This article introduces the paper "High Thermal Conductivity Steel and its Application to Die Casting Tools" presented at the NADCA Die Casting Congress & Exposition in 2012.
1. Overview:
- Title: High Thermal Conductivity Steel and its Application to Die Casting Tools
- Authors: K. Namiki, Masamichi. Kawano (Daido Steel Co., Ltd.), Thomas Schade (International Mold Steel Inc. Hebron, Kentucky)
- Publication Year: 2012
- Publishing Journal/Academic Society: NADCA Die Casting Congress & Exposition / North American Die Casting Association
- Keywords: High thermal conductivity steel, die casting tools, cycle time reduction, heat checking resistance, DHA-THERMO, H13 steel, die casting molds.
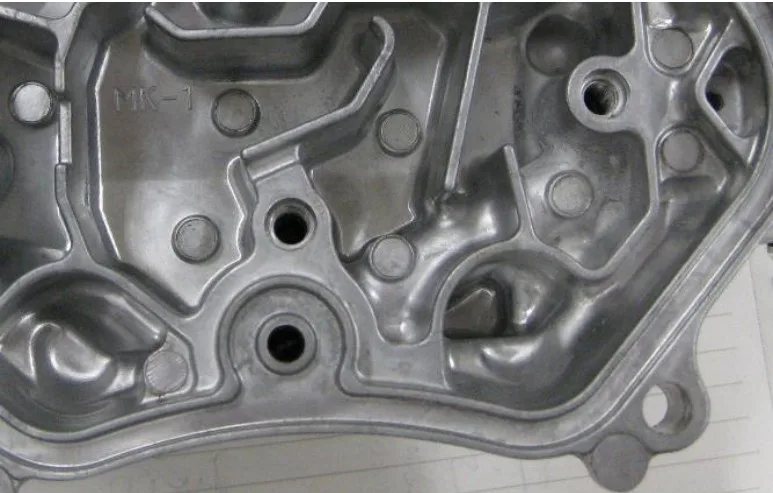
2. Research Background:
- Social/Academic Context of the Research Topic:
- The die casting industry faces increasing demands to produce high-quality products while simultaneously shortening cycle times.
- The growing use of lightweight die-cast components, particularly in the automotive sector (e.g., engine blocks, transmission cases), intensifies the need for reduced cycle times to improve fuel efficiency and reduce costs.
- Achieving fine cast microstructures with fewer defects in shorter solidification times is crucial for expanding the application of die-cast products in automobiles.
- Limitations of Existing Research:
- While Tungsten (W) alloys offer high thermal conductivity, their high cost limits their widespread application in die casting tools.
- Low alloy steels are known to have higher thermal conductivity than the commonly used 5%Cr-1%Mo type die casting mold steel H13. However, these low alloy steels typically have lower hardness (usually below 40 HRC) due to low carbon and chromium content, restricting their use to smaller molds with less thermal stress.
- Non-ferrous materials like Copper-Beryllium (Cu-Be) and W alloys, despite superior thermal conductivity, present challenges. Cu-Be alloys are mainly used for plastic injection molds, and W alloys, while having about three times higher thermal conductivity than H13 (e.g., Anviloy), are expensive, brittle, and difficult to machine.
- Necessity of the Research:
- To overcome the limitations of existing materials, there is a need for a new die casting tool material that combines high thermal conductivity with high hardness.
- Such a material would enable faster heat extraction from molds, leading to shorter cycle times, improved product quality (finer microstructure, fewer defects), and enhanced mold durability (heat checking and soldering resistance).
3. Research Purpose and Research Questions:
- Research Purpose:
- To introduce and evaluate DHA-THERMO, a newly developed high thermal conductivity, hardened and tempered hot work die steel, specifically designed for die casting applications.
- To demonstrate the fundamental properties of DHA-THERMO and showcase its application in various die casting tools, comparing its performance against conventional materials like H13 steel.
- Key Research Questions:
- How does the thermal conductivity of DHA-THERMO compare to that of H13 steel at both room and elevated temperatures relevant to die casting operations?
- What is the hardness achievable with DHA-THERMO, and how does it vary with tempering temperature compared to H13 steel?
- How does the hardenability of DHA-THERMO compare to H13 steel?
- In actual die casting tests, how does DHA-THERMO perform in terms of sprue core temperature, solidified biscuit microstructure, and heat check resistance compared to H13 steel?
- What are the practical benefits of using DHA-THERMO in die casting tools, such as quality improvement, cycle time reduction, and cost reduction?
- Research Hypotheses:
- DHA-THERMO will exhibit significantly higher thermal conductivity than H13 steel, leading to improved heat dissipation in die casting molds.
- DHA-THERMO will achieve a high hardness level (around 48 HRC) suitable for die casting tool applications through quenching and tempering.
