This article introduces the paper "An Overview of Heat Sink Technology" presented at the IJME
1. Overview:
- Title: AN OVERVIEW OF HEAT SINK TECHNOLOGY
- Author: Ehsan F. Abbas
- Publication Year: 2024
- Publishing Journal/Academic Society: Int. J. of Applied Mechanics and Engineering (IJME)
- Keywords: heat sink design, longitudinal fin, performance of a heat sink, improving fin performance, fin optimization.

2. Research Background:
- Social/Academic Context of the Research Topic:
The research addresses the critical role of heat sinks in managing thermal energy in various applications, including electric and electronic equipment, chemical industries, refrigeration, air conditioning systems, and power plants. The paper highlights the historical evolution of heat sink technology, starting from early cast iron designs to contemporary solutions, driven by increasing demands for efficient thermal management in industrial and domestic settings. The context is set against a backdrop of evolving industrial revolutions and increasing standards of living, which have driven the need for more sophisticated and efficient heat sink designs. - Limitations of Existing Research:
The paper does not explicitly detail limitations of existing research in the introduction, but it implicitly suggests a need for a comprehensive overview of heat sink technology, particularly focusing on longitudinal rectangular fins. The historical review suggests that while heat sink technology has evolved, there is a continuous need for optimization and understanding of design principles. The paper points out that despite advancements, challenges remain in achieving optimal heat sink performance, particularly concerning fin design and configuration. - Necessity of the Research:
The research is necessary to provide a structured overview of heat sink technology, focusing on the design and optimization of longitudinal rectangular fins. The paper emphasizes the importance of efficient heat dissipation for the reliability and performance of various devices. By reviewing the historical development, manufacturing methods, cooling methods, design parameters, and optimization techniques, the paper aims to consolidate knowledge and provide a valuable resource for engineers and researchers in the field. The focus on longitudinal rectangular fins is justified by their common usage and the availability of extensive research data for optimization.
3. Research Purpose and Research Questions:
- Research Purpose:
The primary goal of this research is to provide an overview of heat sink technology, with a specific focus on the optimization of longitudinal rectangular fins in arrays subjected to forced and natural convection. The paper aims to look back at the development of heat sink technology and consolidate the fundamental principles and optimization techniques for longitudinal rectangular fins. - Key Research Questions:
While not explicitly stated as questions, the research implicitly addresses the following:- How has heat sink technology evolved over time?
- What are the different manufacturing methods for heat sinks and their implications?
- What are the various cooling methods employed in heat sink technology?
- What are the key design parameters and assumptions in heat sink design?
- What are the theoretical approaches to designing and optimizing heat sinks, particularly longitudinal rectangular fins?
- How can fin efficiency and effectiveness be evaluated and optimized?
- What are the optimal dimensions for different fin profiles under various conditions?
- How can the thermal resistance of multi-finned arrays be analyzed?
- What are the findings from experimental and numerical studies on heat sink performance?
- Research Hypotheses:
This paper is an overview and does not test specific hypotheses. However, it is based on the implicit assumption that a comprehensive review of existing literature can provide valuable insights and guidelines for the design and optimization of heat sinks, particularly longitudinal rectangular fins. The paper synthesizes existing knowledge to present a structured understanding of the field.
4. Research Methodology
- Research Design:
Literature Review. This paper is a review article that synthesizes existing research and knowledge on heat sink technology, focusing on longitudinal rectangular fins. - Data Collection Method:
The data collection method involves a comprehensive review of published literature, including research articles, books, and technical reports, related to heat sink technology. The references listed at the end of the paper indicate the sources of information. - Analysis Method:
The analysis method is qualitative and involves summarizing, synthesizing, and organizing information from the reviewed literature. The paper presents a structured overview of different aspects of heat sink technology, including historical development, manufacturing methods, cooling methods, design parameters, theoretical models, optimization techniques, and experimental/numerical findings. Mathematical equations and figures from cited works are used to illustrate key concepts and results. - Research Subjects and Scope:
The research subject is heat sink technology, with a specific scope on longitudinal rectangular fins. The review covers various aspects of heat sink design, optimization, and performance evaluation, drawing upon a wide range of studies in the field. The scope is primarily focused on theoretical and experimental research related to heat transfer in heat sinks, particularly those with longitudinal rectangular fin configurations.
