This introduction paper is based on the paper "Interface microstructure and evolution mechanism of wire arc additively manufactured H13 steel-copper hybrid components" published by "Journal of Materials Research and Technology".
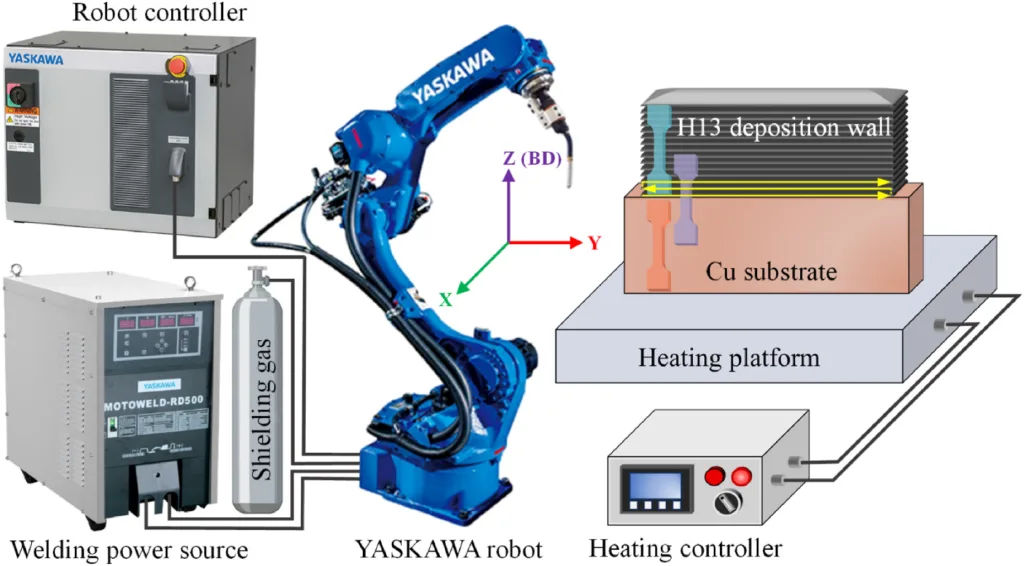
1. Overview:
- Title: Interface microstructure and evolution mechanism of wire arc additively manufactured H13 steel-copper hybrid components
- Author: Xinwei Du, Yanhong Wei, Kai Guo, Jinwei Long, Xiangbo Liu, Wenyong Zhao, Renpei Liu
- Year of publication: 2025
- Journal/academic society of publication: Journal of Materials Research and Technology
- Keywords: Wire arc additive manufacturing, Copper-steel hybrid structure, Bimetal, Interfacial behavior, Liquid phase separation
2. Abstract:
The H13 steel-copper hybrid structure fabricated by additive manufacturing (AM) can achieve enhanced cooling of the system while ensuring certain high-temperature mechanical properties, showing broad application prospects in high-pressure die-casting molds. In this work, H13 steel was directly deposited onto a copper substrate by wire arc additive manufacturing, and the interface microstructure was studied in detail. The formation and evolution mechanism of the interface structure was revealed in combination with temperature field simulation. The Fe-Cu mixed liquid at the interface underwent two liquid phase separations, forming Fe-rich islands and Cu-rich islands, as well as dispersed Cu-rich particles. A small number of pores was formed due to the volume shrinkage of Cu during cooling. Microcracks were attributed to the effect of thermal stress and the high crack sensitivity caused by the distribution of Cu-rich particles at the original austenite grain boundaries. Due to the sharp changes in the element distribution at the H13-Cu interface and the continuous change in the temperature distribution, an extended molten pool with a temperature lower than the melting point of H13 and higher than the melting point of Cu was formed below the interface. The microhardness decreases gradually from the H13 side to the Cu side in a narrow range (~0.5 mm) near the interface. The tensile sample of the hybrid component fractured on the Cu side away from the interface, and its tensile strength (221 ± 2 MPa) reached the level of the Cu substrate, indicating that the interface formed a good bond.
3. Introduction:
Multi-material hybrid components, particularly copper-steel bimetallic structures, offer a combination of high thermal/electrical conductivity (from copper) and good mechanical properties (from steel), making them suitable for demanding applications like aerospace, nuclear industry, molds, and automotive parts. Traditional manufacturing methods like welding or diffusion bonding have limitations in geometric design flexibility. Additive manufacturing (AM) provides near-net-shaping capabilities, enhancing design freedom for such hybrid components. However, AM of copper-steel structures faces challenges due to significant differences in thermophysical and mechanical properties. The Fe-Cu phase diagram indicates very limited solid solubility and no intermetallic compounds, leading to liquid phase separation during solidification, potentially forming detrimental Cu-rich and Fe-rich islands at the interface. Furthermore, the high thermal conductivity of copper causes rapid heat dissipation, making it difficult to achieve stable melting, especially when copper is the substrate. The mismatch in thermal expansion coefficients can also induce high residual stresses and cracking at the interface.
4. Summary of the study:
Background of the research topic:
H13-Cu bimetallic structures are of interest, particularly for high-pressure die casting (HPDC) molds, as they combine the high-temperature mechanical properties and thermal fatigue resistance of H13 steel with the high thermal conductivity of copper, potentially enhancing mold cooling capacity and efficiency. Fabricating these structures via AM, specifically depositing H13 steel onto a copper substrate, presents challenges due to the materials' property mismatches.
Status of previous research:
Previous research on AM of copper-steel hybrids has explored various strategies, including optimizing process parameters, using specific scanning strategies (e.g., island scanning) to reduce defects, employing beam shaping (ring-mode laser) to minimize mixing, and post-processing like hot isostatic pressing (HIP) to eliminate pores and cracks. Adding transition layers, often Ni-based alloys like Inconel 718 or Deloro 22, has been shown to effectively reduce interface defects and improve bonding strength by mitigating the sharp property transition. Most studies focused on depositing copper onto steel substrates. Research involving depositing steel onto copper substrates, especially using Wire Arc Additive Manufacturing (WAAM), is limited. WAAM offers higher deposition rates and lower costs compared to laser-based AM and avoids issues with high laser reflectivity from copper. However, preliminary work indicated difficulty in melting the Cu substrate using conventional WAAM parameters due to its high thermal conductivity. There were no known reports on producing H13-Cu hybrid components by directly depositing H13 on Cu using WAAM.
Purpose of the study:
The study aimed to evaluate the feasibility of directly depositing H13 steel onto a copper substrate using WAAM. The specific objectives were to:
- Successfully manufacture an H13-Cu hybrid component via WAAM using tailored deposition strategies.
- Investigate the microstructure of the H13-Cu interface in detail.
- Reveal the formation and evolution mechanism of the interface structure, aided by temperature field simulation.
- Identify and analyze defects (pores, microcracks) near the interface and understand their formation mechanisms.
- Evaluate the mechanical properties (microhardness, tensile strength) of the resulting H13-Cu hybrid component.
Core study:
The core of the study involved the direct deposition of H13 steel wire onto an annealed copper substrate using GMAW-based WAAM. Special strategies were employed: preheating the Cu substrate (200 °C), using higher heat input (higher current, lower speed) for the initial layers close to the substrate, and implementing an oscillating deposition strategy. The resulting interface microstructure was characterized using SEM, EDS, EBSD, and TEM. A finite element model was developed to simulate the temperature distribution and thermal history during deposition, helping to explain the observed microstructural features and interface evolution. Defects like pores and microcracks were analyzed, and their causes were discussed based on microstructural observations and thermal analysis. Finally, microhardness profiles across the interface and tensile properties of the hybrid component were measured.
5. Research Methodology
Research Design:
The study employed an experimental approach combined with numerical modeling. H13 steel was additively manufactured onto a copper substrate using WAAM. The process parameters were specifically adapted to manage the high thermal conductivity of the copper substrate. The resulting bimetallic component's interface was then subjected to detailed microstructural analysis and mechanical property testing. Finite element simulation was used to model the thermal aspects of the deposition process to aid in understanding the interface formation mechanisms.
Data Collection and Analysis Methods:
- Materials: H13 steel wire (1.6 mm diameter) and an annealed copper substrate (200 × 50 × 15 mm³). Chemical compositions are detailed in Table 1 (Cu substrate) and Table 2 (H13 wire).
- Manufacturing Process: GMAW-based WAAM system (YASKAWA robot and power source). A reciprocating deposition path was used. Strategies included preheating the Cu substrate to 200 °C, using adjusted parameters (Current, Voltage, Wire feed speed, Travel speed) for the first 7 layers, and employing an oscillation strategy (2 mm amplitude, 1 Hz frequency). Detailed parameters are listed in Table 3.
