This introduction paper is based on the paper "On Inter-bar Currents in Induction Motors with Cast Aluminium and Cast Copper Rotors" published by "KTH Electrical Engineering".
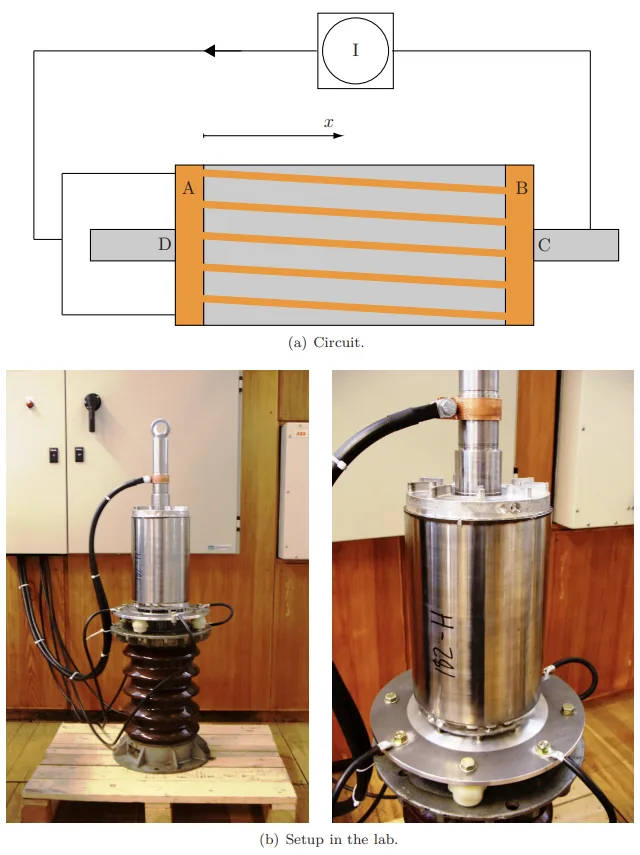
1. Overview:
- Title: On Inter-bar Currents in Induction Motors with Cast Aluminium and Cast Copper Rotors
- Author: ALEXANDER STENING
- Year of publication: 2010
- Journal/academic society of publication: KTH Electrical Engineering (Licentiate Thesis)
- Keywords: Induction motors, Inter-bar currents, Copper rotors, Aluminium rotors, Starting torque, Asynchronous torques, Starting current, Stray losses.
2. Abstract:
This thesis presents a study of the effects of inter-bar currents on induction motor starting performance and stray-load losses. The work is focused on the performance differences between aluminium and copper casted rotors.
A method to predict the stator current when starting direct-on-line is developed. This includes modelling of skin-effect, saturation of the leakage flux paths and additional iron losses. The results are verified by measurements. An analytical model accounting for inter-bar currents is derived, and the dependency of the harmonic rotor currents on the inter-bar resistivity is investigated. It is found that the inter-bar currents can have considerable effect on motor starting performance and stray-load losses, the amount being strongly dependent on the harmonic content of the primary MMF.
Based on measurements of inter-bar resistivity, the starting performance of an aluminium and a copper casted rotor is simulated. The results indicate a higher pull-out torque of the aluminium rotor than for the equivalent copper rotor. This is rather due to an increase of the fundamental starting torque of the aluminium rotor, than due to braking torques from the space harmonics in the copper rotor. The results are verified by measurements. It is found that the difference between the pull-out torques is even larger than calculated from the model. Thereby, it can be concluded that the inter-bar currents have a considerable effect on motor starting performance.
At rated speed the braking torques are larger in the aluminium rotor than in the copper rotor. This is seen as increased harmonic joule losses in the rotor cage. Simulations have shown, that these losses can be as large as 1% of the output power for the studied machine.