5. Main Research Results:
- Key Research Results:
- Historical Development: The paper traces the evolution of heat sinks from multi-column cast iron designs in the early 20th century to modern materials and manufacturing techniques, highlighting key milestones and shifts in design priorities driven by social and industrial changes.
- Manufacturing Methods: The review outlines various manufacturing methods for heat sinks, including stamping, extrusion, bonded fins, casting, and welded fins, detailing their respective advantages, limitations, and applications. Figure 1 illustrates heat sink samples according to manufacturing methods.
- Cooling Methods: The paper categorizes cooling methods into passive, active, simi-active, liquid cooled plate, and phase-change recirculating systems, explaining the principles of operation and typical applications for each method. Figure 2 shows illustrations of heat sink samples according to cooling methods.
- Design Parameters and Assumptions: Key design parameters for heat sinks are identified, including flow speed, pressure drop, cross-sectional area, heat transfer requirements, operating temperature, size limitations, gravitational orientation, appearance, and cost. Assumptions made in heat sink design for simplified analysis are also listed, such as negligible radiation heat transfer and uniform base temperature.
- Theoretical Approach to Design: The paper presents a theoretical framework for designing heat sinks, focusing on longitudinal rectangular fins. It provides the temperature distribution equation (Figure 3), heat transfer equations for different fin tip conditions (Table 1 and 2), and equations for fin efficiency and effectiveness.
- Fin Optimization: The review discusses fin optimization techniques, including corrected profile length, fin effectiveness, and methods for optimizing fin thickness and length under constant heat flux and constant volume conditions. Equations for optimal fin dimensions are presented.
- Thermal Resistance of Multi-Finned Arrays: The paper analyzes the thermal resistance of multi-finned arrays, providing formulas for calculating heat transfer rates and overall surface efficiency (Figure 4).
- Longitudinal Fins with Non-uniform Profile Area: The review extends to longitudinal fins with non-uniform profiles (triangular, concave, convex), presenting optimal dimension equations and heat transfer equations for these fin shapes (Figure 5 and Table 3).
- Array of Longitudinal Fins: The paper discusses the optimization of spacing between parallel vertical plates in fin arrays for natural laminar convection, presenting equations for heat transfer rate and optimal parameters for array design (Figure 6 and 7).
- Experimental and Numerical Studies: The review summarizes findings from numerous experimental and numerical studies investigating various aspects of heat sink performance, including the effects of fin geometry, spacing, orientation, and flow conditions. Figure 8 illustrates conventional and hybrid heat sink models, and Figure 9 shows studied heat sink models.
- Statistical/Qualitative Analysis Results:
The paper primarily synthesizes qualitative findings from various studies. Quantitative results are presented in the form of equations and formulas for heat transfer rate, fin efficiency, optimal dimensions, and thermal resistance. The review highlights trends and general conclusions from experimental and numerical studies, such as the impact of fin spacing on heat transfer coefficient, the effectiveness of interrupted fins, and the performance of different fin shapes. - Data Interpretation:
The data presented and synthesized in the paper indicate that the design and optimization of heat sinks, particularly longitudinal rectangular fins, is a complex process involving numerous parameters and considerations. The optimal design depends on various factors, including the application, cooling method, material properties, and environmental conditions. The review emphasizes the importance of theoretical modeling, numerical simulations, and experimental validation in achieving efficient heat sink designs. - Figure Name List:
- Fig. 1. Illustrations of heat sink samples according to the manufacturing method.
- Fig. 2. Illustrations of heat sink samples according to the cooling method.
- Fig. 3. Longitudinal fin with a rectangular cross-section [8].
- Fig. 4. Sketching the heat loss from a combination of fins with a plane wall.
- Fig. 5. Sketches of longitudinal fins with non-uniform profile area: (a) triangular, (b) concave, and (c) convex [9].
- Fig. 6. A sketch of an array of longitudinal fins and its geometric definitions [9], [18].
- Fig. 7. Optimal β values for any array of longitudinal fins [9, 18].
- Fig. 8. Sketch for two heat sink models: (a) conventional, (b) hybrid.
- Fig. 9. Sketch of studied heat sink models, (a) straight fin, (b) topology.
