This paper introduction was written based on the "THE Aluminium Automotive MANUAL Manufacturing – Casting methods" published by the European Aluminium Association.
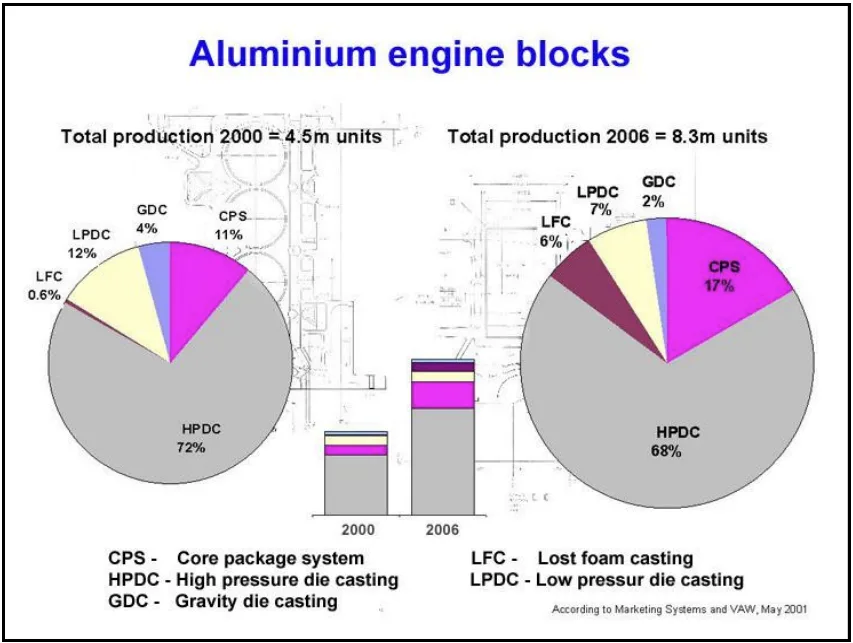
Introduction
This document provides an overview of various casting methods, with a focus on their applications in the automotive industry. It covers a range of techniques from traditional sand casting to more advanced die casting processes, including their characteristics, process descriptions, design considerations, and examples of automotive parts produced using these methods.
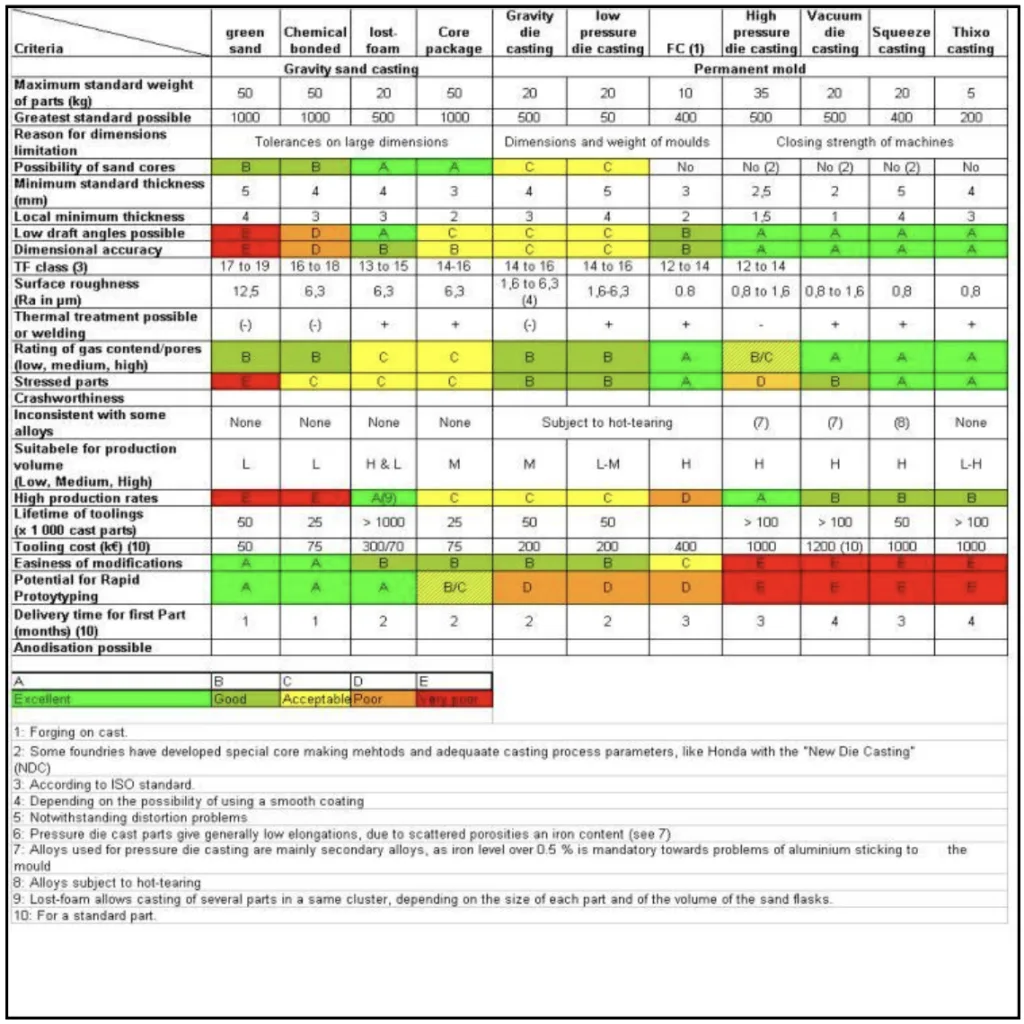
1. Casting Methods
1.1 Overview of Casting Processes and Automotive Applications
Automotive casting processes are categorized by mould filling and moulding technologies. Key methods discussed are:
- Green sand casting
- Modified DISAmatic casting
- Core package casting
- Gravity die casting
- Low pressure die casting
- High pressure die casting
- Vacuum die casting
- Squeeze casting
- Thixocasting
- Vacuum riserless casting
- Lost foam casting
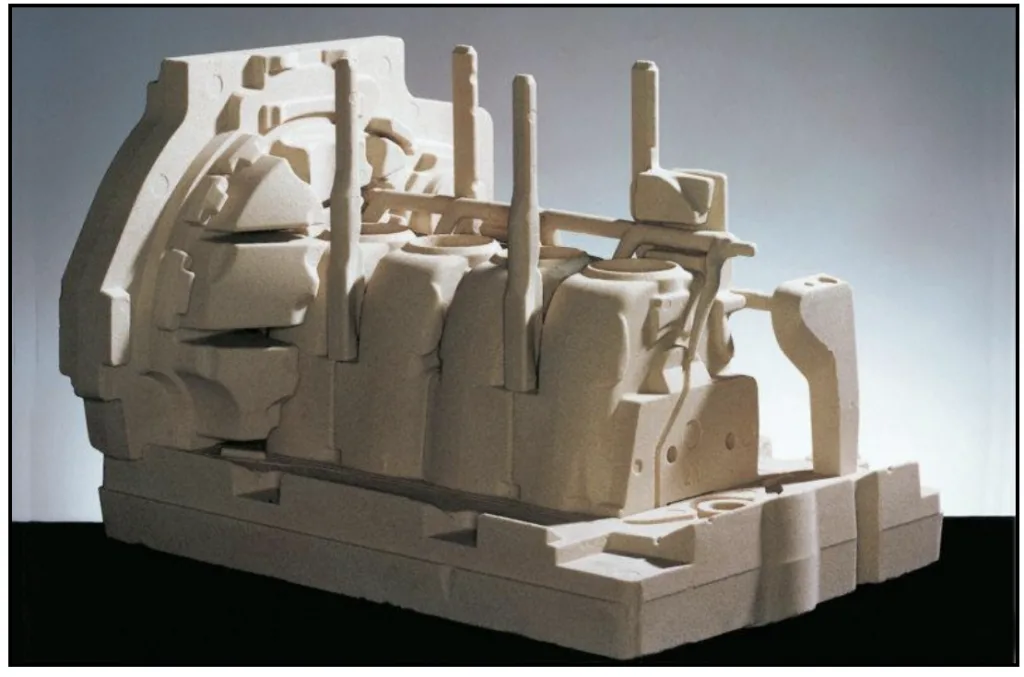
1.2 Market Trends for Engine Blocks and Heads
- Analysis of market share trends for different casting methods used in the production of aluminum engine blocks and cylinder heads.
- Aluminium engine blocks: According to Marketing Systems and VAW, May 2001, high-pressure die casting (HPDC) was the dominant method in 2000 and 2006, while core package systems (CPS) and low-pressure die casting (LPDC) also held significant shares.
- Aluminium cylinder heads: Gravity die casting (GDC) was the primary method in both 2000 and 2006, with increasing presence of Rotacast (RC).
1.3 Green Sand Castings
- Green sand casting (Horizontal moulding): High productivity, flexible process, Automatic pattern-change.
- Used for: Intake manifolds, Oil pan housings, Structural parts, Chassis parts.
- Moulding process: Loose moulding sand is compacted by compressed air and then pressed for final strength.
- DISAmatic casting: Automated green sand casting suitable for middle to high volume series, especially for automotive applications.
- AGSC (Alcoa Green Sand Casting): Alcoa's variant green sand casting. Examples: Heat Exchanger, Hat Profile, Brake Calipers, Knuckles.
