This article introduces the paper [Design of Wear-Resistant Diecast AlSi9Cu3(Fe) Alloys for High-Temperature Components] published in the journal [Metals].
1. Paper Overview
This research focuses on enhancing the AlSi9Cu3(Fe) alloy with iron (Fe), manganese (Mn), and chromium (Cr) to develop wear-resistant diecast aluminum-silicon-copper alloys suitable for high-temperature applications. Several alloys with varying levels of iron, manganese, and chromium content (Fe: 0.80, 1.00, 1.20 wt.%; Mn: 0.25, 0.40, 0.55 wt.%; Cr: 0.06, 0.10 wt.%) were produced and subjected to Brinell hardness measurements and pin-on-disk wear tests from room temperature up to 200°C. Microstructural changes due to different alloying levels were quantitatively analyzed using metallography and image analysis techniques. The results showed that increasing Fe, Mn, and Cr content promoted the precipitation of primary and secondary Fe-rich particles, mainly in polyhedral, blocky, and star-like morphologies. These compounds exhibited high hardness unaffected by chemical composition and morphology variations. At high temperatures, diecast alloys consistently showed lower average hardness and wear resistance, especially at 200°C; however, a greater amount of Fe-rich particles could compensate for alloy softening.
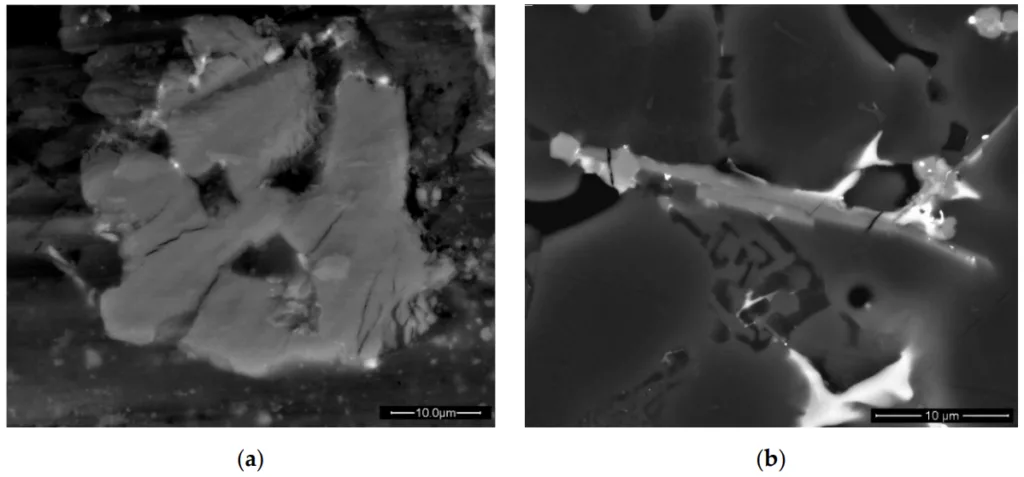
Key Information:
- Title: Design of Wear-Resistant Diecast AlSi9Cu3(Fe) Alloys for High-Temperature Components
- Authors: Giulio Timelli, Alberto Fabrizi, Simone Vezzù, Alessandro De Mori
- Publication Year: 2020
- Journal: Metals
- Keywords: aluminum alloys, high-pressure die casting, sludge, Fe-rich compounds, high temperature, wearing, hardness
2. Research Background: Automotive Lightweighting, High-Temperature Components, and Limitations of Aluminum Alloys
The increasing demand for aluminum-based alloys in the automotive sector is driven by the need for vehicle weight reduction and performance enhancement. The use of lightweight materials is crucial for meeting energy and environmental requirements. Al-Si alloys are widely used in the automotive industry due to their excellent castability and high mechanical properties relative to their weight.
Beyond tensile and fatigue properties, significant research efforts are directed towards improving the tribological properties of Al-Si based alloys, especially for high-temperature components such as pistons, cylinder blocks, and cylinder liners in internal combustion engines [1-4].
However, aluminum alloys inherently lack sufficient wear resistance [5]. While silicon alloying is a common method to improve wear response in casting Al alloys by promoting hard Si crystal formation, it reduces machinability. Hypereutectic Al–Si alloys (Si > 13 wt.%) are generally used for tribological applications, but Si content is limited to 20 wt.% in commercial applications [9].
