This article introduces the paper ['3D characterization of pores expansion behavior in high pressure die castings during heat treatment'] presented at the ['SSRN']
1. Overview:
- Title: 3D characterization of pores expansion behavior in high pressure die castings during heat treatment
- Author: Yihu MA, Wenbo YU, Zihao YUAN, Chaosheng MA, Wantong Chen, Mengwu WU, Shoumei XIONG
- Publication Year: Preprint
- Publishing Journal/Academic Society: SSRN
- Keywords: High pressure die casting; Pores expansion; Heat treatment; 3D reconstruction
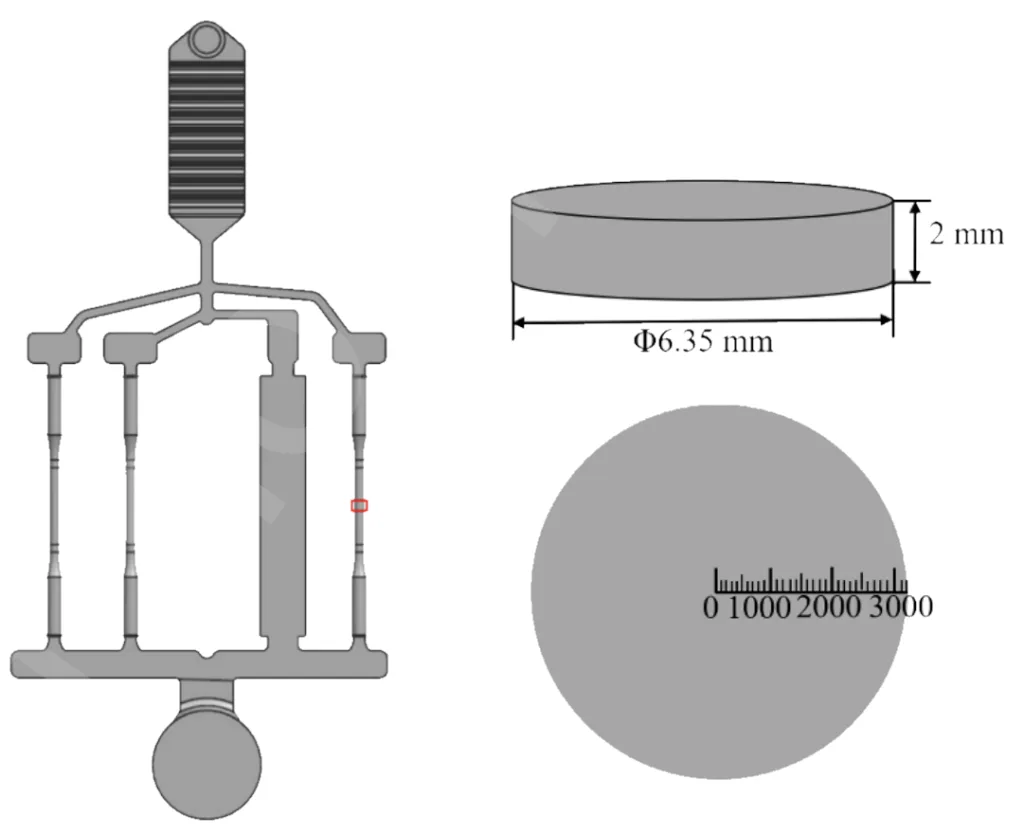
2. Research Background:
Background of the Research Topic:
Heat treatment is a well-established method for enhancing the mechanical properties of as-cast components by modifying phase composition and morphology. However, the application of heat treatment to High Pressure Die Castings (HPDC) is challenging due to the inherent presence of porosity. Pore expansion during heat treatment in HPDC is a critical issue that can limit the application of this beneficial post-processing technique.
Status of Existing Research:
Prior research has extensively documented the expansion of pores in HPDC, particularly focusing on surface pore expansion leading to bubbling defects. These surface defects are known to compromise component integrity and can lead to failure. Studies have characterized surface bubbles and identified influencing factors such as inner-pressure, axial ratio, pore size, temperature, and heat treatment duration. However, investigations into the expansion behavior of inner pores within HPDC castings have been limited, despite evidence suggesting their significant impact on mechanical properties due to stress concentration.
Necessity of the Research:
While surface pore expansion has been relatively well-studied, the expansion behavior of inner pores in HPDC and its spatial variation within the casting remains less understood. As inner pores can induce stress concentration and degrade mechanical performance, a comprehensive understanding of their expansion behavior during heat treatment is crucial. This research addresses the gap in knowledge by focusing on the 3D characterization of pore expansion in different regions of HPDC castings, specifically comparing the behavior of pores in the center zone versus the edge zone.
