This article introduces the paper "Topology and Free Size Optimization with Manufacturing Constraints for Lightweight Die Cast Automotive Backrest Frame," presented at the ASME International Mechanical Engineering Congress and Exposition (IMECE2009).
1. Overview:
- Title: TOPOLOGY AND FREE SIZE OPTIMIZATION WITH MANUFACTURING CONSTRAINTS FOR LIGHT WEIGHT DIE CAST AUTOMOTIVE BACKREST FRAME
- Authors: Sreeram Polavarapu, Lonny L. Thompson and Mica Grujicic
- Year of Publication: 2009
- Published in: ASME International Mechanical Engineering Congress and Exposition (IMECE2009)
- Keywords: Finite element analysis, topology optimization, free-size optimization, die casting, automotive backrest frame, lightweight design, manufacturing constraints
2. Research Background:
- Social/Academic Context of Research Topic:
- The automotive industry faces increasing demands for vehicle weight reduction to enhance fuel efficiency and vehicle performance.
- Automotive structural components, traditionally made from stamped steel assemblies, contribute significantly to overall vehicle weight.
- Replacing stamped steel components with high-pressure die cast (HPDC) aluminum or magnesium alloy parts offers a promising avenue for weight reduction.
- Limitations of Existing Research:
- Conventional stamped steel designs possess limited potential for geometric and topology optimization due to restrictions in bend radii and welding of varying sheet thicknesses.
- Designing geometrically and topologically optimized lightweight seats using traditional stamped sheet metal construction is challenging.
- Necessity of Research:
- High-pressure die casting (HPDC) with aluminum or magnesium alloys presents a compelling alternative to stamped steel for seat frame design.
- Die casting enables variable thickness distribution and intricate geometric features like supporting ribs, offering significant potential for lightweight design optimization.
- Optimizing material distribution and rib placement in die-cast seat frames can justify die costs, especially for high-volume, functionally demanding automotive seat designs across multiple vehicle platforms.
3. Research Objectives and Research Questions:
- Research Objective:
- To investigate the characteristics of a die-cast automotive front seat backrest frame.
- To develop a methodology for predicting optimized material and support rib distribution.
- To achieve a lightweight seat design that satisfies both strength and deflection requirements within a design space considering multiple load cases.
- Core Research Question:
- How can topology and free-size optimization, incorporating manufacturing constraints specific to die casting, be effectively utilized to design a lightweight automotive backrest frame that meets stringent performance and safety standards under various loading conditions?
- Research Hypothesis:
- The integration of finite element analysis with topology and free-size optimization, while considering die casting manufacturing constraints, can successfully generate an optimized material distribution and stiffening rib structure for a lightweight die-cast automotive seat backrest frame.
- This optimized design will achieve a significant weight reduction compared to commercially available counterparts without compromising structural integrity and performance under multiple load scenarios.
4. Research Methodology:
- Research Design:
- A multi-stage optimization process was employed, combining topology optimization and free-size optimization techniques.
- The process starts with topology optimization on a 3D solid model to determine optimal rib placement, followed by free-size optimization on a 3D surface model to optimize material thickness distribution.
- Data Collection Method:
- A commercially available die-cast magnesium alloy automotive seat backrest frame served as the reference design.
- The geometric model of the backrest frame was reverse-engineered from physical hardware and modeled using CATIA V5 CAD software.
- Material properties of as-cast AM50 Magnesium alloy were utilized, considering its ductile behavior at the relevant section thicknesses.
- Load requirements were defined based on ECE R17 European government regulations for seat strength and deflection, supplemented by additional load cases simulating crash events (offset and side loads).
- Analysis Method:
- Finite Element Analysis (FEA): Linear FEA was performed using OptiStruct (Altair) for topology and free-size optimization. Nonlinear FEA using ABAQUS/Standard 6.7 was used for validation, incorporating both geometric and material nonlinearities.
- Topology Optimization: Employed the Simple Isotropic Material with Penalization (SIMP) method in OptiStruct to determine optimal material distribution and guide rib placement in the 3D solid model, considering die draw direction and symmetry manufacturing constraints.
- Free-Size Optimization: Utilized element-level free-size optimization in OptiStruct on a 3D surface model to optimize shell element thicknesses, aiming to minimize mass while satisfying stress and displacement constraints.
- Validation: Nonlinear finite element analysis was conducted on the interpreted optimized design to verify strength and deflection requirements under all load cases, ensuring functional performance.
