This introduction paper is based on the paper "Progress and prospects in Mg-alloy super-sized high pressure die casting for automotive structural components" published by "Journal of Magnesium and Alloys".
![Fig. 1. Mg-alloy super-sized die casting produced by Chongqing University, Millison Inc. and Boao Magnesium Aluminium Manufacturing Company Ltd. The geometry of the Mg-alloy super-sized castings has been withheld due to commercial confidentiality [5].](https://castman.co.kr/wp-content/uploads/image-2011-png.webp)
1. Overview:
- Title: Progress and prospects in Mg-alloy super-sized high pressure die casting for automotive structural components
- Author: Tian Li, Jiangfeng Song, Ang Zhang, Guoqiang You, Yan Yang, Bin Jiang, XianYue Qin, Cheng Xu, Fushen Pan
- Year of publication: 2023
- Journal/academic society of publication: Journal of Magnesium and Alloys
- Keywords: Mg alloy; Giga-casting; HPDC; Super-sized.
2. Abstract:
Since the introduction of Tesla's Giga-Casting process, the automotive industry has widely accepted the concept of super-sized structural components due to their significant potential for enhancing the light-weighting of both electric and internal combustion engine vehicles. These super-sized components can be further lightened by using Mg alloys because of their exceptional lightweight characteristics, with a density only two-thirds that of aluminium alloys and one-fourth that of steel. This outstanding attribute offers the attractive prospect of achieving significant weight reduction without compromising structural integrity. This review examines studies on the Mg-alloy High-Pressure Die Casting (HPDC) process, providing insights into the future prospects of incorporating Mg alloys into super-sized automotive HPDC components.
3. Introduction:
Driven by concerns over climate change and greenhouse gas emissions, the automotive industry is increasingly focused on electric vehicles (EVs). However, EVs are often heavier than internal combustion engine (ICE) vehicles, primarily due to battery weight, making vehicle light-weighting critical. Tesla's Giga-Casting technology, an advanced high-pressure die-casting (HPDC) process, enables the production of super-sized, single-piece structural components, significantly reducing part count, weight, and cost, as demonstrated by their consolidation of 171 parts into two underbody castings [1]. This success has spurred widespread industry adoption of super-sized components. Concurrently, interest is growing in using even lighter materials, particularly Magnesium (Mg) alloys, which are the lightest structural metals (density ~2/3 of Al, ~1/4 of steel). Mg alloys offer potential for substantial weight reduction without compromising structural integrity. A recent trial by Chongqing University, Millison Inc., and Boao Magnesium Aluminium Manufacturing Company Ltd successfully produced the world's largest Mg-alloy automotive die-castings (Fig. 1), demonstrating a 32% weight reduction compared to Al-alloy counterparts [5]. This review examines the Mg-alloy HPDC process for large-scale, thin-walled automotive components, exploring its potential and challenges for super-sized applications.
4. Summary of the study:
Background of the research topic:
The automotive industry faces pressure to reduce vehicle weight for improved efficiency and environmental performance, especially with the rise of heavier EVs. Super-sized structural components, pioneered by Tesla's Giga-Casting, offer a path to consolidation, cost reduction, and lightweighting using Al-alloys. Further weight reduction is possible by exploring lighter materials like Mg alloys.
Status of previous research:
Giga-Casting using Al-alloys is becoming established in the automotive industry [1, 2, 3, 4]. Research into Mg alloys for automotive applications has identified suitable alloy systems (e.g., AM, AZ, AJ, AE series) with desirable properties like castability and ductility, often in non-heat treatable (NHT) forms suitable for large structural parts [6-11]. Studies have investigated the influence of alloying elements (Al, Si, Zn, Sr, Ca, RE) on Mg properties [12-40]. Melt treatment techniques (degassing, flux refining, non-flux refining like electromagnetic, ultrasonic, flotation, filtration) are known to be crucial for Mg alloy casting quality [41-78]. Common defects in Mg HPDC, such as die soldering (though less severe than in Al), entrained oxides/bifilms, and hot tearing, have been studied [79-132]. Advanced casting techniques like vacuum HPDC (VADC/SVDC) and VACURAL are used to improve casting integrity [135-146]. Successful trial production of large Mg-alloy castings has been reported [5, Fig. 8].
