This article introduces the paper "Automated identification of complex undercut features for side-core design for die-casting parts".
1. Overview:
- Title: Automated identification of complex undercut features for side-core design for die-casting parts
- Author: Ranjit Singh, Jatinder Madan, and Rajesh Kumar
- Publication Year: 2014
- Publishing Journal/Academic Society: Proc IMechE Part B: Journal of Engineering Manufacture
- Keywords: Die casting, complex undercut features, feature recognition, side-core design, release direction
2. Research Background:
- Social/Academic Context of the Research Topic:
- Die casting is a crucial manufacturing process where molten metal is injected into a die consisting of core and cavity halves.
- Die design is a complex and time-consuming process that significantly impacts the lead time and manufacturing cost of die-casting parts.
- Identifying undercut features is a critical step in die design, directly influencing the determination of the parting line and the design of core and cavity.
- Side-cores, specialized tooling components, are essential for molding undercut features and are designed after these features are identified.
- Traditionally, the identification of undercut features is performed manually by die design experts.
- Limitations of Existing Research:
- Despite valuable prior research in feature recognition and undercut feature detection, the literature review reveals gaps in addressing complex undercut features.
- Specifically, previous works have not fully attended to:
- Recognition of complex undercut features.
- Classification of complex undercut features.
- Division of complex undercut features into simple ones.
- Necessity of the Research:
- The manual identification of undercut features represents a bottleneck and a gap in the design-manufacturing integration within the die-casting process.
- This research is motivated by the necessity to bridge this gap by developing an automated system for identifying complex undercut features.
- Furthermore, a methodology to divide complex undercut features into simpler components is needed to facilitate the subsequent side-core design process.
3. Research Purpose and Research Questions:
- Research Purpose:
- The primary purpose of this research is to develop an automated system for the identification, classification, division, and determination of the release direction of complex undercut features in die-cast parts.
- The proposed system leverages the concepts of visibility and accessibility to achieve these objectives.
- Key Research Questions:
- How can complex undercut features in die-casting parts be automatically identified from a B-rep model?
- How can these identified complex undercut features be effectively classified?
- How can complex undercut features be divided into simpler, manageable undercut features?
- How can the release direction for each simple undercut feature be determined and grouped for efficient side-core design?
- Research Hypotheses:
- It is hypothesized that a system utilizing visibility and accessibility concepts can be developed to automate the identification, classification, division, and release direction determination of complex undercut features in die-casting parts.
- The rule-based algorithm proposed in this research can effectively classify and divide undercut features, enabling automated side-core design.
4. Research Methodology:
- Research Design:
- The research employs a system development approach, focusing on creating an automated system for undercut feature processing.
- A rule-based algorithm is designed and implemented to classify and divide undercut features.
- The proposed system's effectiveness is evaluated through case studies using example die-cast parts.
- The results obtained from the system are verified to ensure accuracy and practical applicability.
- Data Collection Method:
- The primary input data consists of B-rep (Boundary Representation) files of die-cast parts.
- These B-rep models represent the geometric information of the die-casting parts, including complex undercut features.
- Example die-cast parts are used as case studies to test and validate the proposed system.
- Analysis Method:
- The core analysis method is based on a rule-based algorithm that utilizes the concepts of visibility and accessibility.
- Visibility: Local visibility is considered, where the normal at a point on a surface indicates the locally visible direction. The visibility map (V-map) is used, which is a hemisphere.
- Accessibility: Accessibility of a Non-Convex Surface (NCS) is determined by checking obstruction from other surfaces within the same Non-Convex Region (NCR).
- Geometric and topological data of the part are analyzed to identify edges, surfaces, and their relationships.
- Dot product (DP) of the parting direction and surface normal is used to classify surfaces into up, down, and neutral surfaces.
- Research Subjects and Scope:
- The research focuses on die-casting parts with complex undercut features that can be represented by B-rep models.
- The scope is limited to complex undercut features having planar surfaces, as stated in the assumptions: "The complex undercut features have planar surfaces only."
- The system is designed for mouldable die-casting parts, assuming "The die-casting part is mouldable."
