This article introduces the paper "A Study on Development of a Die Design System for Diecasting" presented in The International Journal of Advanced Manufacturing Technology.
1. Overview:
- Title: A Study on Development of a Die Design System for Diecasting
- Authors: J. C. Choi, T. H. Kwon, J. H. Park, J. H. Kim and C. H. Kim
- Publication Year: 2002
- Publishing Journal/Academic Society: The International Journal of Advanced Manufacturing Technology
- Keywords: Diecasting; Die design system; Gate; Rule base; Runner
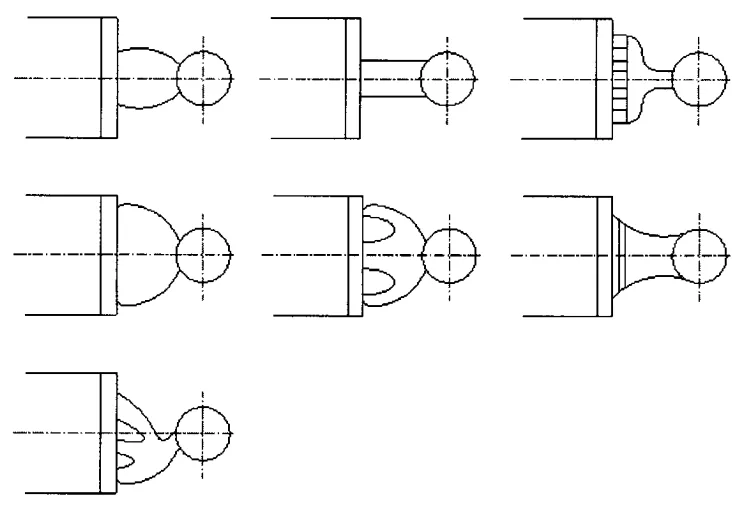
2. Research Background:
Die casting stands as a pivotal forming method in modern manufacturing, particularly for high-volume production of components requiring short lead times and superior surface finishes. Its efficacy in processing complex geometries and thin-wall sections, coupled with high productivity and dimensional accuracy, has fueled its rapid adoption across industries like automotive, aerospace, and electronics. However, conventional die design for diecasting has been encumbered by a reliance on trial-and-error methodologies. This approach, while leveraging the experience of seasoned die designers, inherently introduces economic inefficiencies and protracted development cycles.
Existing Computer-Aided Design (CAD) and Computer-Aided Manufacturing (CAM) systems, while prevalent in injection molding and other manufacturing domains, have seen limited application in diecasting die design. Furthermore, current shop floor practices often lack robust analytical capabilities for predicting molten metal flow and heat transfer within the die. This deficiency necessitates iterative experimental diecasting runs and subsequent corrections, especially concerning the runner-gate system, leading to increased processing times and costs. The intricate nature of diecasting die design, encompassing component system factors such as runner, gate, biscuit, overflow, and air vents, demands considerable expertise. Design flaws discovered late in the process can result in significant time and resource wastage during die modification.
3. Research Purpose and Research Questions:
This research endeavors to mitigate the limitations of traditional diecasting die design by developing a Computer-Aided Design (CAD) system. The primary research purpose is to automate the die design process, with a specific focus on the runner-gate system. The study addresses the following key research questions:
- How can a CAD system be developed to automate the die design process for diecasting, particularly the runner-gate system?
- How can specific rules and equations be integrated into a CAD system to minimize the reliance on trial-and-error in diecasting die design?
- How can 3D geometry handling and process planning technologies be integrated to achieve comprehensive automation of die design?
The underlying research hypothesis is that a rule-based CAD system, incorporating established diecasting principles and algorithms, can significantly enhance the efficiency and accuracy of die design, thereby reducing development time and costs associated with trial-and-error iterations.
4. Research Methodology:
This research adopts a system development approach, focusing on the creation of a CAD system for diecasting die design. The research design centers on algorithmic development and system implementation within the AutoCAD environment using AutoLISP language. A flowchart-based methodology is presented to illustrate the automation process for die design, particularly for the runner-gate system.
