This introduction paper is based on the paper "Green Innovations in Foundry Production Processes of Automobile Castings" published by "Rocznik Ochrona Środowiska".
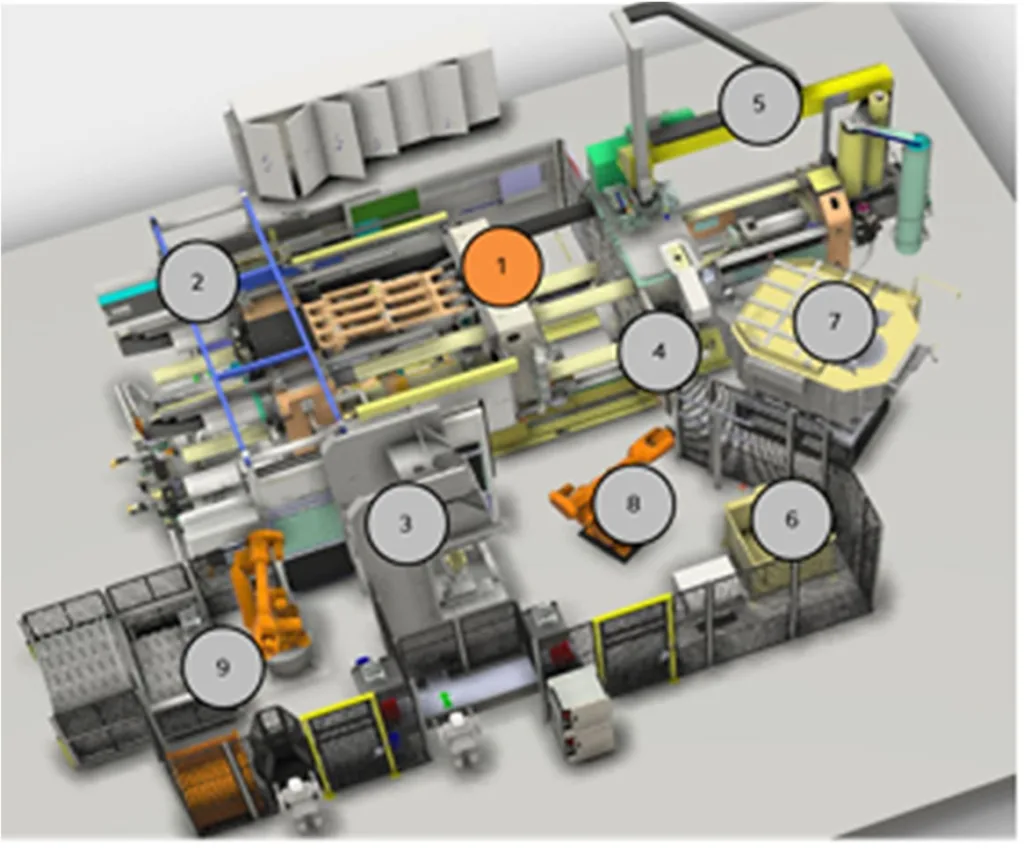
1. Overview:
- Title: Green Innovations in Foundry Production Processes of Automobile Castings
- Author: Josef Bradáč, Martin Folta, Jiří Machuta, Jiří Slabý, Michal Beneš
- Year of publication: 2024
- Journal/academic society of publication: Rocznik Ochrona Środowiska
- Keywords: foundry, innovations, energy savings, environmental impact
2. Abstract:
The paper deals with individual possibilities for energy savings and the use of chemicals in the production of automotive components. Specifically, it focuses on operating an aluminium foundry where shape-complex castings such as engine blocks and gear and clutch housings are produced using high-pressure die-casting technology. Regarding the production process, foundry operations are characterized by high energy consumption and high wastewater production. On the other hand, there is also a great potential for introducing various innovations and seeking savings. This paper aims to present selected innovative solutions throughout the foundry operation and assess their benefits in energy consumption savings, reduced wastewater production, and chemicals usage. The impact of the presented savings is financial in terms of the production of components and environmental in terms of CO2 production.
3. Introduction:
There is an increasing interest in environmental protection and reducing harmful substances across all human activities, including the industrial sector. Trends like green production, waste minimization, recovery, and comprehensive life cycle assessment (LCA) are being applied. Modern industrial production emphasizes energy savings as essential for efficient and environmentally friendly operations. Digitization and Industry 4.0 offer opportunities to increase process efficiency and reduce environmental impact through data monitoring and analysis. The automotive industry, characterized by dynamic development and innovation, demands high standardization and quality while minimizing costs and time. This necessitates constant innovation, particularly in energy-intensive areas like foundries. Foundries in the automotive sector, mainly producing engine and gearbox parts from materials like aluminium alloys using high-pressure die casting, have significant potential for cost savings and process optimization due to high energy and fuel consumption. High-pressure die casting allows high productivity for complex castings but requires precise process control, often monitored digitally. Identifying and reducing energy losses and process fluid consumption is crucial for efficiency.
