This article introduces the paper "A feasibility study of the partial squeeze and vacuum die casting process".
1. Overview:
- Title: A feasibility study of the partial squeeze and vacuum die casting process
- Authors: E.S. Kim, K.H. Lee, Y.H. Moon
- Year: 2000
- Journal/Conference: Journal of Materials Processing Technology
- Keywords: Partial squeeze and vacuum die casting, Hypereutectic Al-Si alloy, Squeeze pressure, Plunger stroke, Injection pressure, Injection speed
2. Research Background:
The manufacturing of aluminum alloys is increasingly important due to demands for lightweight materials, improved functionality, higher quality, and environmentally friendly production techniques [1–3]. Die casting offers speed and precision but suffers from porosity due to high velocity injection, trapping air. Existing methods such as high-pressure die casting, ACCURAD [4], pore-free die casting [5], gas-free vacuum die casting [6], and squeeze casting [7] each have limitations in balancing productivity and quality. This research aimed to address these limitations.
3. Research Objectives and Questions:
- Objective: To investigate the feasibility of a partial squeeze and vacuum die casting process for producing defect-free castings with superior mechanical properties.
- Key Research Question: How does the combination of squeezing and vacuum effects influence the defect level and mechanical properties of die-cast products?
- Hypothesis: Combining a vacuum effect before injection and a squeezing effect after injection will result in defect-free castings and improved mechanical properties due to a uniform distribution of fine acicular eutectic and proeutectic silicon.
4. Research Methodology:
- Research Design: An industrial trial die casting process was implemented to produce reaction shaft supports from a hypereutectic Al-15%Si alloy.
- Data Collection: A plunger injection system was integrated with a chill-vent type vacuum system to combine squeezing and vacuum effects. Conventional die casting (CD), squeeze die casting (SD), vacuum die casting (VD), and the proposed partial squeeze and vacuum die casting (SVD) processes were compared.
- Analytical Methods: Cross-sections of cast parts were analyzed for defects. Specific gravity was measured to assess densification. Tensile testing determined mechanical properties. Microstructural analysis was performed.
- Subjects and Scope: The research focused on the die casting of reaction shaft supports using a hypereutectic Al-15%Si alloy.
5. Main Research Findings:
- Key Findings: The SVD process resulted in significantly fewer defects and superior mechanical properties compared to CD, SD, and VD. Squeeze pressure and time lag significantly affected densification, with an optimal range identified.
- Quantitative/Qualitative Results: CD and SD showed extensive porosity (Fig. 4a, b). VD exhibited shrinkage defects (Fig. 4c). SVD produced nearly defect-free castings (Fig. 4d). Optimal densification (2.736 g/cm³) occurred at 2000 kg/cm² squeeze pressure and a 1.0-second time lag (Fig. 5). SVD yielded the highest tensile strength (24.92 kg/cm²) and elongation (0.26%) (Table 3). Microstructural analysis revealed a uniform distribution of fine acicular eutectic and proeutectic silicon in SVD (Fig. 8).
- Data Interpretation: Vacuum removal of air and squeeze pressure compensation for shrinkage minimized defects. The uniform microstructure contributed to superior mechanical properties.
- Figure List:
- Fig. 1: Schematic drawing of the partial squeeze and vacuum die casting machinery.
- Fig. 2: Schematic drawing of the injection curve.
- Fig. 3: Photographs of the die cast trial product of a reaction shaft support.
- Fig. 4: Photographs showing sectional views of the reaction shaft support: (a) CD; (b) SD; (c) VD; and (d) SVD.
- Fig. 5: The effect of the squeeze pressure and time lag on the specific gravity of cast products.
- Fig. 6: The relationship between plunger stroke and squeeze pressure.
- Fig. 7: Local density variation at a squeeze pressure 2000 kg/cm ² and a time lag of: (a) 0.5 s; (b) 1.0 s; (c) 1.5 s; and (d) 2.0 s.
- Fig. 8: Typical microstructure at various squeeze pressures (time lag=1.0 s): (a) 1500 kg/cm ²; (b) 2000 kg/cm ²; (c) 2500 kg/cm ²; and (d) 3000 kg/cm ².
