This article introduces the paper"Exploring the concept of castability in magnesium die-casting alloys" published in the Journal of Magnesium and Alloys in 2021. The paper, authored by J.P. Weiler, delves into the multifaceted concept of castability within the magnesium die-casting industry, a critical aspect for developing advanced alloys and optimizing manufacturing processes. This summary is structured to mirror the original paper, providing a detailed yet accessible breakdown of its key findings and implications.
1. Overview:
- Title: Exploring the concept of castability in magnesium die-casting alloys
- Author: J.P. Weiler
- Publication Year: 2021
- Publishing Journal/Academic Society: Journal of Magnesium and Alloys
- Keywords: magnesium die-casting, castability, magnesium alloys, alloying elements, literature review
![Fig. 1. 2017 Chrysler Pacifica showing the liftgate assembly highlighted by a magnesium die-cast inner [4] (Copyright 2018 by FCA. Used with permission. Chrysler is a registered trademark of FCA US LLC).](https://castman.co.kr/wp-content/uploads/Fig.-1.-2017-Chrysler-Pacifica-showing-the-liftgate-assembly-highlighted-by-a-magnesium-die-cast-inner-4-Copyright-2018-by-FCA.-Used-with-permission.-Chrysler-is-a-registered-trademark-of-FCA-US-LLC.webp)
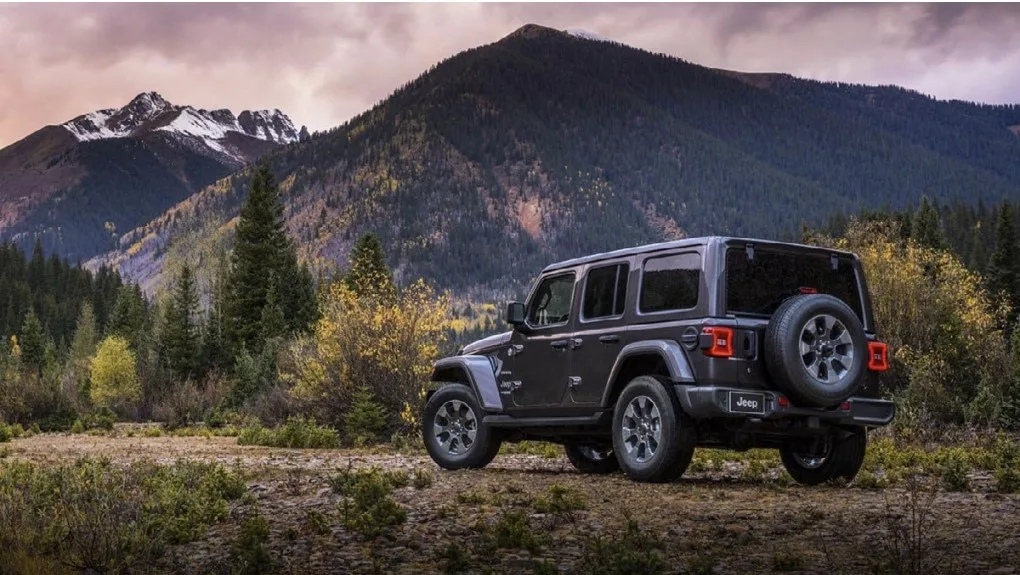
2. Research Background:
- Social/Academic Context of the Research Topic: The utilization of magnesium alloy products has seen a significant surge in recent years, driven by the demand for weight reduction across various industries. Magnesium die-casting stands out as a primary application, serving the automotive, aviation, and 3C (computers, communication, and consumer electronics) sectors. As noted in the paper, the production of pure magnesium in China increased by 20% between 2015 and 2017 [1], and consumption rose by 12% in the same period. Die-casting of magnesium alloys accounts for a substantial portion of primary magnesium use, estimated at 36-40% in 2017, with a projected increase by 25% from 2015 levels, anticipated to grow further by 2027 [1, 2]. High-volume applications in the automotive industry, such as the Chrysler Pacifica rear liftgate inner casting (Fig. 1), Jeep Wrangler rear swinggate inner casting (Fig. 2), Honda Odyssey and Acura RDX steering hanger beams, and Ford F-series radiator support castings, exemplify this trend. In 2017 alone, these applications accounted for over 1.5 million vehicle sales in North America [3].