4. Summary of the study:
Background of the research topic:
Foundry operations, particularly aluminium high-pressure die casting for automotive components like engine blocks and gear/clutch housings, are inherently energy-intensive, consuming significant amounts of natural gas, electricity, compressed air, and industrial water. They also generate wastewater and require chemical usage. Concurrently, there is strong industry pressure for increased environmental protection, efficiency, and cost reduction.
Status of previous research:
General trends in industrial production include implementing green production principles, waste management systems, life cycle assessments (LCA), achieving energy savings across all energy types, and leveraging digitization and Industry 4.0 for process efficiency monitoring and improvement. The automotive industry specifically focuses on innovation, standardization, quality, and cost optimization in complex manufacturing processes. Research highlights the potential for savings and optimization within the metallurgical sector, including foundries.
Purpose of the study:
This paper aims to present selected innovative solutions implemented throughout the Škoda Auto aluminium foundry operation and assess their benefits concerning energy consumption savings, reduced wastewater production, and chemicals usage. It also evaluates the financial and environmental (CO2 production) impact of these savings.
Core study:
The study focuses on specific green innovations implemented in the Škoda Auto aluminium foundry, which uses high-pressure die-casting technology. It details solutions implemented to reduce consumption of natural gas (furnace lining renovation), electricity (frequency converters on casting machines, optimized extraction systems, efficient cutting press controls, waste heat recovery from annealing furnaces, LED lighting), industrial water (micro-spraying mould treatment, optimized cooling circuits), and chemicals (automated dosing for cooling water). The paper quantifies the savings achieved through these innovations and discusses their impact on process efficiency and environmental footprint.
5. Research Methodology
Research Design:
The research presents a series of case studies detailing specific technological innovations implemented within an operational automotive foundry (Škoda Auto). It adopts a descriptive and evaluative approach, outlining the problem, the implemented solution (innovation), and the resulting benefits.
Data Collection and Analysis Methods:
Data was collected through monitoring energy and resource consumption before and after the implementation of innovations. This involved using digital monitoring systems (e.g., Power BI reports for gas consumption as shown in Fig. 2, and for water consumption monitoring mentioned in section 4.2) and direct measurement. Analysis involved comparing consumption data (e.g., Tables 1-4), calculating energy savings (kWh/year, m³/year), quantifying reductions in water and chemical use, and assessing the impact on process parameters (e.g., cycle time, efficiency) and environmental factors (CO2 reduction). The 3D Trasar online device was used for continuous water analysis and automated chemical dosing (Fig. 10).
Research Topics and Scope:
The research is scoped to the aluminium foundry production processes at Škoda Auto, specifically focusing on high-pressure die casting of automotive components (engine blocks, gearboxes, clutch housings). The topics investigated are specific implemented innovations aimed at reducing consumption of natural gas, electricity, industrial water, and chemicals, thereby improving energy efficiency and reducing environmental impact.
6. Key Results:
Key Results:
The study demonstrated significant savings through various innovations:
- Natural Gas: Renovation of furnace lining reduced annual natural gas consumption by 584 m³/year, saving costs and reducing CO2, while also shortening melting times.
- Electricity (Casting Workplace):
- Frequency converters on casting machine hydraulics saved 257,852 kWh/year (Table 2).
- Optimized extraction system control saved 35,224 kWh/year (Table 3).
- New cutting press control saved 48,738 kWh/year (calculated from Table 4: 60480 - 11742).
- Electricity (General):
- Waste heat recovery from annealing furnaces for hall heating saved 691,000 kWh/year during winter. Optimization of annealing temperature (250°C to 210°C) also contributed to reduced power consumption without affecting quality.
- Replacing conventional lighting with fluorescent and LED lamps saved 2680 MWh in 2022.
- Water and Chemicals:
- Micro-spraying technology for mould treatment eliminated industrial water use in this step (replacing 6 l water + 100 ml agent with 25 ml agent only per cycle), reduced separator consumption, decreased wastewater, shortened cycle times, and improved casting quality.
- Optimized mould cooling using innovative tempering devices with precise control and data logging improved efficiency.
- Using the 3D Trasar system for continuous monitoring and automated dosing of chemicals in demineralised cooling water allowed for precise control, timely leak detection, and reduced overall water and chemical consumption.
- Overall: Digitization and data monitoring (e.g., Power BI) were crucial for identifying potential savings, evaluating innovation impact, and minimizing losses.
