This paper summary is based on the article ['Design and Analysis of Pressure Die Casting Die for Automobile Component'] presented at the ['Global Journal of Researches in Engineering: A Mechanical and Mechanics Engineering']
1. Overview:
- Title: Design and Analysis of Pressure Die Casting Die for Automobile Component
- Author: Y. Abdulfatah Abdu, T. M. Shafii, K. K. Dubey & Prof U. K. Gupta
- Publication Year: 2016
- Publishing Journal/Academic Society: Global Journal of Researches in Engineering: A Mechanical and Mechanics Engineering
- Keywords: pressure die casting, automobile industry, aluminium alloys, solid works, 3-diamensional flow, pro-engineer.
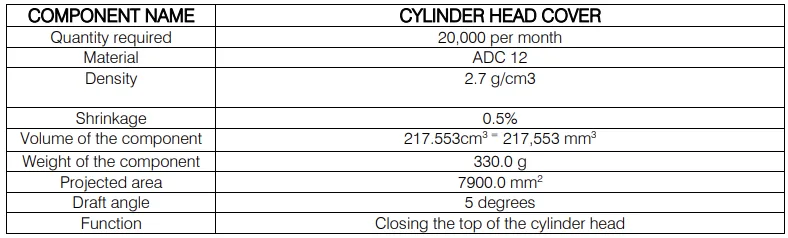
2. Research Background:
Background of the Research Topic:
The paper addresses the design and analysis of dies used in pressure die casting, a manufacturing process crucial for producing geometrically complex metal parts with tight tolerances and reduced machining requirements. Pressure die casting is highlighted as an optimal choice for small volume production, particularly for the automobile industry where lightweight and precise parts are essential for fuel efficiency and user satisfaction. The process leverages materials like aluminium alloys, high strength steels, and fibre-reinforced composites for structural components.
Status of Existing Research:
Existing research indicates that casting defects such as cold fills, dross, and alumina skins are prevalent in die casting. Studies have explored the impact of runner and sprue designs on fatigue strength, integrated CAD/CAM systems to reduce lead and cycle times in die design, and the influence of gating system designs on defects like shrinkage and gas porosities in critical automotive components like front axle housings made of spheroid graphite iron. Furthermore, computer-aided die design systems have been developed to optimize ejector, die-base, and gating designs. Non-uniform cooling and its correlation with runner and gating system design have also been investigated using flow simulation.
Necessity of the Research:
The research is necessitated by the need to minimize defects in pressure die castings, such as shrinkage cavities, gas defects, and material flaws. The paper emphasizes the importance of comprehensive die design and analysis to control all aspects of the casting process and prevent wastage. Specifically, the research aims to design a die and develop a gating system using Computer Aided Engineering (CAE) software to identify and mitigate these defects, thereby improving casting quality and efficiency.
3. Research Purpose and Research Questions:
Research Purpose:
The primary purpose of this research is to design and analyze a pressure die casting die for an automobile component, focusing on minimizing casting defects and optimizing the die design for efficient production. This involves developing a die and gating system using CAE software to address issues like shrinkage cavities, gas defects, and pouring material defects.
Key Research:
The key research objectives are:
- To design a pressure die casting die for an automobile component, considering critical dimensions and filling analysis.
- To develop tools and a gating system to identify and minimize casting defects.
- To utilize CAE software (Solid Works, 3-Diamesional Flow, Pro-Engineer) for design, analysis, and testing.
- To determine the optimal parameters for die casting, including runner system design, cooling system, and process parameters.
Research Hypotheses:
While the paper does not explicitly state research hypotheses, implicit hypotheses can be inferred:
- A properly designed die and gating system, analyzed using CAE software, will significantly reduce casting defects in the automobile component.
- Optimized runner and gating system designs will ensure complete and balanced filling of the die cavity, leading to improved casting quality.
- CAE software simulations can accurately predict and help mitigate potential casting defects, leading to a more efficient die design process.