1.4 Core Package Casting
- Introduction: All sand mould consists of single sand cores. CPS® (Core Package System) has become an established casting process for the volume production of engine blocks.
- Design features: Complicated oil galleries and pre-cast oil channels, complex exhaust gas return systems, secondary air ducts, thin cooling water passages, casting-in of cylinder liners.
- Process description: Apply resin bonded sand cores and silica sand. Core packages assembled automatically.
1.5 Gravity Die Casting
- Characteristics: Process is used in carousel casting units or in shuttle technique particularly for the manufacture of engine castings. Optimum heat dissipation from the solidifying casting through the die leads to short solidification times.
- Process description: Melt is treated in the holding furnace, and the quantity of melt is transported in a ladle and poured into the riser system of the mould.
- Rotacast®: The combustion chamber of the die cavity shoots upwards.
1.6 Low Pressure Die Casting
- Description: Used for aluminium wheels and big V-engine blocks, mould filling controlled by regulating the pressure in the casting furnace.
1.7 High Pressure Die Castings
- HPDC process: Filling speed and intensification pressure differentiates high-pressure die casting from most other casting processes.
- HPDC process cycle: The pressure cycle in a modern HPDC machine is closely controlled in all stages. Filling times are typically on the order of 10-25 milliseconds.
- Typical automotive applications: Transmission cases and Belt Tensioners.
- Design considerations:
- Only straight steel core pulls can be used to define internal passages.
- Inserts can frequently be cast into the part.
- Common and special purpose HPDC alloys: Al18Si (AA 391), AlSi8Cu3 (AA 380), AlSi10Cu (AA 383), AlSi5 (AA C443), AlSi12 (AA 413) , AlSi17Cu4Mg (AA 390).
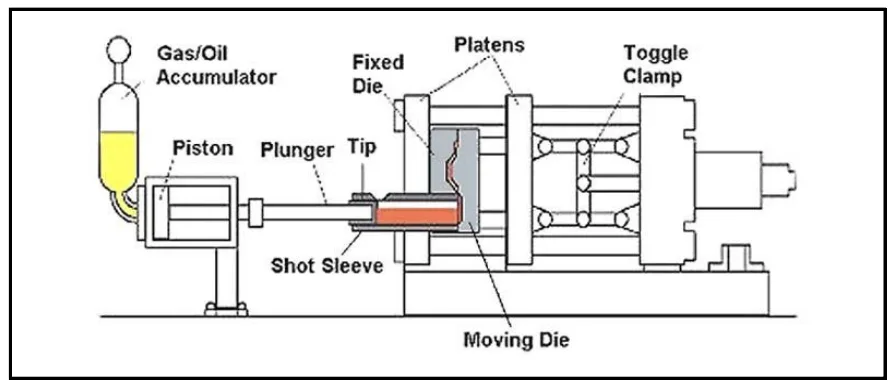
1.8 Vacuum Die Castings
- Characteristics: thin walls in large structures, joining with standard welding techniques as well as Laser welding and self-piercing rivets, crash worthy structures.
- VDC Process:
- Dosage: low air pressure in the filling chamber sucks a portion of melt into the filling chamber.
- Metal Transport: piston drives up and seals the suction pipe. The melt is pressed to the gate.
- Injection: the vacuum valves are closed the melt is injected into the die at high rate.
- Post injection densification: the piston exerts high pressure (> 150 bar) until complete solidification.
1.9 Squeeze Castings
- Characteristics: The metal is drastically lowered, so as to avoid any turbulence. Solidification must be progressive from the thinner area of the cast part to the biscuit.
1.10 Thixocastings
- Semi-solid forming: The metal behaves like a solid (high viscosity) if not sheared. As soon as shearing occurs, viscosity decreases by orders of magnitude. Under some conditions this effect is reversible.
- Suitable alloys and their mechanical properties: The metal can be brought homogeneously to a liquid fraction between 40 and 60%, the solid phase is prone to build a fine globular structure.
1.11 Vacuum Riserless Castings
- VRC / PRC: Combination of Vacuum Riserless Casting (VRC) with Pressure Riserless Casting (PRC).
- VRC / PRC – Process: Liquid aluminium is distributed by a channel system feeding furnaces equipped with impellers. From there the melt flows to dosage furnaces feeding the casting furnaces after every shot.