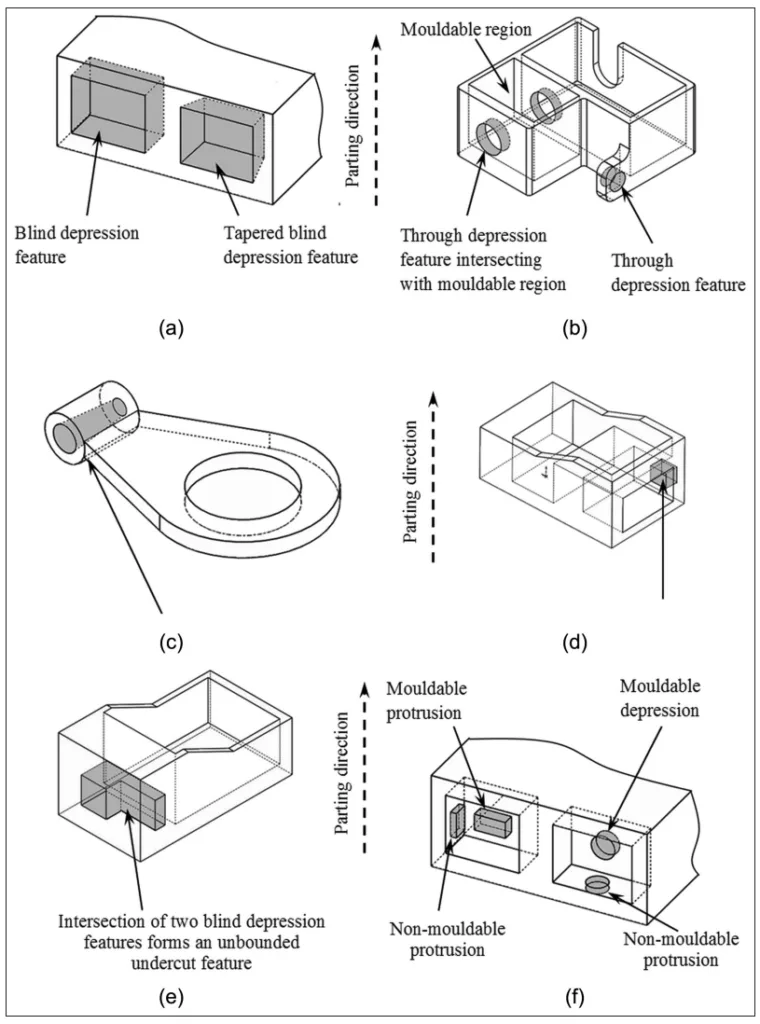
5. Main Research Results:
- Key Research Results:
- The research successfully developed an automated system capable of:
- Automated identification of complex undercut features.
- Classification of these features into different types (e.g., blind depression, through depression, unbounded undercut feature, etc.).
- Division of complex undercut features into simple undercut features.
- Determination of the release direction for each simple undercut feature.
- The system was implemented and tested on example die-cast parts, demonstrating its functionality and effectiveness.
- The results were verified, indicating the system's accuracy and practical applicability in a die-casting design context.
- The research successfully developed an automated system capable of:
- Statistical/Qualitative Analysis Results:
- While the paper does not present statistical analysis in the traditional sense, it provides qualitative results based on case study implementations.
- The system's performance is evaluated by comparing the time taken for undercut feature analysis manually versus using the automated system.
- "A die-casting die design expert spends on an average 30-40 min to identify, classify and separate the complex undercut features into simple ones along with determination of release direction. However, with the help of the developed system, it takes only 1-2 min for the same activities." This demonstrates a significant reduction in time using the automated system.
- Data Interpretation:
- The system effectively automates the complex and time-consuming task of undercut feature analysis in die-casting part design.
- By automatically identifying, classifying, and dividing complex undercut features, the system provides valuable information for subsequent side-core design.
- The determination of release directions for simple undercut features further facilitates the automated design of side-cores and contributes to bridging the design-manufacturing integration gap.
- Figure Name List:
- Figure 1. Pictorial representation of the die-casting die terminology
- Figure 2. Classification of surfaces of a die-cast part.
- Figure 3. A schematic of a non-convex region
- Figure 4. Mouldability of the partially accessible surfaces.