- Microstructural Characterization: Samples were sectioned using wire EDM. Standard metallographic preparation (grinding, polishing, etching with 70% ethanol, 25% HCl, 5% FeCl3) was performed. Analysis techniques included Scanning Electron Microscopy (SEM) with Energy Dispersive Spectrometry (EDS), Electron Backscatter Diffraction (EBSD) after ion beam etching, X-ray Diffraction (XRD), and Transmission Electron Microscopy (TEM) on samples prepared by twin-jet polishing (12.5 vol% perchloric acid ethanol solution).
- Numerical Modeling: A finite element model was created to simulate the temperature field during deposition using the birth-death element technique. Temperature-dependent thermophysical and mechanical properties for H13 and Cu (Fig. 3(e-h)) were used. The model employed a 3D transient heat conduction equation (Eq. (1)) and a double ellipsoid heat source model (Fig. 3(i), Eqs. (4)-(7)) considering heat loss via convection and radiation (Eqs. (2)-(3)). The model was verified against the actual deposition morphology (Fig. 3(j)).
- Mechanical Testing: Tensile tests were conducted at room temperature using a universal testing machine (loading speed 1 mm/min) on samples extracted from H13 deposit, Cu substrate, and the H13-Cu hybrid region (sample dimensions in Fig. 2). Microhardness was measured using a Vickers tester (500 g load, 10 s dwell time) with a 0.2 mm step size across the interface along the building direction (BD).
