The content of this introduction paper is based on the article "Efficiency improvement of induction motors based on rotor slot and tooth structures" published by Journal of Intelligent Systems and Control.
![Figure 1. Efficiency levels of electric motor with the output powers [5]](https://castman.co.kr/wp-content/uploads/image-1806-1024x489.webp)
1. Overview:
- Title: Efficiency improvement of induction motors based on rotor slot and tooth structures
- Author: Hung Bui Duc, Chi-Phi Do, Manh Doan Cong, Vuong Dang Quoc
- Year of publication: 2023
- Journal/academic society of publication: Journal of Intelligent Systems and Control
- Keywords: Induction motors; Optimization design; Sequential quadratic algorithm; Fmincon function; Efficiency
2. Abstract:
Due to simple structure, easy maintenance and low cost, induction motors (IMs) are widely applied in various industries, accounting for 60-80% alternating current (AC) motors used in industry. However, the efficiency of IMs is very low, and even small improvement can result in significant energy saving. For instance, 1% efficiency increase saves billions of kilowatt hours. Therefore, this paper aimed to improve the efficiency of IMs, thus reducing energy consumption and greenhouse gas emissions. For an IM with 7.5kW rated power and IE3 energy efficiency, the efficiency is improved by making various changes. Sequential quadratic algorithm and fmincon function are proposed to change the rotor slot and teeth structures, realizing nearly 91% motor efficiency, which is a significant improvement over the original efficiency. It is worth noting that improving the efficiency of IMs saves a lot of energy, especially in cases where IMs account for a large proportion of AC motors.
3. Introduction:
Induction motors (IMs) are the most prevalent type of electric motors in the industrial sector due to their cost-effectiveness, ease of maintenance, and reliability. However, a significant drawback of IMs is their low efficiency, which contributes substantially to operational costs. Losses in IMs are categorized into rotor and stator copper losses, core losses, friction and windage losses, and other losses. While efficiency varies from 70% to 95% depending on power, designing for maximum efficiency at rated values is crucial. Energy-efficient IMs exhibit higher power factors and efficiencies, especially at high speeds. The development of highly efficient IMs is critical for reducing energy consumption in industrial applications. Despite their advantages, the low efficiency of IMs necessitates improvements to enhance overall energy efficiency and reduce costs.
4. Summary of the study:
Background of the research topic:
Induction motors consume a significant portion of electrical energy in the industrial sector. Their inherent low efficiency, despite their widespread use, presents a major opportunity for energy savings. Even a marginal increase in IM efficiency can lead to substantial reductions in energy consumption and greenhouse gas emissions.
Status of previous research:
Prior research has explored various methods to enhance IM performance. These include control strategies based on slip power recovery, material changes in rotor cages (e.g., copper and premium steel), modifications to stator and rotor slot shapes, and control techniques with constant frequency. Finite Element Method (FEM) coupled with genetic algorithms and high magnetic flux materials have also been investigated. Furthermore, approaches for variable speed IM drives and swarm optimization techniques for efficiency evaluation have been developed.
Purpose of the study:
This study aims to improve the efficiency and reduce the weight of a 7.5kW, IE3 efficiency class IM. The primary objective is to optimize the rotor slot and teeth structures to achieve a significant enhancement in motor efficiency.
Core study:
The core of this study involves the application of the Sequential Quadratic Algorithm (SQA) and fmincon function within the Matlab environment to optimize the rotor slot and teeth structures. This optimization process seeks to maximize motor efficiency. The calculation process of the IM is depicted in Figure 2, illustrating the design module, control module, and database interaction for parameter optimization.
5. Research Methodology
Research Design:
The methodology employs an optimization function (fmincon function) within Matlab. The calculation process, illustrated in Figure 2, involves a design module, control module, and database. The design module defines the parameters of the proposed IM, while the control module performs optimization calculations based on the database and design module to maximize efficiency under specified constraints.
