This article introduces the paper "[Casting of Combustion Engine Pistons Before and Now on the Example of FM Gorzyce]"
1. Overview:
- Title: Casting of Combustion Engine Pistons Before and Now on the Example of FM Gorzyce
- Authors: M. Czerepak, J. Piątkowski
- Publication Year: 2023
- Journal/Publisher: Archives of Foundry Engineering
- Keywords: Casting, Silumins, Pistons, Permanent Moulding Casting Machines, Surface Treatment
![Fig. 1. Old method of casting pistons: a) manual casting; b) single permanent mould casting machine [7]](https://castman.co.kr/wp-content/uploads/image-271-png.webp)
2. Research Background:
Social/Academic Context:
Combustion engine pistons face increasingly stringent demands driven by the need for enhanced thermo-mechanical loads, reduced exhaust emissions, and improved fuel efficiency. The automotive industry's push for lighter vehicles and higher engine speeds intensifies pressure and inertial forces within cylinders, placing significant burdens on piston design.
Limitations of Existing Research:
Older piston casting methods and designs were inadequate for meeting the high-performance and high-efficiency requirements of modern engines. Early casting relied on manual processes, single permanent molds, and basic cooling systems, leading to inconsistent crystallization and lower production efficiency. Pistons from the 1970s and 1980s were described as "quite massive" and lacked advanced features like cooling channels or sophisticated surface treatments.
Necessity of the Research:
This research is crucial for understanding the evolution of permanent mold casting machines and piston design to meet the ever-tightening standards of contemporary combustion engines. With the imperative to improve engine efficiency, reduce fuel consumption and emissions, and enhance piston durability under extreme conditions, analyzing the 50-year transformation at FM Gorzyce provides a valuable real-world case study.
3. Research Purpose and Research Questions:
Research Purpose:
The study aims to highlight the key changes in permanent mold casting machines and silumin piston casting technology at Federal-Mogul Gorzyce over five decades.
Key Research Questions:
This paper addresses the following core areas of change:
- Transformations in the construction of casting machines and permanent molds for silumin engine piston casting.
- Modernization of cooling systems for primary permanent mold components.
- Evolution of piston designs for both diesel and gasoline engines.
Research Hypotheses:
While not explicitly stated, the paper implicitly explores the hypothesis that advancements in casting machine technology (automation, cooling systems) and piston design (materials, features, surface treatments) at FM Gorzyce have significantly improved production efficiency, piston performance, and overall engine efficiency.
4. Research Methodology:
Research Design:
This research employs a case study approach, examining the historical evolution of casting technology and piston design at Federal-Mogul Gorzyce over 50 years. It is a descriptive and comparative study, showcasing the "before and after" states of piston casting and design to illustrate technological progress.
Data Collection Methods:
Data was gathered from Federal-Mogul Gorzyce's operational history and technical documentation, including proprietary company materials and observations of their manufacturing processes. Visual examples are provided through figures illustrating casting machines, molds, and piston designs from different eras.
Analysis Methods:
The analysis is primarily qualitative, describing and comparing changes in casting machines, mold designs, cooling systems, and piston construction over time. It uses a historical and descriptive approach to illustrate advancements and their impact. Production data (Figure 13) quantifies the impact of these changes on piston production volume.
Research Subjects and Scope:
The research focuses specifically on the evolution of permanent mold casting machines and silumin piston castings at Federal-Mogul Gorzyce. The scope covers a 50-year production period, examining changes relevant to both gasoline and diesel engine pistons.
5. Main Research Results:
Key Research Results:
- Evolution of Casting Machines: Transition from manual casting with single permanent molds to fully automated casting stations with double permanent molds and robotic handling. Modern machines feature sophisticated hydraulic systems and advanced, numerically controlled cooling systems.
- Improved Cooling Systems: Modern permanent mold casting machines utilize complex cooling systems with multiple circuits and electrovalve assemblies, ensuring uniform cooling and controlled crystallization of piston casts. This significantly reduced cooling time and improved process efficiency.
- Piston Design Transformation: Piston designs have undergone a "diametric transformation" to meet modern engine demands. Key changes include:
- Variously shaped crowns optimized for direct or indirect injection engines.
- Slimmed internal construction to reduce mass and improve cooling.
- Incorporation of components like cooling channels (salt cores) and ring inserts ("alfin" inserts).
- Advanced surface treatment procedures for piston skirts and ring grooves.
- Material Advancements: Continued use of near-eutectic Al-Si alloys for piston castings, with detailed chemical compositions (Table 1). Use of austenitic cast iron for ring inserts (Table 2).
- Increased Production Efficiency: Automation and improved technology dramatically increased production volume. Before automation (1990-2005), annual production was around 4 million pistons. After modernizing lines (2006-2021), production surged to over 25 million pistons annually (Figure 13).
