The content of this introduction paper is based on the article "Squirrel Cage Induction Motor: A Design-Based Comparison Between Aluminium and Copper Cages" published by "IEEE Open Journal of Industry Applications".
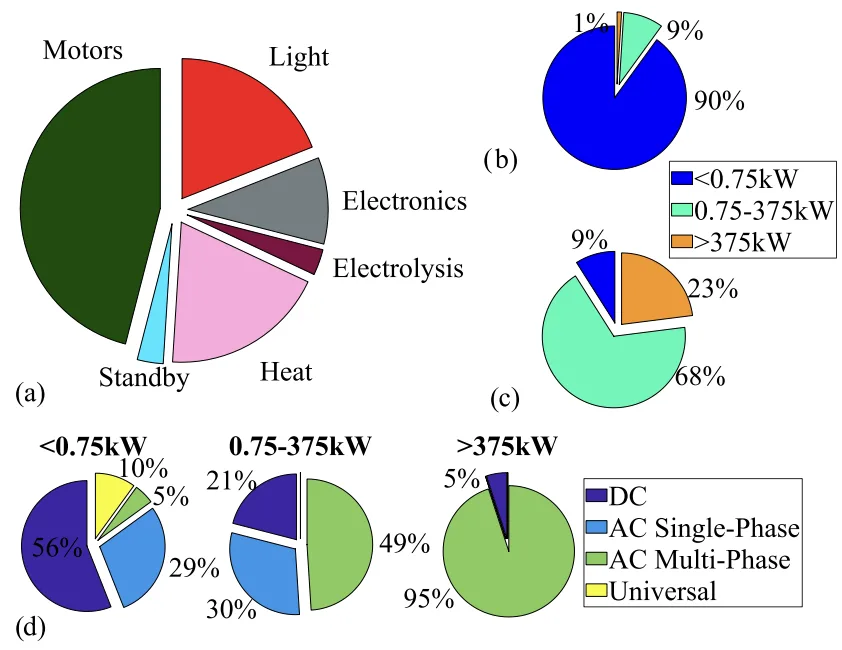
1. Overview:
- Title: Squirrel Cage Induction Motor: A Design-Based Comparison Between Aluminium and Copper Cages
- Author: Alessandro Marfoli, Mauro Di Nardo, Michele Degano, Chris Gerada, and Werner Jara
- Year of publication: 2021
- Journal/academic society of publication: IEEE Open Journal of Industry Applications
- Keywords: Aluminium cage, copper cage, efficiency improvement, fast performance computation, finite element analysis, induction motor, multi-objective optimization, rotor slot design, squirrel cage.
2. Abstract:
In many industrial applications the self-starting capability of electric motors is still an important requirement enabling to simplify the drive architecture and increase the system's reliability. The efficiency improvement of this motor topology has been targeted by various national and international regulatory authorities with ad-hoc policies. Indeed, a lower energy consumption leads to the twofold benefits of reducing the operational costs and the CO2 emissions. The adoption of a copper cage has been successfully proven to reduce the motor losses. However, this could affect other performance indexes, such as the starting torque. In this paper, the advantages and drawbacks of adopting a copper cage are analysed in depth by comparing the motors performance at different operating conditions, with respect to the more common aluminium cage. Starting from a set of induction machines optimized with an aluminium cage, the effect of the direct material cage substitution is analysed both in terms of electromagnetic and thermal aspects. The overall performance are also compared against machines specifically optimized with a copper cage. With the presented performance comparison exercise, general design guidelines are outlined aimed at improving the efficiency without deteriorating other performance metrics.
