본 문서는 European Aluminium Association에서 발행한 "THE Aluminium Automotive MANUAL - Manufacturing – Casting methods"를 기반으로 작성되었습니다. 다이캐스팅 분야의 최고 전문가로서, 해당 내용을 핸드북 수준으로 요약하여 워드프레스 게시용으로 제공합니다.
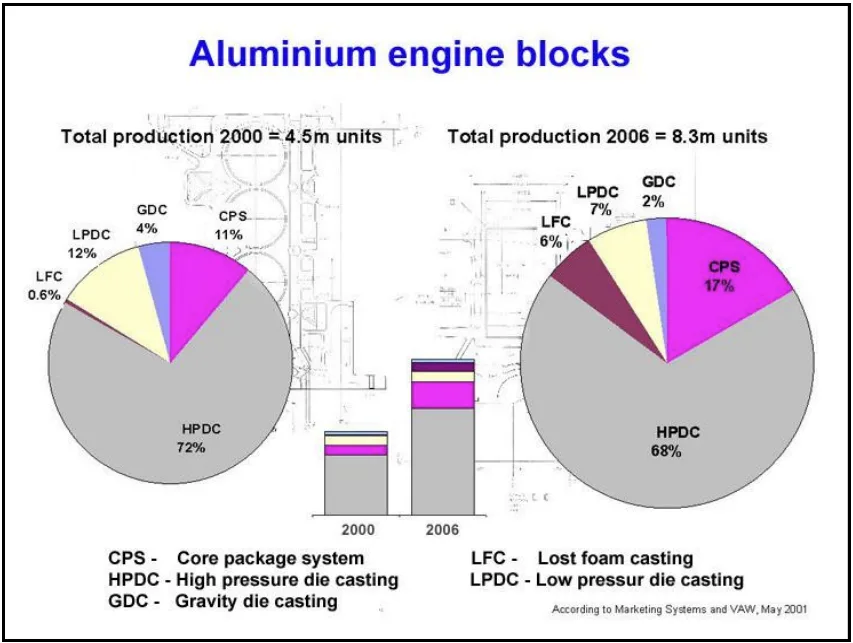
소개
본 문서는 자동차 산업에서의 응용 분야에 초점을 맞춰 다양한 주조 방법에 대한 개요를 제공합니다. 전통적인 사형 주조(Green sand casting)부터 고급 다이캐스팅 공정에 이르기까지 다양한 기술의 특성, 공정 설명, 설계 고려 사항 및 이러한 방법을 사용하여 생산된 자동차 부품의 예시를 다룹니다.
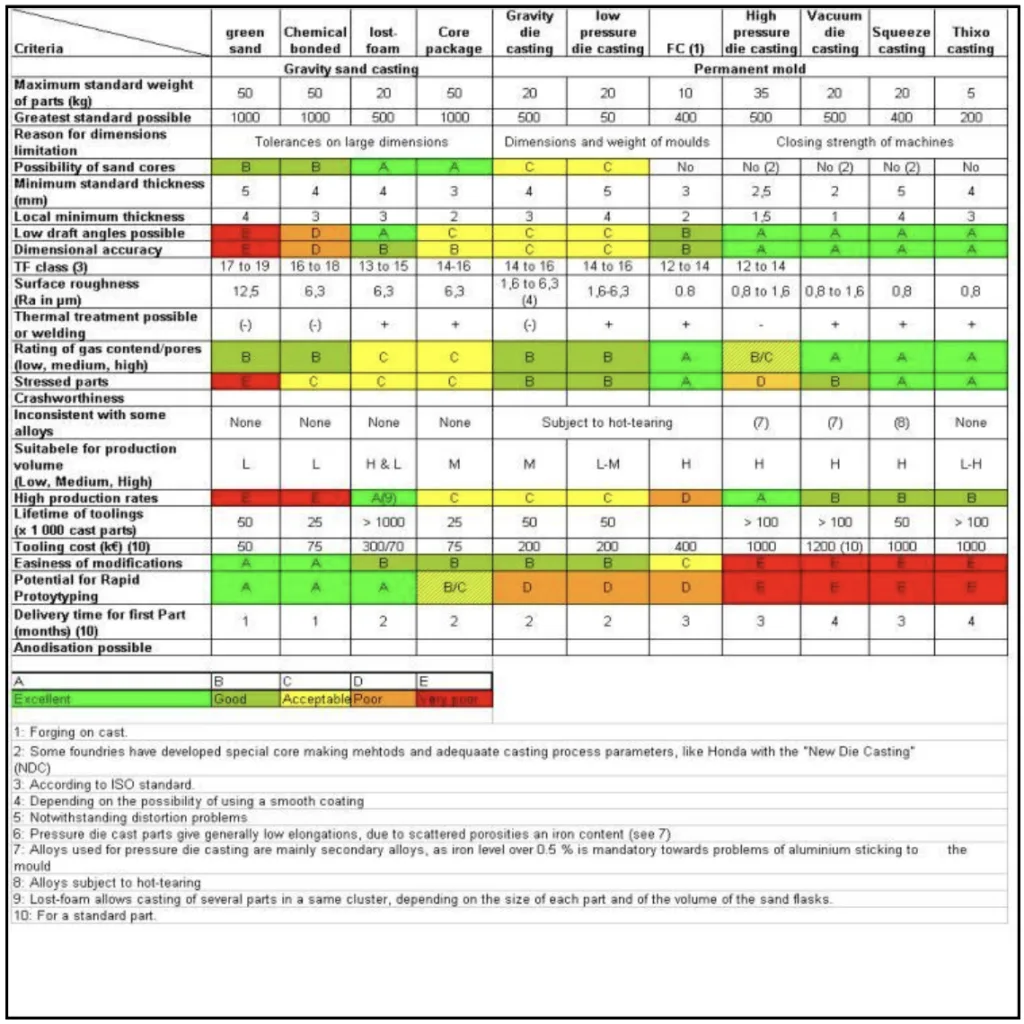
1. 주조 방법
1.1 주조 공정 및 자동차 응용 분야 개요
자동차 주조 공정은 (A) 몰드 충전 방식과 (B) 몰딩 기술에 따라 분류됩니다. 주요 논의된 방법은 다음과 같습니다:
