This article introduces the paper['Effect of Cr Addition on Mechanical Properties and Wear Rate of Cast Al-Cu Alloy'] published by ['Indian Journal of Science and Technology'].
1. Overview:
- Title: Effect of Cr Addition on Mechanical Properties and Wear Rate of Cast Al-Cu Alloy
- Author: Aneesh Ravikumar, R. Sellamuthu and R. Saravanan
- Publication Year: September 2016
- Publishing Journal/Academic Society: Indian Journal of Science and Technology, Vol 9(34)
- Keywords: Al-Cu Alloy, Cr Addition, Heat Treatment, Tensile Properties, Wear Rate
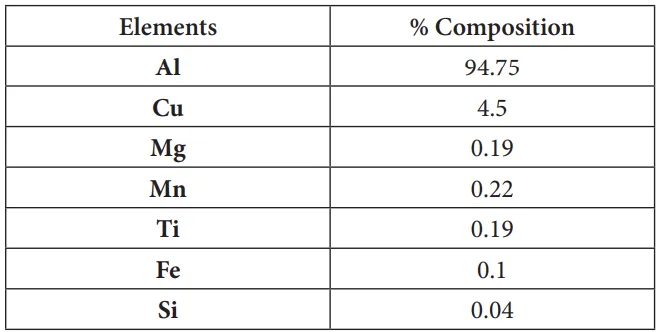
2. Abstracts or Introduction
This paper investigates the effect of Chromium (Cr) addition on the hardness, tensile properties, and wear behavior of Aluminum-4.5%Copper (Al-4.5Cu) alloy A206. The methodology involved melting a base alloy, adding fine Cr powder, and casting specimens in a permanent cast iron mold. Specimens underwent solution heat treatment at 540°C for 4 hours and aging at 170°C for 17 and 20 hours. As-cast and aged specimens were characterized using microstructure and EDAX evaluation, followed by hardness, tensile, and wear testing. The findings revealed that microstructure and EDAX analysis indicated irregularly distributed polyhedral structures, appearing blocky due to the phase formation of Al-Cr-Mn-Fe-Si. Hardness, Ultimate Tensile Strength (UTS), and Yield Strength (YS) initially increased, reached a peak, and then decreased with further Cr addition in the aged condition. Wear rate decreased with increasing hardness, while the coefficient of friction remained constant. The application of this research is to evaluate the effect of Cr in Al alloys on mechanical strength and wear properties.
3. Research Background:
Background of the Research Topic:
Al-Cu alloys are recognized as high-strength, heat-treatable alloys utilized in critical applications such as cryogenic storage tanks, steering knuckles, engine pistons, brake valves, missile fins, aircraft structures, and oil pumps. These alloys exhibit excellent thermal and electrical conductivity due to their composition of Aluminum (Al) and Copper (Cu). They are responsive to precipitation heat treatment, which includes solution treatment and artificial aging, and are suitable for shaping processes involving external pressure like pressure die casting, squeeze casting, and hot isostatic pressing. These processes enhance product strength through residual plastic stresses from strain hardening, which in turn facilitates the nucleation of coherent metastable θ" solute particles, leading to precipitation hardening.
Status of Existing Research:
Prior research has established that Al-4.5Cu alloy achieves peak hardness when homogenized at 540°C for 4 hours and aged at 170°C for 17 hours, reaching a maximum hardness of 70 HV after 17 hours of aging, followed by a reduction in hardness. Studies on Al-Mg-Si alloys have shown that Copper (Cu) retards early-stage clustering kinetics but accelerates them later, while Magnesium (Mg) and Silicon (Si) enhance clustering kinetics depending on solute vacancy interaction. Manganese (Mn) in Al-Cu-Mg-Ag A201 alloy was found to reduce tensile strength due to brittle failure from Al<0xE2><0x82><0x99>Cu<0xE2><0x82><0x99>Mn phase induced micro-cracking. In Al-Cu-Li alloys, Zirconium (Zr) deficiency leads to AlZr formation, reducing Zr interaction with strengthening phases and causing Zr segregation. Equal Channel Angular Pressing (ECAP) of semi-solid cast A356 alloy improved hardness and wear properties compared to conventional casting. Spray forming of Al-12Si and Al-20Si alloys resulted in superior hardness and wear properties compared to chill cast alloys. However, the effect of Cr addition to Al-Cu alloys remains largely unexplored.