Figure Name List:
- Fig. 1. The procedure of cylinder block production, from molten metal to final product
- Fig. 2. Power BI report of gas consumption in individual melting devices for a selected period
- Fig. 3. Melting furnace with an example of an inner lining of the melting space
- Fig. 4. Schematic view of individual devices in the casting workplace: (1 – high pressure casting machine, 2 – machine extraction, 3 – cutting press, 4 – data matrix code punch, 5 – foundry mould treatment manipulator, 6 – cooling bath, 7 – holding furnace, 8 – handling robot, 9 – robotic, automatic palletizing)
- Fig. 5. Control status of the casting machine hydraulic circuit before and after applying the frequency converter
- Fig. 6. Comparison of energy consumption of an extraction system, before (top) and after (bottom)
- Fig. 7. Graphical representation of the innovation concerning savings of the cutting press, before (red), after application of the innovation (green)
- Fig. 8. Situation before and after the implementation of waste heat recovery system from annealing furnaces
- Fig. 9. Transition from the old type of lighting on the left to the modern type of LED lamps on the right
- Fig. 10. Transition from manual water sampling and manual laboratory analysis to the use of the 3D Trasar online equipment for precise analysis and dosing of chemical products to be used in the cooling water
7. Conclusion:
The automotive industry increasingly emphasizes higher efficiency and lower environmental impact in both vehicle operation and production. Foundries, being energy-intensive and handling high-temperature materials, face challenges in meeting these goals but possess significant potential for energy savings. Implementing effective innovations requires correct identification of potential, benefit evaluation (including financial aspects and downtime), and careful planning. The solutions presented in this paper (furnace lining renovation, energy efficiency measures in casting workplaces, waste heat recovery, lighting upgrades, micro-spraying, optimized water treatment) represent individual steps towards more sustainable and environmentally friendly component production, contributing to energy savings and CO2 reduction. Digitization and data evaluation are highlighted as important drivers for monitoring processes, identifying losses, and maximizing the impact of innovations. The paper recommends the use of 100% micro-spraying for moulds and daily monitoring/reduction of all process substance leakages as measures with substantial environmental benefits, not necessarily requiring large initial investments.
8. References:
- Bajdur, W., Zielińska, A., Gronba-Chyła, A. (2023). Product Life Cycle Assessment (LCA) as a Tool for Environmental Management. Rocznik Ochrona Środowiska, 25(1), 389-398.
- Chamier-Gliszczynski, N., Krzyzynski, T. (2005). On modelling three-stage system of receipt and automotive recycling. REWAS'04, Global Symposium on Recycling, Waste Treatment and Clean Technology 2005, 2813-2814, Madrid, Spain, 26-29 September 2004, Conference Paper, ISBN: 8495520060.
- Chamier-Gliszczyński, N. (2012). Modeling system mobility in urban areas. Congress Proceedings, CLC 2012: Carpathian Logistics Congress, 501-508, 111467.
- Espuny, M., Costa, A.C.F., Reis, J.S.M., Barbosa, L.C.F.M, Snatos, R.C.G., Oliveira, O.J. (2022). Identification of the Elements and Systematisation of the Pillars of Solid Waste Management. Quality Innovation Prosperity, 26(2), 147-169.
- Gabrylewicz, I., Lenort, R., Wędrychowski, M., Krupa, P., Woźniak, W. (2021). Environmental Loads Resulting from Manufacturing Technology. Rocznik Ochrona Srodowiska, 23, 613-628. https://doi.org/0.54740/ros.2021.043
- Ghadge, A., Mogale, D.G., Bourlakis, M., Maiyar, L.M., Moradlou, H. (2022). Link between Industry 4.0 and green supply chain management: Evidence from the automotive industry. Computers & Industrial Engineering, 169(1), 1-14.
- Ignatowicz, K., Piekarski, J., Kogut, P. (2021). Influence of selected substrate dosage on the process of biogas installation start-up in real conditions. Energies, 14(18), 5948. https://doi.org/10.3390/en14185948
- Jenek, M., Ociepa, M., Woźniak, W., Vilmová, Š., Švecová, E. (2022). Rocznik Ochrona Srodowiska, 24, 360-370. https://doi.org/10.54740/ros.2022.025
- Kostrzewski, M., Chamier-Gliszczynski, N., Królikowski, T. (2020). Selected reflections on formal modeling in Industry 4.0. Procedia Computer Science, 176, 3293-3300. https://doi.org/10.1016/j.procs.2020.09.118
- Kuczynski, W., Kaminski, K., Znaczko, P., Chamier-Gliszczynski, N., Piatkowski, P. (2021). Features and Thermal Efficiency of Flat-Plate Solar Collectors. Energies, 14(2), 261. https://doi.org/10.3390/en14020261
- Lenort, R., Baran, J., Wysokinski, M., Golasa, P., Bienkowska-Golasa, W., Golonko, M., Chamier-Gliszczynski, N. (2019). Economic and Environmental Efficiency of the Chemical Industry in Europe in 2010-2016. Rocznik Ochrona Srodowiska, 21(2), 1393-1404.