- Contribution to Engine Efficiency: These advancements contribute to improved engine efficiency (currently around 52%, up from ~40%), reduced fuel consumption, and lower emissions.
Statistical/Qualitative Analysis Results:
- Figure 13 demonstrates a significant increase in piston production at Federal-Mogul Gorzyce from 2006 to 2021, highlighting the impact of modernized casting lines.
- Cooling time decreased from approximately 60 seconds in older machines to 13 seconds or less in modern automated systems.
- Piston crown temperature reduced by 25-30°C in modern designs compared to 1980s-1990s designs.
- Upper ring temperature lowered to below 250°C with ring inserts.
- Engine efficiency increased from approximately 40% to 52%.
Data Interpretation:
The data clearly indicates a progression in casting technology and piston design at FM Gorzyce. Automation, advanced cooling, and design innovations have collectively driven significant improvements in production efficiency, piston performance characteristics (strength, cooling, friction reduction), and ultimately, engine efficiency and durability.
Figure List:
- Fig. 1. Old method of casting pistons
- Fig. 2. Permanent mould casting machine for casting single pistons
- Fig. 3. Casts of an previous gasoline engine piston with diameter Ø 90 mm
- Fig. 4. Cast of an old Diesel engine piston with a) diameter Ø 110 mm
- Fig. 5. Automatized station for casting piston MFGD (Multi Functional Gasoline Diesel)
- Fig. 6. Model of a modern double permanent mould for piston casting (Gasoline)
- Fig. 7. Exemplary pistons for engines with direct ejection
- Fig. 8. Exemplary pistons for Light Vehicles engines
- Fig. 9. Internal construction of the present pistons
- Fig. 10. Modern pistons with a ring insert and a salt core for
- Fig. 11. Pistons for a Diesel engine
- Fig. 12. Piston skirt after graphite covering
- Fig. 13. Piston production at Federal-Mogul 2006 - 2021

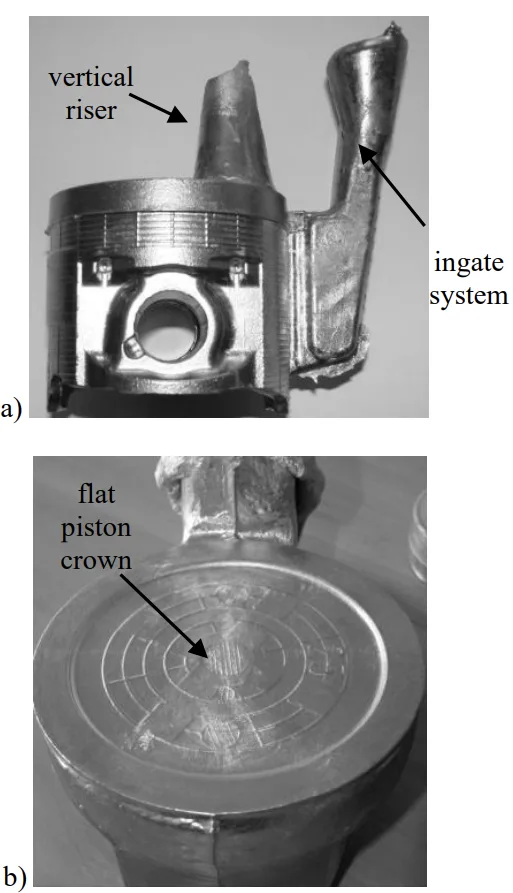
![Fig. 6. Model of a modern double permanent mould for piston casting (Gasoline) [7]](https://castman.co.kr/wp-content/uploads/Fig.-6.-Model-of-a-modern-double-permanent-mould-for-piston-casting-Gasoline-7.webp)
![Fig. 5. Automatized station for casting piston MFGD (Multi Functional Gasoline Diesel) [7]](https://castman.co.kr/wp-content/uploads/image-274-png.webp)
![Fig. 10. Modern pistons with a ring insert and a salt core for: a) a Diesel engine, b) a gasoline engine [7]](https://castman.co.kr/wp-content/uploads/Fig.-10.-Modern-pistons-with-a-ring-insert-and-a-salt-core-for-a-a-Diesel-engine-b-a-gasoline-engine-7.webp)
6. Conclusion and Discussion:
Summary of Main Results:
The study demonstrates the substantial evolution in combustion engine piston casting and design at FM Gorzyce over the past 50 years. Key advancements include the shift to automated, high-efficiency casting machines with sophisticated cooling, and the transformation of piston designs to incorporate features like cooling channels, ring inserts, and advanced surface treatments. These changes have led to significant improvements in production volume, piston performance, and engine efficiency.
Academic Significance:
This paper provides a valuable historical and technical overview of advancements in die casting technology and piston design within a real-world manufacturing context. It highlights the impact of engineering innovation on improving manufacturing processes and product performance in the automotive industry. It serves as a case study illustrating the evolution of casting techniques to meet increasingly demanding engine requirements.
