This article introduces the paper "BMW's Magnesium-Aluminium Composite Crankcase, State-of-the-Art Light Metal Casting and Manufacturing" presented at the SAE International.
1. Overview:
- Title: BMW's Magnesium-Aluminium Composite Crankcase, State-of-the-Art Light Metal Casting and Manufacturing
- Author: Michael Hoeschl, Wolfram Wagener and Johann Wolf
- Publication Year: 2006
- Publishing Journal/Academic Society: SAE International
- Keywords: magnesium casting, aluminium, composite crankcase, light metal casting, manufacturing, engine design, efficient dynamics, automotive engineering
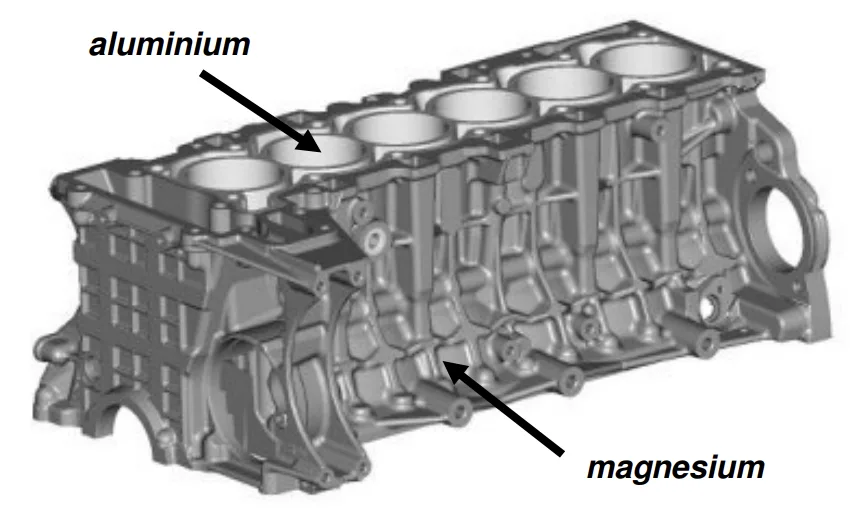
2. Research Background:
- Social/Academic Context of the Research Topic: The automotive industry is continuously driven by the demand for enhanced dynamic performance and reduced fuel consumption. Achieving a balance between increased power and decreased weight is a critical challenge. BMW's brand identity is strongly associated with high agility and driving experience, necessitating innovative approaches to engine design and manufacturing.
- Limitations of Existing Research: Traditional methods of lightweight engine component design were becoming inadequate for meeting the demands of new engine generations. Previous technological leaps in crankcase material, such as the shift from iron casting to aluminium, had already yielded significant weight reductions. Further weight reduction using conventional aluminium crankcases was proving increasingly difficult.
- Necessity of the Research: To realize the concept of "efficient dynamics," BMW needed to explore new directions in engine design, particularly focusing on weight reduction of the crankcase, while simultaneously enhancing power and reducing fuel consumption. This necessitated a departure from incremental improvements and the adoption of revolutionary approaches, including the investigation of magnesium and composite materials.
3. Research Purpose and Research Questions:
- Research Purpose: The primary purpose of this research was to develop and implement a magnesium-aluminium composite crankcase for BMW's inline six-cylinder engine, representing a significant advancement in lightweight design and manufacturing for mass production.
- Key Research Questions:
- How can magnesium casting be utilized for mass production of a water-cooled crankcase in modern engine design?
- What are the optimal material combinations and constructive structures to overcome the limitations of magnesium, such as lower Young's modulus and corrosion stability, in a crankcase application?
- How can a robust and reliable manufacturing process be established for a complex composite component like the magnesium-aluminium crankcase?
- What innovative testing methodologies are required to ensure the quality and performance of the composite crankcase, particularly regarding the bonding between magnesium and aluminium and the silicon distribution in the aluminium insert?
- Research Hypotheses: The research hypothesized that a composite design, combining a magnesium housing with an aluminium insert and sintered steel inlays, could achieve significant weight reduction and meet the stringent performance and durability requirements for a high-performance engine crankcase. It was also hypothesized that advanced casting, surface treatment, and testing processes would be essential for successful mass production.
4. Research Methodology:
- Research Design: The research employed a design and development approach, focusing on the conceptualization, material selection, structural design, manufacturing process development, and testing of a magnesium-aluminium composite crankcase.
