This article introduces the paper 'Simulation and validation of high-pressure die casting of an electric motor housing for automotive application' presented at the Politecnico di Torino.
1. Overview:
- Title: Simulation and validation of high-pressure die casting of an electric motor housing for automotive application
- Author: Gianluigi Lanzoni
- Publication Year: A.A.2020/2021
- Publishing Journal/Academic Society: Politecnico di Torino, Course of automotive engineering (Thesis of master’s degree)
- Keywords: High-Pressure Die Casting (HPDC), Electric Motor Housing, Automotive Application, Process Simulation, Validation
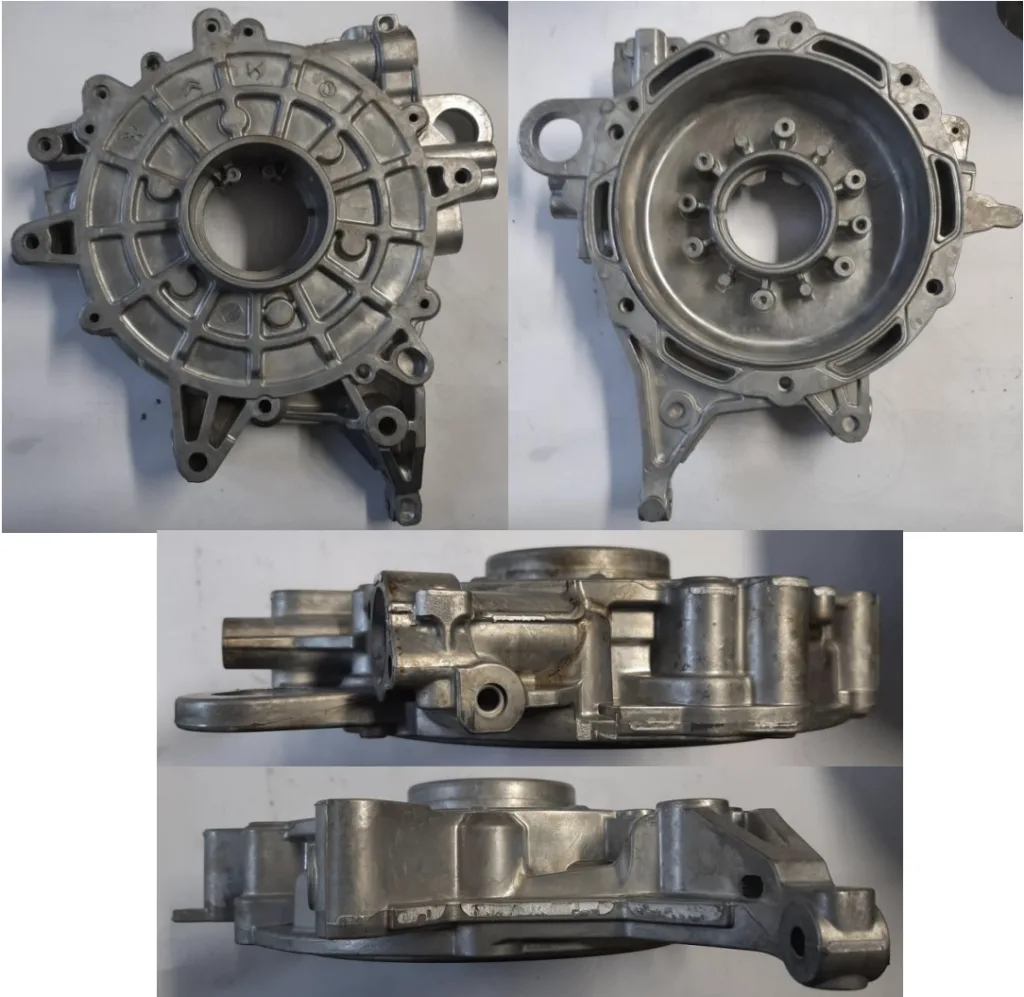
2. Research Background:
Background of the Research Topic:
The increasing demand for lightweight and complex automotive components, particularly for electric vehicles, has amplified the significance of High-Pressure Die Casting (HPDC). This research addresses the application of HPDC to electric motor housings, critical components in modern automotive powertrains. The study emphasizes the inherent complexity of the HPDC process, necessitating advanced simulation techniques for process optimization and defect mitigation.
Status of Existing Research:
Current HPDC practices are described as being rooted in experience, evolving towards a more science-based approach. A significant knowledge gap exists in fully understanding the intricate relationships between injection parameters and the resultant cast quality. Specifically, the production of novel components like electric motor housings lacks established literature and empirical data, highlighting the need for systematic investigation.
Necessity of the Research:
This research is crucial for establishing production guidelines for electric motor housings manufactured via HPDC. These components represent a new class of castings, extending beyond the conventional product range for HPDC. The study leverages process simulations to bridge the knowledge gap and to develop robust manufacturing strategies for these emerging automotive parts. The ultimate aim is to correlate simulation outcomes with real-world casting results, thereby defining best practices for industrial implementation.
3. Research Purpose and Research Questions:
Research Purpose:
The primary purpose of this thesis is to analyze the high-pressure die casting process specifically for the production of an electric motor housing (carter). This research aims to evaluate the efficacy of process simulations, utilizing multiple software platforms, to predict and validate the HPDC process for this novel component. The overarching goal is to establish a set of guidelines for the efficient and high-quality manufacturing of similar electric motor housing components in future production scenarios.
Key Research:
This research focuses on:
- Simulating the HPDC process using three distinct software packages: Flow-3D Cast, Inspire Cast, and PIQ2 Castle.
- Comparing and contrasting the simulation results obtained from each software, focusing on process parameters and predicted defect formation.
- Validating simulation predictions through experimental mold sampling and analysis of real cast components.
- Investigating the influence of critical process parameters on casting quality and identifying optimal parameter settings.
- Analyzing the formation mechanisms of common die casting defects and evaluating simulation accuracy in predicting these defects.