3. Research Purpose and Research Questions:
Research Purpose:
The primary purpose of this research is to clarify the expansion phenomenon of porosity during heat treatment in HPDC components. The study aims to meticulously analyze and compare the expansion behavior of pores located in different regions of the casting, specifically the center zone and the edge zone, using advanced 3D reconstruction techniques.
Key Research:
This research focuses on:
- Performing 3D reconstruction of porosity in HPDC castings produced both with and without vacuum assistance (WV and WOV) using X-ray Computed Tomography (XCT).
- Investigating and comparing the expansion behavior of pores located in the center zone and edge zone of the castings after heat treatment.
- Analyzing the morphological changes and volumetric expansion of individual pores in different regions.
Research Hypotheses:
While not explicitly stated as formal hypotheses, the research is guided by the premise that:
- Pore expansion behavior during heat treatment will vary significantly depending on the location within the HPDC casting (center vs. edge zone).
- Vacuum assistance during HPDC will influence the initial porosity and potentially the subsequent pore expansion behavior during heat treatment.
4. Research Methodology
Research Design:
This study employs an experimental research design. HPDC tensile bar castings were produced using YL112 alloy with and without vacuum assistance. Specimens were then subjected to a controlled heat treatment process. 3D porosity characterization was conducted before and after heat treatment to assess pore expansion.
Data Collection Method:
Synchrotron X-ray micro-tomography was utilized for non-destructive 3D imaging of the porosity. Experiments were performed at the BL13W1 line station of the Shanghai Synchrotron Radiation Facility, China, using an X-ray energy of 30 keV.
Analysis Method:
The acquired XCT images were processed using phoenix datos|x 2 and Avizo reconstruction software to generate 3D reconstructions of the porosity. Statistical analysis was performed to quantify the number density and volume of pores in circular rings of 100 µm thickness along the radial direction of the specimens. Individual pore morphologies and volume changes before and after heat treatment were also analyzed.
Research Subjects and Scope:
The research subjects were HPDC castings made from YL112 alloy. The scope was limited to tensile bar specimens produced using a horizontal cold chamber high pressure die casting machine (TY BD-350V5). Heat treatment was conducted at a solid solution temperature of 490°C for 30 minutes. The analysis focused on comparing pore expansion in the center and edge zones along the radial direction of the tensile bars.
5. Main Research Results:
Key Research Results:
- Differential Pore Expansion: Pores located in the edge zone of the HPDC castings exhibited significantly greater expansion during heat treatment compared to pores in the center zone.
- Quantified Expansion Values: Statistical analysis revealed that the expansion value for single pores in the edge zone was approximately 120 times, whereas in the center zone, it was about 1.5 times.
- Vacuum Effect on Initial Porosity: Castings produced with vacuum (WV) demonstrated a lower initial porosity quantity compared to castings produced without vacuum (WOV), particularly in the center zone.
- Heat Treatment Impact on Porosity: Heat treatment led to a substantial increase in both the quantity and size of porosity in both WV and WOV specimens.
- Porosity Distribution Uniformity: After heat treatment, the distribution of porosity morphology became more uniform across the casting section, from the center zone to the skin layer, regardless of the initial vacuum conditions.
Data Interpretation:
The observed difference in pore expansion between the edge and center zones is attributed to variations in inner-pressure and pore formation mechanisms during solidification. The authors explain this phenomenon using Charles' law, which states that the volume of a gas is directly proportional to its temperature at constant pressure. During heat treatment, the temperature increase leads to an elevated inner-pressure within the pores, driving their expansion. The significantly higher expansion in the edge zone suggests a different initial state of pores in this region compared to the center.
Figure Name List:
- Fig. 1. casting schematic including three tensile bars with one diameter of 6.4 mm at the center and one plate sample with a thickness of 2.5 mm
- Fig. 2. 3-D reconstructed images of castings fabricated without vacuum (WOV) and with vacuum (WV) before and after solution treatment
- Fig. 3 The relationship between the number density and volume of pores in WV and WOV specimens.
- Fig. 4. The variation of (a) number density, (b) fraction, and (c) average size of porosity along the radial direction in tensile bars.
