This article introduces the paper "Cooling of LED headlamp in automotive by heat pipes".
1. Overview:
- Title: Cooling of LED headlamp in automotive by heat pipes
- Authors: Randeep Singh, Masataka Mochizuki, Tadao Yamada, Tien Nguyen
- Year of Publication: 2020
- Journal/Conference of Publication: Applied Thermal Engineering
- Keywords: Passive cooling, Flexible heat pipe, Hinge heat pipe, Piezo fan, Lighting, Automotive thermal management
2. Research Background:
- Social/Academic Context of the Research Topic: Automotive headlamps are transitioning from halogen/xenon to LEDs. LEDs offer twice the luminous efficacy, 10-15 times longer lifespan, and improved styling compared to halogen lamps. Unlike halogen lamps, LEDs require temperature control to maintain monochromaticity, luminous intensity, and longevity.
- Limitations of Existing Research: Traditional aluminum die-cast heat sinks used for LED cooling solutions are thermally inefficient, structurally heavy, and space-intensive.
- Necessity of Research: Research is needed on heat pipe-based cooling systems for various LED headlamp designs and styles, capable of handling thermal performance up to 20W per module.
3. Research Objectives and Research Questions:
- Research Objective: To propose, design, and characterize heat pipe-based cooling systems for different designs and styles of LED headlamps and thermal capability of up to 20 W/per-module.
- Core Research Question: Can heat pipe-based cooling systems provide a more efficient and lighter alternative to die-cast heat sinks for LED headlamps?
- Research Hypothesis: Heat pipe-based cooling systems can offer higher thermal performance and lighter weight compared to die-cast heat sinks for LED headlamps.
4. Research Methodology:
- Research Design: Design and characterization of heat pipe cooling systems for various LED headlamp designs and styles.
- Data Collection Method: Characterization of steady-state thermal performance (operating temperature and thermal resistance), temperature measurement using T-type thermocouples (accuracy +/- 0.1 °C), heat load provision using thermal simulators (current and voltage accuracy +/-0.01 A or V).
- Analysis Method: Thermal resistance analysis, comparison of different cooling solutions.
- Research Subjects and Scope: Various heat pipe designs including high-performance cylindrical/flattened copper-water heat pipes for low/high beam cooling, hinge heat pipes for adaptive headlamps with swivel function cooling, and flexible heat pipes for remotely mounted heat sinks.
5. Key Research Findings:
- Core Findings: Heat pipe heat sinks provide "40-50% lighter" weight and "2-3 times higher thermal capability" compared to die-cast heat sinks. Heat pipe merits include "ultra-thin form factor, higher degrees of freedom and higher design tolerance."
- Statistical/Qualitative Analysis Results:
- Heat pipe heat sinks maintained LED package temperature below 80°C at a 25°C ambient temperature.
- The total thermal resistance from the LED junction to ambient air for the hinge heat pipe assembly was "6.89 °C/W".
- Piezo fan cooling reduced the source temperature by "7.6 °C" and increased the enclosure air temperature by "3.7 °C".
- Data Interpretation: Heat pipes drastically improve heat dissipation capability and enable better space utilization and passive cooling.
- Figure List:
- Fig. 1. Heat load output by different lamp types.
- Fig. 2. Heat output versus device length for different automotive electronic/electric systems.
- Fig. 3. LED package for automotive headlamp.
- Fig. 4. Schematic of LED package with thermal module (top), and system thermal resistance network (bottom).
- Fig. 5a. Cooling module design for automotive headlamp.
- Fig. 5b. Heat pipe heat sink for cooling high beam LED package inside head-lamp.
- Fig. 6. Heat pipe heat sink for headlamp high beam cooling.
- Fig. 7. Thermal test on LED headlamp with heat pipe based cooling of high beam.
- Fig. 8. Breakdown thermal resistance for different components from LED junction to ambient air.
- Fig. 9. Hinge heat pipe assembly.
- Fig. 10. Hinge heat pipe assembly for cooling LED package with swivel function.
- Fig. 11. Flexible heat pipe.
- Fig. 12. Heat pipe assembly with frame as heat sink.
- Fig. 13. Heat pipe assembly for cooling fog light LED package in headlamp.