3. Introduction:
Almost 50% of the final world electric energy consumption is used to supply electric motors [1]. Although the majority of the electric motors has a rated power below 0.75 kW, it is the remaining small fraction of the overall market which has the biggest impact on the electric energy consumption, as shown in Fig. 1(b) and (c). In fact, 10% of the electric motors, the ones having power rating higher than 0.75 kW, are responsible for the 91% of the overall consumed electric energy [2]. Fig. 1(d) shows the distribution of the electric motor types in Europe divided into power ranges [3]. Clearly, the most influential motor topology in terms of electric energy consumption is the AC multi-phase one being the most common in the medium-high power range. Grid connected three phase squirrel cage induction motor (SCIM) represents the largest market share among the wide variety of AC electric motors available on the market [4]. Therefore, improving its efficiency can have the biggest effect on the reduction of the environmental impact in terms of CO2 emissions [5]. In the last two decades, almost all the major economies have introduced some regulatory schemes (first on a voluntary basis and then mandatory), first on the minimum motor efficiency and lately on overall drive system efficiency [6]. For example in Europe, the commission regulation 1781/2019 [7] sets a precise timetable for the minimum energy efficiency requirements for electric motors both inverter and direct-grid supplied. The definition of the efficiency classes of electric motors adopted by the regulatory authorities as well as the methodology to experimentally determine the efficiency are set by the international standards IEC 60034-30-1/2 and IEC 60 034-2-1, respectively.
4. Summary of the study:
Background of the research topic:
Efficiency improvement in squirrel cage induction motors (SCIMs) is crucial due to increasing regulatory pressure and the global focus on reducing energy consumption and CO2 emissions. Copper cages have been shown to reduce motor losses, but their impact on other performance metrics like starting torque needs further investigation.
Status of previous research:
Previous research has explored efficiency improvements in SCIMs through methods like core axial lengthening, better magnetic materials, and copper cages. However, the comprehensive effects of copper cage adoption, especially concerning the trade-offs with other performance parameters, are not fully understood. Existing literature lacks a systematic comparison of aluminium and copper cages, particularly considering different rotor slot designs and performance requirements.
Purpose of the study:
This study aims to analyze the advantages and disadvantages of using copper cages in SCIMs compared to aluminium cages. It investigates the effects of direct material substitution and optimized copper cage designs on electromagnetic and thermal performance. The research seeks to provide design guidelines for improving efficiency without compromising other critical performance metrics, such as starting torque.
Core study:
The core study involves a design-based comparison of SCIMs with aluminium and copper cages. Starting with aluminium cage optimized designs, the paper analyzes the impact of directly substituting aluminium with copper. It further compares these results with SCIMs specifically optimized for copper cages. The analysis covers electromagnetic and thermal aspects, considering various performance indexes like efficiency, starting torque, current ratio, and thermal behavior. The study utilizes a fast performance computation method, validated by experimental tests, and multi-objective optimization algorithms to derive optimal rotor designs and compare the performance of aluminium and copper cage motors.
5. Research Methodology
Research Design:
The research employs a design-based comparative study. It starts with baseline designs of SCIMs optimized with aluminium cages for different performance requirements (starting torque and efficiency). The study then performs a straight material substitution of the cage from aluminium to copper in these baseline designs. Finally, it optimizes SCIM designs specifically for copper cages, comparing their performance against both aluminium baseline designs and straight copper substitutions.
Data Collection and Analysis Methods:
The performance evaluation relies on a mixed analytical-Finite Element Analysis (FEA) method for fast and accurate estimation of torque and efficiency. This method is validated through experimental tests on an off-the-shelf SCIM. Multi-objective optimization algorithms (NSGA-II) are used to design optimal rotor geometries for both aluminium and copper cages, considering various performance metrics and constraints. Thermal-FEA is used for post-processing to evaluate steady-state temperatures of stator and rotor windings. The performance metrics analyzed include rated efficiency, starting torque, current ratio, power factor, and thermal characteristics.
Research Topics and Scope:
The research focuses on the rotor cage design of SCIMs, specifically comparing aluminium and copper as cage materials. The scope includes:
- Analyzing the impact of direct copper substitution in aluminium-optimized designs.
- Optimizing rotor slot geometries for both aluminium and copper cages using multi-objective optimization.
- Comparing the electromagnetic and thermal performance of SCIMs with aluminium and copper cages across a range of starting torque and efficiency requirements.