- The application of DHA-THERMO in die casting tools will result in reduced cycle times due to faster solidification, improved product quality due to finer microstructure, and enhanced mold life due to improved heat check resistance.
- DHA-THERMO can serve as a cost-effective alternative to expensive W alloys in certain die casting applications.
4. Research Methodology:
- Research Design:
- The research employed an experimental approach, involving material characterization tests and die casting performance evaluations.
- The study compared the properties and performance of DHA-THERMO with those of conventional die casting tool materials, primarily H13 steel, and in some cases, W alloy (Anviloy).
- Data Collection Method:
- Material Property Testing:
- Thermal Conductivity Measurement: Thermal conductivity was measured at room temperature and elevated temperatures to assess the heat transfer capability of DHA-THERMO and H13.
- Hardness Testing: Hardness measurements were conducted to evaluate the hardness of DHA-THERMO and H13 after different tempering temperatures.
- Hardenability Evaluation: Continuous Cooling Transformation (CCT) diagrams were used to assess the hardenability characteristics of DHA-THERMO and H13. Hardness distribution in quenched and tempered round bars of varying diameters was also measured.
- Die Casting Tests:
- Sprue Core Temperature Measurement: Actual die casting tests were performed using a 135t die casting machine. DHA-THERMO and H13 were used as sprue core materials, and the surface temperature of the sprue core was measured using radiant thermography.
- Microstructure Observation: Optical microscopy was used to examine the microstructure of the solidified biscuit part in contact with DHA-THERMO and H13 sprue cores.
- Heat Check Resistance Test: Heat check resistance was evaluated by observing the surface of movable molds made of DHA-THERMO and H13 after 10,000 shots in the die casting machine.
- Material Property Testing:
- Analysis Method:
- Comparative Analysis: The measured thermal conductivity, hardness, and hardenability of DHA-THERMO were compared to those of H13 steel.
- Temperature Distribution Analysis: Temperature distributions on the sprue core surface were compared between DHA-THERMO and H13.
- Microstructure Analysis: The microstructure of the solidified biscuit was qualitatively assessed to compare the grain refinement achieved with DHA-THERMO and H13 sprue cores.
- Heat Check Observation: The extent and severity of heat checking on DHA-THERMO and H13 molds were visually compared.
- Performance Evaluation in Die Casting Applications: The results from various die casting tool applications (center pin, core pin, split insert, distributor, squeeze bush) using DHA-THERMO were analyzed in terms of quality improvement (yield rate, shrinkage reduction, surface temperature decrease) and cycle time reduction.
- Research Subjects and Scope:
- Materials: DHA-THERMO high thermal conductivity steel, H13 hot work die steel, W alloy (Anviloy).
- Die Casting Tools: Sprue core, center pin, core pin, distributor, split insert, squeeze bush.
- Die Casting Process: Aluminum die casting using ADC12 alloy.
- Machine: 135t Toshiba die casting machine.
5. Main Research Results:
- Key Research Results:
- Thermal Conductivity: DHA-THERMO exhibits significantly higher thermal conductivity than H13 steel. At room temperature, DHA-THERMO's thermal conductivity is approximately 1.6 times greater than H13. While the difference decreases at higher temperatures, DHA-THERMO still maintains superior thermal conductivity at 500°C, which is representative of mold surface temperatures in die casting.
- Tempering Hardness: DHA-THERMO shows lower hardness than H13 when tempered between 300 to 600°C. However, at tempering temperatures above 600°C, DHA-THERMO maintains higher hardness than H13. By selecting a tempering temperature range of 610 to 680°C, a hardness of 40 to 47 HRC can be achieved for DHA-THERMO.
- Hardenability: DHA-THERMO shows slightly inferior hardenability to H13 in terms of Bainitic hardenability based on CCT diagrams. However, in practical quenching tests of 200mm diameter round bars, the hardness distribution of DHA-THERMO is acceptable, with only a slight decrease in hardness in the center of larger bars.
- Die Casting Test - Sprue Core Temperature: In die casting tests, the sprue core made of DHA-THERMO showed a significantly lower surface temperature (by 120°C) compared to an H13 sprue core under the same conditions.
- Die Casting Test - Microstructure: The optical microstructure of the biscuit surface in contact with the DHA-THERMO sprue core was much finer than that with the H13 sprue core, indicating faster solidification due to enhanced heat transfer.
- Die Casting Test - Heat Check Resistance: After 10,000 shots, the DHA-THERMO mold exhibited milder heat checking, primarily at the gate side, with almost none at the center, compared to the H13 mold, which showed remarkable heat checking at both the gate side and the center.
