This article introduces the paper ["Co-operative Virtual Foundry for Cost-Effective Casting Simulation"] published by [Technical paper for the 54th Indian Foundry Congress, Pune, 2006].
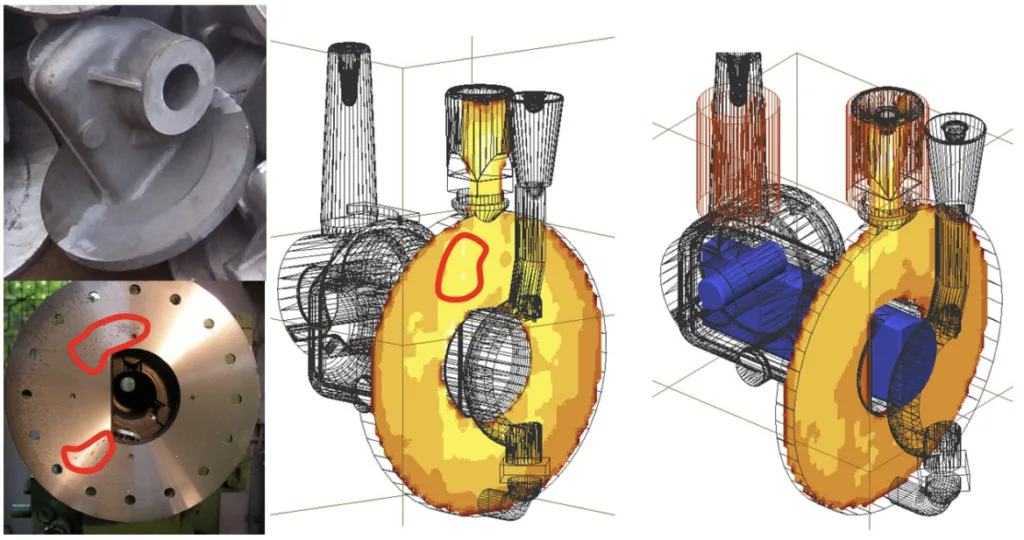
1. Overview:
- Title: Co-operative Virtual Foundry for Cost-Effective Casting Simulation
- Author: B. Ravi, G.L. Datta
- Publication Year: 2006
- Publishing Journal/Academic Society: Technical paper for the 54th Indian Foundry Congress, Pune
- Keywords: Computer-aided Design, Casting Simulation, Foundry, Internet
2. Abstracts or Introduction
Virtual casting trials are crucial for ensuring castings are right the first time, utilizing computer-aided modelling, pattern design, methoding, simulation, and optimisation. Casting simulation technology has demonstrated reliability across various cast metals and processes, even for intricate castings. However, Small and Medium Enterprises (SME) foundries often find it unaffordable and inaccessible. This paper proposes a collaborative national initiative to establish a virtual foundry accessible via the Internet. This platform enables virtual casting trials to optimise tooling, methoding, and process parameters, consuming fewer resources than real trials while providing enhanced insights for quality attainment. Supported by trained casting engineers, the virtual foundry offers guidance and technical support, with its architecture, functions, and mechanism designed for ease of use and benefit for even small, remote foundries.
3. Research Background:
Background of the Research Topic:
Computer-aided casting development is composed of three primary phases: shape design and optimisation, tooling development and methoding optimisation, and casting process planning. Despite the proven benefits of computer-aided casting development technologies, including cost savings in casting trials, regular production, and design improvements, along with value-added benefits and long-term advantages, their adoption, particularly casting simulation programs, remains limited, especially among SME foundries.
Status of Existing Research:
A survey of over 100 foundries in India indicated that while Internet-based applications and CAD/CAM software adoption is growing, casting simulation programs have a low penetration rate (around 15% in the sample group, <3% overall). Despite acknowledging the benefits of casting simulation in faster development, reduced rejections, higher yield, cost reduction, and improved customer satisfaction, foundries are hesitant to adopt the software due to high initial costs, difficulty in securing qualified manpower, and inadequate long-term technical support from vendors. These challenges are amplified for SME foundries in remote areas.