Iron (Fe) has been reported to improve the tribological behavior of Al-Si alloys [10], and small additions of iron enhance the mechanical properties and thermal stability of the material at high temperatures [11]. However, iron is generally considered an impurity in Al-Si casting alloys, negatively affecting final mechanical properties. This is typically attributed to the formation of brittle β-Al₅FeSi (β-Fe) phase, which appears as needle-like particles in the microstructure. Needle-like particle tips act as stress concentration points, and the presence of β-Fe phase generally reduces tensile properties (ductility and ultimate tensile strength) and wear resistance [12]. Nevertheless, a high Fe content is required in aluminum diecasting alloys to alleviate or eliminate die soldering phenomena occurring in high-pressure die casting (HPDC) processes.
Therefore, a common solution to mitigate the negative effects of β-Fe needle-like particles in Al-Si alloys is to add transition metals (Mn, Cr, Ni, Mo, Co) and some alkaline earth metals (Sr, Be) to modify the morphology of the β-Fe phase into a less harmful and more compact shape [13-15].
Manganese, the most widely used alloying element, and chromium induce the precipitation of hard primary α-Al₁₅(Fe,Mn,Cr)₃Si₂ (α-Fe) particles (sludge [18]) instead of the needle-like β-Fe phase. As reported in [19], replacing β-Fe with α-Fe phase enhances wear resistance. α-Fe particles exhibit better bonding with the α-Al matrix compared to the β-Fe phase, thus reducing the possibility of crack formation at the interface matrix/particle.
Sludge formation is a typical problem in HPDC casting processes, where melt temperatures are generally lower than in other casting processes to extend the operating life of dies and tools. In addition to melting and holding temperature and time, the alloy's chemistry influences sludge formation. The sludge factor (also called iron equivalent value [20,21]) is widely accepted as a useful parameter for predicting primary α-Fe particle precipitation. The sludge factor can be determined from the initial iron, manganese, and chromium contents in the alloy [22,23]:
Sludge Factor (SF) = (wt.%Fe × 1) + (wt.%Mn × 2) + (wt.%Cr × 3) (1)
In this context, the automotive industry requires the best compromise between excellent wear and high-temperature resistance and suitability for mass production. For this reason, wear-resistant automotive components are produced using hypereutectic Al-Si alloys via low-pressure die casting instead of HPDC, as the high silicon crystal density in hypereutectic alloys reduces die and tool life.
Conversely, the ability to use HPDC offers several advantages, such as high production rates, short cycle times, and the production of castings with greater geometrical complexity. This can be achieved by maintaining the use of hypoeutectic Al-Si alloys necessary to ensure low die wear rates and by properly designing sludge particles to optimize wear and high-temperature properties.
This study analyzed a diecast AlSi9Cu3(Fe) alloy. Chemical composition variations were systematically obtained by gradually increasing iron, manganese, and chromium content according to the tolerance limits of the EN 1706:2010 standard [24]. This paper investigates a set of proposed alloys with increased Fe, Mn, and Cr alloying elements, considering microstructure, hardness, and wear resistance at high temperatures.
3. Research Purpose and Research Questions
The purpose of this research is to develop wear-resistant diecast Al-Si-Cu alloys suitable for high-temperature components. To achieve this, the study aims to improve the properties of the base AlSi9Cu3(Fe) alloy by controlling the content of iron (Fe), manganese (Mn), and chromium (Cr).
Key Research Questions:
- How does varying the content of iron, manganese, and chromium in AlSi9Cu3(Fe) alloys affect the microstructure, specifically the formation and morphology of Fe-rich intermetallic particles?
- What is the effect of varying iron, manganese, and chromium content on the hardness of AlSi9Cu3(Fe) alloys, both at room temperature and elevated temperatures?
- How do varying additions of iron, manganese, and chromium impact the wear resistance of diecast AlSi9Cu3(Fe) alloys at room temperature and high temperatures?
- Can the sludge factor (SF) be used as a predictive parameter for the wear rate of these alloys?
Research Hypotheses:
- Increasing the content of iron, manganese, and chromium will promote the precipitation of primary and secondary Fe-rich particles, increasing the sludge factor.
- Increased Fe-rich particle precipitation will enhance the hardness and wear resistance of AlSi9Cu3(Fe) alloys.
- While hardness and wear resistance may decrease at high temperatures, higher Fe-rich particle content will mitigate high-temperature softening and maintain relatively better wear resistance.