- Research Subject and Scope:
- The study focused on the design optimization of a thin-walled die-cast automotive front seat backrest frame made of AM50 Magnesium alloy.
- The optimization scope was limited to weight minimization under multiple load cases (backrest strength test, static headrest test, offset loads, and side loads) and manufacturing constraints (die draw direction, symmetry).
- The design space was based on an existing commercially available backrest frame, serving as a reference for comparison and improvement.
5. Key Research Results:
- Core Research Results:
- A multi-stage optimization procedure combining topology and free-size optimization was successfully developed and applied to design a lightweight die-cast automotive seat backrest frame.
- The optimized design achieved a significant weight reduction of 13% compared to the reference commercially available die-cast backrest frame component.
- The procedure generated an optimal material distribution and stiffening rib configuration suitable for die-cast manufacturing.
- Statistical/Qualitative Analysis Results:
- Weight Reduction: An overall weight reduction of 13% was achieved, reducing the mass from 1.76 kg (interpreted optimized seat model) to 1.56 kg (original seat model comparison based on paper text, discrepancy with abstract 1.8kg vs 1.25kg needs clarification from full paper if available, assuming 13% reduction from 1.76kg to 1.56kg based on interpreted design mass in paper). Abstract mentions 13% reduction over 1.8kg reference frame.
- Displacement under Headrest Test: The maximum displacement for the optimized frame design under the headrest test was 17.3 mm, which is 18% below the maximum displacement of 21 mm observed in the nonlinear finite element analysis of the original reference frame design.
- Stress under Headrest Test: The maximum von Mises stress in the optimized backrest frame under the final 890 N load in the headrest test reached 196.9 MPa. This value is above the Yield Strength (124 MPa) but below the Ultimate Tensile Strength (228 MPa) of AM50 Magnesium alloy, indicating localized plastic yielding without fracture.
- Data Interpretation:
- Topology optimization effectively guided the placement of stiffening ribs in the vertical U-shaped sections of the backrest frame, concentrating material in structurally critical areas.
- Free-size optimization successfully optimized the thickness distribution of the shell model, strategically allocating material to areas experiencing higher stress and load, while reducing thickness in less critical regions.
- Nonlinear finite element analysis validated that the interpreted optimized design meets both strength and deflection requirements under the ECE R17 mandated load cases and additional crash load scenarios.
- The optimized design maintains structural integrity while achieving significant weight reduction, demonstrating the effectiveness of the multi-stage optimization approach.
- Figure Name List:
- Figure 1: Reference automotive backrest frame constructed from high-pressure die-cast AM50 Magnesium Alloy (Total Mass = 1.8 kg)
- Figure 2: Geometric Surface CAD model and Nomenclature of the Reference Die Cast Backrest Frame
- Figure 3: Design Envelope for Multiple-Load Cases
- Figure 4: ECE-R17 Backrest Moment Test Loading modeled with pressure distribution across headrest support cross-member.
- Figure 5: ECE-R17 Headrest Test Loading Modeled with equivalent pressure force and couple at headrest support holes and cross-member.
- Figure 6: Offset Load applied as pressure on one-half of the headrest cross-member.
- Figure 7: Pressure load applied to develop side moment.
- Figure 8: Multi-Stage Engineering Optimization Process
- Figure 9: Multi-Stage Engineering Optimization Process for Die-Cast Backrest Frame
- Figure 10: Design Space for Topology Optimization
- Figure 11: Design space solid finite element mesh showing bolt locations.
- Figure 12: Element densities in solid frame subjected to topology optimization
- Figure 13: Details of finite element shell model used for free-size optimization.
- Figure 14: Element thickness distribution from free-size optimization and suggested rib placement from topology optimization.
- Figure 15: New design of backrest frame model with piecewise constant thickness taper and optimal supporting rib placement derived from the topological and free-size optimization proposal (Front View).
- Figure 16: Optimized Backrest frame model (Rear View).
- Figure 17: Von Mises stress distribution in final optimized seat from nonlinear finite element analysis subjected to ECE R17 Headrest Test Load Requirement.