Necessity of the Research:
To overcome the barriers hindering widespread adoption of casting simulation, particularly in SME foundries, there is a need to address the high cost and complexity associated with these technologies. The paper identifies that for broader acceptance, virtual casting trials must demonstrate significantly greater benefits than real trials, and their cost and difficulty must be considerably lower. While the first condition is generally met by current casting simulation programs, the second condition remains a major obstacle, especially for SME foundries.
4. Research Purpose and Research Questions:
Research Purpose:
The primary research purpose is to propose and describe the architecture, functions, and implementation of a "co-operative virtual foundry" system. This system aims to provide cost-effective and accessible casting simulation capabilities to SME foundries, thereby enhancing their competitiveness. The virtual foundry is envisioned as a solution to the limitations of traditional casting simulation software adoption by addressing issues of cost, expertise, and support.
Key Research:
The key research focuses on the development of two critical technologies for the virtual foundry:
- Automated methoding and casting simulation technologies: These technologies are based on the "AutoCAST" system and utilise methodologies for automated methoding (determining casting orientation, parting line, feeder and gating design) and casting simulation (mould filling and solidification).
- Web-based casting project management technologies: This involves developing a web-friendly language (CastML based on XML) for capturing and storing casting project information and creating a client-server system (WebICE) for web-based casting project management and collaborative engineering.
Research Hypotheses:
The paper does not explicitly state research hypotheses. However, the implicit hypothesis is that a co-operative virtual foundry, leveraging automated methoding, casting simulation, and web-based technologies, can effectively address the cost and accessibility barriers for SME foundries to adopt casting simulation, leading to improved efficiency and quality in casting production.
5. Research Methodology
Research Design:
The research employs a system design and development approach. It outlines the conceptual design and architecture of a virtual foundry system. This involves integrating existing technologies in automated methoding and casting simulation (AutoCAST) with newly developed web-based project management tools (WebICE and CastML). The design is driven by the need to create a cost-effective, accessible, and user-friendly platform for casting simulation, specifically targeting SME foundries.
Data Collection Method:
The paper refers to a survey of over 100 foundries to understand the challenges and needs of the industry regarding casting simulation adoption. It also mentions validation of the "AutoCAST" system through troubleshooting and optimising over one hundred industrial castings and implementation in 40+ foundries. Feedback from test users of the WebICE system is also mentioned as valuable input for system development. Case studies of industrial castings are presented to demonstrate the application and benefits of the technology.
Analysis Method:
The analysis primarily involves demonstrating the feasibility and potential benefits of the proposed virtual foundry system through system description, architecture diagrams, and industrial case studies. The effectiveness of the underlying technologies (AutoCAST and WebICE) is validated through prior industrial applications and user feedback. The paper uses descriptive analysis to explain the system's functionalities and working mechanism.
Research Subjects and Scope:
The research focuses on developing a virtual foundry system for the Indian foundry industry, particularly targeting SME foundries. The scope includes the design of the system architecture, development of key technologies (automated methoding, casting simulation, web-based project management), and demonstration of its potential through industrial case studies. The system is designed to support various casting processes and materials relevant to the foundry industry.
6. Main Research Results:
Key Research Results:
- Development of Automated Methoding and Casting Simulation (AutoCAST): The paper highlights the development and validation of AutoCAST, capable of automated methoding (casting orientation, parting line, feeder and gating design) and casting simulation (mould filling and solidification). It uses geometric modulus for feeder design and considers factors like casting weight, section thickness, and fluidity for gating design. Simulation uses vector element method to predict shrinkage defects.
- Development of Web-based Integrated Casting Engineering (WebICE): The paper presents WebICE, a web-based system for casting project management and collaborative engineering. Key components include:
- CastML (Casting Markup Language): An XML-based language for capturing and storing casting project information.