- Fig. 14. Heat pipe heat sink for low beam LED package cooling.
- Fig. 15. Axial fan installed inside headlamp for forced convection cooling.
- Fig. 16. Round type Piezo fan.
- Fig. 17. Velocity profile of round piezo fan.
- Fig. 18. Cooling enhancement for LED headlamp using piezo fan.
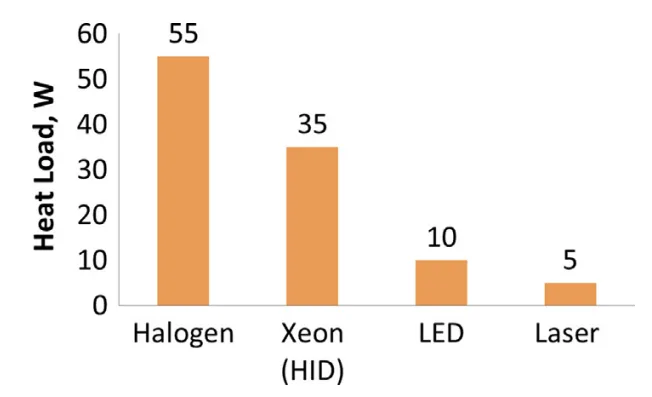
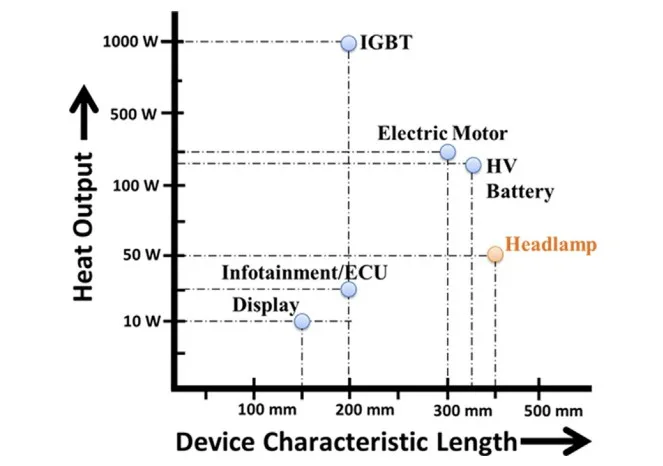
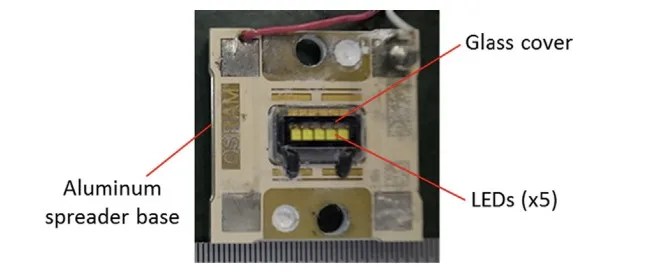
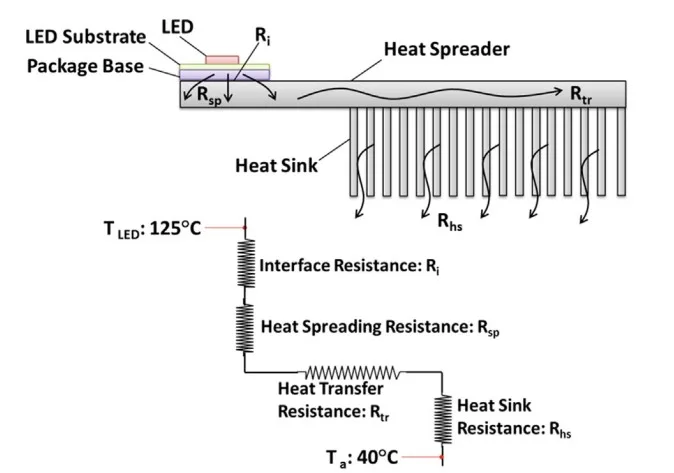
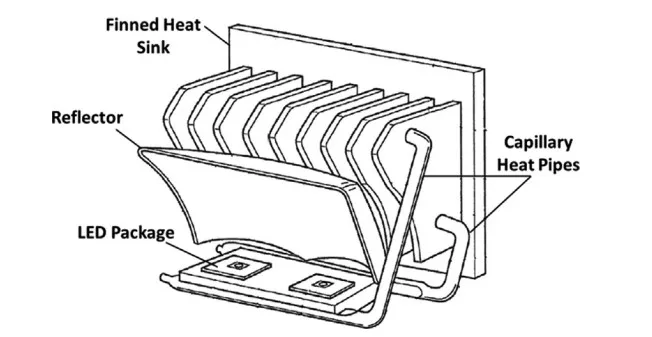
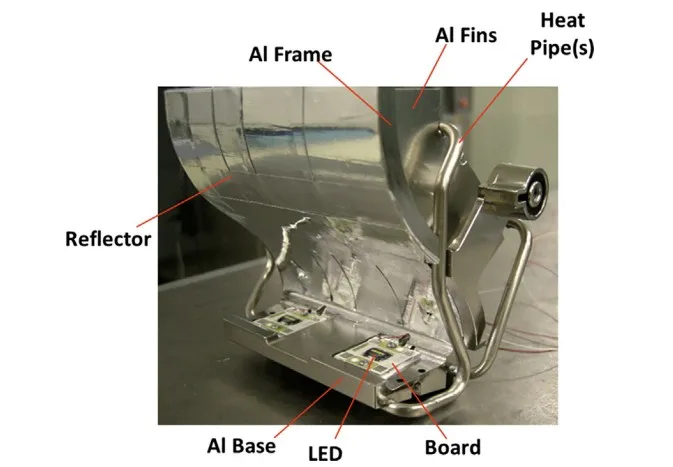
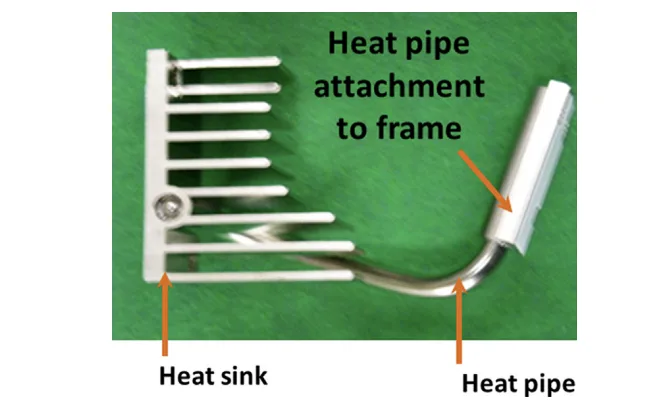
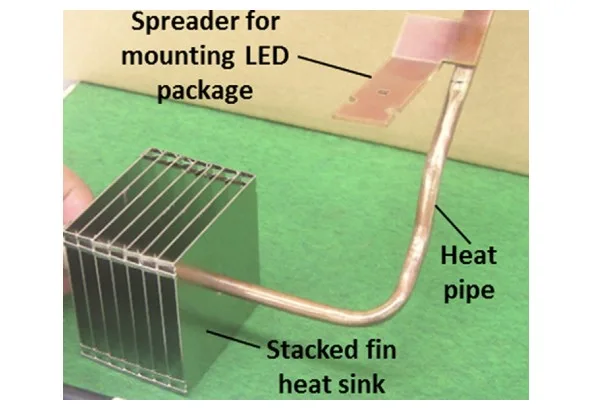
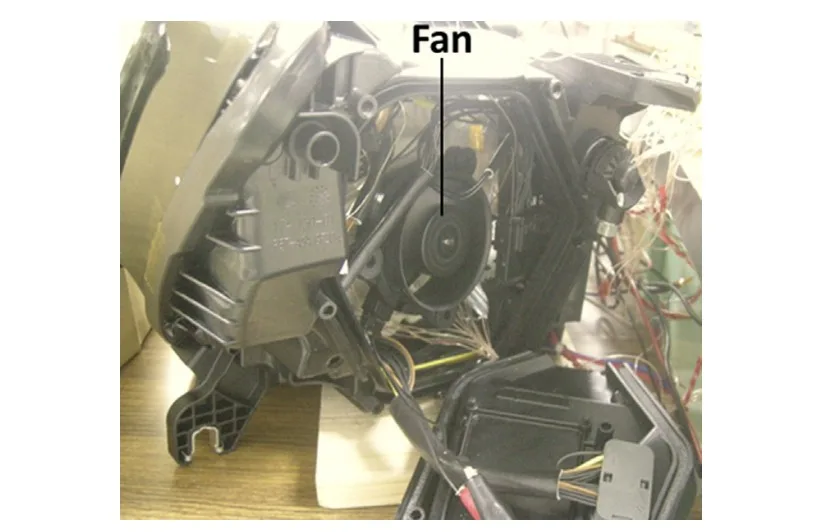
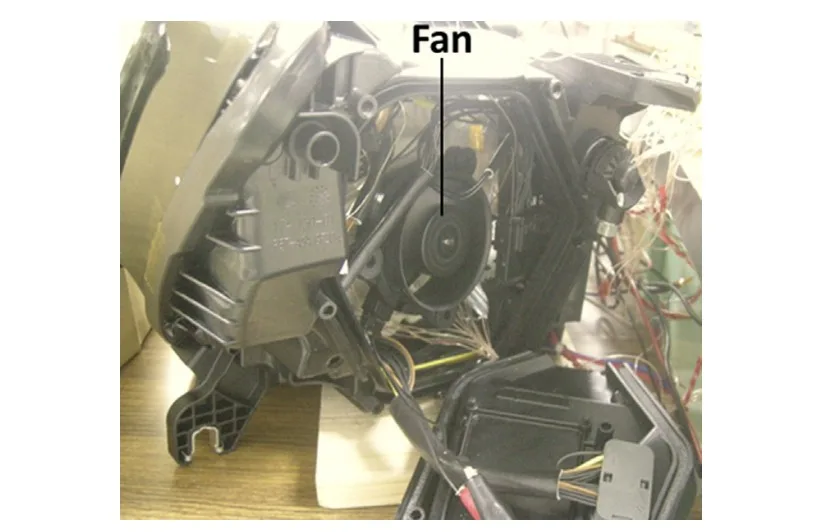
6. Conclusion and Discussion:
- Summary of Key Results: Heat pipe cooling solutions for LED headlamps are lighter and offer higher thermal performance than die-cast heat sinks. Various heat pipe designs (cylindrical, flattened, hinge, flexible) were developed and tested.