- Data Collection Method: The paper primarily details the process development and manufacturing steps. Material data and performance characteristics are referenced but not explicitly derived through experimentation within this paper. Testing methodologies are described, including X-ray inspection, eddy-current testing for silicon distribution, and ultrasonic-stimulated lock-in thermography for bonding quality.
- Analysis Method: The research utilized computer simulation (FDM-software tools from MagmaSoft) for casting process planning and optimization. For quality assurance, methods included data matrix code (DMC) tracking, X-ray inspection, eddy-current testing, and ultrasonic-stimulated lock-in thermography. Microscopic analysis was mentioned as a conventional method for silicon particle analysis, against which the eddy-current method is compared.
- Research Subjects and Scope: The research focused on the development of a crankcase for BMW's inline six-cylinder spark-ignition engine. The scope encompassed the design, material selection, casting, manufacturing, surface treatment, machining, and quality assurance processes specifically for this composite crankcase. The research was conducted at BMW's Landshut plant and engine plant in Steyr, Austria, involving collaboration with external material suppliers.
5. Main Research Results:
- Key Research Results:
- Successful development and mass production implementation of a water-cooled magnesium-aluminium composite crankcase.
- Achievement of significant weight reduction compared to previous aluminium and iron crankcase designs (Figure 2).
- Introduction of a composite structure featuring a magnesium housing (alloy AJ62), a hyper-eutectic aluminium alloy (AlSi17Cu4Mg) insert for cylinder liners, and sintered steel inlays in a magnesium bedplate.
- Development of specialized manufacturing processes, including low-pressure casting for the aluminium insert, high-pressure die casting (HPDC) for the magnesium housing and bedplate, and thermal arc-wire spray process (LDS) for surface treatment.
- Implementation of innovative quality assurance methodologies, including eddy-current testing for silicon distribution and ultrasonic-stimulated lock-in thermography for bonding quality.
- Statistical/Qualitative Analysis Results: The paper primarily focuses on process description and qualitative assessments of design and manufacturing innovations. Quantitative data is presented in Figure 2, illustrating the weight development of crankcases, showing a significant weight reduction with the Mg/Al composite casting.
- Data Interpretation: Figure 1 defines "efficient dynamics" as a combination of weight reduction (-10 kg crankcase), increased engine power (+20 kW), and reduced fuel consumption (-12%). Figure 2 shows the weight reduction achieved with the magnesium-aluminium composite crankcase compared to iron casting, aluminium casting, and AlSi17 with integration. The composite design achieves the lowest weight.
- Figure Name List:
- Figure 1: Definition of efficient dynamics
- Figure 2: Weight development of crankcases
- Figure 3: Composite Mg/Al cylinder crankcase
- Figure 4: Section crankcase with bedplate
- Figure 5: Insert, made of AlSi17Cu4Mg
- Figure 6: Coding of components by DMC [3]
- Figure 7: Aluminium coating of the insert
- Figure 8: Reaction zone between Mg and Al