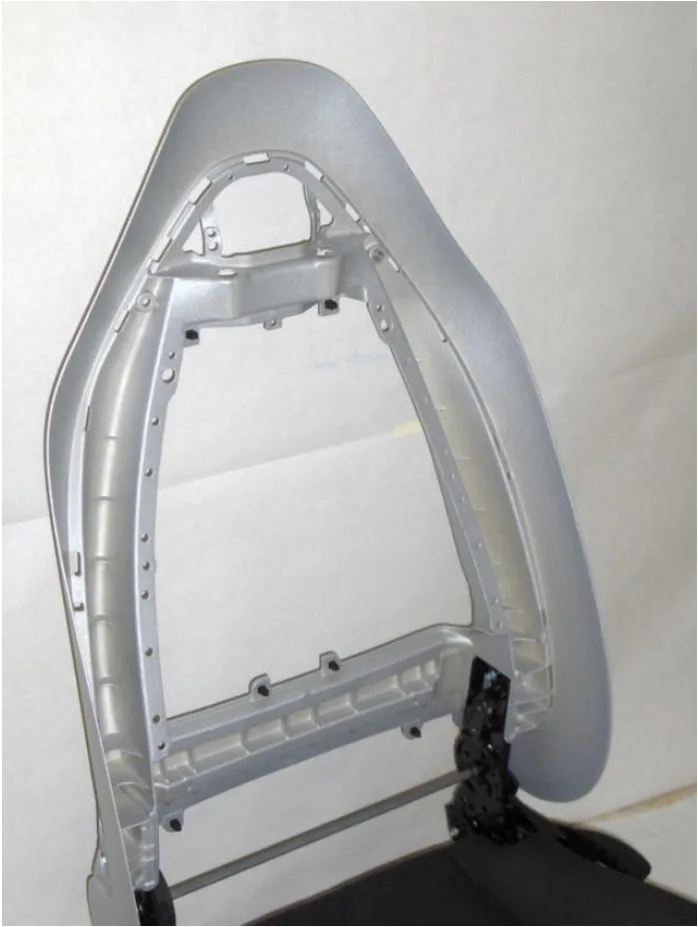
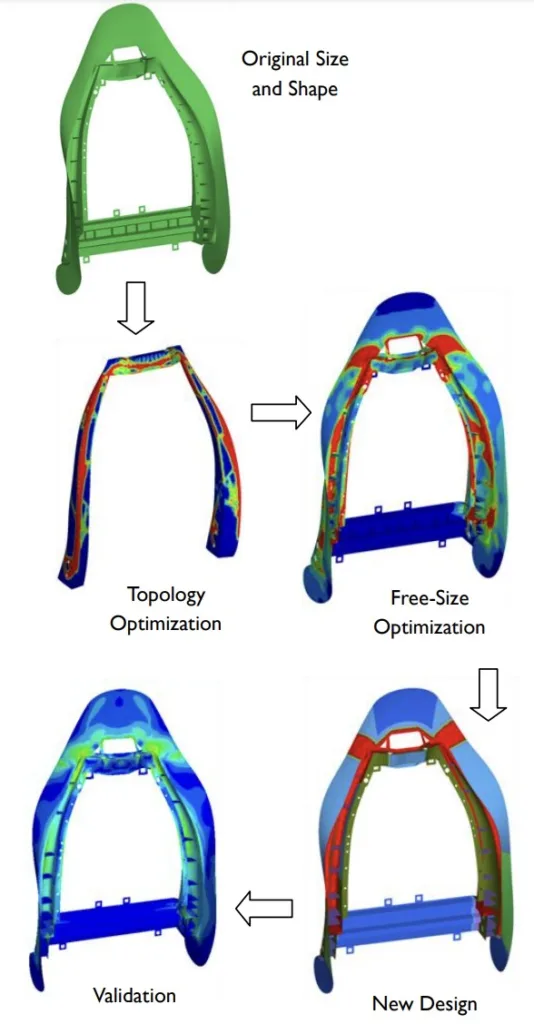
6. Conclusion and Discussion:
- Summary of Key Results:
- The research successfully demonstrated the application of a multi-stage optimization process, combining topology and free-size optimization with die casting manufacturing constraints, to design a lightweight automotive backrest frame.
- The optimized design achieved a 13% weight reduction compared to a commercially available reference frame while maintaining structural integrity and meeting stringent performance requirements under multiple load cases, including those defined by ECE R17 regulations and simulated crash scenarios.
- Academic Significance:
- This study provides a comprehensive example of applying advanced optimization techniques (topology and free-size optimization) to a real-world engineering problem in the automotive industry.
- It highlights the importance of integrating manufacturing constraints, specifically die draw direction and symmetry for die casting, into the optimization process to ensure design feasibility.
- The multi-stage optimization approach presented offers a valuable framework for designing lightweight structural components, particularly for thin-walled die-cast parts.
- Practical Implications:
- The developed methodology offers a practical and effective approach for automotive engineers to design lightweight die-cast components, contributing to vehicle weight reduction and improved fuel efficiency.