Research Topics and Scope:
The research focused specifically on the interface region formed between WAAM-deposited H13 steel and a copper substrate. The scope included:
- Characterization of the interface macrostructure and microstructure (phases, grain morphology, precipitates).
- Investigation of elemental distribution and diffusion across the interface.
- Analysis of defect formation (pores, microcracks) mechanisms near the interface.
- Simulation of the thermal field and molten pool behavior during the deposition of initial layers.
- Elucidation of the interface evolution mechanism based on experimental and simulation results.
- Evaluation of local mechanical properties (microhardness gradient) across the interface and overall tensile behavior of the hybrid component.
6. Key Results:
Key Results:
- A H13-Cu hybrid component was successfully fabricated by directly depositing H13 steel on a Cu substrate using WAAM with tailored strategies (preheating, adjusted initial parameters, oscillation).
- The H13-Cu interface exhibited a wavy morphology, located approximately 1.5 mm below the original top surface of the Cu (OTSC), indicating substantial melting and mixing of the Cu substrate.
- Microstructurally, the Cu side near the interface showed coarse columnar grains (~750 µm wide) growing epitaxially, transitioning to finer equiaxed grains further away. The H13 side consisted of a martensitic (α-Fe) matrix with fine, dispersed Cu-rich precipitates.
- Liquid phase separation occurred at the interface due to the Fe-Cu miscibility gap, forming Fe-rich and Cu-rich islands/phases. Secondary liquid phase separation was observed within Fe-rich phases. Multi-scale Cu-rich particles (micron-sized and nano-sized) were found on the H13 side. TEM analysis confirmed the nanoscale (~17.9 nm) Cu-rich particles were FCC structure, semi-coherent with the α-Fe matrix.
- Defects were observed: irregular pores were found within large Cu-rich islands, attributed to volume shrinkage of Cu during solidification. Microcracks were concentrated on the H13 side, ~800-1200 µm from the interface (near the bottom of the second layer's melt pool), propagating along prior austenite grain boundaries (PAGBs). Crack formation was attributed to the reheating effect during subsequent layer deposition, which remelted low-melting-point Cu-rich phases segregated at PAGBs, increasing crack sensitivity under thermal stress (copper contamination cracking mechanism).