- Figure 9: Central melting facility at BMW Landshut plant
- Figure 10: Magnesium ingot pallet
- Figure 11: Transportation of liquid magnesium
- Figure 12: Die casting machines at BMW Landshut plant
- Figure 13: Robots remove crankcases from the hpdc
- Figure 14: Encapsulated machining centre (BAZ)
- Figure 15: BAZ design to prevent chip accumulation
- Figure 16: Briquette made of Mg-Al-chips
- Figure 17: Primary and secondary silicon particles (microscopic analysis)
- Figure 18: Eddy-current analysis of a cylinder liner
- Figure 19: Schematic illustration of the US-lock-in-thermography [6]
- Figure 20: Result of a US-lock-in-thermography
- Figure 21: the new BMW 6-cyclinder engine
- Figure 22: The BMW 6-Series Coupé (2004)
- Figure 23: The new BMW 3-Series Estate
- Figure 24: BMW Concept Z4 Coupé and Z4 roadster
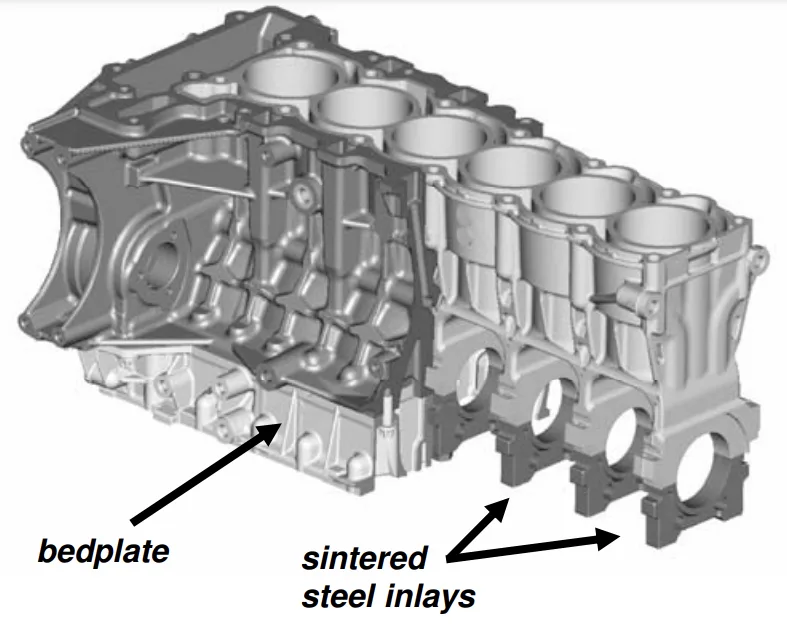
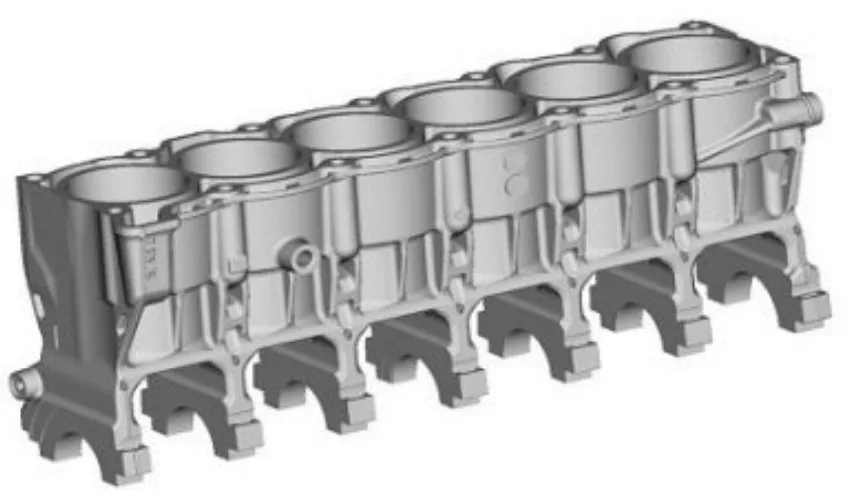
![Figure 6: Coding of components by DMC [3]](https://castman.co.kr/wp-content/uploads/image-327-png.webp)

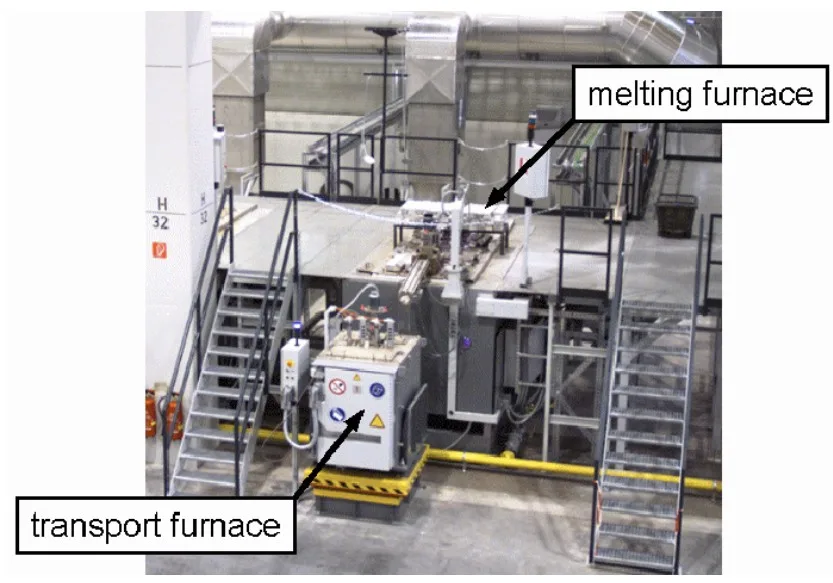
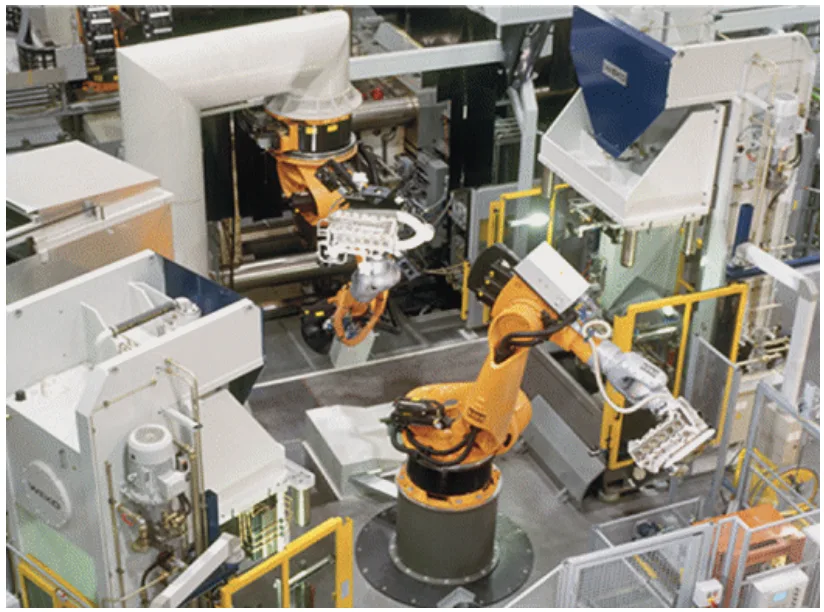
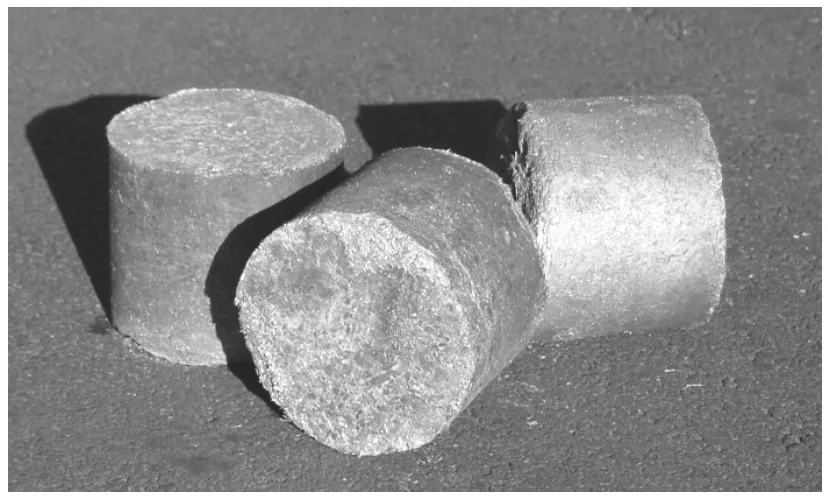
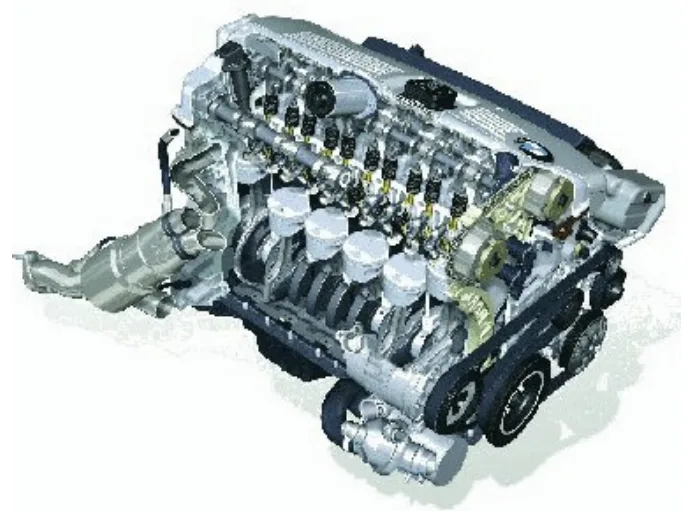
6. Conclusion and Discussion:
- Summary of Main Results: The research successfully demonstrated the feasibility of mass-producing a magnesium-aluminium composite crankcase for BMW's inline six-cylinder engine. This innovation achieved significant weight reduction while maintaining or enhancing engine performance and durability. Key to this success were the intelligent composite design, advanced casting and manufacturing processes, and innovative quality assurance methodologies.