- Investigating the effects on various performance indexes such as efficiency, starting torque, current ratio, power factor, losses, and thermal behavior.
- Deriving general design guidelines for copper cage adoption in SCIMs.
6. Key Results:
Key Results:
- Efficiency Improvement: Copper cages consistently improve rated efficiency compared to aluminium cages, with gains ranging from 0.5% to 1.25%. The improvement is more significant for less efficient baseline machines (high starting torque, low current ratio limit).
- Thermal Benefits: Copper cages lead to lower stator and rotor winding temperatures due to reduced losses. A significant portion (20-40%) of the efficiency gain from copper substitution is attributed to these lower operating temperatures.
- Starting Current Increase: Straight copper substitution increases the starting current ratio, potentially violating design constraints. The increment ranges from 0% to 25% and is proportional to the efficiency gain.
- Starting Torque Variation: The effect on starting torque varies. For low current ratio designs, copper cages increase starting torque. For high current ratio designs, starting torque decreases. In the middle range, the effect depends on the baseline design.
- Rotor Design Similarity: Optimal copper and aluminium cages exhibit similar bar shapes, but optimal aluminium cages have larger cross-section areas. Copper cages achieve similar starting impedance with a lower ratio of outer to total bar area, enhancing skin effect utilization.
- Breakdown Torque: Material cage substitution does not affect breakdown torque, but it reduces breakdown slip by approximately 35%.
- Optimized Copper Cage Performance: Optimized copper cage designs achieve the same starting torque range as aluminium cages but with higher rated efficiency. For relaxed current ratio constraints, straight copper substitution can outperform optimized copper designs in efficiency but at the cost of higher starting current.
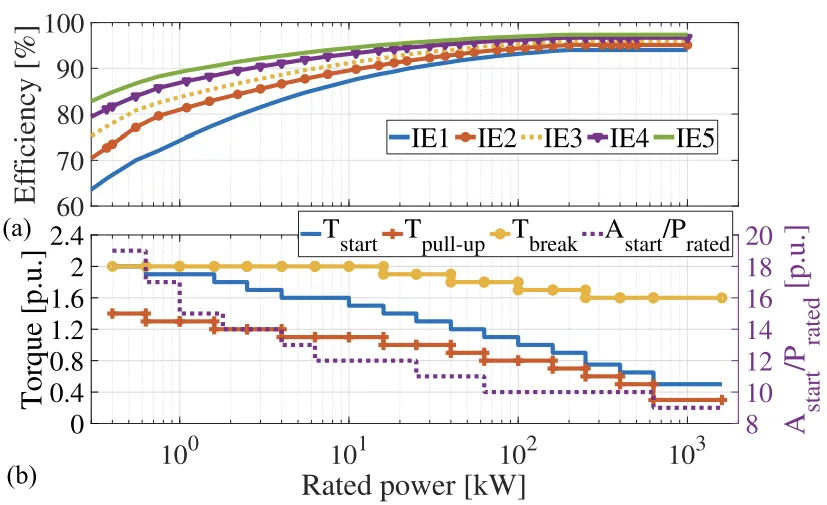
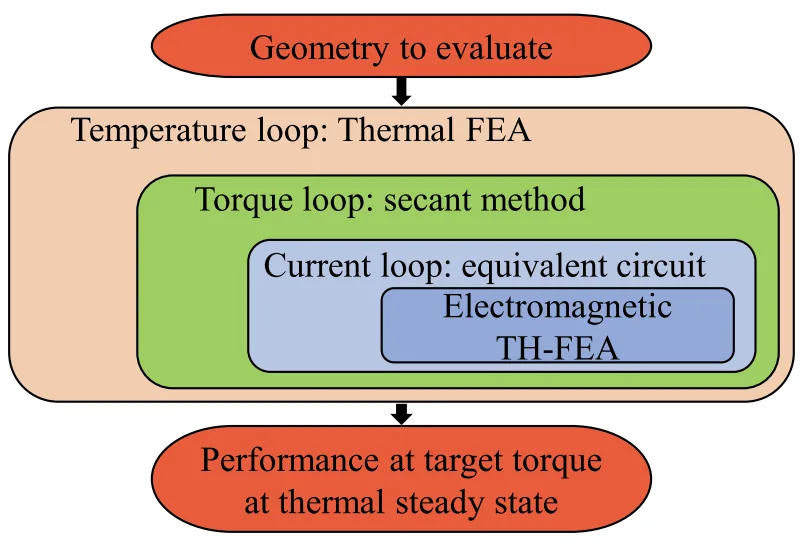
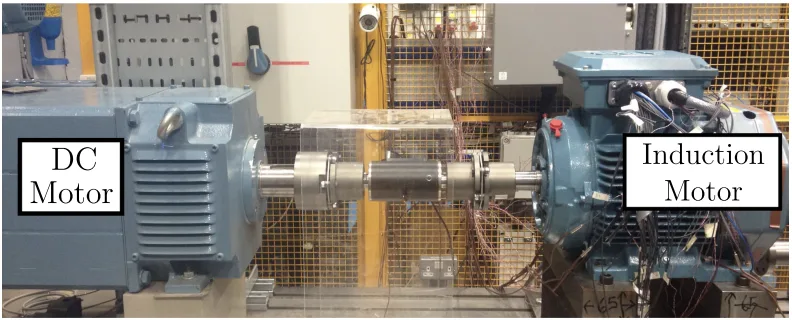
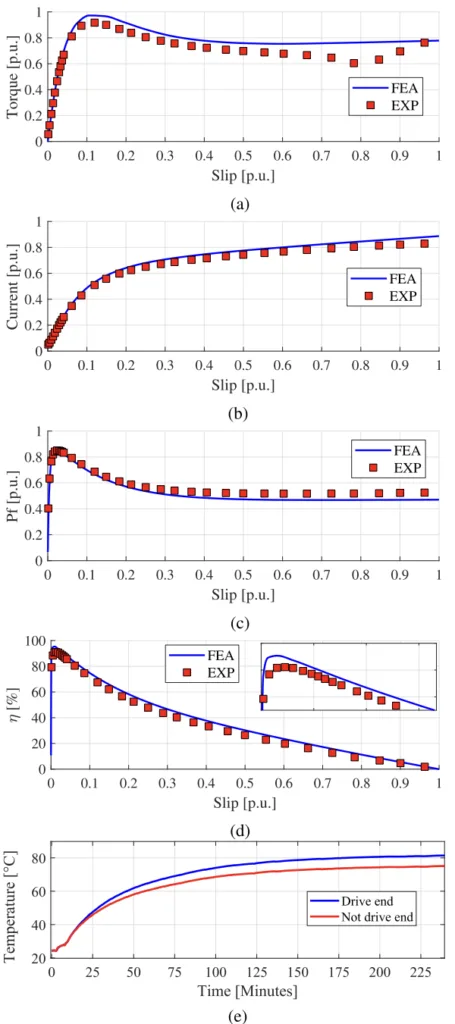
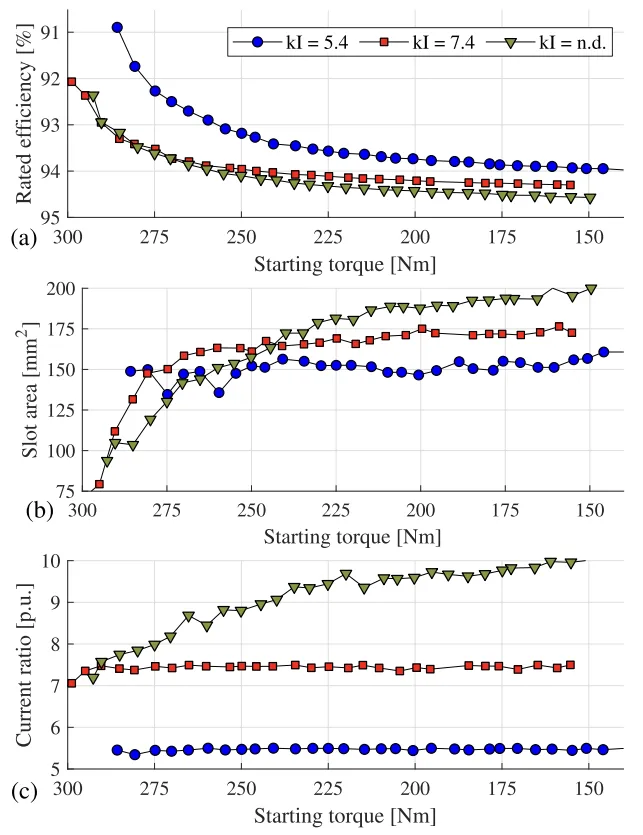
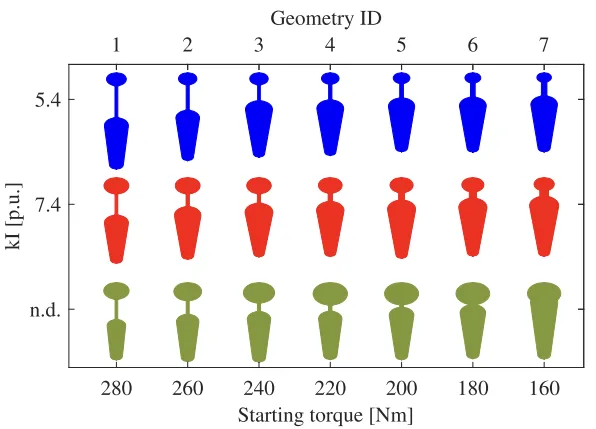
