This article introduces the paper "Mechanical Properties and Deformation Behaviour of High-Pressure Die-Cast Magnesium-Aluminium Based Alloys".
1. Overview:
- Title: Mechanical Properties and Deformation Behaviour of High-Pressure Die-Cast Magnesium-Aluminium Based Alloys
- Author: Hua Qian Ang (Vivian)
- Publication Year: October 2017
- Publishing Journal/Academic Society: RMIT University, School of Engineering, College of Science Engineering and Health (Doctor of Philosophy Thesis)
- Keywords: High-pressure die-casting; magnesium alloys; deformation behaviour; mechanical properties; strain-rate sensitivity; constitutive modelling
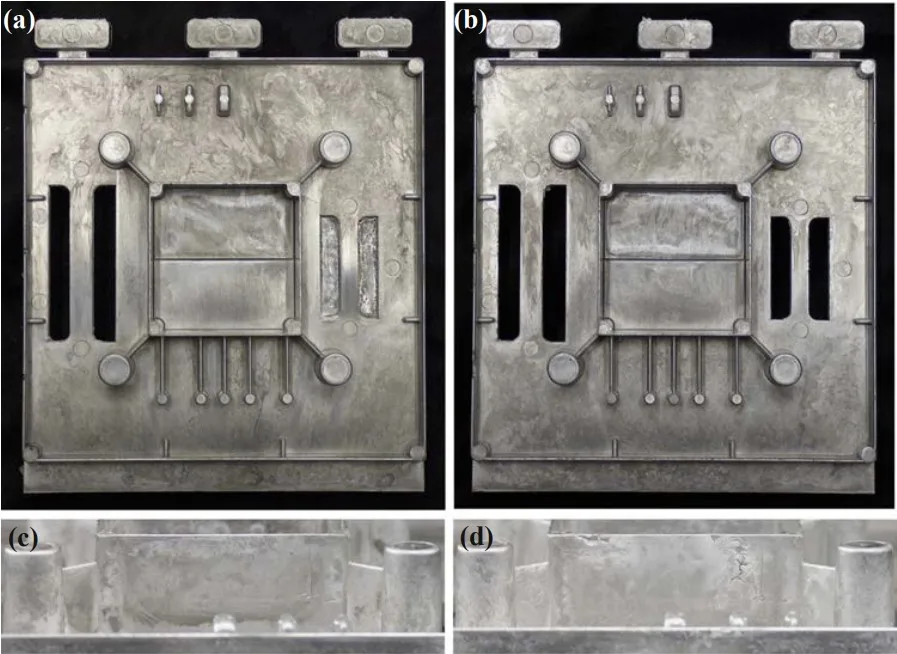
2. Research Background:
- Social/Academic Context of the Research Topic: The increasing demand for enhanced fuel efficiency and reduced greenhouse gas emissions necessitates weight reduction in automotive applications. High-pressure die-cast magnesium alloys are promising candidates for automotive structural components due to their low density and high specific strength, offering significant weight reduction compared to aluminum, steel, and cast iron. Structural alloys require high strength and ductility for energy absorption in crash scenarios and manufacturing processes like self-piercing riveting.
- Limitations of Existing Research: While anelasticity plays a crucial role in magnesium alloy deformation, it has received less attention compared to elasticity and plasticity. Existing research lacks comprehensive investigation into the effects of strain rate and aluminium content on anelasticity.
- Necessity of the Research: To enhance the mechanical properties of high-pressure die-cast magnesium alloys for structural applications, a fundamental understanding of their deformation behavior under loading is essential. This research aims to address this gap by investigating the deformation mechanisms of these alloys.
3. Research Purpose and Research Questions:
- Research Purpose: The primary aim of this research is to investigate the mechanical properties and deformation behaviour of commercial high-pressure die-cast magnesium-aluminium based alloys, specifically Mg-4Al-0.3Mn (AM40), Mg-6Al-0.3Mn (AM60), Mg-9Al-1Zn (AZ91) and Mg-4Al-4RE (AE44), across a broad strain-rate range of 10-6-10-1 s-1.
- Key Research Questions:
- How do strain rate and aluminium content affect the mechanical properties and deformation behaviour of high-pressure die-cast magnesium-aluminium alloys?