Data collection in this context involves the compilation of existing diecasting knowledge, empirical rules, and established equations related to runner and gate design. This knowledge base forms the foundation for the rule-based system. The analysis method involves the development and implementation of algorithms for cast design, die layout design, and die generation. The system's functionality is demonstrated through its application to example products, namely a cap-shaped product (motor pulley) and a motor pulley product, showcasing its capability to automate the design process. The research scope is limited to die design for aluminum alloy diecasting, with a primary emphasis on the runner-gate system.
5. Main Research Results:
The core outcome of this research is the development of a functional CAD system for diecasting die design. Key results include:
- Automated Die Design Algorithm: An algorithm for automating die design, particularly for the runner-gate system, was successfully developed. This algorithm facilitates efficient and effective die design, reducing the need for extensive manual adjustments.
- CAD System Implementation: The proposed die design algorithm and associated databases were implemented within AutoCAD using AutoLISP. This resulted in a practical CAD system capable of assisting engineers in diecasting die design.
- Flowchart-Based System Architecture: The research presented detailed flowcharts outlining the steps for cast design (Fig. 2), die layout design (Fig. 3), and die generation (Fig. 4). These flowcharts provide a structured approach to automating the die design process.
- Database Integration: The system incorporates essential databases, including:
- Material and Shrinkage Database: Containing physical and mechanical properties of aluminum diecasting alloys (Table 1) and shrinkage data.
- Gate and Runner Database: Providing data for gate area calculation based on filling speed and minimum cast thickness (Table 2), and runner design parameters.
- Overflow, Airvent and Cavity Block Database: Including design guidelines for overflows, air vents, and cavity block configurations.
- System Application Examples: The developed system was successfully applied to design dies for a cap-shaped product (Fig. 9) and a motor pulley product (Fig. 10), demonstrating its practical applicability.
Figure Name List:
- Fig. 1. Flowchart of the die design system for diecasting.
- Fig. 2. Flowchart for cast design.
- Fig. 3. Flowchart for die layout design.
- Fig. 4. Flowchart for die generation.
- Fig. 5. Schematic drawing of general section shape for runner.
- Fig. 6. Schematic drawing of runner type.
- Fig. 7. Schematic drawing of general shape for overflow.
- Fig. 8. Schematic drawing of general shape for cavity block.
- Fig. 9. Application of the developed system for a cap-shaped product. (a), (b), (c)
- Fig. 10. Application of the developed system for a motor pulley product. (a), (b), (c)
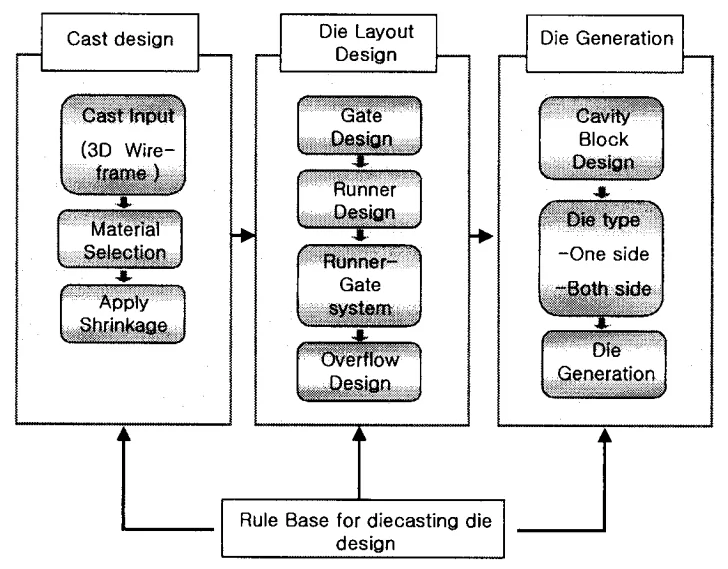
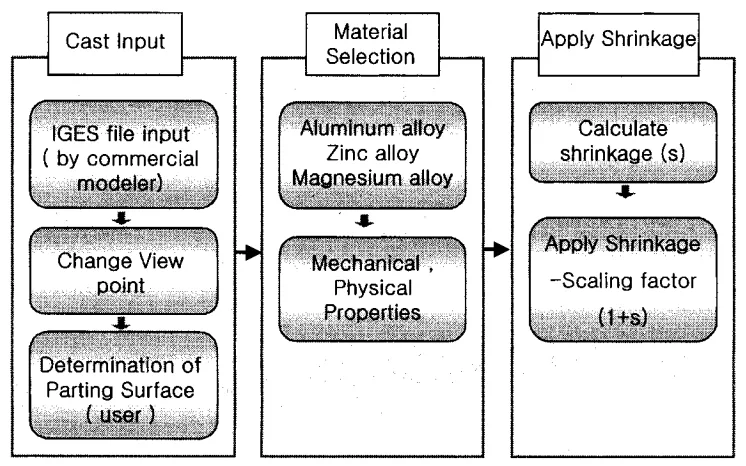
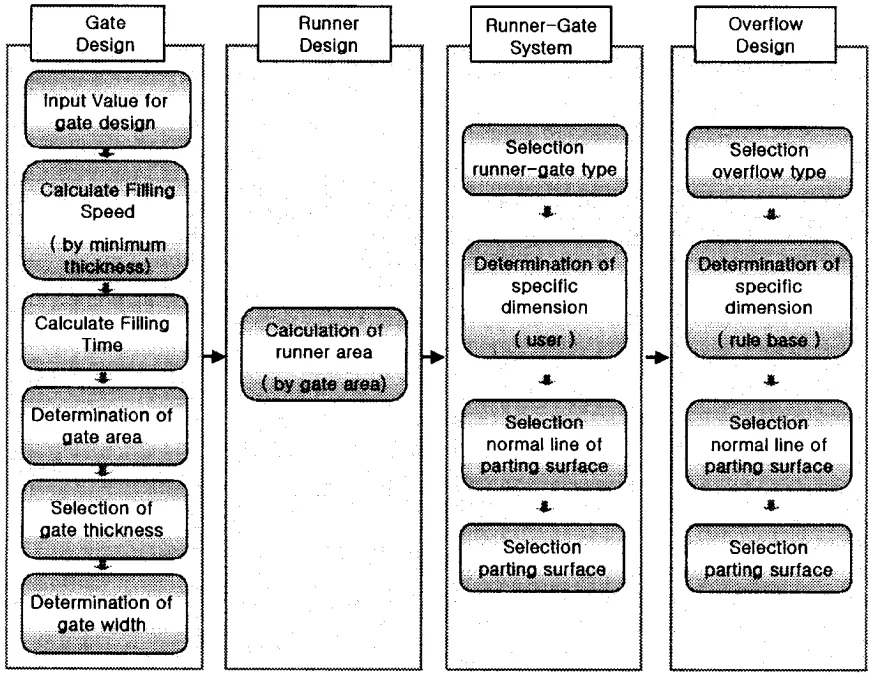
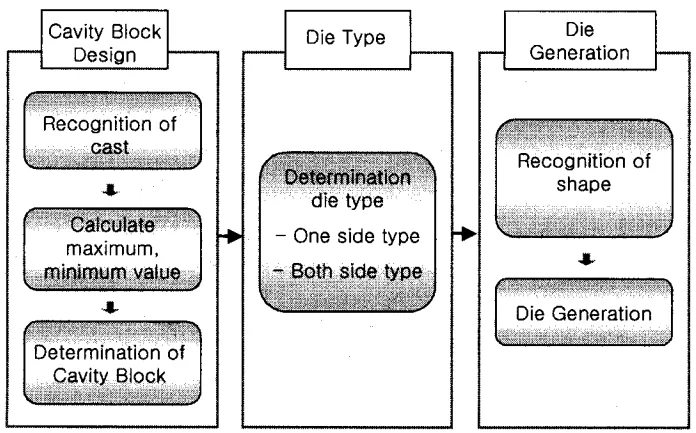
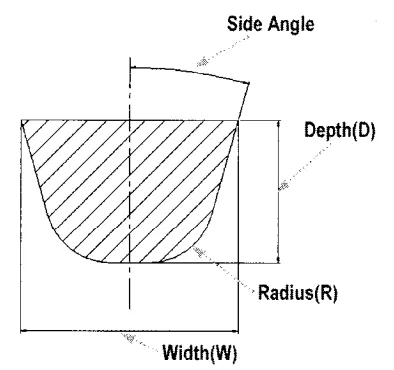
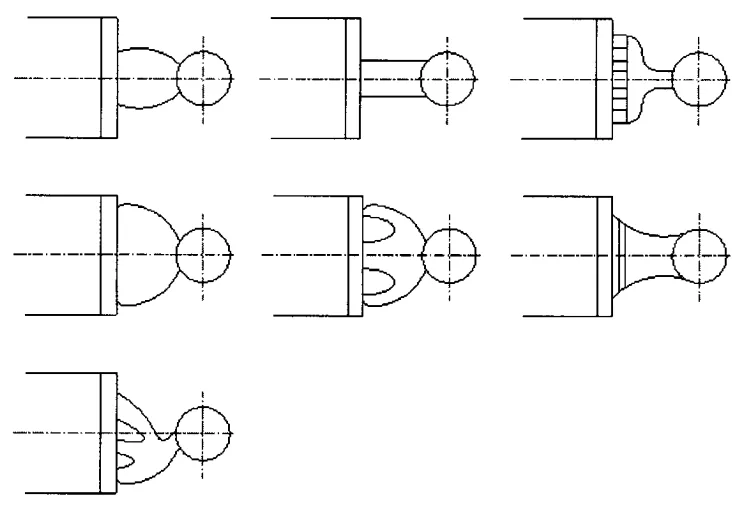
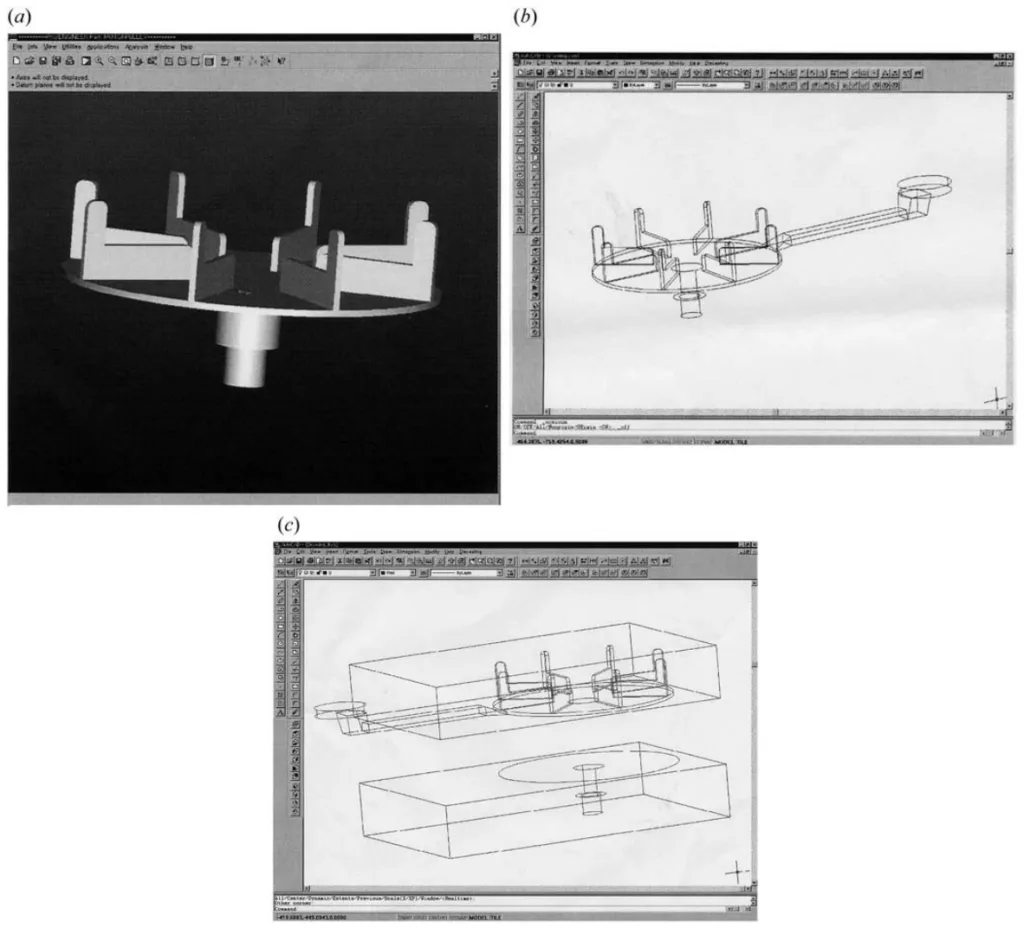
6. Conclusion and Discussion:
This study successfully developed an automated CAD system tailored for diecasting die design, with a primary emphasis on automating the runner-gate system. The research demonstrates the feasibility of using a rule-based approach, integrated within a CAD environment, to streamline and enhance the die design process.