Purpose of the study:
This review aims to examine the existing research on the Mg-alloy High-Pressure Die Casting (HPDC) process specifically for large-scale and thin-walled automotive structural components. It seeks to provide insights into the feasibility, advantages, challenges, and future prospects of incorporating Mg alloys into super-sized automotive HPDC components.
Core study:
This paper reviews several key areas related to Mg-alloy super-sized HPDC:
- Suitable Mg Alloys: Discusses various Mg alloy systems (Mg-Al-Si, Mg-Al-Zn, Mg-Al-Sr, Ca-containing, Mg-Al-RE) focusing on properties relevant to large, thin-walled NHT structural parts, such as castability, fluidity, ductility, and creep resistance [12-40].
- Melt Treatment: Covers the necessity and methods for treating Mg alloy melts before casting, including degassing techniques (inert gas sparging, active gas, vacuum) and inclusion removal methods (flux refining, non-flux refining like electromagnetic, ultrasonic, bubble flotation, filtration) [41-78].
- Major Defects: Analyzes common defects encountered in Mg-alloy HPDC, including die soldering (comparing susceptibility to Al-alloys), the formation of entrained oxides and bifilms due to Mg's reactivity and casting turbulence, and hot tearing phenomena (influence of alloy composition and casting conditions) [79-132].
- Casting Equipment/Techniques: Reviews the requirements for HPDC machines for large Mg parts (including potential for lower locking force compared to Al), and advanced processes like vacuum/super vacuum HPDC (VADC/SVDC) and VACURAL technology aimed at improving casting quality [2, 133-146].
- Current Applications & Potential: Presents examples of existing Mg-alloy HPDC automotive components and recent developments in super-sized Mg castings, highlighting the demonstrated potential [5, 17, 40, 133, 136, 147-152].
5. Research Methodology
Research Design:
This study is a comprehensive literature review. It synthesizes and evaluates existing knowledge from scientific papers, technical reports, and industry publications.
Data Collection and Analysis Methods:
The authors gathered information from a wide range of published sources, including peer-reviewed journals (like Journal of Magnesium and Alloys, Materials Science and Engineering A, Metallurgical and Materials Transactions), conference proceedings, technical papers (e.g., SAE Technical Papers), patents, and handbooks. The analysis involved summarizing key findings, identifying trends and correlations (e.g., alloy composition vs. properties/defects), comparing different processes and materials, highlighting challenges, and assessing the overall progress and future potential of the technology based on the collected evidence.
Research Topics and Scope:
The research focuses specifically on the application of High-Pressure Die Casting (HPDC) technology to Magnesium (Mg) alloys for producing super-sized automotive structural components. The scope includes:
- Selection criteria and properties of suitable Mg alloys (NHT, castability, ductility).
- Melt preparation techniques critical for Mg alloys (degassing, refining).
- Analysis of major casting defects pertinent to Mg HPDC (die soldering, oxides/bifilms, hot tearing) and their mitigation.
- Evaluation of casting equipment and advanced HPDC process variations (large presses, vacuum assist, VACURAL).
- Review of current and emerging applications of Mg-alloy HPDC in automotive structures, particularly large-scale ones.
6. Key Results:
Key Results:
- Mg alloys offer significant lightweighting potential for super-sized automotive components compared to Al-alloys (e.g., 32% reduction reported [5]), owing to their much lower density.
- Mg alloys demonstrate excellent mould filling capabilities in HPDC, enabling the production of very large components with thin walls (down to 1.8 mm) and long filling distances (up to 1.2 m) [Fig. 8, 150].
- Alloys like AE44 show promise for structural parts due to a good balance of fluidity, strength, and ductility [39, 150, Fig. 7]. Non-heat treatable (NHT) alloys are preferred for large structural components.
- Effective melt treatment (degassing and inclusion removal) is essential for producing high-quality Mg castings due to Mg's high reactivity and susceptibility to hydrogen pickup [41-78].
- Mg alloys exhibit significantly lower susceptibility to die soldering compared to Al alloys in HPDC, allowing for a wider processing window and facilitating the casting of thinner sections [88, 89].