- WebICE Interface: A client-server system facilitating web-based access to casting project data, cost estimation, and collaborative tools (Figure 6).
- Virtual Foundry Architecture: The paper proposes a three-gate security architecture for the virtual foundry zone and individual virtual foundries (Figure 8). It outlines five major sections within a virtual foundry: Part, Tooling, Methoding, Casting, and Planning (Figure 9), detailing the functions within each section.
- Industrial Case Studies: The paper presents three case studies demonstrating the application of the technology:
- Aluminium-alloy switchgear tank: Gravity die casting, improved methoding using simulation reduced rejection from 35% to less than 6% (Figure 3).
- Ductile iron railway insert casting: Disamatic process, modified feeder design based on simulation improved yield from 66% to 67% (Figure 4).
- Steel press cylinder: Green sand casting, simulation identified micro-porosity issue, design modification improved service life (Figure 5).
Analysis of presented data:
- Figure 1. Phases and work-flow in computer-aided casting development: Illustrates the three phases of computer-aided casting development (shape design, tooling development, process planning) and the iterative workflow involving part designer, CAE engineer, tool designer, planning engineer, and casting engineer.
- Figure 2. Benefits and concerns of computer-aided casting software: Bar charts comparing perceived benefits (customer satisfaction, faster development, lower rejection, higher yield, cost reduction) and concerns (initial cost, trained manpower, technical support, maintenance) of computer-aided casting software.
- Figure 3. Aluminium-alloy circuit breaker tank by gravity die casting: Shows images of the casting and simulation results, highlighting shrinkage areas and the effect of methoding changes.
- Figure 4. Ductile iron railway insert casting by Disamatic process: Depicts the casting and simulation results, demonstrating the impact of feeder modification on shrinkage.
- Figure 5. Steel press cylinder by green sand casting process: Presents images of the casting and simulation results, illustrating porosity issue and design modification.
- Figure 6. Web-based integrated casting engineering (WebICE) system: Screenshot of the WebICE interface showing cost estimation features.
- Figure 7. Architecture of virtual foundry system: Diagram illustrating the hierarchical architecture of the virtual foundry, including casting software, VF server, technical support team, software development team, virtual foundries (VF-A, VF-B, VF-C), real foundries (RF-A, RF-B, RF-C), and OEM firms (OEM-X, OEM-Y, OEM-Z).
- Figure 8. Security gates of virtual foundry zone and a selected foundry: Diagram showing the three security gates for accessing the virtual foundry zone, a particular virtual foundry, and a specific casting project.
- Figure 9. Major sections and functions of the virtual foundry: Table outlining the five major sections of the virtual foundry (Part, Tooling, Methoding, Casting, Planning) and their respective functions (part modeling, mould parting, feeder design, charge mix, process planning, etc.).
