This introduction paper is based on the paper "The Mechanical Properties of a Transient Liquid Phase Diffusion Bonded SSM-ADC12 Aluminum Alloy with a ZnAl4Cu3 Zinc Alloy Interlayer" published by "Journal of Manufacturing and Materials Processing (MDPI)".
![Table 2. The chemical compositions and mechanical properties of the SSM-ADC12 aluminum alloy and the ZnAl4Cu3 zinc alloy chosen for this study [18,19].](https://castman.co.kr/wp-content/uploads/image-2255-1024x289.webp)
1. Overview:
- Title: The Mechanical Properties of a Transient Liquid Phase Diffusion Bonded SSM-ADC12 Aluminum Alloy with a ZnAl4Cu3 Zinc Alloy Interlayer
- Author: Chaiyoot Meengam, Yongyuth Dunyakul and Dech Maunkhaw
- Year of publication: 2024
- Journal/academic society of publication: Journal of Manufacturing and Materials Processing (J. Manuf. Mater. Process.)
- Keywords: transient liquid phase diffusion bonding; SSM-ADC12 aluminum alloy; semi-solid status; ZnAl4Cu3 Zinc alloy; interlayer materials
2. Abstract:
In this study, the mechanical properties of SSM-ADC12 aluminum alloy specimens with a ZnAl4Cu3 zinc alloy interlayer were observed after Transient Liquid Phase Diffusion Bonding (TLPDB), a welding process conducted in a semi-solid state. The purpose of the experiment was to study how the following parameters—bonding temperature (400, 430, 460, 490, and 520 °C), bonding time (60, 90, and 120 min), and thickness of the ZnAl4Cu3 zinc alloy (0.5, 1.0, and 2.0 mm)—affect the mechanical properties and the types of defects that formed. The results show that the bonding strength varied significantly with different parameters following the TLPDB process. A maximum bonding strength of 32.21 MPa was achieved at a bonding temperature of 490 °C, with 20 min of bonding and a ZnAl4Cu3 zinc alloy layer that was 2.0 mm thick. Conversely, changing the welding parameters influenced the bonding strength. A minimum bonding strength of 2.73 MPa was achieved at a bonding temperature of 400 °C, with a bonding time of 90 min and a ZnAl4Cu3 zinc alloy interlayer that was 2.0 mm thick. The Vickers microhardness results showed that the bonded zone had a lower hardness value compared to the base materials (BMs) of the SSM-ADC12 aluminum alloy (86.60 HV) and the ZnAl4Cu3 zinc alloy (129.37 HV). The maximum hardness was 83.27 HV, which resulted from a bonding temperature of 520 °C, a bonding time of 90 min, and a ZnAl4Cu3 zinc alloy that was 2.0 mm thick. However, in the near interface, the hardness value increased because of the formation of MgZn2 intermetallic compounds (IMCs). The fatigue results showed that the stress amplitude was 31.21 MPa in the BMs of the SSM-ADC12 aluminum alloy and 20.92 MPa in the material that results from this TLPDB process (TLPDB Material) when the limit of cyclic loading exceeded 10^6 cycles. Microstructural examination revealed that transformation from a β-eutectic Si IMC recrystallization structure to η(Zn–Al–Cu) and β(Al2Mg3Zn3) IMCs occurred. A size reduction to a width of 6–11 µm and a length of 16–44 µm was observed via SEM. Finally, voids or porosity and bucking defects were found in this experiment.
3. Introduction:
ADC12 aluminum alloys are extensively used in automotive components like engine parts and transmission cases, as well as in the aerospace and electronics industries due to their lightweight nature, strength, heat resistance, thermal conductivity, and machinability [1–3]. The usage rate of ADC12 aluminum alloys is increasing due to their excellent castability, high strength, corrosion resistance, and good thermal conductivity [4].
Gas-induced semi-solid (GISS) processing is a method used for fabricating metal matrix composites, particularly aluminum-based alloys, by introducing gas bubbles into a molten metal matrix to achieve a semi-solid state with a globular microstructure [5]. ADC12 alloys are commonly formed using GISS, producing materials with improved properties and microstructural uniformity [6,7].
Transient liquid phase diffusion bonding (TLPDB) is a specialized welding technique for joining metal materials, especially those difficult to weld by conventional methods, often used in the aerospace industry [8]. It involves applying heat and pressure, with an interlayer material having a lower melting point than the base materials (BMs). The interlayer melts, promoting atomic mixing and diffusion across the interface, eliminating voids and defects for a strong metallurgical bond [9,10]. TLPDB offers advantages like joining dissimilar materials, lower processing temperatures, and precise control over bond interface microstructure [11].