- The high reactivity of Mg makes melts prone to oxidation and bifilm defect formation during the turbulent filling of HPDC; specialized techniques like vacuum HPDC (VADC/SVDC) or VACURAL can mitigate this but face scalability challenges for super-sized parts [90-105, 135-146].
- Hot tearing is a potential defect influenced by alloy composition (freezing range, eutectic phases) and casting conditions (mould temperature, cooling rate, inclusions, grain structure); some alloys like AZ91 show relatively low susceptibility [Table 2, 106-132].
- Due to lower density, casting equivalent-volume Mg parts may require HPDC machines with lower locking forces compared to Al parts, potentially reducing equipment costs [Section 5.1].
- Several examples demonstrate the successful application of Mg-alloy HPDC for various automotive components, including recent trials on super-sized parts like underbodies and battery enclosures [Fig. 1, Fig. 8, 40, 133, 147-152].
![Fig. 2. Microstructure of AZ91D with and without degassing under different casting conditions [41].](https://castman.co.kr/wp-content/uploads/image-2012-png.webp)
![Fig. 3. the die soldering issue occurred during a 1.6 mm ultra-thin-walled HPDC test [86].](https://castman.co.kr/wp-content/uploads/image-2013-png.webp)
![Fig. 4. Sketch of a surface-film entrainment event in a light alloy casting [44,99].](https://castman.co.kr/wp-content/uploads/image-2014-png.webp)
![Fig. 5. Sketch of VACURAL Technology [145].](https://castman.co.kr/wp-content/uploads/image-2015-png.webp)
![Fig. 6. Sketch of the casting technique used by Gibbs Die Casting to cast Mg alloys [144].](https://castman.co.kr/wp-content/uploads/image-2016-png.webp)
![Fig. 7. A shock tower cast using AE44 alloy, dimensions 571 mm × 210 mm × 352 mm. (a) Appearance of the shock tower, with numbers denoting test bar sampling locations. (b) Tensile properties of the shock tower cast at different switchover positions of 560 mm, 580 mm, 600 mm [150].](https://castman.co.kr/wp-content/uploads/image-2017-png.webp)
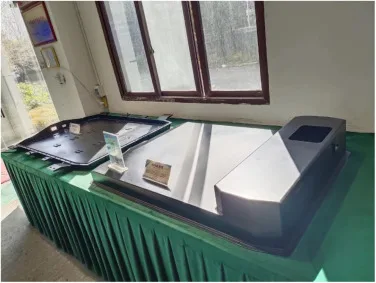
Figure Name List:
- Fig. 1. Mg-alloy super-sized die casting produced by Chongqing University, Millison Inc. and Boao Magnesium Aluminium Manufacturing Company Ltd. The geometry of the Mg-alloy super-sized castings has been withheld due to commercial confidentiality [5].
- Fig. 2. Microstructure of AZ91D with and without degassing under different casting conditions [41].
- Table 1 Vapour pressure of magnesium at various temperatures [49].
- Fig. 3. the die soldering issue occurred during a 1.6 mm ultra-thin-walled HPDC test [86].
- Fig. 4. Sketch of a surface-film entrainment event in a light alloy casting [44,99].
- Table 2 Hot tearing ratings of various commercial Mg alloys. Higher rating indicates higher HTS [114].
- Fig. 5. Sketch of VACURAL Technology [145].
- Fig. 6. Sketch of the casting technique used by Gibbs Die Casting to cast Mg alloys [144].
- Fig. 7. A shock tower cast using AE44 alloy, dimensions 571 mm x 210 mm x 352 mm. (a) Appearance of the shock tower, with numbers denoting test bar sampling locations. (b) Tensile properties of the shock tower cast at different switchover positions of 560 mm, 580 mm, 600 mm [150].
- Fig. 8. Mg-alloy battery enclosure components cast by Chongqing Qianhe Magnesium Tech Co., with a 1.8 mm thickness, and 1.2 m * 0.8 m size.