3. Introduction:
Induction motors are the most commonly used electrical machines due to their simplicity and robustness. Designing efficient motors requires accurate models, especially with increasing demands for improved efficiency and challenging starting performance requirements. Reducing stray-load losses (additional losses beyond standard calculations) is crucial. Inter-bar currents, flowing between rotor bars through the lamination in cast rotors, are identified as a significant component of these losses, particularly in small to medium-sized motors [2]. These currents, influenced by stator slot harmonics, can also negatively impact starting torque and pull-out torque [6].
Die-cast aluminium rotors are common in small/medium motors. Advancements allow for die-cast copper rotors, offering higher conductivity and potential efficiency gains. However, measurements show inter-bar resistivity in copper rotors can be significantly lower (up to 10 times) than in aluminium rotors [9], promoting inter-bar current flow.
Rotor skewing is often employed to suppress high-frequency currents induced by stator slot harmonics, improving efficiency if bars are insulated. However, in cast rotors with low inter-bar resistivity, skewing can facilitate inter-bar currents, potentially negating its benefits. The magnitude depends strongly on skew and resistivity.
This thesis aims to study these effects by developing analytical models for starting performance and additional rotor losses, verifying them with measurements on aluminium and copper cast rotors (specifically Motor A: 11 kW, 4-pole, 36/44 slots, Al; Motor B: 11 kW, 4-pole, 36/28 slots, Al & Cu).
4. Summary of the study:
Background of the research topic:
The need for high-efficiency induction motors drives the requirement for accurate performance models. Stray-load losses, particularly those caused by inter-bar currents in die-cast rotors (aluminium and increasingly copper), significantly impact efficiency and starting performance. The low inter-bar resistivity inherent in the casting process, especially with copper, interacts complexly with design features like rotor skewing.
Status of previous research:
Previous work identified components of stray-load losses [2], including inter-bar current losses [5, 6]. Methods for measuring inter-bar resistance were developed [6, 9, 11]. Analytical models for inter-bar currents [14], skin effect in rotor bars [19, 20], and saturation effects [21, 23, 25] exist, but integrating these phenomena, especially comparing cast aluminium and copper, requires further investigation.
Purpose of the study:
To investigate the effects of inter-bar currents on the starting performance (torque, current) and stray-load losses (additional rotor losses) of induction motors equipped with cast aluminium and cast copper rotors. This involves developing and verifying analytical models capable of simulating these effects.
Core study:
The research involved:
- Measuring inter-bar resistivity on cast aluminium and copper rotors using a developed test rig and equivalent circuit model.
- Developing an analytical model based on [14] to calculate the distribution of inter-bar currents and their effect on rotor bar currents, considering stator and rotor flux linkages, MMF harmonics, and rotor skew.
- Developing methods to account for skin effect (using a 1D numerical model [22]), leakage path saturation (using a combined analytical/FEM approach), and additional iron losses during direct-on-line starting.
- Simulating the starting torque-speed characteristics and rated-speed rotor losses for motors with different inter-bar resistivities (representing insulated, cast Al, cast Cu).
- Verifying the models through FEM simulations and experimental measurements of starting torque and current on a test motor (Motor B) with interchangeable aluminium and copper rotors.
- Analyzing the differences in performance between aluminium and copper rotors, focusing on the role of inter-bar currents.
5. Research Methodology
Research Design:
The study employed a combination of analytical modeling, numerical simulation, Finite Element Method (FEM) verification, and experimental validation. A comparative approach was used, analyzing the performance differences between cast aluminium and cast copper rotors (Motor B) under the influence of inter-bar currents. An additional motor configuration (Motor A) was used for parametric analytical studies.
Data Collection and Analysis Methods:
- Inter-bar Resistance Measurement: A dedicated test rig was constructed (Figure 2.1, 2.2). DC current was applied, and voltages (UAB, UAD, UBC, UAX) were measured. An equivalent circuit model (Figure 2.3) based on [9], accounting for bar, shaft, and inter-bar resistances/conductivities, was used to calculate the inter-bar resistivity (Rtn) from measured voltages (Equations 2.1-2.6).
