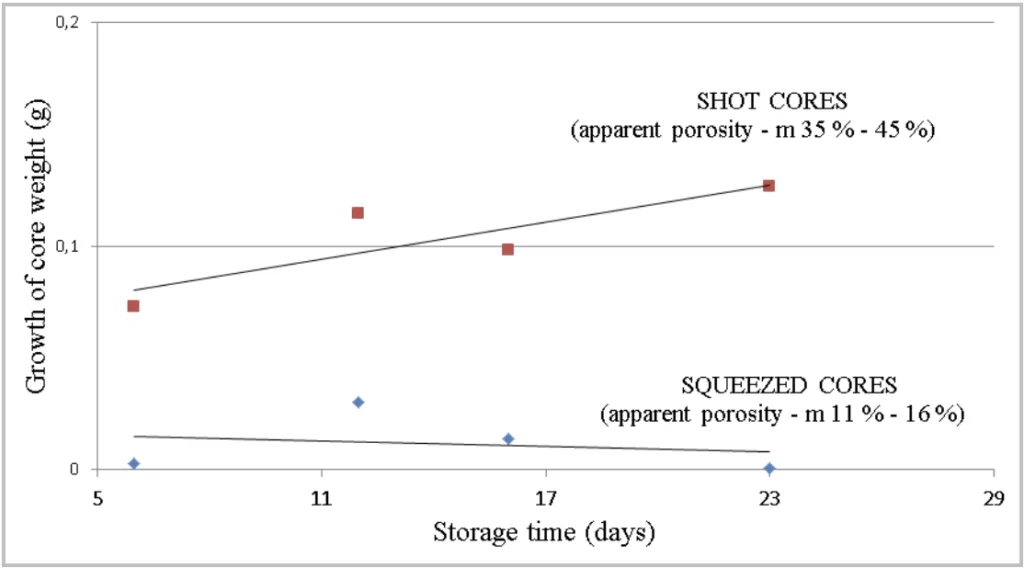
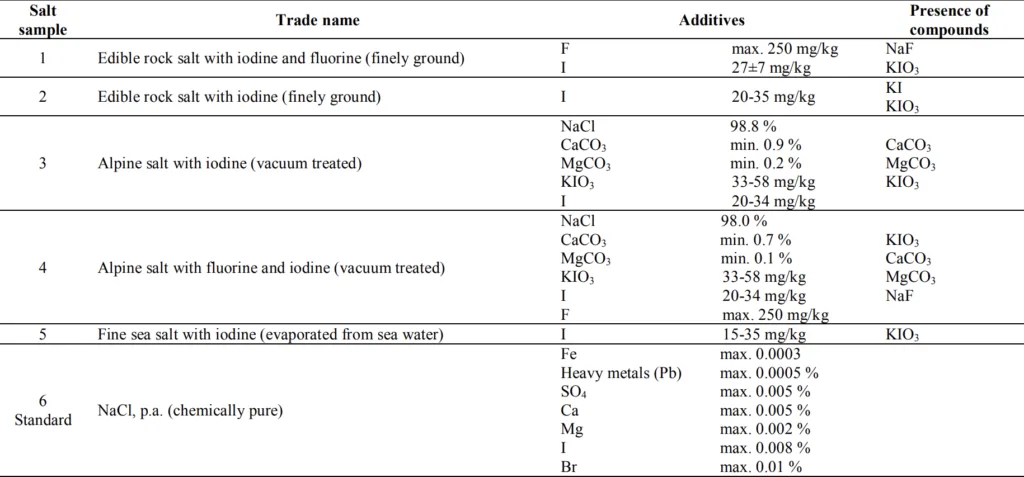
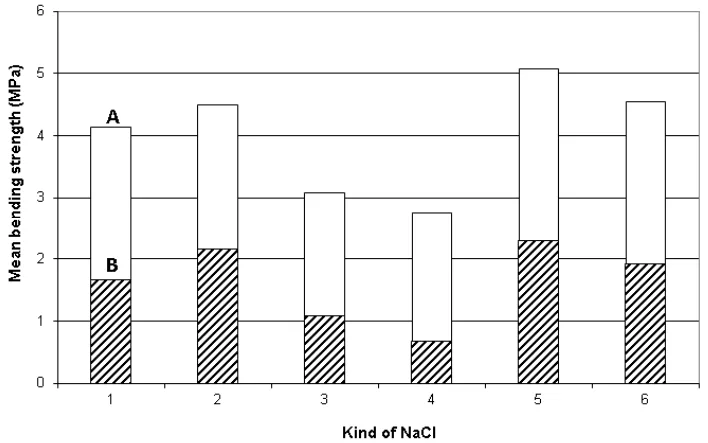
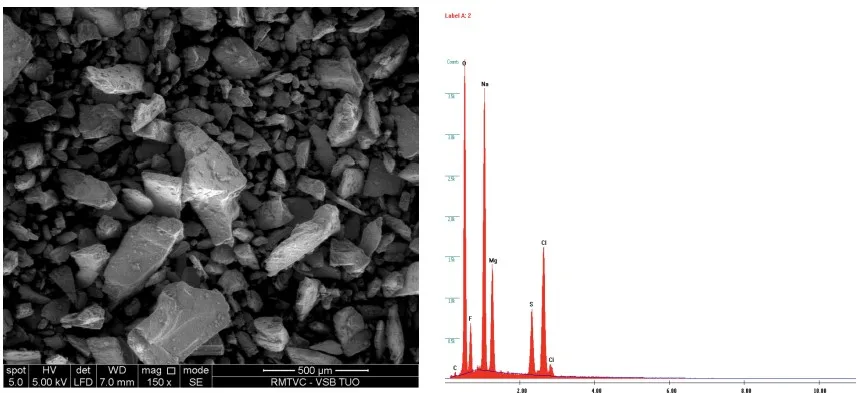
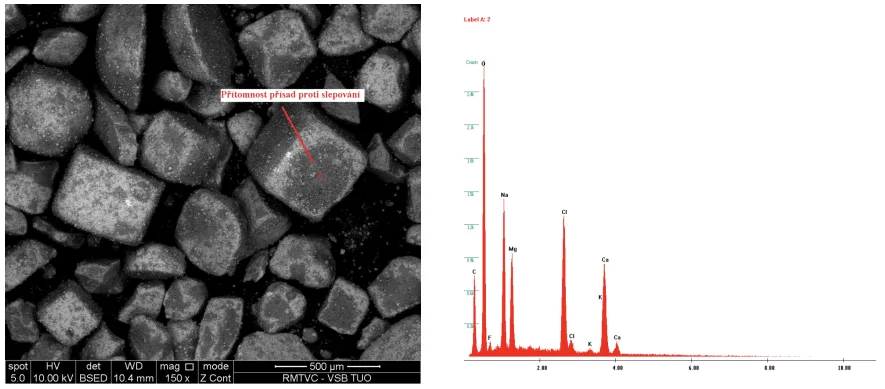
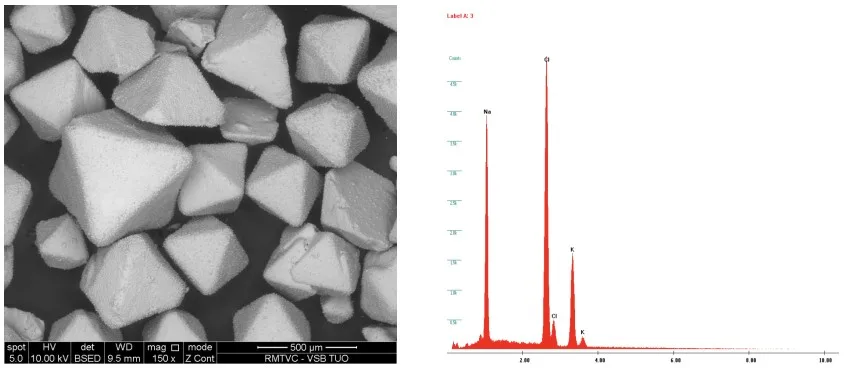
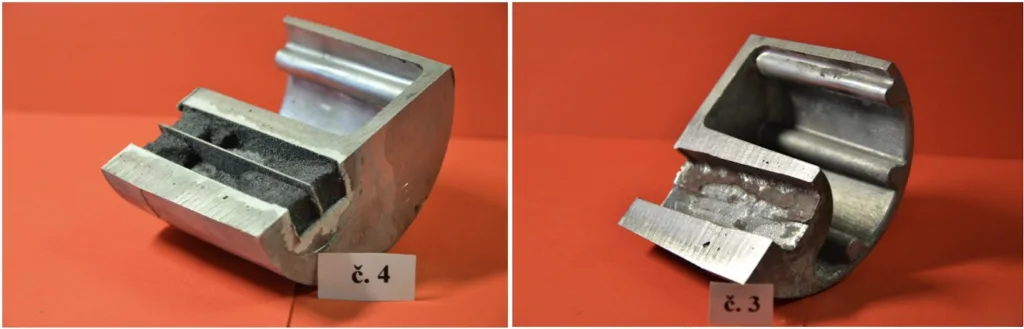
6. Conclusion and Discussion:
This research confirms that salt water soluble cores offer significant potential for demanding die casting applications. The study highlights the critical influence of manufacturing methods, salt type, grain shape, and additives on the properties of salt cores. High-pressure squeezing emerges as a superior method for achieving high-strength cores. The "dipyramidal, regular" grain shape of NaCl and the use of composite salts with additives are key factors in enhancing core strength. Furthermore, the successful development of gluing techniques expands the design possibilities for complex internal casting geometries using salt cores, even in combination with metal components. The application of electrical conductance monitoring provides a practical method for managing water salinity in core removal processes, potentially enabling closed-loop water recycling systems.