7. Conclusion:
The increasing demand for vehicle lightweighting positions Mg alloys as highly attractive materials for the automotive industry, particularly for the emerging trend of super-sized structural components produced via HPDC. This review highlighted the critical aspects of utilizing Mg alloys in this context. Mg alloys possess remarkable mould-filling capabilities, enabling the casting of extremely large components with thin walls (e.g., 1.8 mm) over long filling distances (e.g., 1.2 m). However, achieving consistent quality in these super-sized parts necessitates effective control over potential defects (like oxides, bifilms, hot tears) and microstructural features, demanding careful management of melt treatment and casting process parameters. Overall, Mg alloys demonstrate significant potential for producing super-sized automotive components, offering substantial lightweighting benefits, although further research and development are needed to fully realize this potential and address associated challenges.
8. References:
- [1] E. Musk, Tesla 2020 Annual Meeting of Stockholders and Battery Day, 2020.
- [2] T.A. Baser, E. Umay, V. Akıncı, in: International Conference on Technology, Engineering and Science, 2022, pp. 79-87.
- [3] H. Nakajima, Toyota Technical Workshop, Toyota Motor Corporation, Toyota City, Japan, 2023.
- [4] I. Dnistran, Toyota Showcases its Own Giga Casting in a Bid to Lower EV Costs, 2023 [cited 2023 3rd Aug] Available from: https://insideevs.com/news/671943/toyota-giga-casting/.
- [5] Z. Tong, South China Morning Post, South China Morning Post, Singapore, 2023.
- [6] Das, S.K., H.W. Hayden, and G.B. Barthold, Development of Non-Heat-Treatable Automotive Aluminum Sheet Alloys. 2000. p. 913-919.
- [7] A.W. Shah, et al., Int. J. Metalcast. (2023).
- [8] X.Z. Zhu, et al., J. Mater. Sci. 56 (18) (2021) 11083-11097.
- [9] RHEINFELDEN-ALLOYSHandbook Die Casting Aluminium Alloys, 2023 Alloys for Pressure Die Casting 2016 [citedAug 14]; Available from: https://rheinfelden-alloys.eu/wp-content/uploads/2017/01/Handbook-Die-Casting-Aluminium-Alloys_RHEINFELDEN-ALLOYS_2016_EN.pdf.
- [10] AlcoaAlcoa Specialty Alloys: C611 EZCastTM, 2022 [cited 2023 Aug 14]; Available from: https://www.alcoa.com/global/en/what-we-do/aluminum/cast-products/pdfs/ALC-C611-EzCast-SellSheet.pdf .
- [11] AlcoaAlcoa Specialty Alloys: C891F EZCastPlusTM, 2022 [cited 2023 Aug 14]; Available from: https://www.alcoa.com/global/en/what-we-do/aluminum/cast-products/pdfs/ALC-C891F-EzCastPlus-SellSheet.pdf.
- [12] A.L. Bowles, Q. Han, J.A. Horton, TMS (2005) 99-104.
- [13] Y.-Z. Lü, Q.-D. Wang, X.-Q. Zeng, W.-J. Ding, Y.-P. Zhu, Mater. Sci. Technol 17 (2) (2013) 207-214.
- [14] M. Pekguleryuz, M. Celikin, Int. Mater. Rev. 55 (4) (2013) 197-217.
- [15] S. Candan, E. Candan, Trans. Nonferrous Metals Soc. China 27 (8) (2017) 1725-1734.
- [16] A. LUO, M.O. Pekguleryuz, J. Mater. Sci. 29 (1994) 5259-5271.
- [17] J.P. Weiler, J. Magnes. Alloys 9 (1) (2021) 102-111.
- [18] Q.C. Jiang, et al., Mater. Sci. Eng.: A 392 (1-2) (2005) 130-135.
- [19] L.Y. Wei, G.L. Dunlop, H. Westengen, Mater. Sci. Technol. 12 (9) (1996) 741-750.
- [20] M. Easton, et al., Mater. Sci. Forum 828-829 (2015) 3-8.
- [21] M.O. Pekguleryuz, M.M. Avedesian, Inst. Magnes. Technol. 42 (12) (1992) 679-686.
- [22] V.E. Bazhenov, et al., J. Magnes. Alloys 9 (5) (2021) 1567-1577.
- [23] V.E. Bazhenov, et al., J. Magnes. Alloys 8 (1) (2020) 184-191.