- Analytical Modeling:
- Inter-bar currents: Model derived based on [14], using differential equations (Eq. 3.8, 3.43, 3.48) solved with boundary conditions (Eq. 3.51) considering bar impedance (Zbn), inter-bar resistivity (Rtn), and linked fluxes (Φsn, Φrn).
- Flux Calculation: Airgap flux density derived using Fourier analysis of simplified MMF/permeance distributions (Model A/B, Figure 3.4, 3.5, 3.9), verified with FEM (Figure 3.6). Stator and rotor fluxes linked by the circuit element were calculated (Eq. 3.26, 3.39, 3.42).
- Skin Effect: A 1D numerical method [22] was used to calculate frequency-dependent impedance correction factors (kr, kx) for rotor bars (Figure 4.1, 4.2, 4.3). Verified with FEM (Figure 4.4-4.7).
- Saturation: A combined analytical/FEM approach was used. A saturation factor (ksat) varying with slip (Eq. 4.14) was defined based on FEM locked-rotor tests (Figure 4.10) and circle diagram analysis (Figure 4.11) to modify leakage reactances (Eq. 4.13).
- Iron Losses: Modeled as additional resistance/reactance components in the equivalent circuit based on empirical factors (kLR, kLX) [22] (Figure 4.13, Eq. 4.20, 4.21).
- Simulation: The models were implemented (Figure 5.1) to calculate torque components (Eq. 4.28, 4.29) and losses (Eq. 4.22-4.25) across the speed range for different inter-bar resistivities.
- Experimental Validation: Direct-on-line starting tests were performed on Motor B with Al and Cu rotors, loaded by a flywheel (Figure 5.5). Torque (Magtrol TM-312) and speed were measured dynamically. Data was filtered (Figure 5.6) and RMS current calculated. Measured torque and current were compared with simulations (Figure 5.7, 5.9).
Research Topics and Scope:
The research focused on quantifying the impact of inter-bar currents, arising from finite inter-bar resistivity in cast rotors, on:
- Starting torque-speed characteristics (including pull-out torque and asynchronous harmonic torques).
- Starting current.
- Additional rotor losses (stray-load losses) at rated speed.
The scope included the development and integration of models for skin effect, leakage path saturation, and associated iron losses relevant during starting. The study primarily compared skewed cast aluminium and cast copper rotors for a specific 4-pole, 11 kW motor geometry (Motor B, 36/28 slots) and included analytical studies on another geometry (Motor A, 36/44 slots). The influence of main flux saturation on harmonic effects at rated load was not included.
6. Key Results:
Key Results:
- Measurements confirmed inter-bar resistivity is significantly lower (approx. 10 times) in cast copper rotors compared to cast aluminium rotors for the studied geometry. Evidence suggested uneven resistivity distribution along the bars in aluminium rotors, while copper rotors showed more uniform distribution (Chapter 2, Table 2.1, Figure 2.7, 2.8).
- A numerical method for skin effect calculation was developed and verified against FEM simulations, showing good correlation but slight overestimation at the bar top due to neglected tooth tip saturation (Chapter 4, Figure 4.4-4.7).
- A method combining analytical calculations with FEM results was developed to account for leakage path saturation during starting, showing saturation increases starting current significantly (~35%) (Chapter 4, Figure 4.10, 4.12).
- Simulations showed inter-bar currents have minimal effect on starting torque in unskewed rotors but a considerable effect in skewed rotors. Low inter-bar resistivity makes skewing ineffective at suppressing slot harmonic torques and can significantly reduce pull-out torque (Chapter 3, 4, Figure 3.17, 3.18, 4.15, 4.16).
- For the tested motor (Motor B, skewed), simulations predicted the aluminium rotor would have a higher pull-out torque (4.5%) than the copper rotor due to inter-bar current effects (increased fundamental torque in Al vs. harmonic braking torques in Cu) (Chapter 5, Figure 5.2, 5.3).
- Measurements verified the higher pull-out torque for the aluminium rotor, with the difference being even larger (7%) than simulated, confirming the significant impact of inter-bar currents on starting performance (Chapter 5, Figure 5.8, 5.9).