- The wear rate of diecast AlSi9Cu3(Fe) alloys can be predicted using the sludge factor.
4. Research Methodology
This research focused on modifying alloy composition to improve the wear resistance of AlSi9Cu3(Fe) alloys.
Research Design:
- 18 experimental alloys were produced by systematically varying Fe, Mn, and Cr content based on a base alloy (Alloy 1).
- Fe content levels: 0.80, 1.00, 1.20 wt.%
- Mn content levels: 0.25, 0.40, 0.55 wt.%
- Cr content levels: 0.06, 0.10 wt.%
Data Collection Methods:
- Chemical Composition Analysis: Chemical composition analysis of the base alloy and experimental alloys (Tables 1, 2).
- Microstructural Analysis: Metallographic analysis using optical microscopy (OM) and scanning electron microscopy (SEM) with energy-dispersive X-ray spectroscopy (EDS). Image analysis software for quantitative microstructural analysis.
- Hardness Measurements: Brinell hardness tests (ASTM E10-15a [27]) at room temperature, 150°C, and 200°C. Nanoindentation tests at room temperature using a Berkovich diamond indenter and the Oliver-Pharr model [28] to measure hardness and reduced elastic modulus of Fe-rich particles.
- Wear Tests: Pin-on-disk wear tests under dry sliding conditions at room temperature, 150 ± 5°C, and 200 ± 5°C. Constant sliding speed of 0.1 m/s and a load of 15 N over a distance of 540 m. Mass loss measurement to calculate wear rate.
Analysis Methods:
- Quantitative Metallography: Image analysis to quantify sludge particle area fraction and analyze microstructural features.
- Statistical Analysis: Regression analysis to model wear rate as a function of sludge factor and temperature. Average hardness and wear rate values calculated from multiple measurements.
- Sludge Factor Calculation: Sludge factor (SF) calculated using Equation (1): Sludge Factor (SF) = (wt.%Fe × 1) + (wt.%Mn × 2) + (wt.%Cr × 3) [22,23].
- Oliver-Pharr Model: Oliver-Pharr model applied to nanoindentation data to evaluate hardness and Young's modulus of Fe-rich particles [28].
Research Subjects and Scope:
- Diecast AlSi9Cu3(Fe) alloys.
- Experimental alloys based on a secondary AlSi9Cu3(Fe) foundry alloy (Alloy 1).
- Three levels of Fe content, three levels of Mn content, and two levels of Cr content variation.
- Wear and hardness tests conducted up to 200°C.
- Microstructural analysis to characterize Fe-rich phases.
5. Main Research Results: Importance of Fe-rich Particles and Sludge Factor
This study demonstrated that increasing Fe, Mn, and Cr content in AlSi9Cu3(Fe) alloys effectively promotes the precipitation of primary and secondary Fe-rich particles. These particles exhibited polyhedral, blocky, and star-like morphologies. The sludge factor (SF) of the alloys increased with higher Fe, Mn, and Cr levels. Brinell hardness measurements and pin-on-disk wear tests revealed that while all diecast alloys showed reduced hardness and wear resistance at high temperatures, especially at 200°C, a greater amount of Fe-rich particles helped compensate for alloy softening at high temperatures.
Statistical/Qualitative Analysis Results:
- Sludge Fraction vs. Sludge Factor: "The graph in Figure 6 shows the sludge fraction of the experimental alloys as a function of their sludge factor; the sludge amount increases proportionally with the SF."
- Wear Rate vs. Sludge Fraction and Sludge Factor: "Figure 10a shows the average wear rate of the experimental AlSi9Cu3(Fe) alloys against the area fraction of sludge compounds for the different testing temperatures. The wear rate decreases progressively with the sludge fraction… the variations of the wear rate at different temperatures well fit with the sludge factor too (Figure 10b)."
- Brinell Hardness vs. Sludge Factor: "The average hardness values as a function of the sludge factor are plotted in Figure 9. At room temperature, the hardness ranges from 80 HB (Alloy 1 with a SF of 1.32) to 95 HB (Alloy 18 with SF of 2.90) with an increasing tendency by greater content of iron, manganese, and chromium."
- Hardness of Sludge Particles: "Sludge particles exhibit high hardness and reduced modulus, which are almost constant regardless of the iron, manganese, and chromium levels in the alloy… the different sludge morphology seems to not be reflected in the hardness value (Table 4)." The hardness of polyhedral sludge shape is 10.6 ± 1.5 GPa and star-like shape is 10.8 ± 1.0 GPa.
