This introduction paper is based on the paper "Thermal Management of Bright LEDs for Automotive Applications" published by "7th. Int. Conf. on Thermal, Mechanical and Multiphysics Simulation and Experiments in Micro-Electronics and Micro-Systems, EuroSimE 2006".
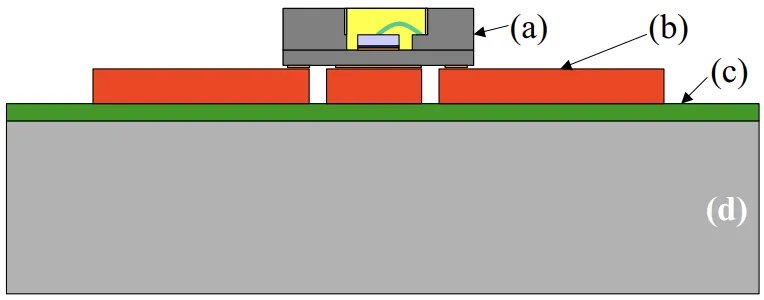
1. Overview:
- Title: Thermal Management of Bright LEDs for Automotive Applications
- Author: Yan Lai, Nicolás Cordero
- Year of publication: 2006
- Journal/academic society of publication: 7th. Int. Conf. on Thermal, Mechanical and Multiphysics Simulation and Experiments in Micro-Electronics and Micro-Systems, EuroSimE 2006
- Keywords: Not specified in the paper.
2. Abstract:
High brightness white light emitting diodes (LEDs) have shown to be very promising for many illumination applications such as outdoor illumination, task and decorative lighting as well as aircraft and automobile illumination, including automotive headlights. The objective of this paper is to investigate the cooling solutions of such LEDs in automotive applications. In this research, a thermal design from device to board to system level has been carried out, and optimisation work has been done to find the optimum thermal performance. Both natural and forced convection have been explored and conclusions are drawn for each case in this specific application.
3. Introduction:
With advances in GaN-based materials technology, high brightness white LEDs have significantly progressed and are increasingly utilized in automotive exteriors such as brake lights, turn indicators, and tail lights, with emerging potential for forward lighting systems. However, current LEDs for production vehicles present a high-cost solution with insufficient lumen output; legal requirements stipulate 750 lm per lamp for headlamps, while average bright LED output is only 40 lm/W, necessitating more LEDs and higher driving powers. This increase in driving power makes thermal management of LED packaging crucial, as elevated diode junction temperatures reduce LED efficiency and cause shifts in emission wavelength. To achieve high efficiency and a relatively fixed wavelength, a thermal solution must keep the LED well below its maximum operating temperature (i.e., < 125 °C). Such a solution must be all-inclusive, addressing thermal issues at the device, package, board, and system levels. This study utilizes commercially available bare die bright LEDs and Computational Fluid Dynamics (CFD) simulations to develop a suitable thermal management solution.
4. Summary of the study:
Background of the research topic:
The demand for increased light output from LEDs leads to higher driving powers, making effective thermal management essential for their efficiency, performance, and reliability. An increase in LED junction temperature results in decreased efficiency and a shift in the emission wavelength. For automotive applications, particularly headlights, it is critical to maintain the LED junction temperature well below the maximum operating limit (e.g., < 125 °C) to ensure optimal and stable performance.
Status of previous research:
The paper notes that while LEDs are common in automotive exterior lighting, customized LEDs for headlight applications are not yet standard. Current LEDs are costly and do not provide sufficient lumen output for production vehicles, where headlamps require 750 lm per lamp. Given that current bright LEDs output approximately 40 lm/W, achieving the required illumination necessitates using a larger number of LEDs operating at higher power levels, thereby highlighting the critical need for advanced thermal management strategies.
Purpose of the study:
The primary objective of this paper is to investigate and identify optimal cooling solutions for high brightness LEDs used in automotive applications, specifically headlights. The study involves a comprehensive thermal design process, from the device level through to the board and system levels, coupled with optimization work to achieve the best possible thermal performance. The research explores both natural and forced convection cooling methods.
Core study:
The core of the study involved the thermal design and optimization for a system comprising 15 Cree XBright900 LEDs. These LEDs, each capable of generating up to 2.5 W of heat, were configured with 3 LEDs per board across 5 boards. Key aspects of the study include:
- LED Packaging: Individual packaging of LEDs using AlN (k=200 W/mK) to ensure a low thermal resistance path from the LED to the package bottom (calculated as less than 2 °C/W).
