This introductory paper is the research content of the paper ["Die Casting or Sheet Metal Forming: A Comparison of Car Body Manufacturing in Times of the "Giga Press""] published by ["TECHNICAL JOURNAL"].
![Figure 1 Body with self-supporting shell construction ([3], p.18)](https://castman.co.kr/wp-content/uploads/image-1410-1024x445.webp)
1. Overview:
- Title: Die Casting or Sheet Metal Forming: A Comparison of Car Body Manufacturing in Times of the "Giga Press"
- Author: Martin Bednarz
- Publication Year: 2025
- Publishing Journal/Academic Society: TECHNICAL JOURNAL
- Keywords: car body manufacturing; large-scale die casting; sheet metal construction
2. Abstracts / Introduction
This paper investigates the application of die casting as an alternative to sheet metal structures in automotive body design, a concept that has garnered attention in recent years. While legacy automotive manufacturers have shown limited adoption of die cast body components, particularly in mass market vehicles, Tesla has notably employed extremely large die cast structural parts in their mass-produced automobiles. This divergence in strategy necessitates a re-evaluation of established car body manufacturing paradigms. This study leverages published data and expert interviews to rigorously assess the strengths and weaknesses inherent in these competing car body manufacturing philosophies, namely large-scale die casting and sheet metal shell construction.
The impetus for this research stems from the ongoing evolution of manufacturing technologies within the automotive industry, specifically concerning vehicle body production. In the context of mass production, two dominant technologies emerge: the increasingly prevalent large die-casting technology and the conventional sheet metal shell construction method. This research endeavors to provide a comprehensive comparative analysis of these two pivotal manufacturing processes. The automotive sector is perpetually confronted with demands for enhanced efficiency, cost reduction, and adherence to progressively stringent environmental regulations. The judicious selection of manufacturing technology exerts a substantial influence on the overall performance and competitive positioning of automotive manufacturers. Consequently, a thorough understanding of the relative advantages and disadvantages of large die casting technology, when juxtaposed with the established sheet metal shell construction method, is of paramount importance.
3. Research Background:
Background of the Research Topic:
The automotive industry is continuously challenged by demands for increased efficiency, cost savings, and stricter environmental regulations. The selection of an appropriate manufacturing technology is critical for the overall performance and competitiveness of automotive manufacturers. Therefore, a comprehensive understanding of the advantages and disadvantages of large die casting technology compared to the established sheet metal shell construction method is essential.
Status of Existing Research:
Sheet metal shell construction, also known as self-supporting shell construction, is the current industry standard for passenger car body construction utilizing steel, as depicted in "Figure 1 Body with self-supporting shell construction ([3], p.18)". This method involves connecting steel or aluminum half-shells, eliminating the traditional distinction between chassis and body. Individual body sections like the roof, floor, and side walls are composed of large sheet metal panels that bear structural loads. This construction technique facilitates the creation of complex three-dimensional structures and enables targeted lightweighting through component integration. Sheet metal shell design also allows for a high degree of automation and is suitable for high-volume, low-cost production. However, the substantial acquisition costs associated with tooling for sheet metal forming render customization and high variant production economically unviable [2].
In contrast, mega-casting, a term synonymous with large-scale casting [3], large-scale die casting, or high-performance die casting, represents a transformative process in the automotive industry. The primary distinction from conventional die casting lies in the scale of the systems [4]. For vehicle manufacturing, mega-casting offers the potential to reduce joining complexity, automation requirements, cycle time, and spatial footprint due to a decreased component count. However, ensuring reproducible quality remains a challenge, attributed to limited knowledge and experience with the intricate die casting process [5]. Large-scale die casting impacts car body design by enabling further lightweight construction optimization. It facilitates joint reduction and the direct integration of connection points into components, streamlining the assembly of add-on parts. Nevertheless, compared to existing methods, body adaptability and modification are limited. As of 2022, challenges related to component quality, pore formation, and repairability in car body series production persist [5].
Necessity of the Research:
The strategic shift by manufacturers, exemplified by Tesla's implementation of large die cast structure parts, necessitates a re-evaluation of conventional car body manufacturing approaches. This study is crucial to evaluate the strengths and weaknesses of the competing philosophies of car body manufacturing in this evolving landscape.
4. Research Purpose and Research Questions:
Research Purpose:
The primary research purpose is to conduct a comprehensive comparison between large die casting technology and sheet metal shell construction for automotive body manufacturing. This comparison aims to delineate the advantages and disadvantages of each technology in the context of modern automotive production demands.
Key Research:
The key research objective is to evaluate the strengths and weaknesses of large-scale die casting versus sheet metal shell construction. This evaluation is based on published information and insights gathered from expert interviews within the die casting and automotive manufacturing sectors.