4. Summary of the study:
Background of the research topic:
ADC12 aluminum alloys, often processed using GISS techniques to achieve desirable microstructures, are vital in various industries. TLPDB is an advanced joining technique suitable for such materials, especially when aiming for high-quality bonds and joining dissimilar materials or those difficult to weld conventionally. The parameters of the TLPDB process, including the choice of interlayer material, significantly affect the mechanical properties and microstructure of the joint.
Status of previous research:
Previous studies have investigated TLPDB for various aluminum alloys and other materials, exploring different interlayer materials and process parameters (summarized in Table 1 of the paper). For example, TLPDB has been studied for Al2219 with Cu interlayer [12], Al6063 with copper foil [13], Al-Mg-Si alloy with Sn-based material [14], AR500 steel and AA7075 with Al-Si-Zn interlayer [15], and 1420 Al-Li alloy [16]. However, the specific combination of SSM-ADC12 aluminum alloy with a ZnAl4Cu3 zinc alloy interlayer using the GISS technique, and the detailed investigation of bonding temperature, time, and interlayer thickness effects, represents a novel area of research.
Purpose of the study:
The purpose of this experiment was to study how the following TLPDB parameters—bonding temperature (400, 430, 460, 490, and 520 °C), bonding time (60, 90, and 120 min), and thickness of the ZnAl4Cu3 zinc alloy interlayer (0.5, 1.0, and 2.0 mm)—affect the mechanical properties (bonding strength, fatigue, and hardness) and the types of defects that formed in SSM-ADC12 aluminum alloy joints. The study also aimed to evaluate the mechanism of IMC phase transformation.
Core study:
The core of the study involved performing TLPDB on SSM-ADC12 aluminum alloy specimens using a ZnAl4Cu3 zinc alloy as an interlayer material. The experiments systematically varied bonding temperature, bonding time, and interlayer thickness. The resulting joints were then characterized for their mechanical properties (bonding strength, fatigue life, microhardness) and microstructural features (IMC formation, defect presence, phase transformations) using techniques like optical microscopy, SEM, and EDX.
5. Research Methodology
Research Design:
The research was designed as an experimental study. SSM-ADC12 aluminum alloy, formed using the GISS technique, was used as the base material. A ZnAl4Cu3 zinc alloy (commercial-grade ZA27) served as the interlayer material. The TLPDB process was conducted by varying bonding temperatures (400, 430, 460, 490, and 520 °C), bonding times (60, 90, and 120 min), and interlayer thicknesses (0.5, 1.0, and 2.0 mm) under a constant bonding pressure of 3.4 MPa in an argon atmosphere.
Data Collection and Analysis Methods:
- Materials: SSM-ADC12 aluminum alloy (melting point 548 °C) formed by GISS technique and ZnAl4Cu3 zinc alloy interlayer (melting point 399 °C). Chemical compositions and mechanical properties are detailed in Table 2.
- TLPDB Process: Cylindrical SSM-ADC12 samples (45 mm length, 10 mm diameter) and ZnAl4Cu3 interlayer disks (10 mm diameter; 0.5, 1.0, 2.0 mm thick) were used. Surfaces were polished and cleaned. Bonding was performed in a gas chamber with argon flow (7 L/min). Temperature control during TLPDB is shown in Figure 3.
- Fatigue Testing: Conducted using a NARIN NRI-CPT500-2 Static and Dynamic Testing Machine at 20 Hz, stress ratio R = −1. Stroke values were adjusted (0.35 to 0.80 mm). Fatigue limit was set over 10^6 cycles. S–N curves were generated. Specimens prepared according to ASTM E466-15.
- Metallurgy and Mechanical Testing:
- Bond strength tests were conducted at room temperature using a Lloyd EZ50 universal testing machine (crosshead speed 1.67 × 10^−2 mm/s) following ASTM E8M-04.
- Microhardness was assessed using an FM-700e Vickers microhardness tester (100 g force, 10 s duration), with indentations 0.2 mm from the bond center.
- Microstructure examination involved cutting, polishing (SiC paper P320-P1200, alumina powder 5.0, 3.0, 1.0 µm), and etching with Keller’s reagent. Analysis was done using a BH2-UMA light microscope and an FEI-Quanta 400 electron microscope (SEM) with EDX for chemical composition.
