This introduction paper is based on the paper "Optimization of Runner Design in Pressure Die Casting" published by "International Journal of Engineering Research & Technology (IJERT)".
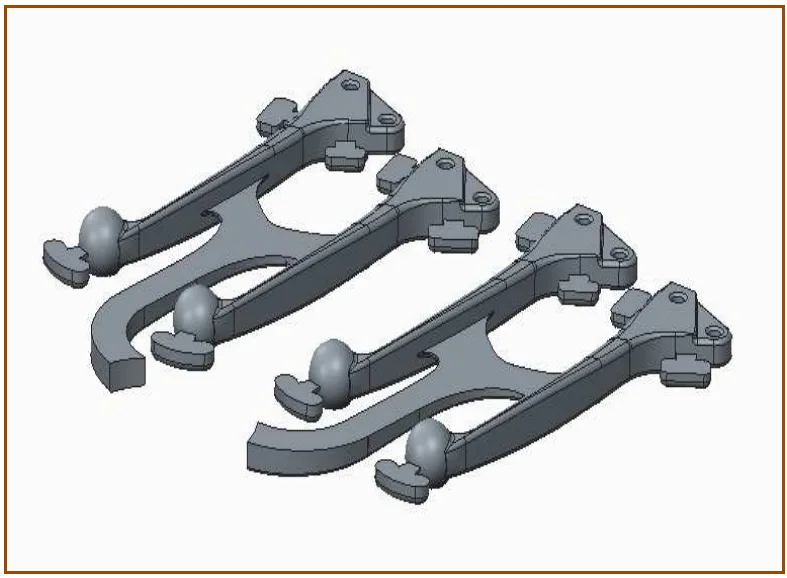
1. Overview:
- Title: Optimization of Runner Design in Pressure Die Casting
- Author: Nair Akhil K. Raveendran, Prof. Amol N. Patil
- Year of publication: 2017
- Journal/academic society of publication: International Journal of Engineering Research & Technology (IJERT)
- Keywords: Runner, Gate, High pressure die casting, Fill time
2. Abstract:
In order to produce high quality parts with high pressure die casting, computer aided simulation has been used to optimize mold designs. Finite difference (differential), finite volume and finite element methods have been used in the filling process simulation and significant progress has been made for general problems. Further work on mold design optimizations is still desired to address specific issues. In die casting, the die often has more than one cavity with multiple cavities producing the same or different parts. Multiple cavities require the application of branch runners connecting to a main runner. The design of the runner system has always been a topic for die casting, since it is important for the designer to ensure that multiple cavities start filling at the same time and have the same fill time. A key factor in the design is to adjust the cross section area of each branch runner according to the cavities' volumes; however, this may not be enough to fill the cavities simultaneously. The angle between the branch runner and the main runner has been observed to have effects on the filling pressure, filling time and residual stresses, but the observations were limited to very simple lab level die design rather than practical castings.
3. Introduction:
Die casting is a process where molten metal is injected into a die cavity under high pressure. This paper deals with problems in the runner of Cold chamber high Pressure Die casting, where an inaccurately designed feed system caused jet marks on the product. This jetting of molten metal leads to erosion on the runner walls, and over a long production run, this wear forms a local depression that alters the flow direction. This issue necessitates a solution where the runner is designed to create a smoother molten metal flow with minimal jetting to prevent wear on the runner walls. The paper utilizes the P-Q2 diagram, a critical tool in die casting design, to determine the operational window for process parameters.
4. Summary of the study:
Background of the research topic:
High-quality parts in pressure die casting depend heavily on optimal mold design. For dies with multiple cavities, the runner system is critical to ensure that all cavities fill simultaneously and uniformly. An improperly designed runner can lead to defects, increased production costs, and die wear.
Status of previous research:
Computer-aided simulations have been widely used to optimize mold designs. Previous studies have shown that factors like the angle between the branch and main runner influence filling pressure and time. However, these observations were often limited to simple lab-level designs. This study builds on existing knowledge by applying computational fluid dynamic (CFD) methods to a practical, multi-cavity industrial component. It also refers to established design methodologies, such as Herman's for gating systems and the use of the P-Q2 diagram for process parameter optimization as noted in Ref..
Purpose of the study:
The primary purpose of this study was to optimize the runner design in a high-pressure die-casting die to eliminate product defects such as jet marks. The research aimed to design a runner that minimizes jetting on the runner side walls, prevents erosion, ensures complete filling of the mold cavities, and ultimately reduces the rejection rate of the cast parts.