Data Collection and Analysis Methods:
The study utilizes computational analysis and optimization algorithms. The fmincon function is used to achieve a convergent solution, targeting two objectives: maximizing efficiency and minimizing the weight of the magnetic circuit. Optimal parameters include rotor teeth diameters (outer and inner), rotor teeth height, and the number of rotor slots. Constraints are applied to factors such as starting current and torque.
Research Topics and Scope:
The research focuses on optimizing the rotor slot and teeth structures of a 7.5kW IE3 induction motor. The optimization process considers various steel types to assess the impact on efficiency and motor characteristics. The scope includes analyzing the efficiency, weight, starting current, starting torque, and maximum torque of the optimized motor compared to a conventional design.
6. Key Results:
Key Results:
The optimization process resulted in a significant efficiency improvement, reaching nearly 91% for the M235-35A steel type, up from a reference efficiency of 89.71%. This optimized efficiency aligns with the IE3 motor class. Figure 5 and Table 3 show the comparison of efficiency and weight for different steel types, demonstrating that the optimized motor achieves higher efficiency with a reduced weight (28kg vs 29kg for M235-35A). The starting current multiple remained within acceptable limits (Figure 6, Table 4), and the starting torque multiple was improved, exceeding the initial constraint condition (Figure 7, Table 5). The maximum torque multiple also saw a slight increase (Figure 8, Table 6). Figure 9 and Figure 10 illustrate the mechanical and current characteristics, and output power characteristics, respectively, of the conventional and optimized motors, validating the improved performance.