- Academic Significance of the Research: Demonstrated the effectiveness of heat pipes for LED headlamp cooling and provided design options for various headlamp styles.
- Practical Implications: Heat pipe technology offers a viable solution for efficient and compact cooling of next-generation LED headlamps, enabling passive cooling and better space utilization.
- Limitations of the Research: The paper does not explicitly mention limitations.
8. References:
[1] US Department of Energy, Energy Efficiency of LEDs, PNNL-SA-94206, March 2013, Available: http://energy.gov/eere/ssl/downloads/energy-efficiency-leds.
[2] OSRAM GmBH, Viewed: 27 March 2016, Available: http://www.osram-os.com/osram_os/en/index.jsp.
[3] R. Singh, M. Mochizuki, Y. Saito, T. Yamada, T. Nguyen, Ti Nguyen, Heat pipes applications in cooling automotive electronics, Heat Pipe Sci. Technol. An Int. J. 6 (3) (2015) 1-13.
[4] M. Mochizuki, Y. Saito, K. Mashiko, T. Raay, R. Singh, High power heat removal by heat pipes & two phase heat transfer for electric vehicle, 53rd Japan Heat Transfer Symposium, (2016).
[5] B. Orr, A. Akbarzadeh, M. Mochizuki, R. Singh, A review of car waste heat recovery systems utilising thermoelectric generators and heat pipes, Appl. Therm. Eng. (2016), https://doi.org/10.1016/j.applthermaleng.2015.10.081.
[6] R. Singh, M. Mochizuki, Y. Saito, T. Yamada, T. Nguyen, Ti Nguyen, A. Akbarzadeh, Loop heat pipe applications in automotive thermal control, Proc. 17th International Heat
9. Copyright:
This material is based on the paper: [Original Paper Title] by [Paper Author].
This material is a summary based on the above paper, and unauthorized use for commercial purposes is prohibited.
Copyright © 2025 CASTMAN. All rights reserved.