This article introduces the paper ["Investigation on Microstructure and Wear Study on Al-Zn-Mg Alloy Hybrid Composites Fabricated Through Die Casting Process"] published by EVERGREEN Joint Journal of Novel Carbon Resource Sciences & Green Asia Strategy.
1. Overview:
- Title: Investigation on Microstructure and Wear Study on Al-Zn-Mg Alloy Hybrid Composites Fabricated Through Die Casting Process
- Author: L Bharath, J Kumaraswamy, T V Manjunatha, Suchendra K R
- Publication Year: 2024
- Publishing Journal/Academic Society: EVERGREEN Joint Journal of Novel Carbon Resource Sciences & Green Asia Strategy
- Keywords: Al-Zn-Mg alloy; Stir casting; Wear rate; SEM image; Graphite; Microstructure
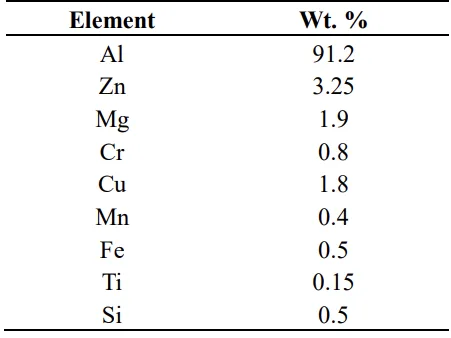
2. Abstracts or Introduction
This research paper investigates the fabrication of Al-Zn-Mg hybrid metal matrix composites using die casting technique to enhance mechanical and tribological properties for aerospace applications. The study focuses on varying graphite (Gr.) weight percentages (1%, 3%, 5%, and 7%) while maintaining a constant 2% silicon carbide (SiC) in the Al-Zn-Mg matrix. Test specimens were prepared according to ASTM standards for surface and wear studies. Wear rate analysis was conducted using pin-on-disc equipment under varying sliding distances and applied loads at a constant sliding velocity. Microstructure analysis and SEM imaging were employed to characterize the composite material and worn surfaces. The results indicate that increasing graphite content initially decreases wear rate, but wear rate increases with higher speed and load. Notably, the Al-Zn-Mg/2% SiC/7% Gr hybrid composite exhibited a 57.83% reduction in wear rate compared to the unreinforced Al-Zn-Mg alloy. SEM analysis of worn surfaces revealed features such as scratching, ploughing, delaminated layers, and plastic deformation.
3. Research Background:
Background of the Research Topic:
The selection of materials with specific properties is crucial in engineering design. Aluminum (Al) alloys are favored for automotive applications due to their superior physical and mechanical behavior, particularly in reducing adhesive wear. Metal Matrix Composites (MMCs) are engineered to control mechanical characteristics through structural reinforcement. Al 7075 alloy is commonly used in aerospace and automotive sectors due to its high toughness and tensile strength. Graphite is utilized as a solid lubricant for its chemical inertness, low friction, and film-forming capabilities. Adding graphite particles to aluminum-based composites can reduce wear rate. Hybrid composites, incorporating two or more types of metal particles as reinforcement in a matrix alloy, are increasingly important for applications like satellite bearings and laser reflectors due to their enhanced properties.
Status of Existing Research:
Fabrication methods for MMCs, such as powder metallurgy, squeeze casting, and stir casting, are well-established. Stir casting is particularly favored for its cost-effectiveness and operational simplicity. Various techniques, including squeeze casting, compo casting, spray deposition, and stir casting, are employed to produce MMCs. Friction Stir Processing (FSP) has shown improved wear results in aluminum alloys. Studies indicate that Boron Carbide (B4C) particles in AA2024 alloy enhance mechanical properties. MMCs generally offer improved mechanical properties over conventional materials, making them suitable for automotive and marine applications. Research has explored wear properties of Al7075 alloy reinforced with Al2O3/SiC using orthogonal arrays. Composite materials are created by incorporating whiskers, fibers, and metal particles to enhance conventional material properties. Efforts have been made to determine the properties of AW2024/B4C composites produced via stir casting.