- How does anelasticity influence the proof stress measurement of magnesium alloys?
- What are the individual contributions of elasticity, anelasticity, and plasticity to the overall deformation behaviour, and how are they influenced by strain rate and aluminium content?
- How can the deformation mechanisms (slip and twinning) be correlated to the different stages of the stress-strain curve, and can constitutive equations be developed to model these stages?
- Research Hypotheses:
- Anelasticity introduces ambiguities in proof stress measurement of magnesium alloys.
- Strain-rate sensitivity in die-cast magnesium-aluminium alloys decreases with increasing aluminium solute level in the α-magnesium matrix.
- Anelasticity is strain-rate insensitive, while plasticity by prismatic slip is strain-rate sensitive.
4. Research Methodology
- Research Design: This research employed an experimental design involving a critical review of standardized proof stress measurement methods and a series of experimental studies. These studies focused on:
- Proof stress measurement of die-cast magnesium alloys.
- The effect of strain rate and aluminium content on the deformation behaviour.
- Anelasticity of die-cast magnesium-aluminium based alloys under different strain rates.
- Constitutive modelling of the deformation behaviour.
- Data Collection Method: Data was collected through:
- Monotonic tension testing across a range of strain rates (10-6-10-1 s-1).
- Cyclic tension loading-unloading testing to characterize anelasticity.
- Application of four standardized proof stress measurement methods (Method 1, Method 2, Method 3, and Method 4).
- Analysis Method: The collected data was analyzed using:
- Statistical and qualitative analysis of mechanical properties.
- Stress-strain curve analysis to identify deformation stages and parameters.
- Constitutive modelling to develop a predictive model for deformation behaviour.
- Microstructural characterization using Scanning Electron Microscopy (SEM), Energy Dispersive X-ray Spectroscopy (EDX), and Electron Backscattered Diffraction (EBSD).
- Research Subjects and Scope: The research focused on commercial high-pressure die-cast magnesium-aluminium based alloys:
- Mg-4Al-0.3Mn (AM40)
- Mg-6Al-0.3Mn (AM60)
- Mg-9Al-1Zn (AZ91)
- Mg-4Al-4RE (AE44)
- T5-aged AE44
5. Main Research Results:
- Key Research Results:
- Proof Stress Measurement: Anelasticity was found to cause inconsistencies in proof stress measurements using standardized methods. A pragmatic approach using a higher offset strain of 0.45% was proposed to achieve a more accurate 0.2% residual plastic strain for proof stress determination in die-cast magnesium alloys.
- Strain-rate Sensitivity: Alloys with lower aluminium content in solid solution exhibited higher strain-rate sensitivity, manifesting as increased work hardening and tensile/yield ratio. The decrease in strain-rate sensitivity with increasing aluminium solute level was attributed to dynamic strain ageing within the α-magnesium matrix. High strain-rate sensitivity of prismatic and pyramidal slip was also observed.
- Anelasticity: Anelasticity was found to be strain-rate insensitive, while plasticity by prismatic slip was strain-rate sensitive. The high strain-rate sensitivity of prismatic slip led to variations in maximum anelasticity with strain rate. AZ91, with the highest aluminium content in solution, exhibited the largest maximum anelasticity.
- Constitutive Modelling: A semi-empirical model was developed that provides a good fit to the experimental stress-strain curves for most alloys, slightly overestimating stress in the Stage II-III transition region for AZ91.
- Statistical/Qualitative Analysis Results:
- Proof stress measurement by Method 1 varies with elastic modulus E, decreasing from 45 GPa to 38 GPa with increasing stress.
- Secant elastic modulus, Esec, decreases with increasing plastic strain and loop width in cyclic tests.
- Anelastic strain is approximately 0.25% at 0.2% permanent plastic strain for tested alloys.
- Strain-rate sensitivity, m, decreases rapidly with increasing aluminium content, becoming negligible above 3 wt.% Al.
- Strain hardening rate, Θ, in Stage III varies from 1 to 2 GPa depending on alloy composition.
- Data Interpretation: The deformation behaviour of die-cast magnesium alloys is complex and can be separated into three deformation regions: elastic, anelastic, and plastic. Further decomposition reveals four stages in the stress-strain curve: elastic (stage I), basal slip and twinning (stage II), prismatic slip (stage III), and pyramidal slip (stage IV).