Necessity of the Research:
The effect of Chromium (Cr) addition on Aluminum (Al) alloys, specifically Al-Cu alloys, is not extensively studied. Existing research indicates that Cr and Zirconium (Zr) additions can influence the hardness of Al matrix alloys under varying aging sequences. For instance, solution-treated Al-0.8Cr alloy showed a maximum hardness of 48 HV, which decreased with aging at 450°C. Adding 0.4% Zr to this alloy increased peak hardness to 58 HV when aged at 400°C for 24 hours. Furthermore, studies on secondary foundry alloys revealed that 0.1% Cr addition in the base alloy resulted in a maximum tensile strength of 146 MPa. This highlights the need for further investigation into the specific effects of Cr addition on the mechanical properties and wear rate of Al-Cu alloys, particularly in cast conditions relevant to die casting applications.
4. Research Purpose and Research Questions:
Research Purpose:
The primary purpose of this research is to evaluate the effect of Chromium (Cr) addition on the mechanical properties, specifically hardness and tensile strength, and wear rate of cast Aluminum-Copper (Al-Cu) alloy A206. This evaluation aims to understand how varying concentrations of Cr, combined with heat treatment processes, influence these critical material properties.
Key Research:
The key research questions addressed in this study are:
- How does the addition of varying concentrations of Chromium (Cr) (0.1%, 1%, and 2%) affect the microstructure of cast Al-4.5Cu alloy A206 in as-cast, solution-treated, and aged conditions?
- What is the impact of Cr addition on the hardness of Al-4.5Cu alloy A206 under different heat treatment conditions (as-cast, solution-treated, and aged at 170°C for 17 and 20 hours)?
- How does Cr addition influence the tensile properties (Ultimate Tensile Strength, Yield Strength, and ductility) of Al-4.5Cu alloy A206 under the same heat treatment conditions?
- What is the effect of Cr addition on the wear rate and coefficient of friction of Al-4.5Cu alloy A206, and how does it correlate with hardness changes?
Research Hypotheses:
While not explicitly stated as hypotheses, the research is implicitly based on the premise that:
- The addition of Cr to Al-4.5Cu alloy will modify its microstructure, potentially leading to the formation of intermetallic phases and influencing grain structure.
- Cr addition, particularly at lower concentrations, will enhance the hardness and tensile strength of Al-4.5Cu alloy due to solid solution strengthening and interaction with precipitation hardening mechanisms. However, excessive Cr may lead to the formation of brittle phases, reducing mechanical properties.
- Improved hardness resulting from Cr addition will lead to a reduction in the wear rate of the Al-4.5Cu alloy.
5. Research Methodology
Research Design:
The research employed an experimental design involving the preparation of Al-4.5Cu alloy A206 with varying Chromium (Cr) additions (0%, 0.1%, 1%, and 2% by weight). The alloys were cast and then subjected to different heat treatment conditions: as-cast, solution treatment (540°C for 4 hours), and aging (170°C for 17 and 20 hours). The study then systematically evaluated the microstructure, chemical composition, hardness, tensile properties, and wear behavior of these alloys under different conditions.
Data Collection Method:
- Chemical Composition Analysis: Emission Spectrometer was used to determine the chemical composition of the base alloy. Energy Dispersive Spectrometry (EDS) was employed to identify phases and verify Cr content in the alloys.
- Microstructure Examination: Optical microscopy (Lyzer Instruments) at 100X magnification was used to observe and capture microstructures of polished and etched (0.5% HF solution) specimens. Dewinter software was used for image acquisition.
