This article introduces the paper "[Original Paper Title]" focusing on die casting technology for welding applications, originally published in the Journal of the Korea Foundry Society.
1. Overview:
- Title: Die Casting Technology for Welding Application (용접 가능한 알루미늄합금 다이캐스트기술)
- Author: Takao Kaneuchi (金内良夫)
- Publication Year: 2010
- Publishing Journal/Academic Society: Journal of the Korea Foundry Society (한국주조공학회지), Vol. 30, No. 3
- Keywords: 유럽, 독일, 다이캐스, 용접, 차체, 프레임, 진공, 이형제, 동향. (Europe, Germany, Die casting, Welding, Car body, Frame, Vacuum, Release agent, Trend)
2. Research Background:
- Social/Academic Context of the Research Topic: Die casting is widely recognized as a high-productivity casting method. Its rapid solidification process using cooled molds allows for high-speed production and intricate shapes, even with undercuts. The process also ensures high dimensional accuracy and mass production capabilities without the need for cores in many cases. However, the size of die-cast products is limited by the die casting machine capacity. For larger components, alternative methods like using extrusions, bent sheet metal, or assembling multiple die-cast parts are typically employed. These approaches often lead to increased part count, assembly labor, and weight, negating some of the benefits of die casting. There is a growing demand to expand the application of die casting to larger and more complex structures, particularly in industries like automotive, where reducing component count and enhancing structural rigidity are crucial.
- Limitations of Existing Research: A significant challenge in utilizing die-cast components, especially those made from common die casting alloys, is their weldability. General die-cast materials are considered difficult to weld and subject to T6 heat treatment due to gas porosity entrapped during the casting process. During T6 heat treatment, the elevated temperatures in the solution treatment phase cause the entrapped gas to expand, leading to surface blisters and internal shrinkage porosity expansion. Welding, which involves re-melting and solidifying a portion of the material, exacerbates this issue. Excessive gas content can result in blisters in the heat-affected zone during welding, blowholes within the weld bead, and pinholes on the weld bead surface. Furthermore, oxides and inclusions present within the die-cast material can surface during re-melting, further degrading the weld bead quality.
- Necessity of the Research: To overcome the limitations associated with welding conventional die-cast materials, research and development of die casting technologies that enable welding are essential. The paper highlights the increasing trend, particularly in Europe, towards adopting die-cast components in automotive body frames and structures. This trend is driven by the advantages of die casting in reducing part count, assembly costs, and weight. Therefore, establishing reliable die casting technologies that produce weldable aluminum alloy components is crucial for expanding the application of die casting and meeting the evolving demands of industries seeking lightweight and high-performance structural solutions. The research aims to address the challenges of gas porosity in die-castings and explore process optimizations to achieve weldable aluminum die-cast products.
3. Research Purpose and Research Questions:
- Research Purpose: The primary purpose of this research is to investigate and demonstrate die casting technology capable of producing weldable aluminum alloy components. The focus is on minimizing gas entrapment during the die casting process to facilitate successful welding and explore practical methods for ensuring weld quality in mass production. The paper specifically introduces and evaluates the HIVAC-V (Hitachi Vacuum Casting - Vacuum) method as a solution to achieve weldable die-cast products.
- Key Research Questions:
- What are the critical process parameters in die casting that significantly influence the amount of gas entrapped within the cast product and subsequently affect its weldability?
- How can the die casting process, specifically the HIVAC-V method, be optimized to minimize gas porosity in aluminum alloy die-castings to a level suitable for welding?
- What are effective and practical quality assurance methods that can be implemented in a mass production environment to guarantee the weldability of die-cast components?
- How do different types and application rates of release agents and plunger lubricants affect the gas content and weldability of die-cast products?
- Research Hypotheses:
- By employing advanced vacuum die casting techniques, such as the HIVAC-V method, and meticulously controlling process parameters, it is possible to significantly reduce gas porosity in aluminum alloy die-castings.
- Optimizing the selection and application of release agents and plunger lubricants plays a crucial role in minimizing gas generation and entrapment during the die casting process, thereby enhancing weldability.