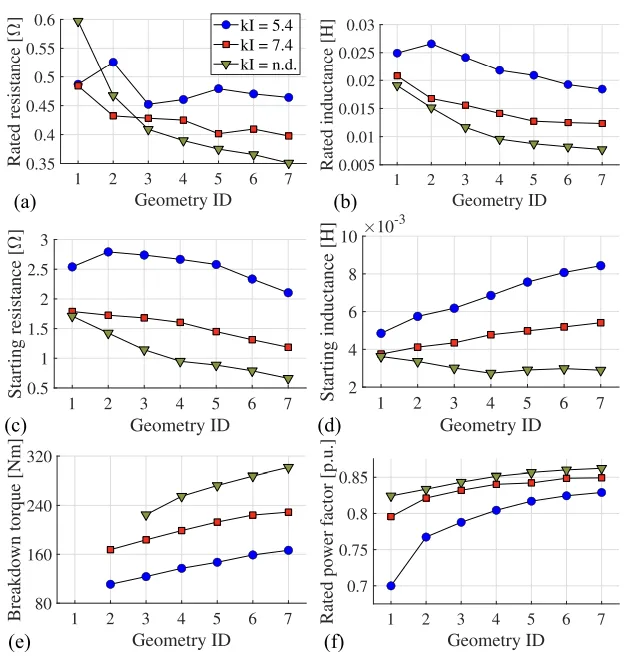
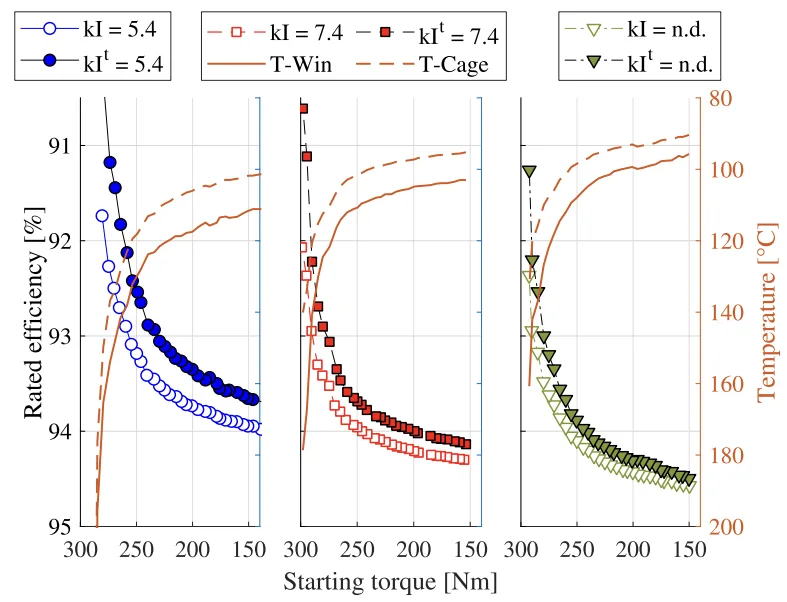
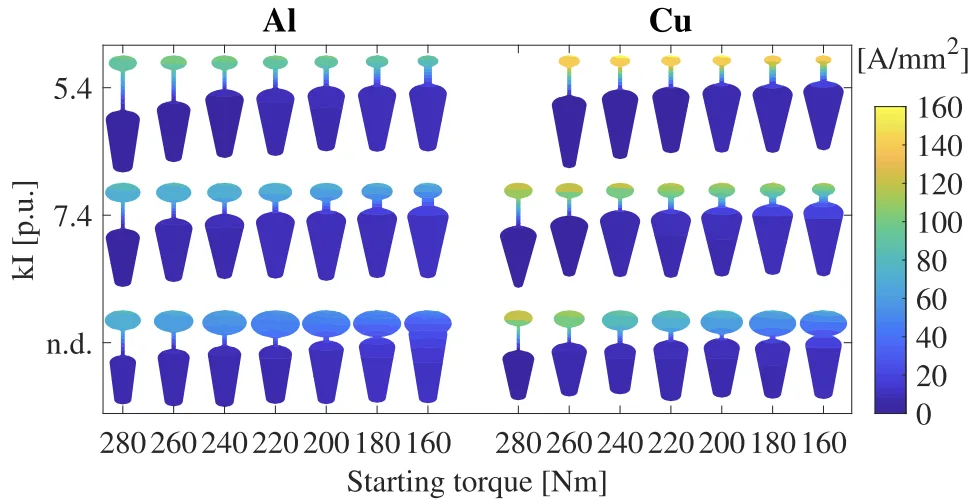
Figure Name List:
- FIGURE 1. a) Electric energy consumption by end use, b) Number of motors by power range, c) Motor energy consumption by power range, d) Motor type distribution by power range.
- FIGURE 2. a) Efficiency levels defined by IEC 60 034-30 for a 4-poles, 50 Hz SCIM, b) Minimum torque values and locked rotor apparent power for design N defined by the IEC 60 034-12.
- FIGURE 3. Flow chart of the iterative procedure for the evaluation of the machine performance for a given torque.
- FIGURE 4. a) Rotor slot parametrization, b) examples of slot shapes investigated during the optimization.
- FIGURE 5. Experimental test rig layout.
- FIGURE 6. Comparison between measured and estimated torque (a), stator current (b), power factor (c) and efficiency (d). Winding temperatures at the rated operating condition from cold to thermal steady state.
- FIGURE 7. a) Optimized performance of the aluminium rotor cage for three different maximum current ratios kl; b) rotor slot area and current ratio c) of the optimal geometries.
- FIGURE 8. Optimal rotor slot geometries with an aluminium cage.
- FIGURE 9. Rotor resistance and leakage inductance at the rated (a, b) and starting conditions (c, d) of the optimal aluminium cage solutions along with the breakdown torque (e) and rated power factor (f).
- FIGURE 10. Comparison between the rated efficiencies calculated with constant windings temperature (kl) and re-evaluated at the correct temperature (kit); the steady state temperatures of stator and rotor windings (T - Win, T – Cage) are also reported.
- FIGURE 11. Performance and rotor parameters variations when directly replacing the aluminium cage with the copper one: a) Rated efficiency at the same temperature and new steady state temperature, b) stator and rotor temperatures, c) rated resistance and inductance, d) iron and joule losses, e) power factor and rated slip value, f) starting torque and current ration kl, g) resistance and inductance at the starting operating point, h) breakdown torque and slip, i) breakdown resistance and inductance and I) variation of the current density distribution.