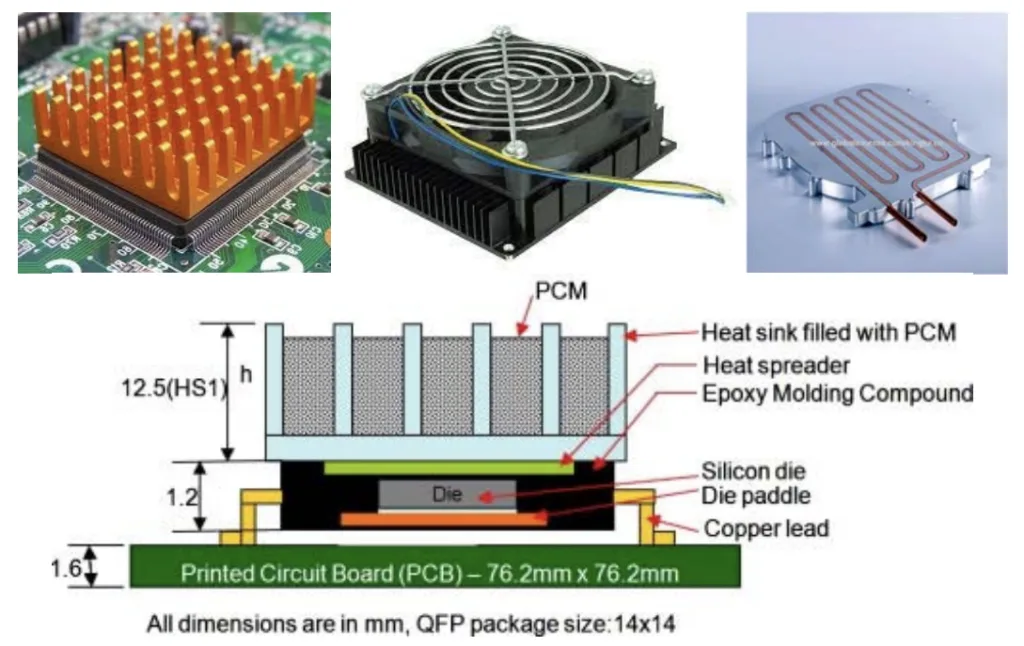

6. Conclusion and Discussion:
- Summary of Main Results:
This overview paper concludes that the design optimization of heat sinks with rectangular longitudinal fins has been extensively studied over the past centuries. Various experimental, numerical, and theoretical methods have been employed to determine optimal configurations. Key findings indicate that fin height and spacing significantly affect heat transfer rates, with optimal fin spacing being crucial for maximizing heat transfer. Duralumin fins outperform stainless steel in similar geometries. Interrupted and inclined fins, as well as specific fin geometries like rectangular notched fins, can enhance heat transfer performance. - Academic Significance of the Research:
This review paper provides a valuable academic contribution by consolidating a wide range of research findings on heat sink technology, specifically focusing on longitudinal rectangular fins. It offers a structured overview of historical developments, design principles, optimization techniques, and experimental results, serving as a comprehensive resource for researchers and students in thermal engineering. The paper highlights the evolution of heat sink design and the key factors influencing performance. - Practical Implications:
The practical implications of this research are significant for engineers and designers involved in thermal management across various industries. The paper offers guidelines and equations for designing and optimizing heat sinks for different applications and cooling conditions. The summarized findings can aid in selecting appropriate manufacturing methods, cooling strategies, fin geometries, and materials to achieve efficient and cost-effective heat dissipation in electronic devices, power systems, and other thermal applications. The emphasis on optimal fin spacing and the performance benefits of interrupted and inclined fins provides actionable insights for practical design improvements. - Limitations of the Research:
As a review paper, the limitations are inherent in the scope of the reviewed literature. While the paper provides a broad overview, it may not cover every single study or aspect of heat sink technology in exhaustive detail. The focus is primarily on longitudinal rectangular fins, and other fin configurations or advanced heat sink technologies might be less extensively covered. The review is also limited by the selection of studies included, potentially reflecting a bias towards commonly researched areas.
7. Future Follow-up Research:
- Directions for Follow-up Research:
The paper implicitly suggests several directions for future research:- Further investigation into advanced heat sink geometries and materials to enhance heat transfer performance beyond conventional designs.