- Figure Name List:
- Figure 2.14: An overview of the cyclic tension loading-unloading stress-strain curve of pure magnesium
- Figure 2.17: Anelastic strain (%) at 2% of plastic strain of pure magnesium, AZ91, Mg-0.8Zn and Mg-2.3Zn and Mg-1.5Gd as a function of grain size.
- Figure 2.18: The anelastic strain as a function of the applied tensile (solid lines) or compressive (dashed lines) plastic strain, for AZ91 in two different casting conditions: sand-cast (sc) and high-pressure die-cast (hpdc)
- Figure 2.19: Anelastic strain as a function of the tensile (solid lines) and compressive (dashed lines) plastic strain, for pure magnesium and various (a) zinc contents, (b) gadolinium contents and (c) aluminium contents.
- Figure 2.20: Stress-strain curves of HPDC AS21 with a best fit model of stress, σ as a function of strain, ε and strain rate, ε̇.
- Figure 2.21: Strain-rate sensitivity, m versus aluminium content (wt.%) for pure magnesium, and various ternary magnesium alloys.
- Figure 2.22: Strain-rate sensitivity, m as a function of strain rates covering from creep to dynamic strain rates, for pure magnesium and other ternary magnesium alloys.
- Figure 3.14: Room-temperature monotonic tensile curves of die-cast magnesium alloys AM40, AM60, AZ91, AE44 and T5-aged AE44 at strain rate, ε̇ of 10-4 s-1
- Figure 3.15: A comparison of monotonic and cyclic tensile curves of AM60 at strain rate 10-3 s-1
- Figure 1: Proof stress measurement methods: (a) Method 1, (b) Method 2 as specified in ASTM E8M-09 and (c) Method 3 and (d) Method 4 as stated in ISO 6892-1
- Figure 2: Proof stress values measurement by Method 1 for die-cast AE44, AM60 and AZ91 alloys
- Figure 3: Tensile curves of die-cast AE44, AM60, AZ91 and A380 showing respectively proof stress values measured by Method 2
- Figure 4: Cyclic stress-strain curve of AE44 showing proof stress measured by Method 3
- Figure 5: Cyclic stress-strain curve of A380 showing proof stress measurement by Method 3
- Figure 6: (a) Secant elastic modulus, Esec (GPa) and (b) anelastic strain (%) as a function of tensile permanent plastic strain (%)
- Figure 7: Proof stress measurement by Method 4 for AE44 where the alternative elastic modulus, Ealt is 33.3 GPa
- Figure 8: Inconsistency within Method 4 providing different alternative elastic moduli, Ealt, leading to a variation in proof stress values
- Figure 9: An overview of monotonic and cyclic stress-strain curves of die-cast (a) AE44, (b) AM60 and (c) AZ91
- Figure 10: Permanent plastic strain as a function of offset strain (plastic strain + anelastic strain) for die-cast magnesium alloys.
- Figure 11: Stress-strain curve ofAM60 showing a comparison of 0.2% and 0.5% offsets and the influence of errors in modulus determination
- Figure 1: True stress-strain curves of as-cast (a) AM40, (b) AM60, (c) AZ91, (d) AE44 and T5-aged (e) AE44 at different nominal strain rates, ε̇
- Figure 2: Effects of strain rate on (a) strength (MPa) and (b) elongation to fracture (%) of as-cast AM40, AM60, AZ91, AE44 and T5-aged AE44
- Figure 3: Variations of strain-rate sensitivity with (a) true strain, covering strain rates, ε̇ from 10-6-10-1 s-1 and (b) with strain rate at 3% strain.
- Figure 4: EBSD maps showing formation of different types of twins in as-cast AE44, AM60, and AZ91 specimens after tensile testing at different strain rates.
- Figure 5: Secondary electron images of fracture surfaces of (a, b) AM60, (c, d) AZ91 and (e, f) AE44 at different strain rates
- Figure 6: Backscattered electron images and EDX line profiles of the α-Mg matrix in (a) AM40, (b) AM60, (c) AZ91, (d) AE44, and (e) AE44-T5.