- FIGURE 12. Rated efficiency (a), effective current ratio (b), stator (c) and rotor (d) winding temperatures as function of the starting torque for machines optimized with the aluminium (Al) and the copper (Cu) cage along with the straight substitution of the material cage (Cu → Al).
- FIGURE 13. Optimal aluminium and copper a) slot area and ratio between outer and inner cage area (dotted lines), b) rated rotor resistance and reactance (dotted lines), c) starting resistance and reactance (dotted lines). First row corresponds to the lowest maximum current ratio k₁ = 5.4 while for the third row k₁ = n.d.
- FIGURE 14. Current density distribution of the optimal aluminium and copper cage designs.
7. Conclusion:
The study concludes that copper cages offer a viable solution for enhancing the efficiency of SCIMs. Straight substitution of aluminium with copper improves efficiency but may increase starting current and variably affect starting torque. Optimized copper cage designs can maintain starting torque capability while achieving higher efficiency than aluminium cage motors. Design guidelines emphasize that for unconstrained current ratios, straight copper substitution is highly effective. However, when current limits are imposed, optimized copper rotor designs are necessary to maximize efficiency gains without compromising starting performance. The choice between straight substitution and optimized design depends on the specific application requirements and design priorities, particularly concerning starting current limitations and desired efficiency levels.
8. References:
- [1] P. Waide and C. Brunner, “Energy-efficiency policy opportunities for electric motor-driven systems,” in IEA Energy Papers, No. 2011/07. OECD Publishing, Paris, 2011. [Online]. Available: https://doi.org/10.1787/5kg58gbb2g9d-en
- [2] de Almeida, H. Fonseca, A. T. de Almeida, P. E. Baptista, and L. D. Economidou, “Minimum energy performance standards and labelling for electric motors and their impact: Final Report for the European Commission,” Institute of Systems and Robotics - Univ. of Coimbra, 2014.
- [3] W. Kleinschmidt, A. Tong, H. Bremmer, and P. Radgen, “From laggard to world leader - the role of policies in the EU motors and drives market transformation,” in Proc. 7th Conf. Industrial Energy Efficiency, Oct. 2015, pp. 1549–1557.
- [4] A. Boglietti, P. Ferraris, and M. Lazzari, “Technical and economical considerations on super-high efficiency three-phase motors,” IEEE Trans. Ind. Appl., vol. 50, no. 2, pp. 1274–1285, Mar./Apr. 2014.
- [5] A. T. de Almeida, P. Fonseca, and L. Bertoldi, “Energy-efficient motor systems in the industrial and commercial sectors: Status, drivers, barriers and policies,” Energy Effic., vol. 9, no. 1, pp. 273–290, Jan. 2016.
- [6] L. Alberti and D. Tronchin, “Design of electric motors and power drive systems in view of the new ecodesign regulation,” IEEE Trans. Ind. Electron., to be published, doi: 10.1109/TIE.2020.3020028.
- [7] EUROPEAN COMMISSION, “COMMISSION REGULATION (EU) 2019/1781 of 1 October 2019,” [Online]. Available: https://eur-lex.europa.eu/eli/reg/2019/1781/oj
- [8] IEC, “IEC 60034-12 Rotating electrical machines - Part 12: Starting Performance of Single-Speed, Three-Phase, Cage Induction Motors,” Int. Std. IEC/EN 60034-12, 2016.
- [9] A. Boglietti, A. Cavagnino, L. Ferraris, M. Lazzari, and G. Luparia, “No-naturally ventilated induction motors with efficiency optimized according to Iecs standards,” IEEE Trans. Ind. Appl., vol. 41, no. 3, pp. 808–816, May 2005.
- [10] E. Armando, A. Boglietti, and S. Calligaro, “Induction motor design efficiency improvement by commercially manufactured industrial motors,” IEEE Trans. Ind. Appl., vol. 49, no. 6, pp. 2496–2504, Nov./Dec. 2013.