- Insulated Metal Substrate (IMS) Optimisation: The AlN packages were mounted on an IMS. The IMS structure was optimized by evaluating different materials and layer thicknesses. The final design consisted of a 70 µm copper circuit layer, a 75 µm dielectric layer (made of ceramic/polymer with k=2.2 W/mK), and a 1 mm Aluminium core board (as detailed in Table 1).
- Heat Sink Optimisation: An aluminium heat sink was designed and optimized for natural convection cooling. This involved an iterative process using CFD software (FloTherm) to determine optimal parameters such as surface area, fin number, fin thickness, fin height, and base thickness, considering manufacturing and application constraints.
- Evaluation of Cooling Methods:
- Natural Convection: Performance was simulated with the optimized IMS and heat sink, both in open air and within a confined headlight enclosure.
- Forced Convection (Air): This was briefly explored but dismissed as not feasible due to constraints related to space, reliability, cost, and the need for high flow fans.
- Liquid Cooling: Both passive and active liquid cooling solutions were investigated as alternatives. Passive liquid cooling was found unsuitable due to geometric constraints of the application. Active liquid cooling, employing a water-cooled cold plate connected to a remote heat exchanger, was simulated and analyzed.
5. Research Methodology
Research Design:
The research adopted a multi-level thermal design strategy, addressing thermal management issues from the LED die (device level) through the package, the Insulated Metal Substrate (IMS board), and up to the system level, which includes the heat sink and its operational environment (e.g., headlight enclosure). An iterative optimization methodology was central to the design process, particularly for the heat sink, to balance conflicting design parameters (e.g., thermal performance vs. weight, size, and manufacturability). The study focused on a system using Cree XBright900 LEDs, with a configuration of 15 LEDs distributed across 5 boards (3 LEDs per board).
Data Collection and Analysis Methods:
Thermal performance was analyzed and optimized using commercial Computational Fluid Dynamics (CFD) software, FloTherm [3]. The methodology involved:
- Calculating the thermal resistance of the LED package.
- Conducting parametric studies for IMS optimization by comparing various materials and layer thicknesses to minimize thermal resistance.
- Performing iterative simulations to optimize heat sink design parameters, including fin number, fin thickness, fin height, and base plate dimensions, with the goal of minimizing LED junction temperature under natural convection.
- Simulating and comparing the thermal performance of different cooling strategies: natural convection (in open air and within an enclosure) and active liquid cooling.
Research Topics and Scope:
The research concentrated on the thermal management of high brightness white LEDs, specifically the Cree XBright900 model, for automotive headlight applications. The scope of the study encompassed:
- The design of individual LED packages using Aluminium Nitride (AlN) for efficient heat dissipation.
- The design and optimization of an Insulated Metal Substrate (IMS) board for mounting the LED packages.
- The design and optimization of an aluminium heat sink tailored for natural convection cooling.
- Evaluation of the system's thermal performance in different environments: open air versus placement inside a headlight enclosure.
- Investigation of alternative cooling solutions, including a brief consideration of forced air convection, and more detailed analyses of passive liquid cooling and active liquid cooling systems.
- The system under test consisted of 15 LEDs, where each LED could generate up to 2.5 W of heat, with a primary thermal management goal of maintaining the LED junction temperature below 125 °C.
6. Key Results:
Key Results:
- IMS Optimisation: An optimized Insulated Metal Substrate (IMS) board structure was determined, comprising a 70 µm copper circuit layer, a 75 µm ceramic/polymer dielectric layer with a thermal conductivity (k) of 2.2 W/mK, and a 1 mm thick Aluminium substrate. This configuration, detailed in Table 1, was designed to enhance heat spreading and reduce overall thermal resistance.
- Heat Sink Optimisation for Natural Convection:
- An iterative optimization process using CFD simulations was employed to define the optimal fin number (Figure 3), fin thickness (Figure 4), fin height (Figure 5), and base plate area (Figure 6) for an aluminium heat sink.
- Simulations of an IMS board with three LEDs (each dissipating 3W) mounted on the optimized heat sink under natural convection in open air showed temperature profiles ranging from 60 to 100°C (Figure 7).
- Limitations of Natural Convection in Enclosure: When the LED assembly with the optimized heat sink was placed inside a headlight enclosure, natural convection proved insufficient to maintain the LED junction temperature below the desired 125°C. Simulations indicated that the junction temperature could exceed this limit, reaching as high as 200°C (Figure 8), due to air recirculation within the confined space.
- Forced Air Convection Assessment: Forced air convection was considered but deemed not a feasible solution due to practical constraints related to space limitations within the headlight, reliability concerns of fans, cost, and assembly complexities.