Research Hypotheses:
While not explicitly stated as formal hypotheses, the research operates under the implicit assumption that:
- Process simulations can provide a reasonably accurate representation of the HPDC process for complex electric motor housings.
- Optimized process parameters derived from simulation studies will lead to tangible improvements in casting quality, reduced defect rates, and enhanced production efficiency.
- A correlation can be established between simulation predictions and real-world casting outcomes, validating the use of simulation as a predictive tool in HPDC of electric motor housings.
4. Research Methodology
Research Design:
This research employs a case study approach centered on the simulation and validation of the HPDC process for a specific automotive component: the PSA front electric motor housing. The methodology integrates computational simulations with experimental validation to provide a comprehensive analysis.
Data Collection Method:
Data acquisition is multi-faceted, encompassing:
- Simulation Data: Numerical data generated from process simulations conducted using Flow-3D Cast, Inspire Cast, and PIQ2 Castle software. This includes data on temperature distribution, air entrapment, die erosion, solidification times, and PQ2 diagrams.
- Experimental Data: Empirical data collected from physical mold sampling and component analysis, including:
- Thermographs: Thermal imaging data capturing die temperature variations during the casting cycle.
- X-ray Analysis: Non-destructive evaluation data identifying internal porosities and defects within the cast components.
- Dimensional Measurements: Data verifying the dimensional accuracy of the cast parts against design specifications.
Analysis Method:
The research employs a comparative and validation-centric analysis approach:
- Software Comparison: A comparative analysis of simulation results across the three software platforms to assess their respective capabilities and limitations in predicting HPDC process phenomena.
- Mesh Sensitivity Study: Evaluation of simulation accuracy as a function of mesh density, analyzing results across different mesh dimensions (7.5 mm, 3.7 mm, 2.5 mm, and 2 mm).
- Simulation-Experiment Validation: Correlation of simulation predictions with experimental data from thermography and X-ray analysis to validate the accuracy and reliability of the simulation models.
- Process Parameter Analysis: Investigation of the influence of key process parameters, such as filling time, flow rate, and gate thickness, on casting quality and defect formation.
- PQ2 Diagram Analysis: Utilization of PQ2 diagrams to analyze the interaction between the HPDC machine and the mold, and to assess the process operating window.
Research Subjects and Scope:
The research is specifically scoped to the HPDC process for:
- Component: PSA front electric motor housing (Figure 26: PSA front housing model, Figure 27: PSA front housing die model)
- Material: Aluminum 43400 alloy (Figure 28: alloy composition)
- Process: Horizontal cold chamber HPDC process, as employed at Fondalpress S.p.a (Figure 1: Fondalpress S.p.a plant).
- Software: Flow-3D Cast, Inspire Cast, and PIQ2 Castle for process simulation.
- Validation Methods: Mold sampling, thermography, and X-ray analysis for experimental validation.
5. Main Research Results:
Key Research Results:
The study yielded comprehensive simulation results across varying mesh dimensions and software platforms. Key findings include:
- Mesh Dimension Impact: Simulations with a 7.5 mm mesh were deemed unreliable. A 2.5 mm mesh was identified as providing an optimal balance between accuracy and computational efficiency, aligning with industry guidelines suggesting a mesh dimension approximately one-third of the part's mean thickness. (Figure 29: geometry approximation plan view, Figure 30: intricate geometry approximation)
- Temperature Distribution: Temperature simulations revealed consistent patterns across different mesh densities, with higher temperatures at the injection cylinder exit and near the gate. Finer meshes provided more nuanced temperature gradients. (Figure 31: temperature results with various mesh dimension part 1, Figure 32: temperature results with various mesh dimension part 2)
- Air Entrapment Prediction: Simulations highlighted potential air entrapment zones, particularly in the upper regions of the casting. Finer meshes indicated a more refined representation of air pocket formation. (Figure 33: air trapped with various mesh dimensions part 1, Figure 34: air trapped with various mesh dimensions part 2)
- Die Erosion Analysis: Die erosion simulations indicated higher erosion potential at the gate and runner-mold cavity interface, correlating with areas of high alloy velocity. (Figure 35: die erosion with various mesh dimensions)
- Solidification Time Prediction: Solidification simulations consistently identified the biscuit as the last region to solidify, crucial for feeding shrinkage. (Figure 36: solidification times with various mesh dimensions)
- Software Comparison: Flow-3D Cast was recognized as the most comprehensive and accurate software, offering advanced features like die cycling and detailed oxide tracking. Inspire Cast was noted for its user-friendliness, while PIQ2 Castle provided a balance of ease of use and machine-specific parameter integration. (Figure 37: Inspire Cast and Castle modeling interface, Figure 38: Flow-3D Cast thermal die cycling, Figure 39: Thermal die cycling length (Flow-3D Cast), Figure 40: Filling setup with the three software)
- Experimental Validation: Thermographic measurements of die temperature showed qualitative agreement with simulation predictions, although absolute temperature values differed due to experimental conditions. X-ray analysis of castings revealed porosity distributions that generally aligned with simulated porosity risk areas. (Figure 79: thermograph fixed side die open, Figure 80: thermograph and simulation results part 1, Figure 81: thermograph and simulation results part 2, Figure 82: X-ray with porosities, Figure 83: porosity risk and X-ray results part 1, Figure 84: porosity risk and X-ray results part 2, Figure 85: porosity risk and X-ray results part 3)
- PQ2 Diagram Analysis: PQ2 diagram analysis indicated that the actual casting process operated outside the optimal zone, suggesting potential for process optimization by adjusting machine parameters or gate design. (Figure 86: example of Pq^2 diagram, Figure 87: Pq^2 diagram actual condition, Figure 88: Pq^2 diagram on optimal machine)
Data Interpretation:
Simulation results effectively predicted potential defect locations and process bottlenecks. Experimental validation, while showing some discrepancies in absolute values, generally corroborated simulation findings, particularly in identifying porosity-prone regions. The PQ2 diagram analysis highlighted opportunities for process optimization to enhance casting quality and efficiency. The study underscores the importance of mesh refinement for accurate simulation results and the complementary strengths of different simulation software for comprehensive HPDC process analysis.