- Fig. 5: The morphologies of pores locating in the center of tensile bars before and after heat treatment
- Fig. 6: The morphologies of pores near surface of tensile bars before and after heat treatment
- Fig. 7: Yield strength of YL112 at different temperature
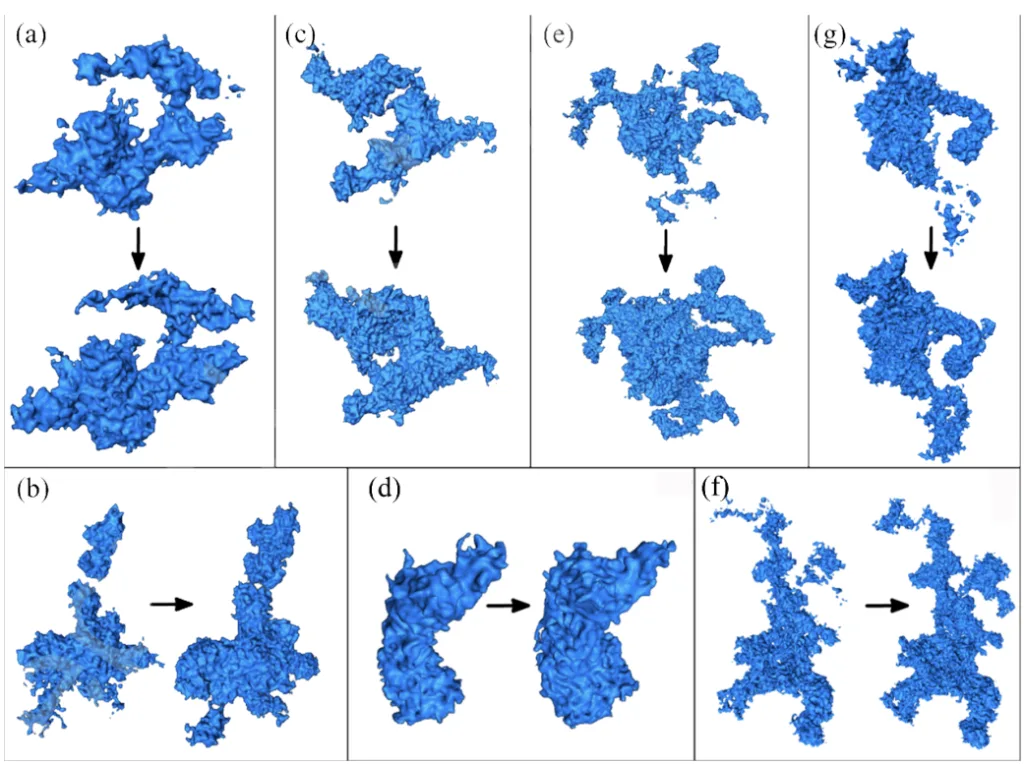
6. Conclusion:
Summary of Main Results:
This study successfully employed 3D XCT to characterize the expansion behavior of pores in HPDC castings during heat treatment. The key finding is the significant difference in pore expansion between the edge and center zones, with edge pores expanding much more dramatically. Vacuum application during casting reduces initial porosity but does not prevent pore expansion during subsequent heat treatment.
Academic Significance of the Research:
This research provides valuable insights into the spatially varying nature of pore expansion in HPDC components. The detailed 3D characterization and quantitative analysis contribute to a deeper understanding of porosity evolution during heat treatment and its dependence on pore location within the casting. This work highlights the importance of considering regional variations in porosity behavior for accurate prediction of component performance after heat treatment.
Practical Implications:
The findings have practical implications for optimizing HPDC processes and heat treatment parameters. Understanding the enhanced pore expansion in edge zones can guide the development of strategies to minimize porosity in these critical regions, potentially through localized process adjustments or modified heat treatment cycles. This can lead to improved casting quality, particularly in terms of reduced surface defects and enhanced mechanical integrity.
Limitations of the Research
The study is focused on a specific aluminum alloy (YL112) and a defined set of heat treatment conditions. The generalizability of these findings to other alloys, casting geometries, and heat treatment parameters requires further investigation. Additionally, while the study elucidates the difference in expansion behavior, further research is needed to fully elucidate the underlying mechanisms causing the disparity in pore expansion between different casting zones.
7. Future Follow-up Research:
- Directions for Follow-up Research
Future research should explore the pore expansion behavior in a broader range of HPDC alloys and under varying heat treatment parameters, including different temperatures and durations. Investigating the influence of HPDC process parameters, such as injection speed and intensification pressure, on the spatial distribution of pore expansion would also be beneficial. - Areas Requiring Further Exploration
Further exploration is needed to develop detailed numerical models that can predict pore expansion behavior in HPDC, considering factors such as local solidification conditions, gas content, and stress distributions. In-situ observation techniques during heat treatment could provide more direct evidence of the pore expansion mechanisms and their spatial variations.
8. References:
- [1] A. Mohamed, F.H. Samuel, A Review on the Heat Treatment of Al-Si-Cu/Mg Casting Alloys, (2012).
- [2] A.J. Ardell, Precipitation hardening, Metallurgical Transactions A, (1985).
- [3] L. Wang, P. Turnley, G. Savage, Gas content in high pressure die castings, Journal of Materials Processing Technology, 211 (2011) 1510-1515.
- [4] S.O. Wanna, H.I. Laukli, C.M. Gourlay, Feeding Mechanisms in High-Pressure Die Castings.