Research Topics and Scope:
The research focused on the effects of TLPDB parameters (bonding temperature, bonding time, interlayer thickness) on the mechanical properties (bonding strength, fatigue, hardness) and microstructural evolution (IMC phase transformation, defect formation) of joints between SSM-ADC12 aluminum alloy and a ZnAl4Cu3 zinc alloy interlayer. The study covered bonding temperatures from 400 to 520 °C, bonding times from 60 to 120 min, and interlayer thicknesses of 0.5, 1.0, and 2.0 mm.
6. Key Results:
Key Results:
- Physical Characteristics: Bonding time and temperature influenced sample deformation. Longer times and higher temperatures led to more ejection of the ZnAl4Cu3 interlayer and potential deflection defects (Figure 4).
- Bonding Strength: Bonding strength was dependent on temperature, time, and interlayer thickness (Figure 5). A maximum bonding strength of 32.21 MPa was achieved at 490 °C, 120 min bonding time, and 2.0 mm interlayer thickness. A minimum of 2.73 MPa was recorded at 400 °C, 90 min, and 2.0 mm thickness. Increased bonding time and temperature generally increased bonding strength due to better diffusion and IMC formation, and elimination of surface oxide films. Table 3 compares these results with previous studies.
- Fatigue Analysis: The TLPDB material showed a lower fatigue endurance limit (20.29 MPa at 10^6 cycles) compared to the SSM-ADC12 BM (31.12 MPa at 10^6 cycles) (Table 4, Figure 6, Table 5). This was attributed to new precipitates (β-eutectic phase, α-primary aluminum matrix phase) and crack/void defects from the TLPDB process.
- Microstructure:
- Appropriate bonding temperature and time led to the disappearance of voids. Tiny MgZn2 particles formed and scattered in the α-Al phase. Rapid diffusion of Zn led to β + η phases, with β(Al2Mg3Zn3) supersaturating to β' and η(Zn-Al-Cu) merging into β to form η'. ZnAl4Cu3 zinc alloy shrinkage led to cracks at higher temperatures (520 °C) due to rapid cooling (Figure 7a-c).
- At 490 °C, 90 min, 2.0 mm interlayer, complete diffusion was observed with few defects (Figure 7d-f).
- Eutectic Si IMCs in BMs transformed from globular to distorted grains after TLPDB, with particle size increasing from 78–97 µm to 118–139 µm (Figure 7g).
- SEM analysis (Figure 8) showed transformation of eutectic Si IMCs. In BMs, they were gauze-like (21–70 µm length, 2–9 µm width). In the bonding zone, HAZ, and NBZ, Si IMCs became smaller and elongated (e.g., 6–11 µm length, 2–4 µm width in HAZ; 16–44 µm length, 2–3 µm width in NBZ). In the center interlayer, Si IMCs had refined grain size (12–27 µm length, 19–29 µm width).
- EDX mapping (Figure 9, Table 6) showed Al (65.25 wt%), Zn (19.01 wt%), C (9.94 wt%), Si (5.68 wt%), and Cu (2.34 wt%) in the bonding zone.
- Vickers Microhardness: Hardness in the bonding zone increased with elevated temperatures due to IMC precipitation (especially MgZn2). Maximum hardness of 83.20 HV was achieved at 520 °C, 120 min bonding time, 2.0 mm interlayer (Figure 10c). Insufficient bonding times/temperatures resulted in lower hardness (Figure 10a,b). η(Zn-Al–Cu), β(Al2Mg3Zn3), and MgZn2 IMCs contributed to hardness increases.