- Limitations of Existing Research: Despite the growing importance of magnesium die-casting, the paper highlights a concerning trend: a decrease in peer-reviewed publications focusing on magnesium die-casting technology. Keyword searches using Scopus [5] reveal a decline of over 50% in such publications since a peak in 2005 (Fig. 3). Further keyword analysis indicates that while 'microstructure' and 'mechanical properties' are frequently addressed in publications since 2006 (30% and 25% respectively), the term 'castability' appears in a mere 2% of these publications. This scarcity of research is particularly noteworthy because, as the paper emphasizes, die-casting is the primary magnesium-based use of magnesium metal. A significant gap exists in the well-defined understanding and quantitative assessment of "castability" as a material property in magnesium die-casting.
- Necessity of the Research: The paper underscores the critical need for a focused investigation into the concept of castability in magnesium die-cast alloys. Given the dominance of die-casting in magnesium applications and the relative lack of attention to castability in recent research, there is a clear necessity to explore this concept. Understanding castability is crucial for the continued development of magnesium alloys tailored for innovative applications and improved performance characteristics. This research aims to address this gap by reviewing existing literature, defining castability, and examining the influence of alloying elements.
3. Research Purpose and Research Questions:
- Research Purpose: The primary purpose of this research is to investigate and clarify the concept of "castability" as it applies to magnesium die-cast alloys. The paper aims to provide a comprehensive understanding of this often-cited but vaguely defined term within the context of magnesium die-casting.
- Key Research Questions: The research is structured around several key questions:
- How is "castability" defined and evaluated in the context of magnesium die-casting alloys?
- What is the historical perspective on the concept of castability in magnesium alloy development?
- What is the impact of different alloying elements on the castability of magnesium alloys?
- What are the potential directions for future research and development related to castability in magnesium die-casting?
- Research Hypotheses: While the paper does not explicitly state research hypotheses in a traditional format, it operates under the implicit understanding that:
- "Castability" is a complex, multi-faceted concept rather than a simple, quantifiable material property.
- The perceived "castability" of magnesium alloys is significantly influenced by alloy composition, particularly the type and concentration of alloying elements.
- A deeper understanding of castability is essential for the design and development of next-generation magnesium die-casting alloys with enhanced performance and broader applications.
4. Research Methodology:
- Research Design: This research employs a comprehensive literature review approach. The author systematically examines existing publications to synthesize knowledge and identify trends related to castability in magnesium die-casting.
- Data Collection Method: The data collection process involved keyword searches and surveys of publications from specific sources:
- Scopus Service [5]: Used for broader keyword searches to analyze publication trends in magnesium die-casting technology and the frequency of terms like 'microstructure', 'mechanical properties', and 'castability'.
- TMS Magnesium Technology Symposium Papers (2002-2019): Annual publications from this symposium, dedicated to magnesium technology, were reviewed.
- Journal of Magnesium and Alloys (2013-2019): Publications from this journal, focused on magnesium and its alloys, were also included in the review.
- Keyword Survey for 'Castability': Papers from the above sources were surveyed for the occurrence of the keyword 'castability' to assess the focus on this topic over time. Papers with more than 6 occurrences of 'castability' were classified as focusing on this topic.
- Keyword Search for 'Norsk' and 'Noranda': A keyword search for 'Norsk' and 'Noranda' was conducted to investigate the influence of the departure of these companies from the magnesium industry on research trends.
- Analysis Method: The analysis methods employed in the paper are both quantitative and qualitative:
- Quantitative Analysis: Statistical analysis of publication numbers and keyword frequencies over time, as presented in Figures 3, 4, and 5. Calculation of ratios and percentages to illustrate trends in castability research.