Data Interpretation:
The research results suggest that the sludge factor is a useful parameter for predicting the amount of Fe-rich particles and, consequently, the wear resistance of diecast AlSi9Cu3(Fe) alloys. Fe-rich particles, despite variations in morphology and chemical composition due to different alloying levels, consistently exhibit high hardness, contributing to overall wear resistance. While high temperatures reduce both hardness and wear resistance, increasing the volume fraction of Fe-rich particles through controlled additions of Fe, Mn, and Cr can effectively mitigate high-temperature softening and maintain improved wear performance.
- Figure Name List:
- Figure 1. Die cast plate showing the investigated location (dimensions in mm).
- Figure 2. OM micrograph of diecast base alloy (Alloy 1).
- Figure 3. SEM micrograph of base alloy; α₁-Fe and α₂-Fe particles are indicated.
- Figure 4. Bright field TEM micrographs of diecast AlSi9Cu3(Fe) alloy (Alloy 1) showing precipitation in the α-Al matrix: (a) before thermal exposure; after 30 min at (b) 150 °C and (c) 200 °C.
- Figure 5. Etched microstructure of (a) Alloy 1, SF = 1.32, (b) Alloy 13, SF = 1.82, (c) Alloy 15, SF = 2.21, and (d) Alloy 18, SF = 2.90; the Fe-rich particles appear dark.
- Figure 6. Sludge area fraction as function of sludge factor, SF.
- Figure 7. Evolution of the area fraction of sludge particles along the cross section of the plates die cast with different experimental alloys, here indicated with their sludge factor (SF), which was calculated according to Equation (1). The micrographs refer to (a) the casting surface and (b) the center of the plate (Alloy 14); the Fe-rich particles appear dark in the etched microstructures.
- Figure 8. SEM images of nanoindentation impressions in (a) polyhedral and (b) star-like sludge particles.
- Figure 9. Brinell hardness tendency as a function of the sludge factor, SF, in the diecast experimental AlSi9Cu3(Fe) alloys.
- Figure 10. Average wear rate at different temperatures as function of (a) the sludge area fraction and (b) the sludge factor in the diecast experimental AlSi9Cu3(Fe) alloys.
- Figure 11. Micrographs of fractured (a) α-Al₁₅(Fe,Mn,Cr)₃Si₂ particle and (b) β-Al₅FeSi platelet after wear testing.