- [24] G. Chen, et al., Trans. Nonferrous Metals Soc. China 21 (4) (2011) 725-731.
- [25] K. Hirai, et al., Mater. Sci. Eng.: A 403 (1-2) (2005) 276-280.
- [26] C. Jingyang, et al., Spec. Cast. Nonferrous Alloys 8 (2005) 454.
- [27] H.L. Zhao, S.K. Guan, F.Y. Zheng, J. Mater. Res. 22 (9) (2011) 2423-2428.
- [28] Y. Turen, Mater. Des. 49 (2013) 1009-1015.
- [29] E. Baril, P. Labelle, M.O. Pekguleryuz, Res. Summary 55 (2003) 34-39.
- [30] M.H. Kim, et al., Mater. Sci. Forum 419-422 (2003) 575-580.
- [31] S.-Y. Chang, J.-C. Choi, Met. Mater. 4 (2) (1998) 165-171.
- [32] C.D. Yim, et al., J. Mater. Sci. (8) (2006) 41.
- [33] Y. Nakaura, A. Watanabe, K. Ohori, Mater. Trans. 47 (4) (2006) 1031-1039.
- [34] Y. Fu, et al., J. Rare Earths 35 (5) (2017) 503-509.
- [35] Y. Cui, et al., Materials 13 (16) (2020).
- [36] Y. Lu, et al., Mater. Sci. Eng. A 278 (2000) 66-76.
- [37] W.Q. dong, et al., Trans. Nonferrous Metals Soc. China 02 (2000) 235-239.
- [38] Q. Hua, et al., Mater. Sci. Eng.: A 444 (1-2) (2007) 69-74.
- [39] T. Rzychoń, et al., Mater. Charact. 60 (10) (2009) 1107-1113.
- [40] B. Liu, et al., J. Magnes. Alloys 11 (1) (2023) 15-47.
- [41] E. Zhang, G.J. Wang, Z.C. Hu, Mater. Sci. Technol. 26 (10) (2010) 1253-1258.
- [42] Z.C. Hu, E.L. Zhang, S.Y. Zeng, Mater. Sci. Technol. 24 (11) (2008) 1304-1308.
- [43] A. Elsayed, et al., Trans. Am. Foundry Soc. 120 (2012) 423-429, Vol 120.
- [44] T. Li, J.M.T. Davies, D. Luo, Metall. Mater. Trans. B-Process Metall. Mater. Process. Sci. 52 (5) (2021) 3093-3106.
- [45] S.E. Housh, V. Petrovich, SAE Technical Paper, 920071, SAE international, Warrendale, Pa, USA, 1992.
- [46] S.E. Housh, V. Petrovich, Magnesium Refining: A Fluxless Alternative, 1992 SAE Technical Paper.
- [47] J. Thomson, et al., Transactions of the American Foundry Society and the One Hundred Eighth Annual Metalcasting Congress, 2004.
- [48] E.F. Emley, Metals Technol. 3 (1) (1976) 118-127.
- [49] S. Bell, et al., the Minerals and Metals Sector of Natural Resources Canada, 2006.
- [50] Y. Luo, Appl. Math. Model. 37 (9) (2013) 6177-6182.
- [51] T. Watanabe, et al., J. Jpn. Inst. Light Metals 26 (6) (1976) 266-272.
- [52] H.X. Cao, et al., J. Magnes. Alloys 7 (3) (2019) 370-380.
- [53] L.F. Zhang, T. Dupont, State of the Art in the Refining and Recycling of Magnesium, 2007 p. 25-+.
- [54] F. Pan, et al., J. Magnes. Alloys 4 (1) (2016) 8–14.
- [55] J. Wu, et al., Mater. Res. Express 9 (3) (2022) 032001.
- [56] Moon, B.G., B.S. You, and Koh. Kiho, in Magnesium Technology 2013, N. Hort, et al., Editors. 2013, John Wiley & Sons: New Jersey.
- [57] S.M. Patel, M.M. Patel, V.J. Rao, Mater. Res. Express 8 (11) (2021).
- [58] S.M. Patel, M.M. Patel, V.J. Rao, Mater. Res. Express 8 (11) (2021) 116503.
- [59] F.S. Pan, et al., J. Magnes. Alloys 4 (1) (2016) 8-14.
