Dr. C. Ramesh, A. Subbiah, K. Sivakumar, T. Sri Gokul
Abstract
This project is about a comparative study of different types of fins and with different types of materials. The main aim of this research is to optimize the cooling rate of the fin in electric motors. Since now a day’s the fossil fuels are deteriorating gradually, so the automobile industry is changing to E-Vehicles. In EV’s the motor is the very important part, if that motor has a best design for fins to eliminate heat from the motor then it will be helpful for the efficient running of the vehicle. So, to resolve the heat transfer problem various designs of motor fins are modeled in 3-D modeling software (DSS-Solidworks) and analyzed by the analysis software (Ansys-2016) for their heat transfer properties. To improve the results even more a research has been done and by the help of various research paper study, the materials are selected. Those materials are first applied to the 3 basic verities of the fins. Then by the results we can able to find out the best material among the chosen 3 materials. Then to improve the results even more another 3 hybrid models are created and analyzed by applying only the best material which was found and find out the best design with the best material.
KEYWORDS
Ansys, Solidwork 3D Modeling, Fins, Electric Motor
Introduction
We all are in the world filled with machines, gadgets, and electricity. These machines are powered by electricity and works with respect to their purposes. In most of the cases the generated heat is only used for some extent and the remaining is just left out as a loss. For this issue our scientist created a small design modification in the place where the heat is generated is the FINS.But these fins too, does not completely eliminate the residual heat so to increase therate of heat dissipation the variations inthe fins are invented and with respect to the purpose & design structure they are used. We all know that the necessity is the mother of invention, so to increase the heat dissipation even more than better the cooling fans are introduced. This project’s main goal is to improve the rate of convection through the fins of any hot bodies like heat sinks, motors, etc.The electric energy into mechanical energy transformation is known as electric motor. It is one of the most imperative application of electromagnetism. It is the main end-use of electric energy in industries in general, and its used more in this area is due to its simple construction model and applying load in wide range.In vacuum the heat transfer of radiation is more effective. Radiation energy is transported by electromagnetic waves. Fins are the extended surfaces that are joined with any of the surface in order to increase the rate of heat transfer from that surface. It will transfer the heat from the solid medium to another solid medium and that solid medium into a liquid or gas medium is called fins. Motor to fins it will be a conduction heat transfer. The solid medium to the liquid or gas medium is named as the convection heat transfer. Fins are available in many shapes and forms.