- Hardness Testing: Vickers hardness test (Wolpert Wilson, Germany) was conducted using a 500 gm load on specimens in as-cast, solution-treated, and aged conditions, as per ASTM B557M standards.
- Tensile Testing: Tensile tests were performed using Auto-Instruments UTM on specimens prepared according to ASTM B557M standards with a gauge diameter of 6.25 mm and gauge length of 31.75±0.25 mm, under as-cast, solution-treated, and aged conditions.
- Wear Testing: Dry sliding wear tests were conducted using a Ducom pin-on-disc tribometer, adhering to ASTM G99 standards. Specimens with a hemispherical end (6 mm diameter, 32 mm length) were tested against an EN 31 alloy steel disc (60 HRC hardness, 0.15µm surface roughness). Testing parameters included a sliding distance of 1.5 km, load of 2kg, track width of 110 mm, and rpm of 494.
Analysis Method:
- Microstructural Analysis: Micrographs were analyzed to observe grain structure, phase distribution, and the presence of intermetallic compounds.
- Compositional Analysis: EDS data was used to quantify elemental composition and identify phases formed with Cr addition.
- Hardness and Tensile Data Analysis: Hardness values and tensile properties (UTS, YS, elongation) were compared across different Cr concentrations and heat treatment conditions to determine the effect of Cr addition.
- Wear Rate Calculation: Wear rate (k) was calculated using the formula k = ΔV/S, where ΔV is the volume worn out and S is the sliding distance (1.5 km). Wear rates and coefficient of friction were analyzed to assess wear behavior in relation to Cr content and hardness.
Research Subjects and Scope:
The research subjects were cast specimens of Al-4.5Cu alloy A206 with Chromium (Cr) additions of 0%, 0.1%, 1%, and 2%. The scope of the study was limited to evaluating the effect of these Cr additions on microstructure, hardness, tensile properties, and wear rate under specific heat treatment conditions (solution treatment at 540°C for 4 hours and aging at 170°C for 17 and 20 hours) and wear testing parameters (1.5 km sliding distance, 2kg load, 2.5 m/s sliding speed).
6. Main Research Results:
Key Research Results:
- Microstructure and Phase Analysis: EDAX analysis indicated the formation of irregularly distributed polyhedral structures due to Al-Cr-Mn-Fe-Si phase formation. Microstructure examination showed dendritic structures in as-cast conditions, which disappeared after homogenization and aging, leading to the formation of coherent metastable θ" solute particles and grain boundaries. Cr addition resulted in blocky patches of intermetallic phases containing Cr, Mn, Fe, and Si with Al.
- Hardness: Hardness increased with Cr addition up to 0.1% in aged conditions, reaching a peak, and then decreased with further Cr addition (1% and 2%). The highest hardness was observed for Al-4.5Cu-0.1Cr alloy aged for 17 hours. Solution treatment and aging increased hardness compared to as-cast conditions.
- Tensile Properties: Ultimate Tensile Strength (UTS) and Yield Strength (YS) showed a similar trend to hardness, increasing with 0.1% Cr addition in aged conditions and then decreasing with higher Cr content. Ductility decreased continuously with increasing Cr addition.
- Wear Rate: Wear rate decreased with increasing hardness. Al-4.5Cu-0.1Cr alloy aged for 20 hours exhibited the lowest wear rate. The coefficient of friction remained relatively constant at around 0.4 for the base alloy and 0.42 for Al-4.5Cu-0.1Cr, irrespective of time.
Analysis of presented data:
- Microstructure Evolution: The transition from dendritic to grain boundary structures with heat treatment confirms the effectiveness of homogenization and aging in Al-Cu alloys. The presence of Al-Cr-Mn-Fe-Si phase suggests that Cr interacts with other alloying elements to form complex intermetallics, which can influence mechanical properties.