- Qualitative Analysis: Detailed review and synthesis of literature definitions of castability, historical accounts of castability in magnesium alloy development, and descriptions of the effects of various alloying elements on castability. Interpretation of data from figures and tables presented in cited literature.
- Research Subjects and Scope: The research focuses on peer-reviewed publications specifically addressing the castability of magnesium die-castings or die-cast alloys. The scope is limited to literature available in the selected databases and publications, primarily covering the period from the early 2000s to 2019, with some historical context extending back to the early days of magnesium die-casting.
5. Main Research Results:
- Key Research Results: The literature review yielded several key findings regarding castability in magnesium die-casting alloys:
- Decline in Castability Research: There has been a noticeable decrease in the number of publications focusing on magnesium die-casting technology and, more specifically, on the concept of castability over the past 15 years (Fig. 3, 4, 5). The percentage of papers focusing on castability has decreased from over 5% in 2002-2004 to less than 1% in 2015-2019 (Fig. 5). This decline may be partly attributed to the departure of key industry players like Dow Chemical, Noranda, and Norsk Hydro from the magnesium business [6].
- Castability Definition is Subjective: "Castability" is not a well-defined, quantitative material property. Instead, it is a somewhat subjective term with various descriptions in the literature. Generally, castability is defined as "the ability to form a product from a die pattern with satisfactory results" [11, 12]. Specific aspects of castability in magnesium alloys include:
- Die Filling Ability [11, 13-15]
- Fluidity in the Molten State [11, 16, 17]
- Resistance to Hot Tearing [11, 13, 14, 16, 18]
- Consistency of Chemistry [14, 16, 18, 19]
- Resistance to Die Sticking/Soldering [11, 15, 18]
- Feeding Ability (to compensate for solidification shrinkage) [11, 14-16, 18]
However, not all these characteristics are easily quantifiable.
- AZ91 as Castability Benchmark: The AZ91 alloy is frequently used as a baseline for castability evaluations [14, 18] and is generally considered to possess the greatest castability among common magnesium die-casting alloys [12, 13, 19].
- Historical Context of Castability: Historically, magnesium alloys were recognized for not soldering or sticking to dies like aluminum alloys [20, 22-24]. Early research identified aluminum and zinc as key alloying elements affecting castability [25, 26]. The Mg-Al-Zn system was developed for die-casting due to its good flow properties [22]. AZ91 alloy composition (Mg-Al-Zn family) was optimized to maximize cast product quality [20, 21, 26]. Later, AM60 was developed for automotive wheels requiring toughness, even if reportedly less castable than AZ91 [21, 30]. Subsequent alloy developments like AS41 and AE42 aimed to maintain AZ91-level castability while improving creep resistance [21]. Examples of automotive applications using advanced magnesium alloys include the Corvette Z06 front crossmember (AE44, Fig. 6) and Ford Mustang Shelby GT500 strut brace (AE44, Fig. 7).
- Effect of Alloying Elements on Castability: The paper systematically reviews the impact of various alloying elements on magnesium alloy castability:
- Aluminum: Improves mold filling and fluidity up to ~10% content [11, 14, 16, 25]. Reduces viscosity and surface tension [12]. Improves feeding properties but can increase shrinkage porosity [11, 16]. Hot tearing risk at 1-2% Al [12, 14]. Soldering issues increase above 7% Al [12, 14].
- Zinc: Improves fluidity up to 3% [11, 12, 16, 38]. Above 3%, hot cracking and microporosity can occur [16, 25, 38]. Hot tearing increases at 6% Zn with low Al [16, 40] (Fig. 12).
- Calcium: First used to improve creep resistance [21]. Can cause die-sticking and hot cracking [21]. Between 0.3-1.5% in AM50, issues like sinks, cold shuts, solder drag, die-sticking, and cracking are observed [15, 18, 38, 41]. Calcium additions generally reduce castability [12].