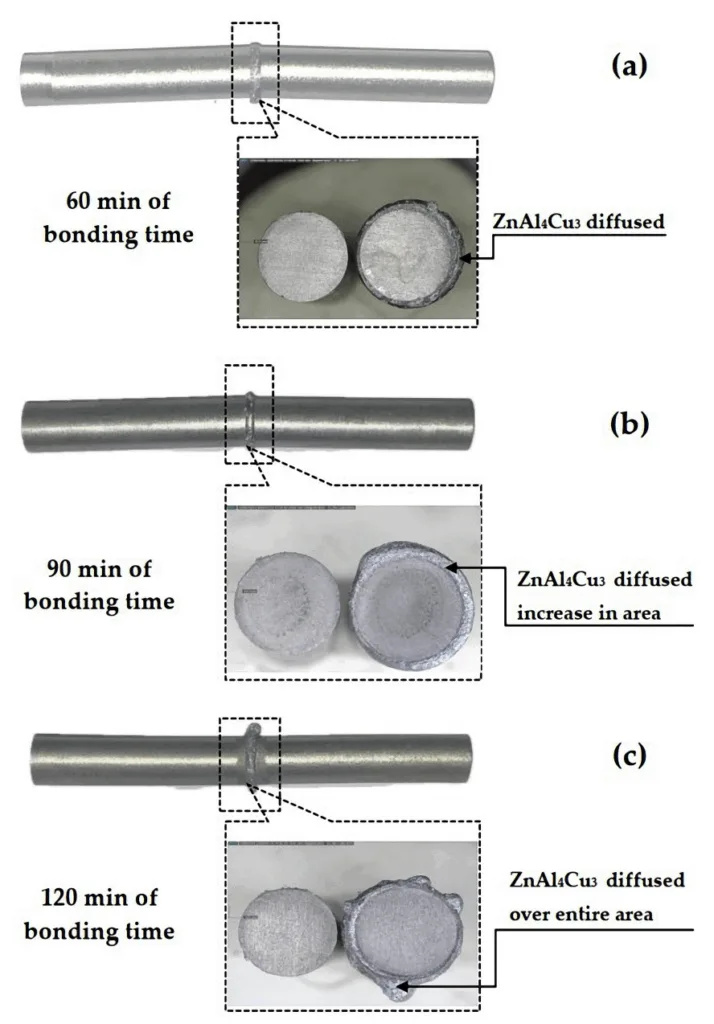
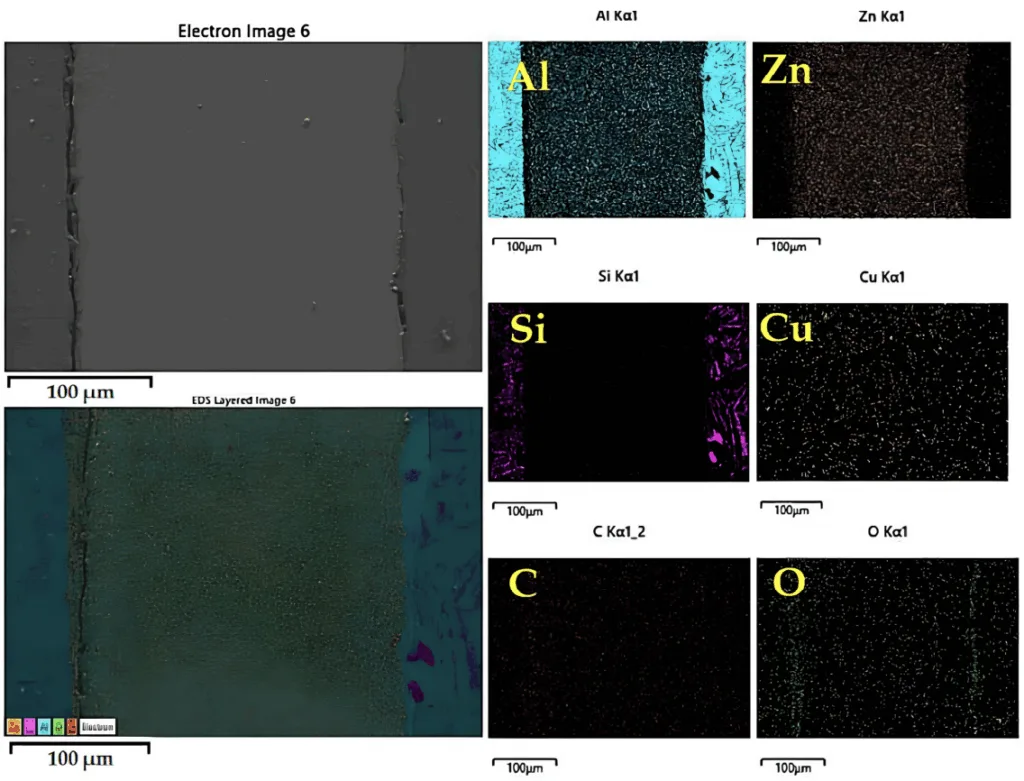
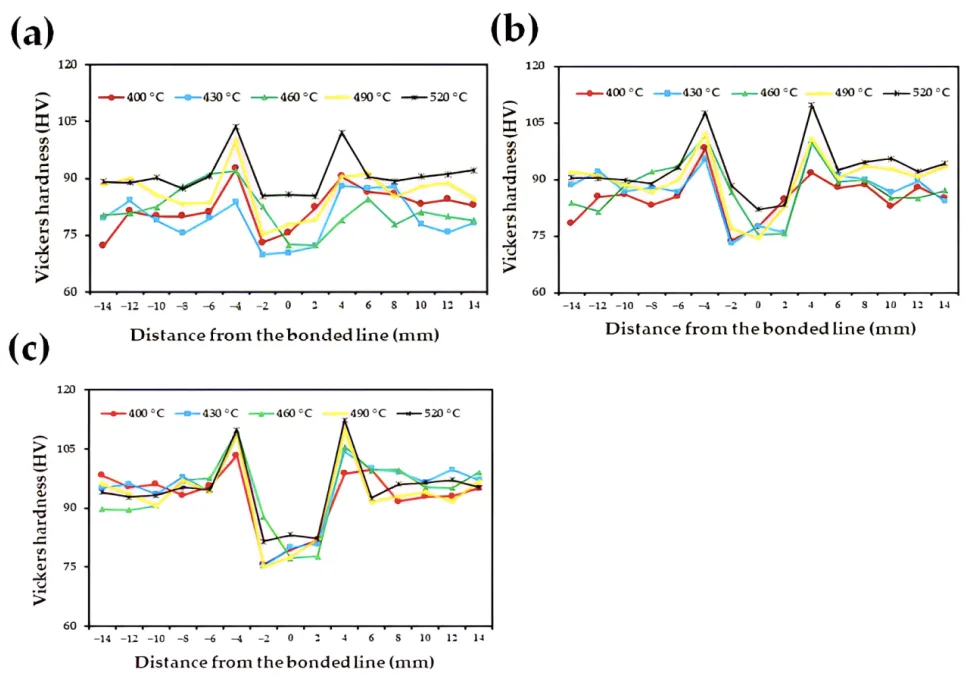
Figure Name List:
- Figure 1. Photograph of the base microstructure of the SSM-ADC12 aluminum alloy formed using GISS casting.
- Figure 2. Equipment used for the TLPDB of SSM-ADC12 aluminum alloy using the ZnAl4Cu3 zinc alloy interlayer material.
- Figure 3. A schematic view of the temperature of TLPDB of the SSM-ADC12 aluminum alloy.
- Figure 4. Micrographs showing the characteristics of the samples and cross sections after TLPDB of the SSM-ADC12 aluminum alloy using a ZnAl4Cu3 zinc alloy with a 2.0 mm interlayer at 490 °C for (a) 60 min, (b) 90 min, and (c) 120 min.
- Figure 5. Bond strengths for the TLPDB of the SSM-ADC12 aluminum alloy using a ZnAl4Cu3 zinc alloy as the interlayer with different bonding times of (a) 60 min, (b) 90 min, and (c) 120 min.
- Figure 6. The fatigue S-N curves for the BMs and TLPDB material of the SSM-ADC12 aluminum alloy using a ZnAl4Cu3 zinc alloy as an interlayer.
- Figure 7. Micrographs of the microstructure in the bonded zone (a–g) and BM around diffused area after TLPDB.
