This introduction paper is based on the paper "Neural Network-Based Model for Supporting the Expert Driven Project Estimation Process in Mold Manufacturing" published by "Strojniški vestnik - Journal of Mechanical Engineering".
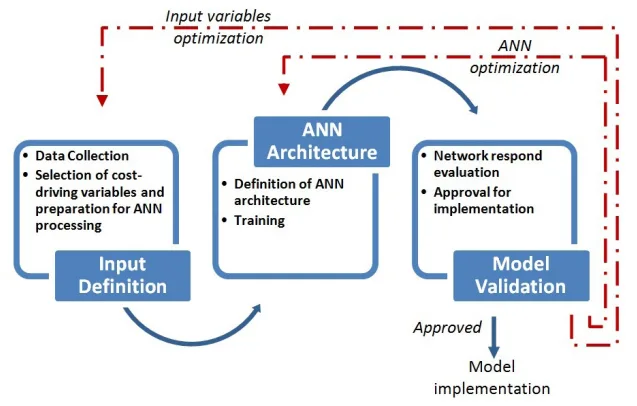
1. Overview:
- Title: Neural Network-Based Model for Supporting the Expert Driven Project Estimation Process in Mold Manufacturing
- Author: Blaž Florjanič, Edvard Govekar, Karl Kuzman
- Year of publication: 2013
- Journal/academic society of publication: Strojniški vestnik - Journal of Mechanical Engineering
- Keywords: mold making, manufacturing, artificial neural networks, estimation process
2. Abstract:
One of the crucial activities for running a successful mold manufacturing business is project estimation. The estimation process is an early project activity which is usually handled by highly skilled, in-house experts. One of the most important parameters affecting the estimation process is the volume of manufacturing hours (VMH) to produce the mold. This article suggests how to address the problem of estimating the volume of manufacturing hours by using the support of an artificial neural network (ANN) model, and its inclusion into the expert driven project estimation process. Based on the histogram of ANN estimations the percentage of unwanted underestimations of the VMH can be estimated as well and decreased by an introduced safety factor. The developed model-based estimation enables an expert to improve project estimation by using easily obtainable input data.
3. Introduction:
The mold making industry is project-driven, characterized by individual production processes. A significant source of risk in project management stems from inaccurate forecasts of project costs and other impacts [1]. Minimizing uncertainty in the early project estimation phase is crucial. This phase is typically a human expert-driven activity, susceptible to bias, potentially leading to underestimation or overestimation of project resources, both of which negatively impact business. Estimators face the challenge of spending minimal time on estimation, as typically less than 10% of offers convert to orders [2]-[4]. Current estimation practices in mold manufacturing heavily rely on intuitive methods, which are subjective and prone to reliability issues.
This paper addresses these challenges by proposing the development of a supported expert-driven project estimation process. The Volume of Manufacturing Hours (VMH) is a critical parameter in project estimation, reflecting the majority of costs and significantly shaping the project schedule. The research objective is to develop an Artificial Neural Network (ANN) supported, expert-driven project estimation process to improve the estimation of VMH in mold production. Additionally, the paper addresses the proper positioning of this supporting model within the existing expert-driven estimation process.
4. Summary of the study:
Background of the research topic:
Project estimation in mold manufacturing is a critical early-stage activity, essential for business success. It is often performed by experienced in-house experts but is challenged by the need for accuracy under time constraints and the inherent subjectivity of intuitive methods. The Volume of Manufacturing Hours (VMH) is a key cost driver and schedule determinant. Inaccurate VMH estimation can lead to economic loss or uncompetitive bids.
Status of previous research:
Various estimation methods exist, including intuitive, analogical, parametric, and analytical methods, each suited to different project stages and data availability (Fig. 1). Much of the existing research focuses on models linking geometric characteristics to cost/price, often overlooking market influences [9]-[12]. While some approaches use single estimation models, this paper proposes a hybrid approach. The literature (Table 1) indicates a focus on cost estimation, with ANN being explored for mold complexity and cost. This study aims to integrate an ANN model as a support tool within an expert-driven framework, combining the strengths of intuitive and data-driven methods.