- A high-temperature blister test can serve as a reliable and practical quality assurance method to predict the weldability of die-cast components by correlating blister formation with internal gas content.
4. Research Methodology:
- Research Design: The research employs an experimental design focused on process optimization and quality evaluation. The study investigates the impact of various process parameters within the HIVAC-V die casting method on the gas content and weldability of aluminum alloy die-cast components.
- Data Collection Method:
- Gas Content Measurement: The amount of gas within the die-cast samples was quantified using a vacuum extraction method. Samples were cut to a consistent size using a band saw and then cleaned with acetone and acid-alkali solutions as pre-treatment. Measurements were taken on samples with the as-cast surface condition to simulate welding conditions.
- Weldability Evaluation: TIG (Tungsten Inert Gas) welding tests were conducted to assess the weldability of the die-cast samples. The appearance of the weld bead, including the presence of porosity and surface defects, was visually inspected and evaluated.
- Blister Test: A high-temperature blister test was employed as a potential quality assurance method. Die-cast samples were subjected to elevated temperatures, and the formation of blisters on the surface was observed and categorized.
- Analysis Method:
- Comparative Analysis: The research compared the gas content and weldability of die-cast samples produced under varying process conditions, including different types and application rates of release agents and plunger lubricant amounts.
- Correlation Analysis: The study investigated the correlation between the results of the blister test and the measured gas content to determine the blister test's effectiveness as a predictor of weldability.
- Qualitative Assessment: Visual inspection and qualitative assessment of weld bead appearance were conducted to evaluate the weld quality of samples produced using different die casting methods (HIVAC-V vs. conventional vacuum die casting).
- Research Subjects and Scope: The research focused on aluminum alloy die-cast components produced using the HIVAC-V method. The primary process parameters investigated were:
- Release Agent Type: Two types of water-based release agents (Type A and Type B) were tested at a 50x dilution ratio.
- Release Agent Output: The output volume of release agent applied to the die was varied by adjusting the pressure.
- Plunger Lubricant Amount: Different amounts of plunger lubricant were tested.
The study also compared the weld bead quality of components produced using the HIVAC-V method with those produced using a conventional vacuum die casting method. The application example presented is a snowmobile frame component, which is welded to surrounding aluminum extrusions using MIG (Metal Inert Gas) welding.
5. Main Research Results:
- Key Research Results:
- HIVAC-V Die Casting for Weldability: The research demonstrated that the HIVAC-V die casting method is capable of producing aluminum alloy components suitable for welding.
- Impact of Release Agent Type: Figure 3 illustrates the relationship between release agent type and gas content. Release agent A consistently resulted in lower gas content in the die-cast products compared to release agent B across different filling times. Furthermore, the trend of gas content change with filling time differed between the two release agents, suggesting variations in the thermal properties and robustness of the release agent film formed on the die surface.
- Impact of Release Agent Output: Figure 4 shows the effect of release agent output on gas content. Interestingly, increasing the release agent output initially led to a decrease in gas content. This is attributed to the increased atomization of the release agent at higher pressures, resulting in finer droplets and improved evaporation of water and volatile components before die closure, leading to reduced gas entrapment.
- Impact of Plunger Lubricant Amount: Figure 5 demonstrates the relationship between plunger lubricant amount and gas content. Increasing the amount of plunger lubricant resulted in a higher gas content in the die-cast products. This is because plunger lubricant is also a source of gas generation during the die casting process.
- Blister Test as Quality Assurance: Figure 6 shows the correlation between blister occurrence and gas content. Samples with lower gas content (around 4.7 ml/100g) passed the blister test (OK), while samples with higher gas content (42 ml/100g) exhibited surface blisters and failed. Samples with intermediate gas content (8.6 ml/100g) were conditionally acceptable (OK if no blisters in weld-affected areas). This indicates that the blister test can be used as an indicator of weldability and gas content.
- Weld Bead Quality: Figures 7 and 8 compare the weld bead appearance of components produced using HIVAC-V and conventional vacuum die casting. The HIVAC-V samples exhibited significantly better weld bead quality, with fewer pores and a smoother, more lustrous surface, indicating reduced gas porosity and oxide formation.