4. Research Methodology
Research Design:
The research employs a design and analysis methodology, utilizing CAE software to simulate and optimize the pressure die casting process. The design process involves several steps, from component identification and data collection to 3-Dimensional modeling and 2-Dimensional drawing creation using Solidworks software. The design incorporates considerations for material shrinkage and employs 3-Diamesional Flow analysis for runner system design and filling analysis.
Data Collection Method:
The research primarily utilizes theoretical calculations and CAE software simulations for data generation. Component details, material properties (ADC 12 aluminium alloy), and machine specifications for an 80T machine are used as input parameters for design calculations and simulations. Experimental data collection is not explicitly mentioned in this paper.
Analysis Method:
The analysis methods include:
- Design Calculations: Manual calculations for determining the number of cavities, tonnage requirement, shot weight, fill ratio, fill time, dry shot flow rate, metal pressure, and runner dimensions. These calculations are based on established die casting principles and formulas.
- 3-Dimensional Flow Simulation: Utilizing "3-Diamesional Flow" software to simulate the filling process in both vertical and horizontal part arrangements. This analysis aims to visualize and evaluate the flow behavior of molten metal and identify potential defects like air porosity.
- P-Q² Diagram Analysis: Employing a P-Q² diagram to analyze the relationship between metal pressure and flow rate to optimize the gating system design.
Research Subjects and Scope:
The research focuses on the design of a pressure die casting die for a specific automobile component: a "CYLINDER HEAD COVER" made of ADC 12 aluminium alloy. The scope is limited to the die design and analysis aspects, including gating system and runner design, cooling system considerations, and defect analysis through simulation. The design and analysis work were conducted at Automotive Private Limited, Gurgaon, Haryana.
5. Main Research Results:
Key Research Results:
The key research results are summarized in Table 2 "Results Summary", which outlines the optimized parameters for the die design:
- Number of Cavities: 1
- Tonnage Requirement: 80 T
- Shot Weight: 0.9kg
- Fill Ratio: 0.6
- Fill Time: 54 milliseconds
- Max. Static Pressure: 838.02kgf/cm2
- Dry Shot Flow Rate: 10,692.62 cm3/sec
- Max. Metal Pressure: 131.5 kgf/cm2
- Min. Metal Pressure: 51.4 kgf/cm2
- Flow Rate: 4,834.5 cm3/sec
- Metal Pressure (P): 91.5 kgf/cm2
- Flow Rate (Q): 7,255.7 cm3/sec
- Gate Area: 69 mm2
- Gate Length: 23mm
- Runner Size: L=86.7 mm2, D= 10.42mm, W= 20.84 mm
The flow simulation analysis indicated that the horizontal arrangement of the part exhibits a lower air porosity defect rate compared to the vertical arrangement. The filling pattern simulation showed the molten aluminium entering the gate and filling the cavity effectively after 0.5 seconds.
Data Interpretation:
The design calculations and simulation results provide a comprehensive set of parameters for manufacturing the pressure die casting die for the cylinder head cover. The P-Q² diagram analysis (Figure 2.1) and flow simulation visualizations (Figure 3.01 and 3.02) support the optimized design parameters. The results suggest that the designed die and gating system are capable of producing castings with minimized defects. The choice of a horizontal part arrangement is favored due to reduced air porosity.
