Martin Lagler, Process Engineer Applications
Bühler AG Uzwil, Switzerland
Abstract
Lost Core is a technology which is becoming increasingly more popular as the need for lightweight construction increases. The advantages are obvious: Completely new components can be developed since the use of salt cores in HPDC allows for complex internal designs. In addition, combining several components makes a high degree of function integration possible. Bühler AG – Die Casting is consistently working on the further development of this process. The whole package is convincing: Along with die casting machines and systems, Bühler offers its customers support in the areas of casting development and die design.
Bühler experts are working intensively to simulate die casting with Lost Core technology. Standard simulation tools for the die casting industry, as they are available for example in Flow 3D, are used for this. The simulation opportunities for Lost Core technology thus correspond to those in standard aluminum HPDC. Simulations are used to test the gating- and venting system designs. Possible diffi- culties and optimizations can be recognized at an early stage in this way. It is virtually no longer necessary to make costly and time-consuming changes to the die at a later time. For the Lost Core technology, Bühler used a sample part to show that simulation makes it possible to predict whether a salt core will be destroyed during the HPDC process or will withstand the pressure of the aluminum melt.
Lost Core는 경량 구조의 필요성이 증가함에 따라 점점 더 대중화되고 있는 기술입니다. 장점은 분명합니다. HPDC에서 솔트 코어를 사용하면 복잡한 내부 설계가 가능하므로 완전히 새로운 구성 요소를 개발할 수 있습니다. 또한 여러 구성 요소를 결합하여 높은 수준의 기능 통합을 가능하게 합니다. Bühler AG – Die Casting은 이 공정의 추가 개발을 위해 지속적으로 노력하고 있습니다.
전체 패키지는 설득력이 있습니다. Bühler는 다이 캐스팅 기계 및 시스템과 함께 캐스팅 개발 및 다이 설계 영역에서 고객 지원을 제공합니다.
Bühler 전문가는 Lost Core 기술로 다이 캐스팅을 시뮬레이션하기 위해 집중적으로 노력하고 있습니다. 이를 위해 예를 들어 Flow 3D에서 사용할 수 있는 다이 캐스팅 산업을 위한 표준 시뮬레이션 도구가 사용됩니다.
따라서 Lost Core 기술의 시뮬레이션 기회는 표준 알루미늄 HPDC의 시뮬레이션 기회와 일치합니다. 시뮬레이션은 게이팅 및 환기 시스템 설계를 테스트하는 데 사용됩니다. 이러한 방식으로 초기 단계에서 가능한 어려움과 최적화를 인식할 수 있습니다.
나중에 비용이 많이 들고 시간이 많이 소요되는 다이를 변경할 필요가 더 이상 없습니다. 로스트 코어 기술의 경우 Bühler는 시뮬레이션을 통해 HPDC 프로세스 중에 염심 코어가 파괴되거나 알루미늄 용융물의 압력을 견딜지 여부를 예측할 수 있음을 보여주기 위해 샘플 부품을 사용했습니다.

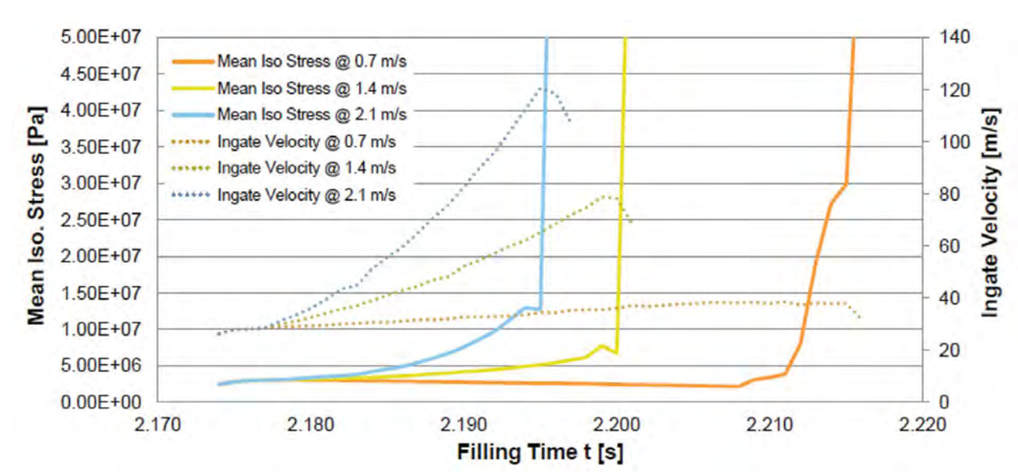
Fine Adjustment of the Shot Curve as the Key to Success
Usage of Fluid Structure Interaction (FSI) simulation is help- ful in this connection. It predicts the effect which the liquid aluminum will have on the salt core. The stresses occurring in the core are computed in this simulation (Figure 1). Knowl- edge of these stresses is important – they can, after all, cause the core to break in an unfavorable case. The FSI simulation reveals which shot parameters must be maintained to achieve a successful cast. The stresses occurring in the core and the ingate velocity, i.e. the velocity of the liquid aluminum at a point immediately before it hits the core, are displayed in a diagram (Figure 2). The maximum tolerated stress of the salt core is clearly exceeded in the intensification pressure phase. It is therefore important that the filling process is complete at the time of the pressure changeover and that the salt core is completely surrounded by melt. If this is not the case, then the salt core can break. The diagram shows first and foremost that the decisive factor for the viability of a salt core is not the ingate velocity but rather the point of pressure changeover. Various shot curves can be tested for this behavior and evalu- ated by means of simulation.
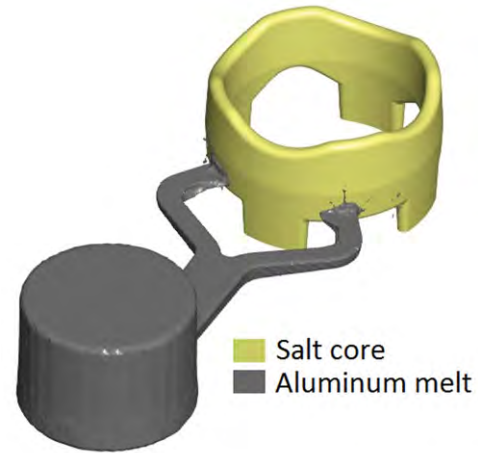
Bühler as a Partner
Simulation of the casting process plays an important role for efficient and quick implementation of projects for die casting components. Especially for new processes, such as Lost Core, it provides essential information for the design and optimization of the process. Bühler experts will provide this know-how as a service to its customers. The extensive knowledge about die design, simulation and the HPDC process additionally guarantees our optimal support – from the development of die casting parts up to serial production.