- Figure 5. Information flow diagram for identification of undercut features.
- Figure 6. Classification tree of die-casting undercut features.
- Figure 7. Instances of undercut features
- Figure 8. Division of unbounded undercut feature
- Figure 9. Division of complex intersecting undercut feature
- Figure 10. Division of undercut feature and intersecting mouldable region
- Figure 11. Information flow diagram for determination of release direction of a simple undercut feature.
- Figure 12. Determination of release direction.
- Figure 13. Results for example part No. 1
- Figure 14. Results for example part No. 2
6. Conclusion and Discussion:
- Summary of Main Results:
- The research successfully developed and implemented a system for the automated recognition of complex undercut features in die-cast parts, specifically for side-core design.
- The system automates the process of identifying, classifying, and dividing complex undercut features into simpler components.
- It also determines the release direction for these simple features, which is crucial for side-core design.
- The system's effectiveness was demonstrated and verified through case studies on example die-cast parts.
- Academic Significance of the Research:
- This research addresses significant gaps identified in previous studies concerning the recognition and processing of complex undercut features.
- It introduces a novel methodology for identifying, classifying, and dividing complex undercut features, contributing to the body of knowledge in feature recognition and die design automation.
- The proposed system provides a valuable framework for further research in automated die design and manufacturing integration.
- Practical Implications:
- The developed system has significant practical implications for the die-casting industry.
- It facilitates the automation of the die design process, leading to reduced lead times and design costs.
- The system generates essential information for downstream activities, including core and cavity design and side-core design.
- By automating undercut feature analysis, the system contributes to realizing design-manufacturing integration in die-casting.
- The significant reduction in analysis time (from 30-40 minutes manually to 1-2 minutes using the system) highlights its practical efficiency.
- Limitations of the Research:
- The current system is limited to die-cast parts and complex undercut features with planar surfaces. "The proposed system can identify die-cast parts and complex undercut features with planar surfaces only."
- The system's applicability is demonstrated on specific geometric shapes of undercut features, although the algorithm is noted to be generic and adaptable.
7. Future Follow-up Research:
- Directions for Follow-up Research:
- Future work should focus on extending the system's capabilities to handle die-cast parts with non-planar surfaces. "The future work may involve parts having non-planar surfaces."
- Integrating the undercut feature processing system with automated side-core design would be a valuable next step. "With the identification of complex undercut feature and their division into simple undercut features, the work presented in this article can be extended to automated design of side-cores."
- Areas Requiring Further Exploration:
- Further exploration is needed to adapt the algorithm for a wider range of geometric shapes and feature complexities, potentially requiring slight modifications. "For some of the other features, a slight modification in the algorithm will serve the purpose."
- Investigating the integration of this system with other die design and manufacturing processes to achieve a more comprehensive automated die-casting design workflow.
8. References:
- Kalpakjian S and Schmid SR. Manufacturing engineering and technology. 4th ed. New Delhi: Pearson Education, 2011.
- Singh R and Madan J. Systematic approach for automated determination of parting line for die-cast parts. Robot Cim: Int Manuf 2013; 29: 346-366.
- Kumar V, Madan J and Gupta P. A system for design of multicavity die casting dies from part product model. Int J Adv Manuf Tech 2013; 67: 2083-2107.
- Gan GH, Woo TC and Tang K. Spherical maps: their construction, properties and approximation. J Mech Des: T ASME 1994; 116: 357-363.
- Elber G and Cohen E. Arbitrarily precise computation of Gauss maps and visibility sets for freeform surface. In: Proceedings of the third ACM symposium on solid modeling and applications (SMA ‘95), Salt Lake City, UT, 17–19 May 1995, pp.271–279. New York: ACM.
- Fuh JYH, Wu SH and Lee KS. Development of a semi-automated die casting die design system. Proc IMechE, Part B: J Engineering Manufacture 2002; 216: 1575-1588.
- Dhaliwal S, Gupta SK, Huang J, et al. Algorithms for computing global accessibility cones. J Comput Inf Sci Eng 2003; 3(3): 200-209.