- Simulations indicated that at rated speed, harmonic joule losses (stray-load losses) due to inter-bar currents are larger in the aluminium rotor than the copper rotor (due to higher Rtn) and can be as high as 1% of the output power for the studied machine (Chapter 5, Figure 5.4).
Figure Name List:
- 1.1 Stray-load loss components (0,2-37 kW induction motors) [2].
- 2.1 Rotor test setup for measurements of inter-bar resistance.
- 2.2 Conducting washer between test-plate and rotor short-circuit ring.
- 2.3 Equivalent circuit of the rotor used for the calculation of the inter-bar resistivity.
- 2.4 Calculated voltages for the aluminium rotor at a total current of 200 A.
- 2.5 Calculated voltages for the copper rotor at a total current of 200 A.
- 2.6 Two of the studied aluminium and copper rotors.
- 2.7 Measured and calculated voltage UAX for rotor Al 2 at a total current of 200 A.
- 2.8 Measured and calculated voltage UAX for rotor Cu 2 at a total current of 100 A
- 3.1 Definition of bar- and inter-bar currents in a small element of the rotor circuit.
- 3.2 Phase displacement between inter-bar currents.
- 3.3 Definitions of inter-bar resistances.
- 3.4 Airgap flux density due to current in phase a, Model A.
- 3.5 Airgap flux density due to current in phase a, Model B.
- 3.6 Comparison between analytical and FEM-simulated airgap flux density at no-load.
- 3.7 Position of a wave of order n at time t = 0 in the rotor reference frame.
- 3.8 Current in bar number k and the corresponding MMF in the airgap.
- 3.9 Permeance variation along the airgap circumference as defined by Model A.
- 3.10 Rotor currents at the boundary x = -l/2.
- 3.11 Change in rotor bar current due to the interaction with inter-bar currents.
- 3.12 Magnitude of the fundamental locked rotor inter-bar current density and the resulting angle β1, for Motor A with unskewed rotor.
- 3.13 Magnitude of fundamental locked rotor bar current and the corresponding angle γ1, for Motor A with unskewed rotor.
- 3.14 Magnitude of the currents in the unskewed rotor caused by the fundamental and the first pair of slot space harmonics when Rtn = 5 · 10−5 Ωm.
- 3.15 Magnitude of the fundamental locked-rotor inter-bar current density and the resulting angle β1 for Motor A with skewed rotor.
- 3.16 Magnitude of fundamental locked-rotor bar current and the corresponding angle γ1, for Motor A with skewed rotor.
- 3.17 Magnitude of the currents in the rotor skewed by one stator slot pitch, caused by the fundamental and the first pair of slot space harmonics when Rtn = 5 · 10−2 Ωm.
- 3.18 Magnitude of the currents in the rotor skewed by one stator slot pitch, caused by the fundamental and the first pair of slot space harmonics when Rtn = 5 · 10−5 Ωm.
- 4.1 Different types of rotor bars.
- 4.2 The vth section of the rotor slot.
- 4.3 Procedure for the calculation of the impedance correction factors kr and kx that accounts for skin- effect.
- 4.4 Locked rotor bar current density for the aluminium rotor.
- 4.5 Locked rotor bar current phase angle relative to the bottom of the bar for the aluminium rotor.
- 4.6 Locked rotor bar current density for the copper rotor.
- 4.7 Locked rotor bar current phase relative to the bottom of the bar for the copper rotor.
- 4.8 Skin-effect correction factors for the studied rotor slot.
- 4.9 Equivalent circuit during online start.
- 4.10 FEM-simulated locked rotor test.
- 4.11 Simplified circle diagram for the induction motor defining the starting current and the current at break-down torque.
- 4.12 Saturation factors as a function of rotor speed.
- 4.13 Additional resistance taking iron losses into account.
- 4.14 Starting torque of Motor A with unskewed rotor.
- 4.15 Starting torque of Motor A with a rotor skewed by one stator slot pitch.
- 4.16 Main torque components for Motor A with a rotor skewed by one stator slot pitch.