- Silicon: Used for high-temperature creep strength [21]. Increases susceptibility to hot tearing but also fluidity of AM60 [12]. Increases liquidus temperature [16]. With lower Al, reduces fluidity and castability [16]. Overall, silicon can increase castability but may decrease it in low-Al alloys [12, 16].
- Rare Earths (RE): Used to improve creep strength [21]. Can improve castability [12]. Improves fluidity, especially at lower Al contents [12, 16]. Effect on hot tearing varies [12, 16, 28]. Above 4% RE, alloys become brittle [28]. REs increase oxidation susceptibility [16]. Lanthanum can reduce hot tearing [13, 28].
- Strontium: Used as RE replacement for creep strength [31]. Small amounts (<0.5%) modify intermetallics [33, 43]. 0.5% Sr in AZ91 increases fluidity [42]. Combined with calcium, strontium improves creep strength [41, 43]. Specific content ranges needed to avoid embrittlement and die sticking [43].
- Tin: Improves castability and reduces die sticking above 0.3% [46]. 0.5% tin in AZ91 improves fluidity but decreases it above 1% [47]. Can improve fluidity in Mg-Zn-Al alloys but decrease it at higher Zn levels [49]. 0.2% tin in Mg-Al-Ca alloys reduces casting cracking [48]. 0.5% tin improves hot tearing resistance in AZ91, but higher contents increase it [47].
- Manganese: Primarily for corrosion inhibition [25]. Limited castability research. Negligible effect on flow length with 0.56% calcium [51]. Increased soldering on H13 die steel at higher Mn content [52].
- Compositional Ranges for Optimum Castability: Based on the literature, the paper summarizes compositional ranges for optimum castability for various alloying elements (Fig. 13). Aluminum, REs, and Zinc have relatively broad ranges, while Manganese and Calcium have narrow ranges. Strontium, Silicon, and Tin have ranges around 1%.
- Statistical/Qualitative Analysis Results:
- Figure 3. Number of peer-reviewed publications focusing on magnesium die-casting technology published annually from 1995 to 2019 [5]: This figure visually demonstrates the decline in publications related to magnesium die-casting technology after a peak around 2005.
- Figure 4. Literature keyword survey of the occurrences of 'castability' per published paper as a function of year. The literature survey was completed using Magnesium Technology volumes from 2002 to 2019, and Journal of Magnesium Alloys volumes from 2013 to 2019: This figure shows that the frequency of the keyword 'castability' in publications peaked in 2002 and then significantly decreased, remaining low since 2009.
- Figure 5. Percentage of papers with magnesium castability focus as a function of year published in Magnesium Technology volumes from 2002 to 2019, and Journal of Magnesium Alloys volumes from 2013 to 2019: This figure illustrates the percentage of papers specifically focused on magnesium castability, showing a decline from over 5% in the early 2000s to less than 1% in recent years.
- Figure 8. Creep performance vs. castability representation for several die-cast magnesium alloys as given by Gibson et al. [27]: This figure plots creep performance against castability rating for various magnesium alloys, visually representing the trade-offs between these properties. AZ91D (labeled as 1) is positioned towards the higher castability end.
- Figure 9. Creep performance (at 150°C) vs. castability index for several die-cast magnesium alloys as given by Easton et al. [29]: Similar to Figure 8, this figure presents a scatter plot of creep performance versus castability index for different magnesium alloys, again highlighting AZ91's favorable castability.
- Figure 13. Compositional ranges for optimum castability of magnesium alloys for aluminum, rare-earths, zinc, strontium, silicon, tin, manganese and calcium, calculated from the literature sources cited here: This bar chart summarizes the optimal compositional ranges for different alloying elements to achieve the best castability in magnesium alloys, based on the reviewed literature.