- The optimized backrest frame design serves as a tangible example of how topology and free-size optimization can lead to significant material savings and weight reduction in automotive seat structures.
- The findings suggest that combining these optimization techniques with careful consideration of manufacturing constraints can result in innovative and efficient die-cast designs for various automotive applications beyond seat frames.
- Limitations of Research:
- The interpretation of topology optimization results and translation into a manufacturable CAD model required manual intervention and engineering judgment, as fully automated interpretation tools considering all manufacturing constraints were not available.
- The optimization process primarily focused on structural performance and weight reduction, with limited consideration of detailed manufacturing cost analysis and die design complexities.
- The validation was performed through nonlinear finite element analysis. Experimental validation through physical prototyping and testing was not conducted in this study.
7. Future Follow-up Research:
- Future Research Directions:
- Further refine rib placement and shaping in the optimized design by incorporating geometric shape and dimension optimization techniques, potentially parameterizing rib spacing and scalloping geometry.
- Integrate manufacturing process simulation tools (e.g., ProCAST, MagmaSOFT) into the optimization loop to account for die filling, solidification, and potential defects in the die casting process, leading to more robust and manufacturable designs.
- Develop automated interpretation tools and algorithms that can directly translate topology optimization results into manufacturable CAD models, fully considering die casting specific manufacturing constraints and design rules.
- Areas for Further Exploration:
- Conduct a detailed die design and manufacturing cost analysis for the optimized backrest frame to assess the economic viability and practical manufacturability of the design.
- Perform experimental validation of the optimized design through prototyping and physical testing to confirm the FEA predicted structural performance and weight reduction benefits.
- Extend the multi-stage optimization methodology to other automotive die-cast components and explore its applicability to different materials and manufacturing processes.
8. References:
- [1] Andresen, B., (2005), Die Casting Engineering, Marcel Dekker, New York, NY.
- [2] ECE R17 UNECE Agreement Concerning the Adoption of Uniform Technical Prescriptions for Wheeled Vehicles, Uniform Provisions Concerning the Approval of Vehicles with Regard to the Seats, their Anchorages and Any Head Restraints.
- [3] Rozvany, G., (2008) "A critical review of established methods of structural topology optimization" Journal Structural and Multidisciplinary Optimization, Online Forum, Publisher Springer Berlin / Heidelberg, February 21, 2008.
- [4] Bendsoe, M. P. (1995). Optimization of Structural Topology, Shape, and Material. Berlin: Springer.
- [5] Eschenauer, H. A., & Olhoff, N. (2001). Topology optimization of continuum structures – a review. Applied Mechanics Reviews, 54 (4), 331-390.
- [6] Olhoff, N., Bensoe, M.P., Rasmussen, J., (1991) “On CAD-integrated structural topology and design optimization", Comput Methods Appl Mech Eng, 89, 259-279.
- [7] Bremicker, M., Chirehdast, M., Kikuchi, N., Papalambros, P.Y., (1991) "Integrated topology and shape optimization in structural design", Mech Struct Mach, 19, 551-587.
- [8] C-Y Lin, L-S Chao, (2000) "Automated image interpretation for integrated topology and shape optimization", Struct Multidiscip Optim, 20, 125-137.
- [9] A.V. Kumar, D.C. Gossard, (1996) "Synthesis of optimal shape and topology of structures", J. Mech Des, 118, 68-74.
- [10] S.K. Youn, S-H. Park, (1997) “A study on the shape extraction process in the structural topology optimization using homogenized material", Comput Struct, 62 (3), 527-538.
- [11] Hsu, Y.L., Hsu, M.S., Chen, C.T., 2001, "Interpreting Results from Topology Optimization using Density Contours", Comput. Struct. 79 (10), 1049-1058.
- [12] Hsu, Y.L., Hsu, M.S., 2005, “Interpreting three-dimensional structural topology optimization results", Comput. Struct. 83, 327-337.
- [13] Harzheim, L., Graf, G., 2005, "A Review of Optimization of Cast Parts using Topology optimization: I-Topology optimization without manufacturing constraints", Struct Multidisc Optim 30: 491-497
- [14] Harzheim, L., Graf, G., 2006, "A Review of Optimization of Cast Parts using Topology optimization: II-Topology optimization with manufacturing constraints", Struct Multidisc Optim 31: 388-399
- [15] Schramm, U., Thomas, H., Zhou, M., 2002, "Manufacturing Considerations and Structural Optimization of Automotive Components, SAE International, SAE Paper 2002-01-1242.
