This introductory paper is the research content of the paper "High strength aluminum alloys in car manufacturing" published by IOP Publishing.
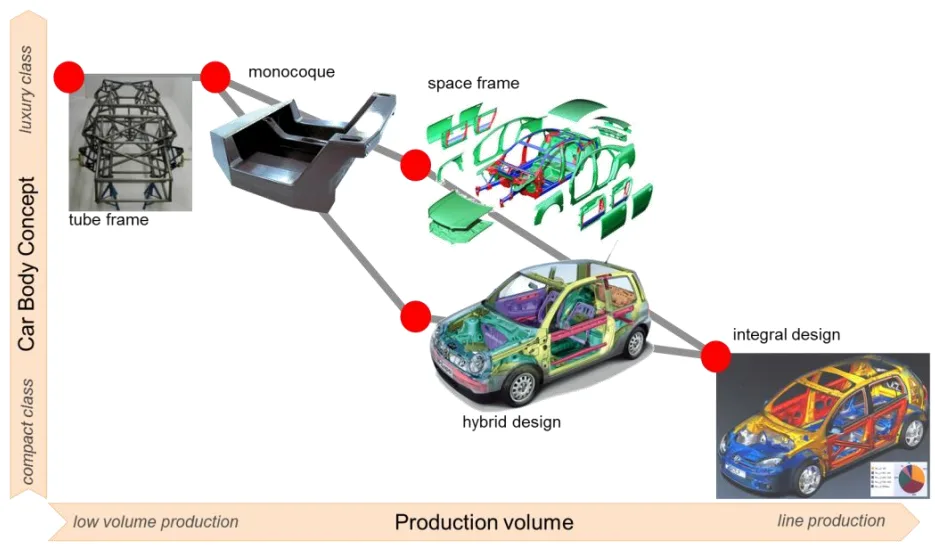
1. Overview:
- Title: High strength aluminum alloys in car manufacturing
- Author: M Tisza and Zs Lukács
- Publication Year: 2018
- Published Journal/Society: IOP Conference Series: Materials Science and Engineering, 418 (2018) 012033
- Keywords: aluminum alloys, lightweight design, car body construction, hot forming, formability, HFQ
2. Abstract
In recent decades, there are many requirements stated against car manufacturing both from the customers' side and also as legal requirements to reduce harmful emissions to provide increased environment protection, as well as to achieve increased safety, higher comfort and more economical vehicles. To meet these often contradictory requirements, application of light weight design principles is one of the most widely applied solutions. There are two main trends for producing lightweight automotive structures with low cost manufacturing which are particularly valid for car body elements produced by sheet metal forming. The application of lightweight alloy materials – particularly various aluminum alloys – is regarded as the other possible solution to meet the requirements of lightweight car body constructions. Aluminum has even higher weight reduction potential than steel materials, but aluminium has lower formability than steel; replacing steel with lighter materials such as aluminum can be costly and is not simply straightforward. This is one of the main reasons that recently the hot forming of aluminum alloys came to the forefront of research activities. In this paper, some recent results obtained within a joint European project entitled Low Cost Materials Processing Technologies for Mass Production of Lightweight Vehicles will be introduced.
3. Research Background:
Background of the research topic:
The main development trends in car manufacturing are driven by customer demands (lower consumption, increased safety, functionality, and comfort) and stricter legal requirements (lower harmful emissions, increased crashworthiness) [1]. Weight reduction is a key strategy to meet these, often contradictory, requirements.
Status of previous research:
Traditionally, steel has been the dominant material in Body in White (BIW) manufacturing. However, developments include various generations of high-strength steels (e.g., DP-steels, TRIP steels, XHSS, and UHSS) [Figure 2]. The application of lightweight alloy materials especially aluminum is regarded as an effective solution.
Need for research:
Aluminum has lower formability than steel at room temperature, making direct substitution challenging and costly. This has driven research into hot forming of aluminum alloys.
4. Research Purpose and Research Question:
Research Purpose:
To review the main possibilities to meet requirements including material and process developments, and also compare the possibilities and development trends in future car making solutions. To Introduce recent results obtained in a joint European Project(Low Cost Materials Processing Technologies for Mass Production of Lightweight Vehicles)
Core research:
Focuses on addressing the challenges of using aluminum alloys in car body manufacturing, particularly the lower formability of aluminum compared to steel at room temperature.
5. Research Methodology
- Literature Review: Review of existing car body concepts (integral design, space-frame, hybrid design, tube frame, monocoque) and their relationship to production volume and economy [Figure 1] [3]. Review of material developments, including high-strength steels and aluminum alloys, and their weight reduction potential [Figure 2] [4]. Review on aluminum historical overview and multi-material approach.
- Material and formability Tests: Several material and formability tests. Formability investigations were done with the modified Nakajima test(computer controlled universal sheet formability-testing machine with optical strain measurement system). Determination of Flow curves and Forming Limit Curves of AA7075 alloy at various temperatures [Figure 6].