- Elemental diffusion across the interface was very limited, with a sharp transition (~1.5 µm width) observed via EDS line scan.
- Temperature field simulation supported the experimental findings, showing significant melting of the Cu substrate. It revealed the formation of an "extended molten pool" (liquid Cu below the H13 melting point but above the Cu melting point) beneath the H13 molten pool due to the melting point difference and continuous temperature gradient. This explained the formation of the Cu columnar zone and provided a mechanism for the observed exfoliation of solid/semi-solid Fe-rich phases into the liquid Cu.
- Microhardness showed a gradual transition across a narrow zone (TZ, ~0.5-0.6 mm wide, mainly within the Cu columnar zone) from ~68 HV (Cu substrate) to ~568 HV (H13 deposit). Hardness decreased slightly in the first H13 layer potentially due to larger Cu-rich particles.
- Tensile testing showed that the hybrid sample fractured on the Cu side, away from the interface, with significant necking. The ultimate tensile strength (UTS) of the hybrid component (221 ± 2 MPa) was comparable to that of the Cu substrate (214 ± 4 MPa), indicating good metallurgical bonding at the H13-Cu interface.
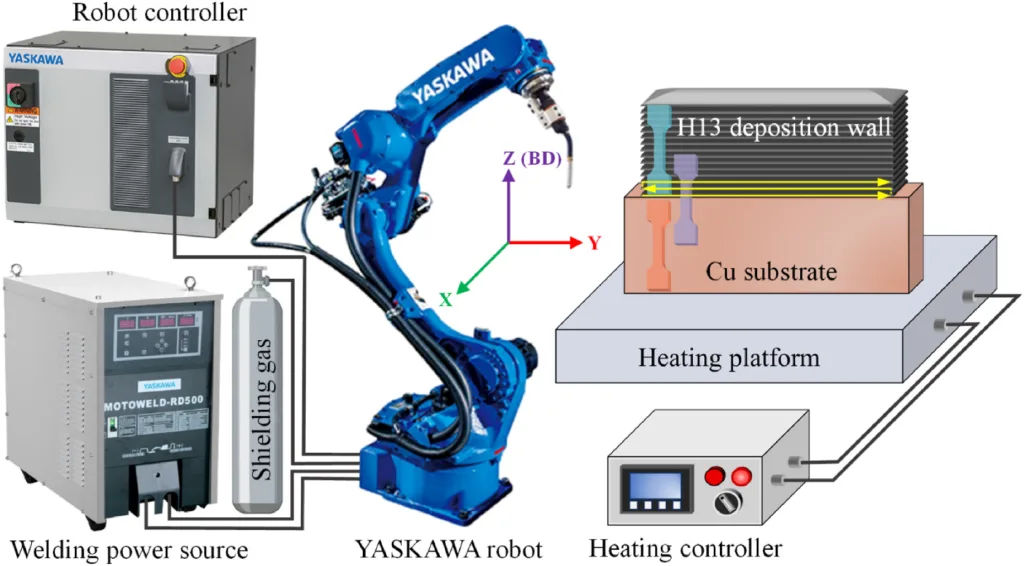
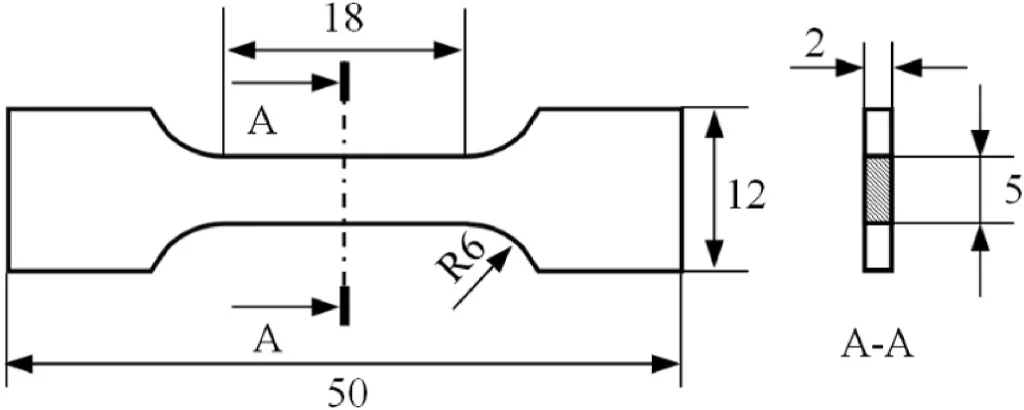
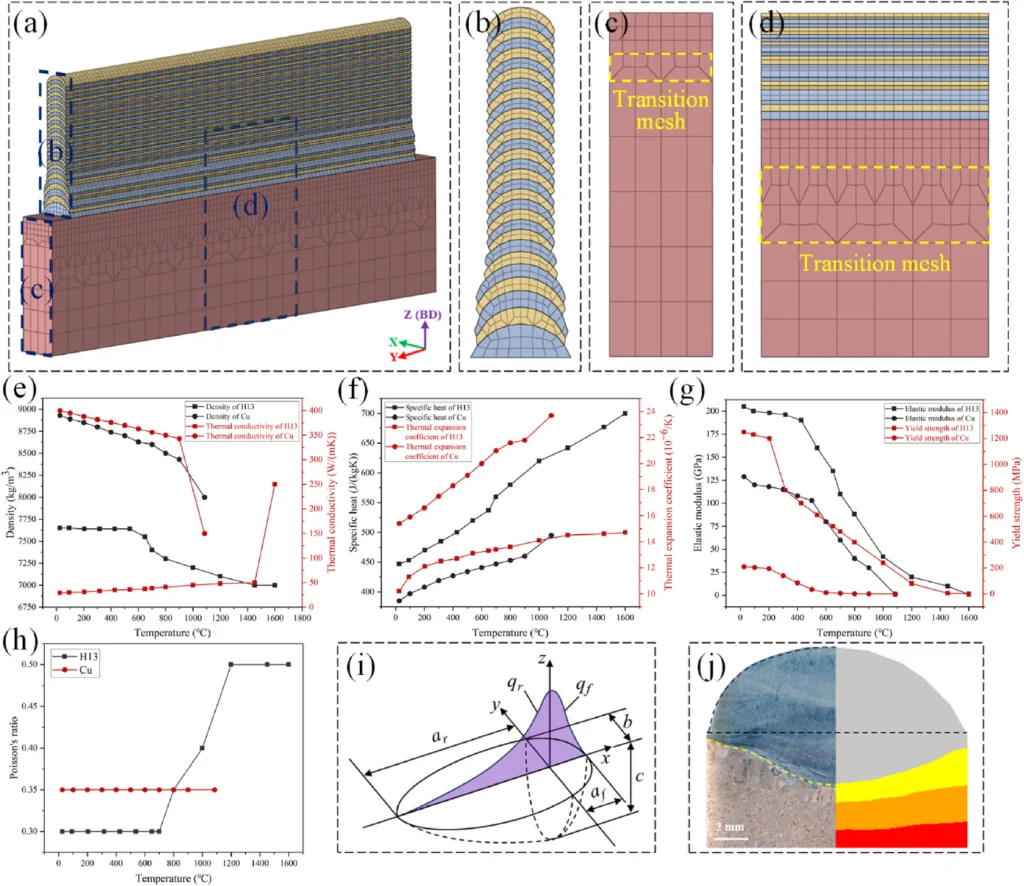