- Exploration of novel manufacturing techniques to enable the production of complex and optimized fin structures.
- More research on hybrid cooling methods that combine passive and active cooling strategies for improved efficiency and adaptability.
- Deeper studies into the long-term reliability and performance of optimized heat sinks under real-world operating conditions.
- Investigation of heat sink designs for emerging applications with specific thermal management challenges, such as high-power density electronics and sustainable energy systems.
- Further research to refine and validate existing theoretical models and numerical simulations with more comprehensive experimental data, particularly for complex fin geometries and flow conditions.
- Areas Requiring Further Exploration:
- Optimization of heat sinks for specific applications and environmental conditions, considering factors like space constraints, weight limitations, and cost-effectiveness.
- Development of more accurate and computationally efficient numerical models for predicting heat sink performance under complex flow regimes.
- Investigation of the impact of manufacturing tolerances and surface finish on the actual thermal performance of heat sinks.
- Exploration of innovative heat sink designs that integrate with system-level thermal management strategies for holistic thermal solutions.
8. References:
- [1] Kordyban T. (1998): Hot Air Rises and Heat Sinks: Everything You Know About Cooling Electronics Is Wrong.- ASME Press, p.236, https://doi.org/10.1115/1.800741.
- [2] Lee S. (1995): Optimum design and selection of heat sinks.– IEEE Transactions on Components, Packaging, and Manufacturing Technology: Part A, vol.18, No.4, pp. 812-817, doi: 10.1109/95.477468.
- [3] Londhe K. and Kaushik V.R. (2017): Heat sink design for optimal performance of compact electronic appliances - a review.- Journal for Advanced Research in Applied Sciences, vol.4, No.5, pp.13-21.
- [4] Kandasamy R., Wang X.Q. and Mujumdar A.S. (2008): Transient cooling of electronics using phase change material (PCM)-based heat sinks.- Appl. Therm. Eng., vol.28, No.8-9, pp.1047-1057, doi: 10.1016/J.APPLTHERMALENG.2007.06.010.
- [5] Kays W.M. and London A.L. (2011): Compact Heat Exchangers.– Third Edition,
- [6] https://celsiainc.com/technology/heat-sink-design/.
- [7] Lee H.S. (2010): Thermal Design: Heat Sinks, Thermoelectrics, Heat Pipes, Compact Heat Exchangers, and Solar Cells.- John Wiley & Sons, Inc., doi: 10.1002/9780470949979.
- [8] Holman J.P. (2010): Heat Transfer.– 10th ed., p.758, McGraw-Hill Education
- [9] Kraus A.D., Aziz A. and Welty J. (2001): Extended Surface Heat Transfer.– A Wiley-Interscience Publication J.WILEY & SONS, Inc., doi: 10.1002/9780470172582.
- [10] Cengel Y., Turner R. and Smith R. (2001): Fundamentals of thermal-fluid sciences.- Appl. Mech. Rev., vol.54, No.6, doi: 10.1115/1.1421126.
- [11] Brown A. (1965): Optimum dimensions of uniform annular fins.– Int. J. Heat Mass Transf., vol.8, No.4, pp.655-662, doi: 10.1016/0017-9310(65)90051-7.
- [12] Cobble M.H. (1971): Optimum fin shape.- J. Franklin Inst., vol.291, No.4, pp.283-292, doi: 10.1016/0016-0032(71)90184-0.
- [13] Snider A.D. and Kraus A.D. (1987): The quest for the optimum longitudinal fin profile.– Heat Transfer Engineering, vol.8, No.2, doi: 10.1080/01457638708962790.
- [14] Duffin R. (1959): A variational problem relating to cooling fins.- Indiana University Mathematics Journal, vol.8, No.1, doi: 10.1512/iumj.1959.8.58003.
- [15] Maday C.J. (1974): The minimum weight one-dimensional straight cooling fin.– J. Eng. Ind., vol.96, No.1, pp.161-165, https://doi.org/10.1115/1.3438291 .
- [16] Ernst E.R.G., Eckert R.G. and Drake R.M. (1987): Analysis of heat and mass transfer.- Hemisphere Pub. Corp., accessed: Nov. 21, 2023, [Online], available: https://inis.iaea.org/search/search.aspx?orig_q=RN:19100674
- [17] Razelos P. and Imre K. (1983): Minimum mass convective fins with variable heat transfer coefficients.- J. Franklin Inst., vol.315, No.4, doi: 10.1016/0016-0032(83)90078-9.