Figure Name List:
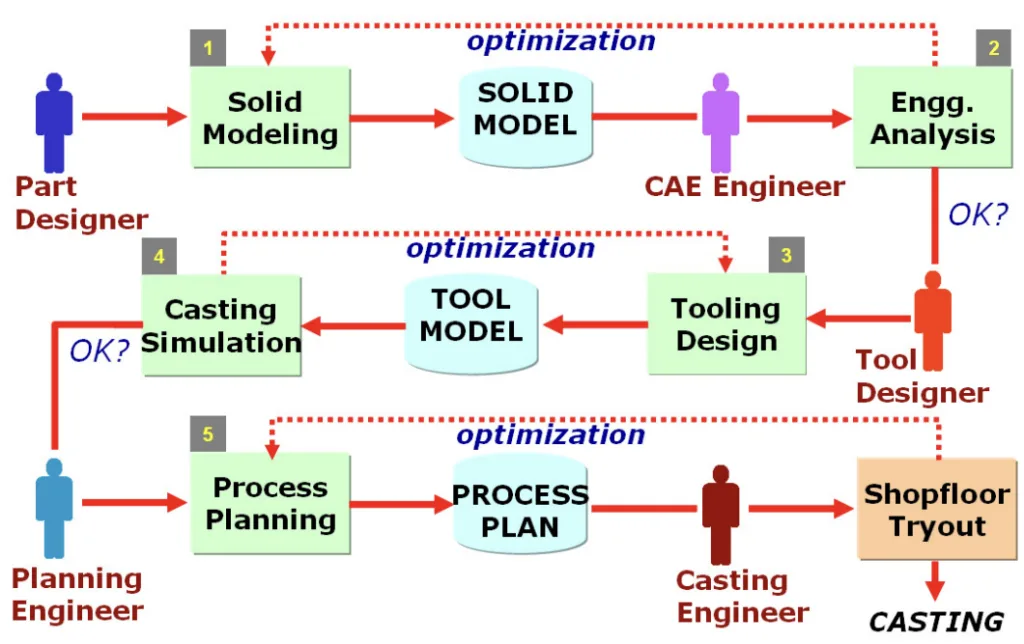

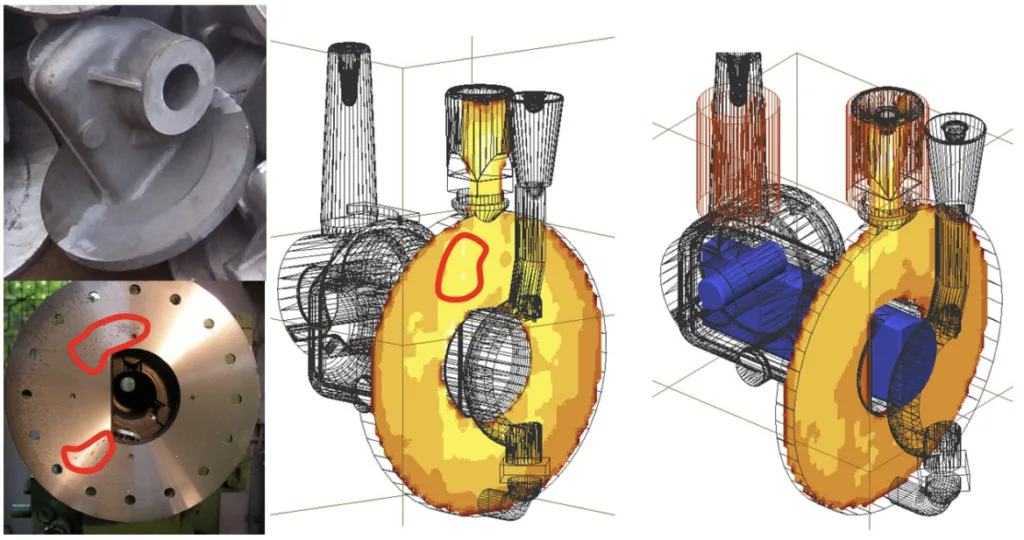
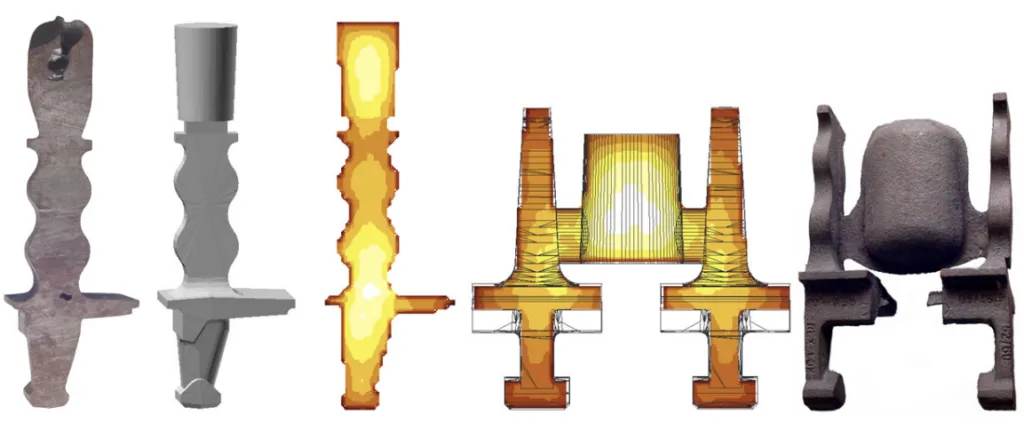
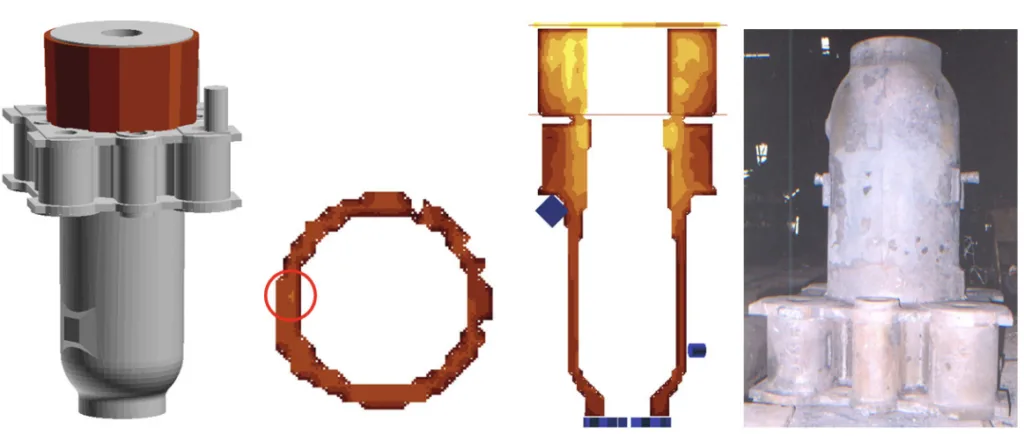
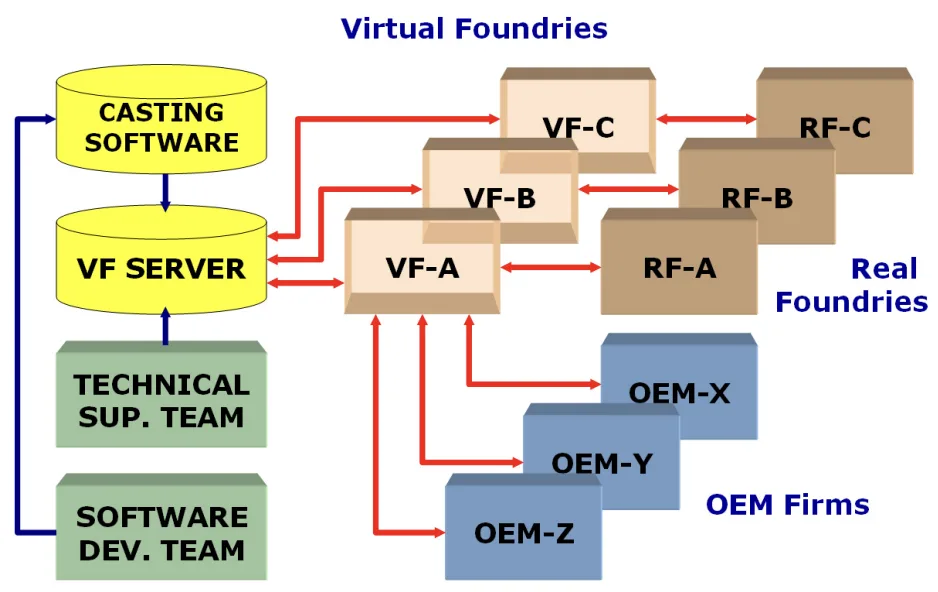
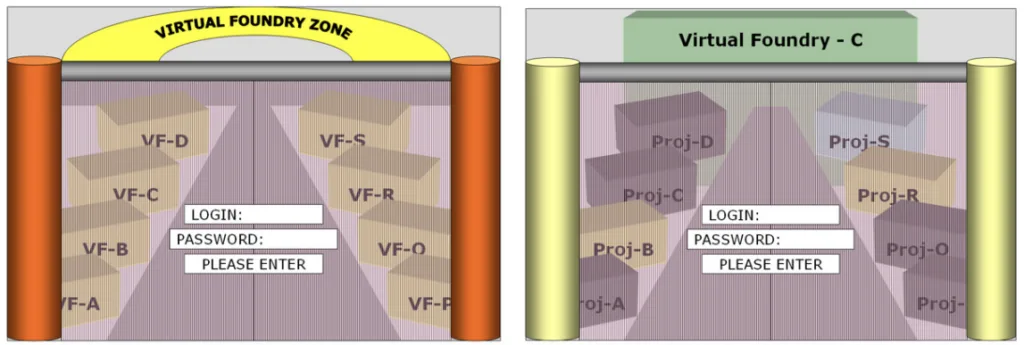
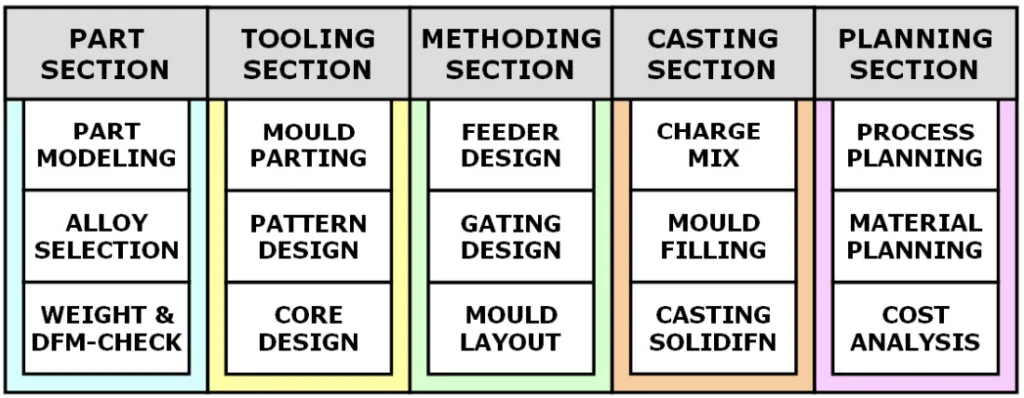
- Figure 1. Phases and work-flow in computer-aided casting development
- Figure 2. Benefits and concerns of computer-aided casting software.
- Figure 3. Aluminium-alloy circuit breaker tank by gravity die casting
- Figure 4. Ductile iron railway insert casting by Disamatic process
- Figure 5. Steel press cylinder by green sand casting process
- Figure 6. Web-based integrated casting engineering (WebICE) system
- Figure 7. Architecture of virtual foundry system
- Figure 8. Security gates of virtual foundry zone and a selected foundry
- Figure 9. Major sections and functions of the virtual foundry
7. Conclusion:
Summary of Key Findings:
The paper proposes a "co-operative virtual foundry" as a solution to enhance the competitiveness of the foundry industry, particularly SME foundries, by providing cost-effective access to casting simulation services via the Internet. The virtual foundry integrates automated methoding and casting simulation technologies (AutoCAST) with web-based project management tools (WebICE and CastML). Industrial case studies demonstrate the effectiveness of these technologies in improving casting quality and yield. The proposed system architecture includes security measures and functional sections designed to facilitate collaborative casting development.