- Figure 12. Effects of Fe, Mn, and Cr additions and test temperature on the friction coefficient at constant sliding distance. Alloys 1 (SF = 1.32) and 18 (SF = 2.90) with the lowest and highest sludge factors are taken as references.
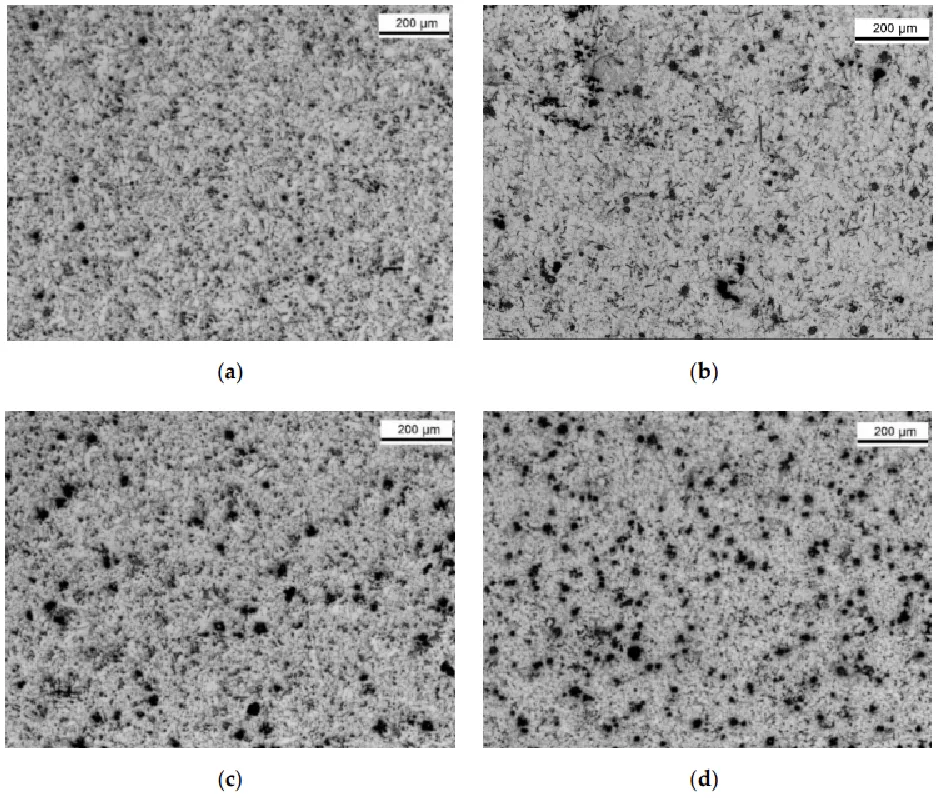
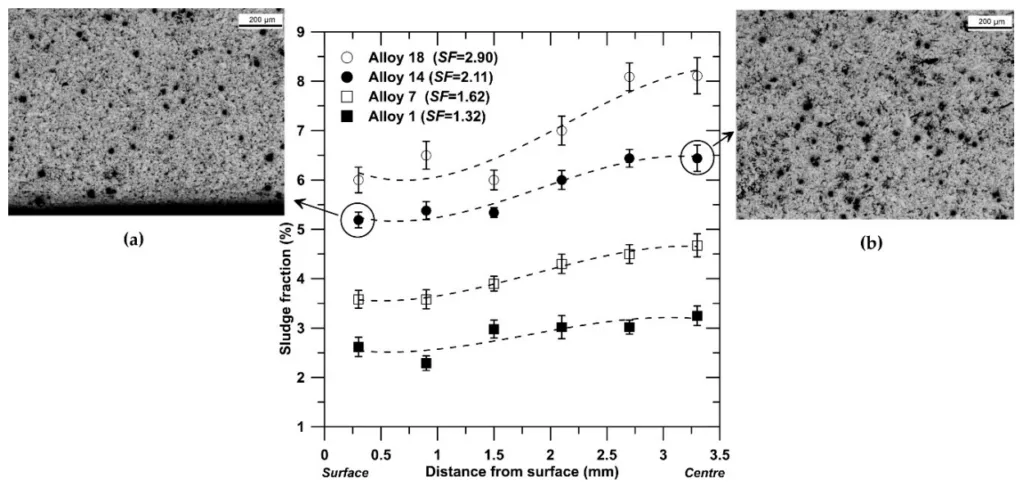
6. Conclusion and Discussion: New Possibilities for Designing High-Temperature Wear-Resistant Al Alloys
Summary of Main Results:
This research successfully designed and produced novel diecast AlSi9Cu3(Fe) alloys with varying amounts of Fe, Mn, and Cr. The study found that increasing Fe, Mn, and Cr content leads to a greater volume fraction of primary and secondary Fe-rich particles with polyhedral, blocky, and star-like morphologies. These Fe-rich particles contribute to increased hardness and improved wear resistance at room temperature. While elevated temperatures (up to 200°C) reduce the hardness and wear resistance of all alloys, alloys with higher sludge factors, indicating more Fe-rich particles, exhibited comparatively better performance at high temperatures. The sludge factor was identified as a useful parameter for predicting the wear rate of these alloys.
Academic Significance of the Research:
This research contributes to the fundamental understanding of how controlled additions of Fe, Mn, and Cr can be utilized to tailor the microstructure and enhance the wear resistance of diecast hypoeutectic Al-Si-Cu alloys, particularly for high-temperature applications. The study highlights the role of Fe-rich intermetallic particles in improving tribological properties and validates the sludge factor as a predictive tool in alloy design.
Practical Implications:
The findings of this study have practical implications for the die casting industry, especially in the automotive sector. By optimizing Fe, Mn, and Cr content in AlSi9Cu3(Fe) alloys, it is possible to produce high-pressure die-cast components with enhanced wear resistance and improved performance at elevated temperatures. This is crucial for components like pistons and cylinder liners in internal combustion engines, where both wear resistance and high-temperature strength are critical.
Limitations of the Research:
This study primarily focused on characterizing microstructure, hardness, and wear rate. A detailed investigation of worn surfaces and specific wear mechanisms was not conducted. Future research could explore these aspects for a more comprehensive understanding of wear behavior.