- 사형 주조 (Green sand casting)
- 변형된 DISAmatic 주조 (Modified DISAmatic casting)
- 코어 패키지 주조 (Core package casting)
- 중력 다이캐스팅 (Gravity die casting)
- 저압 다이캐스팅 (Low pressure die casting)
- 고압 다이캐스팅 (High pressure die casting)
- 진공 다이캐스팅 (Vacuum die casting)
- 스퀴즈 주조 (Squeeze casting)
- Thixocasting (Thixocasting)
- 진공 라이저리스 주조 (Vacuum riserless casting)
- 로스트 폼 주조 (Lost foam casting)
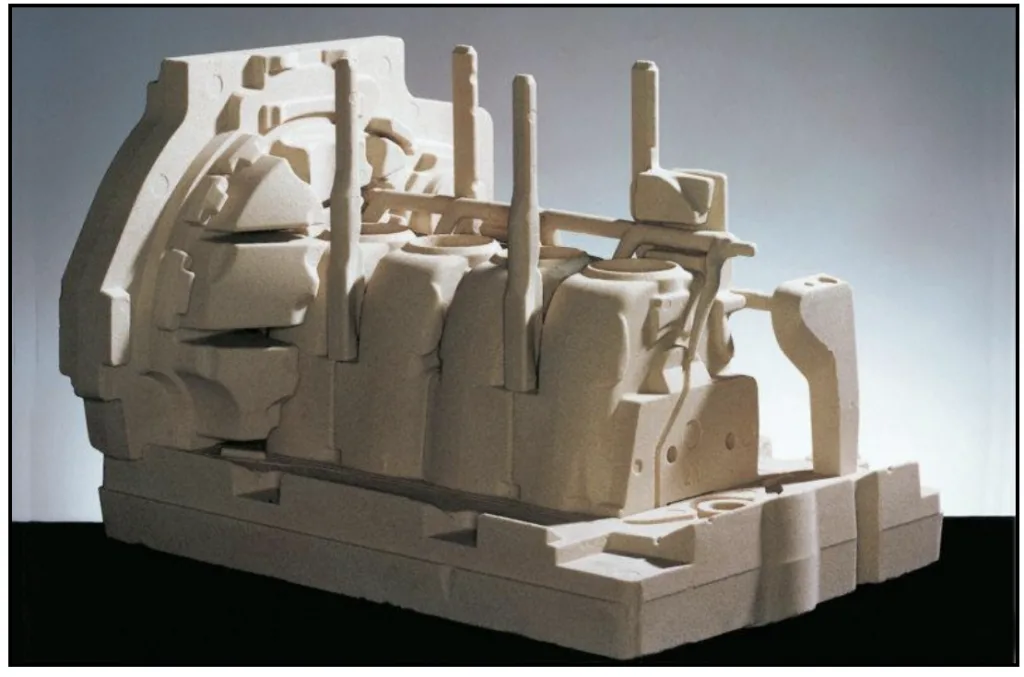
1.2 엔진 블록 및 헤드에 대한 시장 동향
- 알루미늄 엔진 블록 및 실린더 헤드 생산에 사용되는 다양한 주조 방법의 시장 점유율 추세 분석.