Purpose of the study:
The primary purpose of this study is to develop an ANN-supported, expert-driven project estimation process specifically to improve the estimation of the Volume of Manufacturing Hours (VMH) in mold production. A secondary aim is to determine the proper placement and integration of such a supporting model within the overall expert-driven estimation workflow.
Core study:
The core of the study involves the development and validation of an ANN-based model for estimating VMH. This model is designed to be integrated into a systematic, expert-driven project estimation process (Fig. 3), acting as a decision support tool. The process consists of phases: Input Data Retrieval (IDR), Conceptual Design and Product Manufacturability Verification (CDPMV), Resource Estimation Phase (REP) – where the ANN model provides VMH estimation support – and Economic Calculation Phase (ECP). The VMH is defined as the total of all machining hours (t_m), loading times (t_l), and unloading times (t_u) for all parts (P) and operations (OP) of the mold, as per Eq. (1):VMH = Σ_P Σ_OP (t_m + t_l + t_u)
(1)
The study details the input variable selection for the ANN, its architecture, training, validation, and a proposed safety-factor approach to handle estimation uncertainties.
5. Research Methodology
Research Design:
The research employed an empirical modeling approach. An Artificial Neural Network (ANN) model was developed to predict the Volume of Manufacturing Hours (VMH). This model was designed to be integrated as a supportive component within a structured, expert-driven project estimation process. The methodology for ANN model creation involved three main phases: input variable definition, ANN architecture definition and training, and model validation (Fig. 4).
Data Collection and Analysis Methods:
Data for the ANN model consisted of 105 samples obtained from a mid-sized mold shop, primarily from automotive industry projects involving 1+1 cavity molds (Fig. 7). Twenty-two input variables were selected based on expert opinion, categorised as: micro and macro part geometry and quality requirements (MMPGQR), technical requirements for the injection mold (TRFIM), and mold design principles/rules (MDP/R) (Table 2, Fig. 5).
A multi-layer feed-forward network trained with the Levenberg-Marquardt algorithm was used. Due to the limited number of samples, a multifold cross-validation procedure was implemented (105 samples divided into five subsets of 21 samples each; training and testing repeated five times). Model performance was evaluated using the correlation coefficient, Relative Percentage Error (RPE), and Mean Absolute Percentage Error (MAPE).
RPE is defined as: RPE = (y_i - t_i) / t_i * 100
(2)
where y_i
is the ANN estimated value and t_i
is the target value.
MAPE is defined as: MAPE = (1/N) Σ_i |(y_i - t_i)/t_i|
(3)
The ANN structure was implemented in a MATLAB environment.
Research Topics and Scope:
The research focused on:
- Developing an ANN model for estimating the Volume of Manufacturing Hours (VMH) for injection molds.
- Identifying and selecting appropriate input variables (22 variables covering part geometry, mold requirements, and design principles) for the ANN model (Table 2).
- Defining and optimizing the ANN architecture (final: 22 input neurons, 4 hidden neurons with sigmoid activation, 1 output neuron with linear activation).
- Validating the ANN model's performance and proposing a practical safety-factor approach to manage estimation uncertainty, particularly underestimation.
The scope was primarily on injection molds used in the automotive industry, specifically 1+1 cavity molds.
6. Key Results:
Key Results:
The developed ANN model demonstrated a good ability to map input data to VMH estimations.
- A strong correlation (correlation coefficient = 0.92545) was observed between the ANN model's output and the target VMH values (Fig. 8).
- The overall network Mean Absolute Percentage Error (MAPE) based on cross-validation using five subsets was 0.133 (Table 3).
- The Relative Percentage Error (RPE) for the overall network ranged from -38.1% (underestimation) to +34.1% (overestimation) (Table 3).
- The majority (89.5%) of the predicted VMH values had an RPE within the range of -25% to +25%. However, 4.8% of predictions resulted in an RPE below -25%, indicating significant underestimation in these cases (Fig. 9, Fig. 10).
- The most extreme underestimation observed was an RPE of -38.1%.
- To address the risk of underestimation, a safety-factor approach was proposed. Based on the RPE histogram (Fig. 10), it was found that 20% of all outputs have an RPE of -15% or less.