Necessity of the Research:
Prior research has investigated the influence of process parameters on the tensile strength and hardness of composites, the effect of SiC particles on the tribological properties of Al7075 alloy, and the characteristics of nickel alloy-based hybrid composites. Experimental studies have also been conducted on carbon fiber reinforced composites and the tribological behavior of lubricant additives. Furthermore, the effect of carbon fiber content on Sisal/PMMA composites and the mechanical behavior of Al-Cu based hybrid composites produced by stir casting have been explored. Investigations into friction stir welding of nanoparticle-reinforced joints have focused on microstructural and macrostructural analysis. Considering the existing body of work, this research aims to contribute to the understanding of how reinforcements affect the surface examination and wear behavior of Al-Zn-Mg/SiC/Gr hybrid composites, utilizing die casting, a widely used industrial process.
4. Research Purpose and Research Questions:
Research Purpose:
The primary aim of this study is to investigate the effect of silicon carbide (SiC) and graphite (Gr.) reinforcements on the microstructure and wear characteristics of Al-Zn-Mg alloy hybrid composites fabricated through die casting. This research seeks to optimize the composition of these hybrid composites to enhance their wear resistance for potential aerospace applications.
Key Research:
- To fabricate Al-Zn-Mg hybrid composites with varying graphite percentages (1%, 3%, 5%, and 7%) and a constant silicon carbide percentage (2%) using die casting.
- To characterize the microstructure of the fabricated hybrid composites to assess the dispersion of reinforcement particles.
- To evaluate the wear rate of the hybrid composites under different loads and speeds using pin-on-disc wear testing equipment.
- To analyze the worn surfaces using SEM to identify wear mechanisms and correlate them with composite composition and testing conditions.
- To determine the optimal composition of Al-Zn-Mg/SiC/Gr hybrid composite that exhibits the lowest wear rate.
5. Research Methodology
Research Design:
This study employs an experimental research design focused on the fabrication and testing of Al-Zn-Mg hybrid composites. The research involves varying the weight percentage of graphite reinforcement while keeping silicon carbide constant, and then systematically evaluating the microstructure and wear properties of these composites.
Data Collection Method:
- Microstructural Analysis: Optical microscopy was used to examine the microstructure of the composites, assessing the dispersion of SiC and Graphite particles within the Al-Zn-Mg matrix.
- Wear Testing: Pin-on-disc wear tests were conducted according to ASTM G99-17 standards using NTS-POD-V01 equipment. Wear tests were performed under varying sliding distances (250, 500, 750, 1000, 1250, 1500 m) and applied loads (5, 10, 15, 20, 25, 30 N) at a constant sliding velocity of 1.5 m/sec. Volume loss technique was used to determine wear rate.
- Surface Analysis: Scanning Electron Microscopy (SEM) was used to analyze the worn surfaces of the composite specimens to identify wear mechanisms. Energy Dispersive X-ray Spectroscopy (EDX) was used to confirm the elemental composition of the Al-Zn-Mg alloy matrix.
Analysis Method:
- Quantitative Wear Rate Analysis: Wear rate was calculated using the volume loss technique, employing equations (1-3) as described in the paper, and plotted against varying loads and speeds to analyze trends.
- Qualitative Microstructural and Worn Surface Analysis: Micrographs from optical microscopy and SEM images were analyzed to assess reinforcement dispersion, matrix-reinforcement bonding, and wear mechanisms such as scratching, ploughing, delamination, and plastic deformation.
Research Subjects and Scope:
The research subjects were Al-Zn-Mg hybrid composites reinforced with silicon carbide (SiC) and graphite (Gr.). The matrix material was a hypo eutectic Al-Zn-Mg alloy ingot. The scope of the study was limited to investigating the effect of varying graphite content (1 wt.%, 3 wt.%, 5 wt.%, 7 wt.%) at a constant SiC content (2 wt.%) on the microstructure and wear properties of die-cast Al-Zn-Mg composites. The particle sizes of SiC and Gr. were 156µm and 165µm, respectively.