![Fig. 3. Number of peer-reviewed publications focusing on magnesium diecasting technology published annually from 1995 to 2019 [5].](https://castman.co.kr/wp-content/uploads/image-149-png.webp)

![Fig. 7. 2020 Ford Mustang Shelby GT500 with cast Magnesium strut brace [37]. (Copyright 2019 by Detroit Free Press. Used with Permission.)](https://castman.co.kr/wp-content/uploads/Fig.-7.-2020-Ford-Mustang-Shelby-GT500-with-cast-Magnesium-strut-brace-37.-Copyright-2019-by-Detroit-Free-Press.-Used-with-Permission.webp)
![Fig. 8. Creep performance vs. castability representation for several die-cast
magnesium alloys as given by Gibson et al. [27]. In the Fig. 1: AZ91D,
2: AS21X, 3: MRI153M, 4: AJ62X, 5: AE42, 6: AJ52X, 7: ACM522, 8:
AX52J, 9: MRI230D. (Copyright 2006 by The Minerals, Metals and Materials Society. Used with permission).](https://castman.co.kr/wp-content/uploads/Fig.-8.-Creep-performance-vs.-castability-representation-for-several-die-cast-magnesium-alloys-as-given-by-Gibson-et-al.-27.webp)
![Fig. 9. Creep performance (at 150◦C) vs. castability index for several diecast magnesium alloys as given by Easton et al. [29]. (Copyright 2017 by
The Minerals, Metals and Materials Society. Used with permission).](https://castman.co.kr/wp-content/uploads/Fig.-9.-Creep-performance-at-150◦C-vs.-castability-index-for-several-diecast-magnesium-alloys-as-given-by-Easton-et-al.-29.webp)
![Fig. 11. Solid solubility of various rare earth elements as a function of increasing temperature [39]. (Copyright 2008, by the Polish Academy of Sciences’ Institute of Metallurgy and Material Science. Used with Permission.).](https://castman.co.kr/wp-content/uploads/image-150-png.webp)
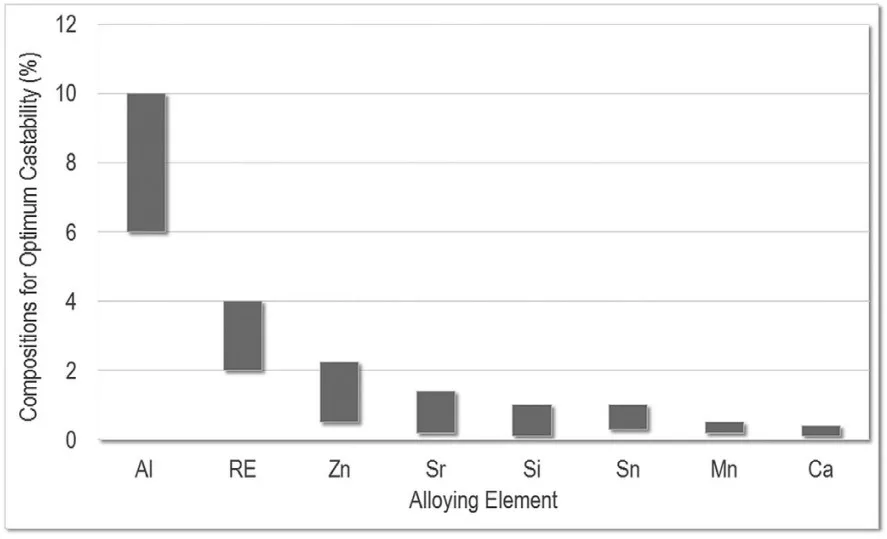
- Data Interpretation: The data consistently points to a reduced focus on castability research in magnesium die-casting despite its critical importance. "Castability" is confirmed as a complex and subjective concept, influenced by numerous factors, especially alloy composition. AZ91 remains the benchmark for castability. Alloying elements have diverse and often complex effects on castability, requiring careful consideration in alloy design.