5. Research Methodology
Research Design:
The research employed a quantitative expert interview methodology. Initially, a target group of experts was identified through professional online platforms using die casting-related keywords. A structured questionnaire was then administered to this sample group.
Data Collection Method:
Data collection was achieved through the distribution and completion of questionnaires by experts in the field. A sample size of 24 complete expert questionnaires was utilized for quantitative analysis.
Analysis Method:
The collected questionnaire data underwent quantitative analysis to assess the current state of large die casting in comparison to sheet metal shell design. This analysis focused on comparing the two technologies across 14 predefined criteria relevant to car body manufacturing.
Research Subjects and Scope:
The research subjects comprised experts in die casting technology, categorized into "Foundry and Production," "Process and Technology Development," and "Research and Development" as shown in "Figure 3 Expert sample group composition". The scope of the research was limited to the comparative analysis of car body manufacturing technologies, specifically large-scale die casting and sheet metal shell construction.
6. Main Research Results:
Key Research Results:
The expert interviews revealed that in 11 out of 14 evaluated criteria, large-scale die casting was considered advantageous. While some criteria showed near parity between the two technologies, six criteria exhibited a distinctly clear outcome favoring one technology over the other. According to the interviewed experts, sheet metal design presented two indisputable advantages: product safety and repairability. Conversely, large-scale die casting was rated superior in light weight potential, production time savings, scalability, and space savings.
Regarding specific criteria:
- Product Safety: Despite favorable crash test results for vehicles utilizing large die casting parts, a challenge remains in part quality. "At the current state of the art lunkers and other casting errors are not completely avoidable for parts with the weight of 50 kg and above."
- Light Weight Potential: While some experts believed sheet metal forming could achieve comparable or superior results, the majority recognized die casting's advantage, primarily due to the lower specific weight of aluminum compared to steel and the reduction of multiple joining or bonding surfaces.
- Energy Consumption and CO2 Emission: Both technologies were rated similarly. However, considering the specific energy consumption of base materials, sheet metal forming using steel could be more sustainable in terms of CO2 emissions, contingent on the energy source used for aluminum production. "In CO2 emission in most cases steel would also be lower and therefore preferable to aluminium, but this is highly dependable on the energy source used for aluminium production."
- Repairability: "Building a car structure out of big casting parts has a great disadvantage when it comes to repairability." Repairing die cast structures after accidents is significantly more challenging than sheet metal, as welding is not feasible without altering material properties, potentially leading to total vehicle loss even from minor damage.
- Stiffness: Large Casting Parts can offer design flexibility for a greater area moment of inertia, potentially compensating for aluminum's lower Young's Modulus compared to steel. However, this is design-dependent, resulting in no clear technological advantage for either method.
- Quality and Tolerances: Large die castings face challenges with "lunkers and other casting errors." Dimensional accuracy is also not on par with sheet metal parts, although the reduction in joining points can partially offset this.
- Manual Labour Savings: Both technologies offer high automation potential. Die casting provides a slight edge due to fewer parts, despite potentially requiring more manual quality checks and deburring.
- Production Time Savings: Experts identified production time savings as a major advantage of large-scale die casting. "Although the big casting parts have a significantly higher cycle time than any sheet metal part, the reduction of parts and joining operations means a significant time saving."
- Scalability: Sheet metal shell design is proven scalable to millions of units. Die casting scalability is achieved by deploying more die casting machines.
- Investment Costs: Die casting machines represent substantial investment, comparable to press lines. The potential cost advantage of die casting stems from reduced downstream joining and assembly processes.
- Maintenance Savings: Sheet metal design holds a slight advantage in maintenance. While part reduction in die casting lowers tool count, "Die casting tools on the other hand are not only burdened with high pressures, but also high temperatures and aggressive liquid aluminium. This results in a significantly shorter time of these tools before they need to be serviced."
- Suitable for E-Mobility: "The design flexibility of large-scale die casting structures allows a high functional integration of the battery into the car body structure." This integration capability is a significant advantage for electric vehicle manufacturing.
- Space Savings: "According to expert information sheet metal car body manufacturing needs approximately double the footprint of large-scale die casting." Die casting machines have a smaller footprint than press lines and associated assembly infrastructure.
Analysis of presented data:
"Figure 6 Results of Expert Interview Questionnaire" visually summarizes the expert opinions across the 14 criteria, demonstrating a general trend favoring die casting, particularly in areas like lightweighting, production efficiency, and scalability, while acknowledging sheet metal's strengths in safety and repair. "Figure 7 Future Technology Preference of the interviewed" further emphasizes this trend, illustrating a clear preference among experts for die casting as the prioritized technology for future car body manufacturing.