- Applying a 15% safety factor (artificially shifting the RPE histogram towards overestimation) is expected to result in approximately 20% of cases falling into a safer underestimation interval (Fig. 11).
- A more conservative 25% safety factor is advised, which would lead to only around 4.8% of cases falling into an underestimation interval.
The study provides a systematic, expert-driven project estimation process supported by ANN (Fig. 3), where the ANN output serves as an evaluation indicator for the expert.
Figure Name List:
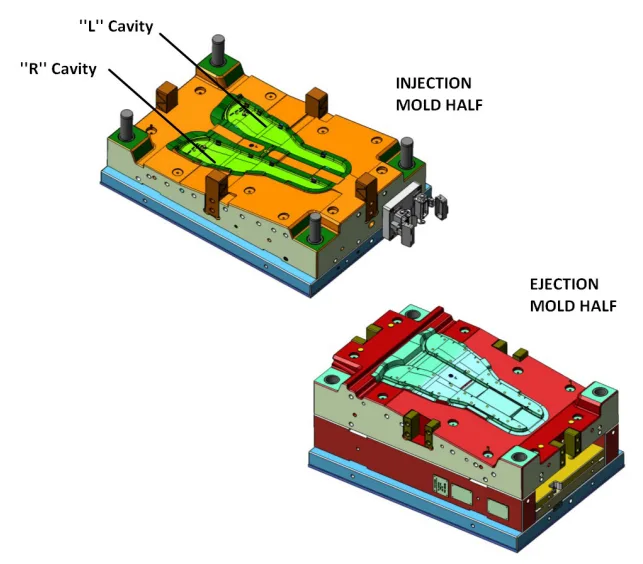

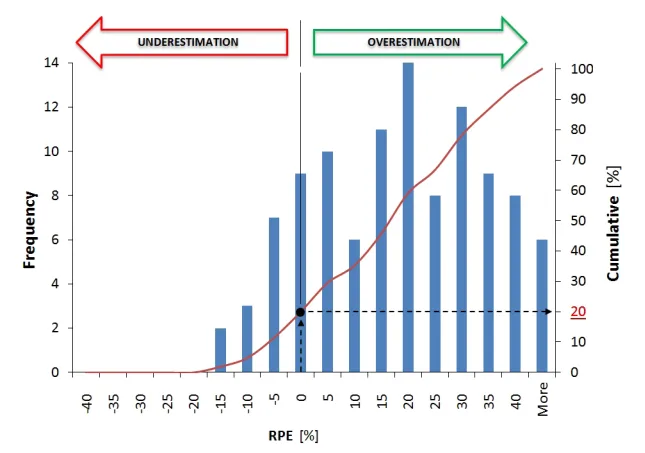
- Fig. 1. Estimation methods applicable in different stages of the project
- Fig. 2. Expert estimation solution space
- Fig. 3. The systematic, expert driven project estimation process supported by ANN
- Fig. 4. General ANN-based estimation model creation
- Fig. 5. Dominant factors defining ANN inputs
- Fig. 6. ANN initial architecture
- Fig. 7. Example of typical injection mold for automotive industry holding geometry for mirrored parts (left and right side of the vehicle)
- Fig. 8. Scatter plot of network outputs vs. target outputs
- Fig. 9. RPE for each sample
- Fig. 10. RPE sample histogram and cumulative distribution
- Fig. 11. RPE sample histogram and cumulative distribution using 15% safety factor
7. Conclusion:
The paper successfully proposes an implementation of an ANN-based model as an expert support tool within the project estimation process for mold manufacturing. This supported project estimation process acts as a bridge between traditional expert-driven intuitive models and data-driven models. The presented ANN model for estimating VMH meets the requirements of relevancy, simplicity, and reliability. A key benefit of ANN is its ability to model complex multivariable relationships. However, the model did exhibit output deviations in some instances, which should not be overlooked in practical applications.
By implementing a safety-factor approach, guidance is provided to experts on interpreting network outputs to reduce the probability of unwanted project underestimation and achieve acceptable estimation confidence. The proposed supported estimation approach offers several benefits:
- Lowered risk of underestimating project complexity.
- Embedded repeatability and stability in the decision-making process.