- Passive Liquid Cooling Assessment: Passive liquid cooling was found unsuitable for this specific application. The required orientation for effective passive convection (heat source below the heat sink) would obstruct the light output from the LEDs. Furthermore, relying solely on conduction through water (with a thermal conductivity of 0.6 W/mK) was insufficient for the heat loads.
- Active Liquid Cooling Performance: Active liquid cooling, utilizing a water-cooled cold plate mounted under the IMS board and connected to a remote heat exchanger (Figure 9), demonstrated a significant improvement in thermal performance. The calculated LED junction temperature with this system was 110°C (Figure 10), representing an improvement of 90°C compared to natural convection within the enclosure.
- Identified Trade-offs: The study underscored the inherent trade-offs between achieving a thermally optimal solution and adhering to practical application constraints such as manufacturing feasibility, weight restrictions, and available space. While active liquid cooling offered superior thermal performance, it also introduced potential drawbacks, including risks of pumping leakage, concerns about pump reliability, increased power consumption, liquid evaporation, potential for dry out and clogging, and the need for additional maintenance.
Figure Name List:
- Figure 1. Insulated Metal Substrate assembly. (a) AlN cup with wire-bonded LED, (b) Circuit layer, (c) Dielectric layer and (d) Aluminium substrate.
- Figure 2. Simulated IMS Board with three LEDS mounted on a vertical Heat Sink.
- Figure 3. LED Junction Temperature vs. Fin Number
- Figure 4. LED Junction Temperature vs. Fin Thickness
- Figure 5. LED Junction Temperature vs. Fin Height
- Figure 6. LED Junction Temperature vs. Base Plate Area
- Figure 7. Cross Section Temperature Profiles in Natural Convection for assembly in Figure 2. (a) Top view and (b) Side view. Temperature range shown is 60 to 100°C.
- Figure 8. Optimised Heat Sink inside a headlight enclosure (Tj = 200°C). Temperature range shown is 25 to 180°C.
- Figure 9. Active Liquid Cooling. The IMS board is mounted on a liquid-cooled cold plate which is connected with hoses to a heat exchanger.
- Figure 10. Temperature Profile of Active Liquid Cooling (Figure 9). Temperature range shown is 35 to 95°C. The flow velocity range is 0 to 4.5 m/s.
7. Conclusion:
This paper outlines a systematic procedure for selecting an optimal cooling solution for LEDs specifically customized for novel automotive headlight applications. The study found that natural convection cooling was insufficient to maintain the LED junction temperature below the maximum allowable levels for the high-power LED system under investigation, especially when enclosed. Forced convection cooling with air was also determined to be not viable due to space and reliability constraints within the automotive context. Simulation results demonstrated that, for the thermal management of bright LEDs in automotive applications, active liquid cooling can significantly enhance cooling capability, reducing the junction temperature from approximately 200°C (achieved with natural convection in an enclosure) to 110°C. However, the paper also acknowledges several major drawbacks associated with liquid cooling, such as potential for pumping leakage, pump reliability issues, additional power consumption, liquid evaporation, risks of dry out and clogging, and increased maintenance requirements. The authors suggest that with the future development of even brighter white LEDs that require less driving power for a given light output, simpler air-cooling solutions may once again become adequate.
8. References:
- [1] Pearson, T., Mounier, E., Eloy, J.C., Jourdan, D., "Solid-state lighting in the automobile: concept, market timing and performance," LEDs Magazine, pp. 25-27, Apr. 2005.
- [2] Stratford, J and Musters, A, “Insulated metal printed circuits – a user-friendly revolution in power design," Electronics Cooling, vol. 10, pp. 30-34, Nov. 2004.
- [3] Flomerics Ltd., FloThermTM 6.1 Instruction Manual, 2005.
- [4] Karimpourian, B. and Mahmoudi, J., “Some important considerations in heatsink design," Proc. of the 6th EuroSimE Conference, pp 406-413 (2005)
- [5] Azar, K., “Cooling technology options, part 1," Electronics Cooling, vol. 9, Aug. 2003
- [6] Azar, K., "Cooling technology options, part 2," Electronics Cooling, vol. 9, Nov. 2003
9. Copyright:
- This material is a paper by "Yan Lai, Nicolás Cordero". Based on "Thermal Management of Bright LEDs for Automotive Applications".
- Source of the paper: https://doi.org/10.1109/ESIME.2006.1643953
This material is summarized based on the above paper, and unauthorized use for commercial purposes is prohibited.
Copyright © 2025 CASTMAN. All rights reserved.