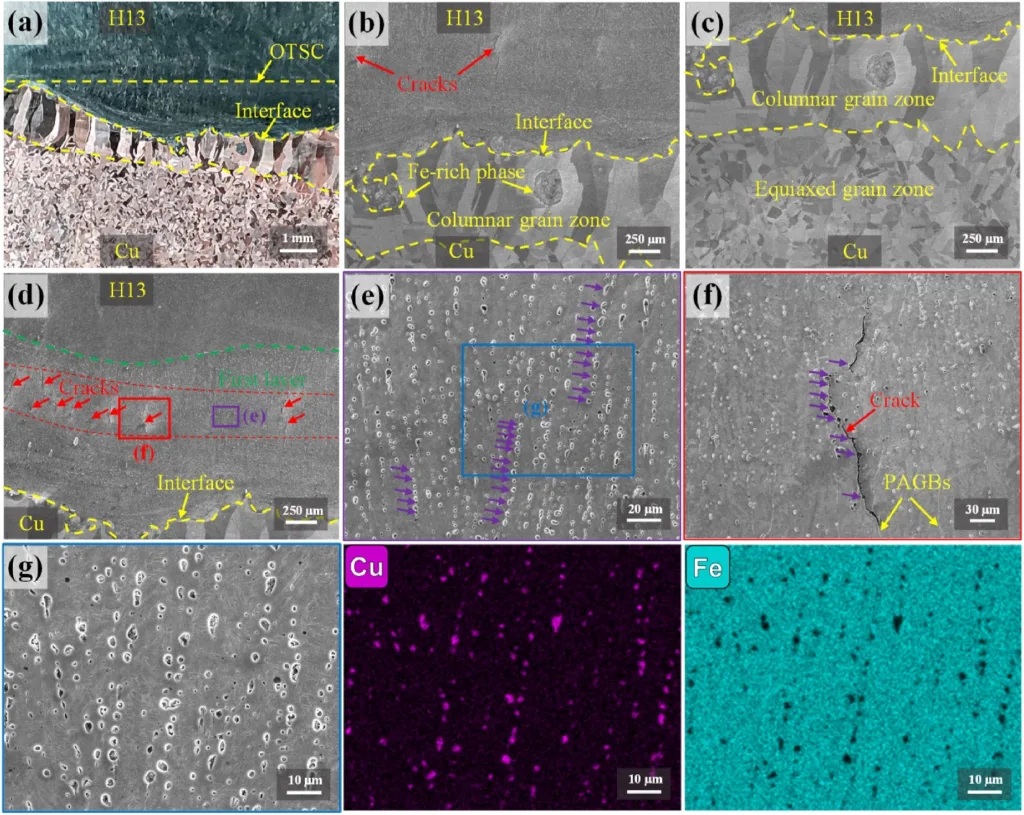
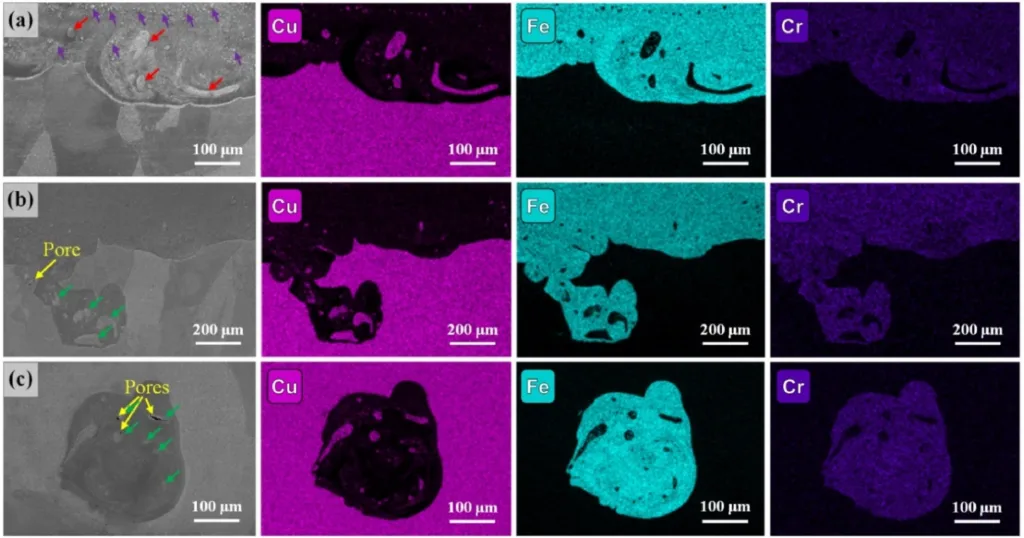
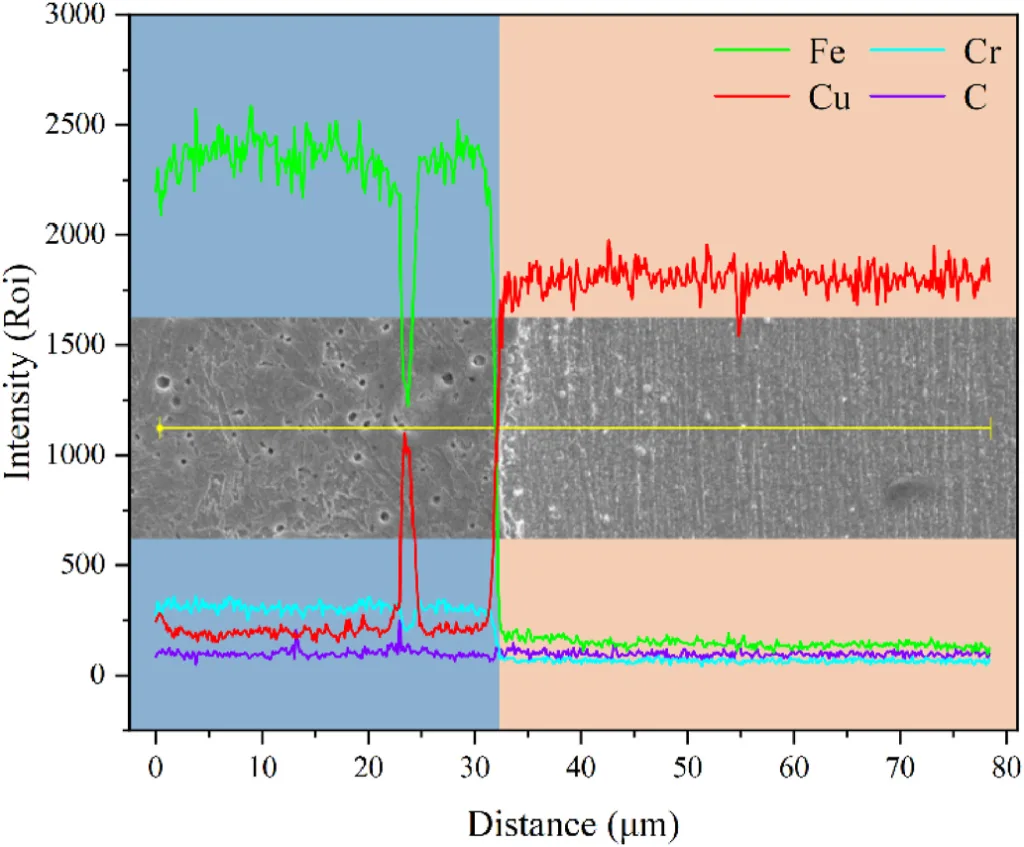
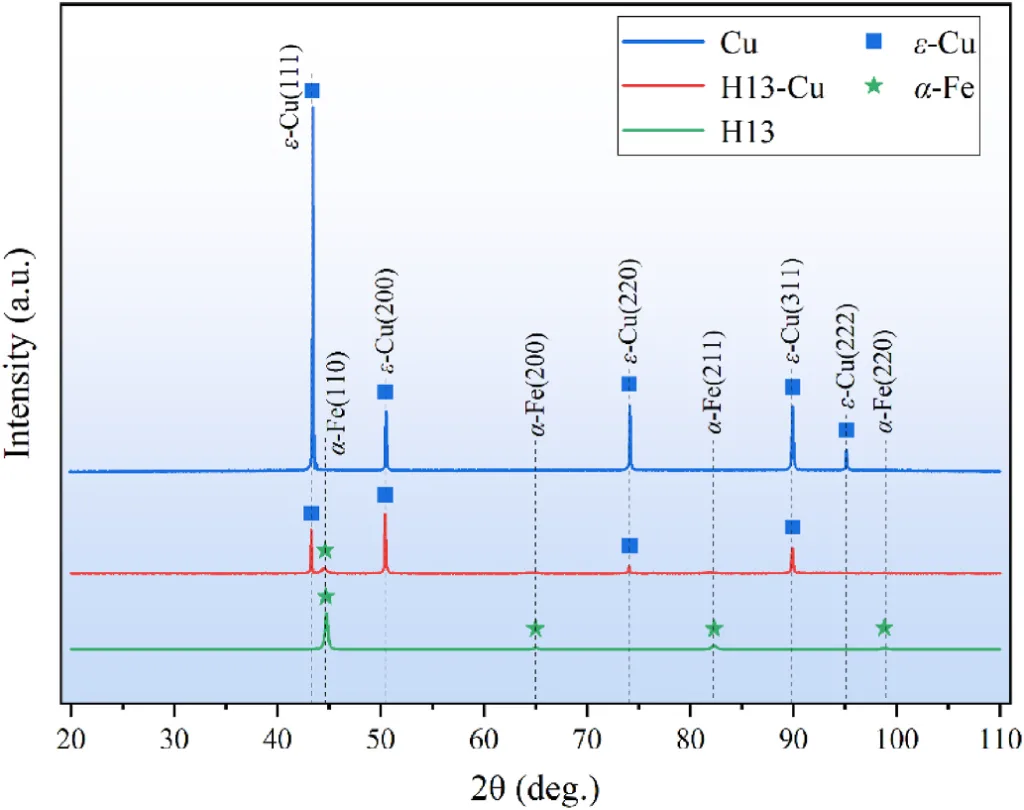
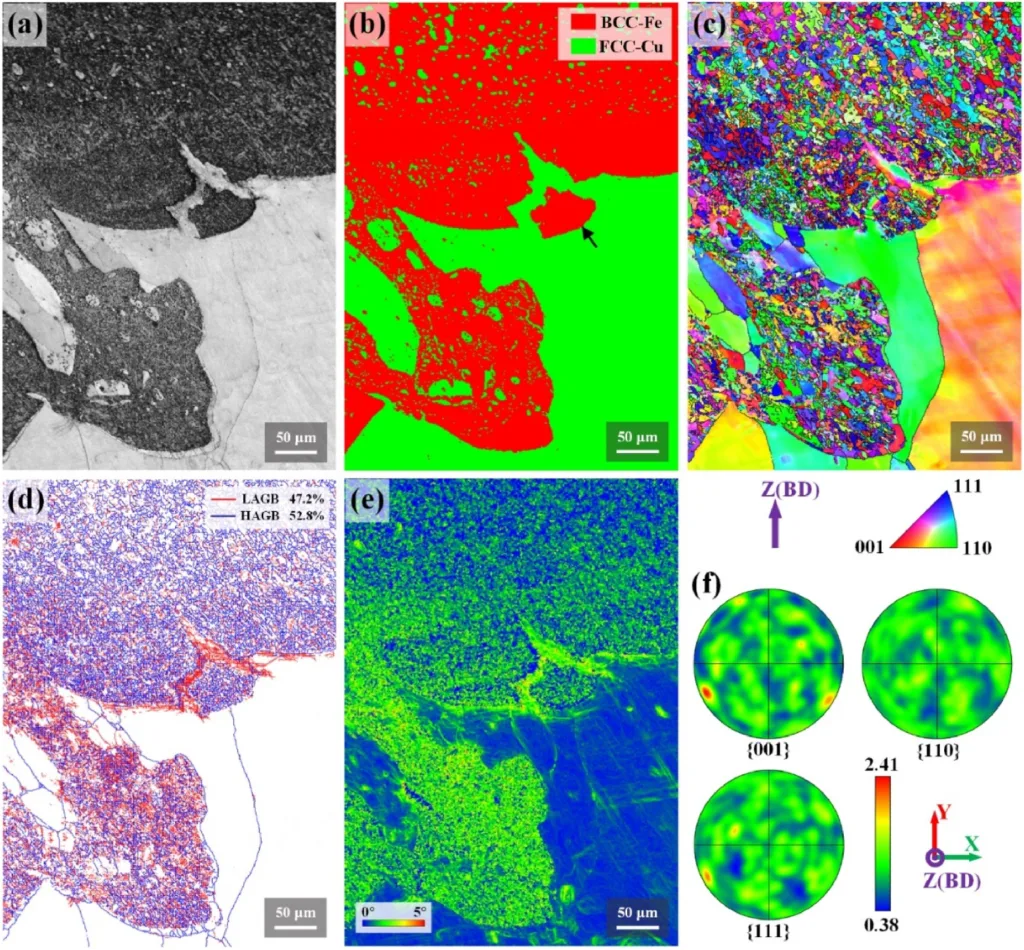
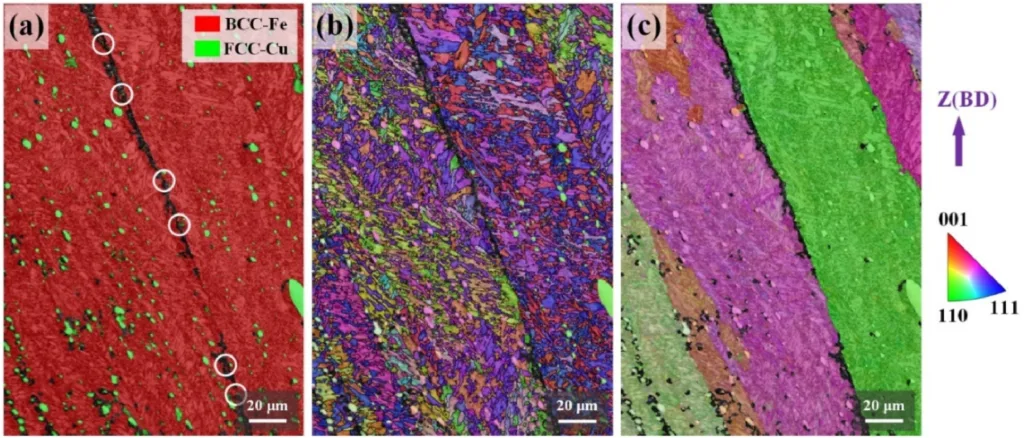
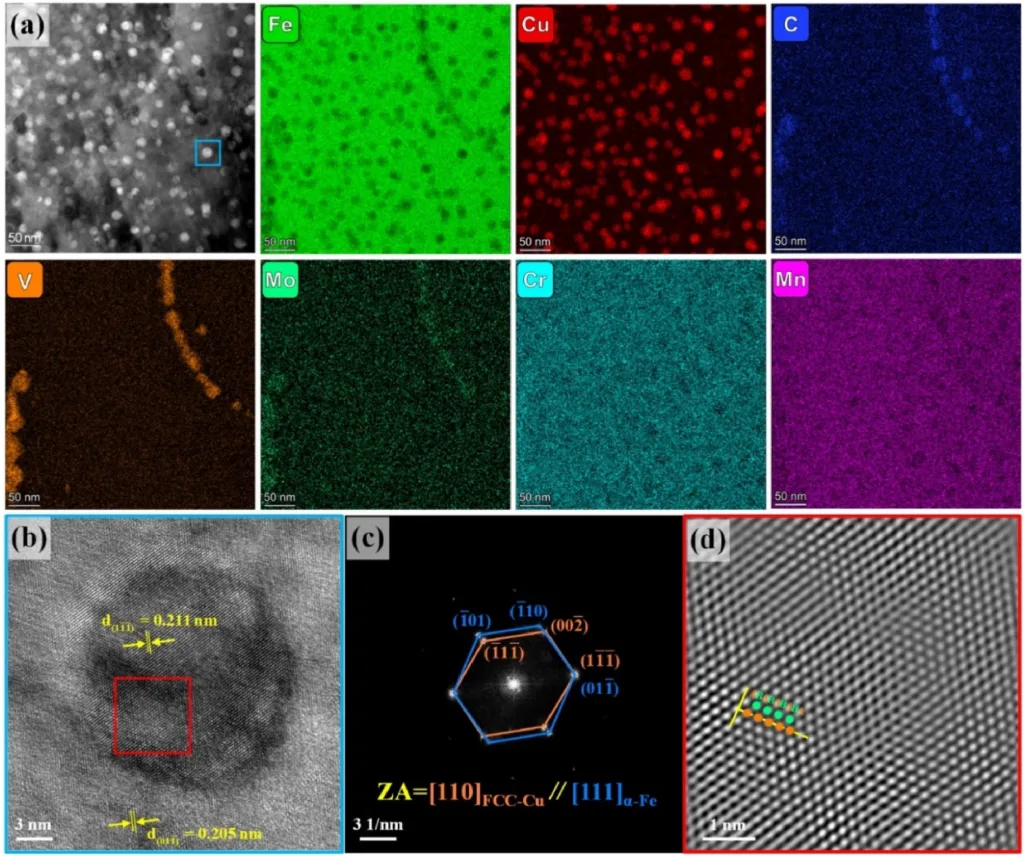
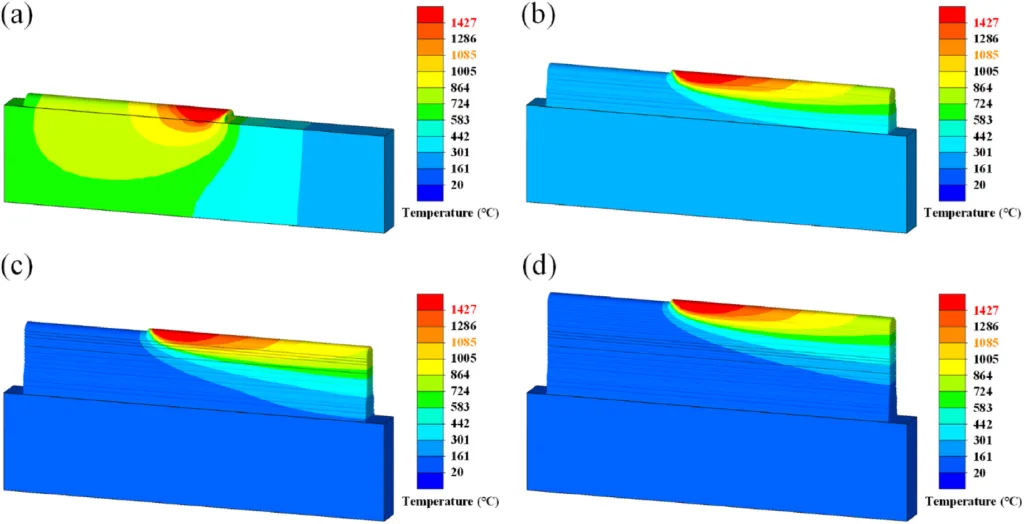
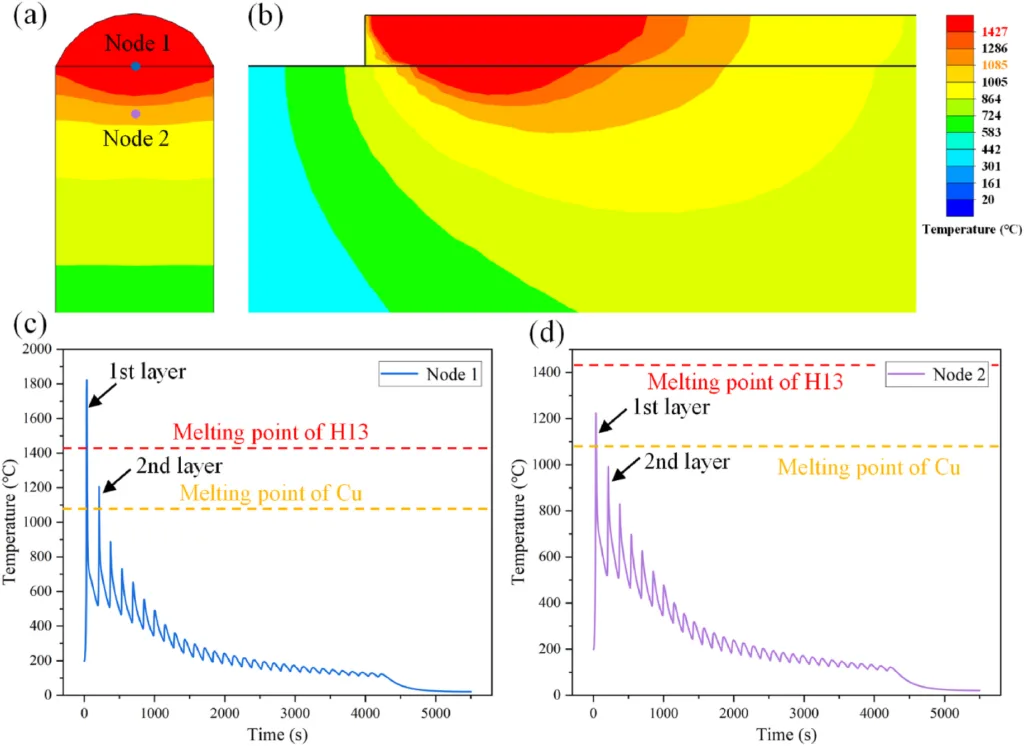
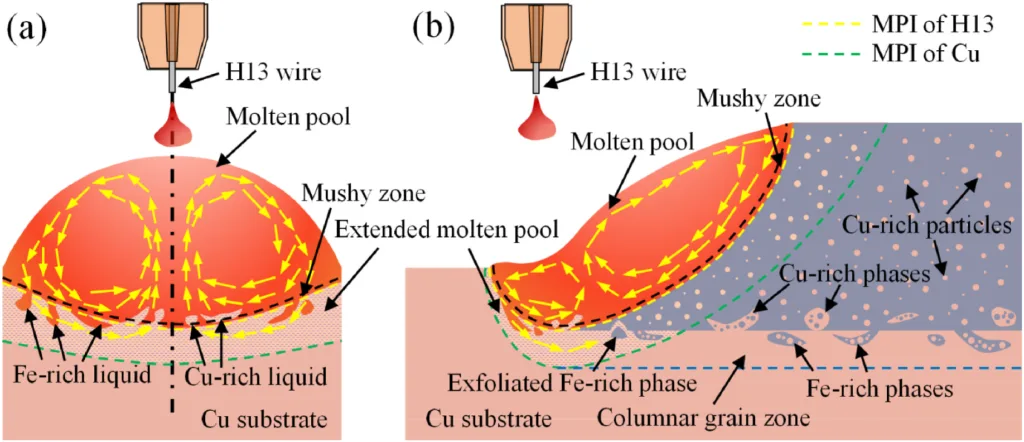
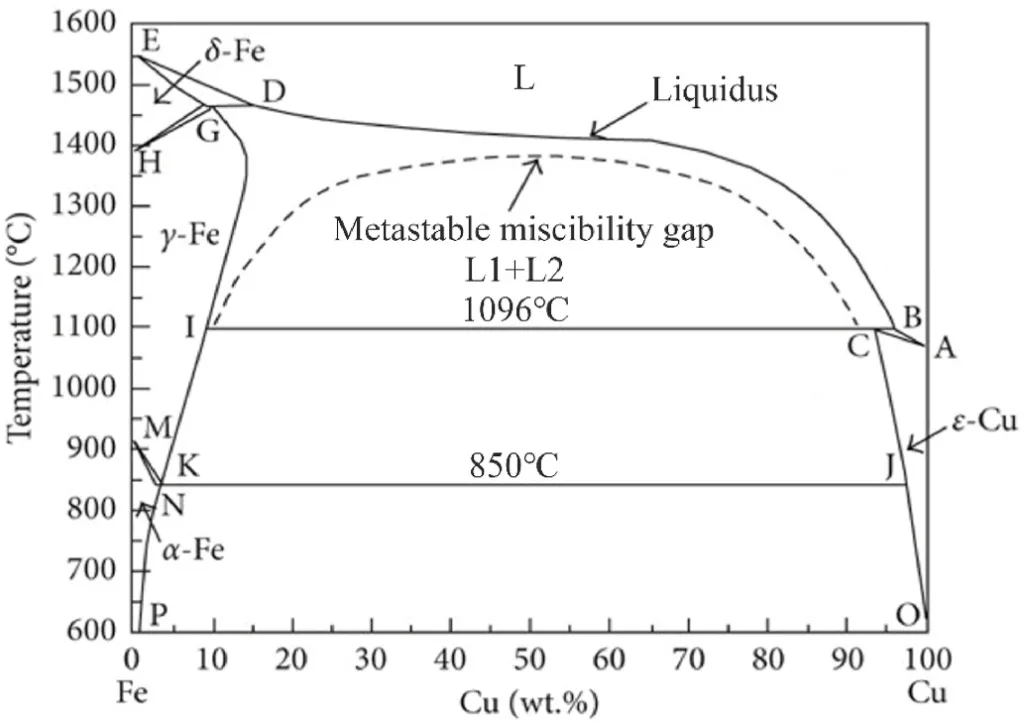
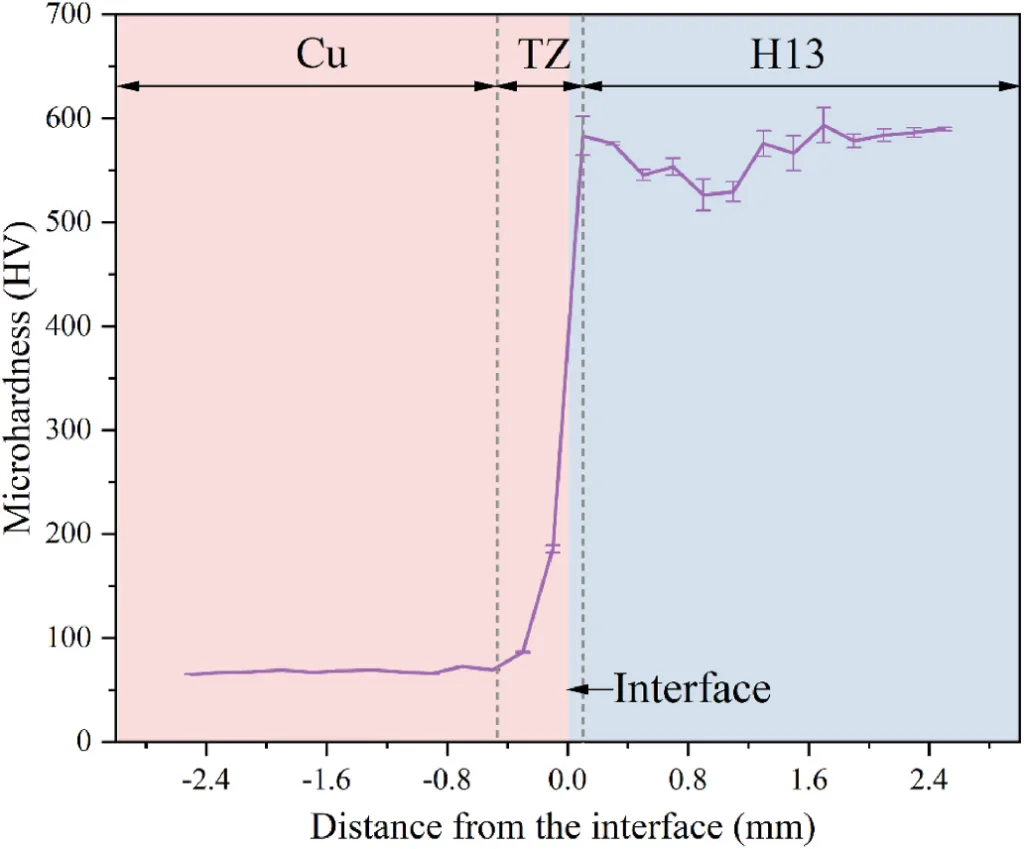
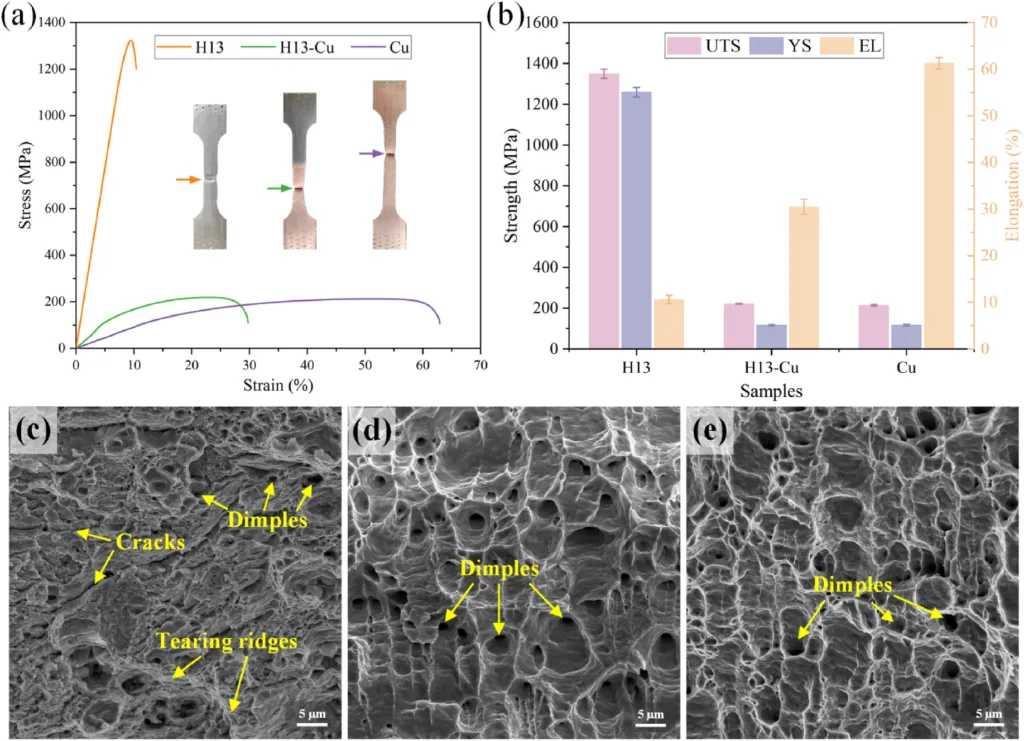
Figure Name List:
- Fig. 1. Schematic diagram of the experimental setup used to manufacture H13-Cu hybrid components.
- Fig. 2. Dimensions of tensile samples.
- Fig. 3. Modeling details of numerical simulation: (a-d) mesh model; (e-h) thermophysical and mechanical properties of H13 and Cu; (i) double ellipsoid heat source model; (j) heat source model verification.
- Fig. 4. Macrostructure, microstructure, and elemental distribution of the H13-Cu interface: (a) macrostructure of the H13-Cu interface; SEM images of (b) center, (c) below, and (d) above the H13-Cu interface; (e) the higher magnification SEM image of the purple boxed area in (d); (f) the higher magnification SEM image of the red boxed area in (d); (g) EDS mapping of the main elements in the blue boxed area in (e).