- Improvement in expert estimation reliability.
- A significantly shorter estimation process.
- Enabling enterprises to foresee sufficient manufacturing resources in the early project stage.
- Adaptability to any mold shop by using environment-specific input data.
- Potential use as a learning assistant for novice estimators.
The primary limitation of this study is the restricted number of samples used for model development. Furthermore, the assumption that information is incomplete due to a limited number of parameters is acknowledged. Future research will consider the implementation and development of a specially tailored expert elicitation model to overcome these limitations.
8. References:
- [1] Flyvbjerg, B. (2006). From Nobel prize to project management: getting risks right. Project Management Journal, vol. 37, no. 3, p. 5-15.
- [2] Fonseca, M., Henriques, E., Ferreira, A., Jorge, J. (2007). Assisting mould quotation though retrieval of similar data. Digital Enterprise Technology, Session 5, p. 527-534, DOI:10.1007/978-0-387-49864-5_62.
- [3] Duverlie, P., Castelain, J.M. (1999). Cost estimation during design step: Parametric method versus case based reasoning method. The International Journal of Advanced Manufacturing Technology, vol. 15, no. 12, p. 895-906, DOI:10.1007/s001700050147.
- [4] Denkena, B., Lorenzen, L.E., Schürmeyer, J. (2009). Rule-based quotation costing of pressure die casting moulds. Production Engineering, vol. 3, no. 1, p. 87-94, DOI:10.1007/s11740-008-0139-8.
- [5] Ficko, M., Drstvenšek, I., Brezočnik, M., Balič, J., Vaupotič, B. (2005). Prediction of total manufacturing costs for stamping tool on the basis of CAD-model of finished product. Journal of Materials Processing technology, vol. 164-165, p. 1327-1335, DOI:10.1016/j.jmatprotec.2005.02.013.
- [6] Farineau, T., Rabenasolo, B., Castelain, J.M., Meyer, Y., Duverlie, P. (2001). Use of parametric models in an economic evaluation step during the design phase. The International Journal of Advanced Manufacturing Technology, vol. 17, no. 2, p. 79-86, DOI:10.1007/s001700170195.
- [7] Rihar, L., Kušar, J., Duhovnik, J., Starbek, M. (2010). Teamwork as a pre-condition for simultaneous product realization. Concurrent Engineering Research and Application, vol. 18, no. 4, p. 261-273, DOI:10.1177/1063293X10389789.
- [8] Kušar, J., Rihar, L., Duhovnik, J., Starbek, M. (2008). Product management of product development, Strojniški vestnik - Journal of Mechanical Engineering, vol. 54, no. 9, p. 588-606.
- [9] Raviwongse, R., Allada, V. (1997). Artificial neural network based model for computation of injection mold complexity. The International Journal of Advanced Manufacturing Technology, vol. 13, no. 8, p. 577-586, DOI:10.1007/BF01176302.
- [10] Fagade, A.A., Kazmer, D.O. (1999). Modelling the effects of complexity on manufacturing costs and time-to-market of plastic injection molded products. Proceedings of the Tenth Annual Conference of Production and Operations Management Society, Charleston.
- [11] Fagade, A.A., Kazmer, D.O. (1999). Effects of complexity on tooling cost and time-to-market of plastic injection molded parts. Proceedings ANTEC, p. 3304-3308.
- [12] Che, Z.H. (2010). PSO-based back-propagation artificial neural network for production and mold cost estimation of plastic injection molding. Computer & Industrial Engineering, vol. 58, no. 4, p. 625-637, DOI:10.1016/j.cie.2010.01.004.
- [13] Wang, H., Zhou, X.H., Rouan, X.Y. (2003). Research on injection mould intelligent cost estimation system and key technologies. The International Journal of Advanced Manufacturing Technology, vol. 21, no. 3, p. 215-222, DOI:10.1007/s001700300024.
- [14] Cavalier, S., Maccarone. P., Pinto, R. (2004). Parametrical vs. neural network models for estimation of product costs: a case study in the automotive industry. International Journal of Production Economics, no. 91, p. 165-177, DOI:10.1016/j.ijpe.2003.08.005.