- Statistical/Qualitative Analysis Results:
- Figure 3 (이형제 종류와 제품 내 가스량의 관계): Quantitative data showing lower gas content with Release Agent A compared to Release Agent B across various filling times.
- Figure 4 (이형제 도출량과 제품 내 가스량과의 관계): Quantitative data showing an initial decrease in gas content with increasing release agent output, followed by a potential increase at very high output levels (although not explicitly shown in the provided figure excerpt).
- Figure 5 (플랜저윤활제량과 제품 내 가스량과의 관계): Quantitative data demonstrating a positive correlation between plunger lubricant amount and gas content.
- Figure 6 (브리스타 발생 상황과 제품 내 가스량): Qualitative categorization of blister occurrence (OK, Conditional OK, NG) correlated with gas content ranges (4.7 ml/100g, 8.6 ml/100g, 42 ml/100g).
- Figure 7 (본 제품에 용접비드 외관): Visual representation of a weld bead on a die-cast product.
- Figure 8 (비드부 외관의 비교): Qualitative visual comparison of weld bead appearance between vacuum die-cast (conventional) and HIVAC-V die-cast samples, showing superior bead quality for HIVAC-V.
- Data Interpretation: The results strongly suggest that controlling process parameters, particularly the type and application of release agent and the amount of plunger lubricant, is crucial for minimizing gas porosity in aluminum alloy die-castings intended for welding. The HIVAC-V method, with its optimized vacuum system and process control, effectively reduces gas entrapment. The blister test provides a practical and rapid quality assurance method for predicting weldability in a production setting.