- [16] Zhou, M., Fleury, R., Shyy, Y.K., Thomas, H., Brennan, J.M., 2002, "Progress in Topology Optimization with Manufacturing Constraints”, 9th AIAA/ISSMO Symposium on Multidisciplinary Analysis and Optimization, Sept. 2002, Atlanta, Georgia. Paper AIAA 2002-5614.
- [17] Nelson, E.A., 2003, "Draw Direction Constraints in Topology Optimization – A Practical Example", SAE International, Proceedings 2003 SAE World Congress, Detroit, Michigan, SAE Paper 2003-01-1306.
- [18] S. Chen and D. Tortorelli, "Three-dimensional shape optimization with variational geometry", Struct. Optim., 13(1997)81-94.
- [19] Vanderplaats, G.N., "Numerical Optimization Techniques for Engineering Design: With Application, 3rd Edition, Vanderplaats Research & Development, 1999.
- [20] Papalambros, P.Y., and Wilde, D.J., Principles of Optimal Design: Modeling and Computation, Cambridge University Press, 2nd ed., 2000.
- [21] K. Saitou, K. Izui, S. Nishiwaki, P. Papalambros, (2005) “A Survey of Structural Optimization in Mechanical Product Development", Journal of Computing and Information Science in Engineering, Vol. 5, 214-226.
- [22] Grujicic, M. et.al. “Application of Topology, Size and Shape Optimization Methods in Polymer Metal Hybrid Structural Lightweight Engineering", Multidiscipline Modeling in Materials and Structures, Volume 4, Number 4, 2008, pp. 305-330(26)
- [23] Altair Engineering Inc., 2007, "OptiStruct 8.0, User's Guide".
- [24] Dassault Systèmes, CATIA V5. http://www.3ds.com/products/catia/
- [25] Zhizhong Sun, Ming Zhou, Henry Hu, and Naiyi Li, "Strain-Hardening and Fracture Behavior of Die Cast Magnesium Alloy AM50," Research Letters in Materials Science, 2007.
- [26] Hesser, D.S., "Integration of Finite Element Method to Enhance Modeling and Analysis for Reverse Engineering", M.S. Thesis, Department of Mechanical Engineering, Clemson University, 2006.
- [27] Altair Engineering Inc., 2007, "Hypermesh 8.0, User's Guide".
- [28] Petersson, J., & Sigmund, O. (1998). Slope constrained topology optimization. International Journal for Numerical Methods in Engineering, 41 (8), 1417-1434.
- [29] Sigmund, O. (1997). On the design of compliant mechanisms using topology optimization. Mechanics of Structures and Machines, 25 (4), 493-524.
- [30] Blendsoe, M.P. and Kikuchi, N., 1988, "Generating optimal topologies in structural design using a homogenization method", Comp. Meth. in Applied Mech. and Engin., Vol. 71, pp. 197-224.
- [31] Bendsoe MP (1989) Optimal shape design as a material distribution problem. Struct Optim 1:193-202
- [32] Suzuki, K. and Kikuchi, N., (1991), “A homogenization method for shape and topology optimization", Comp. Meth. in Applied Mech. and Engin., Vol. 93, pp. 291-318.
- [33] Diaz AR, Bendsoe MP (1992) Shape optimization of structures for multiple loading situations using a homogenization method. Struct Optim 4:17-22
- [34] Diaz AR, Lipton R (2000) Optimal material layout in 3D elastic structures subjected to multiple loads. Mech Struct March 28:219-236
- [35] Dassault Systèmes, SIMULIA: ABAQUS Analysis User's Manual, ABAQUS Documentation V6.6.
- [36] http://www.esi-group.com/products/casting/procast
- [37] http://www.magmasoft.de/ms/home_en/index.php
- [38] P. Krajnik and J. Kopac, "Modern machining of die and mold tools," Journal of Materials Processing Technology, 2004, 157-158, pp. 543-552.
9. Copyright:
This material is based on the paper by [Sreeram Polavarapu, Lonny L. Thompson and Mica Grujicic]
titled: [TOPOLOGY AND FREE SIZE OPTIMIZATION WITH MANUFACTURING CONSTRAINTS FOR LIGHT WEIGHT DIE CAST AUTOMOTIVE BACKREST FRAME].
Paper Source: [https://doi.org/10.1146/annurev-matsci-070218-010134]
This material is a summary based on the above paper and is for informational purposes only. Unauthorized commercial use is prohibited.
Copyright © 2025 CASTMAN. All rights reserved.