This article introduces the paper "High Density Die Casting (HDDC): New Frontiers in the Manufacturing of Heat Sinks".
- Core Research Objective: To develop a High Density Die Casting (HDDC) process to overcome the limitations of conventional die casting and extrusion methods for manufacturing high-performance heat sinks for electronic systems requiring efficient thermal management.
- Methodology: Development and evaluation of an HDDC process utilizing high-thermal conductivity aluminum alloys. Fabrication of heat sinks with various fin designs. Performance assessment through computational fluid dynamics (CFD) simulations and experimental testing. Investigation of incorporating different materials (e.g., copper) within the HDDC process.
- Key Findings: The HDDC process demonstrates significantly improved heat dissipation efficiency compared to conventional die casting. It offers greater flexibility in 3D design, enabling the creation of complex fin geometries not feasible with extrusion. The process produces porosity-free, high-strength components with enhanced thermal conductivity through the use of superior aluminum alloys and the potential for incorporating other high-conductivity materials.
Researcher Information
- Affiliation: Aavid Thermalloy S.r.l.
- Authors: Andrea Sce, Lorenzo Caporale
- Research Areas: Thermal Management, Die Casting Processes
Research Background and Objectives
- Industrial Context: The increasing power density and miniaturization of electronic devices necessitate more efficient thermal management solutions. High-volume manufacturing requires cost-effective and scalable processes.
- Technical Challenges: Conventional extrusion processes are limited to 2D designs, specific aluminum alloys (6xxx series), and restricted fin geometries. Traditional die casting suffers from low thermal conductivity of the alloys used, resulting in poor heat dissipation, and porosity issues affecting mechanical strength and surface finish. Integrating dissimilar materials (e.g., copper for enhanced conductivity) is difficult.
- Research Goals: To develop a novel HDDC process to overcome the limitations of extrusion and conventional die casting. This includes achieving higher thermal conductivity, greater design flexibility (3D designs), improved mechanical properties (porosity elimination), and the ability to integrate multiple materials for optimal performance.
Main Objectives and Research Content
- Main Objectives: The primary objective is the development and validation of the HDDC process for manufacturing high-performance heat sinks, surpassing the limitations of existing technologies (extrusion and die casting). Secondary objectives include the investigation of material integration and the scalability of the HDDC process for high-volume manufacturing.
- Challenges Addressed: The research directly addresses the limitations of extrusion and conventional die-casting. Specifically, it tackles issues of limited design flexibility (2D vs. 3D), restricted material selection (limited to specific aluminum alloys), poor thermal conductivity (inherent to commonly used die-casting alloys), and porosity leading to mechanical weakness and surface finish problems.
- Stepwise Approach: The research followed a phased approach:
- Initial Research (Phase 1): Fundamental studies of material selection and process parameters.
- Medium-Scale Development (Phase 2): Development and testing of the HDDC process using smaller components.
- Large-Scale Development (Phases 3 & 4): Scaling up the HDDC process for larger components and higher volumes.
- Advanced Process Development (Phase 5): Further refinement of the HDDC process, including the integration of different materials and heat pipes.
- Key Figures (detailed descriptions below): Figures 1, 2, 3, 4, 5, 6, 7, 8, 9, 10, and 11 illustrate various aspects of the research, including limitations of extrusion and die-casting, the HDDC process steps, CFD simulations, microstructural analysis, mechanical properties, development roadmap, example products, material integration, and a large-scale HDDC component.
Detailed Figure Descriptions:
(Note: The following descriptions rely heavily on direct quotes from the paper's captions and surrounding text to avoid interpretation. Full descriptions would require reproducing the figures themselves.)
- Figure 1. Extrusion limits: This figure highlights the limitations of extrusion in terms of fin geometry, fin density, and allowable aluminum alloys. Sharp differences between adjacent sections are prohibited, and the maximum ratio between fin height and gap is limited. Only 6xxx series aluminum alloys can be used.
- Figure 2. Die-casting limits: This figure illustrates limitations of die casting, such as restricted geometry (due to the casting process), limitations on alloy selection (limited corrosion resistance for outdoor applications due to higher copper content in easier-to-cast alloys), inherent porosity, and difficulty with surface treatments.