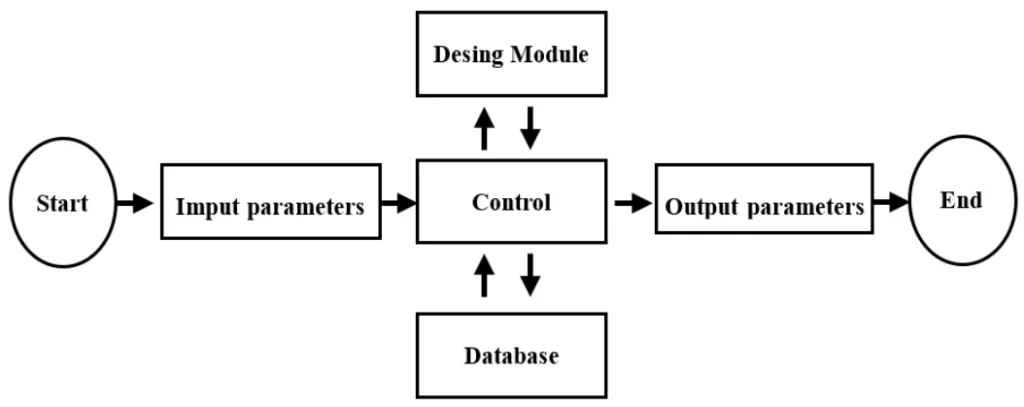
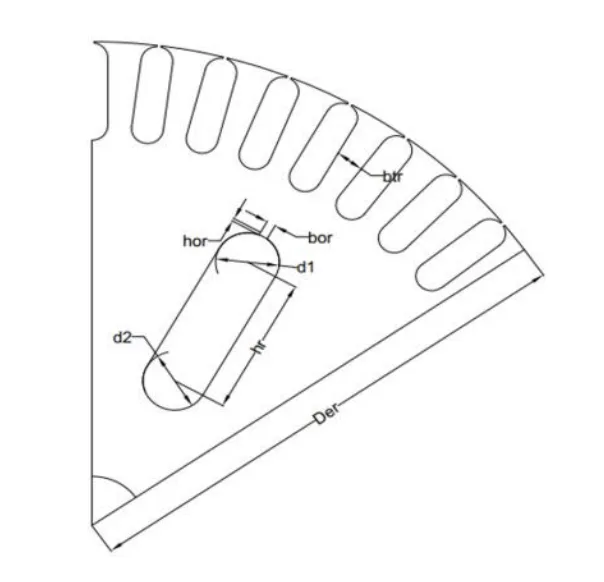

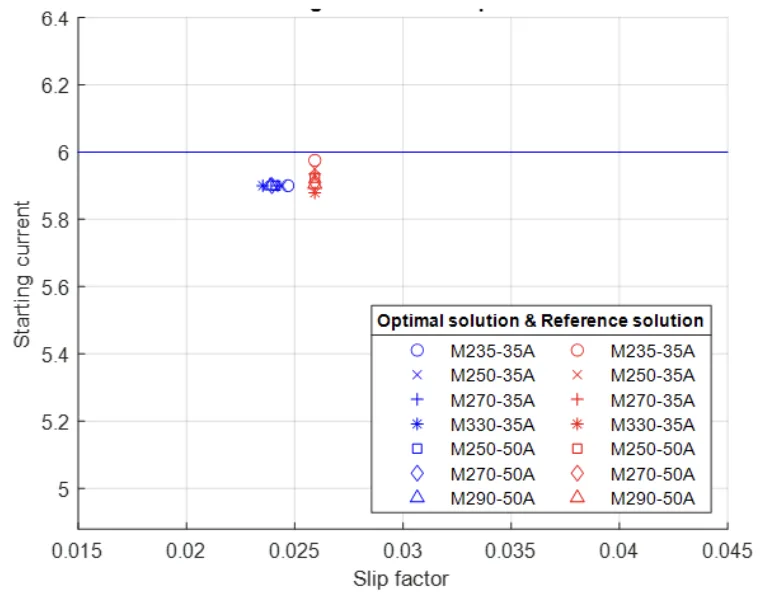
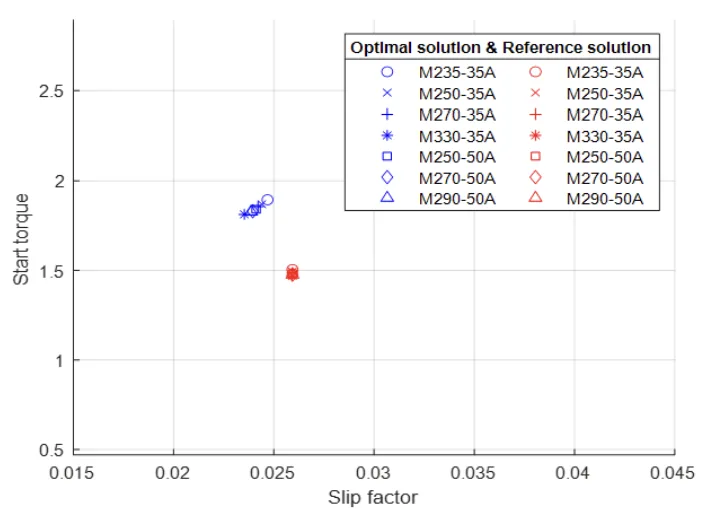
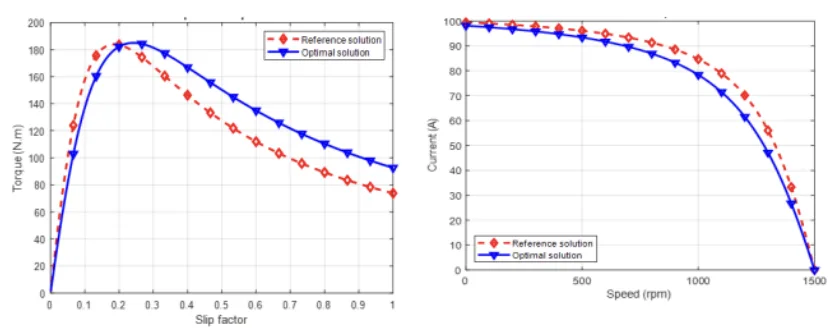
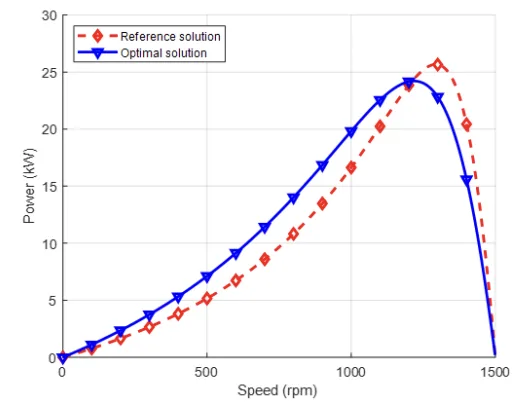
Figure Name List:
- Figure 1. Efficiency levels of electric motor with the output powers [5]
- Figure 2. Calculation process of the IM
- Figure 3. Structure of rotor slots and tooth
- Figure 4. Algorithm for optimazation design
- Figure 5. Comparison of efficiency between conventional and optimal solutions with different steel types
- Figure 6. Conventional and optimal starting current multiples with different steel types
- Figure 7. Conventional and optimal starting torque multiples with different steel types
- Figure 8. Conventional and optimal maximum torque multiples with different steel types
- Figure 9. Mechanical and current characteristics of conventional and optimal motors
- Figure 10. Output power characteristic of conventional and optimal solutions
7. Conclusion:
This study successfully demonstrated a novel approach to enhance the efficiency and reduce the weight of induction motors by optimizing rotor slot and teeth structures. The optimized design achieved a significant efficiency increase, reaching 90.16% for M235-35A steel, consistent with the IE3 motor class. The optimized motor also maintained acceptable starting current and improved starting and maximum torque characteristics. The presented mechanical, current, and output power characteristics validate the proposed method. The findings of this research offer valuable insights for manufacturers and designers seeking to leverage optimization techniques to improve IM efficiency.