- Figure 7: A correlation of strain-rate sensitivity and Al solute concentration: (a) Inverse strain-rate sensitivity versus Al solute level in Mg phase and (b) strain-rate sensitivity as a function of sample diameter and thicknesses in die-cast AM60.
- Figure 1: An overview of cyclic stress-strain curve of die-cast AE44 at 10-4 s-1
- Figure 2: Monotonic flow curves of (a) AZ91 and (b) AE44 at strain rates 10-6-10-1 s-1
- Figure 3: Anelastic strain (defined in Fig. 1) as a function of strain, for as-cast (a) AM40, (b) AM60, (c) AZ91, (d) AE44 and (e) T5-aged AE44, at strain rate range 10-6-10-1 s-1
- Figure 4: EBSD maps of AE44 showing (a) twin-free microstructure in as-cast condition and the formation of different types of twins at (b,c) 10-6 s-1 and (d, e) 10-1 s-1 after cyclic testing to 3% strain.
- Figure 5: TEM observations of dislocations pile-ups at twin and grain boundaries in AE44 cyclic tested to 3% strain at (a) 10-6 s-1 and (c) 10-1 s-1
- Figure 6: A correlation between onsets of stages II and III with anelastic strain. (a) Monotonic tensile flow curve with the onsets of stage II marked by ‘O’ and stage III marked by ‘X’ and (b) stress as a function of anelastic strain at strain rate 10-4 s-1.
- Figure 7: Maximum anelastic strain as a function of strain rate, for all alloys tested.
- Figure 8: Offset strain (plastic strain + anelastic strain) as a function of permanent plastic strain for (a) AZ91 and (b) AE44 at strain rate range 10-6-10-1 s-1.
- Figure 1: Monotonic (dashed) and cyclic (solid) stress-strain behaviour of (a) AZ91 and (b) AE44 at different strain rates, ε̇ =10-6-10-2 s-1
- Figure 2: Applied stress as a function of Stage II strain, for as-cast (a) AM40, (b) AM60, (c) AZ91, (d) AE44 and (e) AE44-T5, at strain-rate range 10-6-10-1 s-1.
- Figure 3: Comparison of Weibull function and power law.
- Figure 4: Stress when εIII reaches 0.01 for as-cast AM40, AM60, AZ91, AE44 and T5-aged AE44 and 0.015 for AZ91 as a function of maximum anelastic stress.
- Figure 5: Average deformation behaviour of stage II for AZ91 and AE44, best fit using Eq. (3) (dashed) are compared with experiments (solid).
- Figure 6: Experimental flow curves (solid) of (a) AZ91 and (b) AE44 at strain rates 10-6-10-1 s-1 are compared with best fit linear lines (dashed) according to Eq. (4).
- Figure 7: The strain hardening rate, Θ in Stage III for present alloys at different strain rates.
- Figure 8: The prismatic yield stress, σy of present alloys at different strain rates.
- Figure 9: Experimental (solid) and best fit (dashed) stress-strain curve of stage IV for (a) AZ91 and (b) AE44.
- Figure 10: Comparison of Ludwik’s and Hollomon’s models with KIV and nIV of best fit of Eq. (13).
- Figure 11: Comparison of experimental (coloured) and modelled (black) stress-strain curves of (a) AM40, (b) AM60, (c) AZ91, (d) AE44, and (e) AE44-T5 at wide strain-rate range 10-6-10-1 s-1
- Figure 12: Enlarged stress-strain curve in the Stage II-III transition region for the present die-cast alloys.
- Figure 8.2: Comparison of (a) proof stress and (b) % elongation to fracture of magnesium and aluminium casting alloys.
- Figure 8.3: Fractions of (a) elastic and (b) anelastic + plastic for present die-cast magnesium alloys.