- Figure Name List:
- Fig. 1. ASF 구조의 예 (Example of ASF structure)
- Fig. 2. 적용제품 (용접 Assy 상태) (Application product (Welded Assy state))
- Fig. 3. 이형제 종류와 제품 내 가스량의 관계. (Relationship between release agent type and gas content in product)
- Fig. 4. 이형제 도출량과 제품 내 가스량과의 관계. (Relationship between release agent output and gas content in product)
- Fig. 5. 플랜저윤활제량과 제품 내 가스량과의 관계. (Relationship between plunger lubricant amount and gas content in product)
- Fig. 6. 브리스타 발생 상황과 제품 내 가스량. (Blister occurrence status and gas content in product)
- Fig. 7. 본 제품에 용접비드 외관. (Weld bead appearance of this product)
- Fig. 8. 비드부 외관의 비교. (Comparison of bead appearance)
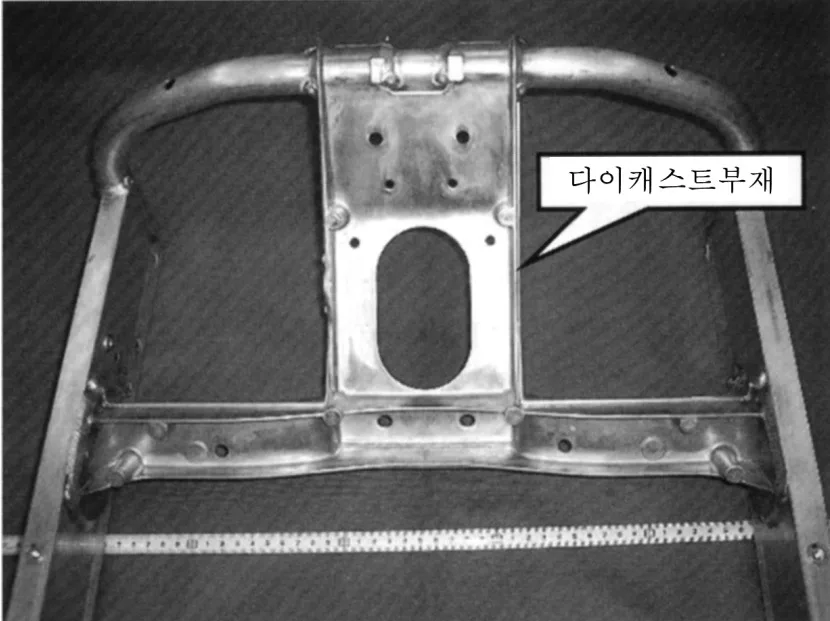

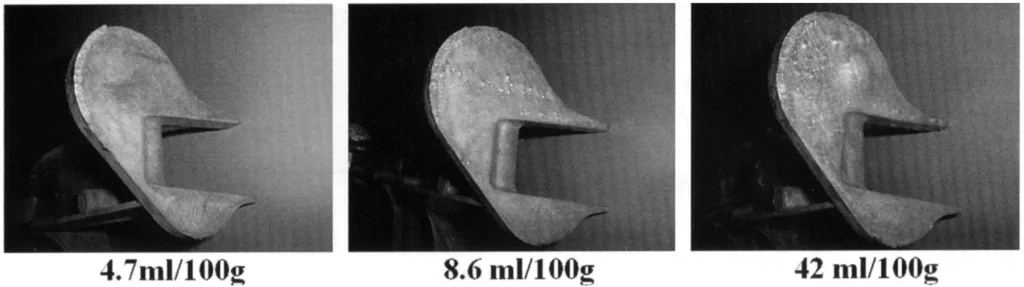
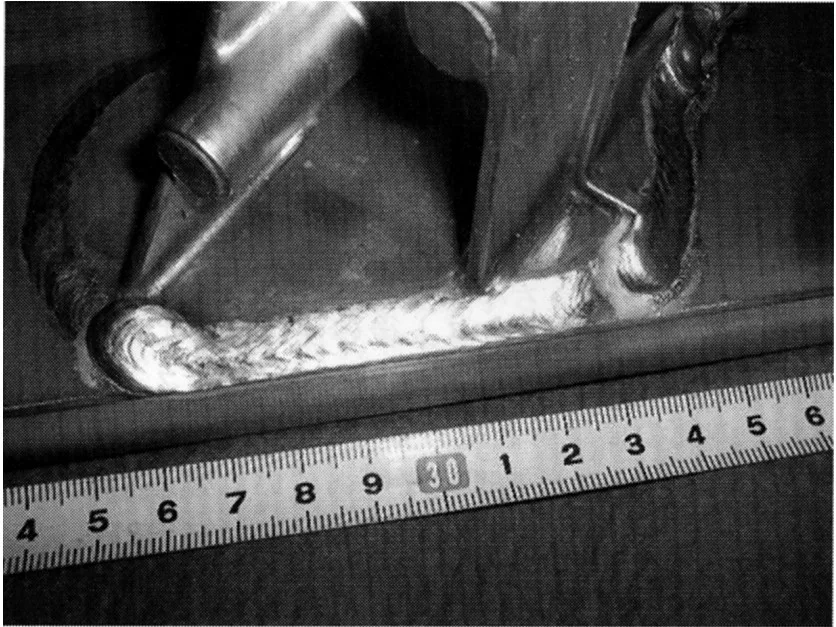
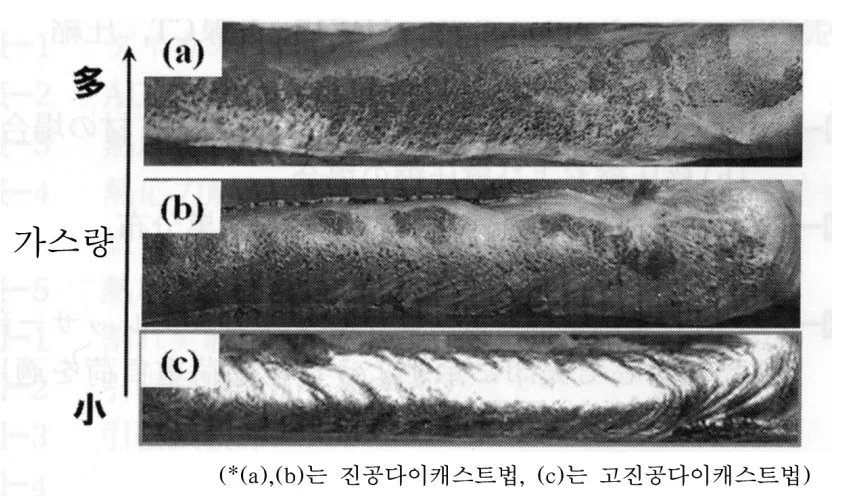
6. Conclusion and Discussion:
- Summary of Main Results: The research successfully demonstrated the feasibility of producing weldable aluminum alloy die-cast components using the HIVAC-V method. Key factors identified for achieving weldability include minimizing gas content through optimized selection and application of release agents and plunger lubricants, and implementing a blister test as a practical quality assurance measure. The HIVAC-V method significantly improved weld bead quality compared to conventional vacuum die casting.