- 5.1 Procedure for the calculation of motor performance at different speeds and inter-bar resistivities.
- 5.2 Simulated starting torque for the studied aluminium and copper rotors skewed by one stator slot pitch.
- 5.3 Starting torque components for the studied aluminium and copper rotors calculated with measured values of inter-bar resistivity.
- 5.4 High frequency cage losses as a function of inter-bar resistivity Rtn at 75 °C.
- 5.5 Setup for measurements of starting torque.
- 5.6 Measured and filtered torque and speed as a function of time.
- 5.7 Simulated and measured starting currents.
- 5.8 Measured torque for the aluminium and the copper rotor when starting direct-on-line at rated voltage.
- 5.9 Simulated and measured torques for the aluminium and the copper rotor when starting direct-on-line at rated voltage.
7. Conclusion:
A numerical model for skin-effect calculation was verified with FEM. A combined analytical/FEM model was developed to calculate fundamental starting current, accounting for saturation and additional iron losses; FEM simulations showed starting current increased by ~35% due to saturation and skin-effect. A test rig was built to measure inter-bar resistivity, revealing it is ~10 times higher in cast aluminium than copper, with aluminium rotors showing uneven distribution. An analytical model for inter-bar currents was derived; simulations showed these currents increase rapidly with decreasing resistivity in skewed machines, making skewing ineffective and consistent with findings in [18].
In skewed rotors, inter-bar currents significantly affect starting performance. Fundamental frequency inter-bar currents contribute useful torque. Slot harmonic inter-bar currents cause large asynchronous torques, reducing pull-out torque, potentially preventing starting in some cases (Motor A). These effects depend strongly on the stator/rotor slot combination.
Good agreement was found between simulated and measured starting characteristics for Motor B (Al and Cu rotors). Simulations predicted a 4.5% higher pull-out torque for the Al rotor than the equivalent Cu rotor, attributed to increased fundamental torque (Al) rather than braking torques (Cu). Measurements confirmed this trend, showing an even larger difference (7%), concluding that inter-bar currents have a considerable effect on starting performance. At rated speed, braking torques and associated harmonic joule losses are larger in the Al rotor than the Cu rotor, potentially reaching 1% of output power.
8. References:
- [1] A.R. Hagen, A. Binder, M. Aoulkadi, T. Knopik, and K. Bradley. Comparison of measured and analytically calculated stray load losses in standard cage induction machines. 18th International Conference on Electrical Machines, pages 1–6, 2008.
- [2] H. Nishizawa, K. Itomi, S. Hibino, and F. Ishibashi. Study on reliable reduction of stray load losses in three-phase induction motor for mass production. IEEE Transactions on Energy Conversion, EC-2:489–495, 1987.
- [3] A. Boglietli, A. Cavagnino, M. Lazzari, and A. Pastorelli. Induction motor efficiency measurements in accordance to ieee 112-b, iec 34-2 and jec 37 international standards. IEEE International Electric Machines and Drives Conference, 3:1599–1605, 2003.
- [4] A.A. Jimoh, R.D. Findlay, and M. Poloujadoff. Stray losses in induction machines: Part i, definition, origin and measurement. IEEE Transactions on Power Apparatus and Systems, PAS-104:1500–1505, 1985.
- [5] Y.N. Feng, J. Apsley, S. Williamson, A.C. Smith, and D.M. Ionel. Reduced losses in die-cast machines with insulated rotors. IEEE International Electric Machines and Drives Conference, pages 57–64, 2009.
- [6] A. M. Odok. Stray-load losses and stray torques in induction machines. Power Apparatus and Systems, Transactions of the American Institute of Electrical Engineers, 77(3):43–53, 1958.
- [7] P. L. Alger. Induction Machines: Their Behavior and Uses. Taylor & Francis, 1995.
- [8] A. Harson, P.H. Mellor, and D. Howe. Design considerations for induction machines for electric vehicle drives. Seventh International Conference on Electrical Machines and Drives, pages 16–20, 1995.
