고압 다이캐스팅의 열처리
Metallurgical and Materials Transactions A volume 38, pages2564–2574 (2007)Cite this article
- 1517 Accesses
- 99 Citations
- 3 Altmetric
- Metricsdetails
Abstract
High-pressure die-cast Al alloys cannot normally be heated at high temperatures due to the presence of pores containing entrapped gases, which lead to the formation of surface blisters. It has been found that blistering can be avoided by using considerably shorter solution-treatment times and lower temperatures. Experiments with alloys 360 (Al-9.5Si-0.5Mg) and 380 (Al-8.5Si-3.5Cu) have shown that strong responses to age hardening are still possible following these modified solution treatments.[1–3] For T6 tempers, increases in 0.2 pct proof stress of 80 pct for 360 and 115 pct for 380 have been obtained compared with as-cast values. Using a T4 temper, ductility is improved without any sacrifice in strength.
고압 다이캐스트 Al 합금은 포획된 가스를 포함하는 기공이 존재하여 표면 기포를 형성하기 때문에 일반적으로 고온에서 가열할 수 없습니다. 블리스터링은 용액 처리 시간을 상당히 단축하고 온도를 낮춤으로써 피할 수 있음이 밝혀졌습니다.
합금 360(Al-9.5Si-0.5Mg) 및 380(Al-8.5Si-3.5Cu)을 사용한 실험은 시효 경화에 대한 강한 반응이 이러한 수정된 용액 처리 후에도 여전히 가능하다는 것을 보여주었습니다.[1-3] T6 템퍼의 경우, 주조 값과 비교하여 360의 경우 80%, 380의 경우 115%의 0.2% 내력 증가가 얻어졌습니다. T4 템퍼를 사용하여 강도 저하 없이 연성을 향상시킵니다.
This is a preview of subscription content, access via your institution.
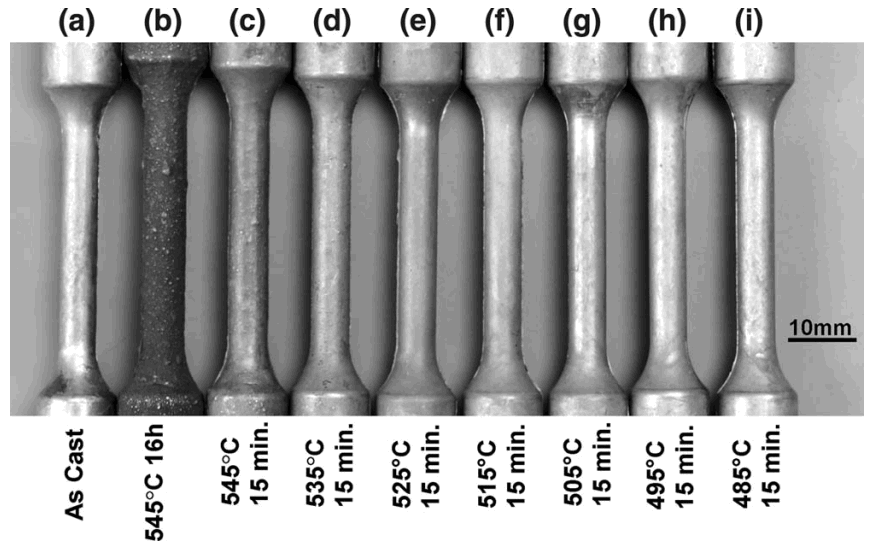
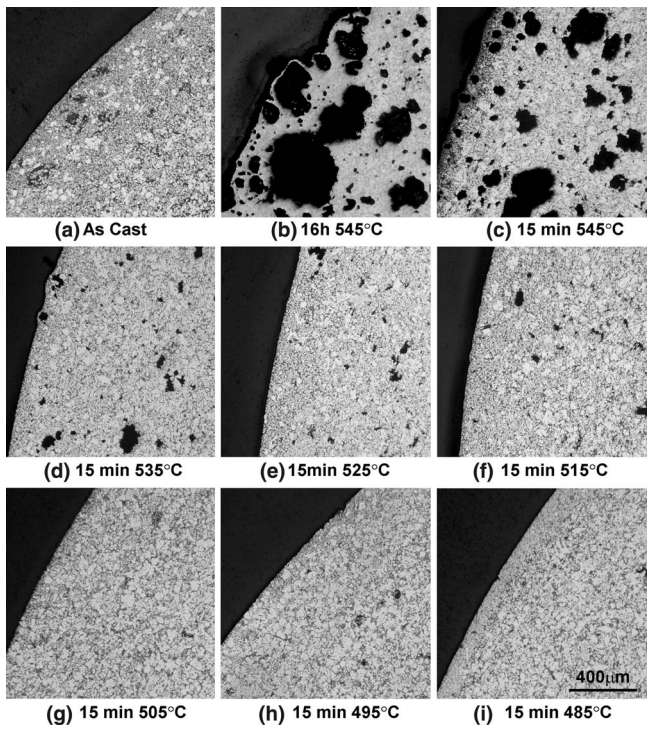
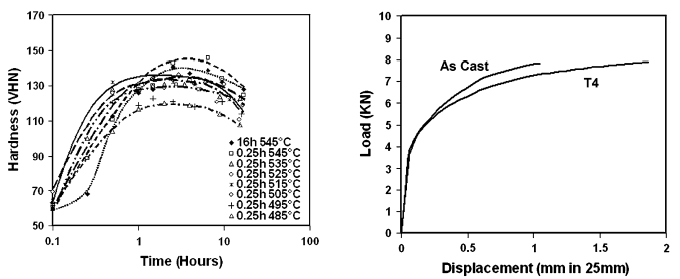
Fig. 5—Comparative tensile curves for alloy 360 in the as-cast and T4 condition exhibiting similar 0.2 pct proof stress and tensile strength.