Core study:
The core of the study involved using CFD simulation to analyze an existing die for a clutch lever that was producing defective parts. The analysis identified issues with the filling pattern, where uneven filling caused solidification defects and jet marks. Based on this analysis, the runner design was modified from a fan type to a tangential type. This new design was then simulated and analyzed to verify its effectiveness in creating a smooth fill, reducing porosity, and eliminating defects.
5. Research Methodology
Research Design:
The research followed a comparative analysis methodology. An existing die design for a four-cavity clutch lever was first analyzed to understand its flaws. Subsequently, a modified runner design was developed and simulated. The performance of the modified design was then compared to the original by evaluating key casting parameters to validate the improvements.
Data Collection and Analysis Methods:
The study primarily employed computational fluid dynamic (CFD) simulation to analyze the casting process. Parameters such as Filling Time, solidification, ingate velocity, mold erosion, air entrapment, and cold shuts were considered. The analysis compared results from different runner iterations (including fan and tangential types) using analytical software to determine the most suitable design.
Research Topics and Scope:
The research is focused on the optimization of the runner system for a high-pressure die casting (HPDC) die with four cavities producing a clutch lever. The scope includes the analysis of the runner trajectory and directional changes to achieve a smooth filling of the cavities, reduce product defects, and improve overall casting quality.
6. Key Results:
Key Results:
The CFD analysis demonstrated that changing the runner from a fan type to a tangential type successfully reduced the adverse effects of the metal flow on the die and the product. This change resulted in a significant reduction in jet marks on the casting. Consequently, the rejection rate decreased as the molten metal completely filled the mold without premature solidification. The analysis also confirmed a decrease in porosity with the new design compared to the previous iteration. As the jet marks were eliminated, the need for post-processing operations like polishing was also removed.
Figure Name List:
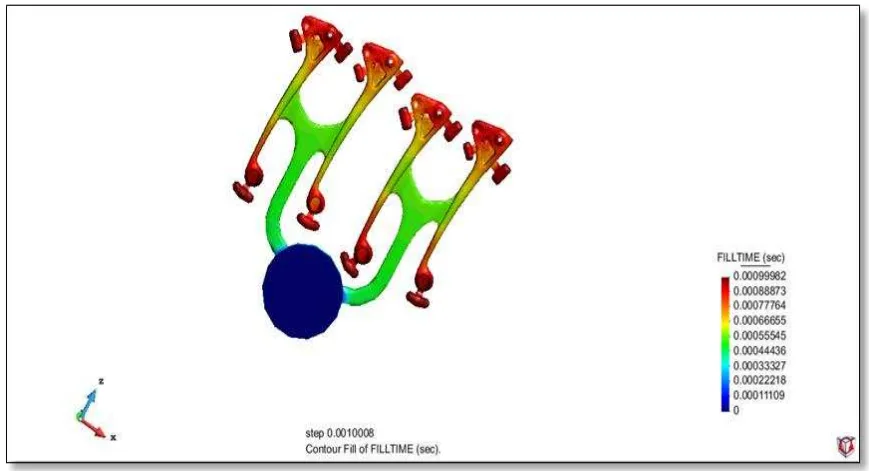
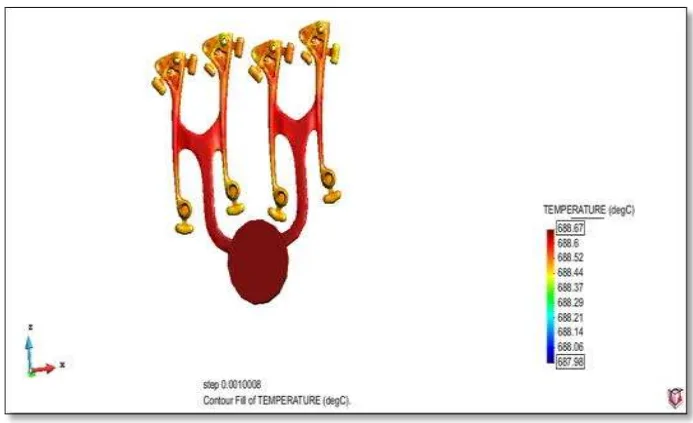
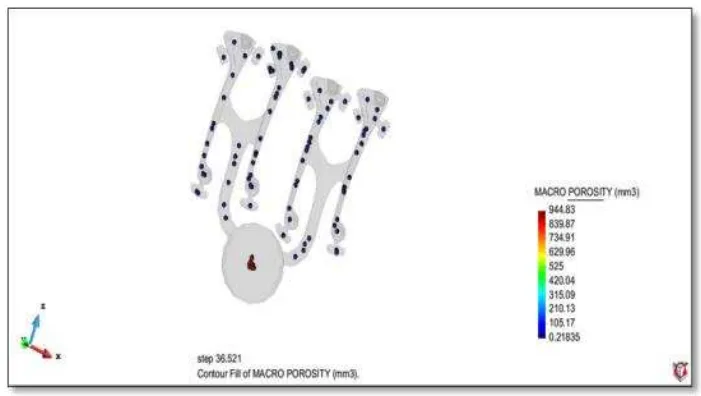
- Fig. 1. Runner System of the Modified Design
- Fig. 2. Filling Time of the Modified Design
- Fig. 3. Temperature of molten metal in Modified Design
- Fig. 4. Porosity in runner system of Modified Design
7. Conclusion:
In CFD analysis we found that by changing the runner from fan runner to tangential it reduced the effect of flow on the die and the product. The chances of jet marks on the die and product became less. The rejection rate decreased as the molten metal now completely fills the mould now. Also there is decrease in porosity as compared to the first iteration that was made. As the jet marks were reduced the post-processing of the product like polishing was not required.
