This introductory paper is the research content of the paper "Features and Vehicle Application of Heat Resistant Die Cast Magnesium Alloy" published by SEI TECHNICAL REVIEW.
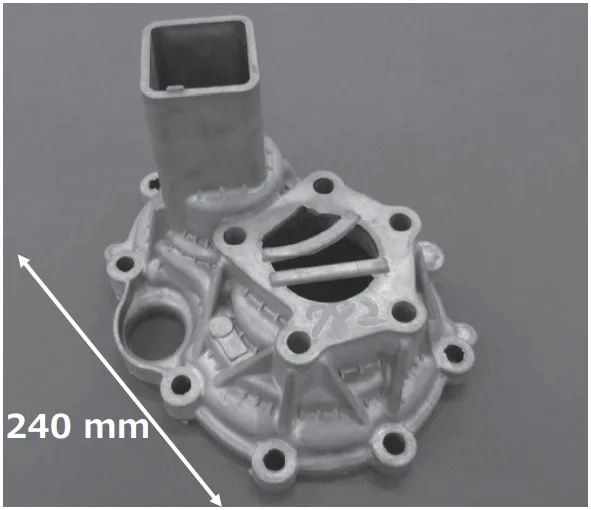
1. Overview:
- Title: Features and Vehicle Application of Heat Resistant Die Cast Magnesium Alloy
- Author: Manabu MIZUTANI, Katsuhito YOSHIDA, Nozomu KAWABE, and Seiji SAIKAWA
- Publication Year: 2019
- Publishing Journal/Academic Society: SEI TECHNICAL REVIEW
- Keywords: creep-resistant, heat-resistant, magnesium alloy, die casting, weight reduction
2. Abstracts / Introduction
Magnesium (Mg) alloys are desirable for lightweighting applications, particularly in automotive powertrains. However, commonly used alloys like AZ91 and AM60 suffer from poor creep resistance at elevated temperatures (150°C). This paper introduces a newly developed high-temperature creep-resistant Mg alloy (AJX931) that overcomes the limitations of conventional creep-resistant Mg alloys, such as low castability and inferior recyclability.
3. Research Background:
Background of the Research Topic:
Magnesium is the lightest structural metal, making it attractive for weight reduction in automotive components.
Status of Existing Research:
Existing alloys like AZ91D, AM60, and AM50 have limitations:
- AZ91 and AM60 exhibit poor creep resistance at 150°C due to the weakening of β-phase precipitates (Mg17Al12) at temperatures above 120°C.
- Existing heat-resistant alloys achieve improved high-temperature performance by reducing Al content and adding elements like Si, REs, Ca, and Sr. However, these additions often compromise castability and recyclability.
Necessity of the Research:
There is a need for a Mg alloy that combines high-temperature creep resistance with good castability and recyclability for use in automotive powertrain components, where weight reduction, heat resistant is cruicial.
4. Research Purpose and Research Questions:
Research Purpose:
To develop a heat-resistant magnesium alloy that overcomes the challenges associated with existing heat-resistant magnesium alloys, particularly concerning castability and recyclability.
Key Research:
-How to design an alloy composition that minimizes β-phase precipitation while maintaining good castability, corrosion resistance, and recyclability.
-Evaluate the mechanical properties, microstructure, heat resistance, and corrosion resistance of the newly developed alloy.
-Comparison between new alloy and Existing Alloys.
5. Research Methodology
Research Design:
Experimental alloy design and comparative analysis.
Data Collection Method:
- Die casting of samples using a 650t cold chamber die-casting machine.
- Scanning Electron Microscopy (SEM) and Field Emission SEM (FE-SEM) for microstructural analysis.
- Energy-Dispersive X-ray Spectroscopy (EDX) for elemental analysis.
- X-ray Diffraction (XRD) for phase identification.
- Tensile testing for mechanical property evaluation.
- Bolt-load retention (BLR) testing at 150°C for creep resistance evaluation.
- Salt spray testing (JIS Z 2371) for corrosion resistance evaluation.
- Recyclability evaluation through remelting and impurity analysis.
- Casting crack evaluation.
Analysis Method:
- Quantitative analysis of microstructural features.