- 알루미늄 엔진 블록: Marketing Systems and VAW, 2001년 5월에 따르면 고압 다이캐스팅(HPDC)이 2000년과 2006년에 지배적인 방법이었으며, 코어 패키지 시스템(CPS)과 저압 다이캐스팅(LPDC)도 상당한 점유율을 차지했습니다.
- 알루미늄 실린더 헤드: 중력 다이캐스팅(GDC)이 2000년과 2006년 모두 주요 방법이었으며, Rotacast (RC)의 존재가 증가했습니다.
1.3 사형 주조 (Green Sand Castings)
- 사형 주조 (수평 몰딩): 높은 생산성, 유연한 공정, 자동 패턴 변경 (Automatic pattern-change).
- 사용 용도: 흡기 매니폴드 (Intake manifolds), 오일 팬 하우징 (Oil pan housings), 구조 부품 (Structural parts), 섀시 부품 (Chassis parts).
- 몰딩 공정: 느슨한 몰딩 사를 압축 공기로 압축한 다음 최종 강도를 위해 프레스로 누릅니다.
- DISAmatic casting: 자동차 응용 분야, 특히 중형에서 대량 시리즈에 적합한 자동화된 사형 주조.
- AGSC (Alcoa Green Sand Casting): Alcoa의 변형된 사형 주조. 예: 열 교환기 (Heat Exchanger), 모자 프로파일 (Hat Profile), 브레이크 캘리퍼스 (Brake Calipers), 너클 (Knuckles).
1.4 코어 패키지 주조 (Core Package Casting)
- 소개: 모든 사형 몰드가 단일 사형 코어로 구성됩니다. CPS® (Core Package System)는 엔진 블록의 대량 생산을 위한 확립된 주조 공정이 되었습니다.
- 설계 특징: 복잡한 오일 갤러리 (Complicated oil galleries) 및 사전 주조 오일 채널 (pre-cast oil channels), 복잡한 배기 가스 복귀 시스템 (complex exhaust gas return systems), 2차 공기 덕트 (secondary air ducts), 얇은 냉각수 통로 (thin cooling water passages), 실린더 라이너 주조 (casting-in of cylinder liners).
- 공정 설명: 수지 접착 사형 코어 (resin bonded sand cores)와 실리카 사 (silica sand)를 적용합니다. 코어 패키지가 자동으로 조립됩니다.
1.5 중력 다이캐스팅 (Gravity Die Casting)
- 특징: 공정은 카루셀 주조 장치 또는 셔틀 기술에서 특히 엔진 주조 생산에 사용됩니다. 다이를 통한 응고 주조의 최적의 열 발산은 짧은 응고 시간으로 이어집니다.
- 공정 설명: 용융물이 유지 용광로 (holding furnace)에서 처리되고, 용융물의 양이 국자 (ladle)에 옮겨져 몰드의 라이저 시스템 (riser system)에 붓습니다.
- Rotacast®: 다이 캐비티의 연소실이 위로 향합니다.
1.6 저압 다이캐스팅 (Low Pressure Die Casting)
- 설명: 알루미늄 휠 및 대형 V형 엔진 블록에 사용되며, 몰드 충전은 주조 용광로 (casting furnace)의 압력을 조절하여 제어됩니다.
1.7 고압 다이캐스팅 (High Pressure Die Castings)
- HPDC 공정: 충전 속도 (Filling speed)와 강화 압력 (intensification pressure)은 고압 다이캐스팅을 다른 주조 공정과 차별화합니다.
- HPDC 공정 주기: 최신 HPDC 기계의 압력 사이클은 모든 단계에서 정밀하게 제어됩니다. 충전 시간은 일반적으로 10~25밀리초입니다.
- 일반적인 자동차 응용 분야: 변속기 케이스 (Transmission cases) 및 벨트 텐셔너 (Belt Tensioners).
- 설계 고려 사항:
- 내부 통로를 정의하는 데에는 직선형 강철 코어 풀(steel core pulls)만 사용할 수 있습니다.
- 인서트(inserts)는 부품에 주조할 수 있습니다.