- Figure 8. SEM micrographs (taken in EDX mode) of different characteristics of the eutectic Si IMCs show the following: (a) entire bond, (b) BMs, (c) bonding zone, (d) near-bonding zone, and (e) center interlayer.
- Figure 9. EDX mapping analysis of the composition (wt%) in the bonded zone.
- Figure 10. The Vickers microhardness values of the SSM-ADC12 aluminum alloy after TLPDB with a ZnAl4Cu3 zinc alloy interlayer that was 2.0 mm thick: (a) 60 min bonding time, (b) 90 min bonding time, and (c) 120 min bonding time.
7. Conclusion:
The study successfully investigated the effects of TLPDB parameters on SSM-ADC12 aluminum alloy joints with a ZnAl4Cu3 zinc alloy interlayer. Key conclusions are:
- An average maximum bonding strength of 32.21 MPa was achieved at a bonding temperature of 490 °C, a bonding time of 120 min, and a ZnAl4Cu3 zinc alloy interlayer material thickness of 2.0 mm.
- Crack, void, and deformation defects were detected in the TLPDB material after evaluation.
- The endurance limits of the TLPDB material and BMs were 20.29 MPa and 31.12 MPa, respectively.
- The maximum Vickers microhardness of 83.20 HV was obtained with 120 min of bonding, 520 °C, and a 2.0 mm thick ZnAl4Cu3 interlayer. Formation of η(Zn-Al–Cu), β(Al2Mg3Zn3), and MgZn2 IMCs led to increased hardness.