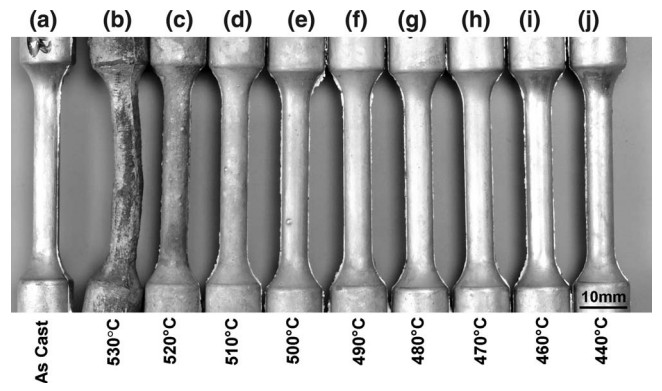
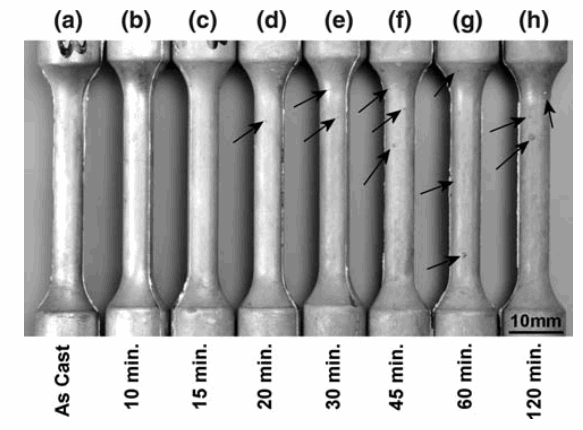
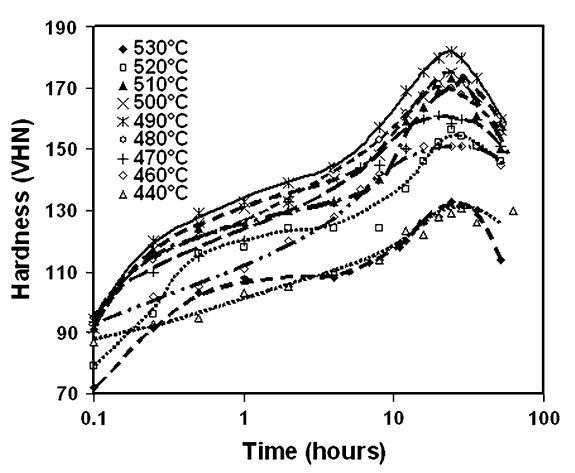
![Fig. 10—TEM images of (a) the as-cast alloy showing large h¢ precipitates and (b) the T6-treated alloy, showing h¢ precipitates. Both images were taken near to [101]a. In the as-cast condition, there were few strengthening precipitates observed with many grains appearing to contain no precipitates.](https://castman.co.kr/wp-content/uploads/Fig.-10—TEM-images-of-a-the-as-cast-alloy--1024x525.png)
Notes
- T4 tempers were a standard 14 days at ∼25 °C, which was found to produce a stabilized condition.
- JEOL is a trademark of Japan Electron Optics Ltd., Tokyo.