Figure Name List:
- Figure 1: Fondalpress S.p.a plant
- Figure 2: alloy standard ingots
- Figure 3: alloy melting path
- Figure 4: melting furnace
- Figure 5: hydrogen solubilization in the aluminum
- Figure 6: picking with the bucket
- Figure 7: degassing station
- Figure 8: holder furnaces
- Figure 9: high-pressure die casting machine
- Figure 10: die fixed side
- Figure 11: die moving side
- Figure 12: interaction between aluminum and lubricant
- Figure 13: Die lubrication
- Figure 14: interaction between lubricant drop and the hot mold
- Figure 15: effects of different pulverizations on die wettability
- Figure 16: three injection phases
- Figure 17: robot transporting the cast to the trimming machine
- Figure 18: trimming machine
- Figure 19: trapped air defects
- Figure 20: hydrogen inclusions defects
- Figure 21: shrinkage defects
- Figure 22: hot cracks
- Figure 23: cold joints
- Figure 24: oxidations
- Figure 25: mean frequency of defects in the cast
- Figure 26: PSA front housing model
- Figure 27: PSA front housing die model
- Figure 28: alloy composition
- Figure 29: geometry approximation plan view
- Figure 30: intricate geometry approximation
- Figure 31: temperature results with various mesh dimension part 1
- Figure 32: temperature results with various mesh dimension part 2
- Figure 33: air trapped with various mesh dimensions part 1
- Figure 34: air trapped with various mesh dimensions part 2
- Figure 35: die erosion with various mesh dimensions
- Figure 36: solidification times with various mesh dimensions
- Figure 37: Inspire Cast and Castle modeling interface
- Figure 38: Flow-3D Cast thermal die cycling