- Academic Significance of the Research: This research contributes to the field of lightweight materials application in automotive engineering, specifically in engine design. It showcases a successful implementation of magnesium casting in a critical engine component, overcoming inherent material limitations through composite design and process innovation. The development of new testing methodologies, such as ultrasonic-stimulated lock-in thermography and advanced eddy-current analysis, also represents a significant academic contribution to non-destructive testing techniques.
- Practical Implications: The practical implications are substantial for the automotive industry. The magnesium-aluminium composite crankcase enables lighter and more fuel-efficient vehicles without compromising performance. The developed manufacturing and quality assurance processes provide a blueprint for mass production of complex composite components. The technology has been implemented in BMW's inline six-cylinder engines and expanded to various models.
- Limitations of the Research: The paper primarily focuses on the development and implementation process. Detailed performance data, such as comparative fuel consumption or emissions data, are not presented. Further research could explore the long-term durability and cost-effectiveness of this composite crankcase in mass production.
7. Future Follow-up Research:
- Directions for Follow-up Research: Future research could focus on:
- Further optimization of the composite design and material selection for enhanced performance and cost reduction.
- Exploration of alternative magnesium alloys and aluminium alloys for improved properties and processability.
- Development of even more efficient and environmentally friendly manufacturing processes for magnesium and aluminium components.
- Investigation of the long-term durability and reliability of the composite crankcase under various operating conditions.
- Application of similar composite design principles to other engine components and automotive structures.
- Areas Requiring Further Exploration: The area of joining technologies for dissimilar materials, particularly magnesium and aluminium, warrants further exploration to enhance the performance and reliability of composite structures. Additionally, advancements in non-destructive testing methods for complex interfaces and materials are crucial for ensuring the quality and safety of lightweight automotive components.
8. References:
- [1] C. Landerl, R. Jooß, A. Fischersworring-Bunk, J. Wolf, A. Fent, S. Jagodzinski, ‘Aluminium and magnesium compound construction-an innovative approach to lightweight technology in crankcases', 12th Aachen Colloquium (2003)
- [2] C. Landerl, M. Klueting: ‘The new BMW six-cylinder in-line spark-ignition engine', part 1: concept and constructive structure, Motortechnische Zeitschrift 65 (2004)
- [3] J. Wolf, W. Wagener, 'The BMW magnesium-aluminium crankcase a challenge for state-of-the-art light metal casting', IMA's 62nd Annual World Magnesium Conference, Berlin (2005)
- [4] E. Baril, P. Labelle, A. Fischersworring-Bunk, 'AJ(Mg-AI-Sr) Alloy System Used for New Engine Block', SAE2004-01-0659 (2004)
- [5] E. Baril, P. Labelle, M.O. Pekguleryuz, 'Elevated Temperature Mg-Al-Sr: Creep Resistance, Mechanical Properties and Microstructure' JOM (2003)
- [6] A. Fent, W. Wagener, F. Dörnenburg, A. Fischer-worring-Bunk, 'Innovative Testing Methodology for Quality Assurance of the new 6-Cylinder-Mg/Al-Composite Crankcase', 13.Magnesium-Abnehmer-seminar, EFM, Aalen (2005)
- [7] H. Brosinsky, ‘Stereoscan-Aufnahmen und Fax-Film-Bilder von Oberflächen gußeisener Motorenzylinder Technische Zeitung für praktische Metallbearbeitung, 64.Jahrgang (1970)
9. Copyright:
*This material is Michael Hoeschl, Wolfram Wagener and Johann Wolf's paper: Based on BMW's Magnesium-Aluminium Composite Crankcase, State-of-the-Art Light Metal Casting and Manufacturing.
*Paper Source: doi:10.4271/2006-01-0069
This material was summarized based on the above paper, and unauthorized use for commercial purposes is prohibited.
Copyright © 2025 CASTMAN. All rights reserved.