- [60] G.-h. Wu, et al., Trans. Nonferrous Metals Soc. China 20 (11) (2010) 2037-2045.
- [61] N. El-Kaddah, A.D. Patel, T.T. Natarajan, JOM 47 (5) (1995) 46-49.
- [62] N. Balasubramani, et al., J. Magnes. Alloys 9 (3) (2021) 829-839.
- [63] A. Kumar, P.M. Pandey, J. Magnes. Alloys 9 (6) (2021) 1989-2008.
- [64] Y. Chen, et al., J. Magnes. Alloys 10 (3) (2022) 614-626.
- [65] P. Emadi, B. Andilab, C. Ravindran, J. Magnes. Alloys 10 (12) (2022) 3397-3405.
- [66] H. Peng, et al., J. Magnes. Alloys 8 (2) (2020) 552-563.
- [67] A.R. Eivani, et al., J. Magnes. Alloys 9 (4) (2021) 1304-1328.
- [68] X. Ding, et al., J. Magnes. Alloys 11 (3) (2023) 903-915.
- [69] J.Y. Zhang, et al., J. Magnes. Alloys 9 (4) (2021) 1187-1200.
- [70] G.I. Eskin, Ultrason. Sonochem. 8 (3) (2001) 319-325.
- [71] Y.J. Chen, W.N. Hsu, J.R. Shih, Mater. Trans. 50 (2) (2009) 401-408.
- [72] Z.W. Shao, et al., Met. Mater. Int. 18 (2) (2012) 209-215.
- [73] Z.-W. Shao, et al., Trans. Nonferrous Metals Soc. China 20 (2010) s382-s387.
- [74] M. Khosro Aghayani, B. Niroumand, J. Alloys Compd. 509 (1) (2011) 114-122.
- [75] V. PETROVICH, W. MERCER E., W. GREEN, Patentscope, Espacenet, E.P. Office, Editor, U.S, 1993.
- [76] J. Zha, et al., in: Manufacturing Science and Technology, Pts 1-3, Р.С. Wang, 2011, pp. 2151-2154. Editors.
- [77] J. Wang, et al., Trans. Nonferrous Metals Soc. China 20 (7) (2010) 1235-1239.
- [78] J.L. Zha, et al., Adv. Mat. Res. 295-297 (2011) 2151-2154.
- [79] H. Huang, et al., Int. J. Cast Met. Res. 26 (4) (2013) 213-219.
- [80] Y.L. Li, et al., J. Mater. Sci. Technol. 33 (6) (2017) 558-566.
- [81] A. Juriani, Casting Defects Analysis in Foundry and Their Remedial Measures with Industrial Case Studies, 2015.
- [82] Akhyar, et al., Metalurgija 61 (2) (2022) 309-312.
- [83] Q.Y. Han, China Foundry 12 (2) (2015) 136-143.
- [84] S. Shankar, D. Apelian, Metall. Mater. Trans. B-Process Metall. Mater. Process. Sci. 33 (3) (2002) 465-476.
- [85] Z.W. Chen, Mater. Sci. Eng. a-Struct. Mater. Properties Microstruct. Process. 397 (1-2) (2005) 356-369.
- [86] Z.C. Niu, et al., J. Mater. Process. Technol. (2022) 303.
- [87] D. Schwam, A. Miller, Thin-Wall and High-Strength Die Casting Alloys, Defence Technical Information Center, 2017.
- [88] A.L. Bowles, Q. Han, J.A. Horton, et al., in: S.N. Mathaudhu, et al. (Eds.), Essential Readings in Magnesium Technology, Springer International Publishing, Cham, 2016, pp. 187-192. Editors.
- [89] C. Tang, M.Z. Jahedi, M. Brandt, the 6th International Tooling Conference, Karlstad Univ, Karlstad, Sweden, 2002.
- [90] M.M. Jalilvand, et al., J. Magnes. Alloys 8 (1) (2020) 219-230.
- [91] C.L. Cheng, et al., J. Magnes. Alloys 8 (4) (2020) 1281-1295.
- [92] S. Ma, et al., J. Magnes. Alloys 8 (3) (2020) 819-831.