Figure Name List:
![Figure 2 Change of car body parts due to large die casting a Tesla Model Y [6]](https://castman.co.kr/wp-content/uploads/image-1411-1024x278.webp)
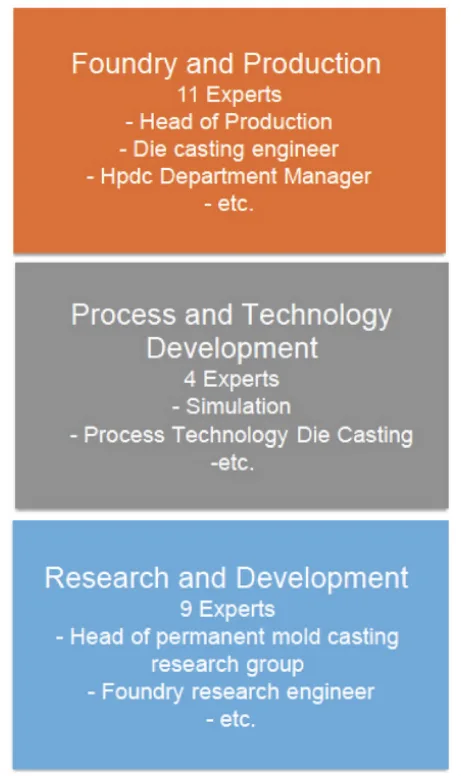
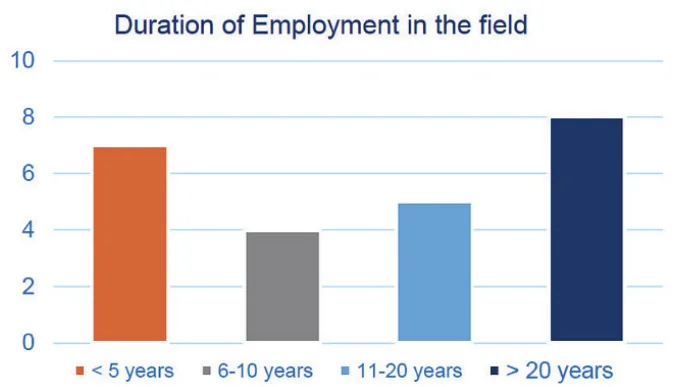
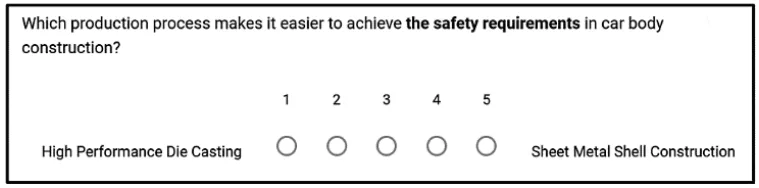
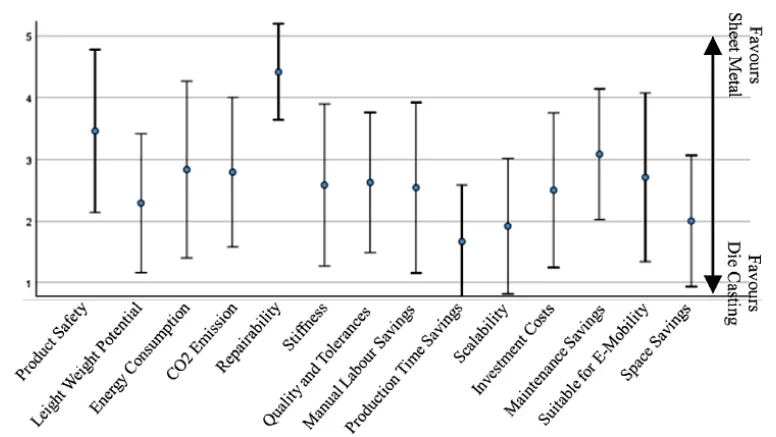
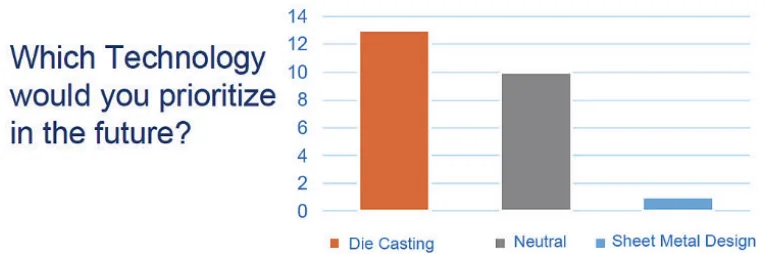
- Figure 1 Body with self-supporting shell construction ([3], p.18)
- Figure 2 Change of car body parts due to large die casting a Tesla Model Y [6]
- Figure 3 Expert sample group composition
- Figure 4 Expert sample group Working Experience.