Figure Name List:
- Figure 2.1: P-Q2 Diagram
- Figure 2.1.1: Core Insert
- Figure 2.1.2: Cavity Insert
- Figure 2.1.3: Tool Cavity & Core Assembly
- Figure 2.1.4: Assembled Die Tool
- Figure 3.01: Vertical Arrangements of Part
- Figure 3.02: Horizontal Arrangements of Part
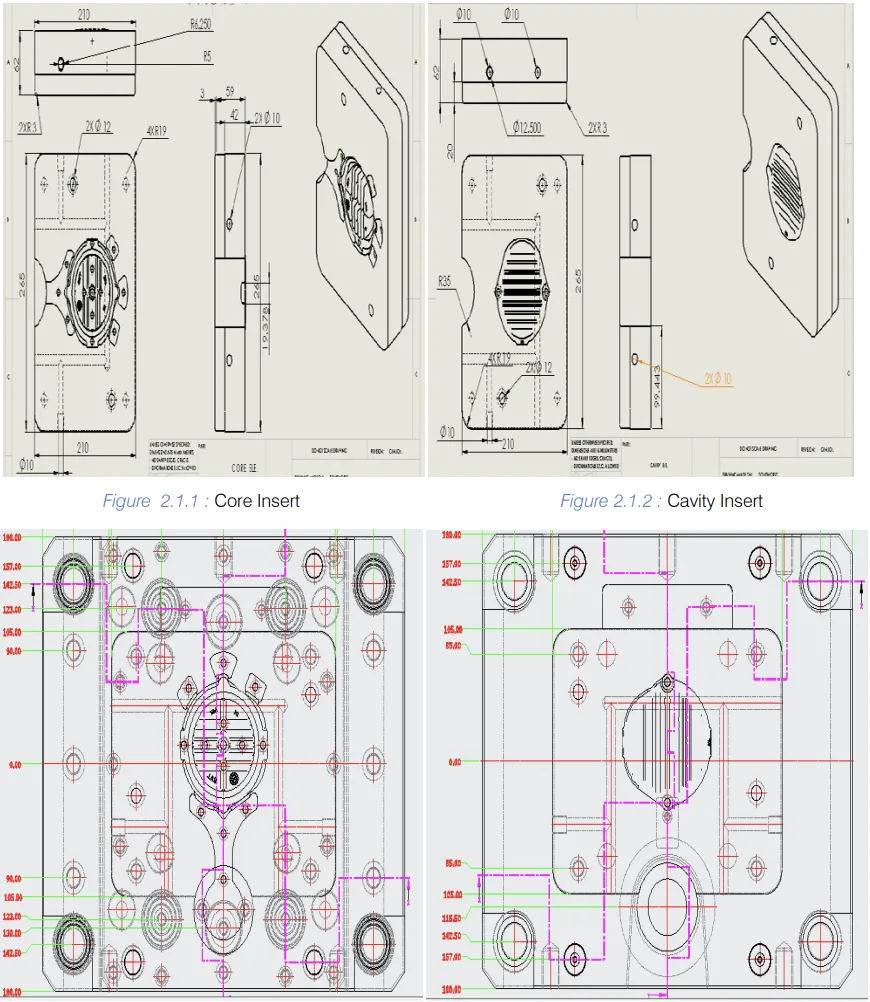
6. Conclusion:
Summary of Main Results:
The research successfully designed and analyzed a pressure die casting die for an automobile cylinder head cover using CAE software. The study determined optimal die design parameters through calculations and flow simulations, aiming to minimize casting defects. The horizontal part arrangement was found to be superior in reducing air porosity compared to the vertical arrangement. The simulation results validated the effectiveness of the designed gating system and filling process.
Academic Significance of the Research:
This research contributes to the body of knowledge in die casting die design by demonstrating a systematic approach using CAE tools for design optimization and defect minimization. It provides a practical example of applying theoretical calculations and simulation techniques in designing a pressure die casting die for a specific automotive component. The study highlights the importance of considering part orientation (vertical vs. horizontal) in die design to mitigate air porosity.
Practical Implications:
The findings of this research have direct practical implications for die casting manufacturers, particularly in the automotive industry. The optimized die design parameters and the methodology presented can be directly applied to manufacture a die for the cylinder head cover, potentially leading to improved casting quality, reduced defects, and enhanced production efficiency. The use of CAE software in the design process can significantly reduce development time and costs associated with trial-and-error die making.