- Application Examples: Applications of DHA-THERMO in various die casting tools demonstrated improvements in quality, cycle time reduction, and cost reduction. For example, using DHA-THERMO for center pins and core pins improved yield rates by reducing shrinkage. DHA-THERMO distributor inserts resulted in a deeper chill layer and improved microstructure. DHA-THERMO sprue cores reduced cycle time by 18% and decreased surface temperature by 45-80°C. In core pin applications, DHA-THERMO achieved the same lifespan as W alloy (Anviloy) at a lower cost.
- Statistical/Qualitative Analysis Results:
- Figure 1: "Thermal conductivity of DHA-THERMO is as 1.6 times larger than that of H13 at room temperature."
- Figure 2: "DHA-THERMO shows lower hardness than H13 when tempered at 300 to 600 °C. At higher than 600 °C, however, DHA-THERMO maintains higher hardness than H13."
- Figure 6: "The sprue core made of DHA-THERMO showed lower temperature than that of H13 by 120 °C."
- Figure 7: "optical microstructure of the center surface of the biscuit which touched with DHA-THERMO sprue core was much finer than that of H13."
- Table 3: Examples of applications show "Improved yield rate (Shrinkage reduced)", "Reduction in cycle time by 18%", "Same life as W alloy".
- Data Interpretation:
- The higher thermal conductivity of DHA-THERMO facilitates faster heat extraction from the die casting mold.
- This faster heat transfer leads to lower mold surface temperatures, accelerated solidification of the molten aluminum, and consequently, finer grain structures in the cast product.
- The reduced mold temperature and improved heat dissipation contribute to enhanced heat check resistance and potentially longer tool life.
- The practical applications demonstrate that DHA-THERMO effectively improves die casting quality, reduces cycle times, and offers a cost-effective alternative to expensive materials like W alloys in certain applications.
- Figure Name List:
- Figure 1 Thermal conductivity vs. test temperature.
- Figure 2 Hardness vs. tempering temperature.
- Figure 3 CCT diagram.
- Figure 4 Examples of hardness in round bars 4Bar gas Quenched and tempered.
- Figure 5 Application of DHA-THERMO in die casting test.
- Figure 6 Surface temperature of sprue core.
- Figure 7 Optical micrographs taken from biscuit surface.
- Figure 8 Heat checking observed on the surface of movable molds as of 10,000 shots.
- Figure 9 A part of Al die cast product where internal soundness was improved by the application of DHA-THERMO core pins.
- Figure 10 An example of core pin and failed area.


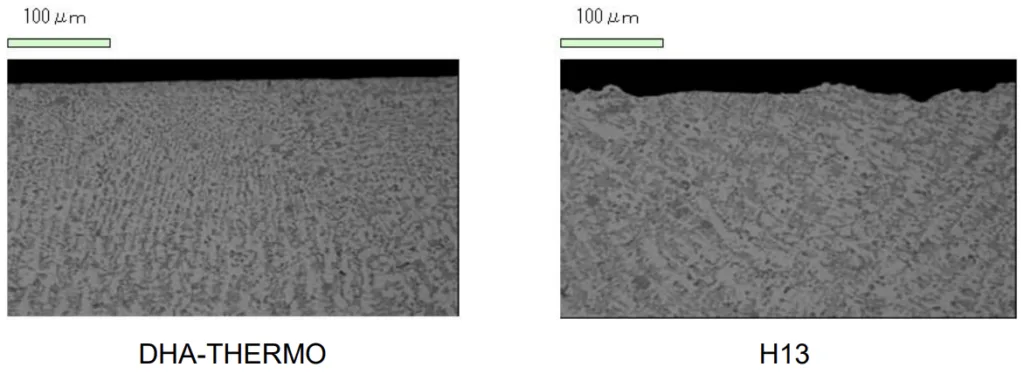
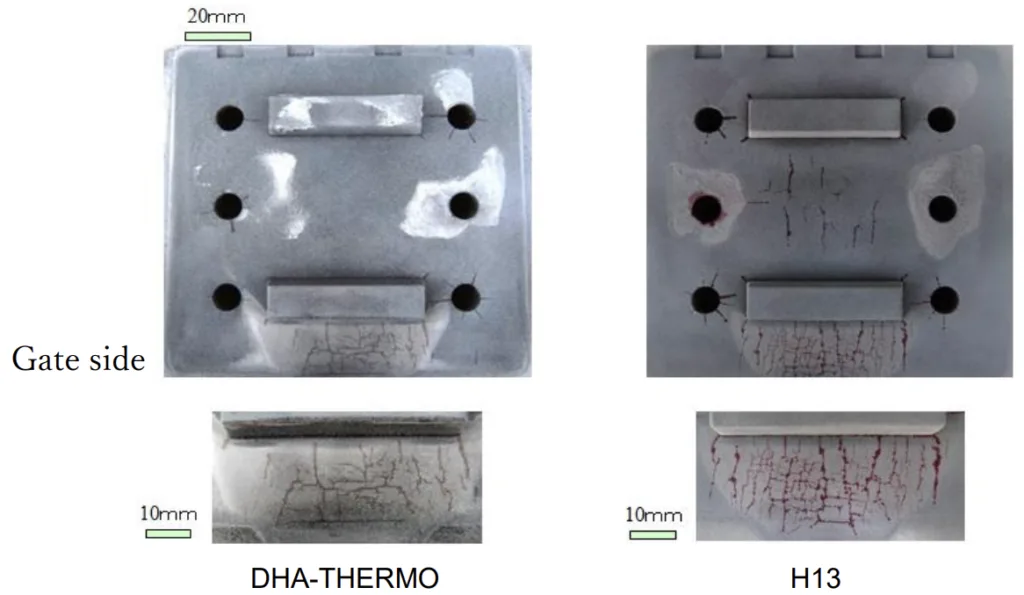

6. Conclusion and Discussion:
- Summary of Main Results:
- DHA-THERMO is a newly developed high thermal conductivity steel that offers a significant improvement over conventional H13 steel for die casting tool applications.