- 일반 및 특수 목적 HPDC 합금: Al18Si (AA 391), AlSi8Cu3 (AA 380), AlSi10Cu (AA 383), AlSi5 (AA C443), AlSi12 (AA 413) , AlSi17Cu4Mg (AA 390).
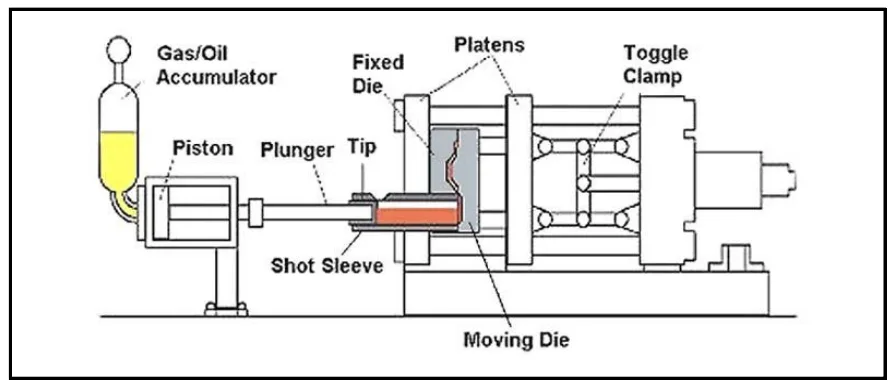
1.8 진공 다이캐스팅 (Vacuum Die Castings)
- 특징: 대형 구조물의 얇은 벽 (thin walls), 레이저 용접 (Laser welding) 및 자체 피어싱 리벳 (self-piercing rivets)뿐만 아니라 표준 용접 기술 (standard welding techniques)을 사용한 접합, 충돌 방지 구조 (crash worthy structures).
- VDC 공정:
- 투입 (Dosage): 충전실의 낮은 기압 (low air pressure)으로 인해 용융물이 충전실 (filling chamber)로 흡입됩니다.
- 금속 이송 (Metal Transport): 피스톤 (piston)이 올라가 흡입 파이프 (suction pipe)를 밀봉합니다. 용융물이 게이트 (gate)로 눌려집니다.
- 사출 (Injection): 진공 밸브 (vacuum valve)가 닫힌 후 용융물이 높은 속도로 다이로 사출됩니다.
- 사출 후 압축 (Post injection densification): 피스톤은 완전한 응고가 될 때까지 높은 압력 (> 150 bar)을 가합니다.
1.9 스퀴즈 주조 (Squeeze Castings)
- 특징: 금속의 속도를 크게 낮춰 난류를 방지합니다. 응고는 주조 부품의 더 얇은 영역에서 비스킷 (biscuit)으로 진행되어야 합니다.
1.10 Thixocasting (Thixocasting)
- 반고체 성형 (Semi-solid forming): 금속은 전단되지 않으면 고체(높은 점도)처럼 거동합니다. 전단이 발생하자마자 점도가 급격히 감소합니다. 일부 조건에서 이 효과는 가역적입니다.
- 적합한 합금 및 기계적 특성: 금속은 40~60%의 액체 분율로 균일하게 가져올 수 있으며, 고체상은 미세한 구상 구조를 형성하는 경향이 있습니다.
1.11 진공 라이저리스 주조 (Vacuum Riserless Castings)
- VRC / PRC: 진공 라이저리스 주조(Vacuum Riserless Casting, VRC)와 압력 라이저리스 주조(Pressure Riserless Casting, PRC)의 조합입니다.
- VRC / PRC – 공정: 액체 알루미늄은 임펠러가 장착된 용광로를 공급하는 채널 시스템에 의해 분배됩니다. 거기에서 용융물은 모든 샷 후에 주조 용광로를 공급하는 투입 용광로로 흐릅니다.