7. Future Follow-up Research Directions
Directions for Follow-up Research:
Future research should focus on a more in-depth analysis of wear mechanisms in these modified AlSi9Cu3(Fe) alloys, including detailed examination of worn surfaces and subsurface damage. Further optimization of alloy composition, particularly the ratios of Fe, Mn, and Cr, could be explored to maximize wear resistance and high-temperature performance for specific applications. Investigating long-term high-temperature performance, including creep and fatigue behavior, would also be valuable.
Areas Requiring Further Exploration:
Further exploration is needed to assess the cost-effectiveness of these alloying additions in industrial production. The influence of other alloying elements and heat treatments on the microstructure and properties of these alloys could also be investigated. Additionally, exploring the potential for further refinement of Fe-rich particle morphology and distribution to optimize their contribution to wear resistance is warranted.
8. References
- [1] Rajaram, G.; Kumaran, S.; Srinivasa Rao, T. High temperature tensile and wear behaviour of aluminum silicon alloy. Mater. Sci. Eng. A 2010, 528, 247–253.
- [2] Slattery, B.E.; Perry, T.; Edrisya, A. Microstructural evolution of a eutectic Al-Si engine subjected to severe running conditions. Mater. Sci. Eng. A 2009, 512, 76-81.
- [3] Slattery, B.E.; Edrisya, A.; Perry, T. Investigation of wear induced surface and subsurface deformation in a linerless Al-Si engine. Wear 2010, 269, 298–309.
- [4] Abouei, V.; Saghafian, H.; Shabestari, S.G.; Zarghami, M. Effect of Fe-rich intermetallics on the wear behavior of eutectic Al-Si piston alloy (LM13). Mater. Design 2010, 31, 3518-3524.
- [5] Zhang, J.; Alpas, A.T. Transition between mild and severe wear in aluminium alloys. Acta Mater. 1997, 45, 513-528.
- [6] Pauschitz, A.; Roy, M.; Franek, F. Mechanisms of sliding wear of metals and alloys at elevated temperatures. Tribol. Int. 2008, 41, 584-602.
- [7] Culliton, D.; Betts, A.J.; Kennedy, D. Impact of intermetallic precipitates on the tribological and/or corrosion performance of cast aluminium alloys: a short review. Int. J. Cast Metal. Res. 2013, 26, 65–71.
- [8] Lee, K.Y.; Lee, S.L.; Wu, C.T.; Chen, W.C.; Lin, J.C. Effects of T6 heat treatment on thermal stability and wear behaviour of Al-12.5Si-4.5Cu-1.0Mg alloy. Mater. Sci. Technol. 2012, 28, 639–643.
- [9] Tomida, S.; Nakata, K.; Shibata, S.; Zenkouji, I.; Saji, S. Improvement in wear resistance of hyper-eutectic Al-Si cast alloy by laser surface remelting. Surf. Coat. Tech. 2003, 169–170, 468-471.
- [10] Taghiabadi, R.; Ghasemi, H.M.; Shabestari, S.G. Effect of iron-rich intermetallics on the sliding wear behaviour of Al-Si alloys. Mater. Sci. Eng. A 2008, 490, 162-170.
- [11] Makhlouf, M.M.; Apelian, D.; Wang, L. Microstructure and Properties of Aluminium Die Casting Alloys, 1st ed.; North American Die Casting Association: Rosemont, IL, USA, 1998.
- [12] Dhiman, M.; Dwivedi, D.K.; Sehgal, R.; Bhat, I.K. Effect of iron (wt.%) on adhesive wear response of Al-12Si-1Cu-0.1Mg alloy in dry sliding conditions. Trans. Indian Inst. Met. 2008, 61, 451–456.
- [13] Cao, X.; Campbell, J. Morphology of β-Al5FeSi Phase in Al-Si Cast Alloys. Mater. Trans. 2006, 47, 1303-1312.
- [14] Mahta, M.; Emamy, M.; Cao, X.; Campbell, J. Overview of B-Al5FeSi Phase in Al-Si Alloys; Nova Science Publisher: New York, NY, USA, 2008; pp. 251-271.
- [15] Timelli, G.; Fiorese, E. Methods to neutralize the effects of iron in Al-Si foundry alloys. Metall. Ital. 2011, 103, 9-23.
- [16] Timelli, G.; Bonollo, F. The influence of Cr content on the microstructure and mechanical properties of AlSi9Cu3(Fe) die-casting alloys. Mater. Sci. Eng. A 2010, 528, 273-282.