- Hardness and Strength Correlation: The peak in hardness and tensile strength at 0.1% Cr addition suggests an optimal level for solid solution strengthening and precipitation hardening. Higher Cr concentrations likely lead to the formation of excessive brittle intermetallics, reducing these properties.
- Wear Resistance Improvement: The inverse relationship between hardness and wear rate is consistent with Archard's wear law, indicating that increased hardness enhances wear resistance. The relatively constant coefficient of friction suggests that Cr addition primarily affects the material's resistance to wear rather than the frictional behavior.
Figure Name List:
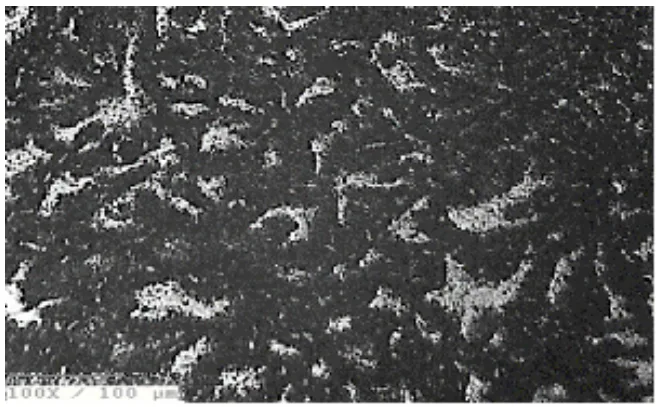
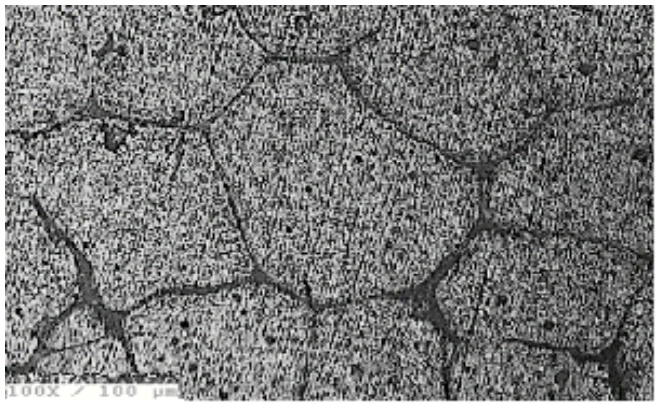
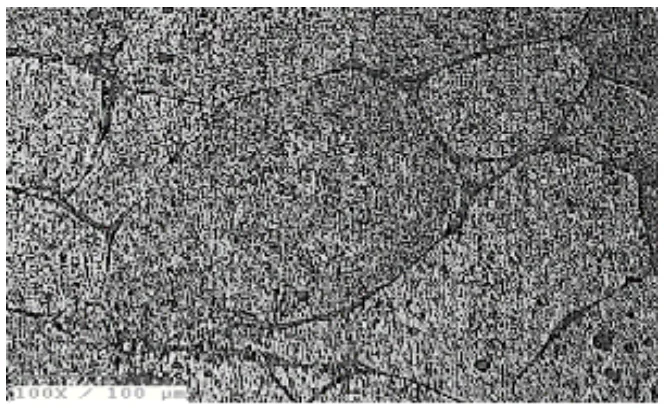
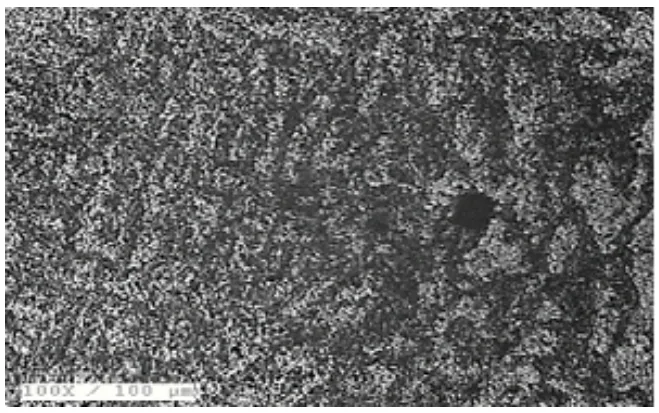
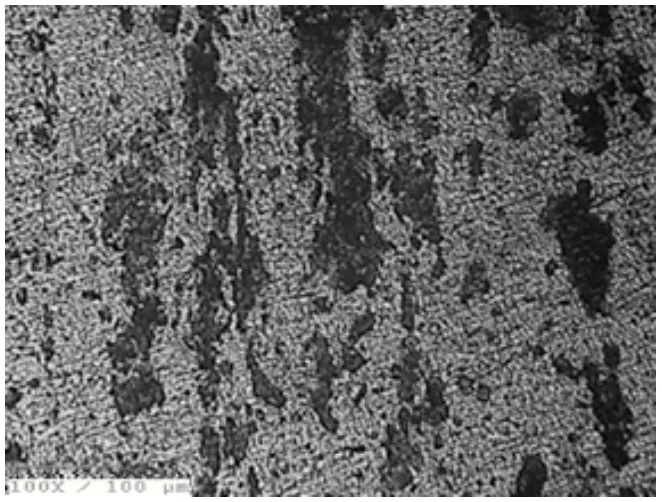
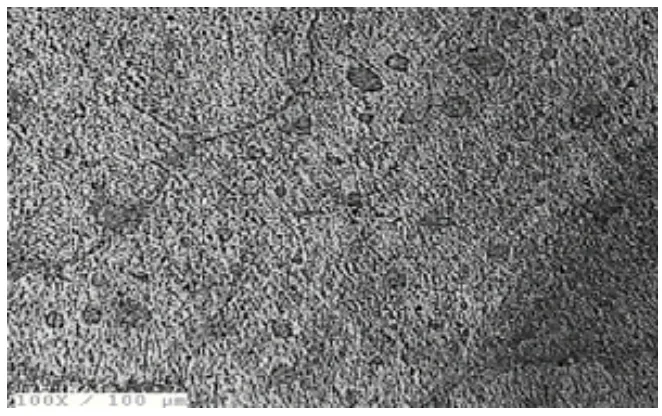
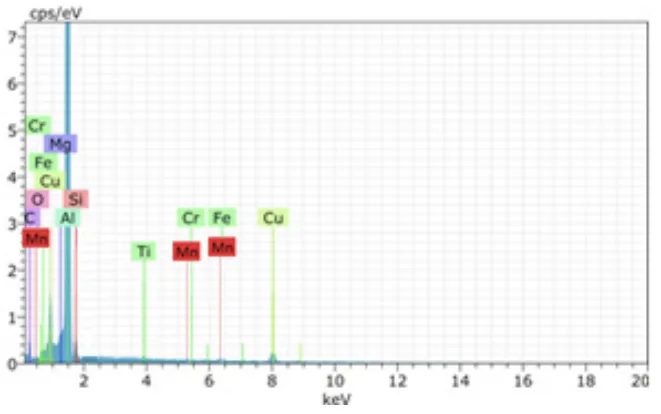
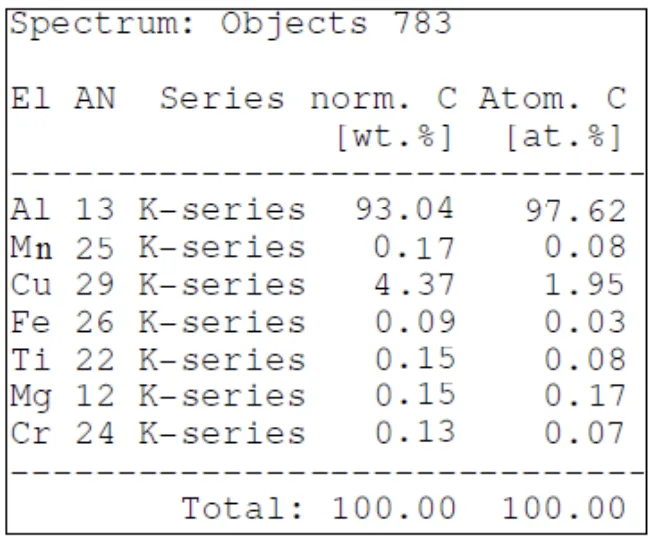
- Figure 9. EDS result for Al-4.5Cu-1Cr.