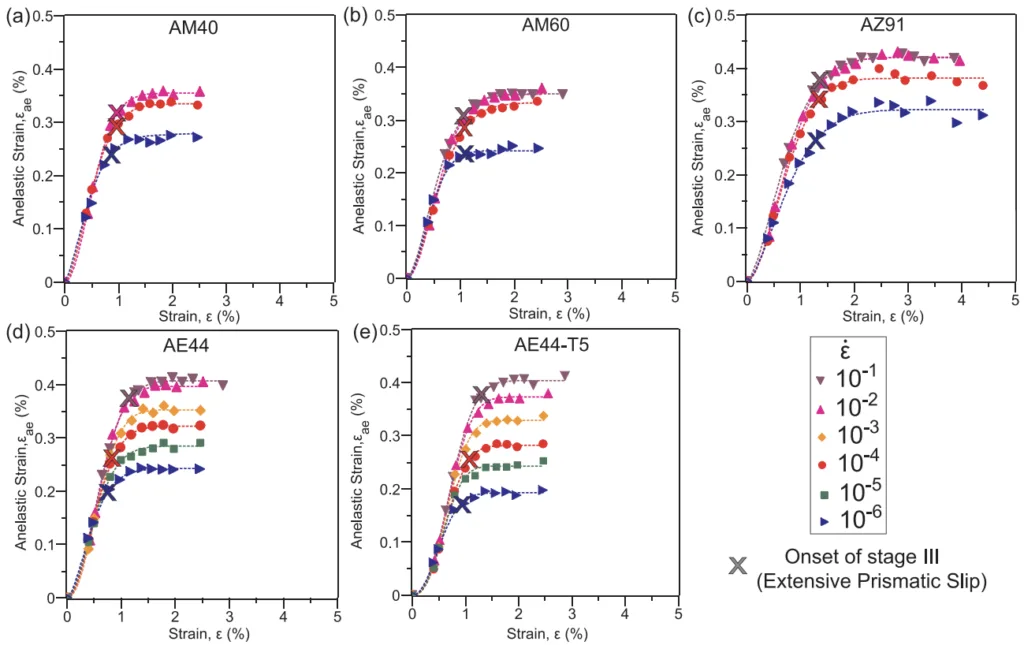
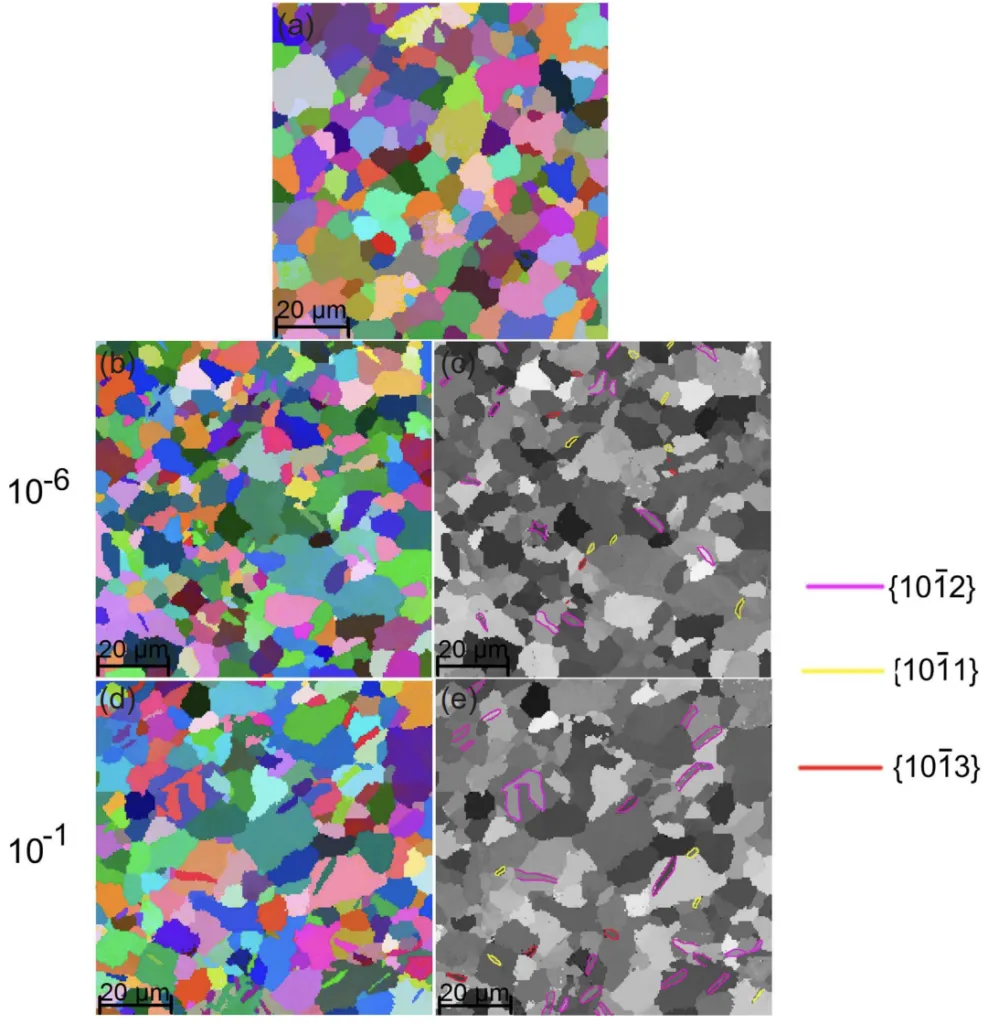
6. Conclusion and Discussion:
- Summary of Main Results: This research addressed inconsistencies in proof stress measurement, strain-rate sensitivity, anelasticity, and developed a constitutive model for die-cast magnesium-aluminium alloys. A higher offset strain method improved proof stress consistency. Strain-rate sensitivity decreased with increasing aluminium solute level due to dynamic strain ageing. Anelasticity was strain-rate insensitive, while plasticity by prismatic slip was strain-rate sensitive. A four-stage constitutive model effectively described the complex deformation behaviour.
- Academic Significance of the Research: This research provides a more consistent method for proof stress determination in die-cast magnesium alloys, enhancing the comparability of material properties. It elucidates the influence of basal slip and reversible twinning on proof stress and comprehensively describes the deformation behaviour of these alloys across four distinct stages. The study highlights the role of aluminium solute in moderating strain-rate sensitivity and the complex interplay between slip and twinning mechanisms in determining anelasticity.
- Practical Implications: The proposed consistent proof stress determination method enables more reliable comparison of magnesium alloy properties for engineering applications. The findings suggest that magnesium alloys, particularly AE44, can exhibit improved energy absorption at higher strain rates, benefiting crashworthiness in automotive structural applications.
- Limitations of the Research: The constitutive model slightly overestimated stress in the Stage II-III transition region for AZ91, indicating a need for further refinement for highly concentrated alloys.