References
- R.N. Lumley, R.G. O’Donnell, D.R. Gunasegaram, and M. Givord: International Patent Application PCT/2005/001909
- R.N. Lumley, R.G. O’Donnell, D.R. Gunasegaram, M. Givord: Mater. Sci. Forum, 2006, vols. 519–522, pp. 351–59Article Google Scholar
- R.N. Lumley, R.G. O’Donnell, D.R. Gunasegaram, and M. Givord: Proc. 13th Die Casting Conf. Australian Die Casting Association, Melbourne, 2006, paper no. 25
- L. Wang, V. Nguyen, G. Savage, R. Chatfield, and D. Matthews: Proc. 12th Die Casting Conf. Australian Die Casting Association, Melbourne, 2004, paper no. 9
- E.J. Vinarcik: High Integrity Die Casting Processes, John Wiley & Sons, New York, NY, 2003, p. 162Google Scholar
- I.J. Polmear: Light Alloys: from Traditional Alloys to Nanocrystals, 4th ed., Butterworth Heinemann, Oxford, United Kingdom, 2006, p. 206Google Scholar
- B.A. Parker, D.S. Saunders, J.R. Griffiths: Met. Forum, 1982, vol. 5 (1), pp. 48–53.CAS Google Scholar
- N. Onishi, T. Takaai, Y. Nakayama, and M. Ohmori: J. Jpn. Inst. Light Met., 1995, pp. 447–52
- P.A. Rometsch, L. Arnberg, D.L. Zhang: Int. J. Cast. Met. Res., 1999, vol. 12, pp. 1–8CAS Google Scholar
- A. Perovic, D.D. Perovic, G.C. Weatherly, D.J. Lloyd: Scripta Mater., 1999, vol. 41 (7), pp. 703–08Article CAS Google Scholar
- D.J. Bryant: Metall. Mater. Trans A, 1999, vol. 30A, pp. 1999–2006Article CAS Google Scholar
- G.C. Weatherley, A. Perovic, N.K. Mukhopadhyay, D.J. Lloyd, D.D. Perovic: Metall. Mater. Trans. A, 2001, vol. 32A, pp. 213–18Article Google Scholar
- J.A. Taylor, D.H. St. John, L.H. Zheng, G.A. Edwards, J. Barresi, M.J. Couper: Alum. Trans., 2001, vols. 4–5, pp. 95–110Google Scholar
- J.A. Taylor, D.H. St. John, M.J. Couper: Alum. Trans., 2001, vol. 4–5, pp. 111–24Google Scholar
- H.J. Li, S. Shivkumar, X.J. Luo, D. Apelian: Cast Met., 1989, vol. 1 (4), pp. 227–34Google Scholar
- D.L. Zhang, L.H. Zheng, D.H. St. John: Conf. Proc. Mater. Res. 96, 1996, vol. 1, pp. 25–28Google Scholar
- D.L. Zhang, L.H. Zheng, D.H. St. John: Mater. Sci. Technol., 1998, vol. 14, pp. 619–25CAS Google Scholar
- J. Campbell: Castings, Butterworth Heinemann Ltd., Oxford, United Kingdom, 1991, pp. 273–75Google Scholar
- S.N. Singh, B.P. Bardes, M.C Flemings: Metall. Trans., 1970, vol. 1, pp. 1383–88CAS Google Scholar
- R.N. Lumley, G.B. Schaffer: Scripta Mater., 1996, vol. 35 (5), pp. 589–95Article CAS Google Scholar
Acknowledgment
The authors thank Professor Ian Polmear for assistance with preparing the manuscript.
Author information
Authors and Affiliations
- Senior Research Scientist, Senior Research Scientist, Senior Research Scientist, Diecasting Engineer, Light Metals Flagship, CSIRO Manufacturing and Materials Technology, Clayton South MDC, Victoria, 3169, AustraliaR.N. Lumley, R.G. O’Donnell, D.R. Gunasegaram & M. Givord
Corresponding author
Additional information
Manuscript submitted February 18, 2007.
Rights and permissions
About this article
Cite this article
Lumley, R., O’Donnell, R., Gunasegaram, D. et al. Heat Treatment of High-Pressure Die Castings. Metall Mater Trans A 38, 2564–2574 (2007). https://doi.org/10.1007/s11661-007-9285-4
- Published29 August 2007
- Issue DateOctober 2007
- DOIhttps://doi.org/10.1007/s11661-007-9285-4
Keywords
- Surface Blister
- HPDC Alloy
- Parallel Gage Length
- Central Gage Length
- Prolonged Solution Treatment