- Figure 10. Composition of Al-4.5Cu-1Cr.
- Figure 11. EDS result for Al-4.5Cu-2Cr.
- Figure 12. Composition of Al-4.5Cu-2Cr.
- Figure 13. Hardness variation with heat treatment and Cr addition.
- Figure 14. Hardness comparison of previous studies with current study.
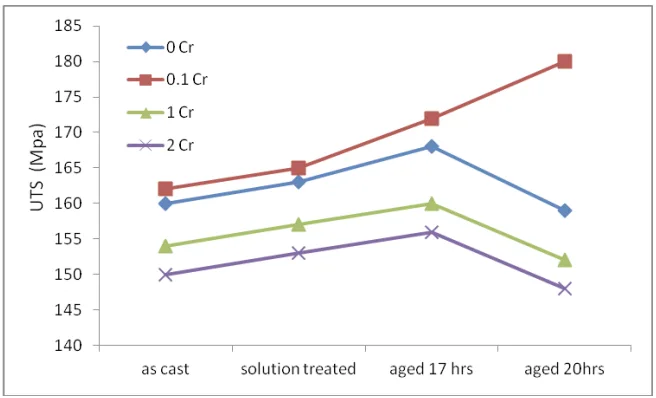
- Figure 16. Wear plot for Al-4.5Cu-0.1Cr.
- Figure 17. Wear rate comparison of K. Raju with current study.
- Figure 18. Coefficient of friction vs time for Al-4.5Cu-0.1Cr.
7. Conclusion:
Summary of Key Findings:
The study concludes that adding 0.1% Chromium (Cr) to Al-4.5Cu alloy A206 enhances its mechanical properties, specifically hardness and tensile strength, in aged conditions. While Cr addition increases peak aging time at 0.1%, further additions reduce it. Al-4.5Cu-0.1Cr exhibits superior hardness and tensile strength after aging, attributed to solid solution strengthening and precipitation hardening. Higher Cr contents (1% and 2%) lead to the formation of Al-Cr-Mn-Fe-Si intermetallic phases, which act as stress concentrators, reducing mechanical properties and potentially leading to failure at lower stress levels. Wear rate decreases with increasing hardness, with Al-4.5Cu-0.1Cr showing the lowest wear rate. The coefficient of friction remains consistent with Cr addition.
Academic Significance of the Study:
This study contributes to the fundamental understanding of the effects of Chromium (Cr) as an alloying element in Al-Cu alloys. It provides valuable insights into the phase transformations, microstructure evolution, and property changes induced by Cr addition and heat treatment. The research clarifies the role of Cr in solid solution strengthening and its interaction with precipitation hardening mechanisms in Al-Cu alloys, which is crucial for materials science and alloy design.
Practical Implications:
The findings have practical implications for the die casting industry, particularly in optimizing the composition of Al-Cu alloys for enhanced mechanical performance and wear resistance. The study suggests that a small addition of Cr (0.1%) can improve the performance of Al-4.5Cu alloys in applications requiring high strength and wear resistance, such as automotive and aerospace components. However, careful control of Cr content is essential to avoid the formation of detrimental intermetallic phases at higher concentrations.