- MgZn2 phase formation and precipitation near the bonded line improved mechanical properties. Transformation of the α-primary matrix with β-eutectic Si IMCs to form an η(Zn-Al–Cu) phase occurred at the bonded line. Optical microscopy showed precipitation changing from globular to coarse structures. SEM showed β-eutectic Si IMCs diffused into β(Al2Mg3Zn3) and MgZn2 IMCs (average width 19–29 µm, length 12–27 µm). EDX mapping confirmed Mg, Si, and Al mobility at the joint.
8. References:
- [1] Lee, H.; Yoon, J.; Yoo, J. Manufacturing of Aerospace Parts with Diffusion Bonding Technology. Appl. Mech. Mater. 2011, 87, 182–185.
- [2] Pola, A.; Tocci, M.; Kapranos, P. Microstructure and Properties of Semi-Solid Aluminum Alloys: A Literature Review. Metals 2018, 8, 181.
- [3] Vinith, S.; Uthayakumar, A.; Rajan, S. Fluidity of ADC12 alloy based on theoretical and computational fluid dynamics. Mech. Eng. 2015, 4, 996–999.
- [4] JIS H 5302:Japan; Japanese Industrial Standard, Aluminum Alloys Die Castings (ADC 12). Japanese Industrial Standard: Tokyo, Japan, 2000; p. 10.
- [5] Wannasin, J.; Janudom, S.; Rattanochaikul, T.; Canyook, R.; Burapa, R.; Chucheep, T.; Thanabumrungkul, S. Research and development of gas induced semi-solid process for industrial applications. Trans. Nonferr. Met. Soc. China 2010, 20, 1010–1015.
- [6] Janudom, S.; Rattanochaikul, T.; Burapa, R.; Wisutmethangoon, S.; Wannasin, J. Feasibility of semi-solid die casting of ADC12 aluminum alloy. Trans. Nonferr. Met. Soc. China 2010, 20, 1756–1762.
- [7] Gautam, S.K.; Singh, B.K. Investigation on the effects of isothermal holding temperature and time on the coarsening mechanism and rheological properties of ADC12 Al semi-solid slurry. Mater Chem Phys. 2024, 314, 128813.
- [8] Simões, S. Diffusion Bonding and Brazing of Advanced Materials. Metals 2018, 8, 959.
- [9] Zhang, L.X.; Chang, Q.; Sun, Z.; Xue, Q.; Feng, J.C. Effects of boron and silicon on microstructural evolution and mechanical properties of transient liquid phase bonded GH3039/IC10 joints. J. Manuf. Process. 2019, 38, 167–173.
- [10] Jiao, Y.J.; Sheng, G.M.; Zhang, Y.T.; Xu, C.; Yuan, X.J. Transient liquid phase bonding of Inconel 625 with Mar-M247 superalloy using Ni-Cr-B interlayer: Microstructure and mechanical properties. Mater. Sci. Eng. A 2022, 831, 142204.
- [11] Yuan, L.; Ren, J.; Xiong, J.T.; Zhao, W.; Shi, J.M.; Li, J.L. Transient liquid phase bonding of Ni3Al based superalloy using Mn-Ni-Cr filler. J. Mater. Res. Technol. 2021, 11, 1583–1593.
- [12] Vatnalmath, M.; Auradi, V.; Murthy, B.V.; Nagaral, M.; Pandian, A.A.; Islam, S.; Khan, M.S.; Anjinappa, C.; Razak, A. Impact of Bonding Temperature on Microstructure, Mechanical, and Fracture Behaviors of TLP Bonded Joints of Al2219 with a Cu Interlayer. ACS Omega 2023, 8, 26332–26339.
- [13] Saleh, M.I.; Roven, H.J.; Khan, T.I.; Iveland, T. Transient Liquid Phase Bonding of Al-6063 to Steel Alloy UNSS32304. J. Manuf. Mater. Process. 2018, 2, 58.
- [14] Dong, J.H.; Liu, H.; Ji, S.D.; Yan, D.J.; Zhao, H.X. Diffusion Bonding of Al-Mg-Si Alloy and 301L Stainless Steel by Friction Stir Lap Welding Using a Zn Interlaye. Materials 2022, 15, 696.
- [15] Muhamed, M.N.; Omar, M.Z.; Abdullah, S.; Sajuri, Z.; Zamri, W.F.H.W. Al-Si-Zn Behaviouron Interface of AR500 Steel and AA7075 Aluminium Alloy BrazedJoint. J. Phys. Conf. Ser. 2020, 1532, 012006.