Academic Significance of the Research:
This research contributes valuable knowledge to the field of die casting by providing a comprehensive investigation into the factors influencing the performance of salt cores. It offers a deeper understanding of material selection, manufacturing processes, and bonding techniques for soluble cores, advancing the scientific basis for their application in high-pressure die casting.
Practical Implications:
The findings of this study offer practical guidelines for die casting professionals seeking to implement salt core technology. The research provides insights into:
- Selecting appropriate salt types and additives to achieve desired core strength and solubility.
- Optimizing manufacturing methods (squeezing vs. shooting) based on required core properties and complexity.
- Utilizing effective gluing techniques for assembling complex core geometries.
- Implementing electrical conductance monitoring for efficient and sustainable core removal processes.
Limitations of the Research:
While the research provides valuable insights, it is important to note that it primarily focuses on laboratory-scale experiments. Further research is needed to validate these findings in industrial die casting environments and to assess the long-term performance and cost-effectiveness of salt core technology in mass production.
7. Future Follow-up Research:
Future research directions should focus on:
- Investigating the dimensional accuracy of glued salt cores and developing methods for its improvement.
- Exploring the application of protective coatings for glued joints to enhance their performance during casting.
- Scaling up the manufacturing and application of salt cores to industrial production levels.
- Optimizing the control of water salinity in closed-loop core removal systems for industrial applications.
- Conducting a comprehensive cost-benefit analysis and environmental impact assessment of salt core technology compared to traditional methods.
8. References:
- [1] Pacyniak, R. & Kaczorowski, R. (2010). Ductile cast iron obtaining by Inmold method with use of LOST FOAM process. Archives of Foundry Engineering. 10(1), 101-104. ISSN: 1897-3310.
- [2] Michels, H., Bűnck, M. & Bührig - Polaszek, A. (2010). Suitability of lost cores in rheocasting process. Transactions of Nonferrous Metals Society of China. 20, 948-953. DOI: 10.1016/S1003-6326(10)60612-7.