- Comparison of mechanical properties, BLR, and corrosion resistance between the new alloy (AJX931) and existing alloys (AS31, AE44, MRI153M, AZ91).
- Assessment of casting crack propensity.
- Analysis of inclusions during recycling.
Research Subjects and Scope:
The research focused on the development and characterization of a new Mg alloy (AJX931) with a composition designed to optimize heat resistance, castability, and recyclability. The scope included comparing AJX931 with commercially available heat-resistant Mg alloys.
6. Main Research Results:
Key Research Results:
- AJX931, with a nominal composition of approximately Mg-9Al-1Ca-3Sr, was successfully developed.
- AJX931 exhibits significantly improved bolt-load retention (BLR) compared to AZ91 and comparable or superior BLR to AS31 and MRI153M.
- AJX931 shows good castability, with lower crack formation than AS31 and MRI153M.
- AJX931 demonstrates superior 0.2% yield strength (156 MPa) compared to AS31 and AE44.
- AJX931 exhibits good corrosion resistance in salt spray testing.
- AJX931 shows potential for easier recycling compared to RE-containing alloys like AE44.
Analysis of presented data:
- Table 1: Summarizes the effects of various alloying elements on the properties of Mg alloys.
- Table 2: Presents the chemical compositions of the evaluated alloys (AJX931, AS31, AE44, MRI153M).
- Figure 2: Shows the microstructure of AJX931, revealing α-Mg primary phase, precipitates, and eutectic structures.
- Figure 3: Presents FE-SEM and EDX analysis, identifying Al2Sr, Al4Sr, and C15-Al2Ca or C36-(Mg, Al)2Ca compounds.
- Figure 4: Shows XRD results, confirming the presence of Al-Sr and Al-Ca compounds and the absence of β-phase.
- Figure 6: Compares the BLR of AJX931 with conventional heat-resistant alloys, demonstrating its superior performance.
- Figure 7: Shows the evaluation results of castability, indicating lower crack formation in AJX931 compared to AS31 and MRI153M.
- Figure 10: Compares the 0.2% yield strength, highlighting AJX931's superior strength.
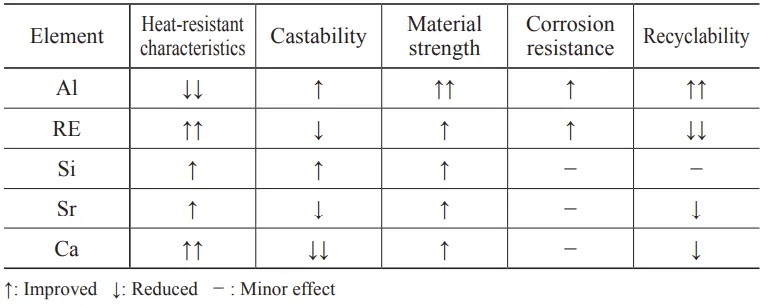
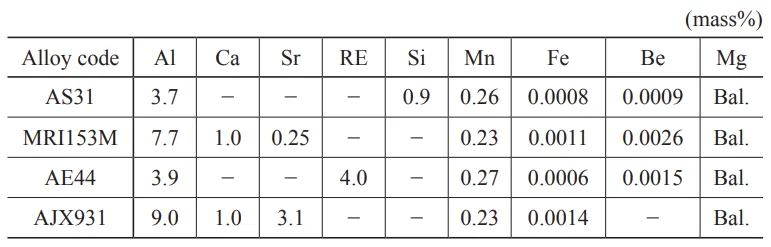
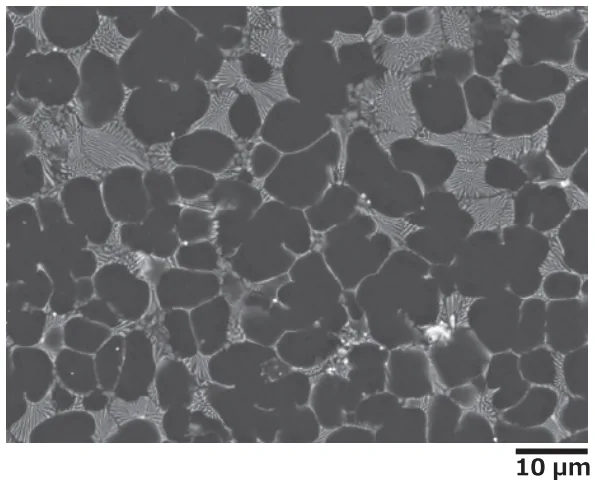
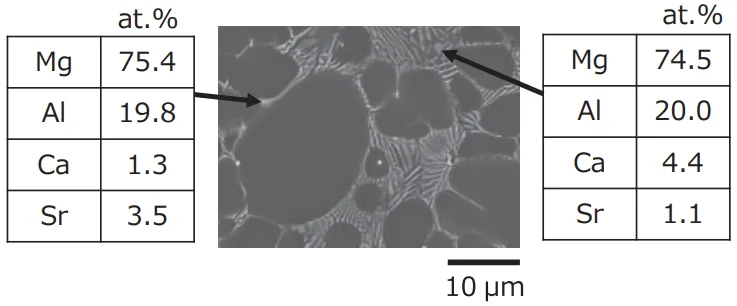
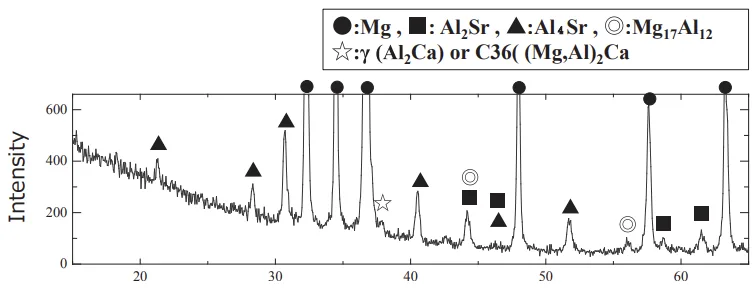
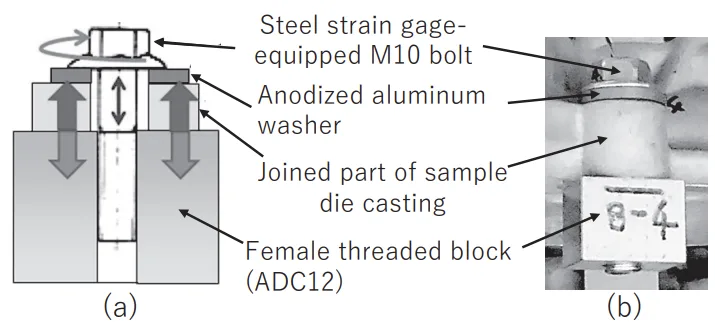
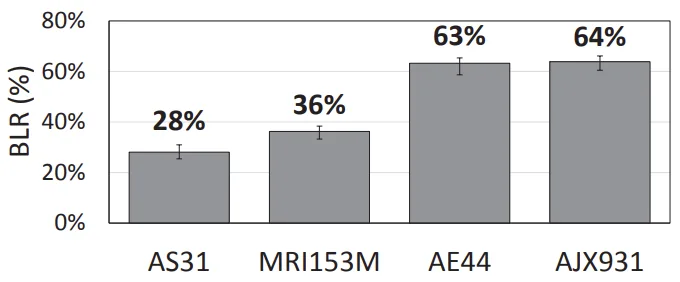
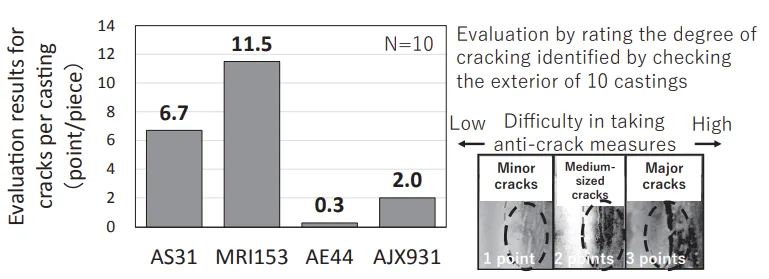
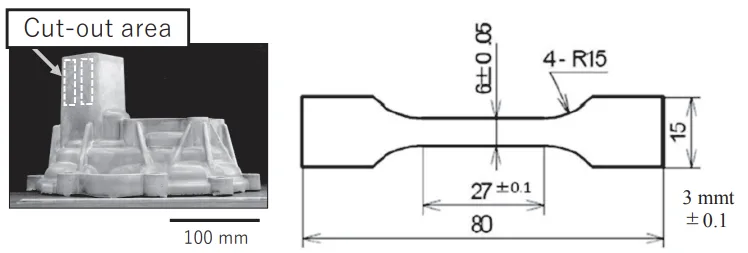
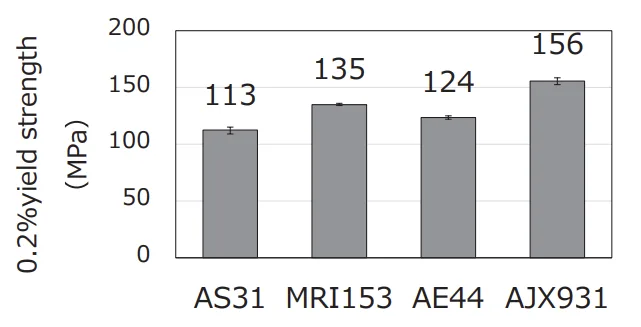
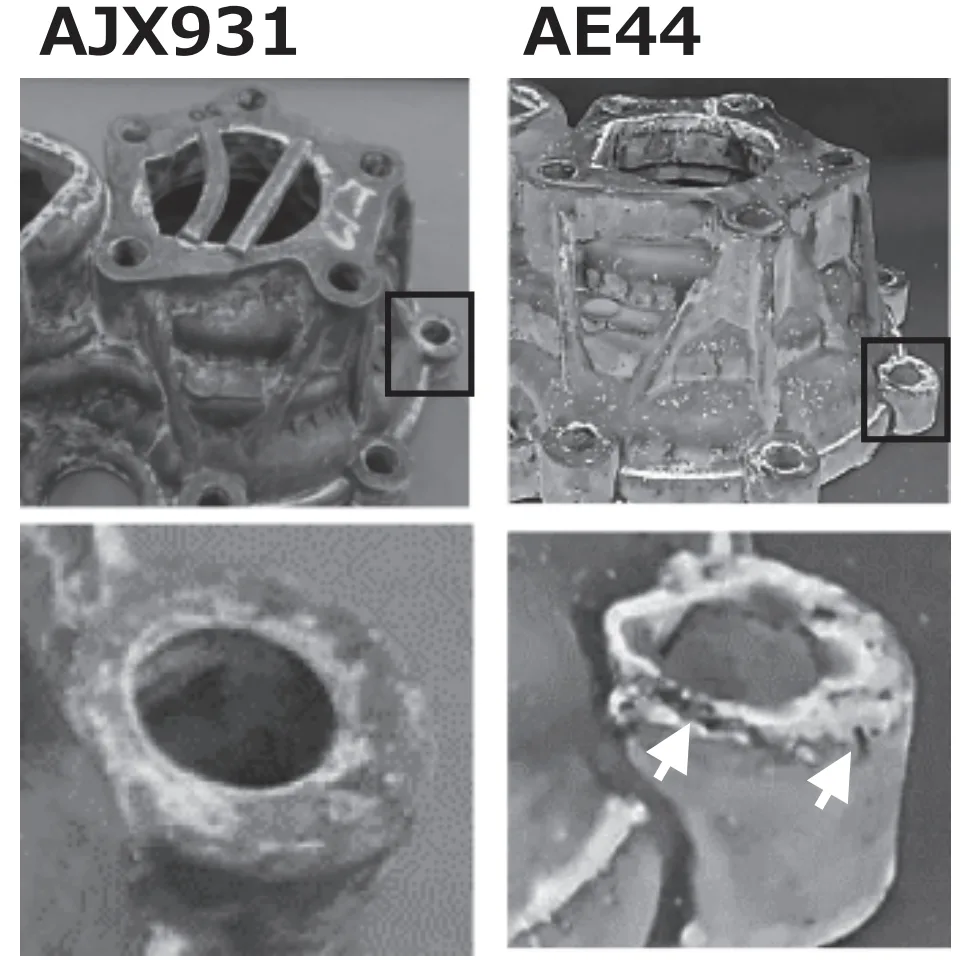
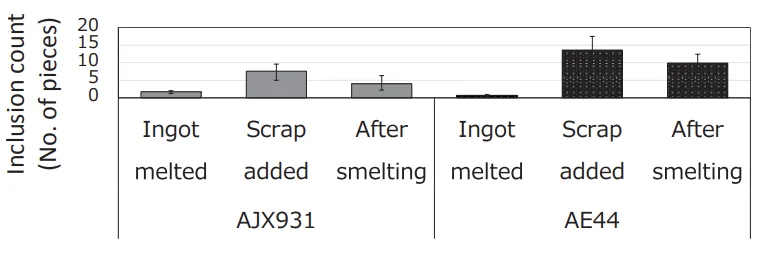
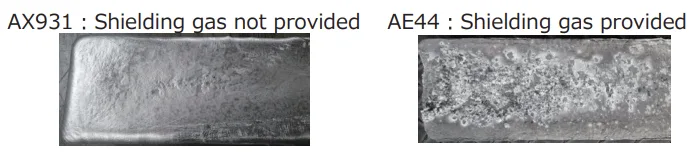
Figure Name List:
- Fig. 1. Die-cast sample shape
- Fig. 2. Microstructure of AJX931 die casting
- Fig. 3. FE-SEM-based EDX analysis of AJX931 die casting
- Fig. 4. XRD measurement of AJX931 die casting
- Fig. 5. Measurement method for remaining axial force
- Fig. 6. BLR of conventional heat-resistant alloys and newly developed alloy
- Fig. 7. Evaluation of castability for die casting (casting cracks)
- Fig. 8. Microstructures of die-cast alloys
- Fig. 9. Test specimen cut-out area and shape of tensile test specimen
- Fig. 10. 0.2% yield strength comparison of existing heat-resistant alloys and newly developed alloy
- Fig. 11. Exterior of samples subjected to 200 h salt spray testing
- Fig. 12. Evaluation results for amount of inclusions
- Fig. 13. Exterior of ingots cast from smelted molten metal
7. Conclusion:
Summary of Key Findings:
The newly developed AJX931 alloy demonstrates a superior combination of heat resistance, castability, mechanical strength, corrosion resistance, and recyclability compared to conventional heat-resistant Mg alloys.
Academic Significance of the Study:
This research demonstrates a novel alloy design approach for heat-resistant Mg alloys, minimizing β-phase precipitation through controlled additions of Sr and Ca, while maintaining a relatively high Al content for improved castability and recyclability.