- [15] Farineau, T., Rabenasolo, B., Castelain, J.M. (2002). Choice of cost-estimation functions based on statistical quality criteria and technical coherence. The International Journal of Advanced Manufacturing Technology, vol. 19, no. 7, p. 544-550, DOI:10.1007/s001700200058.
- [16] Elhag, T.M.S., Boussabine, A.H. (1999). Tender price estimation: Neural networks vs. regression analysis. Proceedings of COBRA RICS Research Foundation, Salford.
- [17] Verlinden, B., Duflou, J.R., Collin, P., Cattrysse, D. (2008). Cost estimation for sheet metal parts using multiple regression and artificial neural networks: A case study. International Journal of Production Economics, vol. 111, no. 2, p. 484-492, DOI:10.1016/j.ijpe.2007.02.004.
- [18] Kim, G.H., An, S.H., Kang, K.I., (2004). Comparison of construction cost estimating models based on regression analysis, neural networks, and case-based reasoning. Building and Environment, vol. 39, no. 10, p. 1235-1242, DOI:10.1016/j.buildenv.2004.02.013.
- [19] Chan, S.F., Law, C.K., Chan, Κ.Κ. (2003). Computerised price quoting system for injection mould manufacture. Journal of Materials Processing Technology, vol. 139, no. 1-3, p. 212-218, DOI:10.1016/S0924-0136(03)00222-X.
- [20] Denkena, B., Schürmeyer, J., Böß, V., Kaddour, R. (2011). CAD-based cost calculation of mould cavities. Production Engineering, vol. 5, no. 1, p. 73-79, DOI:10.1007/s11740-010-0277-7.
- [21] Chin, K.S., Wong, T.N. (1996). Developing a knowledge-based injection mold cost estimation system by decision tables. The International Journal of Advanced Manufacturing Technology, vol. 11, no. 5, p. 353-365, DOI:10.1007/BF01845694.
- [22] Fagade, A.A., Kazmer, D.O. (1998). Economic design of injection molded parts using DFM guidelines - a review of two methods for tooling cost estimation. Proceedings ANTEC, Atlanta, p. 869-873.
- [23] Fagade, A.A., Kazmer, D.O. (2000). Early cost estimation for injection molded components. Journal of Injection Molding Technology, vol. 4, no. 3, p. 97-106.
- [24] Nagahanumaiah, Ravi, B., Mukherjee, N.P., (2005). An integrated framework for die and mold cost estimation using design features and tooling parameters. The International Journal of Advanced Manufacturing Technology, vol. 26, no. 9-10, p. 1138-1149, DOI:10.1007/s00170-004-2084-9.
- [25] Navodnik, J., Kopčič, M. (1998). Plastic – moldmaking handbook, 3rd. revised ed. Navodnik-Chemical Engineering, Velenje. (in Slovene).
- [26] Menges, G., Michaeli, W., Mohren, P. (2000). How To Make Injection Molds, 3rd ed., Hanser Gardner Publications, Cincinatti.
- [27] Kazmer, D.O. (2007). Injection Mold Design Engineering, Hanser Gardner Publications, Cincinnati, DOI:10.3139/9783446434196.
- [28] Kušar, J., Duhovnik, J., Tomaževič, R., Starbek, M. (2007). Finding and evaluating customers needs in the product-development process. Strojniški vestnik - Journal of Mechanical Engineering, vol. 53, no. 2, p. 78-104.
- [29] Beale, M.H, Hagan, M.T., Demuth, H.W. (2010). MATLAB, Neural Network Toolbox™ 7, User's Guide, online edition, The MathWorks, Inc., Natic, from: http://www.mathworks.com/help/pdf_doc/nnet/nnet_ug.pdf, accessed at 11-10-25.
9. Copyright:
- This material is a paper by "Blaž Florjanič, Edvard Govekar, and Karl Kuzman". Based on "Neural Network-Based Model for Supporting the Expert Driven Project Estimation Process in Mold Manufacturing".
- Source of the paper: https://doi.org/10.5545/sv-jme.2012.747
This material is summarized based on the above paper, and unauthorized use for commercial purposes is prohibited.
Copyright © 2025 CASTMAN. All rights reserved.