6. Conclusion and Discussion:
- Summary of Main Results: This paper effectively demonstrates a decline in research focused on castability in magnesium die-casting over the last 15 years. It clarifies that castability is a complex, subjective concept encompassing various aspects of the die-casting process. AZ91 alloy is consistently recognized as having optimum castability. The paper provides a detailed overview of how different alloying elements (aluminum, zinc, calcium, silicon, rare earths, strontium, tin, and manganese) affect castability, offering valuable insights for alloy development.
- Academic Significance of the Research: This research holds significant academic value by highlighting a gap in current research trends. It provides a structured and comprehensive literature review that consolidates existing knowledge on castability in magnesium die-casting. The paper's analysis of the definition, history, and influencing factors of castability contributes to a better understanding of this crucial concept within materials science and engineering.
- Practical Implications: The practical implications of this research are substantial for the magnesium die-casting industry. The detailed summary of alloying element effects on castability serves as a valuable guide for alloy designers and process engineers. By understanding how different elements impact fluidity, hot tearing, die sticking, and other castability aspects, engineers can make informed decisions in developing new alloys and optimizing die-casting processes for improved manufacturability and component performance. The paper emphasizes the need to consider castability as a key factor in alloy development, especially for demanding applications in the automotive and other sectors.
- Limitations of the Research: The primary limitation of this research is inherent to its literature review methodology. The definition and evaluation of "castability" remain somewhat subjective, as reflected in the reviewed literature. The paper relies on interpretations and conclusions drawn from existing publications, which may have varying methodologies and perspectives. Further research may benefit from developing more standardized and quantitative methods for assessing castability.
7. Future Follow-up Research:
- Directions for Follow-up Research: The paper suggests several directions for future research:
- Holistic Alloy Development: Future alloy development should adopt a holistic approach, considering castability alongside mechanical, physical, and corrosion properties, as well as raw material cost, environmental impact, production efficiency, and recyclability. Developing alloys that optimize mechanical properties without compromising castability is crucial.
- New Alloy Systems: Exploration of novel alloy systems that combine different alloying elements to achieve a synergistic effect on both performance and castability is encouraged. This includes investigating combinations that meet end-application requirements while also ensuring good manufacturability for the die-caster.
- Areas Requiring Further Exploration: Further research is needed to:
- Develop a more quantitative definition and evaluation method for castability. Moving beyond subjective assessments to more objective and measurable metrics would be beneficial for alloy development and process optimization.
- Investigate the complex interactions between multiple alloying elements on castability. The effects of alloying elements are not always linear or additive, and understanding these interactions is crucial for designing advanced alloys.
8. References:
- [1] L. Ruhai, Evolution of the Chinese magnesium industry in 2017, in: Proceedings of the 75th Annual World Magnesium Conference, IMA, St. Paul, 2018.
- [2] A. Clark, 2017 global primary magnesium supply demand balance and outlook, in: Proceedings of the 75th Annual World Magnesium Conference, IMA, St. Paul, 2018.
- [3] Automotive News, US Sales Report. https://www.autonews.com/, 2020 (accessed 18 January 2020).
- [4] FCA North America media, 2020 Products. https://media.fcanorthamerica.com/homepage.do;jsessionid=060571A9B3C7C6C3FF0CB95CA92358B6?mid=1, 2020 (accessed 2 February 2020).
- [5] Elsevier, Scopus document search, https://www.scopus.com/home.uri, 2019 (accessed 14 December 2019).
- [6] G. Patzer, TMS, Warrendale, 2010, pp. 85-90.
- [7] E.N. Brandt, We Called it Mag-nificent: Dow Chemical and Magnesium, 1916-1998. East Lansing, Michigan State University Press, 2013.
- [8] J. Li, R. Chen, Y. Ma, W. Ke, J. Magnes. Alloy. 1 (2013) 346-351, doi:10.1016/j.jma.2013.12.001.
- [9] Y. Huang, H. Dieringa, K.U. Kainer, N. Hort, J. Magnes. Alloy. 2 (2014) 124-132, doi:10.1016/j.jma.2014.03.003.