- Figure 5 Example question of the expert interview
- Figure 6 Results of Expert Interview Questionnaire
- Figure 7 Future Technology Preference of the interviewed
7. Conclusion:
Summary of Key Findings:
The expert survey indicated a general preference for large-scale die casting over sheet metal shell construction in 11 out of 14 criteria relevant to car body manufacturing. Die casting was particularly favored for its lightweight potential, production time savings, scalability, and space efficiency. However, sheet metal construction retained advantages in product safety and repairability. It is crucial to note that these results are caveated by the expert group's potential bias towards die casting and the inherent importance of product safety and repairability in automotive design. Furthermore, the comparison was predicated on a Greenfield approach, which may not be universally applicable to all automotive manufacturers.
Academic Significance of the Study:
This study provides a valuable academic contribution by offering a structured and comprehensive comparison of large-scale die casting and sheet metal shell construction for car body manufacturing. It elucidates expert perspectives on the relative merits and drawbacks of each technology across a range of critical manufacturing criteria.
Practical Implications:
The findings suggest that large-scale die casting presents a compelling alternative to traditional sheet metal shell construction, particularly for electric vehicle manufacturing in Greenfield scenarios. Its advantages in lightweighting and production efficiency align with key trends in the automotive industry. However, the established sheet metal shell design remains relevant, especially for legacy automakers operating within existing infrastructure constraints. "Concluding, it can be said, that large-scale die casting is a powerful new alternative to car body manufacturing and offers some interesting potential especially for Battery Electric Vehicles, but is not a best fit solution for all automakers or all future projects."
Limitations of the Study and Areas for Future Research:
The study's limitations include the potential bias inherent in the expert sample group, which was primarily composed of die casting specialists. The Greenfield premise of the comparison may not fully reflect the realities faced by all automotive manufacturers, particularly those with established brownfield sites. Future research should further investigate the critical aspects of product safety and repairability in large-scale die casting applications, potentially through more diverse expert panels and real-world case studies in both Greenfield and Brownfield manufacturing environments.
8. References:
- [1] Horst, E. F. (Hrsg.) (2017). Leichtbau in der Fahrzeugtechnik, 2. Auflage. Wies-baden/Heidelberg: Springer Vieweg. (in German)
- [2] Fang, X. (2023). Karosserieentwicklung und -Leichtbau: Eine ganzheitliche Betrachtung von Design über Konzept- und Materialauswahlprinzipien bis zur Auslegung und Fertigung. Berlin/Heidelberg: Springer Vieweg. (in German)
- [3] Kühling, S. (2022). In der Gießereiwelt einmalig: VW-Mitarbeiter entwickeln neues Elektro-Auto-Teil. https://www.hna.de/lokales/kreis-kassel/baunatal-ort312516/ent-wickelt-baunataler-vw-mitarbeiter-haben-teil-fuer-neues-auto-91550655.html (in German) (Accessed on 2024-01-08)
- [4] Siebel, T. (2022). Wie sich das Mega-Casting auf die Zulieferer auswirkt. https://www.springerprofessional.de/urformen/automobilproduktion/wie-sich-das-mega-casting-auf-die-zulieferer-auswirkt/23776976 (in German) (Accessed on 2023-10-13)
- [5] Schuh, G. et al. (2022). Opportunities and Risks of Mega-Casting in Automotive Production The Aluminum Die-Casted Body in White. WT Werkstattstechnik, 112(9). https://doi.org/10.37544/1436-4980-2022-09-52
- [6] Ν. Ν. (2023). https://www.electrifiedmag.com/news/get-to-know-megacasting-hype-or-the-next-big-thing/
- [7] Imgrund, C. (2023). Neuplanung einer energieeffizienten (Automobil-)Fabrik. https://www.ingenics.com/de/blog/neuplanung-einer-energieeffizienten-automobil-fabrik/ (in German)
9. Copyright:
- This material is "Martin Bednarz"'s paper: Based on "Die Casting or Sheet Metal Forming: A Comparison of Car Body Manufacturing in Times of the "Giga Press"".
- Paper Source: https://doi.org/10.31803/tg-20240510165209
This material was created to introduce the above paper, and unauthorized use for commercial purposes is prohibited.
Copyright © 2025 CASTMAN. All rights reserved.