8. References:
- [1] P. Waide and C. U. Brunner, "Energy-Efficiency Policy Opportunities for Electric Motor-Driven Systems," In IEA Energy Papers, OECD Publishing, 2011.
- [2] G. Singh, T. Kumar, and V. Naikan, "Efficiency monitoring as a strategy for cost effective maintenance of induction motors for minimizing carbon emission and energy consumption," Reliability Eng. Syst. Safety., vol. 184, pp. 193-201, 2019. https://doi.org/10.1016/j.ress.2018.02.015.
- [3] R. L. J. Sprangers, J. J. H. Paulides, K. O. Boynov, J. Waarma, and E. A. Lomonova, "Design and optimization tools for high-efficiency three-phase induction motors," In 2013 15th European Conference on Power Electronics and Applications, Lille, France, pp. 1-10, 2013. https://doi.org/10.1109/EPE.2013.6634672.
- [4] G. S. Grewal and B. S. Rajpurohit, "Efficient energy management measures in steel industry for economic utilization," Energy Rep., vol. 2, pp. 267-273, 2016. https://doi.org/10.1016/j.egyr.2016.10.003.
- [5] C. Ioannis, K. Yannis, and S. Franck, "Effect of Rotor Bars Shape on the Single-Phase Induction Motors Performance: An Analysis toward Their Efficiency Improvement," Energies, vol. 5, Article ID: 717, 2022. https://doi.org/10.3390/en15030717.
- [6] A. Sengupta, "Improvement of Efficiency of a Three-Phase Induction Motor Using Robust Control," In Advances in Power Systems and Energy Management, Springer, Singapore, vol. 436, 2018. https://doi.org/10.1007/978-981-10-4394-9_19.
- [7] E. Chiricozzi, F. Parasiliti, and M. Villani, "New materials and innovative technologies to improve the efficiency of three-phase induction motors A case study," In Proceedings Of The International Conference On Electrical Machines, Krakow, Poland, vol. 273, 2004.