- [10] M.J. Shen, X.J. Wang, M.F. Zhang, B.H. Zhang, M.Y. Zheng, K. Wu, J. Magnes. Alloy. 3 (2015) 155-161, doi:10.1016/j.jma.2015.03.001.
- [11] P. Bakke, K. Pettersen, H. Westengen, TMS, Warrendale, 2003, pp. 171-176.
- [12] A.L. Bowles, Q. Han, J.A. Horton, TMS, Warrendale, 2005, pp. 99-104.
- [13] J.-M. Kim, S.-J. Lee, Int. J. Metalcast. 9 (2015) 15-21, doi:10.1007/BF03355619.
- [14] K. Strobel, M.A. Easton, V. Tyagi, M. Murray, M.A. Gibson, G. Savage, T.B. Abbott, Int. J. Cast Met. Res. 23 (2010) 81-91, doi:10.1179/136404609X12535244328332.
- [15] B.R. Powell, A.A. Luo, B.L. Tiwari, V. Rezhets, TMS, Warrendale, 2002, pp. 123-129.
- [16] A. Luo, M.O. Pekguleryuz, J. Mater. Sci. 29 (1994) 5259-5271, doi:10.1007/BF01171534.
- [17] S.S. Khan, N. Hort, I. Steinbach, S. Schmauder, TMS, Warrendale, 2008, pp. 197-202.
- [18] J. Berkmortel, H. Hu, J.E. Kearns, J.E. Allison, Die Castability Assessment of Magnesium Alloys for High Temperature Applications: Part 1 of 2, SAE, 2000 Technical Paper 2000-01-1119, doi:10.4271/2000-01-1119.
- [19] P. Bakke, H. Westengen, S. Sannes, D. Albright, Powertrain Components Opportunities for the Die Cast AE Family of Alloys, SAE, 2004 Technical Paper 2004-01-0655, doi: 10.4271/2004-01-0655.
- [20] S.C. Erickson, Magnesium: A Proven Material For Light Weight Automotive Die Castings, SAE, 1977 Technical Paper 770323, doi:10.4271/770323.
- [21] J.F. King, Werkstoff-Informationsgesellschaft mbH, Frankfurt, 1998, pp. 37-47.
- [22] A. Beck, The Technology of Magnesium and its Alloys (English translation), F.A. Hughes and Co. Ltd., London, 1943.
- [23] J.D. Hanawalt, J.K. Glaza, New Applications and Developments of Magnesium Alloys in the Automotive Industry, SAE, 1952 Technical Paper 520090, doi: 10.4271/520090.
- [24] J.G. Mezoff, Magnesium for Automobiles, in Perspective, SAE, 1980 Technical Paper 800417, doi:10.4271/800417.
- [25] W.K. Zinszer, Trans. Kans. Acad. Sci. 46 (1943) 161-163.
- [26] J.A. Gann, Magnesium Industry's Lightest Structural Metal, SAE, 1931 Technical Paper 310044, doi:10.4271/310044.
- [27] M.A. Gibson, C.J. Bettles, M.T. Murray, G.L. Dunlop, TMS, Warrendale, 2006, pp. 327-331.
- [28] M. Easton, M.A. Gibson, S. Zhu, T. Abbott, J.-F. Nie, C.J. Bettles, G. Savage, TMS, Warrendale, 2018, pp. 329-336.
- [29] M. Easton, S. Zhu, M. Gibson, T. Abbott, H.W. Ang, X. Chen, N. Birbilis, G. Savage, TMS, Warrendale, 2017, pp. 123-129.
- [30] S.L. Couling, Met. Eng. Q. (1972) 7-13 May.
- [31] M.O. Pekguleryuz, E. Baril, TMS, Warrendale, 2001, pp. 119-125.
- [32] A.A. Luo, B.R. Powell, TMS, Warrendale, 2001, pp. 137-144.
- [33] E. Aghion, B. Bronfin, H. Friedrich, Z. Rubinovich, TMS, Warrendale, 2004, pp. 167-172.