Limitations of the Study and Areas for Future Research:
The study is limited to specific heat treatment conditions (solution treatment at 540°C and aging at 170°C) and a fixed set of wear testing parameters. Further research could explore a broader range of heat treatment cycles and wear testing conditions to fully characterize the effects of Cr addition. Investigating the impact of Cr on other properties like corrosion resistance and fatigue behavior would also be valuable. Additionally, detailed characterization of the Al-Cr-Mn-Fe-Si intermetallic phases, including their morphology, distribution, and impact on fracture mechanisms, could provide a deeper understanding of the alloy's behavior at higher Cr concentrations.
8. References:
- [1] Kabir MS, Minhaj TI, Ashrafi EA, Islam MM. Effect of Cu and Ge on solute clustering in Al-Mg-Si alloys. International Journal of Recent Technology and Engineering. 2014 Jul; 3(3): 1-6.
- [2] Liu M, Banhart J. Effect of Cu and Ge on solute clustering in Al-Mg-Si alloys. Journal of Materials Science and Engineering. 2016 Mar; 658: 238-45.
- [3] Tao GH, Liu CH, Chen JH, Lai YX, Ma PP, Liu LM. The influence of Mg/Si ratio on the negative natural aging effect in Al-Mg-Si-Cu alloys. Journal of Materials Science and Engineering. 2015 Aug; 642: 241-8.
- [4] Marceau RKW, Sha G, Ferragut R, Dupasquier A, Ringer SP. Solute clustering in Al-Cu-Mg alloys during the early stages of elevated temperature ageing. Acta Materialia. 2010 Sep; 58(15): 4923-39.
- [5] Stability of vacancies during solute clustering in Al-Cu-based alloys. Available from: http://journals.aps.org/prb/abstract/10.1103/PhysRevB.65.094107, Date accessed: 07/02/2002.
- [6] Moller H, Masuku EP, Curle UA, Pistorius PC, Knutsen RD, Govender G. The influence of Mn on the tensile properties of SSM-HPDC Al-Cu-Mg-Ag alloy A201. The Journal of the South African Institute of Mining and Metallurgy. 2011 Mar; 111: 167-71.
- [7] Tsivoulas D, Robson JD. Heterogeneous Zr solute segregation and AlZr dispersoid distributions in Al-Cu-Li alloys. Acta Materialia. 2015 Jul; 93:73-86.
- [8] Thuong NV, Zuhailawati H, Seman AA, Huy TD, Dhindaw BK. Microstructural evolution and wear characteristics of equal channel angular pressing processed semi-solid-cast hypoeutectic aluminum alloys. Materials and Design, Elsevier. 2015 Feb; 67:448-56.
- [9] Raju K, Ojha SN. Effect of spray forming on the microstructure and wear properties of Al-Si alloys. International Conference in Advances in Manufacturing and Materials Engineering, AMME 2014. Procedia Materials Science. 2014 Sep; 5: 345-54.
- [10] Strengthening Aluminum by Zirconium and Chromium. Available from: http://www.socialweb.net/Events/150751.lasso, Date accessed: 19/12/2012.
- [11] Timelli G, Ferraro S, Fabrizi A. Effects of chromium and bismuth on secondary aluminium foundry alloys. International Journal of Cast Metals Research. 2013 Nov; 26(4): 239-46.
- [12] Mahajan G, Karve N, Patil U, Kuppan P, Venkatesan K. Analysis of Microstructure, Hardness and Wear of Al-SiC-TiB2 Hybrid Metal Matrix Composite. Indian Journal of Science and Technology. 2015 Jan; 8(S2):101–5.
9. Copyright:
- This material is "Aneesh Ravikumar, R. Sellamuthu and R. Saravanan"'s paper: Based on "Effect of Cr Addition on Mechanical Properties and Wear Rate of Cast Al-Cu Alloy".
- Paper Source: https://doi.org/10.17485/ijst/2016/v9i34/100952
This material was summarized based on the above paper, and unauthorized use for commercial purposes is prohibited.
Copyright © 2025 CASTMAN. All rights reserved.