- [93] M.M. Jalilvand, et al., J. Magnes. Alloys 10 (6) (2022) 1704-1717.
- [94] W.D. Griffiths, N.W. Lai, Metall. Mater. Trans. a-Phys. Metall. Mater. Sci. 38A (1) (2007) 190-196.
- [95] T. Li, W.D. Griffiths, J. Chen, Metall. Mater. Trans. a-Phys. Metall. Mater. Sci. 48A (11) (2017) 5516-5528.
- [96] T. Li, J.M.T. Davies, X. Zhu, J. Mater. Sci. 56 (29) (2021) 16671-16685.
- [97] T. Li, J.M.T. Davies, X.Z. Zhu, J. Magnes. Alloys 10 (1) (2022) 129-145.
- [98] C. Cingi, Mold-metal Reactions in Magnesium Investment Castings, Helsinki University of Technology, 2006.
- [99] J. Campbell, Castings, Butterworth-Heinemann, Oxford, 2004.
- [100] A.R. Mirak, et al., Int. J. Cast Met. Res. 20 (4) (2007) 215-220.
- [101] T. Li, J.M.T. Davies, Metall. Mater. Trans. A 51 (10) (2020) 5389-5400.
- [102] D. Dispinar, J. Campbell, Int. J. Cast Met. Res. 19 (1) (2006) 5–17.
- [103] I.H. Kalkan, et al., Shape Casting, Springer International Publishing, Cham, 2019.
- [104] J. Olofsson, A. Bjurenstedt, S. Seifeddine, Shape Casting, Springer International Publishing, Cham, 2019.
- [105] X. Li, S.M. Xiong, Z. Guo, J. Mater. Process. Technol. 231 (2016) 1-7.
- [106] G. Cao, I. Haygood, S. Kou, Metall. Mater. Trans. a-Phys. Metall. Mater. Sci. 41A (8) (2010) 2139-2150.
- [107] G. Cao, et al., Metall. Mater. Trans. a-Phys. Metall. Mater. Sci. 41A (3) (2010) 706-716.
- [108] Z.S. Zhen, et al., Int. J. Cast Met. Res. 22 (1-4) (2009) 331-334.
- [109] X.D. Du, et al., J. Magnes. Alloys 11 (2) (2023) 694-705.
- [110] Y. Zhou, et al., J. Magnes. Alloys 8 (4) (2020) 1176-1185.
- [111] G.J. Zhang, et al., J. Magnes. Alloys 7 (2) (2019) 272-282.
- [112] Z.Z. Yang, et al., J. Magnes. Alloys 6 (1) (2018) 44-51.
- [113] Q.S. Yang, et al., J. Magnes. Alloys 2 (1) (2014) 8-12.
- [114] J.F. Song, et al., J. Magnes. Alloys 4 (3) (2016) 151-172.
- [115] K. Strobel, et al., Int. J. Cast Met. Res. 23 (2) (2010) 81-91.
- [116] X. Su, et al., Int. J. Metalcast. 15 (2) (2021) 576-586.
- [117] G. Cao, S. Kou, Mater. Sci. Eng. a-Struct. Mater. Properties Microstruct. Process. 417 (1-2) (2006) 230-238.
- [118] Z.S. Zhen, et al., Light Metals Technol. 618-619 (2009) 533-540.
- [119] L. Zhou, et al., Int. J. Cast Met. Res. 24 (3-4) (2011) 170-176.
- [120] L. Zhou, et al., Magnes. Technol. 2011 (2011) 125-130.
- [121] J.F. Song, et al., Metall. Mater. Trans. a-Phys. Metall. Mater. Sci. 46A (12) (2015) 6003-6017.
- [122] A. Srinivasan, et al., Trans. Indian Inst. Met. 65 (6) (2012) 701-706.
- [123] M.A. Easton, et al., Metall. Mater. Trans. a-Phys. Metall. Mater. Sci. 45A (8) (2014) 3586-3595.
- [124] Z. Wang, et al., Metall. Mater. Trans. a-Phys. Metall. Mater. Sci. 46A (5) (2015) 2108-2118.
- [125] G. Cao, S. Kou, Metall. Mater. Trans. a-Phys. Metall. Mater. Sci. 37A (12) (2006) 3647-3663.