7. Future Follow-up Research:
- Directions for Follow-up Research: Future research should further explore the effects of strain rate and aluminium content on anelasticity, particularly outside the quasi-static strain rate regime. Further investigation into the deformation mechanisms, especially the role of precipitates and intermetallic networks, is warranted to refine constitutive models and develop improved structural alloys.
- Areas Requiring Further Exploration:
- The effects of strain rate and aluminium content on anelasticity at higher strain rates.
- The precise mechanisms by which precipitates and intermetallic networks influence anelasticity and deformation behaviour.
- Refinement of the constitutive model to improve its accuracy in the Stage II-III transition region, especially for high aluminium content alloys like AZ91.
- Investigation of fatigue properties of AE44-T5 and the impact of anelastic deformation on fatigue life.
8. References:
- [1] M.A. Meyers, Dynamic Behaviour of Materials, John Wiley & Sons, New York, 1994.
- [2] T.B. Abbott, M.A. Easton, R. Schmidt, Magnesium for crashworthy components, in: M. Byko (Ed.), Journal of The Minerals, Metals, and Materials Society, TMS Annual Meeting, California, 2003, pp. 227-230.
- [2] C.A. Newland, M.T. Murray, Strain rate dependent behaviour of magnesium-based alloys, in: Proceedings of the First Australasian Congress on Applied Mechanics, Institution of Engineers, Australia, 1996, pp. 73-76.
- [4] N. Stanford, M.R. Barnett, Effect of Al and Gd solutes on the strain rate sensitivity of magnesium alloys, Metall. Mater. Trans. A 41 (2010) 734-743.
- [5] T.K. Aune, D. Albright, H. Westengen, T.E. Johnsen, B. Anderson, Behavior of die cast magnesium alloys subject to rapid deformation, SAE Technical Paper, 2000 pp. 2000-01- 1116.