- [9] K. Dabala. Modified method to determine rotor bar-iron resistance in three-phase copper casted squirrel-cage induction motors. Proceedings of ICEM, pages 231–234, 2006.
- [10] P. L. Alger. Induced high-frequency currents in squirrel-cage windings. Power Apparatus and Systems, Transactions of the American Institute of Electrical Engineers, 76(3):724 – 729, 1957.
- [11] K. Dabala. A new experimental-computational method to determine rotor bar-iron resistance. Proceedings of ICEM, 2:69–72, 1996.
- [12] O. Aglén. Calorimetric Measurements of Losses in Induction Motors. Licentiate thesis, Royal Institute of Technology, Stockholm, Sweden, 1995.
- [13] A.H. Bonnett and T. Albers. Squirrel-cage rotor options for ac induction motors. IEEE Transactions on Industry Applications, pages 1197–1209, 2001.
- [14] A. Behdashti and M. Poloujadoff. A new method for the study of inter-bar currents in polyphase squirrel-cage induction motors. IEEE Transactions on Power Apparatus and Systems, PAS-98(3):902–911, 1979.
- [15] B. Heller and V. Hamata. Harmonic Field Effects in Induction Machines. Elsevier Science Ltd, 1977.
- [16] M. Ivanes and M. Bourmault. Etudes des pertes supplementaires dans les moteurs asynchrones. Technical report, Cie Electro-Mecanique, October 1968.
- [17] A. Behdashti. Contribution a l’etude des pertes supplementaires des machines asynchrones dans une tres large zone de fonctionnement. PhD thesis, L’Institut national polytechnique de Grenoble, June 1975.
- [18] A.C. Smith, S. Williamson, and C.Y. Poh. Distribution of inter-bar currents in cage induction machines. Second International Conference on Power Electronics, Machines and Drives, 1:297–302, 2004.
- [19] P. L. Alger and J. H. Wray. Double and triple squirrel cages for polyphase induction motors. Power Apparatus and Systems, Transactions of the American Institute of Electrical Engineers, 72(2):637 – 645, 1953.
- [20] M. Liwschitz-Garik. Skin-effect bars of squirrel-cage rotors. Power Apparatus and Systems, Transactions of the American Institute of Electrical Engineers, 73(1):255 – 258, 1954.
- [21] S. Williamson and D. R. Gersh. Finite element calculation of double-cage rotor equivalent circuit parameters. IEEE Transactions on Energy Conversion, 11(1):41–48, 1996.
- [22] C. Sadarangani. Electrical machines - design and analysis of induction and permanent magnet motors. KTH Hogskoletryckeriet, 2000.
- [23] P. D. Agarwal and P. L. Alger. Saturation factors for leakage reactance of induction motors. Power Apparatus and Systems, Transactions of the American Institute of Electrical Engineers, 79(3):1037–1042, 1960.
- [24] H. M. Norman. Induction motor locked saturation curves. Transactions of the American Institute of Electrical Engineers, 53(4):536 – 541, 1934.
- [25] B. J. Chalmers and R. Dodgson. Saturated leakage reactances of cage induction motors. Proceedings IEE, 116(8):1395–1404, 1969.
- [26] E. Alm. Elektroteknik, Band 3, Del 2B, Elektromaskinlära - Asynkronmaskinens teori, driftegenskaper och beräkning. Alb. Bonniers boktryckeri, 1931.
- [27] R. Chitroju. Improved Performance Characteristics of Induction Machines with Non-Skewed Asymmetrical Rotor Slots. Licentiate thesis, Royal Institute of Technology, Stockholm, Sweden, 2009.
9. Copyright:
- This material is a paper by "ALEXANDER STENING". Based on "On Inter-bar Currents in Induction Motors with Cast Aluminium and Cast Copper Rotors".
- Source of the paper: [DOI URL]
This material is summarized based on the above paper, and unauthorized use for commercial purposes is prohibited.
Copyright © 2025 CASTMAN. All rights reserved.