- Experimental Data Analysis: Analysis of formability parameters at different elevated temperatures and strain rates, particularly for AA7075 aluminum alloy.
6. Key Research Results:
Key research results and presented data analysis:
- Aluminum alloys offer significant weight reduction potential (25-40%) compared to reference HSLA steel [Figure 2].
- Hot forming is a key enabling technology for high-strength aluminum alloys with low room-temperature formability.
- The Hot Forming and Quenching (HFQTM) process [Figure 5] [19] is highlighted, with similarities and differences to hot forming of boron alloyed steels.
- The formability of AA7075 aluminum alloy increases with temperature, with an optimum hot forming temperature around 400°C. [Figure 6]
- AA7075 has flow curve at T=450°C [Figure 6.a], the failure strain in hot uniaxial test was decreased above this temperature [Figure 6.b].
List of figure names:
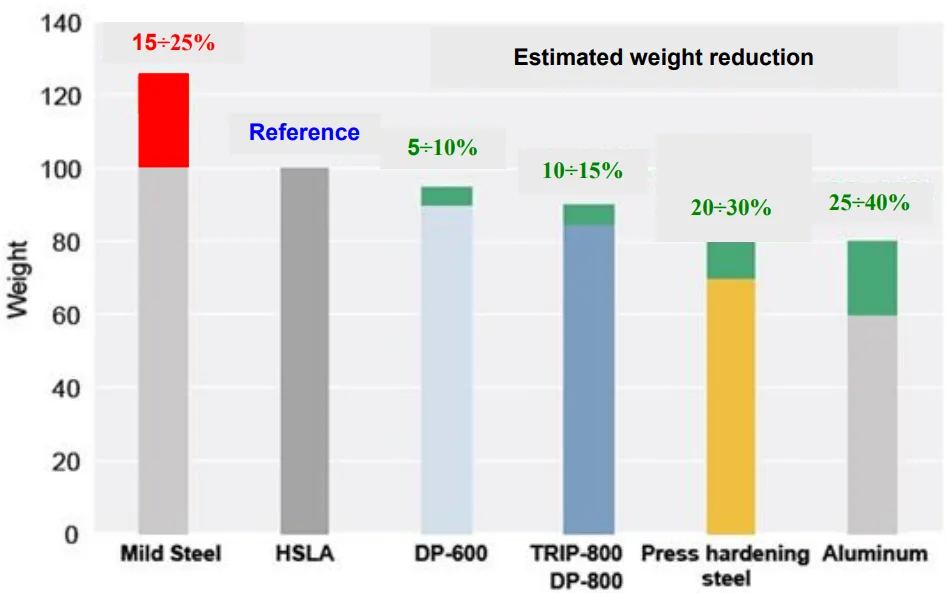

![Figure 4. Affordability of weight reduction using various multi-material concepts [15].](https://castman.co.kr/wp-content/uploads/image-1529-1024x539.webp)
![Figure 5. Basic principle of Hot Forming and QuenchingTM of aluminum alloys [19].](https://castman.co.kr/wp-content/uploads/image-1530-1024x344.webp)
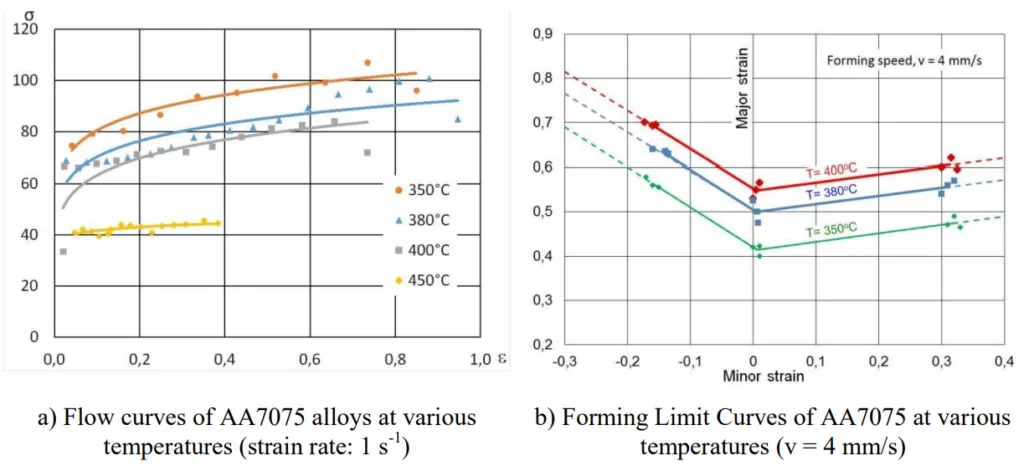
- Figure 1. Car body concepts as a function of production volume.
