본 소개 내용은 [TECHNICAL JOURNAL 19, 1(2025), 58-61]에서 발행한 ["Die Casting or Sheet Metal Forming: A Comparison of Car Body Manufacturing in Times of the "Giga Press""] 의 연구 내용입니다.
![Figure 1 Body with self-supporting shell construction ([3], p.18)](https://castman.co.kr/wp-content/uploads/image-1410-1024x445.webp)
1. Overview:
- Title: Die Casting or Sheet Metal Forming: A Comparison of Car Body Manufacturing in Times of the "Giga Press" (다이캐스팅 또는 판금 성형: "기가 프레스" 시대의 자동차 차체 제조 비교)
- Author: Martin Bednarz
- Publication Year: 2025
- Publishing Journal/Academic Society: TECHNICAL JOURNAL 19, 1(2025), 58-61
- Keywords: car body manufacturing; large-scale die casting; sheet metal construction
2. Abstracts / Introduction
차체 디자인에서 판금 구조의 대안으로서의 다이캐스팅은 수년 동안 존재해 왔다. 기존 자동차 제조업체에 의한 다이캐스트 차체 부품의 적용은 특히 대량 시장 제품의 경우 다소 제한적이지만, 테슬라는 대량 생산차를 몇 개의 매우 큰 다이캐스트 구조 부품을 기반으로 한다. 이러한 전략의 영향으로 인해 차체 제조를 재고할 필요가 있다. 본 연구에서는 발표된 정보와 전문가 인터뷰를 사용하여 경쟁적인 차체 제조 철학의 강점과 약점을 평가하는 데 사용된다.
자동차 산업에서 차량 차체의 제조 기술의 지속적인 발전이 본 연구의 배경 동기이다. 대량 생산과 관련하여 점점 더 중요해지는 대형 다이캐스팅 기술과 판금 쉘 구조 방식이라는 두 가지 주요 기술이 결정적인 역할을 한다. 본 연구 작업의 일환으로, 목표는 이러한 두 가지 제조 공정 간의 포괄적인 비교를 하는 것이다. 자동차 산업은 효율성 및 비용 절감 증가부터 더 엄격한 환경 규제 충족에 이르기까지 끊임없는 과제에 직면해 있다. 올바른 제조 기술을 선택하는 것은 자동차 제조업체의 전반적인 성능과 경쟁력에 상당한 영향을 미칠 수 있다. 따라서 기존의 판금 쉘 구조 방식과 비교하여 대형 다이캐스팅 기술의 장점과 단점을 완전히 이해하는 것이 중요하다.
3. Research Background:
Background of the Research Topic:
자동차 산업에서 차량 차체 제조 기술은 지속적으로 발전하고 있으며, 특히 대량 생산에서 대형 다이캐스팅 기술과 판금 쉘 구조 방식이 중요한 역할을 한다. 자동차 제조업체는 효율성 향상, 비용 절감, 환경 규제 준수 등 다양한 과제에 직면해 있으며, 적절한 제조 기술 선택은 경쟁력에 큰 영향을 미친다. 따라서 대형 다이캐스팅 기술과 기존 판금 쉘 구조 방식의 장단점을 명확히 이해하는 것이 중요하다.
Status of Existing Research:
기존 연구에서는 차체 제조에 있어 판금 쉘 구조가 표준으로 사용되어 왔으며, 강철 또는 알루미늄 하프 쉘을 연결하는 섀시 구조 방식이다 [1]. 최근에는 메가캐스팅 또는 기가캐스팅으로 불리는 대형 다이캐스팅 공정이 자동차 산업에서 변화를 주도하고 있으며, 기존 다이캐스팅 공정에 비해 시스템 크기가 다르다 [4]. 하지만, 복잡한 다이캐스팅 공정에 대한 지식과 경험 부족으로 인해 재현 가능한 품질에 대한 과제가 남아 있으며 [5], 부품 품질, 기공 형성, 수리 가능성 등의 문제도 여전히 해결해야 할 과제이다 [5].
Necessity of the Research:
자동차 산업은 지속적인 효율성 향상 및 비용 절감 압력과 환경 규제 강화에 직면해 있다. 차체 제조 기술 선택은 자동차 제조업체의 경쟁력에 중요한 영향을 미치므로, 대형 다이캐스팅 기술과 기존 판금 쉘 구조 방식의 장단점을 비교 분석하는 연구가 필요하다. 특히 테슬라와 같은 기업이 대형 다이캐스팅을 실제 차량 생산에 적용하면서, 두 제조 방식에 대한 심층적인 비교 연구의 필요성이 더욱 커지고 있다.