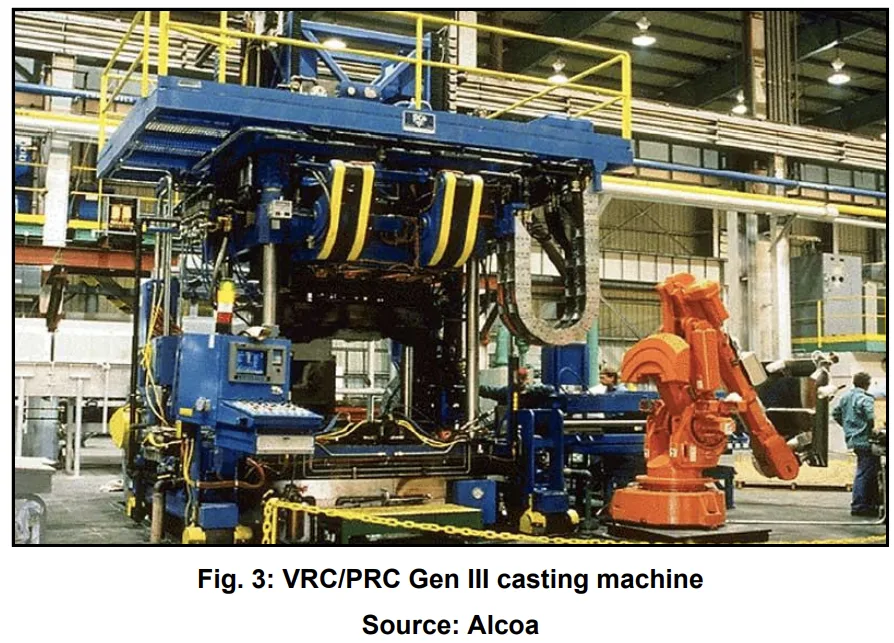
1.12 Lost Foam Castings
- Introduction: LFC offers the possibility of a direct production of nearly any complex geometry.
- Pattern making & cluster assembly: the initial material required for pattern making is expandable polystyrene (EPS).
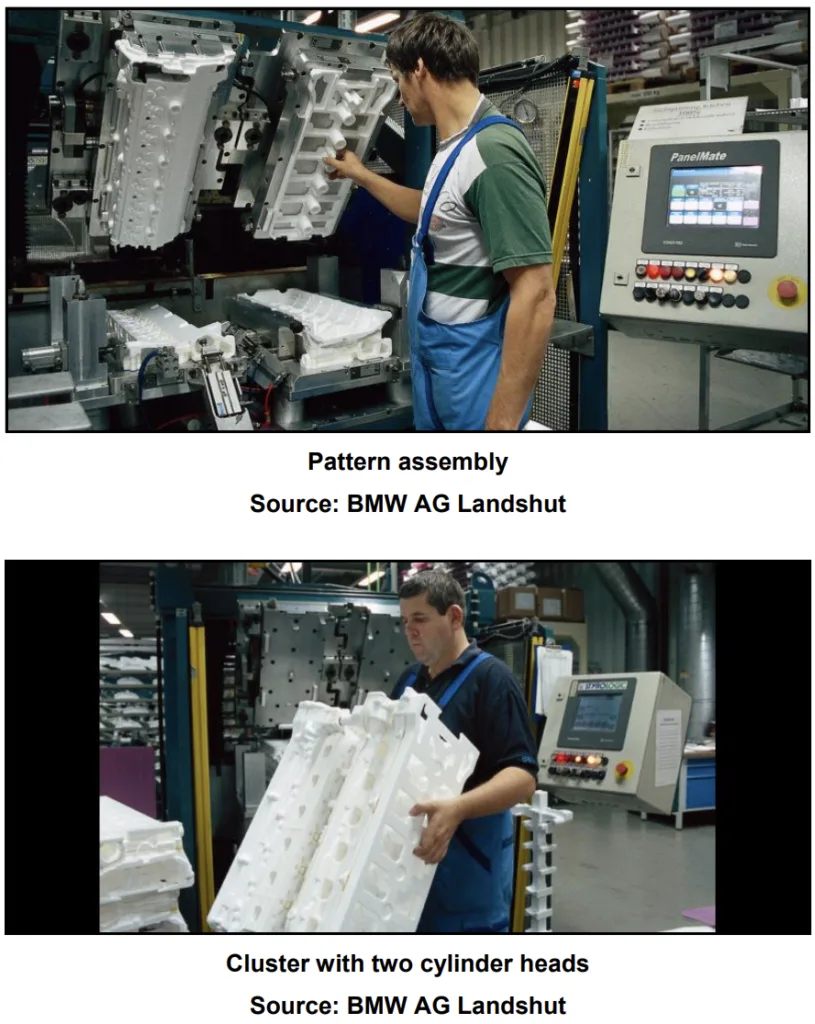
1.13 Comparing casting techniques
1.13.1 Comparing casting techniques for engine blocks and cylinder heads:
- Rotacast
- Die Casting GDC+LPDC
- Core Package
- High Pressure Die Casting
- Lost Foam