Academic Significance: The research contributes an algorithm for creating an accessible and effective die design system. It formalizes and quantifies the practical knowledge and experiential aspects of die design into a structured, procedural framework. This is significant as it moves die design from a largely experience-based art towards a more systematic and engineering-driven process.
Practical Implications: The developed system holds significant practical implications for the diecasting industry. By automating key aspects of die design, particularly the runner-gate system, it empowers engineers, even those with limited diecasting expertise, to perform die design tasks more efficiently. This can lead to reduced design cycle times, lower development costs, and improved die performance through optimized runner and gate configurations. The system's ability to minimize trial-and-error reduces material waste and production delays.
Limitations of the Research: The authors acknowledge that the current system has limitations. It does not yet address the design of dies for products with undercuts. Furthermore, the determination of the parting surface still relies on user input, and the system's applicability is primarily demonstrated for single-impression dies.
7. Future Follow-up Research:
Future research directions are suggested to enhance the capabilities and scope of the developed CAD system:
- Undercut Handling: Expanding the system to incorporate design rules and algorithms for handling undercuts in diecast parts.
- Automated Parting Surface Determination: Developing an algorithm to automate the determination of the optimal parting surface, eliminating the current reliance on user selection.
- Multiple Impression Dies: Extending the system's applicability to the design of multiple impression dies, further increasing its practical utility in high-volume production scenarios.
- Integration of Advanced Simulation: Integrating die casting process simulation tools to further optimize runner and gate designs based on predicted metal flow and heat transfer characteristics.
8. References:
- H. H. Doehler, Diecasting, McGraw-Hill, 1951.
- C. C. Tai and J. C. Lin, "A runner-optimization design study of a die-casting die", Journal of Materials Processing Technology, 84, pp. 1-12, 1998.
- C. C. Tai and J. C. Lin, "The optimal position for the injection gate of a die-casting die", Journal of Materials Processing Technology, 86, pp. 87-100, 1998.
- S. Sulaiman and T. C. Keen, "Flow analysis along and gating system of a casting process", Journal of Materials Processing Technology, 63, pp. 690-695, 1997.
- W. Zhang, S. Xiong and B. Liu, "Study on a CAD/CAM system of diecasting", Journal of Materials Processing Technology, 63, pp. 707-711, 1997.
- J. P. Kruth, "Steps toward an integrated CAD/CAM system for mold design and manufacture: anisotropic shrinkage, component library and link to NC machining and EDM", Annals CIRP, 35, 1986.
- Y.-M. Chen and C.-L. Wei, "Computer-aided feature-based design for net shape manufacturing", Computer Integrated Manufacturing System, 10(2), pp. 147-164, 1997.
- T. Kishinami et al., "Development of interactive mold cavity CAD/CAM system", Annals CIRP, 32(1), pp. 345-349, 1983.
- P. A. Walsham et al., "Further developments of a geometric modeling system for the computer aided manufacture of dies and molds", CIRP Annals, 32(1), pp. 339-342, 1983.
- J. Worbye, "New information points the way to longer die-casting die life", Diecasting Engineer, pp. 42-54, 1998.
9. Copyright:
This material is "[J. C. Choi, T. H. Kwon, J. H. Park, J. H. Kim and C. H. Kim]"'s paper: Based on "A Study on Development of a Die Design System for Diecasting".
This material was summarized based on the above paper, and unauthorized use for commercial purposes is prohibited.
Copyright © 2025 CASTMAN. All rights reserved.