- [17] Zahedi, H.; Emamy, M.; Razaghian, A.; Mahta, M.; Campbell, J.; Tiryakioğlu, M. The effect of Fe-rich intermetallics on the weibull distribution of tensile properties in a cast Al-5 Pct Si-3 Pct Cu-1 Pct Fe-0.3 Pct Mg alloy. Metall. Mater. Trans. A 2007, 38, 659-670.
- [18] Timelli, G.; Capuzzi, S.; Fabrizi, A. Precipitation of primary Fe-rich compounds in secondary AlSi9Cu3(Fe) alloys. J. Therm. Anal. Calorim. 2016, 123, 249-262.
- [19] Bidmeshki, C.; Aboudei, V.; Saghafian, H.; Shabestari, S.G.; Noghani, M.T. Effect of Mn addition on Fe-rich intermetallics morphology and dry sliding wear investigation of hypereutectic Al-17.5%Si alloy. J. Mater. Res. Technol. 2016, 5, 250-258.
- [20] Cao, X.; Campbell, J. Effect of precipitation of primary intermetallic compounds on mechanical properties of cast Al-11.5Si-0.4Mg alloy. AFS Trans. 2000, 108, 391–400.
- [21] Cao, X.; Campbell, J. The nucleation of Fe-rich phases on oxide films in Al-11.5Si-0.4Mg cast alloys. Metall. Mater. Trans. A 2003, 34, 1409-1420.
- [22] Gobrecht, J. Settling-out of Fe, Mn and Cr in Al-Si casting alloys. Giesserei 1975, 62, 263-266.
- [23] Jorstad, J.L. Understanding sludge. Die Cast. Eng. 1986, 30, 30-36.
- [24] Irish Standard, EN 1706:2010. Aluminium and Aluminium Alloys—Castings-Chemical Composition and Mechanical Properties; CEN-Comité Européen de Normalisation: Brussel, Belgium, 2007.
- [25] Timelli, G.; Ferraro, S.; Grosselle, F.; Bonollo, F.; Voltazza, F.; Capra, L. Mechanical and microstructural characterization of diecast aluminium alloys. Metall. Ital. 2011, 103, 5–17.
- [26] Timelli, G.; Grosselle, F.; Voltazza, F.; Della Corte, E. A new reference die for mechanical properties evaluation in diecasting, Part 1-Design and process optimization. In Proceedings of the 4th International Conference High Tech Die Casting (HTDC2008), Montichiari (BS), Italy, 9-10 April 2008; Italian Association of Metallurgy (AIM): Milan, Italy, 2008.
- [27] ASTM E10-15a. Standard Test Method for Brinell Hardness of Metallic Materials; ASTM International: West Conshohocken, PA, USA, 2015.
- [28] Oliver, W.C.; Pharr, G.M. An improved technique for determining hardness and elastic modulus using load and displacement sensing indentation experiments. J. Mater. Res. 1992, 7, 1564-1583.
- [29] Ferraro, S.; Fabrizi, A.; Timelli, G. Evolution of sludge particles in secondary die-cast aluminum alloys as function of Fe, Mn and Cr contents. Mater. Chem. Phys. 2015, 153, 168–179.
- [30] Flemings, M.C. Behavior of metal alloys in the semisolid state. Metall. Trans. A 1991, 22A, 957-981.
- [31] Bäckerud, L.; Chai, G.; Tamminen, J. Solidification Characteristics of Aluminum Alloys, 1st ed.; American Foundrymen's Society Inc.: Des Plaines, IL, USA, 1990; Volume 2, pp. 201-204.
- [32] Helenius, R.; Lohne, O.; Arnberg, L.; Laukli, H.I. The heat transfer during filling of a high-pressure die-casting shot sleeve. Mater. Sci. Eng. A 2005, 413-414, 52-55.
- [33] Guo, Z.-P.; Xiong, S.-M.; Liu, B.-C.; Li, M.; Allison, J. Effect of process parameters, casting thickness, and alloys on the interfacial heat-transfer coefficient in the high-pressure die-casting process. Metall. Mater. Trans. A 2008, 39A, 2896-2905.
- [34] Shabestari, S.G. The effect of iron and manganese on the formation of intermetallic compounds in aluminum-silicon alloys. Mater. Sci. Eng. A 2004, 383, 289–298.
- [35] Mondolfo, L.F. Aluminium Alloys: Structure and Properties; Butterworth-Heinemann: Oxford, UK, 1976.