- [18] Aziz A. (1992): Optimum dimensions of extended surfaces operating in a convective environment.– Appl. Mech. Rev., vol.45, No.5, doi: 10.1115/1.3119754.
- [19] Bergman T.L., Lavine A.S., Incropera F.P. and DeWitt D.P. (2015): Fundamentals of Heat and Mass Transfer.- John Wiley & Sons, USA.
- [20] Chung B.T.F. and Iyer J.R. (1993): Optimum design of longitudinal rectangular fins and cylindrical spines with variable heat transfer coefficient.- Heat Transfer Engineering, vol.14, No.1, pp.31-41, doi: 10.1080/01457639308939792.
- [21] Schmidt E. (1926): Die Wärmeübertragung Durch Rippen.
- [22] Chung B.T.F. and Nguyen L.D. (1986): Optimization of design parameters for radiating longitudinal fins of various geometries.- in AIAA Paper, doi: 10.2514/6.1986-150.
- [23] Levy E.K. (1971): Optimum plate spacings for laminar natural convection heat transfer from parallel vertical isothermal flat plates.– J. Heat Transfer, vol.93, No.4, pp.463-465, doi: 10.1115/1.3449847.
- [24] Elenbaas W. (1942): Heat dissipation of parallel plates by free convection.- Physica, vol.9, No.1, pp.1-28, doi: 10.1016/S0031-8914(42)90053-3.
- [25] Bodoia J.R. and Osterle J.F. (1962): The development of free convection between heated vertical plates.- J. Heat Transfer, vol.84, No.1, pp.40-43, doi: 10.1115/1.3684288.
- [26] Bar-Cohen A. and Jelinek M. (1985): Optimum arrays of longitudinal, rectangular fins in corrective heat transfer.- Heat Transfer Engineering, vol.6, No.3, pp.68-78, doi: 10.1080/01457638508939633.
- [27] Starner K.E. and McManus H.N. (1963): An experimental investigation of free-convection heat transfer from rectangular-fin arrays.- J. Heat Transfer, vol.85, No.3, pp.273-277, doi: 10.1115/1.3686097.
- [28] Jones C.D. and Smith L.F. (1970): Optimum arrangement of rectangular fins on horizontal surfaces for free-convection heat transfer.- J. Heat Transfer, vol.92, No.1, doi: 10.1115/1.3449648.
- [29] Barrett A.V. and Obinelo I.F. (1997): Characterization of longitudinal fin heat sink thermal performance and flow bypass effects through CFD methods.- in Annual IEEE Semiconductor Thermal Measurement and Management Symposium, doi: 10.1109/stherm.1997.566793.
- [30] De Lieto Vollaro A., Grignaffini S. and Gugliermetti F. (1999): Optimum design of vertical rectangular fin arrays.- International Journal of Thermal Sciences, vol.38, No.6, pp. 525-529, doi: 10.1016/S1290-0729(99)80025-8.
- [31] Baskaya S., Sivrioglu M. and Ozek M. (2000): Parametric study of natural convection heat transfer from horizontal rectangular fin arrays.– International Journal of Thermal Sciences, vol.39, No.8, pp.797-805, doi: 10.1016/S1290-0729(00)00271-4.
- [32] Bar-Cohen A., Iyengar M. and Kraus A.D. (2003): Design of optimum plate-fin natural convective heat sinks.- Journal of Electronic Packaging, Transactions of the ASME, vol.125, No.2, pp.208-216, SPEC., doi: 10.1115/1.1568361.
- [33] Yazicioğlu B. and Yüncü H. (2007): Optimum fin spacing of rectangular fins on a vertical base in free convection heat transfer.- Heat and Mass Transfer/Waerme- und Stoffuebertragung, vol.44, No.1, pp.11-21, doi: 10.1007/s00231-006-0207-6.
- [34] Mittelman G., Dayan A., Dado-Turjeman K. and Ullmann A. (2007): Laminar free convection underneath a downward facing inclined hot fin array.- Int. J. Heat Mass Transf., vol.50, No.13-14, pp.2582-2589, doi: 10.1016/j.ijheatmasstransfer.2006.11.033.