- [5] X. Li, S.M. Xiong, Z. Guo, Improved mechanical properties in vacuum-assist high-pressure die casting of AZ91D alloy, Journal of Materials Processing Technology, 231 (2016) 1-7.
- [6] G. Li, W. Yang, W. Jiang, G. Feng, Z. Fan, The role of vacuum degree in the bonding of Al/Mg bimetal prepared by a compound casting process, Journal of Materials Processing Technology, 265 (2018).
- [7] X. Dong, X. Zhu, S. Ji, Effect of super vacuum assisted high pressure die casting on the repeatability of mechanical properties of Al-Si-Mg-Mn die-cast alloys, Journal of Materials Processing Technology, 266 (2019) 105-113.
- [8] LUMLEY, N. R., O'DONNELL, G. R., GUNASEGARAM, R. D., GIVORD, Blister free heat treatment of high pressure die-casting alloys, Materials Science Forum, (2006).
- [9] R. Lumley, HEAT TREATMENT FOR HIGH-PRESSURE DIE-CASTING, Advanced manufacturing technology: Robotics, Rapid Prototyping, Assembly, (2008) 29.
- [10] R.N. Lumley, R.G. O'Donnell, D.R. Gunasegaram, T. Kittel-Sherri, I.J. Polmear, The role of alloy composition in the heat treatment of aluminium high pressure die castings, metallurgical science & tecnology, (2013).
- [11] 0. Ozhoga-Maslovskaja, E. Gariboldi, J.N. Lemke, Conditions for blister formation during thermal cycles of Al–Si–Cu–Fe alloys for high pressure die-casting, Materials & Design, 92 (2016) 151-159.
- [12] C. Xghab, D. Qza, E. Spma, C. Hva, C. Hbd, A. Fz, B. Ylk, Blistering in semi-solid die casting of aluminium alloys and its avoidance, Acta Materialia, 124 (2017) 446-455.
- [13] S. Midson, Q. Zhu, Y. He, H. Lu, D. Li, Controlling and Minimizing Blistering during T6 Heat Treating of Semi-Solid Castings, Diffusion and Defect Data. Solid State Data, Part B. Solid State Phenomena, (2016).
- [14] H. Toda, P.C. Qu, S. Ito, M. Kobayashi, K. Uesugi, 3D/4D observation of the micro-mechanism of blister deformation, (2012).
- [15] H. Toda, P.C. Qu, S. Ito, K. Shimizu, M. Kobayashi, Formation behaviour of blister in cast aluminium alloy, Cast Metals, 27 (2014) 369-377.
- [16] C.H. Caceres, On the effect of macroporosity on the tensile properties of the Al-7%Si-0.4%Mg casting alloy, Scripta Metallurgica et Materialia, 32 (1995).
- [17] W. Yu, C. Ma, Y. Ma, S. Xiong, Correlation of 3D defect-band morphologies and mechanical properties in high pressure die casting magnesium alloy, Journal of Materials Processing Technology, (2020) 116853.
- [18] Y.H. Ma, W.B. Yu, Y.Q. Zhou, S.M. Xiong, Influence of different high pressure die casting processes on 3D porosity distribution of Mg-3.0Nd-0.3Zn-0.6Zr alloy,中国铸造:英文版, (2021).
- [19] A. Cm, B. Wya, A. Tz, A. Zz, A. Ym, C. Sx, The effect of slow shot speed and casting pressure on the 3D microstructure of high pressure die casting AE44 magnesium alloy, Journal of Magnesium and Alloys, (2021).
- [20] V.K. Venkatasamy, Analysis Of In-cavity Thermal And Pressure Characteristics In Aluminum Alloy Die Casting, (1996).
- [21] M.S. Dargusch, G. Dour, N. Schauer, C.M. Dinnis, G. Savage, The influence of pressure during solidification of high pressure die cast aluminium telecommunications components, Journal of Materials Processing Tech, 180 (2006) 37-43.
- [22] X., P., Niu, K., K., Tong, B., H., Hu, I., Cavity pressure sensor study of the gate freezing behaviour in aluminium high pressure die casting, International Journal of Cast Metals Research, 11 (2016) 105-112.
- [23] X. Li, S.M. Xiong, Z. Guo, Correlation between Porosity and Fracture Mechanism in High Pressure Die Casting of AM60B Alloy,材料科学技术:英文版, (2016) 8.
- [24] A. Committe, Properties and selection : nonferrous alloys and special-purpose materials, Metals Handbook, 2 (1990).
9. Copyright:
- This material is "Yihu MA et al."'s paper: Based on "3D characterization of pores expansion behavior in high pressure die castings during heat treatment".
- Paper Source: https://ssrn.com/abstract=4328099
This material was summarized based on the above paper, and unauthorized use for commercial purposes is prohibited.
Copyright © 2025 CASTMAN. All rights reserved.