- [36] Fabrizi, A.; Ferraro, S.; Timelli, G. The influence of Fe, Mn and Cr additions on the formation of iron-rich intermetallic phases in an Al-Si die-casting alloy. In Shape Casting: 5th International Symposium 2014; Tiryakioğlu, M., Campbell, J., Byczynski, G., Eds.; Minerals, Metals and Materials Society: Warrendale, PA, USA, 2014; pp. 277-284. ISBN 9781118888186.
- [37] Timelli, G.; Fabrizi, A.; Capuzzi, S.; Bonollo, F.; Ferraro, S. The role of Cr additions and Fe-rich compounds on microstructural features and impact toughness of AlSi9Cu3(Fe) diecasting alloys. Mater. Sci. Eng. A 2014, 603, 58-68.
- [38] Lombardi, A.; D'Elia, F.; Ravindran, C.; Murty, B.S.; MacKay, R. Analysis of the secondary phases in the microstructure of 319 type Al alloy engine blocks using electron microscopy and nanoindentation. Trans. Indian Inst. Met. 2011, 64, 7-11.
- [39] Chen, C.L.; Richter, A.; Thomson, R.C. Mechanical properties of intermetallic phases in multi-component Al-Si alloys using nanoindentation. Intermetallics 2010, 17, 634-641.
- [40] Fischer-Cripps, A.C. Nanoindentation, 3rd ed.; Springer: New York, NY, USA, 2011.
- [41] Ferraro, S.; Timelli, G. Influence of sludge particles on the tensile properties of die-cast secondary aluminum alloys. Metall. Mater. Trans. B 2015, 46, 1022–1034.
- [42] Scott, G.D.; Shabel, B.S.; Morales, A. Aluminum Alloy Suitable for Pistons. U.S. Patent 5162065, 10 November 1992.
- [43] Cho, Y.-H.; Joo, D.-H.; Kim, C.-H.; Lee, H.-C. The effect of alloy addition on the high temperature properties of over-aged Al-Si(CuNiMg) cast alloys. Mater. Sci. Forum 2006, 519–521, 461-466.
- [44] Qian, Z.; Liu, X.; Zhao, D.; Zhang, G. Effects of trace Mn addition on the elevated temperature tensile strength and microstructure of a low-iron Al-Si piston alloy. Mater. Lett. 2008, 62, 2146-2149.
- [45] Mayer, H.; Papakyriacou, M.; Zettl, B.; Vacic, S. Endurance limit and threshold stress intensity of die cast magnesium and aluminium alloys at elevated temperatures. Int. J. Fatigue 2005, 27, 1076–1088.
- [46] Rohatgi, P.K.; Riu, Y.; Ray, S. Friction, Lubrication and Wear Technology; American Society for Metals: Metals Park, OH, USA, 1992; p. 85.
- [47] Mrówka-Nowotnik, G. The effect of intermetallics on the fracture mechanism in AlSi1MgMn alloy. J. Achiev. Mater. Manuf. Eng. 2008, 30, 35-42.
- [48] Campbell, J. An overview of the effects of bifilms on the structure and properties of cast alloys. Metall. Mater. Trans. B 2006, 37B, 857-863.
- [49] Gariboldi, E.; Lemke, J.N.; Ozhoga-Maslovskaja, O.; Timelli, G.; Bonollo, F. High temperature behaviour of 46000, 46100, 47100 Al die cast parts. Metall. Ital. 2016, 108, 49–52.
- [50] Wang, L.; He, Y.; Zhou, J.; Duszczyk, J. Effect of temperature on the frictional behaviour of an aluminium alloy sliding against steel during ball-on-disc tests. Tribol. Int. 2010, 43, 299-306.
- [51] Kamminga, J.D.; Janssen, G.C.A.M. Experimental discrimination of plowing friction and shear friction. Tribol. Lett. 2007, 25, 149-152.
- [52] Farhat, Z.N. Contribution of crystallographic texturing to the sliding friction behaviour of fcc and hcp metals. Wear 2001, 250, 401-408.
9. Copyright
- This material is a summary based on the paper by Giulio Timelli et al., titled [Design of Wear-Resistant Diecast AlSi9Cu3(Fe) Alloys for High-Temperature Components].
- Paper Source: doi:10.3390/met10010055
This material is summarized based on the above paper, and unauthorized use for commercial purposes is prohibited.
Copyright © 2025 CASTMAN. All rights reserved.