- Figure 39: Thermal die cycling length (Flow-3D Cast)
- Figure 40: Filling setup with the three software
- Figure 41: Rapid evaluation of the best machine parameters
- Figure 42: temperature during filling
- Figure 43: die temperature before lubrication
- Figure 44: die temperature after lubrication
- Figure 45: air trapped at the end of filling and solid fraction
- Figure 46: defect net volume
- Figure 47: temperature distribution at the end of filling
- Figure 48: various results of base simulation
- Figure 49: mould temperature during filling and solidification
- Figure 50: air trapped
- Figure 51: temperature distribution after filling
- Figure 52: air trapped simulation
- Figure 53: filling time
- Figure 54: mould temperature during filling and solidification
- Figure 55: cooling system layout
- Figure 56: cooling system layout, lateral views
- Figure 57: temperature distribution during filling
- Figure 58: air trapped
- Figure 59: mould temperature during filling and solidification
- Figure 60:die temperature at filling end, before part extraction and die reclosing
- Figure 61: solid fraction and temperature at cast extraction
- Figure 62: porosities risk
- Figure 63: filling temperature part 1
- Figure 64: filling temperature part 2
- Figure 65: air trapped
- Figure 66: filling temperature, filling time and total volume restriction
- Figure 67: filling temperature
- Figure 68: trapped air during filling
- Figure 69: net defect volume and dual phase during filling
- Figure 70: die erosion
- Figure 71: velocity trajectories
- Figure 72: channels thickness
- Figure 73: sealing wall thickness
