This paper introduction was written based on the ['Design of Three Cavity Diecasting Die for Rotors'] published by ['International Journal of Engineering Research & Technology (IJERT)'].
1. Overview:
- Title: Design of Three Cavity Diecasting Die for Rotors
- Author: S Chandra Sekhar, Sk.Surjan, M.S. Phani Deep Kumar
- Publication Year: 2017
- Publishing Journal/Academic Society: International Journal of Engineering Research & Technology (IJERT)
- Keywords: Design, Die casting, CATIA, Rotors
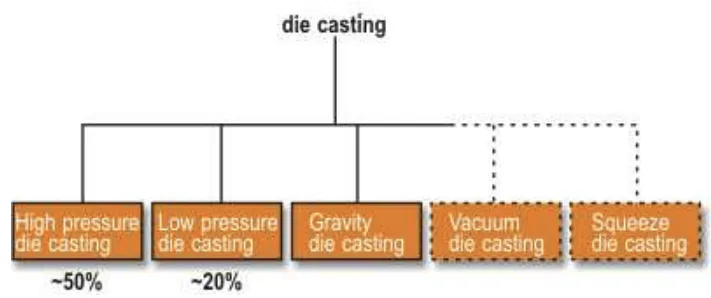
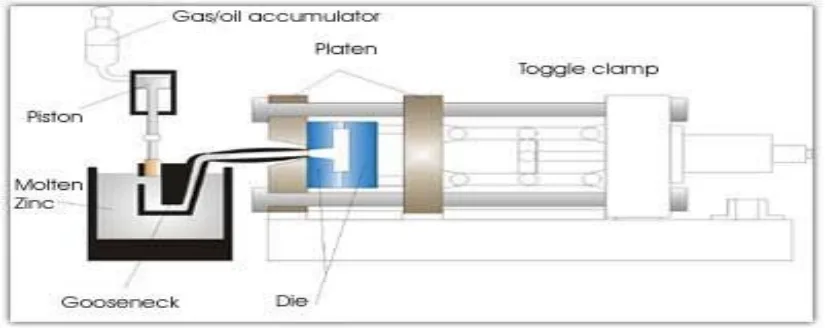
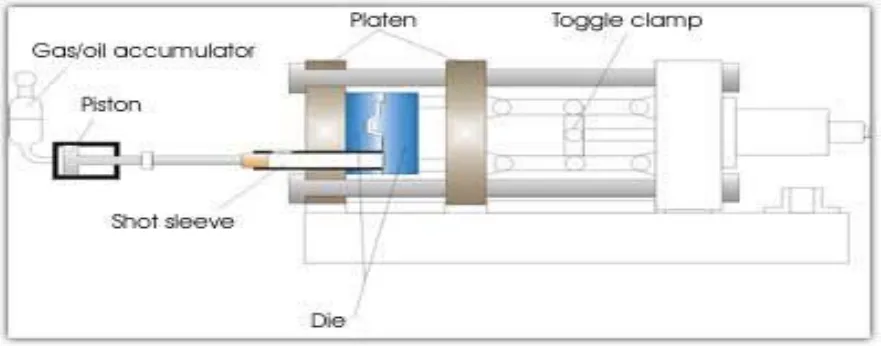
2. Abstracts or Introduction
Abstract
"Die casting components play an important role in every aspects of modern world. Their influence ranges from house hold utensils to automobile components. Requirement of today's world is production, accuracy and interchangeability, which helps to meet the competition. In order to meet these challenges die casting process plays an important role in production. Mass Production aims at high productivity to reduce unit cost and interchangeability to facilitate easy assembly. For die casting components there is no need for further machining and getting components with good surface finish. The Computer Aided Design which helps to reduce the design and production lead time. This paper gives an engineering approach towards design of die casting die for rotors and deals with the design of a three cavity die casting die by using the CATIA V5 Software. In this work the computer aided design of three cavity die casting die is the replacement of traditional design of two cavity die casting die for rotors which is existed.In this paper we also replace cavity and core impressions on hcher block with hchcr inserts.