- [11] L. Alberti, N. Bianchi, A. Boglietti, and A. Cavagnino, “Core axial length and reactive power in line start permanent magnet synchronous machines for efficiency classes,” IET Electr. Power Appl., vol. 5, no. 1, pp. 218–225, Jan. 2011.
- [12] F. Parasiliti, “Design strategies, new materials and technologies to improve induction motor efficiency,” Prace Instytutu Elektrotechniki, vol. 223, pp. 27–42, 2005.
- [13] F. Parasiliti and M. Villani, “Design of high efficiency induction motors with die-casting copper rotors,” Energy Efficiency Motor Driven Syst., vol. 1, pp. 1444–1453, 2003.
- [14] J. G. Heo, J. M. Kim, and G. S. Park, “A design study of rotor bar inclination in squirrel cage induction motor,” IEEE Trans. Magn., vol. 53, no. 11, pp. 1–4, Nov. 2017.
- [15] A. Cavagnino, S. Vaschetto, L. Ferraris, Z. Gmyrek, E. B. Agamloh, and M. Pastorelli, “Cost-oriented design of induction motors with minimum impact for induction motor manufacturers,” IEEE Trans. Ind. Appl., vol. 56, no. 1, pp. 194–204, Jan./Feb. 2020.
- [16] T. Boldea and S. A. Nasar, The Induction Machine Design Handbook. Electric Power Engineering Series. CRC Press/Taylor & Francis, 2010.
- [17] P. L. Alger, Induction Motors: Their Behavior and Uses. New York: Gordon & Breach, Science Publishers, Wiley, 2017.
- [18] A. Keyhani, “An insight into induction motor design-marriage a marriage of inconveniences?” in Proc. IEEE Semiar. Curr. Trends Use Finite Elem. Method Electromagn. Device Anal. (Ref. No. 2000/013), pp. 4/1–4/7, Jan. 2000.
- [19] R. Carlson, J. P. Bastos, and M. I. McCulloch, “Optimization of the geometry of closed rotor slots for cage induction motors,” IEEE Trans. Ind. Appl., vol. 32, no. 3, pp. 500–506, May 1996.
- [20] J. Pyrhonen, S. Saari, and L. Lauronen, “Optimal shape design of rotor slot in squirrel-cage induction motor considering torque characteristics,” IEEE Trans. Magn., vol. 49, no. 5, pp. 2105–2108, May 2013.
- [21] A. Marfoli, M. Di Nardo, M. Degano, C. Gerada, and W. Chen, “Robust design optimization of squirrel cage induction motor - Part I: Problem statement,” IEEE Trans. Energy Convers., to be published, doi: 10.1109/TEC.2021.3058789.
- [22] D. Genovese, P. Bolognesi, M. De Martin, and F. Luise, “A contextual parameter extraction method for the equivalent circuit of induction machines,” in Proc. 22th Int. Conf. Electr. Machines (ICEM), 2016, pp. 25–31.
- [23] A. Marfoli, L. Papini, P. Bolognesi, D. Genovese, and C. Gerada, “Analysis of induction machine: Comparison of modelling techniques,” in 2019 IEEE Int. Electr. Machines Drives Conf. (IEMDC), May 2019, pp. 1–7.
- [24] W. R. Finley and M. M. Hodowanec, “Selection of copper versus aluminum rotor conductor bars for induction motors,” IEEE Trans. Appl. Ind., vol. 37, no. 6, pp. 1563–1573, Nov. 2001.
9. Copyright:
- This material is a paper by "Alessandro Marfoli, Mauro Di Nardo, Michele Degano, Chris Gerada, and Werner Jara". Based on "Squirrel Cage Induction Motor: A Design-Based Comparison Between Aluminium and Copper Cages".
- Source of the paper: https://doi.org/10.1109/OJIA.2021.3073820
This material is summarized based on the above paper, and unauthorized use for commercial purposes is prohibited.
Copyright © 2025 CASTMAN. All rights reserved.