6. Main Research Results:
Key Research Results:
- Microstructure: Optical microscopy revealed good bonding between the Al-Zn-Mg matrix and the reinforcement materials (SiC and Graphite). Uniform dispersion of reinforcement particles was observed due to effective stirring during fabrication. Porosity was observed in the unreinforced Al-Zn-Mg alloy.
- Wear Rate: Wear rate increased with increasing applied load and sliding speed for all composite compositions. Increasing graphite content initially decreased wear rate, with the lowest wear rate observed for the Al-Zn-Mg/2% SiC/7% Gr hybrid composite.
- Wear Reduction: The Al-Zn-Mg/2% SiC/7% Gr hybrid composite exhibited a 57.83% reduction in wear rate compared to the unreinforced Al-Zn-Mg alloy.
- Worn Surface Morphology: SEM analysis of worn surfaces showed different wear mechanisms depending on composite composition and test conditions, including scratching, ploughing, delamination, plastic deformation, particle separation, grooves, and oxidation.
Analysis of presented data:
- Microstructure Analysis: The microstructure analysis confirmed successful incorporation and distribution of SiC and Graphite reinforcements within the Al-Zn-Mg matrix using stir casting within the die casting process. The reduction in porosity in hybrid composites compared to the base alloy suggests that the reinforcements may aid in degassing or modify solidification behavior.
- Wear Rate Analysis: The wear test results indicate that the addition of SiC and Graphite enhances wear resistance. The initial decrease in wear rate with increasing graphite content suggests the solid lubricant effect of graphite at lower concentrations. However, the increase in wear rate at higher speeds and loads is consistent with typical tribological behavior where increased contact pressure and temperature accelerate wear. The significant wear reduction in the 7% Graphite composite highlights the synergistic effect of SiC and Graphite in improving wear resistance.