- [35] Shaeri M.R. and Yaghoubi M. (2009): Thermal enhancement from heat sinks by using perforated fins.– Energy Convers. Manag., vol.50, No.5, pp.1264-1270, doi: 10.1016/j.enconman.2009.01.021.
- [36] Kim D.K. (2012): Thermal optimization of plate-fin heat sinks with fins of variable thickness under natural convection.- Int. J. Heat Mass Transf., vol.55, No.4, pp.752-761, doi: 10.1016/j.ijheatmasstransfer.2011.10.034.
- [37] Ahmadi M., Mostafavi G. and Bahrami M. (2014): Natural convection from rectangular interrupted fins.- International Journal of Thermal Sciences, vol.82, No.1, pp.62-71, doi: 10.1016/j.ijthermalsci.2014.03.016.
- [38] Pouryoussefi S. and Zhang Y. (2015): Experimental study of air-cooled parallel plate fin heat sinks with and without circular pin fins between the plate fins.- Journal of Applied Fluid Mechanics, vol.8, No.3, pp.515-520, doi: 10.18869/acadpub.jafm.67.222.22930.
- [39] Karamanis G. and Hodes M. (2016): Longitudinal-fin heat sink optimization capturing conjugate effects under fully developed conditions.– J. Therm. Sci. Eng. Appl., vol.8, No.4, p.7, doi: 10.1115/1.4034339.
- [40] Shadlaghani A., Tavakoli M.R., Farzaneh M. and Salimpour M.R. (2016): Optimization of triangular fins with/without longitudinal perforate for thermal performance enhancement.– Journal of Mechanical Science and Technology, vol.30, No.4, pp.1903-1910, doi: 10.1007/s12206-016-0349-5.
- [41] Hong S.H. and Chung B.J. (2016): Variations of the optimal fin spacing according to Prandtl number in natural convection.- International Journal of Thermal Sciences, vol.101, pp.1-8, doi: 10.1016/J.IJTHERMALSCI.2015.10.026.
- [42] Dogan M. and Dogan D. (2017): Experimental investigation of natural convection heat transfer from fin arrays for different tip-to-base fin spacing ratios.- Isi Bilimi Ve Teknigi Dergisi/ Journal of Thermal Science and Technology, vol.37, No.1, pp.147-157.
- [43] Jaya Krishna D. (2018): Operational time and melt fraction based optimization of a phase change material longitudinal fin heat sink.– J. Therm. Sci. Eng. Appl., vol.10, No.6, p.4, doi: 10.1115/1.4040988.
- [44] Hou D., Xin X. and Qian J. (2020): Analysis of natural convection heat transfer from vertical and inclined plate fin heat sinks.- in Lecture Notes in Electrical Engineering, Springer Verlag, pp.479-487, doi: 10.1007/978-981-32-9441-7_49.
- [45] Jasim H.H. (2020): Heat transfer enhancement from heat sources using optimal design of combined fins heat-sinks.- Propulsion and Power Research, vol.9, No.4, pp.372-382, doi: 10.1016/j.jppr.2020.11.002.
- [46] Xie L., Zhang Y., Ge M. and Zhao Y. (2022): Topology optimization of heat sink based on variable density method.– Energy Reports, vol.8, pp.718-726, doi: 10.1016/J.EGYR.2021.11.214.
- [47] Obaid A.J. and Hameed V.M. (2023): An experimental and numerical comparison study on a heat sink thermal performance with new fin configuration under mixed convective conditions.– S. Afr. J. Chem. Eng., vol.44, pp.81-88, doi: 10.1016/J.SAJCE.2023.01.009.
- [48] Kaya M. and Kaya Ş. (2023): Optimum fin spacing of rectangular fins on aluminum heat sinks plates.- Proceedings of the Romanian Academy Series A - Mathematics Physics Technical Sciences Information Science, vol.24, No.2, pp.157-157.
9. Copyright:
- This material is "Ehsan F. Abbas"'s paper: Based on "AN OVERVIEW OF HEAT SINK TECHNOLOGY".
- Paper Source: https://doi.org/10.59441/ijame/192127
This material was summarized based on the above paper, and unauthorized use for commercial purposes is prohibited.
Copyright © 2025 CASTMAN. All rights reserved.