8. References:
- B. Vijaya Ramnath et al. (2014), Analysis and Optimization of Gating System for Commutator End Bracket, Procedia Materials Science 6 (2014) 1312–1328
- Marco Antonio Pego Guerr, Die Casting Design – A Parametric Approach, Thesis submitted to Ottawa-Carleton Institute for Mechanical and Aerospace Engineering (1997)
- P.R.Vispute, D.S.Chaudhari, Swapnil Kulkarni, Utilizing Flow Simulation In The Design Phase Of A Die Casting Die To Optimize Design Parameters While Validating Through Experimentation During Trials, International Journal of Scientific Research and Management Studies (IJSRMS) ISSN: 23493771 Volume 1 Issue 8, pg: 263-269
- Shaik Riyaz Ahmed, K.Devaki Devi and S.V.S. Himathejeswini, Design & Analysis of Heat Sink High-Pressure Die Casting Component, International Journal of Current Engineering and Technology, Vol.6, No.5 (Oct 2016)
- Tuula Höök, Tampere University of Technology, HPDC runner and gating system design, CAE Mould Design.
9. Copyright:
- This material is a paper by "Nair Akhil K. Raveendran, Prof. Amol N. Patil". Based on "Optimization of Runner Design in Pressure Die Casting".
- Source of the paper: http://www.ijert.org
This material is summarized based on the above paper, and unauthorized use for commercial purposes is prohibited.
Copyright © 2025 CASTMAN. All rights reserved.
Paper Summarize:
Key questions and answers about the research:
This research aimed to resolve defects like jet marks and high rejection rates in high-pressure die casting by optimizing the runner system. Using CFD analysis, the study demonstrates that changing from a fan to a tangential runner design for a clutch lever component improves metal flow. The new design successfully eliminated jet marks, reduced porosity, and decreased the part rejection rate by ensuring complete and uniform mold filling.
Q1. What was the primary problem with the existing die casting process discussed in the paper?
A1. The primary problem was an inaccurately designed feed system in a cold chamber high-pressure die, which caused jetting, erosion on runner walls, incomplete filling of the mold, and jet marks on the final product, leading to a high rejection rate. (Source: "Optimization of Runner Design in Pressure Die Casting", Introduction and Design and Analysis sections).
Q2. What specific design change was implemented to solve this problem?
A2. The runner design was changed from a fan runner to a tangential runner to reduce the turbulent effect of molten metal flow on the die and product. (Source: "Optimization of Runner Design in Pressure Die Casting", Conclusion).
Q3. What methodology was used to evaluate the new design?
A3. Computational fluid dynamics (CFD) simulation was used to analyze and compare the performance of the existing and modified runner designs, focusing on parameters like filling time, porosity, and temperature distribution. (Source: "Optimization of Runner Design in Pressure Die Casting", Design and Analysis section).
Q4. Did the new runner design affect the filling time?
A4. Yes, the filling time with the modified tangential runner was 0.00099982 seconds, which was a slight, non-drastic increase compared to the previous fan gate runner, and the change did not adversely affect the process. (Source: "Optimization of Runner Design in Pressure Die Casting", Figure 2 and surrounding text).
Q5. How did the modified design impact product quality in terms of defects?
A5. The modified design led to a decrease in porosity, eliminated visible jet marks on the product, and ensured the molten metal filled the mold completely and evenly, which significantly reduced the part rejection rate. (Source: "Optimization of Runner Design in Pressure Die Casting", Conclusion and page 3 text).
Q6. Was post-processing required for products made with the optimized design?
A6. No, post-processing steps like polishing were no longer required for the product because the jet marks were eliminated by the improved runner design. (Source: "Optimization of Runner Design in Pressure Die Casting", Conclusion).