- Fig. 5. EDS mapping of typical features near the H13-Cu interface: (a) H13 intrusion into the Cu side; (b) Cu-rich islands and worm-like Cu-rich phases; (c) Fe-rich islands.
- Fig. 6. EDS line scanning results perpendicular to the interface near the H13-Cu interface.
- Fig. 7. XRD patterns of Cu side, H13 side and interface area.
- Fig. 8. EBSD results of H13-Cu interface: (a) BC map; (b) phase map; (c) IPF map; (d) grain boundary map; (e) KAM map; (f) pole figure of a-Fe.
- Fig. 9. EBSD results of microcracks above the interface: (a) phase map superimposed on BC map; (b) IPF map superimposed on BC map; (c) reconstructed prior austenite grains.
- Fig. 10. TEM analysis of Cu-rich particles above the interface: (a) High-angle annular dark field image (HAADF) and EDS mapping of Cu-rich particles; (b) HRTEM image of the Cu-rich particles of the blue box area in (a); (c) FFT image of (b); (d) IFFT image of the red box area in (b).
- Fig. 11. Temperature distribution of the H13-Cu hybrid component during deposition of (a) the first layer; (b) the tenth layer; (c) the twentieth layer; (d) the thirtieth layer (the last layer).
- Fig. 12. Temperature distribution during the first layer deposition and thermal cycle curves at local positions: (a) Temperature distribution of the cross-section of the molten pool; (b) Temperature distribution of the longitudinal section of the molten pool; (c) Thermal cycle curve of node 1 in (a); (d) Thermal cycle curve of node 2 in (a).
- Fig. 13. Schematic diagram of the molten pool morphology and microstructure evolution during the first layer deposition: (a) molten pool cross section; (b) molten pool longitudinal section.
- Fig. 14. Fe-Cu phase diagram [13].
- Fig. 15. Microhardness near the H13-Cu interface.
- Fig. 16. Room temperature tensile properties and fracture morphologies of H13-Cu hybrid components: (a) engineering stress-strain curve (the inset shows the fracture position of the tensile samples of H13, H13-Cu, and Cu); (b) tensile properties histogram; The fracture morphologies of (c) H13, (d) H13-Cu and (e) Cu samples.
7. Conclusion:
In this work, H13 steel was deposited directly on a Cu substrate by WAAM. The microstructure of the H13-Cu interface was studied, and the molten pool characteristics and interface evolution mechanism were revealed in combination with temperature field simulation. The causes of defects at the interface were discussed. Finally, the mechanical properties of the hybrid components were evaluated. The main conclusions are summarized as follows.
(1) Due to the metastable miscibility gap in the Fe-Cu system and the solubility limit of Fe and Cu in the solid state, the Fe-Cu mixed liquid at the interface underwent two liquid phase separations, forming Fe-rich islands and Cu-rich islands, as well as multi-scale Cu-rich particles. TEM results verified that the nanoscale Cu-rich particles are FCC structures and maintain a semi-coherent relationship with the α-Fe matrix.
(2) Defects such as pores and cracks were observed near the H13-Cu interface. Since the volume shrinkage of the liquid Cu-rich phase during solidification was hindered by the surrounding solidified Fe-rich phase, it could not be supplemented by liquid Cu, forming irregular pores. Microcracks were attributed to the penetration of copper into the prior austenite grain boundaries of the steel, resulting in higher crack sensitivity, which was generated under the action of thermal stress.
(3) The sharp element changes at the H13-Cu interface caused a jump in the melting point of the materials on both sides, but the temperature distribution changed continuously. Based on this result, the hypothesis of the existence of an extended molten pool below the interface was proposed. Near the interface, a mushy zone existed between the H13 molten pool and the Cu extended molten pool. After the extended molten pool solidified, a Cu columnar grain zone was formed.
(4) The microhardness decreased gradually from the H13 side to the Cu side in a narrow range (~0.5 mm) near the interface. The tensile sample of the hybrid component fractured on the Cu side far away from the interface, and its UTS (221 ± 2 MPa) reached the level of the Cu substrate, indicating that the interface formed a good bond.
8. References:
- [1] Reichardt A, Shapiro AA, Otis R, Dillon RP, Borgonia JP, McEnerney BW, Hosemann P, Beese AM. Advances in additive manufacturing of metal-based functionally graded materials. Int Mater Rev 2021;66:1–29.
- [2] Zhang X, Pan T, Flood A, Chen Y, Zhang Y, Liou F. Investigation of copper/stainless steel multi-metallic materials fabricated by laser metal deposition. Mater Sci Eng, A 2021:811.
- [3] Zhang B, Zhang W, Xiao H, Zhu H, Yang H, Wang Y, Chen B. QCr0.8 Cu alloy/S06 stainless steel bimetal structure via In718 multi-interlayer fabricated by laser powder hybrid additive manufacturing. J Mater Res Technol 2023;24:1034–42.
- [4] Rodrigues TA, Bairrão N, Farias FWC, Shamsolhodaei A, Shen J, Zhou N, Maawad E, Schell N, Santos TG, Oliveira JP. Steel-copper functionally graded material produced by twin-wire and arc additive manufacturing (T-WAAM). Mater Des 2022;213.
- [5] Tan C, Zhou K, Ma W, Min L. Interfacial characteristic and mechanical performance of maraging steel-copper functional bimetal produced by selective laser melting based hybrid manufacture. Mater Des 2018;155:77–85.
- [6] Li Z, Kuai Z, Liu B, Chen Y, Li H, Wang Y, Huo W, Wei M, Yang H, Bai P. Selective laser melting of 316L-CuCrZr bimetallic structure via IN718 transition layer. J Mater Res Technol 2023;25:3819–34.
- [7] Zhang X, Li L, Pan T, Chen Y, Zhang Y, Li W, Liou F. Additive manufacturing of copper-tool steel dissimilar joining: experimental characterization and thermal modeling. Mater Char 2020;170.
- [8] Chen S, Huang J, Xia J, Zhang H, Zhao X. Microstructural characteristics of a stainless steel/copper dissimilar Joint made by laser welding. Metall Mater Trans 2013;44:3690–6.
- [9] Cheng Z, Huang J, Ye Z, Chen Y, Yang J, Chen S. Microstructures and mechanical properties of copper-stainless steel butt-welded joints by MIG-TIG double-sided arc welding. J Mater Process Technol 2019;265:87–98.
- [10] Magnabosco I, Ferro P, Bonollo F, Arnberg L. An investigation of fusion zone microstructures in electron beam welding of copper-stainless steel. Mater Sci Eng, A 2006;424:163–73.
- [11] Sabetghadam H, Hanzaki AZ, Araee A. Diffusion bonding of 410 stainless steel to copper using a nickel interlayer. Mater Char 2010;61:626–34.
- [12] Shin S-S, Lee S-K, Kim D-K, Lee B. Enhanced cooling channel efficiency of high-pressure die-casting molds with pure copper linings in cooling channels via explosive bonding. J Mater Process Technol 2021;297.
- [13] Sun X, Hao W, Geng G, Ma T, Li Y, Yen Y-w. Solidification microstructure evolution of undercooled Cu-15 wt.% Fe alloy melt. Adv Mater Sci Eng 2018:2018.
- [14] Rock C, Tarafder P, Ives L, Horn T. Characterization of copper & stainless steel interface produced by electron beam powder bed fusion. Mater Des 2021;212.
- [15] Leedy KD, Stubbins JF. Copper alloy-stainless steel bonded laminates for fusion reactor applications: crack growth and fatigue. Mater Sci Eng, A 2001;297:19–25.
- [16] Zhang X, Li L, Liou F. Additive manufacturing of stainless steel - copper functionally graded materials via Inconel 718 interlayer. J Mater Res Technol 2021;15:2045–58.
- [17] Kibitkin V, Vorontsov A, Osipovich K, Shamarin N, Chumaevskii A, Rubtsov V, Moskvichev E, Savchenko N, Kolubaev E. Characterizing the tensile behavior of double wire-feed electron beam additive manufactured "copper-steel" using digital image correlation. Metals 2022;12.
- [18] Liu ZH, Zhang DQ, Sing SL, Chua CK, Loh LE. Interfacial characterization of SLM parts in multi-material processing: metallurgical diffusion between 316L stainless steel and C18400 copper alloy. Mater Char 2014;94:116–25.
- [19] Chen J, Yang Y, Song C, Zhang M, Wu S, Wang D. Interfacial microstructure and mechanical properties of 316L/CuSn10 multi-material bimetallic structure fabricated by selective laser melting. Mater Sci Eng, A 2019;752:75–85.