- It exhibits superior thermal conductivity, enabling faster heat removal from molds.
- DHA-THERMO achieves high hardness levels suitable for die casting tools through quenching and tempering.
- Die casting tests and application examples demonstrate that DHA-THERMO leads to:
- Improved quality of die-cast products (reduced shrinkage, finer microstructure, improved internal soundness).
- Reduced cycle times due to faster solidification.
- Enhanced heat check resistance, potentially prolonging mold life.
- Cost reduction by serving as a substitute for expensive W alloys in certain applications.
- Academic Significance of the Research:
- The research introduces and characterizes a novel high thermal conductivity steel, DHA-THERMO, specifically tailored for die casting applications.
- It provides valuable experimental data on the material properties of DHA-THERMO and its performance in comparison to H13 steel in various die casting scenarios.
- The findings contribute to the understanding of the benefits of high thermal conductivity materials in die casting and offer a practical solution to improve efficiency and quality in the industry.
- Practical Implications:
- DHA-THERMO offers a practical material solution for die casting tool manufacturers and users seeking to enhance productivity and product quality.
- The use of DHA-THERMO in die casting tools can lead to significant improvements in cycle time, enabling higher production rates and reduced manufacturing costs.
- The improved quality of die-cast components, particularly in critical applications like automotive parts, can enhance product performance and reliability.
- DHA-THERMO provides a cost-effective alternative to expensive W alloys for applications requiring high thermal conductivity, expanding the range of materials available for die casting tool design.
- Limitations of the Research:
- The paper is an abridged version of the original presentation, potentially lacking detailed information on specific aspects of the research.
- While the paper presents compelling results, further detailed studies may be needed to fully characterize the long-term performance and optimize the application of DHA-THERMO in diverse die casting environments and with different alloys.
7. Future Follow-up Research:
- Directions for Follow-up Research:
- Long-term performance evaluation of DHA-THERMO tools in industrial die casting production settings, assessing wear resistance, fatigue life, and heat check evolution over extended production runs.
- Optimization of die casting process parameters (e.g., cooling strategies, injection parameters) specifically tailored for DHA-THERMO tools to maximize the benefits of its high thermal conductivity.
- Investigation of the performance of DHA-THERMO in die casting other alloys beyond ADC12 aluminum, such as magnesium or zinc alloys.
- Areas Requiring Further Exploration:
- Detailed material characterization of DHA-THERMO, including its precise chemical composition, microstructure, and mechanical properties under various operating conditions.
- Comprehensive cost-benefit analysis comparing the overall economic advantages of using DHA-THERMO versus H13 steel and W alloys, considering material costs, tool manufacturing costs, production efficiency gains, and tool lifespan.
- Exploration of surface treatments and coatings for DHA-THERMO tools to further enhance their performance and durability in demanding die casting applications.
8. References:
1) K. Bungardt, W. Spyra: Archiv fur das Eisenhuttenswesen, vol. 36, p 257 (1965)
2) M. Ayabe, K. Shibata, H. Koyama, K. Ozaki, M. Kawano and T. Yanagisawa: SAE Technical Paper Series, 07M-113 (2007)
3) M. Kawano and K. Inoue: Materia Japan, vol.48, p32, (2009)
9. Copyright:
- This material is K. Namiki, Masamichi. Kawano, Thomas Schade's paper: Based on High Thermal Conductivity Steel and its Application to Die Casting Tools.
- Paper Source: NADCA DIE CASTING CONGRESS & EXPOSITION, (2012), Transaction No. T12-071
This material was summarized based on the above paper, and unauthorized use for commercial purposes is prohibited.
Copyright © 2025 CASTMAN. All rights reserved.