- Worn Surface Analysis: SEM images provided visual evidence of the wear mechanisms at play. The presence of scratching and ploughing indicates abrasive wear, while delamination and plastic deformation suggest adhesive and fatigue wear contributions. The observation of oxidation on worn surfaces indicates tribo-oxidation processes occurring during wear testing.
Figure Name List:
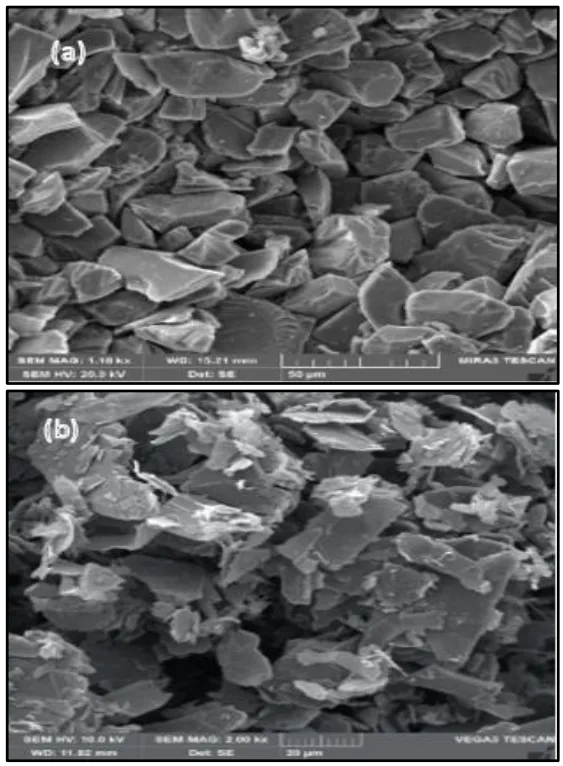
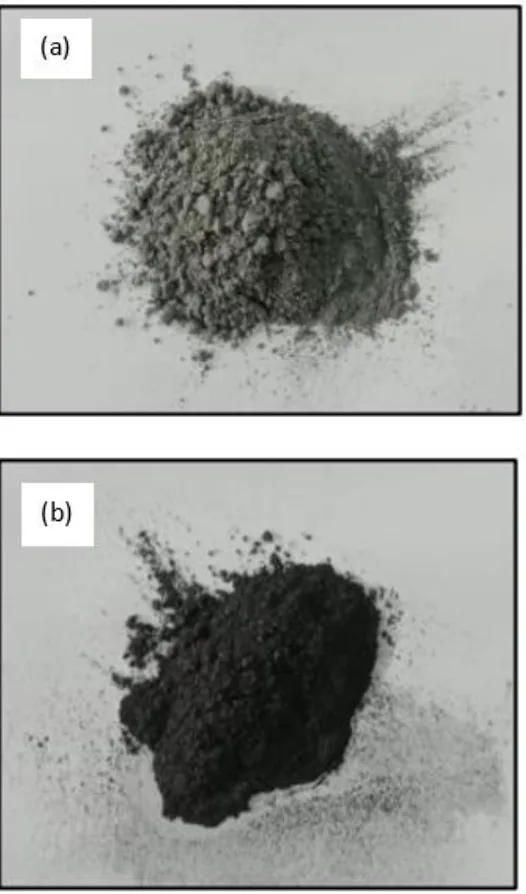
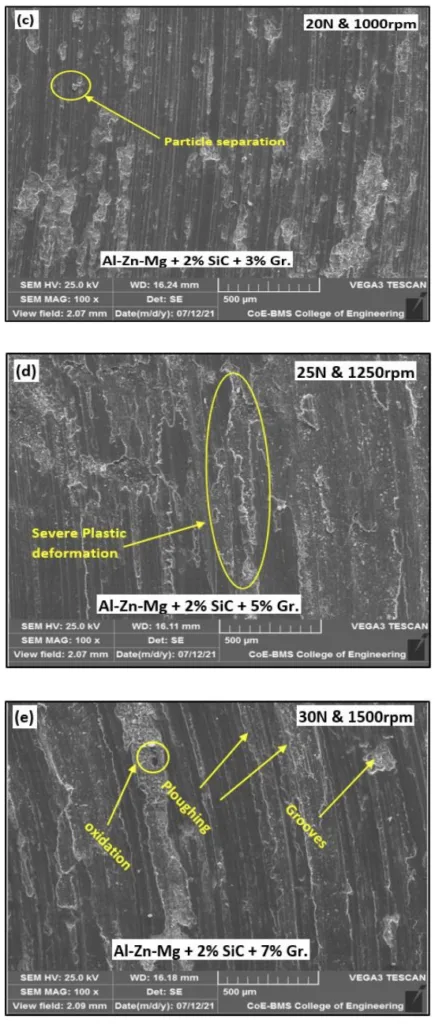
- Fig. 1: SEM images of (a) SiC and (b) Graphite particles.
- Fig. 2: Photograph of (a) SiC and (b) Graphite particles.
- Fig. 3: Photograph of (a) Microstructure specimen and (b) Wear specimen.
- Fig. 4: Photograph of (a) Microscope and (b) Wear testing machine.
- Fig. 5: Microstructure images for (a) Unreinforced Al-Zn-Mg matrix, (b) Al-Zn-Mg alloy/2 wt.% SiC/7 wt.% Gr. hybrid composite.
- Fig. 6: (a) Selected arear for EDX spectrum(b) SEM-EDX image of Al-Zn-Mg alloy
- Fig. 7: Wear rate of Al-Zn-Mg/SiC/Gr. hybrid composite for different load applied.
- Fig. 8: Wear rate of Al-Zn-Mg/SiC/Gr. hybrid composites for different speed applied.
- Fig. 9 (a-e): SEM photographs of worn-out surfaces for samples examined at v = 1.5m/sec
7. Conclusion:
Summary of Key Findings:
This study successfully fabricated Al-Zn-Mg/SiC/Gr hybrid composites using die casting. The incorporation of SiC and Graphite reinforcements improved the wear resistance of the Al-Zn-Mg alloy. The Al-Zn-Mg/2% SiC/7% Gr composite demonstrated the highest wear resistance, with a 57.83% reduction in wear rate compared to the unreinforced alloy. Wear rate increased with higher loads and speeds for all compositions. Microstructural analysis showed uniform reinforcement dispersion and good matrix-reinforcement bonding. SEM analysis of worn surfaces revealed wear mechanisms including scratching, ploughing, delamination, and oxidation.