- [3] Dańko, J., Dańko, R. (2009). Theoretical and technological aspects of the production processes of foundry cores blown In 50. Konferencji Krzepniecie i Krystalizacja Metali (pp. 71-86). Katowice - Gliwice, Poland: Polska Academia Nauk, Komisja Odlewnictwa. ISBN: 978-83-929266-0-3. (in Polish)
- [4] Holtzer, M., Dańko, R. (2009). Theory and practice of regeneration and utilization of waste molding and core. In 50. Konferencji Krzepniecie i Krystalizacja Metali (pp. 133-152). Katowice - Gliwice, Poland: Polska academia nauk, Komisja Odlewnictwa. ISBN: 978-83-929266-0-3. (in Polish).
- [5] Kallien, L., Böhnlein, Ch., Dworak, A. & Müller, B. (2013). Ergebnisse aus dem Forschungsprojekt 3-D-Freiform medienführende Kanäle im Druckguss. Giesserei Praxis. 100(12), 36-43. ISSN: 0016-9781
- [6] Fuchs, B., Eibisch, H. & Körner, C. (2013). Core viability simulation for salt core technology in high pressure die casting. International Journal of Metalcasting. 7(3), 39-45. ISSN: 1939-5981.
- [7] Fuchs, B., et. all (2014). Angepasste Wärmebehandlung von druckgegossenen Aluminiumstrukturbauteilen mit verlorenem Salzkerne. Giesserei Praxis. 101(06), 52-59. ISSN:0016-9781
- [8] Yaokawa, J., Miura, D., Anzai, K., Yamada, Y., & Yoshii, H. (2007). Strength of salt core composed of alkali carbonate and alkali chloride mixtures made by casting technique. Materials transactions. 48(5), 1034-1041.
- [9] Stingl, P., & Shiller, G. (2009). Gichte und rückstandfreie Entkernung - Salzkerne für den Aluminiumguss. Giesserei-Erfahrungsaustausch. 6, 4-8.
- [10] Adámková, E., Jelínek, P., & Študentová, S. (2013). Application of cooking salts in manufacture of water soluble cores for high pressure die casting (Aplikace kuchyňských solí při výrobě vodou rozpustných jader odlitků tlakového lití). Materials and technology. 61(11-12), 689-693. ISSN: 1580-2949, 1580-3414.
- [11] Jelínek, P., Mikšovský, F., Beňo, J. & Adámková, E. (2013). Development of Foundry Cores Based on Inorganic Salts. Materials and technology. 47(6), 689-693. ISSN: 1580-2949, 1580-3414.
- [12] Fuchs, B. & Körner, C. (2013). Dwell pressure induced compression of lost salt cores in high pressure die casting. International Foundry Research. 3, 18-23. ISSN: 0046-5933.
- [13] Rupp, S. & Heppes, F. (2013). Combicore – Giesskerne für den Druckguss. Giesserei-Erfahrungsaustausch. 3/4, 6-9.
- [14] Fabbroni, M. (2013) Lost Core Ein industrieller Prozesspfad für hochwertige Salzkerne. Giesserei Praxis. 100(07), 82-83. ISSN: 0016-9781
- [15] Kaneko, Y. & Morita, A. (1970) 6th SDCE international die casting congress. PAPER NO. 91, Cleveland, Ohio, November 16-19.
- [16] Loper, C. R. et. all. (1985) The Use of Salt In Foundry Cores. AFS Transactions, 85-82, 545-560.
- [17] Jelínek, P., Mikšovský, F., & Adámková, E. (2012). Influencing the strength characteristics of salt cores soluble in water. Slévárenství. 60(3-4), 85-89. ISSN: 0037-6825.
- [18] Major Gabryś, K., & Dobosz, M. (2009). A new ester hardener for moulding sands with water glass having slower activity. Archives of Foundry Engineering. 9(4), 125-128. ISSN: 1897-3310.
9. Copyright:
This material is [P. Jelínek, E. Adámková, F. Mikšovský, J. Beňo]'s paper: Based on [Advances in Technology of Soluble Cores for Die Castings].
Paper Source: [https://doi.org/10.2478/afe-2015-0005]
This material was summarized based on the above paper, and unauthorized use for commercial purposes is prohibited.
Copyright © 2025 CASTMAN. All rights reserved.