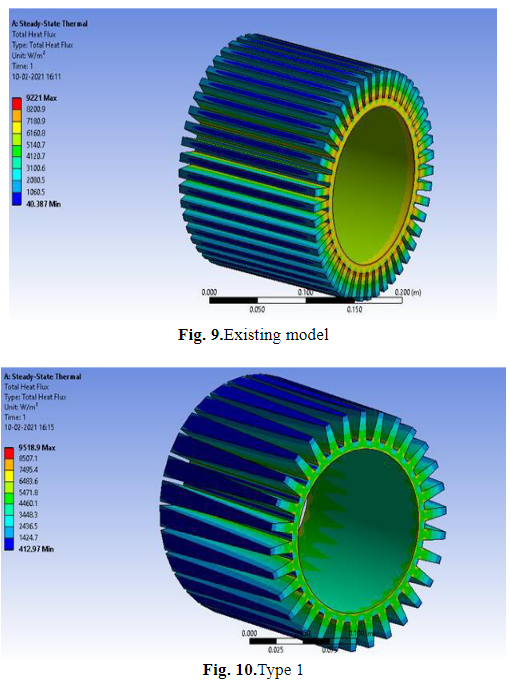
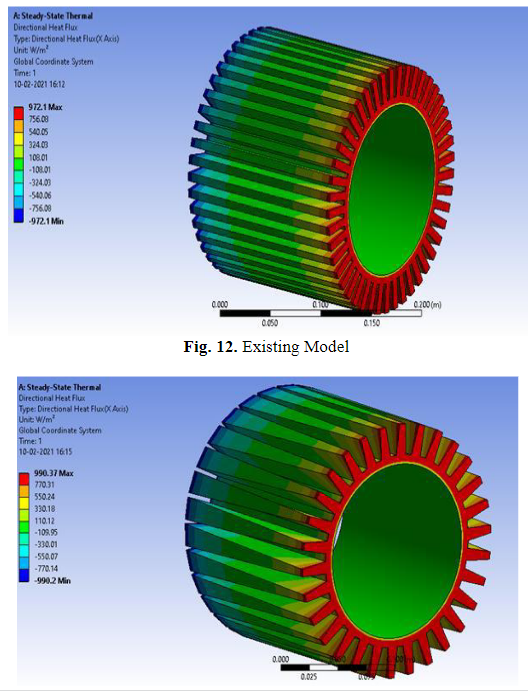
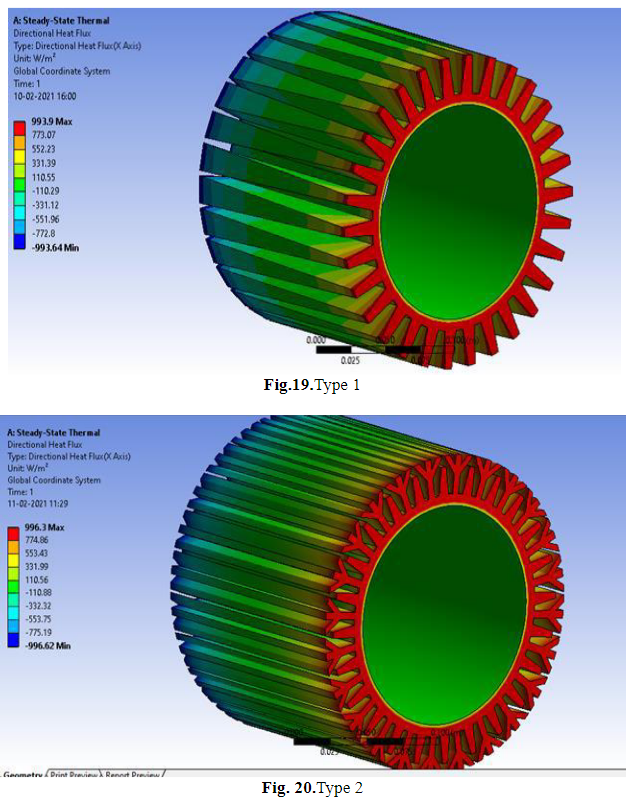
References
[1]Stefan Ulbrich, Jeanette Kopte, and Jens Proske “Cooling Fin Optimization on a TEFC Electric Machine Housing Using a 2-D Conjugate Heat Transfer Model” IEEE Transactions on Industrial Electronics,Vol.65, no.2, P.P:1711-1718, Feb 2018. [2]Pavankumar V Kulkarni, and Dr. S. R. Basavaraddi” Design optimization of Electric Motor Frame and its Study for Thermal Dynamic and Model Stability” International Research Journal of Engineering and Technology, Volume 3, Issue:05, P.P:2915-2923, May 2016.[3]Marcus V. F. Soares and ElcioNoueira” Finned Electric Motor with Prescribed Heat Fluxand influence of the Internal and External Heat Convection Coefficient on the Temperature of the Core” Global Journal of Research in Engineering, Volume 19, Issue:3, P.P: 26-37, year 2019.[4]James Kuria and Pyung Hwang “Optimizing Heat Sink Geometry for Electric Vehicle BLDC Motor Using CFD” International Research Journal of Engineering and Technology,Volume 2, Issue:05, P.P:1185-1190, year 2017.[5]Jerzy MADEJ and Bartlomiej BEDKOWSKI” Air FlowAnalysis for Electrical Motor’s Cooling System with Autodesk Simulation CFD 2013 Program” Acta mechanical et automatica,Volume 7, no.2, P.P:89-92, year 2013.[6]Cenk Ulu, OguzKorman and GuvenKomurgoz” Electromagnetic and Thermal Analysis/Design of an Induction Motor for Electrical Vehicles” International Journal of Mechanical Engineering and Robotics Research, Volume 7, no.6, P.P:617-623, Nov 2018.[7]Chih-Chung Chang, Sy-Chi Kuo, Chen-Kang Huang and Sih-Li Chen” The Investigation of Motor Cooling Performance” International Journal of Mechanical Engineering and Aerospace Engineering,Volume 3, no.1, P.P:43-49, Year 2009.[8]Manuja Pandey, Utkarsh Prasad, Vineet Kumar and Nafish Ahmed “Experimental Analysis of Cooling Fins” International Research Journal for Engineering and Technology,Volume 2, Issue: 3, P.P: 1177-1184, June 2015. [9]N. J. B. Illagolla” Design Study of Cooling Fin Device”, Scientific Research Journal,Volume 2, Issue: X, P.P:34-39, Oct 2014. [10]Duc Thuan Vu and Pyung Hwang” New Cooling system Design of BLDC Motor for Electric Vehicle Using Computation Fluid Dynamics Modeling” Journal of the KSTLE,Volume 29, no.5, P.P:318-323, Oct 2013.