- Figure 74: example of simulation of thermal engine transmission part 1
- Figure 75: example of simulation of thermal engine transmission part 2
- Figure 76: wall thickness
- Figure 77: die before sampling
- Figure 78: trimming machine mould before installation
- Figure 79: thermograph fixed side die open
- Figure 80: thermograph and simulation results part 1
- Figure 81: thermograph and simulation results part 2
- Figure 82: X-ray with porosities
- Figure 83: porosity risk and X-ray results part 1
- Figure 84: porosity risk and X-ray results part 2
- Figure 85: porosity risk and X-ray results part 3
- Figure 86: example of Pq^2 diagram
- Figure 87: Pq^2 diagram actual condition
- Figure 88: Pq^2 diagram on optimal machine
- Figure 89: real component at die extraction
- Figure 90: real component after trimming
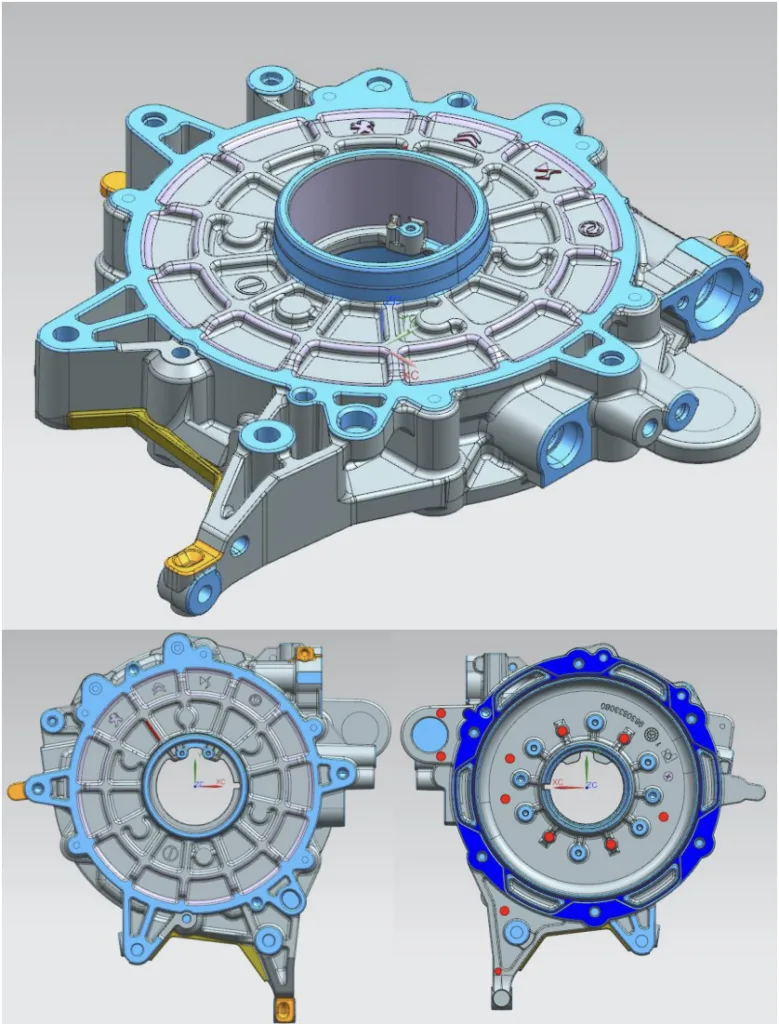
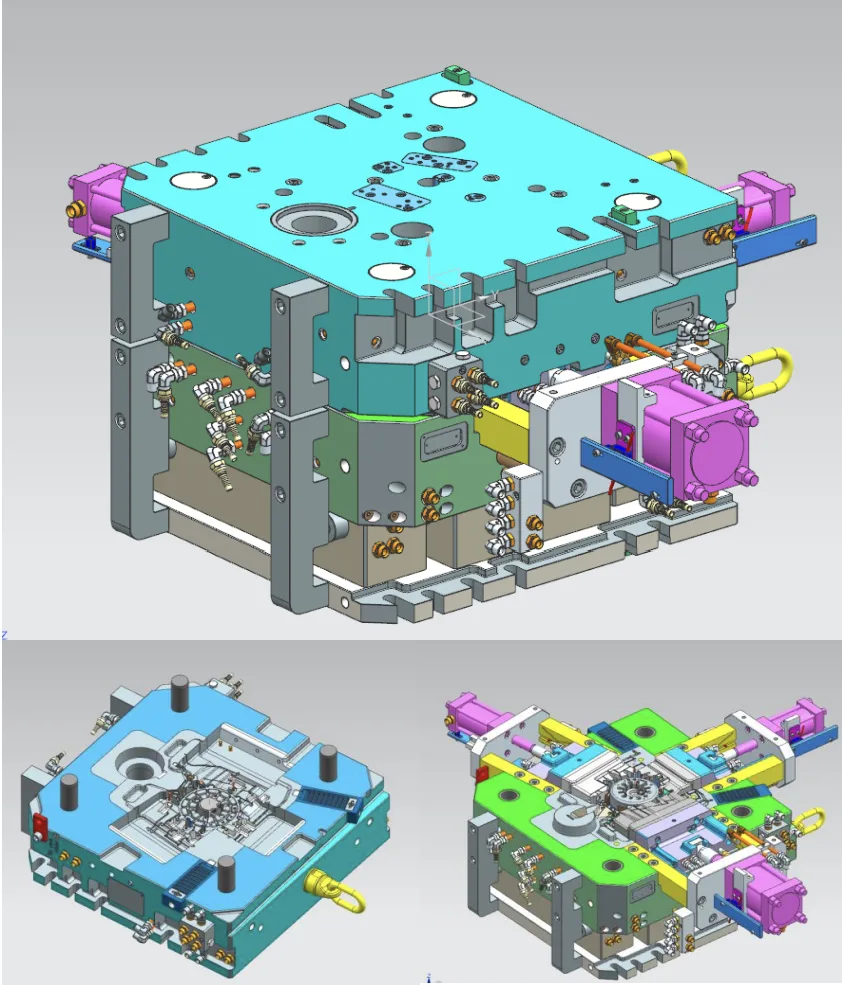
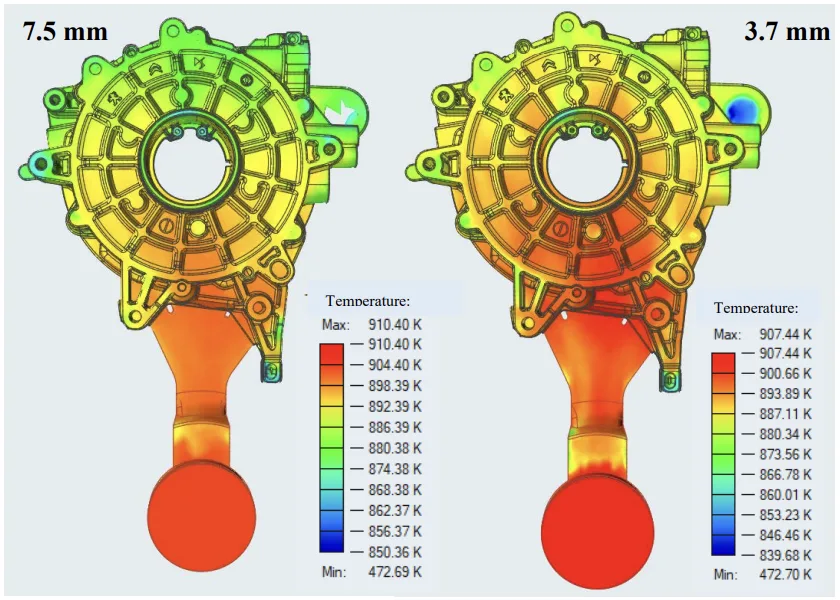
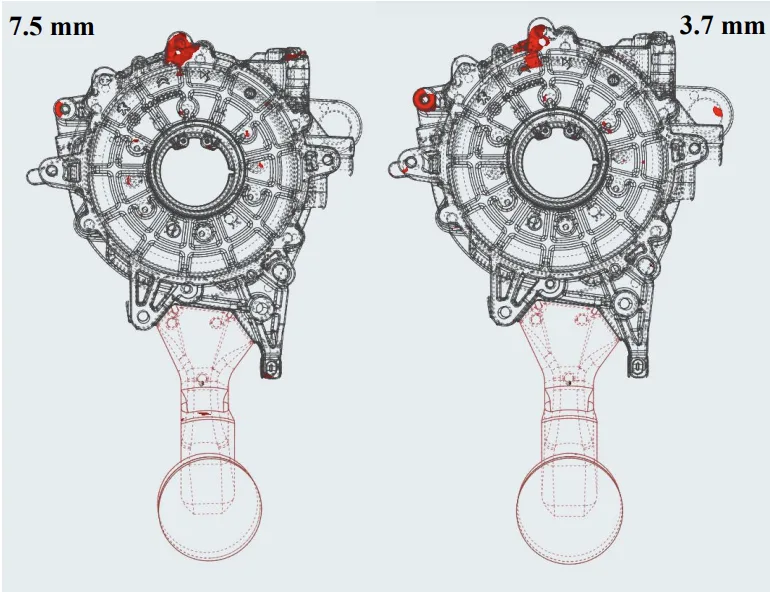
6. Conclusion:
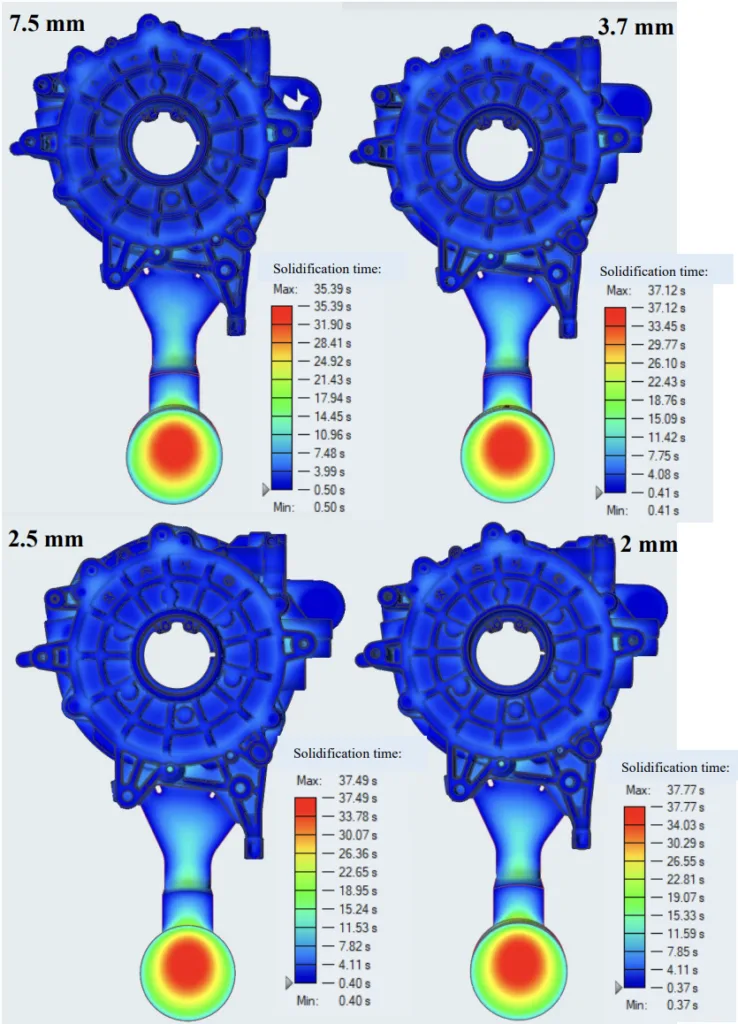
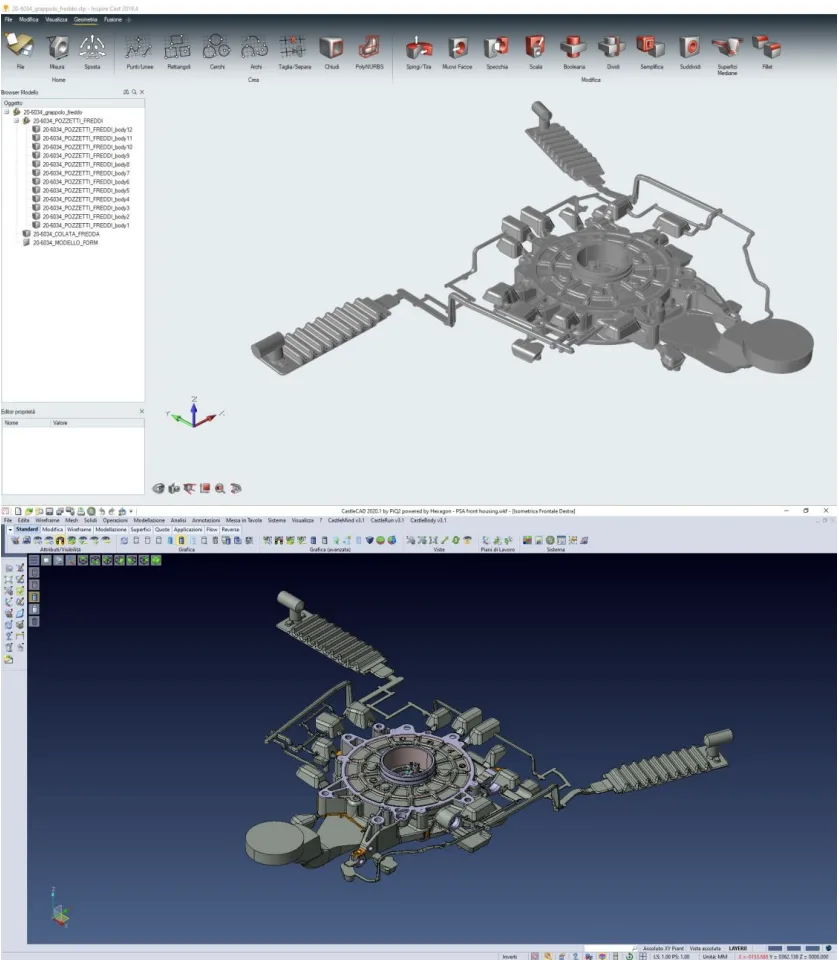
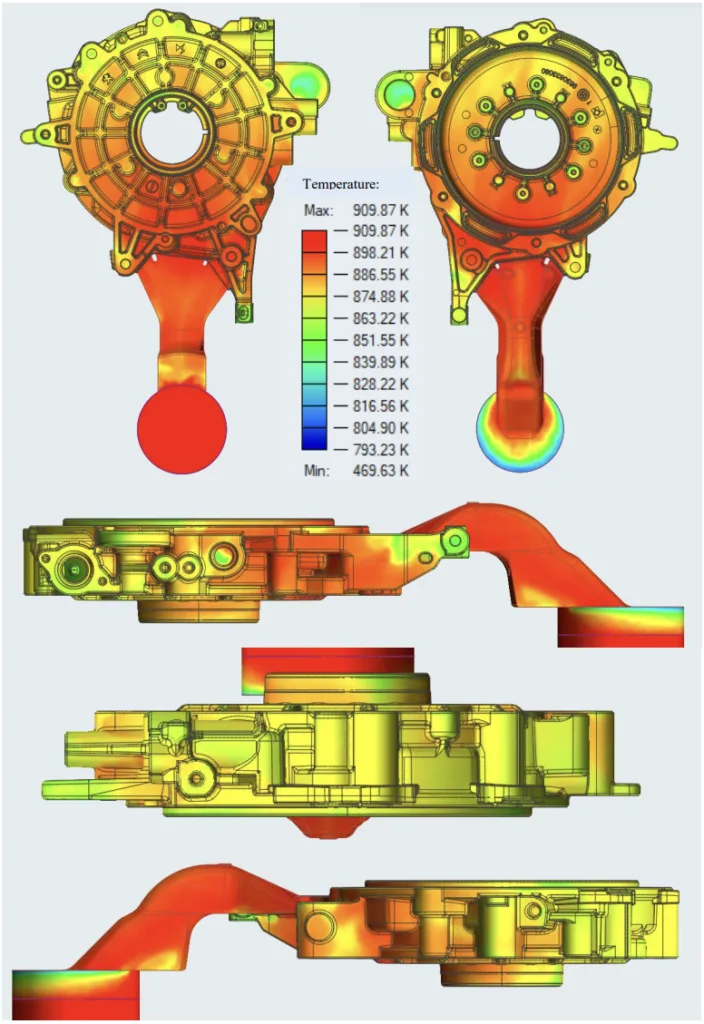
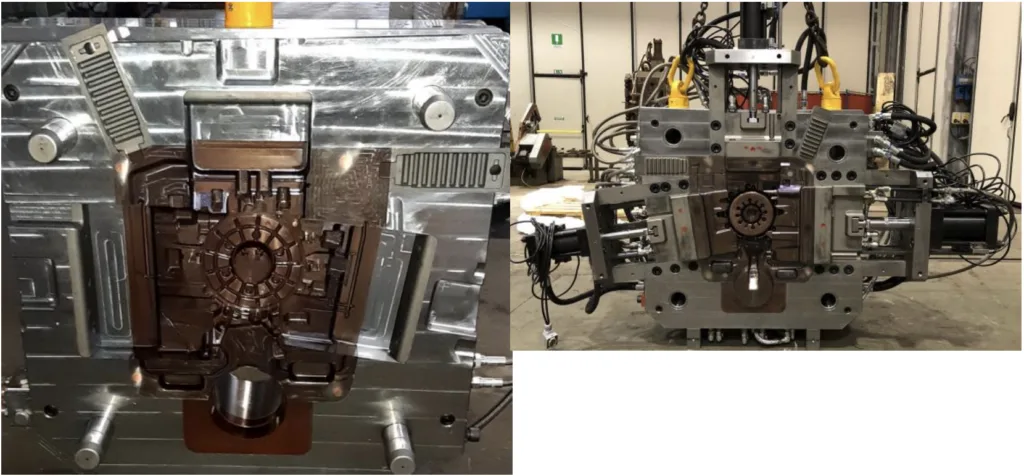
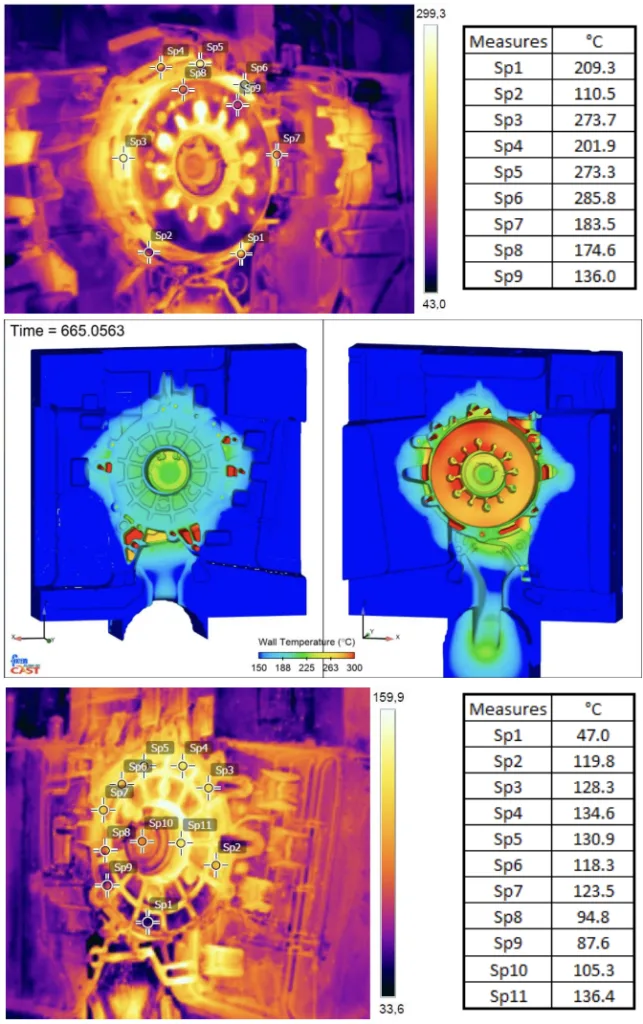
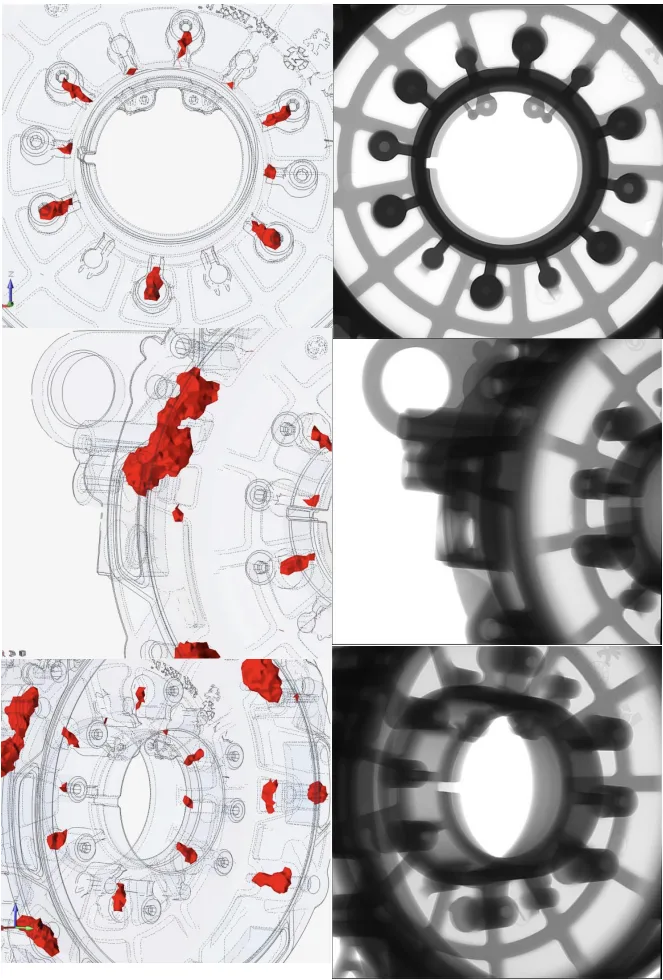
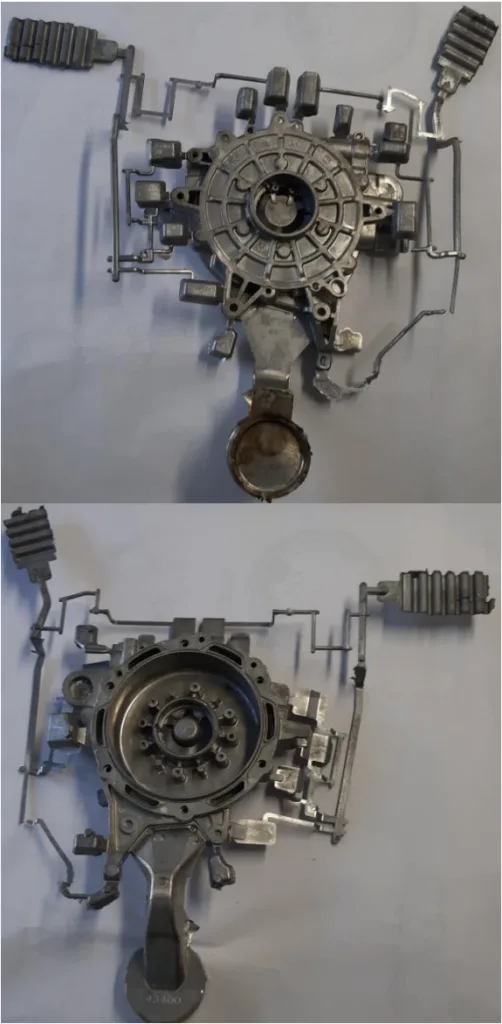
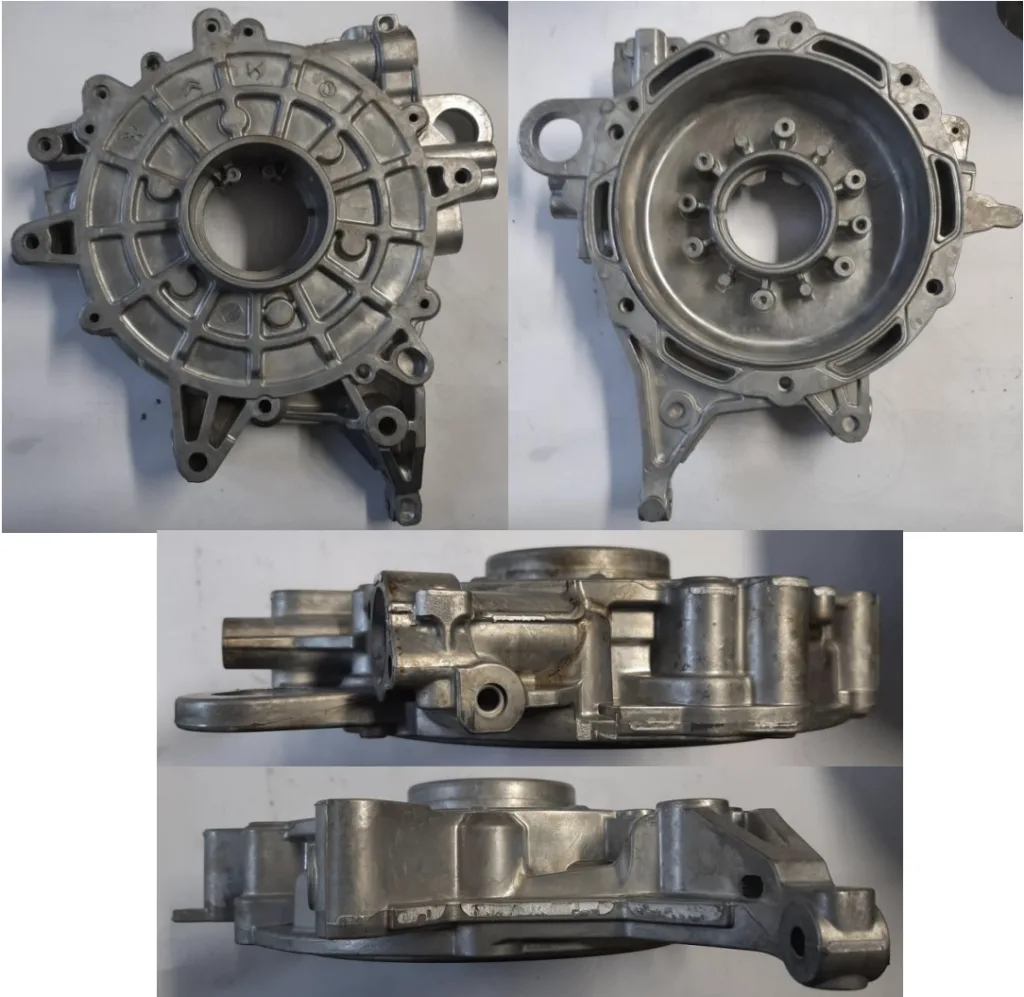
Summary of Main Results:
This research successfully simulated and validated the HPDC process for an electric motor housing using multiple software platforms. The study identified optimal mesh settings, compared software capabilities, and validated simulation predictions with experimental