4. Research Purpose and Research Questions:
Research Purpose:
본 연구의 목적은 대형 다이캐스팅 기술과 판금 쉘 구조 방식, 이 두 가지 차체 제조 공정을 종합적으로 비교 분석하는 것이다. 특히, 전문가 인터뷰와 기존 정보를 활용하여 각 제조 방식의 강점과 약점을 평가하고, 미래 자동차 산업에서 대형 다이캐스팅 기술의 잠재력을 탐색하고자 한다.
Key Research:
- 대형 다이캐스팅과 판금 쉘 구조 방식의 차체 제조 공정 비교 분석
- 전문가 인터뷰 및 기존 정보 활용
- 각 제조 방식의 강점 및 약점 평가
- 미래 자동차 산업, 특히 전기 자동차 분야에서 대형 다이캐스팅 기술의 잠재력 평가
5. Research Methodology
Research Design:
본 연구는 전문가 인터뷰를 정량적으로 분석하는 방식으로 진행되었다. 다이캐스팅 관련 키워드를 사용하여 인터넷 전문 플랫폼에서 전문가 그룹을 식별하고, 설문지를 제공하여 데이터를 수집하였다. 총 24명의 전문가 설문지를 분석하여 대형 다이캐스팅과 판금 쉘 디자인의 현황을 정량적으로 분석하였다.
Data Collection Method:
전문가 인터뷰는 설문지 기반으로 진행되었다. 설문지는 다이캐스팅 관련 키워드를 사용하여 인터넷 전문 플랫폼에서 모집된 전문가 그룹에게 배포되었다. 총 24명의 전문가로부터 설문지를 회수하여 분석에 사용하였다. Figure 3은 전문가 샘플 그룹 구성을 나타낸다.
Analysis Method:
수집된 설문지 데이터를 정량적으로 분석하였다. 설문 문항은 14가지 기준 (Table 1) 에 따라 판금 설계와 다이캐스팅을 비교하는 방식으로 구성되었다. 각 문항은 5점 척도로 평가되었으며, 옵션 "1"은 다이캐스팅에 매우 유리, 옵션 "5"는 판금에 매우 유리, 옵션 "3"은 중립 옵션이다. Figure 5는 전문가 인터뷰 설문 예시를 보여준다. Figure 6은 전문가 인터뷰 설문 결과이다.
Research Subjects and Scope:
본 연구의 대상은 다이캐스팅 분야의 전문가 24명이다. 전문가들은 주조 산업에 장기간 종사한 경험이 있으며, 샘플 그룹의 대부분은 20년 이상의 경력을 가지고 있다 (Figure 4). 설문 조사는 자동차 차체 제조 기술, 특히 대형 다이캐스팅과 판금 쉘 구조 방식에 대한 전문가의 인식을 조사하는 데 초점을 맞추었다.
6. Main Research Results:
Key Research Results:
전문가 인터뷰 결과, 14가지 기준 중 11가지 기준에서 전문가들은 대형 다이캐스팅이 유리하다고 평가했다. 특히 경량화 잠재력, 생산 시간 절약, 확장성, 공간 절약 측면에서 대형 다이캐스팅의 우수성이 두드러졌다. 반면, 제품 안전과 수리 용이성 측면에서는 판금 설계가 유리하다는 평가를 받았다. Figure 6은 전문가 인터뷰 설문 결과를 시각적으로 보여준다.
Analysis of presented data:
Figure 6의 결과를 보면, 대부분의 기준에서 다이캐스팅이 판금 쉘 구조보다 유리하거나 동등한 것으로 평가되었다. 특히, "Leight Weight Potential (경량화 잠재력)", "Production Time Savings (생산 시간 절약)", "Scalability (확장성)", "Space Savings (공간 절약)" 항목에서 다이캐스팅이 뚜렷한 강점을 보이는 것으로 나타났다. 반면, "Product Safety (제품 안전)" 와 "Repairability (수리 용이성)" 항목에서는 판금 쉘 구조가 다이캐스팅보다 우수하다는 평가를 받았다. 이는 대형 다이캐스팅 부품의 품질 문제와 수리 어려움 때문으로 분석된다.
Figure Name List:
- Figure 1 Body with self-supporting shell construction ([3], p.18)
- Figure 2 Change of car body parts due to large die casting a Tesla Model Y [6]
- Figure 3 Expert sample group composition
- Figure 4 Expert sample group Working Experience.