- [126] G. Zhang, et al., Materwiss Werksttech 50 (12) (2019) 1471-1483.
- [127] S.K. Rathi, A. Sharma, M. Di Sabatino, Eng. Fail. Anal. 79 (2017) 592-605.
- [128] L. Bichler, et al., Int. J. Metalcast. 2 (1) (2008) 43-56.
- [129] Z. Wang, et al., J. Mater. Sci. 49 (1) (2014) 353-362.
- [130] S. Li, D. Apelian, Int. J. Metalcast. 5 (1) (2011) 23-40.
- [131] J.M. Middleton, H.T. Protheroe, J. Iron Steel Institute 168 (4) (1951) 384-398.
- [132] G.H. Wu, et al., Acta Metall. Sinica 58 (4) (2022) 385-399.
- [133] Sophia, F., et al., in Magnesium Alloys, T. Tomasz Arkadiusz, C.-A. Katarzyna, and J. Ewa, Editors. 2023, IntechOpen: Rijeka. p. Ch. 2.
- [134] HPMMACHINERYHPM North America to Build 4500 Ton Die Cast Machine [cited 2023 Nov 19th]; Available from:, 2015. https://www.yizumi-hpm.com/hpm-north-america-to-build-4500-ton-die-cast-machine/.
- [135] H. Cao, et al., Vacuum 146 (2017) 278-281.
- [136] A.A. Luo, A.K. Sachdev, D. Apelian, J. Mater. Process. Technol. (2022) 306.
- [137] Cosma-International. Aluminum high pressure die casting. [cited 2023 18 Aug]; Available from: https://www.magna.com/docs/default-source/default-document-library/cosma_casting_brochure_english.pdf?sfvrsn=0.
- [138] T. Le, et al., Mater. Res. Express 7 (11) (2020) 116513.
- [139] X. Liu, et al., J. Mater. Res. Technol. 23 (2023) 4293-4306.
- [140] C. Ma, et al., J. Magnes. Alloys 11 (2) (2023) 753-761.
- [141] Z.-q. Wang, et al., Trans. Nonferrous Metals Soc. China 24 (12) (2014) 3762-3768.
- [142] X. Dong, X. Zhu, S. Ji, J. Mater. Process. Technol. 266 (2019) 105-113.
- [143] V. Nandakumar, Process and Tool Design for the High Integrity Die Casting of Aluminum and Magnesium Alloys, The Ohio State University, 2014.
- [144] A.A. Luo, J. Magnes. Alloys 1 (1) (2013) 2-22.
- [145] FRECH, Vacural Technol. (2023) [cited 2023 18th Aug]; Available from: https://www.frechusa.com/vacural-technology.
- [146] Foundry-Lexicon, Vacural Process (2023) [cited 2023 18 Aug]; Available from: https://www.giessereilexikon.com/en/foundry-lexicon/Encyclopedia/show/vacural-process-4629/?cHash=fa70abc99c24ba84803fb708ad2266a7.
- [147] J.P. Weiler, J. Magnes. Alloys 7 (2) (2019) 297-304.
- [148] M. Abate, M. Willman, Use of Cast Magnesium Back frames in Automotive Seating, 2005 SAE Technical Paper.
- [149] J.P. Weiler, Contemporary Magnesium Die-Casting Research and Technology: A Canadian Viewpoint, Springer International Publishing, Cham, 2021.
- [150] W. Xueyang, et al., Spec. Cast. Nonferrous Alloys 42 (04) (2022) 467-472.
- [151] X. Chen, et al., Cast Magnesium Subframe Development-Bolt Load Retention, 2021 SAE Technical Paper.
- [152] J. Aragones, et al., Development of the 2006 Corvette z06 Structural Cast Magnesium Crossmember, 2005 SAE Technical Paper.
9. Copyright:
- This material is a paper by "Tian Li et al.". Based on "Progress and prospects in Mg-alloy super-sized high pressure die casting for automotive structural components".
- Source of the paper: https://doi.org/10.1016/j.jma.2023.11.003
This material is summarized based on the above paper, and unauthorized use for commercial purposes is prohibited.
Copyright © 2025 CASTMAN. All rights reserved.