Academic Significance of the Study:
This research contributes to the fundamental understanding of the tribological behavior of Al-Zn-Mg hybrid composites. It provides valuable insights into the synergistic effects of SiC and Graphite reinforcements in enhancing wear resistance. The study also demonstrates the effectiveness of die casting as a viable method for producing these advanced composite materials.
Practical Implications:
The findings of this study have practical implications for the aerospace and automotive industries, where lightweight, high-strength, and wear-resistant materials are highly desirable. The Al-Zn-Mg/2% SiC/7% Gr hybrid composite shows promise as a potential material for components requiring enhanced wear performance, such as bearings and sliding parts. The use of die casting for fabrication offers a cost-effective and scalable manufacturing route.
Limitations of the Study and Areas for Future Research:
This study is limited to a specific range of reinforcement compositions and testing conditions. Future research could explore:
- The effect of varying SiC content and particle size on wear properties.
- Optimization of die casting parameters to further improve composite properties.
- Investigation of other mechanical properties such as tensile strength, fatigue, and impact resistance.
- Performance evaluation of these composites in actual aerospace or automotive applications.
- Exploring the use of other solid lubricants in combination with SiC for enhanced tribological performance.
8. References:
- 1) Anil KC, Kumaraswamy, Mahadeva Reddy, Mamatha K M, "Air Jet Erosion studies on Aluminum -Red Mud Composites using Taguchi Design." EVERGREEN Joint Journal of Novel Carbon Resource Sciences & Green Asia Strategy, 10(1), 130-138, (2023). doi.org/10.5109/6781059
- 2) Kumaraswamy, J, Vijaya Kumar and Purushotham, G. "A review on mechanical and wear properties of ASTM a 494 M grade nickel-based alloy metal matrix composites", Materials Today: Proceedings, 37, pp 2027-2032. (2021) Doi: 10.1016/j.matpr.2020.07.499.
- 3) M. Sreenivasa Reddy, Dr. Soma V. Chetty and Dr. Sudheer Premkumar "Influence of reinforcements and heat treatment on Mechanical and Tribological properties of hybrid composite formed by Al 7075 reinforced with fly ash and EGlass short fibers" International Journal of Advanced Materials Science ISSN 2231-1211 Volume 3, Number 3, pp. 267-274, (2012).
- 4) J. Kumaraswamy et al., "Thermal Analysis of Ni-Cu Alloy Nanocomposites Processed by Sand Mold Casting," Advances in Materials Science and Engineering, vol. 2022, Article ID 2530707, 11 pages, 2022. DOI: 10.1155/2022/2530707
- 5) Jayappa, K., Kumar, V. and Purushotham, G. “Effect of reinforcements on mechanical properties of nickel alloy hybrid metal matrix composites processed by sand mold technique", Applied Science and Engineering Progress, 14(1), pp. 44–51. (2021). DOI: 10.14416/j.asep.2020.11.001.
- 6) Sharan kumar, Akash, Anil KC, Kumaraswamy J, "Solid Particle Erosion Performance of Multi-layered Carbide Coatings (WC-SiC-Cr3C2)" EVERGREEN Joint Journal of Novel Carbon Resource Sciences & Green Asia Strategy, Vol. 10(2) pp813-819 (2023). doi.org/10.5109/6792833.
- 7) Uvaraja VC and Natarajan N "Optimization of Friction and Wear Behaviour in Hybrid Metal Matrix Composites Using Taguchi Technique" Journal of Minerals and Materials Characterization and Engineering 11, pp. 757–68, (2012).
- 8) T Senthilvelan, S Gopalakannan, S Vishnuvarthan and K Keerthivaran "Fabrication and Characterization of SiC, Al2O3 and B4C Reinforced Al-Zn-Mg-Cu Alloy (AA 7075) Metal Matrix Composites: A Study” Advanced Materials Research Vols. 622-623, pp. 1295-1299, (2013).