Practical Implications:
AJX931 is a promising candidate for lightweighting applications in automotive powertrain components, offering potential weight reduction and improved performance at elevated temperatures.
Limitations of the Study and Areas for Future Research:
The paper mentions that dross formation during melting of AJX931 needs further investigation, although it is easier to handle than AE44. Future research will focus on exploring the practical applications of AJX931 in transportation vehicle parts.
8. References:
- (1) S. Kamado, Y. Kojima, Materia Japan, 38 (1999) 4
- (2) S. Saikawa, Journal of Japan Institute of Light Metals, 60 (2010) 11
- (3) S. Takeda, Materia Japan, 53 (2014) 12
- (4) I. Nakatsugawa, Materia Japan, 38 (1999) 4
- (5) H. Kawabata, N. Nishino, T. Aikawa, K. Otake, Y. Genma, Journal of Japan, 60 (2010) 11
- (6) The Japan Magnesium Association web site (2013)
9. Copyright:
- This material is MIZUTANI's paper: Based on "Features and Vehicle Application of Heat Resistant Die Cast Magnesium Alloy".
- Paper Source: Not provided in the text. (No DOI was included in the provided OCR text.)
This material was created to introduce the above paper, and unauthorized use for commercial purposes is prohibited.
Copyright © 2025 CASTMAN. All rights reserved.