- Figure 5 Example question of the expert interview
- Figure 6 Results of Expert Interview Questionnaire
- Figure 7 Future Technology Preference of the interviewed
![Figure 2 Change of car body parts due to large die casting a Tesla Model Y [6]](https://castman.co.kr/wp-content/uploads/image-1411-1024x278.webp)
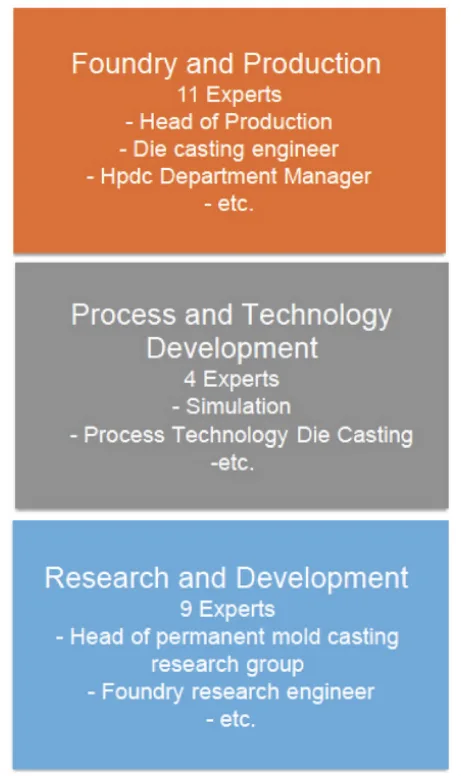
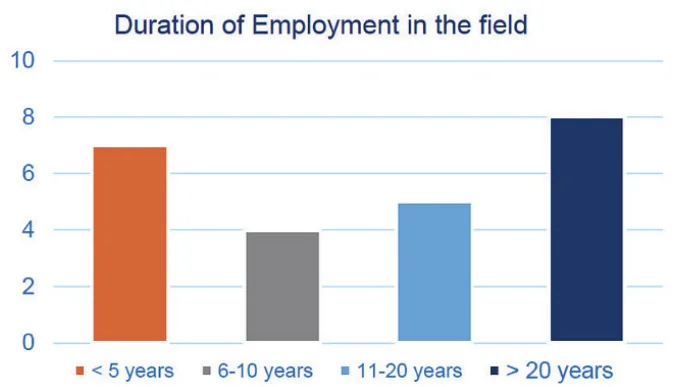
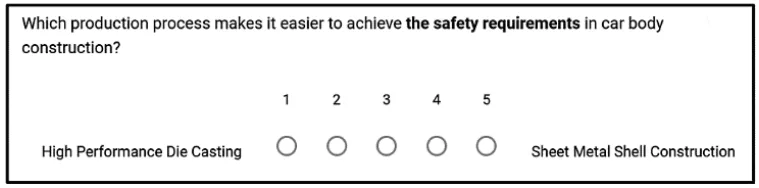
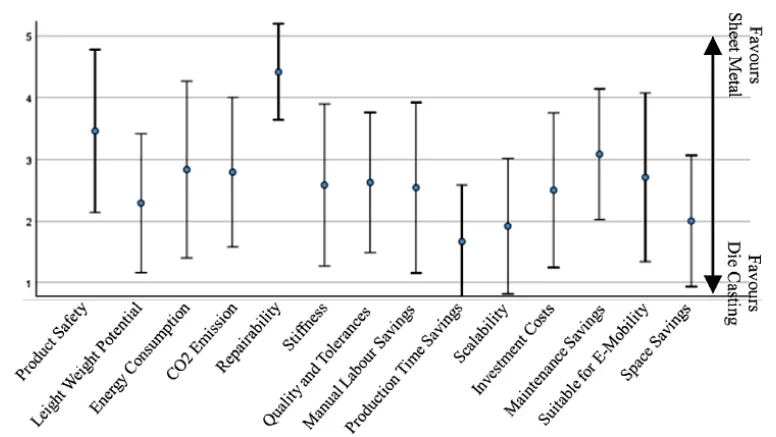
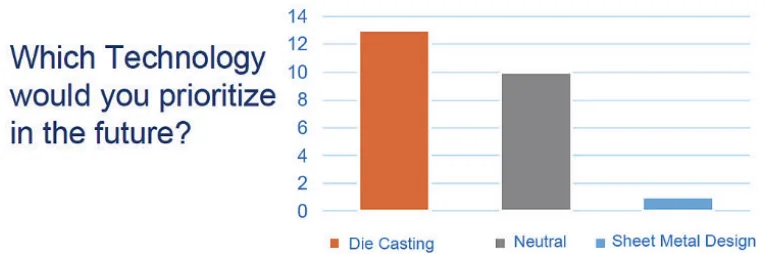
7. Conclusion:
Summary of Key Findings:
전문가 인터뷰 결과, 대형 다이캐스팅 기술은 경량화, 생산 시간, 확장성, 공간 효율성 측면에서 판금 쉘 구조 방식보다 우수한 것으로 평가되었다. 반면, 제품 안전과 수리 용이성은 판금 쉘 구조 방식의 강점으로 나타났다. 전반적으로 전문가들은 미래 자동차 제조, 특히 전기 자동차 분야에서 대형 다이캐스팅 기술의 잠재력을 높게 평가했다 (Figure 7).