- [16] Zhang, H.; Niu, T.; Yuan, M. Influence of High Magnetic Field-Thermal Coupling Processing on Diffusion Bonding Properties and Element Diffusion of 1420 Al-Li Alloy. Crystals 2022, 12, 1508.
- [17] Canyook, R.; Wannasin, J.; Wisutmethangoon, S.; Flemings, M.C. Characterization of the microstructure evolution of a semi-solid metal slurry during the early stages. Acta Mater. 2012, 60, 3501–3510.
- [18] Chainarong, S.; Pitakaso, R.; Sirirak, W.; Srichok, T.; Khonjun, S.; Sethanan, K.; Sangthean, T. Multi-Objective Variable Neighborhood Strategy Adaptive Search for Tuning Optimal Parameters of SSM-ADC12 Aluminum Friction Stir Welding. J. Manuf. Mater. Process. 2021, 5, 123.
- [19] Seah, K.H.W.; Sharma, S.C.; Girish, B.M. Mechanical properties of cast ZA-27 graphite particulate composites. Mater. Des. 1996, 16, 271–275.
- [20] Kittima, S.; Yoshiharu, M.; Yukio, M.; Nobushiro, S. Fatigue Strength Estimation Based on Local Mechanical Properties for Aluminum Alloy FSW Joints. Metals 2017, 10, 186.
- [21] ASTM E466-15; Standard Practice for Conducting Force Controlled Constant Amplitude Axial Fatigue Tests of Metallic Materials. Designation. ASTM International Standards: West Conshohocken, PA, USA, 2015.
- [22] ASTM E8; Standard Test Methods for Tension Testing of Metallic Materials. Designation. ASTM International Standards: West Conshohocken, PA, USA, 2015.
- [23] Malekan, A.; Farvizi, M.; Mirsalehi, S.E.; Saito, N.; Nakashima, K. Holding Time Influence on Creep Behavior of Transient Liquid Phase Bonded Joints of Hastelloy X. Mater. Sci. Eng. A 2020, 772, 138694.
- [24] Al Hazaa, A.; Haneklaus, N.; Almutairi, Z. Impulse pressure-assisted diffusion bonding (IPADB): Review and outlook. Metals 2021, 11, 323.
- [25] Venugopal, S.; Seeman, M.; Seetharaman, R.; Jayaseelan, V. The effect of bonding process parameters on the microstructure and mechanical properties of AA5083 diffusion-bonded joints. Int. J. Ligh. Mater. Manuf. 2022, 5, 555–563.
- [26] Yu, W.; Zhao, H.; Huang, Z.; Chen, X.; Aman, Y.; Li, S.; Zhai, H.; Guo, Z.; Xiong, S. Microstructure evolution and bonding mechanism of Ti2SnC–Ti6Al4V joint by using Cu pure foil interlayer. Mater. Charact. 2017, 127, 53–55.
- [27] Silva, M.; Ramos, A.; Vieira, M.; Simões, S. Diffusion Bonding of Ti6Al4V to Al2O3 Using Ni/Ti Reactive Multilayers. Metals 2021, 11, 655.
- [28] Ben-Haroush, M.; Mittelman, B.; Priel, R.S.E. The Influence of Time, Atmosphere and Surface Roughness on the Interface Strength and Microstructure of AA6061–AA1050 Diffusion Bonded Components. Materials 2023, 16, 769.
- [29] Meengam, C.; Dunyakul, Y.; Maunkhaw, D.; Chainarong, S. Transient Liquid Phase Bonding of Semi-Solid Metal 7075 Aluminum Alloy Using ZA27 Zinc Alloy Interlayer. Metals 2018, 8, 637.
- [30] Alhazaa, A.; Khan, T.; ul Haq, I. Transient liquid phase (TLP) bonding of Al7075 to Ti–6Al–4V alloy. Mater. Charact. 2010, 61, 312–317.
- [31] Wen, Z.; Li, Q.; Liu, F.; Dong, Y.; Zhang, Y.; Hu, W.; Li, L.; Gao, H. Transient Liquid Phase Diffusion Bonding of Ni3Al Superalloy with Low-Boron Nickel-Base Powder Interlayer. Materials 2023, 16, 2554.
- [32] Kejanli, H.; Taşkin, M.; Kolukisa, S.; Topuz, P. Transient liquid phase (TPL) diffusion bonding of Ti45Ni49Cu6 P/M components using Cu interlayer. Int. J. Adv. Manuf. Technol. 2009, 44, 695–699.