- Figure 3. Steps in the HDDC process: A schematic illustrating the sequential steps of the HDDC process: pouring molten metal, lowering the punch, pressurizing the liquid metal, and ejection of the solidified component.
- Figure 4. CFD comparison between traditional DC (left) and HDDC (right); HDDC allow more fins: This figure presents CFD simulation results comparing conventional die casting and HDDC. HDDC demonstrates lower thermal resistance (Rth) and allows for more fins. Specific numerical values (e.g., Tmax, Rth, AP) are provided for both processes.
- Figure 5. Metallographic analysis of HDDC structure vs die-casting structure: Microscopic images comparing the microstructure of HDDC and conventional die casting. HDDC exhibits a pore-free structure.
- Figure 6. Mechanical Properties for Al 6xxx-T4 Series: test results comparison between HDDC and extruded material: This figure presents a comparison of mechanical properties (yield strength and tensile strength) for HDDC components versus extruded components made from the same aluminum alloys.
- Figure 7. Capabilities development path: A roadmap illustrating the phased development of the HDDC process, progressing from initial research to advanced process development involving larger-scale components and integrated features.
- Figure 8. Examples of HDDC products: Images showcasing a variety of components manufactured using the HDDC process, demonstrating its versatility and design flexibility.
- Figure 9. Examples of HDDC products with Al and Cu (cut section – 60x17x40 mm): A cross-sectional view of a component illustrating the successful integration of aluminum and copper within the HDDC process.
- Figure 10. Microscopic and ultrasonic scan on HDDC made with Al and Cu: Microscopic and ultrasonic images verifying the quality of the aluminum-copper interface in the HDDC components.
- Figure 11. A big part made by HDDC with Al and Cu: An image of a large-scale component produced using the HDDC process, highlighting the scalability of the technology.
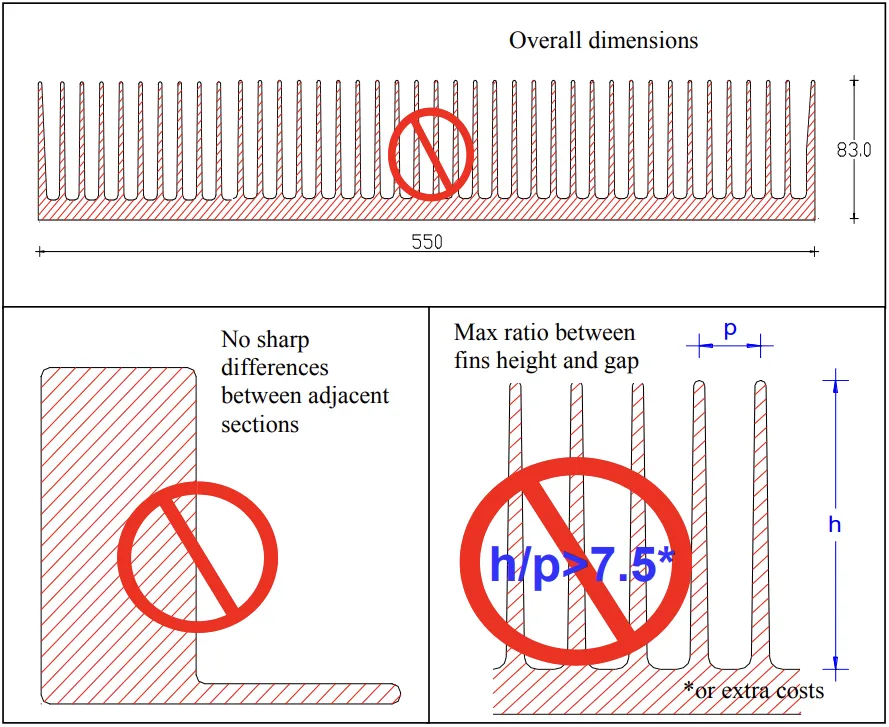
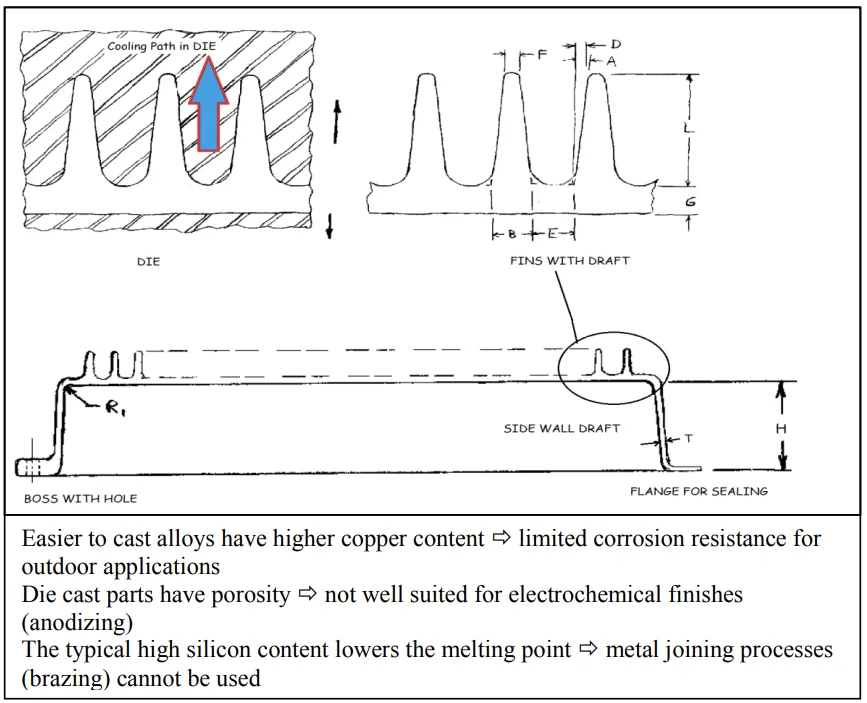
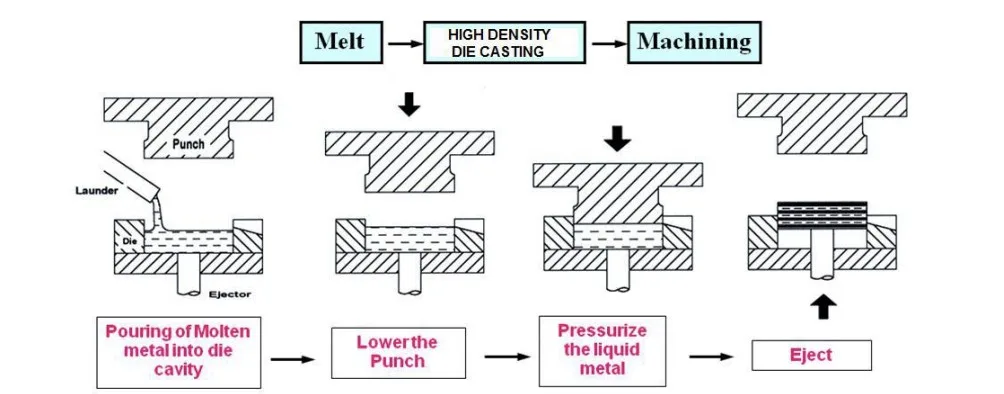
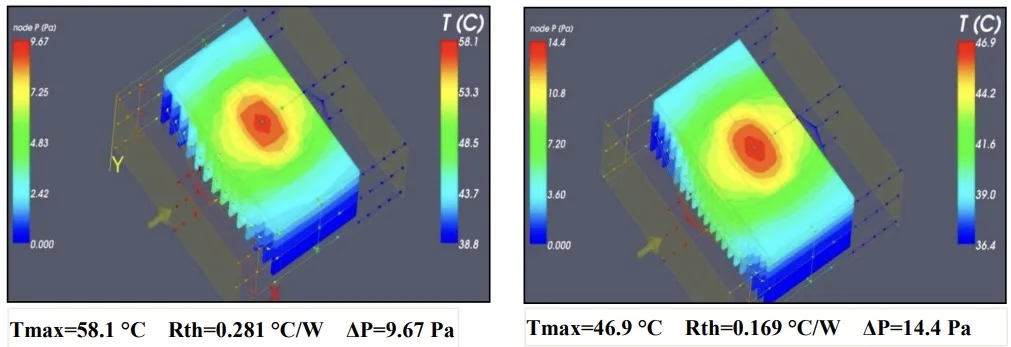
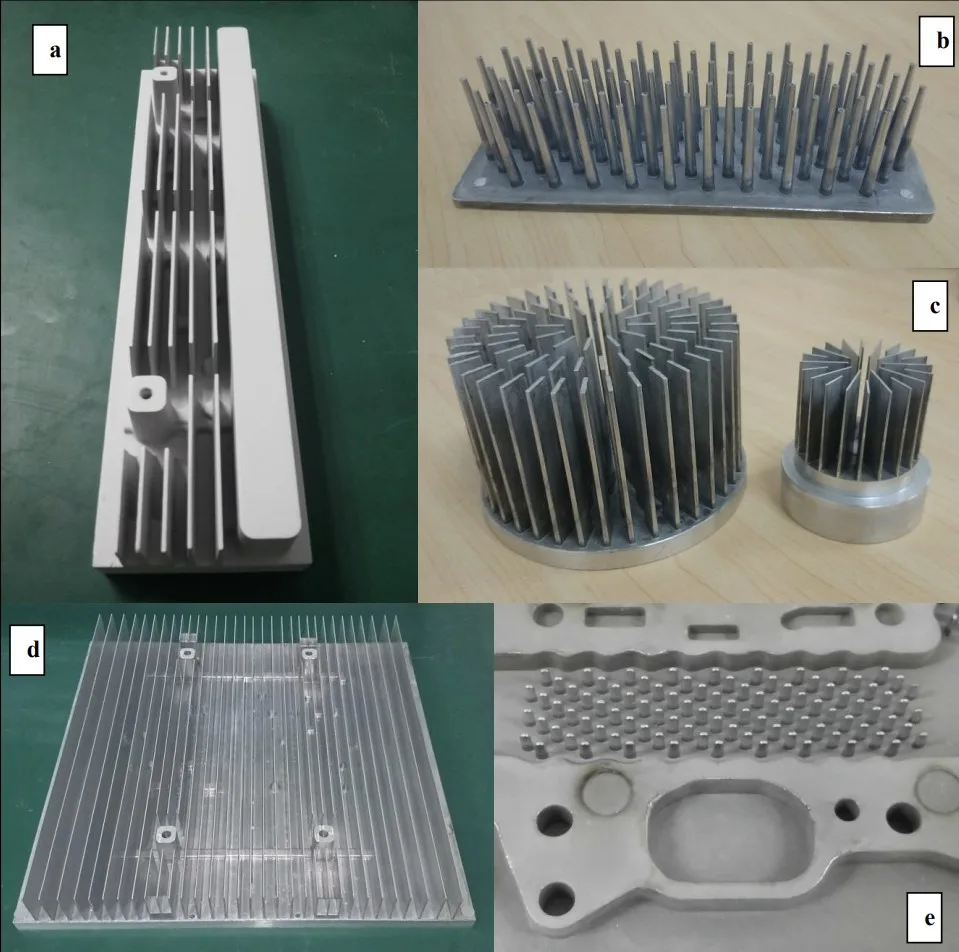
Results and Achievements
- Quantitative Results: CFD simulations showed approximately a 40% reduction in thermal resistance (Rth) for HDDC compared to conventional die casting. Mechanical testing demonstrated that the HDDC process produces components with mechanical properties comparable to or better than extruded parts.
- Qualitative Results: The HDDC process enables the creation of porosity-free, high-strength heat sinks with intricate 3D geometries not possible with extrusion. The process allows for integration of dissimilar materials, such as copper, for further improvements in thermal performance.
- Technological Advances: The research successfully developed and validated a novel HDDC process for manufacturing high-performance heat sinks. The technology demonstrates significant advantages over conventional die casting and extrusion methods in terms of thermal performance, design flexibility, material integration capabilities, and mechanical properties. The HDDC process shows promise for high-volume manufacturing and the potential for further advancements through the integration of embedded heat pipes.
Copyright and References
This document summarizes the research paper "High Density Die Casting (HDDC): new frontiers in the manufacturing of heat sinks" by Andrea Sce and Lorenzo Caporale, published in the Journal of Physics: Conference Series.
DOI: 10.1088/1742-6596/525/1/012020
Copyright © 2014 IOP Publishing Ltd. All rights reserved. This summary is for informational purposes only and should not be used for commercial purposes without permission from the copyright holder.