- 9) A. Baradeswaran and A. Elaya Perumal “Influence of B4C on the tribological and mechanical properties of Al 7075-B4C composites" Composites: Part B, pp. 146-152, (2013).
- 10) A. Baradeswaran, S.C. Vettivel, A. Elaya Perumal, N. Selvakumar, R. Franklin Issac "Experimental investigation on mechanical behaviour, modelling and optimization of wear parameters of B4C and graphite reinforced aluminium hybrid composites" Materials and Design, 63, pp. 620-632, (2014).
- 11) M. Sreenivasa Reddy, Dr. Soma V Chetty, Dr. Sudheer Premkumar and Reddappa H N, "Influence of reinforcements and heat treatment on mechanical and wear properties of Al7075 based hybrid composites" Procedia Materials Science 5, pp. 508 – 516, (2014).
- 12) P. Subramanya Reddy, R. Kesavan, B. Vijaya Ramnath "Investigation of Mechanical Properties of Aluminium 6061-Silicon Carbide, Boron Carbide Metal Matrix Composite", Silicon, (2018).
- 13) M. Kumar, G. Balaji & A. Megalingam Murugan "Experimental Investigations on Friction and Wear Behavior and Parameters Optimization of A17075-T6 Alloy and Al7075/Alumina/ Graphite/ Redmud Hybrid Metal Matrix Composite" Using Grey Relational Analysis" International Journal of Mechanical and Production Engineering Research and Development (IJMPERD) ISSN (P): 2249-6890; ISSN (E): 2249-8001 Vol. 8, Special Issue 7, pp. 1104-1118, (2018).
- 14) Balasubramani Subramaniam, Balaji Natarajan, Balasubramanian Kaliyaperumal, and Samson Jerold Samuel Chelladurai, “Investigation on mechanical properties of aluminium 7075 boron carbide – coconut shell fly ash reinforced hybrid metal matrix composites" Overseas Foundry Vol. 15, No 6, pp. 449-456, (2018).
- 15) Thella Babu Rao “An experimental investigation on mechanical and wear properties of Al7075/SiCp composites: effect of SiC content and particle size" Journal of Tribology ASME, (2017).
- 16) L. Natrayan and M. Senthil Kumar “Optimization of wear behaviour on AA6061/Al2O3/SiC metal matrix composite using squeeze casting technique – Statistical analysis, Materials Today: Proceedings, pp. 1-5, (2017).
- 17) Abhijit Bhowmik, Dipankar Dey & Ajay Biswas "Comparative Study of Microstructure, Physical and Mechanical Characterization of SiC/TiB2 Reinforced Aluminium Matrix Composite", Silicon, (2020).
- 18) J. Kumaraswamy, Anil KC, Mahadeva Reddy, "Influence of Particulates on Microstructure, Mechanical and Fractured Behaviour on Al-7075 Alloy composite by FEA", Australian Journal of Mechanical Engineering, 2023
- 19) Girish G. and Anandakrishnan V, "Tribological behaviour of recursive friction stir processed AA7075, Industrial Lubrication and Tribology, ISSN 0036-8792, (2020).
- 20) L. Bharath and Suneelkumar N. Kulkarni, "Evaluation of UTS and compression strength of Al2024/B4C composites by experimental method and validation through regression analysis", Materials Today: Proceedings, (2021).
- 21) J. Kumaraswamy, V. Kumar and G. Purushotham, "Thermal analysis of nickel alloy/Al2O3/TiO2 hybrid metal matrix composite in automotive engine exhaust valve using FEA method", Journal of Thermal Engineering, Vol. 7, No. 3, March, 2021, pp. 415-428. https://dx.doi.org/10.18186/thermal.882965.
- 22) L. Bharath, M. Sreenivasa Reddy, H.N. Girisha, G. Balakumar, "Influence of process parameters on tensile strength and hardness of AW2024/B4C composite using Taguchi's technique" Materials Today: Proceedings, (2021).
- 23) Mulugundam Siva Surya and G. Prasanthi, "Effect of SiC Weight Percentage on Tribological Characteristics of Al7075/SiC Composites", silicon, springer, (2021).