- [33] Meengam, C.; Dunyakul, Y.; Chainarong, S.; Maunkhaw, D. The Influence of Diffuse Element in Solid-State on Dissimilar Joint between Semi-Solid Cast 7075 with 6061 Al Alloy by Diffusion Welding. Solid State Phenom. 2022, 330, 71–76.
- [34] Maity, J.; Pal, T.K.; Maiti, R. Transient liquid phase diffusion bonding of 6061-15 wt % SiCp in argon environment. J. Mater. Process. Technol. 2009, 209, 3568–3580.
- [35] Seyyed Afghahi, S.S.; Ekrami, A.; Farahany, S.; Jahangiri, A. Fatigue properties of temperature gradient transient liquid phase diffusion bonded Al7075-T6 alloy. Trans. Nonferrous Met. Soc. China 2015, 25, 1073–1079.
- [36] Liu, Y.; Zhang, Y.; Liu, S.; Xiao, S.; Sun, Y.; Wang, X. Effect of unbonded areas around hole on the fatigue crack growth life of diffusion bonded titanium alloy laminates. Eng. Fract. Mech. 2016, 1, 176–188.
- [37] He, X.; Liu, W.; Sun, Y.; Wang, X. Fatigue crack growth characteristic for diffusion bonded laminates of titanium alloy with centered hole. Eng. Mech. 2015, 4, 244–249.
- [38] Syed, A.K.; Zhang, X.; Moffatt, J.E.; Maziarz, R.; Castelletti, L.; Fitzpatrick, M.E. Fatigue performance of bonded crack retarders in the presence of cold worked holes and interference-fit fasteners. Int. J. Fatigue 2017, 105, 111–118.
- [39] Liu, Y.; Liu, S. Experimental Research on Fatigue Crack Growth Behavior of Diffusion-Bonded Titanium Alloy Laminates with Preset Unbonded Areas. Materials 2022, 15, 5224.
- [40] Li, S.; Xuan, F.; Tu, S. Fatigue damage of stainless steel diffusion-bonded joints. Mater. Sci. Eng. A 2008, 480, 125–129.
- [41] Abdolvand, R.; Atapour, M.; Shamanian, M.; Allafchian, A. The effect of bonding time on the microstructure and mechanical properties of transient liquid phase bonding between SAF 2507. J. Manuf. Process. 2017, 25, 172–180.
- [42] Norouzi, E.; Atapour, M.; Shamanian, M.; Allafchian, A. Effect of bonding temperature on the microstructure and mechanical properties of Ti-6Al-4V to AISI 304 transient liquid phase bonded joint. Mater. Des. 2016, 99, 543–551.
- [43] Habisch, S.; Peter, S.; Grund, T.; Mayr, P. The Effect of Interlayer Materials on the Joint Properties of Diffusion-Bonded Aluminium and Magnesium. Metals 2018, 8, 138.
- [44] Yang, L.; Yang, Y.; Zhang, Y.; Xu, F.; Jian, Q.; Lu, W. Microstructure evolution and mechanical properties of the In-Sn-20Cu composite particles TLP bonding solder joints. Appl. Phys. A 2020, 126, 343.
- [45] Kim, S.H.; Cha, J.-H.; Jang, C.; Sah, I. Microstructure and Tensile Properties of Diffusion Bonded Austenitic Fe-Base Alloys—Before and After Exposure to High Temperature Supercritical-CO2. Metals 2020, 10, 480.
- [46] Ghaderi, S.; Karimzadeh, F.; Ashra, A. Evaluation of microstructure and mechanical properties of transient liquid phase bonding of Inconel 718 and nano/ultrafine-grained 304L stainless steel. J. Manuf. Process. 2020, 49, 162–174.
- [47] Peng, Y.Y.; Li, C.; Li, H.J.; Liu, Y.C. Effect of interlayer on microstructure and mechanical properties of diffusional-bonded Ni3Al-based superalloy/S31042 steel joint. J. Manuf. Process. 2021, 72, 252–261.
9. Copyright:
- This material is a paper by "Chaiyoot Meengam, Yongyuth Dunyakul and Dech Maunkhaw". Based on "The Mechanical Properties of a Transient Liquid Phase Diffusion Bonded SSM-ADC12 Aluminum Alloy with a ZnAl4Cu3 Zinc Alloy Interlayer".
- Source of the paper: https://doi.org/10.3390/jmmp8050184
This material is summarized based on the above paper, and unauthorized use for commercial purposes is prohibited.
Copyright © 2025 CASTMAN. All rights reserved.