Depending on the project, aluminium casting is carried out through a "hot" or "low" process.
Diecasting is one of the most economical and fast molding processes. The advantage of this production process is that hundreds of thousands of castings can be produced relatively quickly using a single mold. All parts produced are of uniform quality and relatively low unit price.
Die casting is an automatic casting process that compresses high pressure (150-1200 bar) and high pressure (up to 540 km/h) liquid melt into molds. Generally, alloys with low melting points are used. This casting process is suitable for mass production of parts because it does not require permanent molds unlike sand casting. Thin wall thickness, large and complex parts can be built.
The hot chamber die casting method is to install the injection cylinder in the furnace to apply pressure and cast in a mold with little heat loss. This process uses alloys with low melting points, such as zinc, lead, or tin. This method is more suitable for manufacturing small and thin parts than large and thick parts.
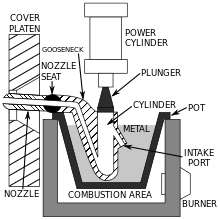
https://en.wikipedia.org/wiki/Die_casting#/media/File:Cold-chamber_die_casting_machine_schematic.svg
Cold casting, on the other hand, does not have a built-in furnace and requires additional steps. When the metal melts, it is passed to the casting machine through the injection cylinder. The biggest advantage of this method is that more materials are available than die casting can be used for hot die casting. Metals with higher melting points that can dissolve too quickly in hot die-casting chambers require more delicate handling and casting, which can be provided through coldcasting.
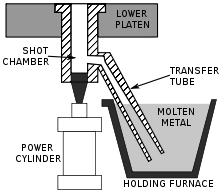
https://en.wikipedia.org/wiki/File:Hot-chamber_die_casting_machine_schematic.svg
After the alloy is pressed into the mold in both processes, the part hardens under strong pressure and the mold latch can be opened. Parts with gates are removed from the mold via automatically operated drainage pins, which can be further processed if necessary. The casting process actually takes place in 1/100 or 1/1000 seconds. Cold chamber die casting is the most widely used process for mass production of light metal castings.
Cast metal[edit]
reference : https://en.wikipedia.org/wiki/Die_casting
The main die casting alloys are: zinc, aluminium, magnesium, copper, lead, and tin; although uncommon, ferrous die casting is also possible.[6] Specific die casting alloys include: zinc aluminium; aluminium to, e.g. The Aluminum Association (AA) standards: AA 380, AA 384, AA 386, AA 390; and AZ91D magnesium.[7] The following is a summary of the advantages of each alloy:[8]
- Zinc: the easiest metal to cast; high ductility; high impact strength; easily plated; economical for small parts; promotes long die life.
- Aluminium: lightweight; high dimensional stability for very complex shapes and thin walls; good corrosion resistance; good mechanical properties; high thermal and electrical conductivity; retains strength at high temperatures.
- Magnesium: the easiest metal to machine; excellent strength-to-weight ratio; lightest alloy commonly die cast.
- Copper: high hardness; high corrosion resistance; highest mechanical properties of alloys die cast; excellent wear resistance; excellent dimensional stability; strength approaching that of steel parts.
- Silicon tombac: high-strength alloy made of copper, zinc and silicon. Often used as an alternative for investment cast steel parts.
- Lead and tin: high density; extremely close dimensional accuracy; used for special forms of corrosion resistance. Such alloys are not used in foodservice applications for public health reasons. Type metal, an alloy of lead, tin and antimony (with sometimes traces of copper) is used for casting hand-set type in letterpress printing and hot foil blocking. Traditionally cast in hand jerk moulds now predominantly die cast after the industrialisation of the type foundries. Around 1900 the slug casting machines came onto the market and added further automation, with sometimes dozens of casting machines at one newspaper office.
As of 2008, maximum weight limits for aluminium, brass, magnesium, and zinc castings are estimated at approximately 70 pounds (32 kg), 10 lb (4.5 kg), 44 lb (20 kg), and 75 lb (34 kg), respectively.[9] By late-2019, Giga Press machines capable of die casting single pieces over-100 kilograms (220 lb) were being used to produce aluminium chassis components for the Tesla Model Y electric car.[10]
The material used defines the minimum section thickness and minimum draft required for a casting as outlined in the table below. The thickest section should be less than 13 mm (0.5 in), but can be greater.[11]
Metal | Minimum section | Minimum draft |
---|---|---|
Aluminium alloys | 0.89 mm (0.035 in) | 1:100 (0.6°) |
Brass and bronze | 1.27 mm (0.050 in) | 1:80 (0.7°) |
Magnesium alloys | 1.27 mm (0.050 in) | 1:100 (0.6°) |
Zinc alloys | 0.63 mm (0.025 in) | 1:200 (0.3°) |