Keywords- Design, Die casting, CATIA, Rotors"
I. INTRODUCTION
"Die castings are highest volume, mass-produced items manufactured by the metalworking industry, and they can be found in thousands of consumer, commercial and industrial products. Die cast parts are important components of products ranging from automobiles to toys. Parts can be as simple as a sink faucet or as complex as a connector housing. The earliest examples of die casting by pressure injection as opposed to casting by gravity pressure occurred in the mid-1800s. A patent was awarded to sturges in 1849 for the first manually operated machine for casting printing type. The process was limited to printer's type for the next 20 years, but development of other shapes began to increase toward the end of the century. By 1892, commercial applications included parts for phonographs and cash registers, and mass production of many types of parts began in the early 1900s. The first die casting alloys were various compositions of tin and lead, but their use declined with the introduction of zinc and aluminum alloys in 1914. Magnesium and copper alloys quickly followed, and by the 1930s, many of the modern alloys come in to existence and become available. The die casting process has evolved from the original low-pressure injection method to techniques including high-pressure casting at forces exceeding 4500 pounds per square inch squeeze casting and semi-solid die casting. These modern processes are capable of producing high integrity, near net-shape castings with excellent surface finishes. Refinements continue in both the alloys used in die casting and the process itself, expanding die casting applications into almost every known market. Once limited to simple lead type, today's die casters can produce castings in a variety of sizes, shapes and wall thicknesses that are strong, durable and dimensionally precise."
3. Research Background:
Background of the Research Topic:
The paper highlights the critical role of die casting in contemporary manufacturing, emphasizing its extensive applicability from household items to automotive components. Modern industrial demands necessitate high production volumes, dimensional accuracy, and component interchangeability. Die casting effectively addresses these requirements, offering advantages in mass production scenarios by enhancing productivity, minimizing unit costs, and ensuring ease of assembly. Furthermore, die cast components often negate the need for extensive post-casting machining, achieving desirable surface finishes directly from the mold. The integration of Computer-Aided Design (CAD) is underscored as a pivotal factor in streamlining both the design and production phases, reducing lead times and improving overall efficiency.
Status of Existing Research:
Prior to this research, the prevalent die design for rotor production utilized a two-cavity configuration. This traditional approach, while functional, presented limitations in achieving higher production rates necessary to meet escalating industrial demands.
Necessity of the Research:
The impetus for this research stems from the need to enhance productivity in rotor die casting. The study addresses this by proposing a transition from the conventional two-cavity die to a more efficient three-cavity die design. Additionally, the paper aims to optimize die longevity and reduce manufacturing costs by advocating for the replacement of integral cavity and core impressions on the bolster block with hardened and tempered chromium hot-work tool steel (HCHCr) inserts. This modular approach facilitates easier maintenance and replacement of high-wear components, thereby extending the die's operational lifespan and reducing overall tooling expenditure.
4. Research Purpose and Research Questions:
Research Purpose:
The primary objective of this research is to engineer a three-cavity die casting die specifically for rotors, leveraging the capabilities of CATIA V5 software for design and simulation. This design aims to supersede the existing two-cavity die paradigm, offering enhanced production efficiency. A secondary, yet crucial, purpose is to incorporate HCHCr inserts for the cavity and core regions. This strategic material selection and design modification is intended to improve die durability, simplify maintenance, and reduce long-term operational costs associated with die wear and replacement.
Key Research:
This study centers on the design and analysis of a three-cavity die casting die. Key research areas include:
- Multi-Cavity Die Design: Developing a die configuration that accommodates three rotor cavities to increase production output per cycle.
- CAD Application: Utilizing CATIA V5 software for the entire design process, from conceptualization to detailed engineering drawings and assembly modeling.
- Two-to-Three Cavity Die Transition: Engineering a direct replacement for existing two-cavity dies, ensuring compatibility with current die casting machinery while enhancing productivity.
- HCHCr Inserts Implementation: Designing and integrating HCHCr inserts for critical wear components (cavity and core) to improve die life and reduce maintenance.
Research Hypotheses:
While not explicitly stated as formal hypotheses, the research is predicated on the following expected outcomes:
- Increased Productivity: The three-cavity die will demonstrably increase the number of rotor castings produced per cycle compared to a two-cavity die, leading to higher overall production rates.
- Reduced Operational Costs: The use of HCHCr inserts will decrease die maintenance frequency and costs due to the enhanced wear resistance and replaceable nature of the inserts.