Practical Implications:
The practical implications are significant for the die casting and automotive industries. The paper showcases proven strategies for enhancing casting efficiency through automation and advanced cooling systems. It also provides insights into effective piston design features and surface treatments that improve engine performance, durability, and reduce fuel consumption and emissions. The FM Gorzyce example can serve as a benchmark for manufacturers seeking to modernize their piston production and design processes.
Limitations of the Research:
The research is primarily focused on a single company, Federal-Mogul Gorzyce. While providing in-depth insights into their specific evolution, the findings may not be fully generalizable to all die casting facilities or piston manufacturers globally. The paper is descriptive and does not delve deeply into the quantitative performance improvements of each specific design or process change, beyond overall production volume and efficiency metrics.
7. Future Follow-up Research:
Directions for Follow-up Research:
Future research could explore:
- Quantitative analysis of the impact of specific design features (e.g., cooling channels, ring inserts, surface treatments) on piston performance metrics like temperature distribution, friction, and wear.
- Comparative studies of piston casting and design evolution across multiple manufacturers and regions to identify common trends and best practices.
- Investigation into the environmental impact of these technological advancements, including energy consumption and material efficiency in piston production.
- Further research into advanced materials and casting techniques for next-generation combustion engines and alternative fuel engines.
Areas Requiring Further Exploration:
- Optimization of cooling channel designs and cooling strategies for different engine types and operating conditions.
- Development of even more advanced surface treatments to further reduce friction and wear in piston systems.
- Exploration of novel piston materials beyond traditional Al-Si alloys to meet future engine performance and emission requirements.
8. References:
- [1] Pietrowski, S. (2001). Silumines. Łodź: Publishing University of Technology. (in Polish).
- [2] Ranjith Kumar, P., Chandrasekaaran, K. & Kannan, TTM. (2021). Investigation and Analysis of Engine Piston Rod Material. Automotive Material. London: LAP Lambert.
- [3] Rowe, J. (2021). Advanced Materials in Automotive Engineering. Woodhead Publishing.
- [4] Kammer, C. (2011). Aluminium Handbook. Vol. 1: Fundamentals and Materials. Beuth Verlag GmbH.
- [5] Manasijevic, S. (2012). Aluminum Piston Alloys. Radiša, R. (Ed.). Serbia: LOLA Institute Belgrade.
- [6] Oppenheim, A.K. (2004). Combustion in Piston Engines. Technology, Evolution and Control. Springer.
- [7] Federal-Mogul Gorzyce. Company own technical materials, Gorzyce 2022. Retrieved October 29, 2022 from https://www.fmgorzyce.pl/ (in Polish).
- [8] Pater, Z. (2014). Basics of metallurgy and foundry. Lublin.
- [9] Pietrowski, S. & Szymczak, T. (2006). The influence of selected factors on the cnstruction of the alfined layer on iron alloys. Archives of Foundry. 6(19), 251-266. (in Polish). ISSN 1642-5308.
- [10] Pietrowski, S. (2001). Structure of alifinishing layer on the gray cast iron. Archives of Foundry. 4(11), 95-104. (in Polish). ISSN 1642-5308.
- [11] Piątkowski, J. & Czerepak, M. (2020). The crystallization of the AlSi9 alloy designed for the alfin processing of ring supports in engine piston. Archives of Foundry Engineering. 20(2), 65-70. DOI: 10.24425/afe.2020.131304.
- [12] Crolla, D.A. (2009). Automotive engineering. powertrain, chassis system and vehicle body. United States of America: Butterworth-Heinemann.
- [13] Wróblewski, E. (2019). The influence of microgeometry of the piston lateral surface on the mechanical efficiency of a combustion engine. Unpublished doctoral dissertation, University of Technology, Poznań. (in Polish).
- [14] Zając, P., Kołodziejczyk, L.M. (2001). Internal combustion engines. Warszawa: WSP. (in Polish).
- [15] Iskra, A. & Kałużny, J. (2000). Effect of the actual shape of the piston side surface on oil film parameters. Journal of Kones. 7(1-2).
- [16] Piątkowski, J., Grabowski, A. & Czerepak, M. (2016). The influence of laser surface remelting on the microstructure of EN AC-48000 cast alloy. Archives of Foundry Engineering. 16(4), 217-221. DOI: 10.1515/afe-2016-0112.
9. Copyright:
*This material is based on the paper by M. Czerepak and J. Piątkowski: "Casting of Combustion Engine Pistons Before and Now on the Example of FM Gorzyce."
*Paper Source: 10.24425/afe.2023.144296
This material is a summary of the above paper, and unauthorized use for commercial purposes is prohibited.
Copyright © 2025 CASTMAN. All rights reserved.