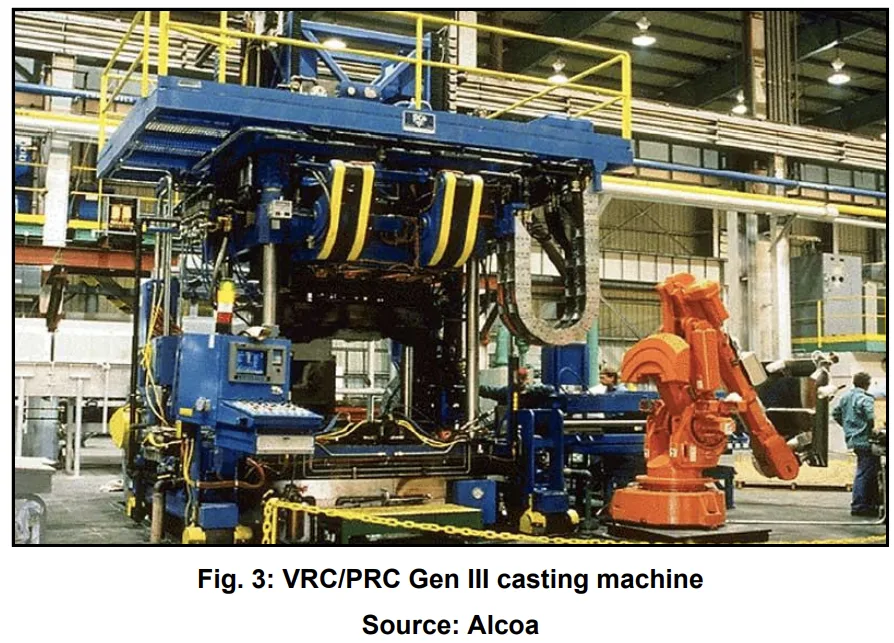
1.12 로스트 폼 주조 (Lost Foam Castings)
- 소개: LFC는 거의 모든 복잡한 형상을 직접 생산할 수 있습니다.
- 패턴 제작 및 클러스터 조립: 패턴 제작에 필요한 초기 재료는 발포성 폴리스티렌(Expandable Polystyrene, EPS)입니다.
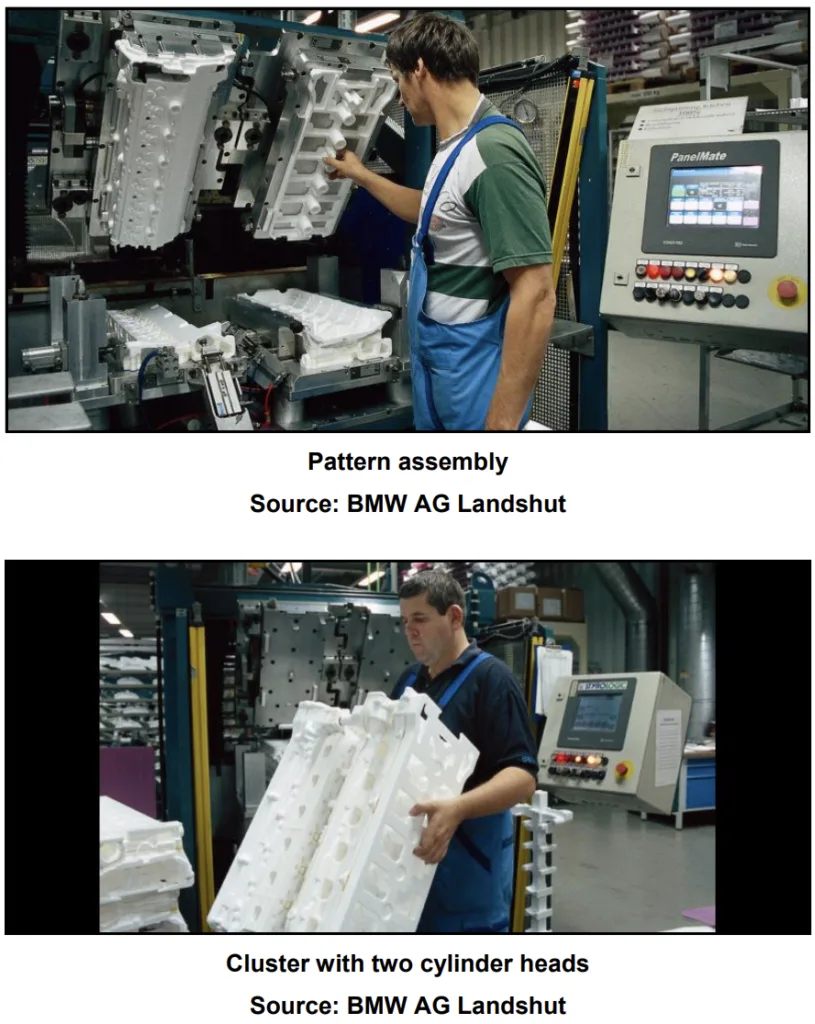
1.13 주조 기술 비교 (Comparing Casting Techniques)
1.13.1 엔진 블록 및 실린더 헤드에 대한 주조 기술 비교:
- Rotacast (Rotacast)
- Die Casting GDC+LPDC
- 코어 패키지 (Core Package)
- 고압 다이캐스팅 (High Pressure Die Casting)
- 로스트 폼 (Lost Foam)