- Improved Design Efficiency: Employing CATIA V5 will streamline the design process, reduce design errors, and shorten the lead time for die development and manufacturing.
5. Research Methodology
Research Design:
The research employs a Computer-Aided Design (CAD) driven approach. The entire die assembly, including individual components and the multi-cavity configuration, is designed and virtually assembled using CATIA V5 software. This methodology allows for precise dimensional control, interference checking, and visualization of the complete die structure before physical manufacturing.
Data Collection Method:
The primary data in this research is generated through the design process itself. This includes:
- CAD Models: Creation of detailed 3D models of all die components (fixed half, moving half, cavity inserts, core inserts, runners, gates, etc.) within CATIA V5.
- Engineering Drawings: Production of 2D engineering drawings derived from the 3D models, specifying dimensions, tolerances, materials, and heat treatment requirements for manufacturing.
- Calculated Parameters: Determination of critical die casting parameters such as gate velocity, gate area, runner dimensions, injection pressure, and die locking force through established empirical formulas and die casting principles. These calculations are based on the material properties of the aluminum alloy and the geometry of the rotor component.
Analysis Method:
The analysis in this study is primarily based on engineering calculations and CAD software capabilities:
- Volumetric and Area Calculations: CATIA V5 is used to calculate volumes of the casting, runner system, and biscuit, as well as projected areas for determining clamping force.
- Empirical Formulae Application: Established die casting equations and empirical data (e.g., Table I. Typical Cavity Fill Times According To Wall Thickness and Table II. GATE VELOCITIES) are utilized to calculate gate size, runner dimensions, injection parameters, and locking force.
- Software Visualization and Validation: CATIA V5's visualization tools are used to ensure proper assembly, identify potential design flaws, and validate the overall die design before physical implementation.
Research Subjects and Scope:
The subject of this research is the design of a die casting die specifically for rotors. The scope is limited to:
- Die Design: Focusing on the complete design of a three-cavity cold-chamber die casting die.
- Component Material: Utilizing ALUMINIUM WROUGHT ALLOY with 99.6% pure Aluminum and 0.4% other metals for the rotor casting.
- Die Material Selection: Specifying materials for die components, including H13 steel for cavity and core inserts and EN-31, EN-36, OHNS, and M.S. for other die parts as detailed in Table V. Bill of Materials.
- Machine Compatibility: Designing the die to be compatible with a 400 T Buhler horizontal cold-chamber die casting machine.
6. Main Research Results:
Key Research Results:
The primary outcome of this research is the complete CAD design of a three-cavity die casting die for rotors, achieved using CATIA V5 software. Key results include:
- Three-Cavity Die Design: A fully detailed design for a three-cavity die, replacing the traditional two-cavity setup, is presented through isometric and sectional views (Fig: 8 Fixed half assembly of three cavity die, Fig: 9 Moving half assembly of three cavity die, Fig: 10 Total assembly of three cavity die, Fig: 11 Total assembly of three cavity die drawing).
- Detailed Component Design: Individual components of the die, including cavity inserts, core inserts, runner system, gating, ejector system, and bolster plates, are designed and specified with materials and dimensions as listed in Table V. Bill of Materials.
- Calculated Die Casting Parameters: Critical process parameters were calculated, including:
- Gate velocity: 3760cm/sec
- Fill rate: 8130 cm³/sec
- Injection pressure: 700 kg/cm²
- Locking force: 202.65 tonnes
- Production Rate Increase: The designed three-cavity die is projected to increase production from 2160 components per day (for a two-cavity die) to 3240 components per day, based on cycle time analysis.
Analysis of presented data:
The paper presents various figures and tables to support the design and analysis:
- Fig: 1 Types of die casting: Illustrates different die casting processes, highlighting the prevalence of high-pressure die casting.
- Fig: 2 Hot-Chamber Die Casting Machine & Fig: 3 Cold-Chamber Die Casting Machine: Depicts the schematics of hot and cold chamber die casting processes, relevant to the chosen cold-chamber approach for aluminum.
- Fig: 4 Traditional two cavity fixed half die & Fig: 5 Traditional two cavity moving half die: Shows sectional views of a conventional two-cavity die, providing a baseline for comparison.