- [8] M. Sundaram and P. Navaneethan, "On the influence of stator slot shape on the energy conservation associated with the submersible induction motors," Am. J. Appl. Sci., vol. 8, no. 4, pp. 393-399, 2011. https://doi.org/10.3844/ajassp.2011.393.399.
- [9] H. C. Chuang, G. D. Li, and C. T. Lee, "The efficiency improvement of AC induction motor with constant frequency technology," Energy, vol. 174, pp. 805-813, 2019. https://doi.org/10.1016/j.energy.2019.03.019.
- [10] M. Cunkas, "Intelligent design of induction motors by multiobjective fuzzy genetic algorithm," J. Intell. Manuf., vol. 21, no. 4, pp. 393-402, 2010. https://doi.org/10.1007/s10845-008-0187-0.
- [11] F. Kentli, "A survey on design optimization studies of induction motors during the last decade," Istanbul Univ. J. Electr. Electron. Eng., vol. 9, no. 2, pp. 969-975, 2009.
- [12] S. Manoharan, N. Devarajan, S. M. Deivasahayam, and G. Ranganathan, "Review on efficiency improvement in squirrel cage induction motor by using DCR technology," J. Electr. Eng., vol. 60, no. 4, pp. 227-236, 2009.
- [13] T. Aho, J. Nerg, and J. Pyrhönen, "The Effect of the Number of Rotor Slits on the Performance Characteristics of MediumSpeed Solid Rotor Induction Motor," In 3rd IET International Conference on Power Electronics, Machines and Drives, Dublin, pp. 515-519, 2006. https://doi.org/10.1049/cp:20060162.
- [14] K. B. Mohanty and M. Singh, "Performance improvement of induction motor drive using feedback linearization and fuzzy torque compensator with RTDS implementation," Int. Rev. Electr. Eng., vol. 7, pp. 4374-4382, 2012.
- [15] B. Dandil and S. Tuncer, "Four-quadrant control of multilevel inverter fed induction motor drives," J. Sci. Ind. Res., vol. 67, pp. 688-696, 2008.
- [16] K. R. Kumar, D. Sakthibala, and S. Palaniswami, "Efficiency optimization of induction motor drive using soft computing techniques," Int. J. Comput. Appl., vol. 3, no. 1, pp. 6-12, 2010. https://doi.org/10.5120/703-986.
- [17] H. B. Duc, D. B. Minh, and V. D. Quoc, "Analytical and FEM methods for line start permanent magnet synchronous motor of 2.2kW," J. Eur. Syst. Autom., vol. 55, no. 6, pp. 715-721, 2022. https://doi.org/10.18280/jesa.550603.
- [18] I. Boldea and S. A. Nasar, The Induction Machines Design Handbook, CRC Press, 2009. https://doi.org/10.1201/9781315222592.
- [19] V. P. Sakthivel and S. Subramanian, "On-site efficiency evaluation of three-phase induction motor based on particle swarm optimization," Energy, vol. 36, pp. 1713-1720, 2011. https://doi.org/10.1016/j.energy.2010.12.057.
- [20] P. Matic and S. N. Vukosavic, "Voltage angle direct torque control of induction machine in field-weakening regime," IET Electr. Power Appl., vol. 5, no. 5, pp. 404-414, 2011. https://doi.org/10.1049/iet-epa.2010.0214.
9. Copyright:
- This material is a paper by "Hung Bui Duc, Chi-Phi Do, Manh Doan Cong, and Vuong Dang Quoc". Based on "Efficiency improvement of induction motors based on rotor slot and tooth structures".
- Source of the paper: https://doi.org/10.56578/jisc020102
This material is summarized based on the above paper, and unauthorized use for commercial purposes is prohibited.
Copyright © 2025 CASTMAN. All rights reserved.