Academic Significance of the Study:
본 연구는 대형 다이캐스팅 기술과 판금 쉘 구조 방식이라는 두 가지 주요 차체 제조 기술을 체계적으로 비교 분석했다는 점에서 학문적 의의를 갖는다. 특히 전문가 인터뷰를 통해 실제 산업 현장의 의견을 반영하여 실증적인 분석 결과를 제시하였다. 이는 자동차 제조 기술 분야의 연구 및 개발 방향 설정에 기여할 수 있을 것으로 기대된다.
Practical Implications:
본 연구 결과는 자동차 제조업체가 차체 제조 기술을 선택할 때 유용한 정보를 제공한다. 특히 전기 자동차와 같이 경량화 및 생산 효율성이 중요한 분야에서 대형 다이캐스팅 기술의 도입을 고려할 수 있는 근거를 제시한다. 다만, 제품 안전 및 수리 용이성 측면의 단점을 보완하기 위한 추가적인 연구 및 기술 개발이 필요하다.
Limitations of the Study and Areas for Future Research:
본 연구는 다이캐스팅 분야 전문가 그룹을 대상으로 인터뷰를 진행하여 다이캐스팅 기술에 대한 편향이 있을 수 있다는 점을 감안해야 한다. 또한, 제품 안전 및 수리 용이성 측면에서 판금 쉘 구조 방식의 장점이 명확히 나타났으므로, 대형 다이캐스팅 기술의 안전성 및 수리 용이성을 개선하기 위한 연구가 필요하다. 미래 연구에서는 다양한 전문가 그룹의 의견을 수렴하고, 기술 개발 동향 및 경제성 분석 등을 종합적으로 고려하여 보다 심층적인 비교 연구를 수행할 필요가 있다.
8. References:
- [1] Horst, E. F. (Hrsg.) (2017). Leichtbau in der Fahrzeugtechnik, 2. Auflage. Wies-baden/Heidelberg: Springer Vieweg. (in German)
- [2] Fang, X. (2023). Karosserieentwicklung und -Leichtbau: Eine ganzheitliche Betrachtung von Design über Konzept- und Materialauswahlprinzipien bis zur Auslegung und Fertigung. Berlin/Heidelberg: Springer Vieweg. (in German)
- [3] Kühling, S. (2022). In der Gießereiwelt einmalig: VW-Mitarbeiter entwickeln neues Elektro-Auto-Teil. https://www.hna.de/lokales/kreis-kassel/baunatal-ort312516/ent-wickelt-baunataler-vw-mitarbeiter-haben-teil-fuer-neues-auto-91550655.html (in German) (Accessed on 2024-01-08)
- [4] Siebel, T. (2022). Wie sich das Mega-Casting auf die Zulieferer auswirkt. https://www.springerprofessional.de/urformen/automobilproduktion/wie-sich-das-mega-casting-auf-die-zulieferer-auswirkt/23776976 (in German) (Accessed on 2023-10-13)
- [5] Schuh, G. et al. (2022). Opportunities and Risks of Mega-Casting in Automotive Production The Aluminum Die-Casted Body in White. WT Werkstattstechnik, 112(9). https://doi.org/10.37544/1436-4980-2022-09-52
- [6] Ν. Ν. (2023). https://www.electrifiedmag.com/news/get-to-know-megacasting-hype-or-the-next-big-thing/
- [7] Imgrund, C. (2023). Neuplanung einer energieeffizienten (Automobil-)Fabrik. https://www.ingenics.com/de/blog/neuplanung-einer-energieeffizienten-automobil-fabrik/ (in German)
9. Copyright:
- This material is "Martin Bednarz"'s paper: Based on "Die Casting or Sheet Metal Forming: A Comparison of Car Body Manufacturing in Times of the "Giga Press"".
- Paper Source: https://doi.org/10.31803/tg-20240510165209
This material was created to introduce the above paper, and unauthorized use for commercial purposes is prohibited.
Copyright © 2025 CASTMAN. All rights reserved.