- Fig: 6 Rotor lamination part & Fig: 7 Rotor Die casted component: Illustrates the rotor component, both as a lamination and the final die casting.
- Fig: 8 Fixed half assembly of three cavity die & Fig: 9 Moving half assembly of three cavity die: Presents isometric views of the designed three-cavity die halves.
- Fig: 10 Total assembly of three cavity die & Fig: 11 Total assembly of three cavity die drawing: Shows the complete assembled die in isometric and sectional views, detailing component arrangement.
- Table I. Typical Cavity Fill Times According To Wall Thickness & Table II. GATE VELOCITIES: Provides empirical data used for calculating gate parameters based on wall thickness and alloy type.
- Table III. Horizontal cold-chamber pressure die casting machine 400 T Buhler Specifications & Table IV. Production data: Specifies the machine parameters and production data relevant to the die design and performance calculations.
- Table V. Bill of Materials: Lists all die components with materials, dimensions, and heat treatment specifications for manufacturing.
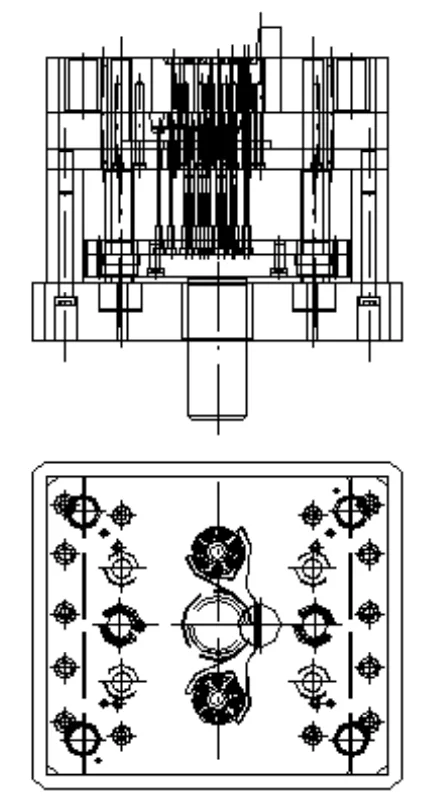
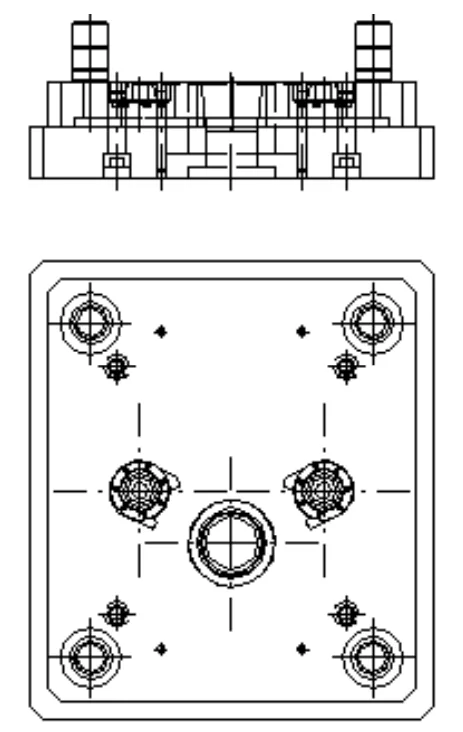
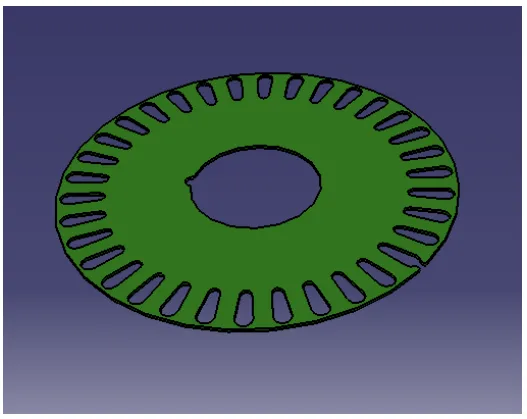
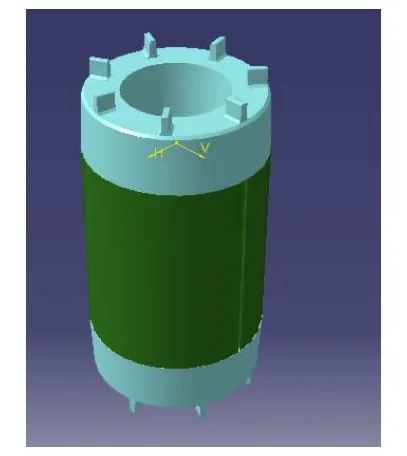
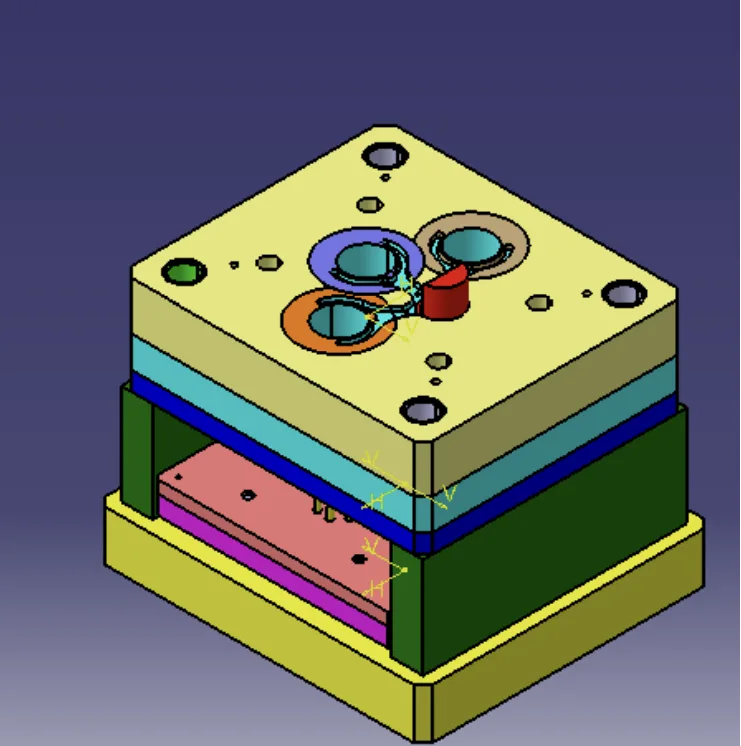
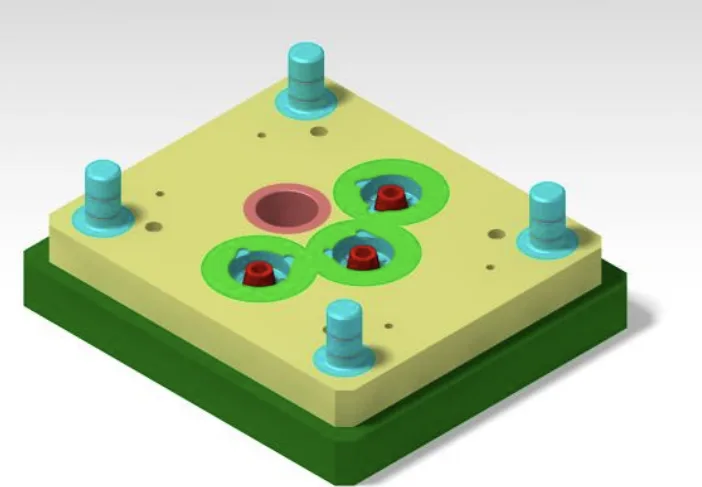
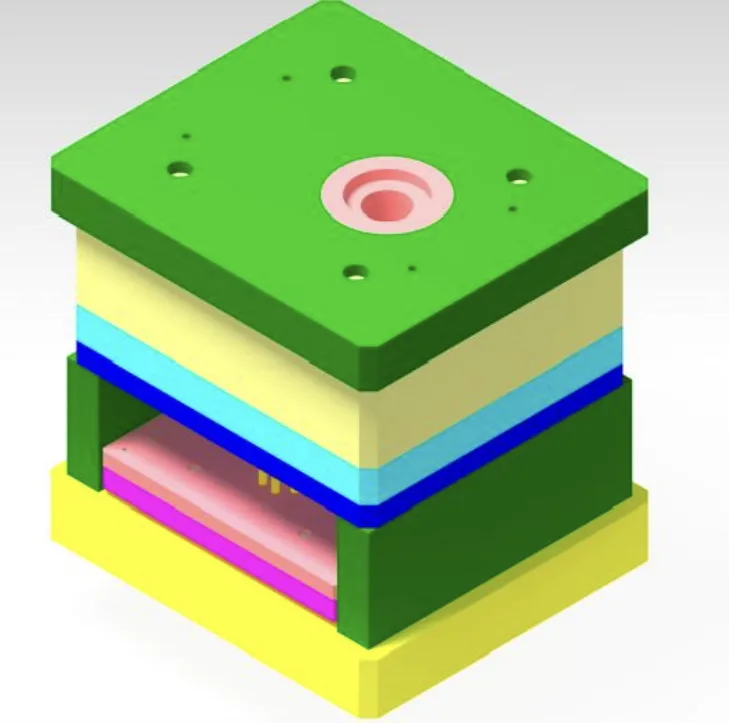
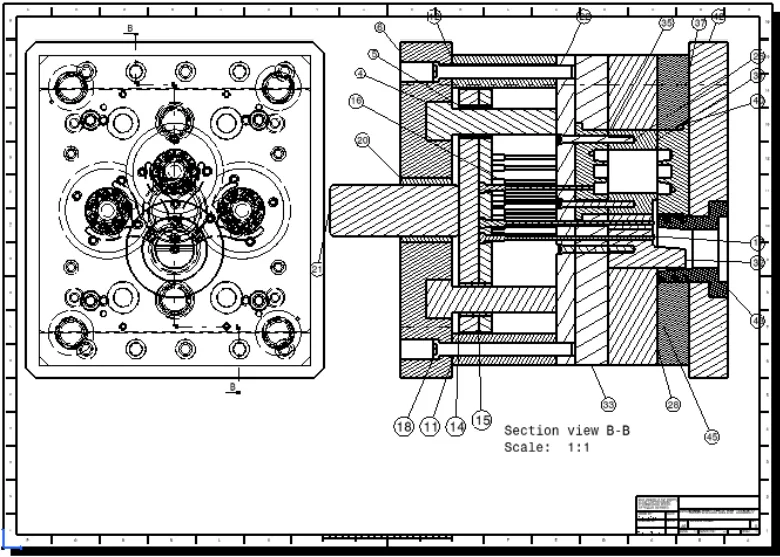
The data presented demonstrates a systematic approach to die design, incorporating empirical data and engineering calculations to achieve a functional and efficient three-cavity die. The projected production increase from 2160 to 3240 components per day underscores the efficiency gains from the three-cavity design.
Figure Name List:
- Fig: 1 Types of die casting
- Fig: 2 Hot-Chamber Die Casting Machine
- Fig: 3 Cold-Chamber Die Casting Machine
- Fig: 4 Traditional two cavity fixed half die
- Fig: 5 Traditional two cavity moving half die
- Fig: 6 Rotor lamination part
- Fig: 7 Rotor Die casted component
- Fig: 8 Fixed half assembly of three cavity die
- Fig: 9 Moving half assembly of three cavity die
- Fig: 10 Total assembly of three cavity die
- Fig: 11 Total assembly of three cavity die drawing
7. Conclusion:
Summary of Key Findings:
The research successfully demonstrated the design of a three-cavity die casting die for rotors using CAD technology. Key findings include:
- CAD-Enhanced Design: Implementation of CAD significantly improves design accuracy and reduces design lead time compared to traditional methods.
- Increased Productivity: The transition to a three-cavity die configuration demonstrably increases the number of components produced per casting cycle, leading to enhanced productivity.
- Cost and Maintenance Reduction: Utilizing a three-cavity die is projected to decrease labor and maintenance costs per unit output compared to a two-cavity die system.
- Modular Die Design with Inserts: The incorporation of replaceable cavity and core inserts made from HCHCr steel reduces die manufacturing costs and simplifies maintenance. Damage to critical areas necessitates only insert replacement, avoiding the expense of replacing entire die plates.