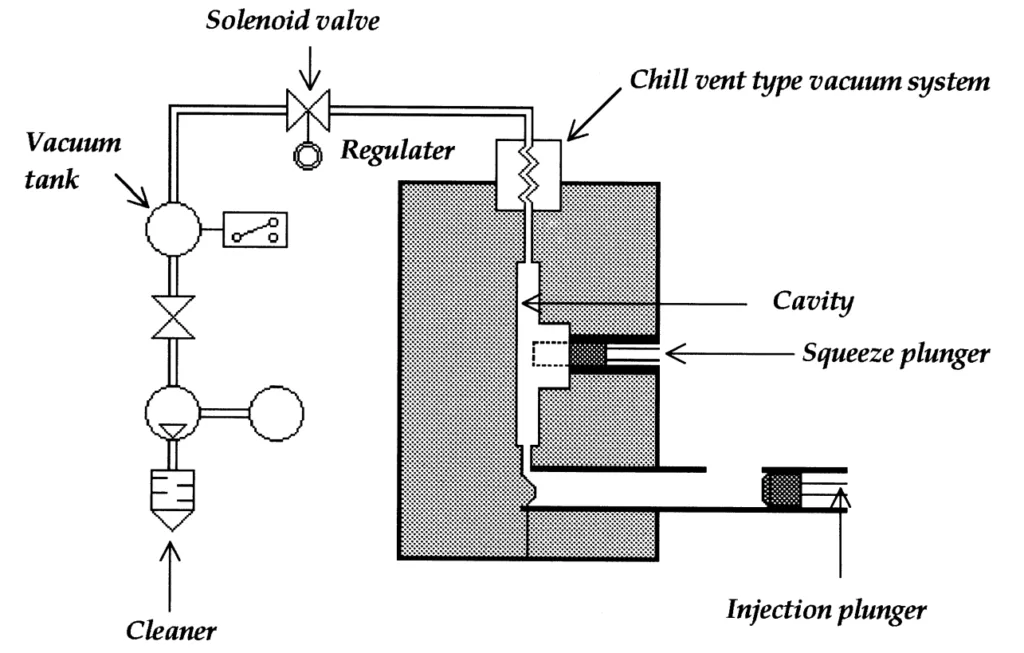
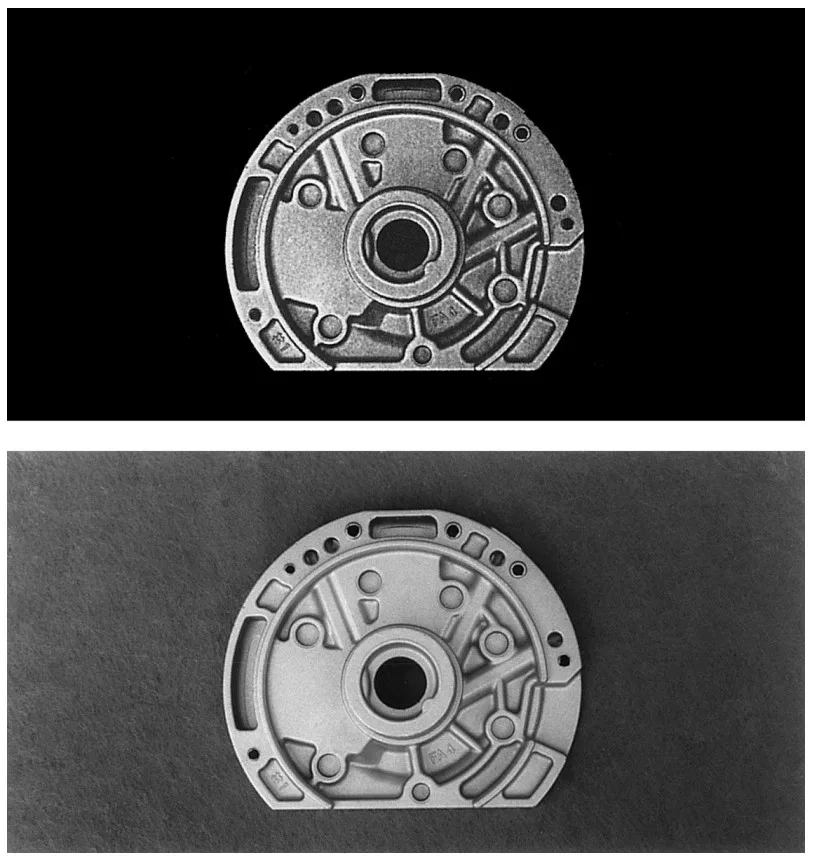
6. Conclusions and Discussion:
The hybrid squeeze-vacuum die casting technique produced defect-free castings with excellent mechanical properties. The combination of vacuum and squeezing effectively prevented porosity and shrinkage. Optimal process parameters (squeeze pressure and time lag) were identified. The study provides practical implications for high-quality die casting. Limitations include the focus on a specific alloy and part geometry.
7. Future Research:
Further research should explore different alloys and part geometries. Optimization of squeeze pressure and time lag requires additional investigation. A more comprehensive analysis of the interplay between process parameters is also needed.
8. References:
The research built upon existing knowledge of die casting and related research [1–9].
[1] K. Fukizawa, H. Shiina, J. Soc. Auto. Eng. Jpn. 46 (5) (1992) 66.
[2] D.O. Kennedy, Mod. Cast. 2 (1992) 34.
[3] Metals Handbook, Vol. 15, 9th Edition, ASM, New York, 1988, p. 204.
[4] L. Maclaren, Die Cast. 31 (1967) 7.
[5] T. Kan, T. Uehara, Die Casting of Aluminum Alloy, Japan Light Metals Press Co., Japan, 1988, p. 438.
[6] Technical History of Die Casting, Japan Die Casting Association, Light Metal Communication Co., Japan, 1995, p. 11.
[7] R.F. Lynch, R.P. Olley, P.C.J. Gallagher, AFS Transactions Paper No. 75±122, 1975, p. 569.
[8] I.J. Polmear, Light Alloys Ð Metallurgy of the Light Metals, Arnold, UK, 1981.
[9] F. King, Aluminum and its Alloys, Wiley, New York, 1987.
Copyright:
This summary is based on the research paper: "A feasibility study of the partial squeeze and vacuum die casting process" by E.S. Kim, K.H. Lee, and Y.H. Moon.
Commercial use is prohibited. (Note: The DOI was not provided.)
Copyright © 2025 CASTMAN. All rights reserved.