Limitations of the Research
The research is limited in scope to the design and analysis of a die for a single automobile component (cylinder head cover) and material (ADC 12). The analysis primarily relies on simulations, and experimental validation of the die design and casting process is not presented in this paper. Furthermore, the optimization considered only a limited set of process parameters.
7. Future Follow-up Research:
- Directions for Follow-up Research
Future research directions include:- Experimental validation of the designed die and casting process to confirm the simulation results and assess the actual casting quality and defect rates.
- Expanding the optimization study to include a wider range of process parameters such as molten metal temperature, injection speed, discharge pressure, cavity fill rate, and cooling rate, potentially incorporating pq² relations for a more comprehensive optimization.
- Investigating the application of this design and analysis methodology to other automobile components and different die casting alloys.
- Areas Requiring Further Exploration
Further exploration is needed in:- Detailed analysis of the cooling system design and its impact on casting solidification and defect formation.
- Quantitative assessment of defect reduction achieved through the optimized die design compared to conventional designs.
- Cost-benefit analysis of implementing CAE-driven die design in pressure die casting manufacturing.
8. References:
- 1. http://www.custompartnet.com/wu/die-casting (Accessed May 20, 2015).
- 2. Kong, L.X., She, F.H., Gao, W.M., Nahavandi, S., Hodgson, P.D. (2008). Integrated optimization system for high pressure dies casting processes. Journal of materials processing technology 201, 629-634.
- 3. Schey, A. J., Introduction to Manufacturing Processes, McGraw-Hill, Singapore, 1987.
- 4. Seo, P.K., Kim, D.U., Kang, C.G., (2006). Effects of die shape and injection conditions proposed with numerical integration design on liquid segregation and mechanical properties in semi-solid die casting process. Journal of Materials Processing Technology 176, 45–54.
- 5. Avalle, M., Belingardi, G., Cavatorta, M.P., Doglione, R., 2002. Casting defects and fatigue strength of a die cast aluminium alloy: a comparison between standard specimens and production components. International Journal of Fatigue 24, 1–9.
- 6. Yue, S., Wang, G., Yin, F., Wang, Y., Yang, J., (2003). Application of an integrated CAD/CAE/CAM system for die casting dies. Journal of Materials Processing Technology 139, 465-468.
- 7. Lin, J. C. (2002). 'Selection of the Optimal Gate Location for a Die-Casting Die with a Freeform Surface,' Int J Adv Manuf Technol, 19(4), pp.278-284.
- 8. Manjunath Swamy H. M., J. R. Nataraj, C. S. Prasad (2012) "Design Optimization of Gating System by Fluid Flow and Solidification Simulation for Front Axle Housing” International Journal of Engineering Research and Development, Vol. 4, Issue 6, pp. 83-88.
- 9. Woon, Y. K. and Lee, K. S. (2004), 'Development of a die design system for die casting,' Int J Adv Manuf Technol, Vol. 23, Issue (5-6), pp.399-411.
- B. Vijaya R., C.E., Vishal C., A. Arun K., S. M. Asif, G. Riyaz M., D. V. Raj, C. Suresh K. (2014). Analysis and Optimization of Gating System for Commutator End Bracket. Procedia Materials Science 6, 1312 – 1328.
- Abdu Y A. (2016). Implementation of Lean Manufacturing: A Case Study at ASK Automotive Private Limited (India), Int. J. Adv. Res. Sci. Technol. 5(1), 556-562.
9. Copyright:
- This material is "Y. Abdulfatah Abdu, T. M. Shafii, K. K. Dubey & Prof U. K. Gupta"'s paper: Based on "Design and Analysis of Pressure Die Casting Die for Automobile Component".
- Paper Source: https://www.researchgate.net/publication/314175819
This material was summarized based on the above paper, and unauthorized use for commercial purposes is prohibited.
Copyright © 2025 CASTMAN. All rights reserved.