Academic Significance of the Study:
This study contributes to the field of die casting by:
- Illustrating CAD Application: Providing a practical example of applying CAD software (CATIA V5) for the comprehensive design of complex die casting tooling.
- Demonstrating Multi-Cavity Die Benefits: Quantifying the productivity gains achievable through the implementation of multi-cavity dies in high-volume production scenarios.
- Highlighting Modular Die Design Advantages: Emphasizing the benefits of modular die design using inserts for improved maintainability and cost-effectiveness in die casting.
Practical Implications:
The outcomes of this research offer significant practical implications for the die casting industry:
- Industry Adoption: Die casting manufacturers can directly adopt the three-cavity die design presented for rotor production to enhance their output capacity.
- CAD Implementation Encouragement: The study underscores the value of integrating CAD tools into die design workflows for improved efficiency and accuracy.
- Modular Tooling Strategy: The use of cavity and core inserts should be considered as a standard practice in die design to minimize tooling costs and downtime associated with maintenance and repairs.
Limitations of the Study and Areas for Future Research:
This study is primarily focused on the design phase and associated calculations. Limitations include:
- Lack of Experimental Validation: The research does not include physical manufacturing and testing of the designed three-cavity die. The projected production increase is based on calculations and cycle time estimations, not empirical testing.
- Simulation Scope: While CAD design is comprehensive, the paper does not detail advanced simulation (e.g., mold filling, thermal analysis) to further optimize the die design and process parameters.
Future research directions could include:
- Die Manufacturing and Testing: Fabricating the designed three-cavity die and conducting physical die casting trials to validate the predicted performance and identify areas for refinement.
- Process Optimization: Performing mold filling and thermal simulations to optimize gate design, runner system, cooling channels, and process parameters for enhanced casting quality and cycle time reduction.
- Material and Process Exploration: Investigating alternative die materials and advanced die casting processes (e.g., vacuum die casting, squeeze casting) to further improve rotor casting production.
8. References:
- [1] A. P.Wadekar1, B.A.Ahire, L.G.Navalel, S.H.Gawande, R.Mathai, R.Mishra "Die Casting Defect Analysis & Experimental Validation for Compressor Housing" IOSR Journal of Mechanical and Civil Engineering (IOSR-JMCE) ISSN(e): 2278- 1684, ISSN(p): 2320-334X, PP: 55-61
- [2] M.R. Barone, D.A. Caulk, "Analysis of liquid metal flow in die casting", International Journal of Engineering Science 38 (24), (2000), pp. 1279-1302
- [3] RyosukeKimuraa, Haruaki Hatayamaa, Kenji Shinozakia, Izumi Murashimab, Jo Asadab, Makoto Yoshidac, "Effect of grain refiner and grain size on the susceptibility of Al-Mg die casting alloy to cracking during solidification", journal of materials processing technology 209 (1) (2009) pp.210-219.
- [4] PenghuaiFua, Alan A. Luob, HaiyanJianga, Liming Penga, YandongYua, ChunquanZhaia, Anil K. Sachdev, "Low-pressure die casting of magnesium alloy AM50: Response to process parameters", journal of materials processing technology 205 (2008) pp.224-234.
- [5] B.S. Sunga, I.S. Kimb, "The molding analysis of automobile parts using the die-casting system", journal of materials processing technology 201 (2009) pp. 635-639.
- [6] H.D. Zhao, F. Wang, "Modeling of mold filling of Al gravity casting and validation with X-ray in-situ observation", Journal of Materials Processing Technology 209 (2009) pp. 4537-4542.
- [7] Paul Cleary, Joseph Ha, Vladimir Alguine, Thang Nguyen "Flow modelling in casting processes", Applied Mathematical Modelling 26 (2002), pp.171-190.
9. Copyright:
- This material is "S Chandra Sekhar, Sk.Surjan, M.S. Phani Deep Kumar"'s paper: Based on "Design of Three Cavity Diecasting Die for Rotors".
- Paper Source: https://www.ijert.org/research/design-of-three-cavity-diecasting-die-for-rotors-IJERTV6IS020017.pdf
This material was summarized based on the above paper, and unauthorized use for commercial purposes is prohibited.
Copyright © 2025 CASTMAN. All rights reserved.