- 24) Muhammad Miqdad, Anne Zulfia Syahrial, "Effect of Nano Al2O3 Addition and T6 Heat Treatment on Characteristics of AA 7075 / Al2O3 Composite Fabricated by Squeeze Casting Method for Ballistic Application" EVERGREEN Joint Journal of Novel Carbon Resource Sciences & Green Asia Strategy, Vol. 9(2) pp531-537 (2022). doi.org/10.5109/4794184.
- 25) J. Kumaraswamy, Vijaya Kumar & G. Purushotham "Evaluation of the microstructure and thermal properties of (ASTM A 494 M grade) nickel alloy hybrid metal matrix composites processed by sand mold casting", International Journal of Ambient Energy, 43 (1), 4899-4908.
- 26) J Kumaraswamy, Anil K. C., Vidyasagar Shetty & C Shashishekar, “Wear behaviour of the Ni-Cu alloy hybrid composites processed by sand mould casting" Advances in Materials and Processing Technologies, Vol. 9, No. 2, pp. 351–367, (2023).
- 27) Harish R S, Sreenivasa Reddy M, Kumaraswamy J "Wear Characterization of Al 7075 Alloy Hybrid Composites", Metallurgical and Materials Engineering, Vol 28 (2), pp. 291-303, (2022).
- 28) Kumaraswamy Jayappa, Kyathasandra Chikkanna Anil and Zulfiqar A. Khan, "Enhancing wear resistance in Al-7075 composites through conventional mixing and casting techniques”, Journal of Materials Research and Technology, (2023).
- 29) Kumaraswamy, J., Anil, K.C., Canbay, C.A., N D Shiva Kumar. Electro-Whirling Stir Casting: a Novel Approach for Fabricating Al7075/SiC MMCs with Enhanced Thermal Characteristics. Silicon (2023). https://doi.org/10.1007/s12633-023-02678-y
- 30) J. Kumaraswamy, Anil KC, TR Veena, G. Purushotham, Sunil Kumar K, "Investigating the Mechanical Properties of Al 7075 Alloy for Automotive Applications: Synthesis and Analysis" in Scopus indexed EVERGREEN Joint Journal of Novel Carbon Resource Sciences & Green Asia Strategy, Vol. 10(3), pp.1286-1295, (2023). doi:10.5109/7151674
- 31) Mr. Dilip Choudhari, Dr. Vyasraj Kakhandki, "Characterization and Analysis of Mechanical Properties of Short Carbon Fiber Reinforced Polyamide66 Composites" EVERGREEN Joint Journal of Novel Carbon Resource Sciences & Green Asia Strategy, Vol. 8(4), pp768-776, (2021). doi.org/10.5109/4742120.
- 32) Anthony Chukwunonso Opia, Mohd Kamei Abdul Hamid, Samion, Syahrullail, Charles A. N. Johnson, Abu Bakar Rahim, Mohammed B. Abdulrahman, "Nano-Particles Additives as a Promising Trend in Tribology: A Review on their Fundamentals and Mechanisms on Friction and Wear Reduction" EVERGREEN Joint Journal of Novel Carbon Resource Sciences & Green Asia Strategy, Vol. 8(4), pp777-798, (2021). doi.org/10.5109/4742121.
- 33) Anthony Chukwunonso Opial, Mohd Kameil Abdul Hamid, Samion Syahrullail, Audu Ibrahim Ali, Charles N. Johnson, Ibham Veza, Mazali Izhari Izmi, Che Daud Zul Hilmi, Abu Bakar Abd Rahim, "Tribological Behavior of Organic Anti-Wear and Friction Reducing Additive of ZDDP under Sliding Condition: Synergism and Antagonism Effect" EVERGREEN Joint Journal of Novel Carbon Resource Sciences & Green Asia Strategy, Vol. 9(2) pp246-253 (2022). doi.org/10.5109/4793628.
