Duoc T Phan, Syed H Masood*, Syed H Riza, and Harsh Modi
Department of Mechanical and Product Design Engineering, Swinburne University of Technology, Hawthorn, Melbourne, Australia
*Email: smasood@swin.edu.au
Abstract
In High Pressure Die Casting (HDPC) process, chill vents are used to allow residual air and gases to exhaust out from the mould cavity. The objective of this paper is to design and develop a high-performance chill vent for high pressure die casting using a new type of copper alloy material, which has high strength and high thermal conductivity, compared to conventional tool steel. Finite element analysis is applied to develop a numerical heat transfer model for chill vent and validated by experimental results. The model is used to compare the performance of copper alloy chill vent with conventional steel chill vent. It was found that the change in the chill vent material had a significant improvement on the cooling time, cooling rate as well as on the internal die temperature distribution. Results show that the copper chill vent increases the cooling efficiency of the solidifying aluminium alloy by about 158% compared to the conventional steel chill vents. It is concluded that the use of high strength copper alloy chill vents will enhance the efficiency and effectiveness of HPDC process with rapid heat transfer and faster release of gases, thus reducing porosity and flashing defects in the parts.
Index Terms
High pressure die casting; Chill vents; Thermal analysis; Copper alloy; Thermal conductivity; Cooling rates
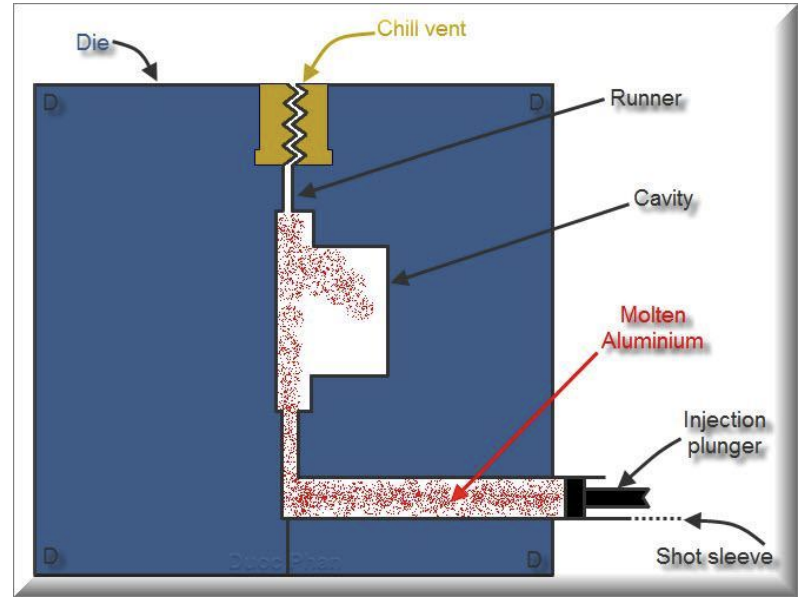
REFERENCES
[1] A Kaye, A Street. Die Casting Metallurgy. Butterworth and Co
Ltd., 1982
[2] F. Bonollo, N. Gramegna, and G. Timelli, “High-pressure diecasting: contradictions and challenges,” The Minerals, Metals &
Materials Society, JOM, vol. 67, no. 5, pp. 901-908, 2015.
[3] L. H. Wang. “Mathematical modelling of air evacuation in die
casting process via CASTvac and other venting devices,” Int
Journal of Cast Metals Research, vol. 20 pp. 191- 197, 2007.
[4] MoldMAX HH Material Property Data, Materion Performance
Alloys, Materion Corporation 2017.
[5] I. Rosindale and K. Davey, “Steady state thermal model for the
hot chamber injection system in the pressure die casting process,”
Journal of Materials Processing Technology, vol. 82, no. 1, pp.
27-45, 1998.
[6] M. T. A. Rasgado, “Bi-metallic dies for rapid die casting,”
Journal of Materials Processing Technology vol. 175, pp. 109–
116, 2006.
[7] S. R. Ahmed, K. D. Devi, and S. V. S. Himathejeswini, “Design
& analysis of heat sink high-pressure die casting component,”
International Journal of Current Engineering and Technology,
2016
[8] H. J. Kwon, H. K. Kwon, “Computer Aided Engineering (CAE)
simulation for the design optimization of gate system on high
pressure die casting (HPDC) process,” Robotics and Computer–
Integrated Manufacturing vol. 55 pp. 147–153, 2018.
[9] W. B. Yu, Y. Y. Cao, X. B. Li et al, “Determination of interfacial
heat transfer behavior at the metal/shot sleeve of high pressure
die casting process of AZ91D alloy,” Journal of Materials
Science & Technology vol. 33 pp. 52–58, 2017
[10] S. I. Jeong, C. K. Jin, H. Y. Seo et al, “Mould design for clutch
housing parts using a casting simulation of high pressure die
casting,” International Journal Of Precision Engineering And
Manufacturing, vol. 17, no. 11, pp. 1523-1531, 2016
[11] R. W. R. W. Jeppson, Analysis of Flow in Pipe Networks,
Butterworth Publications, 1976
[12] MatWeb Material Property Data, Aluminum ADC12 Die Casting
Alloy, Automation Creations, Inc 2009.
[13] K. N. Prabhu, “Casting/mold thermal contact heat transfer during
solidification of Al-Cu-Si alloy (LM 21) plates in thick and thin
molds,” Journal of Materials Engineering and Performance,
ASM International vol. 14, no. 5, pp. 604-609, 2005.