- [6] J.P. Weiler, J.T. Wood, Strain-rate effects of sand-cast and die-cast magnesium alloys under compressive loading, in: S.N. Mathaudhu, W.H. Sillekens, N.R. Neelameggham, N. Hort (Eds.), Magnesium Technology 2012, John Wiley & Sons, Florida, 2012, pp. 365-370.
- [7] A.V. Nagasekhar, M.A. Easton, C.H. Cáceres, Solute content and the grain microstructure of high pressure die cast magnesium–aluminium alloys, Adv. Eng. Mater. 11 (2009). 912- 919.
- [8] H.Q.Ang, S.M.Zhu, T.B.Abbott, Q.Dong, M.A.Easton, Strain-rate sensitivity of die-cast magnesium-aluminium based alloys
- [Accepted]. http://dx.doi.org/10.1016/j.msea.2017.05.093
- [9] H.Q. Ang, T.B. Abbott, S.M. Zhu, C.F. Gu, M.A. Easton, Proof stress measurement of diecast magnesium alloys, Mater. Des. 112 (2016) 402-409.
- [10] E. Karimi, A. Zarei-Hanzaki, M.H. Pishbin, H.R. Abedi, P. Changizian, Instantaneous strain rate sensitivity of wrought AZ31 magnesium alloy, Mater. Des. 49 (2013) 173-180.
- [11] W.S. Lee, T.H. Chen, Rate-dependent deformation and dislocation substructure of Al–Sc alloy, Scr. Mater. 54 (2006) 1463-1468.
- [12] T. Matsunaga, H. Somekawa, H. Hongo, M. Tabuchi, Deformation mechanism transition with strain rate in Mg–3Al–1Zn alloy at room temperature, Mater. Sci. Eng. A 647 (2015) 212-215.
- [13] R.B. Figueiredo, F. Poggiali, C. Silva, P.R. Cetlin, T.G. Langdon, The influence of grain size and strain rate on the mechanical behavior of pure magnesium, J. Mater. Sci. 51 (2016). 3012-3024.
- [14] X.Z. Lin, D.L. Chen, Strain hardening and strain-rate sensitivity of an extruded magnesium alloy, J. Mater. Eng. Perform. 17 (2008). 894-901.
- [15] L.P. Kubin, Y. Estrin, Dynamic strain ageing and the mechanical response of alloys, J. Phys. III 1 (1991) 929-943.
- [16] L. Jiang, J.J. Jonas, R. Mishra, Effect of dynamic strain aging on the appearance of the rare earth texture component in magnesium alloys, Mater. Sci. Eng. A 528 (2011) 6596-6605.
- [17] A. Van den Beukel, Theory of the effect of dynamic strain aging on mechanical properties, Phys. Stat. Sol. (a) 30 (1975) 197-206.
- [18] Z. Trojanová, P. Lukác, K.U. Kainer, V. Gärtnerová, Dynamic strain ageing during stress relaxation in selected magnesium alloys containing rare earth elements, Adv. Eng. Mater. 7 (2005) 1027-1032.
- [19] S.M. Zhu, J.F. Nie, M.A. Gibson, M.A. Easton, P. Bakke, Microstructure and creep behavior of high-pressure die-cast magnesium alloy AE44, Metall. Mater. Trans. A 43 (2012) 4137-4144.
- [20] S.M. Zhu, M.A. Easton, T.B. Abbott, M.A. Gibson, J.F. Nie, The influence of individual rare earth elements (La, Ce, or Nd) on creep resistance of die‐cast magnesium alloy AE44, Adv. Eng. Mater. 18 (2016) 932-937.
- [21] M.I. Khan, A.O. Mostafa, M. Aljarrah, E. Essadiqi, M. Medraj, Influence of cooling rate on microsegregation behavior of magnesium alloys, J. Mater. (2014) 1-18.
9. Copyright:
- This material is Hua Qian Ang (Vivian)'s paper: Based on Mechanical Properties and Deformation Behaviour of High-Pressure Die-Cast Magnesium-Aluminium Based Alloys.
- Paper Source: https://doi.org/10.1016/j.matdes.2016.09.088
This material was summarized based on the above paper, and unauthorized use for commercial purposes is prohibited.
Copyright © 2025 CASTMAN. All rights reserved.