Academic Significance of the Study:
This study contributes to the field of casting technology by presenting a novel approach to democratizing access to advanced casting simulation tools. The concept of a virtual foundry, leveraging web-based technologies and automated simulation, offers a significant paradigm shift in how casting design and optimisation can be conducted, especially for resource-constrained SME foundries. The integration of Holonic Manufacturing System (HMS) concepts for virtual foundry management also adds academic value.
Practical Implications:
The virtual foundry concept has significant practical implications for the foundry industry. It offers a pathway for SME foundries to adopt casting simulation technologies without substantial upfront investment in software and expertise. By reducing the cost and complexity of casting trials, the virtual foundry can lead to faster product development cycles, improved casting quality, reduced rejection rates, and enhanced competitiveness for foundries, particularly in the global market. It can also facilitate better collaboration between OEM firms and foundries.
Limitations of the Study and Areas for Future Research:
The paper is primarily a conceptual proposal and system design description. It lacks empirical validation of the virtual foundry system in a real-world operational environment. Future research should focus on:
- Implementation and deployment: Developing and deploying a fully functional virtual foundry system as outlined in the paper.
- System validation: Conducting extensive testing and validation of the virtual foundry system in industrial settings, assessing its performance, usability, and impact on foundry operations.
- User experience and adoption studies: Investigating the user experience of foundry engineers and OEM customers using the virtual foundry and studying the factors influencing its adoption and long-term sustainability.
- Expansion of functionalities: Exploring and integrating advanced functionalities such as AI-driven optimisation, cloud-based simulation, and integration with other manufacturing systems within the virtual foundry framework.
8. References:
- B. Ravi, Durgesh Joshi, Rahul Chougule, “Survery of Computer Applications in Indian Foundry Industry: Benefits and Concerns," Proceedings of the 53rd Indian Foundry Congress, Kolkata, Jan 2005.
- B. Ravi, R.C. Creese and D. Ramesh, “Design for Casting – A New Paradigm to Prevent Potential Problems,” Transactions of the AFS, 107, 1999.
- M. Nainy-Nejad, R.C. Creese and B. Ravi, “Research Issues in Computer-Aided Parting Design,” Transactions of the AFS, 105, 1997.
- B. Ravi, “Intelligent Design of Gating Channels for Casting,” Materials Science and Technology, 13(9), 785-790, 1997.
- Ravi and M.N. Srinivasan, “Casting Solidification Analysis by Modulus Vector Method," International Cast Metals Journal, 9(1), 1-7, 1996.
- R.G. Chougule and B. Ravi, “Collaborative Design for Manufacture – Metal Casting Applications," 8th IEEE International Conference on Intelligent Engineering Systems, Cluj Napoca, Romania, 19-21 September 2004.
- M.M. Akarte and B. Ravi, “Casting Data Markup Language for Web-based Collaborative Engineering,” Transactions of the AFS, 110, 93-108, 2002.
- R.G. Chougule and B. Ravi, “Casting Process Planning Using Case Base Reasoning,” Transactions of the AFS, 111, 1321-1330, 2003.
- R.G. Chougule and B. Ravi, “Casting Cost Estimation in an Integrated Product and Process Design Environment,” International Journal of Computer Integrated Manufacturing, in press.
- R. Chougule, M.M. Akarte and B. Ravi, “Virtual Foundry Modeling and its Applications," 20th AIMTDR Conference, Ranchi, December 2002.
- M. Muralidhar and G.L. Datta, “Design of a Holonic Casting Test Bed for Typical Automotive Castings,” Proceedings of the 51' Indian Foundry Congress, Jaipur, January 2003.
9. Copyright:
- This material is "B. Ravi, G.L. Datta"'s paper: Based on "Co-operative Virtual Foundry for Cost-Effective Casting Simulation".
- Paper Source: https://www.researchgate.net/publication/228886765
This material was created to introduce the above paper, and unauthorized use for commercial purposes is prohibited.
Copyright © 2025 CASTMAN. All rights reserved.