- Surti A and Reddy NV. Non-discretized approach to visibility analysis for automatic mold feature recognition using step part model. J Adv Manuf Syst 2012; 12(1): 1-16.
- Liu M and Ramani K. Computing an exact spherical visibility map for meshed polyhedral. In: Proceedings of the 2007 ACM symposium on solid and physical modelling, Beijing, China, 4–6 June 2007, pp.367–372. New York: ACM.
- Chen YH. Determination of parting direction based on minimum bonding box and fuzzy logic. Int J Mach Tool Manu 1997; 37(9): 1189-1199.
- Hui KC and Tan ST. Mould design with sweep operations a heuristic search approach. Comput Aided Design 1992; 24(2): 81-92.
- Wong T, Tan ST and Sze WS. Parting line formation by slicing a 3D CAD model. Eng Comput 1998; 14: 330-343.
- Fu MW, Fuh JYH and Nee AYC. Generation of optimal parting direction based on undercut features in injection moulded parts. IIE Trans 1999; 31: 947-955.
- Lu HY and Lee WB. Detection of interference elements and release directions in die-cast and injection-moulded components. Proc IMechE, Part B: J Engineering Manufacture 2000; 214(6): 431-441.
- Yin Z, Ding H and Xiong Y. Virtual prototyping of mould design: geometric mouldability analysis for near net shape manufactured parts by feature recognition and geometric reasoning. Comput Aided Design 2001; 33: 137-157.
- Ye XG, Fuh JYH and Lee KS. A hybrid method for recognition of undercut features from moulded parts. Comput Aided Design 2001; 33: 1023-1034.
- Ye XG, Fuh JYH and Lee KS. Automatic undercut feature recognition for side core design of injection molds. J Mech Design 2004; 126(3): 519-526.
- Khardekar R, Burton G and McMains S. Finding feasible mold parting directions using graphics hardware. Comput Aided Design 2006; 38: 327-341.
- Banerjee AG and Gupta SK. Geometrical algorithms for automated design of side actions in injection moulding of complex parts. Comput Aided Design 2007; 39: 882-897.
- Kumar N, Ranjan R and Tiwari MK. Recognition of undercut features and parting surface of moulded parts using polyhedron face adjacency graph. Int J Adv Manuf Tech 2007; 34(1-2): 47-55.
- Madan J, Rao PVM and Kundra TK. Die-casting feature recognition for automated parting direction and parting line determination. J Comput Inf Sci Eng 2007; 7(3): 236-248.
- Fu MW. The application of surface demoldability and moldability to side-core designing die and mold CAD. Comput Aided Design 2008; 40: 567-575.
- Madan J, Singh A and Kumar S. Recognition of intersecting features and identification of separable regions for design-manufacturing integration. In: Proceedings of the international conference on digital factory (ICDF), Trichy, India, 11-13 August 2008, pp.60-67.
- Huang TS. Algorithms for recognizing undercut feature. J Technol 2008; 23(1): 61-69.
- Bidkar RA and McAdams DA. Methods for automated manufacturability analysis of injection-molded and die-cast parts. Res Eng Des 2010; 21: 1-24.
- Bassi R, Reddy NV and Bedi S. Automatic recognition of intersecting features for side-core design in two piece permanent molds. Int J Adv Manuf Tech 2010; 50: 421-439.
- Ran JQ and Fu MW. Design of internal pins in injection mold CAD via the automatic recognition of undercut features. Comput Aided Design 2010; 42(7): 582-597.
- Sunil VB and Pande SS. Automatic recognition of features from freeform surface CAD models. Comput Aided Design 2008; 40: 502-517.
- Tan ST, Yuen MF, Sze WS, et al. Parting lines and parting surfaces of injection moulded parts. Proc IMechE, Part B: J Engineering Manufacture 1990; 204: 211-221.
9. Copyright:
- This material is Ranjit Singh, Jatinder Madan and Rajesh Kumar's paper: Based on Automated identification of complex undercut features for side-core design for die-casting parts.
- Paper Source: DOI: 10.1177/0954405413514744
This material was summarized based on the above paper, and unauthorized use for commercial purposes is prohibited.
Copyright © 2025 CASTMAN. All rights reserved.