- Menti, F., Romero, D., Jacobsen, P. (2023). A technology assessment and implementation model for evaluating socio-cultural and technical factors for the successful deployment of Logistics 4.0 technologies. Technological Forecasting and Social Change, 190(1), 1-17.
- Mir, M., Llach, J., Casadesus, M. (2022). Degree of Standardization and Innovation Capability Dimensions as Driving Forces for Innovation Performance. Quality Innovation Prosperity, 26(2), 1-20.
- Nawrocki, W., Stryjski, R., Woźniak, W., Jakubowski, J. (2018). Improving the quality of manufacturing processes in Toyota motor manufacturing, Poland. Proceedings of the 31st International Business Information Management Association Conference, IBIMA 2018: Innovation Management and Education Excellence through Vision 2020, 143853, 5931-5945.
- Obzina T., Merta V., Folta M., Bradáč J., Beňo J., Novohradsaká N., Gawronová M., Kroupová I., Lichý P., Radkovský F., Janovská K., Vasková I., Drobíková K., Nguyenová I. Technological and Quality Aspects of the Use of Innovative Inorganic Binders in the Production of Castings. Metals, 11(11), 1-13.
- Orłowska, M. (2022). Saving Energy – a Smart, Ecological and Necessary Trend. Rocznik Ochrona Środowiska, 24(1), 472-480.
- Saetta, S., Caldarelli, V. (2020). Lean production as a tool for green production: the green foundry case study. Procedia Manufacturing, 42(1), 498-502.
- Samtleben, S., Schleich, CH., Chenk, M. (2021). Identifying energy flexible manufacturing layouts in a light metal foundry. Procedia CIRP, 104(1), 1589-1594.
- Sąsiadek, M., Niedziela, M., Woźniak, W., Jachowicz, T., Mikušová, N. (2023). A New Effective Algorithm for Mechanical Assembly Sequence Planning. Advances in Science and Technology Research Journal, 17(5), 56-67. https://doi.org/10.12913/22998624/171271
- Sharma, M., Luthra, S., Joshi, S., Kumar, A., Akshat, J. (2023). Green logistics driven circular practices adoption in industry 4.0 Era: A moderating effect of institution pressure and supply chain flexibility. Journal of Cleaner Production, 383(1), 1-12.
- Scharf, S., Sander, B., Kujath, M., Richter, H., Riedel, E, Stein, N., Felde, J.T. (2022). Sustainability potentials of an innovative technology and plant system in non-ferrous foundries. Procedia CIRP, 105(1), 758-763.
- Scharf, S., Sander, B., Kujath, M., Richter, H., Riedel, E., Stein, N., Felde, J.T. (2021). Foundry 4.0: An innovative technology for sustainable and flexible process design in foundries. Procedia CIRP, 98(1), 73-78.
- Staniuk, W., Staniuk, M., Chamier-Gliszczynski, N., Jacyna, M., Klodawski, M. (2022). Decision-Making under the Risk, Uncertainty and COVID-19 Pandemic Conditions Applying the PL9A Method of Logistics Planning-Case Study. Energies, 15(2), 639. https://doi.org/10.3390/en15020639
- Sumasto, M., Arliananda, Almansuri, F., Aisyah, S., Purwojatmiko, B.H., (2023). Enhancing Automotive Part Quality in SMEs through DMAIC Implementation: A Case Study in Indonesian Automotive Manufacturing. Quality Innovation Prosperity, 27(3), 57-74.
- Szajna, A., Kostrzewski, M., Ciebiera, K., Stryjski, R., Woźniak W. (2021). Application of the deep CNN-based method in industrial system for wire marking identification. Energies, 14(12), 3659. https://doi.org/10.3390/en14123659
- Ťavodová, M., Vargová, M., Stančeková, D., Hajdúch, A., Mrázik, J. (2022). Evaluation of the Influence of Process Parameters on the Mechanical Properties of Castings during High Pressure Die Casting. Manufacturing Technology, 22(6), 764-770.
9. Copyright:
- This material is a paper by "Josef Bradáč et al.". Based on "Green Innovations in Foundry Production Processes of Automobile Castings".
- Source of the paper: https://doi.org/10.54740/ros.2024.050
This material is summarized based on the above paper, and unauthorized use for commercial purposes is prohibited.
Copyright © 2025 CASTMAN. All rights reserved.