- Academic Significance of the Research: This research contributes to the field of die casting by demonstrating a viable approach to overcome the traditional limitations of welding aluminum die-cast parts. It provides valuable insights into the complex interplay between die casting process parameters, gas porosity, and weldability. The study highlights the importance of advanced vacuum die casting techniques and process control for expanding the application of die casting in structural components requiring welding.
- Practical Implications: The findings have significant practical implications for industries, particularly the automotive sector, seeking to utilize die casting for larger and more complex structural components. The ability to weld die-cast parts enables the design and manufacturing of lightweight and high-performance structures with reduced part count and assembly costs. The research provides practical guidelines for die casters to produce weldable aluminum alloy components in mass production, including the use of the blister test for quality control.
- Limitations of the Research: The study is primarily focused on the HIVAC-V die casting method and specific aluminum alloys and process parameters. The generalizability of the findings to other die casting methods, alloy systems, and welding techniques requires further investigation. The research also focuses on MIG and TIG welding; the applicability to other welding processes may need to be explored.
7. Future Follow-up Research:
- Directions for Follow-up Research:
- Further investigation into the fundamental mechanisms of gas entrapment during the HIVAC-V die casting process and the detailed effects of various process parameters on gas porosity formation.
- Exploration of a wider range of release agent chemistries, application methods, and plunger lubricant formulations to further optimize gas reduction and weldability.
- Evaluation of the weldability of HIVAC-V die-cast components using other welding techniques, such as laser welding, friction stir welding, and resistance spot welding.
- Investigation into the mechanical properties, fatigue performance, and long-term durability of welded joints in HIVAC-V die-cast aluminum alloy components.
- Areas Requiring Further Exploration:
- Development of more sophisticated non-destructive testing methods for assessing the internal quality and weldability of die-cast components beyond the blister test.
- Cost-effectiveness analysis of implementing HIVAC-V die casting and welding for large structural components compared to traditional manufacturing methods.
- Research into the recyclability and environmental impact of using weldable die-cast aluminum components in automotive and other applications.
8. References:
[1] 神戸洋史:(社)日本鋳造工学会 ダイカスト研究部会研究報告100, 1
[2] 近藤和利,青山俊三,酒井信行,三中西信治,上田昭暢:日本ダイカスト会議論文集,(2004), 259
[3] 村上衛,安原由章,浅田穣,菅波宏哉,竹田敬,福地文亮:日本ダイカスト会議論文集,(2006),217
[4] 橘内透,山縣裕:日本ダイカスト会議論文集,(2004), 271
[5] 金内良夫:(社)日本鋳造工学会 ダイカスト研究部会研究報告100,19
[6] 金内良夫,伊藤俊久,小暮浩,茂木達也,宮島信明:日本ダイカスト会議論文集, (2006), 229
[7] 水野政夫,蓑田和之,阪口章:「アルミニウムとその合金の溶接」,産報出版(1999)
9. Copyright:
- This material is 金内良夫 (Takao Kaneuchi)'s paper: Based on Die Casting Technology for Welding Application
- Paper Source: 日本鑄造工學會誌 제81권(2009) 제5호 page 249~253에 게재된 자료임
This material was summarized based on the above paper, and unauthorized use for commercial purposes is prohibited.
Copyright © 2025 CASTMAN. All rights reserved.