- [34] J. Greiner, C. Doerr, H. Zauerz, M. Graeve, The New "7G-TRONIC" of Mercedez-Benz: Innovative Transmission Technology for Better Driving Performance, Comfort and Fuel Economy, SAE, 2001 Technical Paper 2004-01-0649, doi: 10.4271/2004-01-0649.
- [35] E. Baril, P. Labelle, A. Fischerworring-Bunk, AJ (Mg-Al-Sr) Alloy System Used for New Engine Block, SAE, 2004 Technical Paper 2004-01-0659, doi:10.4271/2004-01-0659.
- [36] GM Corporate Newsroom, Fiberglass to Carbon Fiber: Corvette's Lightweight Legacy. https://media.gm.com/media/us/en/gm/news.detail.html/content/Pages/news/us/en/2012/Aug/0816_corvette.html., 2012 (accessed 5 February 2020).
- [37] M. Phelan, 760-Horsepower 2020 Ford Mustang Shelby GT500 Strikes Like Lightning. https://www.freep.com/story/money/cars/mark-phelan/2019/10/29/ford-mustang-2020-shelby-gt-500-driving-impressions/2486253001/, 2019 (accessed 7 February 2020).
- [38] M.O. Pekguleryuz, M.M. Avedesian, J. Jpn. Inst. Light Met. 42 (1992) 679-686.
- [39] L.L. Rokhin, Arch. Metall. Mater. 52 (2007) 5-11.
- [40] M. Easton, T. Abbott, J.-F. Nie, G. Savage, TMS, Warrendale, 2008, pp. 323-328.
- [41] Y. Nakaura, A. Watanabe, K. Ohori, Mater. Trans. 47 (2006) 1031-1039, doi:10.2320/matertrans.47.1031.
- [42] H.L. Zhao, S.K. Guan, F.Y. Zheng, J. Mater. Res. 22 (2007) 2423-2428, doi:10.1557/jmr.2007.0331.
- [43] B. Bronfin, E. Aghion, F. Von Buch, S. Schumann, Creep Resistant Magnesium Alloys With Improved Castability, US Patent #7,169,240 B2, 2007.
- [44] A.A. Luo, Int. Mater. Rev. 49 (2004) 13-30, doi:10.1179/095066004225010497.
- [45] P. Bakke, K. Pettersen, D. Albright, TMS, Warrendale, 2004, pp. 289-296.
- [46] B. Bronfin, E. Aghion, F. Von Buch, S. Schumann, M. Katzir, High Strength Creep Resistant Magnesium Alloys, US Patent #7, 041,179 B2, 2006.
- [47] Y. Turen, Mater. Des. 49 (2013) 1009-1015, doi:10.1016/j.matdes.2013.02.037.
- [48] H. Kato, K. Kitayama, K. Hibi, H. Kawabata, Mater. Trans. 57 (2016) 1633-1638, doi:10.2320/matertrans.M2016139.
- [49] M. Yang, F. Pan, Mater. Des. 31 (2010) 68-75, doi:10.1016/j.matdes.2009.07.018.
- [50] J. Zhou, H.R.J. Nodooshan, D. Li, X. Zeng, W. Ding, Met. 9 (2019) 113-127, doi: 10.3390/met9020113.
- [51] H.-S. Kim, T.-G. Kim, Solid State Phenom. 118 (2006) 485-490, doi:10.4028/www.scientific.net/SSP.118.485.
- [52] C. Tang, Soldering in Magnesium High Pressure Die Casting and its Prevention by Surface Engineering Ph.D. Thesis, Swinburne University of Technology, Hawthorn, 2007.
9. Copyright:
- This material is J.P. Weiler's paper: Based on Exploring the concept of castability in magnesium die-casting alloys.
- Paper Source: https://doi.org/10.1016/j.jma.2020.05.008
This material was summarized based on the above paper, and unauthorized use for commercial purposes is prohibited.
Copyright © 2025 CASTMAN. All rights reserved.