data. Key findings include the identification of potential defect areas, the importance of considering die thermal behavior, and the utility of PQ2 diagrams for process optimization. The research demonstrates the value of simulation tools in optimizing HPDC for novel automotive components.
Academic Significance of the Research:
This thesis contributes to the academic understanding of HPDC, particularly in the context of emerging automotive components like electric motor housings. It bridges the gap between traditional, experience-based HPDC practices and modern, simulation-driven approaches. The comparative software analysis provides valuable insights for researchers and practitioners in selecting appropriate simulation tools for die casting applications.
Practical Implications:
The findings offer practical guidelines for the sustainable production of electric transmission components via HPDC. The research demonstrates the effectiveness of simulation in optimizing process parameters, minimizing defects, and reducing production lead times and costs. The established workflow, combining simulation and experimental validation, serves as a valuable template for industrial implementation in die casting new and complex components.
Limitations of the Research
The research acknowledges several limitations:
- Simulation Accuracy: Simulations are inherently approximations of real-world processes and may not capture all complexities of HPDC.
- Computational Cost: High-fidelity simulations, particularly with fine meshes and complex models, demand significant computational resources and time.
- Software Limitations: Each software platform has inherent limitations, such as PIQ2 Castle's simplified thermal die cycling model and Inspire Cast's limited mesh control.
- Simplified Mold Model: The simulated mold was a simplified representation of the actual die, potentially affecting the accuracy of thermal simulations.
- Experimental Discrepancies: Differences between simulated and measured die temperatures were observed, attributed to experimental conditions and measurement limitations.
7. Future Follow-up Research:
- Directions for Follow-up Research
Future research directions include: - Advanced Overflow Optimization: Further refine overflow designs based on simulation insights to enhance air evacuation and minimize porosity.
- Cooling System Optimization: Investigate and optimize different cooling channel configurations and cooling strategies to improve thermal management and reduce solidification times.
- Die Erosion Mitigation: Conduct more detailed analysis of die erosion mechanisms and explore strategies to minimize die wear and extend die life.
- Stress Analysis Integration: Incorporate stress analysis simulations to predict residual stresses and potential component deformation during cooling.
- Software Enhancement: Further development of simulation software to address current limitations, such as improved thermal die cycling models and more user-friendly mesh generation tools.
- Areas Requiring Further Exploration
Areas requiring further exploration include: - Improved Die Thermal Simulation: Enhancing the accuracy of die thermal simulations by incorporating more detailed mold geometry and heat transfer models.