- 34) H. Sosiati, N.D.M. Yuniar, D. Saputra, and S. Hamdan, "The Influence of Carbon Fiber Content on the Tensile, Flexural, and Thermal Properties of the Sisal/PMMA Composites" EVERGREEN Joint Journal of Novel Carbon Resource Sciences & Green Asia Strategy, Vol. 9(1) pp.32-40 (2022). doi.org/10.5109/4774214.
- 35) Anil, K.C., Kumarswamy, J., Reddy, M., Prakash, B., "Mechanical Behaviour and Fractured Surface Analysis of Bauxite Residue & Graphite Reinforced Aluminium Hybrid Composites", Frattura ed Integrità Strutturale, 16 (62) (2022) 168-179. DOI: 10.3221/IGF-ESIS.62.12
- 36) L. Bharath, J. Kumaraswamy, T. V. Manjunath and Suneel Kumar N. Kulkarni "Evaluation of microstructure and prediction of hardness of Al-Cu based composites by using artificial neural network and linear regression through machine learning technique" SPRINGER Multiscale and Multidisciplinary Modeling, Experiments and Design,
- 37) Tanvir Singh "Comparative Analysis of Microstructural and Mechanical Characteristics of Reinforced FSW Welds" book editor, (2024) DOI: 10.1002/9781394169467.ch12.
- 38) Tanvir Singh "Nanoparticles reinforced joints produced using friction stir welding: a review" Engineering Research Express, 5, 022001, (2023) DOI: 10.1088/2631-8695/accb28.
- 39) Tanvir Singh, S. K. Tiwari and D. K. Shukla, "Effects of Al2O3 nanoparticles volume fractions on microstructural and mechanical characteristics of friction stir welded nanocomposites" 6, (2020), pp. 76-84, DOI: 0.1080/20550324.2020.1776504.
- 40) Tanvir Singh, S. K. Tiwari and D. K. Shukla, "Influence of Nanoparticle Addition (TiO2) on Microstructural Evolution and Mechanical Properties of Friction Stir Welded AA6061-T6 Joints" (2020), pp. 219-228, DOI: 10.1007/978-981-15-5519-0_18.
- 41) Tanvir Singh, S. K. Tiwari and D. K. Shukla, "Effect of nano-sized particles on grain structure and mechanical behavior of friction stir welded Al- nanocomposites" 234, Issue 2, (2019), DOI: 10.1177/1464420719885.
- 42) Tanvir Singh, S. K. Tiwari and D. K. Shukla, Production of AA6061-T6/Al2O3 reinforced nanocomposite using friction stir welding” 1, 025052, (2019), DOI: 10.1088/2631-8695/ab5e27.
- 43) Tanvir Singh, S. K. Tiwari and D. K. Shukla, "Friction-stir welding of AA6061-T6: The effects of Al2O3 nano-particles addition" 1, 100005, (2019), DOI: 10.1016/j.rinma.2019.100005.
- 44) Antony, A. Godwin, V. Vijayan, S. Saravanan, Saravanan Baskar, and Marappan Loganathan. "Analysis of wear behaviour of aluminium composite with silicon carbide and titanium reinforcement." Int. J. Mech. Eng. Technol. 9 (2018), pp. 681-691.
- 45) Karikalan, L., Μ. Chandrasekran, S. Ramasubramanian, and S. Baskar. "Hybridization of composites using natural and synthetic fibers for automotive application." International Journal of Scientific Research in Science and Technology 7 (2017), pp. 916-920.
- 46) Santhanam, V., R. Dhanaraj, M. Chandrasekaran, N. Venkateshwaran, and S. Baskar. "Experimental investigation on the mechanical properties of woven hybrid fiber reinforced epoxy composite." Materials Today: Proceedings 37 (2021), pp. 1850-1853.
9. Copyright:
- This material is "L Bharath, J Kumaraswamy, T V Manjunatha, Suchendra K R"'s paper: Based on "Investigation on Microstructure and Wear Study on Al-Zn-Mg Alloy Hybrid Composites Fabricated Through Die Casting Process".
- Paper Source: https://doi.org/10.5109/6930677
This material was created to introduce the above paper, and unauthorized use for commercial purposes is prohibited.
Copyright © 2025 CASTMAN. All rights reserved.