- [20] Tan C, Chew Y, Bi G, Wang D, Ma W, Yang Y, Zhou K. Additive manufacturing of steel-copper functionally graded material with ultrahigh bonding strength. J Mater Sci Technol 2021;72:217–22.
- [21] Martendal CP, Esteves PDB, Deillon L, Malamud F, Jamili AM, Löffler JF, Bambach M. Effects of beam shaping on copper-steel interfaces in multi-material laser beam powder bed fusion. J Mater Process Technol 2024;327.
- [22] Deillon L, Abando Beldarrain N, Li X, Bambach M. Coupling hot isostatic pressing and laser powder bed fusion: a new strategy to manufacture defect-free CuCrZr-316L steel multi-material structures. Mater Des 2024;241.
- [23] Liu K, Yan Z, Pan R, Wang X, Wang F, Chen S. Interfacial bonding and microstructural evolution in Inconel-copper bimetallic structures fabricated by directed energy deposition-arc. Mater Sci Eng, A 2024:898.
- [24] Zhang X, Sun C, Pan T, Flood A, Zhang Y, Li L, Liou F. Additive manufacturing of copper - H13 tool steel bi-metallic structures via Ni-based multi-interlayer. Addit Manuf 2020;36.
- [25] Craig OH, Moreau E, Toddy J, Murphy N, Halliday HS, Corbin SF, Plucknett KP. Functionally gradient H13 tool steel/oxygen-free high thermal conductivity Cu composites manufactured by laser-directed energy deposition. Steel Res Int 2024.
- [26] Zhang W, Liao H, Hu Z, Zhang S, Chen B, Yang H, Wang Y, Zhu H. Interfacial characteristics and mechanical properties of additive manufacturing martensite stainless steel on the Cu-Cr alloy substrate by directed energy deposition. J Mater Sci Technol 2021;90:121–32.
- [27] Liu L, Wang D, Deng G, Yang Y, Chen J, Tang J, Wang Y, Liu Y, Yang X, Zhang Y. Interfacial characteristics and formation mechanisms of copper-steel multimaterial structures fabricated via laser powder bed fusion using different building strategies. Chin J Mech Eng: Addit. Manuf. Front. 2022;1.
- [28] Imran MK, Masood SH, Brandt M. Bimetallic dies with direct metal-deposited steel on Moldmax for high-pressure die casting application. Int J Adv Manuf Technol 2010;52:855–63.
- [29] Bai Y, Zhang J, Zhao C, Li C, Wang H. Dual interfacial characterization and property in multi-material selective laser melting of 316L stainless steel and C52400 copper alloy. Mater Char 2020;167.
- [30] Tomar B, Shiva S. Microstructural and mechanical properties examination of SS316L-Cu functionally graded material fabricated by wire arc additive manufacturing. CIRP J. Manuf. Sci. Technol. 2024;50:26–39.
- [31] Maurya AK, Yeom J-T, Kim JH, Park CH, Hong J-K, Yang J, Kang NH, Cheon S, Reddy NS, Cheepu M, Cho S-M. Wire arc additive manufacturing method for Ti-6Al-4V alloy to improve the grain refinement efficiency and mechanical properties. J Mater Res Technol 2024;31:3003–13.
- [32] Tan Q, Yin Y, Wang F, Chang H, Liu S, Liang G, Wu T, Zhang M-X. Rationalization of brittleness and anisotropic mechanical properties of H13 steel fabricated by selective laser melting. Scr Mater 2022;214.
- [33] Sun Y, Wang J, Li M, Wang Y, Li C, Dai T, Hao M, Ding H. Thermal and mechanical properties of selective laser melted and heat treated H13 hot work tool steel. Mater Des 2022.
- [34] Liu L, Wang D, Deng G, Han C, Yang Y, Chen J, Chen X, Liu Y, Bai Y. Laser additive manufacturing of a 316L/CuSn10 multimaterial coaxial nozzle to alleviate spattering adhesion and burning effect in directed energy deposition. J Manuf Process 2022;82:51–63.
- [35] Al-Jamal OM, Hinduja S, Li L. Characteristics of the bond in Cu-H13 tool steel parts fabricated using SLM. CIRP Ann 2008;57:239–42.
- [36] Telasang G, Narayanaswamy S, D.M S, Bathe R. Selective laser melting of stainless steel on the copper alloy: an investigation of the interfacial microstructure and mechanical properties. J Manuf Process 2022;80:920–9.
- [37] Munitz A, Venkert A, Landau P, Kaufman MJ, Abbaschian R. Microstructure and phase selection in supercooled copper alloys exhibiting metastable liquid miscibility gaps. J Mater Sci 2012;47:7955–70.
- [38] Zhang M, Zhang Y, Du M, Zhang S, Lei L. Experimental characterization and microstructural evaluation of silicon bronze-alloy steel bimetallic structures by additive manufacturing. Metall Mater Trans 2021;52:4664–74.
- [39] Chen G, Shu X, Liu J, Zhang B, Feng J. Crystallographic texture and mechanical properties by electron beam freeform fabrication of copper/steel gradient composite materials. Vacuum 2020;171.
- [40] Cui Q, Lin X, Jiang S, Ren Z, Guo Y, Zhang H, Zhang X, Wen B. High-pressure induced the morphological evolution from lath to integrated martensite with {112} <111> nano-twins of 30MnSi steel. Mater Sci Eng, A 2023:879.
- [41] Wang YM, Voisin T, McKeown JT, Ye J, Calta NP, Li Z, Zeng Z, Zhang Y, Chen W, Roehling TT, Ott RT, Santala MK, Depond PJ, Matthews MJ, Hamza AV, Zhu T. Additively manufactured hierarchical stainless steels with high strength and ductility. Nat Mater 2018;17:63–71.
- [42] Rui S-S, Han Q-N, Wang X, Li S, Ma X, Su Y, Cai Z, Du D, Shi H-J. Correlations between two EBSD-based metrics Kernel Average Misorientation and Image Quality on indicating dislocations of near-failure low alloy steels induced by tensile and cyclic deformations. Mater Today Commun 2021;27.
- [43] Hasani N, Ghoncheh MH, Kindermann RM, Pirgazi H, Sanjari M, Tamimi S, Shakerin S, Kestens LAI, Roy MJ, Mohammadi M. Dislocations mobility in superalloy-steel hybrid components produced using wire arc additive manufacturing. Mater Des 2022;220.
- [44] Huang G, Wei K, Zeng X. Microstructure and mechanical properties of H13 tool steel fabricated by high power laser powder bed fusion. Mater Sci Eng, A 2022:858.
- [45] Tan Q, Chang H, Yin Y, Wang F, Huang D, Liang G, Wu T, Yan M, Cheng X, Zhang M-X. Simultaneous enhancements of strength and ductility of a selective laser melted H13 steel through inoculation treatment. Scr Mater 2022;219.
- [46] Du X, Liu X, Shen Y, Liu R, Wei Y. H13 tool steel fabricated by wire arc additive manufacturing: solidification mode, microstructure evolution mechanism and mechanical properties. Mater Sci Eng 2023;A:883.
- [47] Han G, Shang CJ, Misra RDK, Xie ZJ. Solid phase transition of Cu precipitates in a low carbon TRIP assisted steel. Physica B 2019;569:68–79.
- [48] Zhang Y, Song R, Wang Y, Wang Y, Cai C, Wang K. Evolution of twins and formation mechanism of special fringes inside nanoscale Cu precipitates in ferritic steel. Mater Char 2022;192.
- [49] Monzen R, Iguchi M, Jenkins ML. Structural changes of 9R copper precipitates in an aged Fe-Cu alloy. Philos Mag Lett 2000;80:137–48.
- [50] Chen BL, Wang W, Xie H, Ge RR, Zhang ZY, Li ZW, Zhou XY, Zhou BX. Phase transformation of Cu-rich precipitates from 9R to 3R variant via ledges mechanism in ferritic steel containing copper. J Microsc 2016;262:123–7.
9. Copyright:
- This material is a paper by "Xinwei Du, Yanhong Wei, Kai Guo, Jinwei Long, Xiangbo Liu, Wenyong Zhao, Renpei Liu". Based on "Interface microstructure and evolution mechanism of wire arc additively manufactured H13 steel-copper hybrid components".
- Source of the paper: https://doi.org/10.1016/j.jmrt.2025.02.160
This material is summarized based on the above paper, and unauthorized use for commercial purposes is prohibited.
Copyright © 2025 CASTMAN. All rights reserved.