- Figure 2. The weight reduction potential of various high strength materials in car body manufacturing.
- Figure 3. Multi-material concept in car body manufacturing.
- Figure 4. Affordability of weight reduction using various multi-material concepts [15].
- Figure 5. Basic principle of Hot Forming and Quenching™ of aluminum alloys [19].
- Figure 6. Flow curves and Forming Limit Curves for AA7075 alloy at various temperatures.
7. Conclusion:
Summary of key findings:
- Lightweight construction principles, including the use of high-strength steels and aluminum alloys, are crucial for meeting modern automotive requirements.
- Hot forming processes, like HFQ, are essential for utilizing high-strength aluminum alloys effectively.
- The material properties and forming limits of aluminum alloys are highly dependent on temperature and strain rate during hot forming.
- Application of high strength aluminum alloys is significantly increasing.
Possible areas for future expansion research:
- Further optimization of hot forming processes, including cycle time reduction through fast heating/cooling and integration with other manufacturing processes (e.g., paint baking).
- Continued exploration and characterization of different aluminum alloys for automotive applications.
- Further study related to multi-material lightweight construction.
8. References:
- [1] Tisza M (2015) Metal Forming in the automotive industry, Miskolc University Press, p. 294 ISBN 978-963-358-082-0
- [2] Czinege I (2017) Comparative analysis of steel and aluminum sheets, Proc. 16th Metal Forming Conf. Miskolc-Hungary
- [3] Liewald M and Schleich R (2007) Robust processes in sheet metal forming in car body manufacturing with regard to production volume, Proc. of IDDRG 2007, Győr, Hungary, 21-23. May 2007. pp. 11-20.
- [4] Tisza M (2013) Recent development trends in sheet metal forming, Int. J. Microstructure and Material Prop. 8. No. 1-2. pp. 125-139.
- [5] Tisza, M (2014) Advanced materials in sheet metal forming, Key Engineering Materials, 581 pp. 137-142. DOI:10.4028/www.scientific.net/KEM.581.137
- [6] Ghassemieh E (2011) Materials in Automotive Application – State of the Art and Prospects, in New Trends and Developments in Automotive Industry, InTech Open Publications, DOI: 10.5772/1821
- [7] Banik J et. al (2013) Warmumformung im Automobilbau, Süddeutsche Verlag, Munich, p. 84.
- [8] Lin Jianguo et. al (2011) A method of forming a component of complex shape from aluminum alloy sheet, GB 2473298 British Patent
- [9] Keeler S, Kimchi M and Mooney, P (2017) Advanced High Strength Steels – Application Guidelines 6.0, World Auto Steel April, pp. 314.
- [10] Tisza M (2015) Material and technological developments in sheet metal forming with special regards to the needs of the automotive industry, Archives of Materials Science and Engineering, 71 No.1. pp. 36-45.
- [11] Audi AG.: Historical background on use of aluminium at Audi, https://www.audiworld.com/news/02/aluminum/content1.shtml
- [12] European Aluminium Association (2012) Aluminium in cars-unlocking – The light weighting potential http://www.alueurope.eu/publications-automotive/
- [13] Kelkar A, Roth R and Clark J (2001) Automobile Bodies: Can Aluminum Be an Economical Alternative to Steel, Journal of Manufacturing 53 No. 8. pp. 28-32.
- [14] Lotus Engineering (2010) An assessment of mass reduction opportunities for 2017-2020 model year vehicle program, The International Council on Clean Transportation
- [15] Goede M et. al (2009) Super Light Car - lightweight construction thanks to a multi-material design and function integration, European Transp. Res. Rev No.1. pp. 5-10. DOI 10.1007/s12544-008-0001-2
- [16] Budai D and Tisza M (2017) Investigation of EN AW 5754 Aluminum Alloy's Formability at Elevated Temperatures Material Science Forum, 885, pp 98-103.
- [17] Budai D, Kovács P and Lukács Zs (2016) Formability investigations of Aluminum alloys at elevated temperatures, IDDRG 2016 Conference, Linz, 12-15. June 2016
- [18] Bach, R.: Aluminium in transport industry, https://www.aluminiumleader.com/application/transport/
- [19] LoCoMaTech (2016) Low Cost Materials Processing Technologies for Mass Production of Lightweight Vehicles EU H-2020 project 2016-2019, ID No: 723517.
- [20] Tisza M (2001) Physical Metallurgy for Engineers, ASM Publisher, 2001, Ohio-London, p.405.
9. Copyright:
- This material is a paper by "M Tisza and Zs Lukács": Based on "High strength aluminum alloys in car manufacturing".
- Source of paper: doi:10.1088/1757-899X/418/1/012033
This material was created to introduce the above paper, and unauthorized use for commercial purposes is prohibited. Copyright © 2025 CASTMAN. All rights reserved.