- Refined Mesh Generation Techniques: Developing more automated and robust mesh generation techniques to handle complex die casting geometries and improve mesh quality.
- Robust Simulation Workflows: Establishing standardized and validated simulation workflows for HPDC process design and optimization in industrial settings.
- Multi-physics Simulation: Integrating multi-physics simulations to couple fluid flow, heat transfer, and solidification with other relevant phenomena, such as stress and deformation.
8. References:
- Luigi Andreoni, “Quaderni della colata a pressione delle leghe d’alluminio”, EDIMET, 1993
- Buhler, “Ottimizzazione di processo”
- Andrea Manente, “Igiene delle leghe di alluminio”
- Altair University, “Learn Casting and Solidification with Altair Inspire Cast”
- Top 18 Die-Casting Defects and How to Fix Them, Five-Star Tooling, https://www.fstooling.com/what-cause-die-casting-defects-and-how-to-fix-them/
- EN AC-46000 (46000-F, AISi9Cu3(Fe)) Cast Aluminum, https://www.makeitfrom.com/material-properties/EN-AC-46000-46000-F-AISi9Cu3Fe-Cast-Aluminum/
- Flow 3D-cast, XC engineering, https://www.xceng.com/it/servizi/software-commerciali/flow-3d-cast/
- PIQ2, Castle, https://piq2.com/
- Fondalpress S.p.a, https://fondalpress.it/
9. Copyright:
- This material is "Gianluigi Lanzoni"'s paper: Based on "Simulation and validation of high-pressure die casting of an electric motor housing for automotive application".
- Paper Source: [DOI URL]
This material was summarized based on the above paper, and unauthorized use for commercial purposes is prohibited.
Copyright © 2025 CASTMAN. All rights reserved.